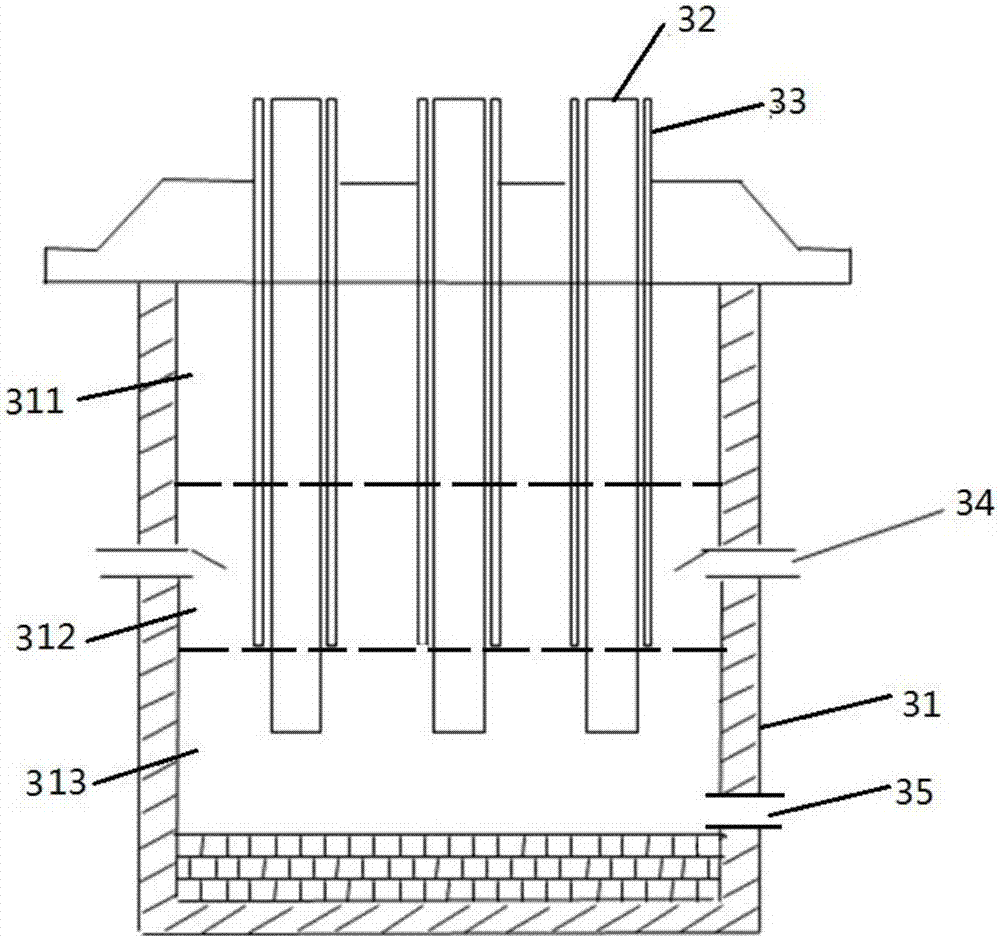
本發(fā)明屬于電石生產(chǎn)
技術(shù)領(lǐng)域:
,尤其涉及一種電石渣回收利用的系統(tǒng)及方法。
背景技術(shù):
:電石是一種重要的化工原料,目前,工業(yè)上生產(chǎn)電石的方法主要是電熱法。其先把符合電石生產(chǎn)需求的石灰和焦碳按規(guī)定的配比進(jìn)行配料,然后用斗式提升機(jī)將爐料送至電石爐爐頂料倉,經(jīng)過料管向電爐內(nèi)加料,爐料在電爐內(nèi)經(jīng)過電極電弧墊和爐料的電阻熱反應(yīng)生成電石,電石定時出爐,放至電石鍋內(nèi),經(jīng)冷卻后,破碎成一定規(guī)格要求的粒度,即得到成品電石。在電石的生產(chǎn)過程中,原料中的雜質(zhì)對生產(chǎn)影響嚴(yán)重。原料中的雜質(zhì)主要包括氧化鎂、氧化硅、氧化鐵、氧化鋁等,當(dāng)爐料在電爐內(nèi)反應(yīng)生成碳化鈣的同時,各種雜質(zhì)也進(jìn)行反應(yīng)。各種雜質(zhì)的反應(yīng)不僅消耗電能和碳材,而且影響操作,破壞爐底,特別是氧化鎂在熔融區(qū)迅速還原成金屬鎂,而使熔融區(qū)成為一個強(qiáng)烈的高溫還原區(qū),鎂蒸氣從這個熾熱的區(qū)域大量逸出時,其中一部分鎂與一氧化碳立即起反應(yīng),生成氧化鎂放出強(qiáng)熱形成高溫,局部硬殼遭到破壞,使帶有雜質(zhì)的液態(tài)電石侵蝕爐底。利用電石生產(chǎn)乙炔時,會排放出大量的電石渣,其主要化學(xué)成份為ca(oh)。目前對于無法利用的固體廢棄物的處理方法大多采用填埋法,占用了大量土地,企業(yè)需支付大量的征地與管理費(fèi)用,而且還會通過滲透污染填埋場周邊的水源,使水源、土地堿化,對生存環(huán)境造成危害。技術(shù)實現(xiàn)要素:為了解決上述問題,本發(fā)明期望提出一種在電石生產(chǎn)時,可避免雜質(zhì)中的鎂在爐體內(nèi)發(fā)生氧化反應(yīng)的系統(tǒng)及方法,同時利用生產(chǎn)乙炔的電石渣作為鈣基原料生產(chǎn)電石,節(jié)約原料,降低生產(chǎn)成本。本發(fā)明的目的之一是提供一種電石渣回收利用的系統(tǒng),包括預(yù)處理單元、熱解爐、電石爐和乙炔發(fā)生裝置;所述預(yù)處理單元包括焙燒裝置和造球裝置;所述焙燒裝置包括鈣基原料入口和造球鈣料出口;所述造球裝置包括造球原煤入口、造球鈣料入口和球形料出口;所述焙燒裝置的造球鈣料出口連接所述造球裝置的造球鈣料入口;所述熱解爐包括球形料入口和固體物料出口;所述電石爐包括爐體、進(jìn)料管、排氣管和電石出口;所述爐體的內(nèi)腔包括熱層區(qū),所述電石爐工作時,所述熱層區(qū)的溫度為1400~1600℃;所述進(jìn)料管由所述爐體的頂部深入到所述爐體的內(nèi)腔;所述排氣管位于所述熱層區(qū),所述排氣管穿過所述爐體的側(cè)壁與外部連通;所述排氣管包括擋板,所述擋板傾斜的固定在所述排氣管的進(jìn)氣口;所述電石出口位于所述電石爐的底部;所述乙炔發(fā)生裝置包括電石入口、乙炔出口和電石渣出口;所述造球裝置的球形料出口連接所述熱解爐的球形料入口,所述熱解爐的固體物料出口連接所述電石爐的進(jìn)料管,所述電石爐的電石出口連接所述乙炔發(fā)生裝置的電石入口,所述乙炔發(fā)生裝置的電石渣出口連接所述焙燒裝置的鈣基原料入口。所述乙炔發(fā)生裝置采用干法乙炔工藝,電石渣出口與所述焙燒裝置的鈣基原料入口采用管帶機(jī)相連。進(jìn)一步的,所述預(yù)處理單元還包括干燥裝置,所述干燥裝置包括原煤入口和造球原煤出口,所述干燥裝置的造球原煤出口連接所述造球裝置的造球原煤入口。本發(fā)明的系統(tǒng),進(jìn)一步包括煙道和吸附裝置;所述煙道包括尾氣進(jìn)口和煙氣出口;所述吸附裝置包括煙氣入口;所述電石爐的排氣管的出氣口連接所述煙道的尾氣進(jìn)口,所述煙道的煙氣出口連接所述吸附裝置的煙氣入口。更進(jìn)一步的,所述吸附裝置進(jìn)一步包括高溫氣出口,所述熱解爐包括高溫氣入口,所述吸附裝置的高溫氣出口連接所述熱解爐的高溫氣入口。作為本發(fā)明的優(yōu)選方案,所述排氣管的擋板與水平方向的夾角為30~60°。本發(fā)明的另一目的是提供一種利用上述系統(tǒng)回收利用電石渣的方法,包括如下步驟:a、將鈣基原料送入焙燒裝置進(jìn)行焙燒,獲得造球鈣料;將所述造球鈣料送入造球裝置,與造球原煤混合造球,獲得球形料;b、將所述球形料送入熱解爐,發(fā)生熱解反應(yīng),獲得固體物料;c、將所述固體物料送入電石爐,加熱至2100~2300℃,生成電石和含鎂蒸氣的尾氣,將所述含鎂蒸氣的尾氣排出所述電石爐;d、將所述電石送入乙炔發(fā)生裝置,獲得乙炔和電石渣;e、將所述電石渣作為鈣基原料送入所述焙燒裝置。優(yōu)選的,此焙燒裝置采用熱解氣、電石爐尾氣、天然氣或其他可燃?xì)怏w作為燃料。進(jìn)一步的,熱解反應(yīng)溫度為500-900℃,優(yōu)選為600-800℃。優(yōu)選的,在步驟a之前包括步驟:將原煤進(jìn)行干燥,獲得造球原煤;將所述造球原煤送入所述造球裝置。進(jìn)一步的,本發(fā)明的方法還包括步驟:將排出所述電石爐的含鎂蒸氣的尾氣通過煙道冷卻,發(fā)生氧化反應(yīng),生成含氧化鎂的煙氣;將所述煙氣送入吸附裝置,吸附收集氧化鎂,排出剩余的高溫氣。更進(jìn)一步的,本發(fā)明的方法還包括步驟:將所述高溫氣送入所述熱解爐,作為熱解反應(yīng)的熱源。具體的,所述鈣基原料包括石灰、石灰石、熟石灰和電石渣中的一種或多種。本發(fā)明提供的電石渣回收利用的系統(tǒng)及方法,將排氣管設(shè)置在電石爐的熱層區(qū),可以保證尾氣中的鎂蒸氣不發(fā)生氧化反應(yīng),避免了料面結(jié)塊和塌料的發(fā)生;排氣管的進(jìn)氣口的管壁上設(shè)置有擋板,在料層內(nèi)可形成局部空腔,尾氣匯集到空腔內(nèi),便于收集后排出;利用除塵布袋吸附氧化鎂,可獲得高附加值副產(chǎn)品;吸附氧化鎂剩余的高溫氣用于球形料的熱解,實現(xiàn)了廢氣的再利用,降低生產(chǎn)成本;本發(fā)明的系統(tǒng)通過將電石爐尾氣出口設(shè)置在電石爐中下部,使得電石爐尾氣溫度在1400~1600℃左右,則原料中的氧化鎂經(jīng)碳還原后,作為鎂蒸氣排出電石爐,實現(xiàn)在電石生產(chǎn)過程中脫除原料雜質(zhì)的目的,從而提高電石渣純度,有利于電石渣回用生產(chǎn)電石。利用生產(chǎn)乙炔剩余的電石渣,作為鈣基原料,實現(xiàn)了廢物的再利用。附圖說明圖1是本發(fā)明實施例的系統(tǒng)的示意圖;圖2是本發(fā)明實施例的電石爐的結(jié)構(gòu)示意圖;圖3是本發(fā)明實施例的方法的流程圖。具體實施方式以下結(jié)合附圖和實施例,對本發(fā)明的具體實施方式進(jìn)行更加詳細(xì)的說明,以便能夠更好地理解本發(fā)明的方案及其各個方面的優(yōu)點。然而,以下描述的具體實施方式和實施例僅是說明的目的,而不是對本發(fā)明的限制。如圖1所示,本發(fā)明實施例提供一種電石渣回收利用的系統(tǒng),包括預(yù)處理單元1、熱解爐2、電石爐3、煙道4、吸附裝置5和乙炔發(fā)生裝置6。本發(fā)明實施例的系統(tǒng),電石爐3產(chǎn)生電石的同時排出含鎂蒸氣的尾氣,對尾氣進(jìn)行處理后獲得氧化鎂,剩余的高溫氣可為熱解爐的熱解反應(yīng)提供熱量;利用生產(chǎn)乙炔剩余的電石渣,作為鈣基原料,實現(xiàn)了廢物的利用,節(jié)約生產(chǎn)成本。預(yù)處理單元1包括干燥裝置11、焙燒裝置12和造球裝置13。預(yù)處理單元1為熱解爐提供原料。干燥裝置11包括原煤入口111和造球原煤出口112。干燥裝置11用于對碳基原料原煤進(jìn)行干燥,獲得造球原煤。焙燒裝置12包括鈣基原料入口121和造球鈣料出口122。焙燒裝置12可對鈣基原料焙燒,獲得造球鈣料。造球裝置13包括造球原煤入口131、造球鈣料入口132和球形料出口133,干燥裝置11的造球原煤出口112連接造球裝置13的造球原煤入口131,焙燒裝置12的造球鈣料出口122連接造球裝置13的造球鈣料入口132。干燥裝置11產(chǎn)生的造球原煤和焙燒裝置12產(chǎn)生的造球鈣料,送入造球裝置13,獲得熱解爐所需的球形料。熱解爐2包括球形料入口21、固體物料出口22和熱解油氣出口23,造球裝置13的球形料出口133連接熱解爐2的球形料入口21。球形料進(jìn)入熱解爐2后,受熱發(fā)生熱解反應(yīng),生成固體物料和熱解油氣。固體物料通過固體物料出口22排出熱解爐2。熱解油氣通過熱解油氣出口23進(jìn)行收集,對收集的熱解油氣進(jìn)行處理后,可獲得高附加值的油氣產(chǎn)品。如圖2所示,電石爐3包括爐體31、電極32、進(jìn)料管33、排氣管34和電石出口35,熱解爐2的固體物料出口連接電石爐3的進(jìn)料管33。固體物料在電石爐3內(nèi),被加熱到高溫,發(fā)生反應(yīng),生成電石。電石出口35位于電石爐的底部,用于電石的排出。爐體31的內(nèi)部為空腔,在生產(chǎn)電石時,爐體31內(nèi)空腔的溫度由下向上逐步降低。根據(jù)生產(chǎn)電石時的腔內(nèi)溫度,將空腔由上至下依次分為料層區(qū)311、熱層區(qū)312和反應(yīng)區(qū)313,熱層區(qū)的溫度為1400~1600℃。在1400~1600℃的溫度區(qū)間,可以保證尾氣中的鎂蒸氣不與co發(fā)生氧化反應(yīng)。料層區(qū)311為物料的預(yù)熱區(qū),物料在料層區(qū)311與下部上升的氣體進(jìn)行熱交換。反應(yīng)區(qū)313的溫度在2000℃左右,物料在此區(qū)域發(fā)生反應(yīng),生成電石,同時雜質(zhì)中的氧化鎂發(fā)生還原反應(yīng),生成鎂蒸氣。電極32嵌入爐頂31的頂部,延伸到爐體31的空腔中,但不與爐底接觸,為電石的生產(chǎn)提供能量。進(jìn)料管33由爐體的頂部深入到爐體31的內(nèi)腔。進(jìn)料管33用于將物料送入爐體內(nèi)。進(jìn)料管33布置在電極32的周圍,可使得進(jìn)入爐體的固體物料均勻的受熱,有利于提高生產(chǎn)效率,節(jié)約能源。排氣管34位于熱層區(qū)312,用于抽出含鎂蒸氣的尾氣。排氣管34穿過爐體31的側(cè)壁與外部連通。排氣管34包括擋板,所述擋板傾斜的固定在排氣管34的進(jìn)氣口管壁上。擋板與水平面的夾角為30~60°,這樣的設(shè)計可以在物料層中形成空腔區(qū)域,便于尾氣匯集到空腔區(qū)域,從排氣管排到爐外。煙道4包括尾氣進(jìn)口41和煙氣出口42,電石爐的排氣管34連通煙道4的尾氣進(jìn)口41。通過排氣管34排出爐體的含有鎂蒸氣的尾氣進(jìn)入煙道4,溫度迅速下降,當(dāng)含有鎂蒸氣的尾氣溫度降至1200℃以下時,發(fā)生反應(yīng):mg+co=mgo+c,生成氧化鎂。吸附裝置5包括煙氣入口51和高溫氣出口52,煙道4的煙氣出口42連接吸附裝置5的煙氣入口51。煙道4中產(chǎn)生的氧化鎂與其他尾氣一同進(jìn)入吸附裝置5,吸附裝置5具有吸附功能,可吸附收集氧化鎂,排出剩余的氣體。本發(fā)明實施例的裝置,不僅避免了電石原料中氧化鎂雜質(zhì)對電石生產(chǎn)的影響,而且可收集高附加值的副產(chǎn)物氧化鎂,取得更大的經(jīng)濟(jì)效益。吸附的氧化鎂由氧化鎂出口53排出。熱解爐2上設(shè)有高溫氣入口24,吸附裝置5的高溫氣出口52連接熱解爐2的高溫氣入口24。吸附裝置5吸附收集氧化鎂后,將剩余的高溫尾氣送入熱解爐2中,作為熱解反應(yīng)的熱源,實現(xiàn)剩余高溫氣的再利用,節(jié)約生產(chǎn)成本。乙炔發(fā)生裝置6包括電石入口61、乙炔出口62和電石渣出口63,電石爐3的電石出口35連接乙炔發(fā)生裝置6的電石入口61,乙炔發(fā)生裝置6的電石渣出口63連接焙燒裝置12的鈣基原料入口121。電石爐3生產(chǎn)的電石進(jìn)入乙炔發(fā)生裝置6,生成乙炔,由乙炔出口62輸送到儲存罐進(jìn)行儲存。產(chǎn)生乙炔剩余的電石渣,作為鈣基原料進(jìn)入焙燒裝置102,用于球形料的制備,充分利用了系統(tǒng)自身的產(chǎn)物,做到了物盡其用,降低生產(chǎn)成本。如圖3所示,另一方面,本發(fā)明實施例提供一種利用上述系統(tǒng)回收利用電石渣的方法,包括如下步驟:1、將原煤進(jìn)行干燥,獲得造球原煤;將造球原煤送入造球裝置。2、將鈣基原料送入焙燒裝置進(jìn)行焙燒,獲得造球鈣料;將造球鈣料送入造球裝置,與造球原煤混合造球,獲得球形料,造球原煤和造球鈣料的質(zhì)量比為0.6~1.4:1,優(yōu)選0.8~1:1。3、將球形料送入熱解爐,發(fā)生熱解反應(yīng),獲得固體物料。4、將固體物料送入電石爐,加熱至2100~2300℃,生成電石和含鎂蒸氣的尾氣,將含鎂蒸氣的尾氣排出電石爐。5、將電石送入乙炔發(fā)生裝置,獲得乙炔和電石渣。6、將電石渣作為鈣基原料送入步驟2的焙燒裝置。7、將排出電石爐的含鎂蒸氣的尾氣通過煙道冷卻,發(fā)生氧化反應(yīng),生成含氧化鎂的煙氣;將煙氣送入吸附裝置,吸附收集氧化鎂,排出剩余的高溫氣。8、將高溫氣送入熱解爐,作為熱解反應(yīng)的熱源。具體的,步驟2中的鈣基原料包括石灰、石灰石、熟石灰和電石渣中的一種或多種。在步驟3中,熱解反應(yīng)溫度為500-900℃,優(yōu)選為600-800℃,例如為650℃、700℃、750℃,本領(lǐng)域人員可根據(jù)具體情況選擇。電石渣中主要雜質(zhì)為二氧化硅和氧化鎂等,電石渣焙燒溫度為600~800℃。實施例1中低階粉煤,采用某地長焰煤,成分如表1,表中收到基是指收到煤炭的狀態(tài),一般煤炭在開采和運(yùn)輸過程中會噴淋大量水,所以,全水的測定是收到基的煤炭;干基是指將煤炭經(jīng)過充分烘干后獲得的煤炭基準(zhǔn),此時煤炭中基本沒有水分。表1長焰煤成分項目單位數(shù)值備注全水wt%5.33收到基固定碳wt%55.7干基揮發(fā)分wt%37.2干基灰分wt%7.1干基對石灰石進(jìn)行焙燒,獲得石灰,石灰的成分如表2:表2石灰成分tfe/%cao/%mgo/%sio2/%al2o3/%mno2/%so3/%p2o5/%其他/%0.3291.72.411.620.550.110.020.033.241、將長焰煤干燥后,與石灰混合均勻,長焰煤與石灰的質(zhì)量比為0.93:1,獲得混合物料,對混合物料進(jìn)行造球處理,獲得球形料。2、將球形料送至熱解爐,以吸附裝置排出的高溫氣為熱解熱源,將球形料加熱至700℃左右,發(fā)生熱解反應(yīng),產(chǎn)出固體物料及高附加值的熱解氣和熱解油。3、將高溫固體物料輸送至密閉電石爐內(nèi),通過電極明弧放熱將物料加熱至2200℃左右,生產(chǎn)電石,同時產(chǎn)出的高溫的含有鎂蒸氣的尾氣;尾氣通過設(shè)置于電石爐側(cè)面中下部的排氣管排出電石爐外,排氣管上部設(shè)置水平向下的擋板,擋板與水平線角度為45°,電石爐中含鎂蒸氣的尾氣出爐溫度為1500℃左右。4、含鎂蒸氣的尾氣通過煙道后,溫度降至1200℃左右,鎂發(fā)生氧化反應(yīng),生成氧化鎂。5、含氧化鎂的煙氣進(jìn)入吸附裝置,獲得副產(chǎn)含量約58%的高附加值氧化鎂產(chǎn)品。產(chǎn)品電石中含碳化鈣80.9%,發(fā)氣量301l/kg。6、電石爐產(chǎn)生的電石,經(jīng)冷卻后送至干法乙炔發(fā)生裝置,產(chǎn)出乙炔和電石渣,乙炔經(jīng)凈化處理后送至儲罐儲存。7、將電石渣送至焙燒裝置,作為石灰原料使用,經(jīng)700℃焙燒后獲得石灰。需要說明的是,以上參照附圖所描述的各個實施例僅用以說明本發(fā)明而非限制本發(fā)明的范圍,本領(lǐng)域的普通技術(shù)人員應(yīng)當(dāng)理解,在不脫離本發(fā)明的精神和范圍的前提下對本發(fā)明進(jìn)行的修改或者等同替換,均應(yīng)涵蓋在本發(fā)明的范圍之內(nèi)。此外,除上下文另有所指外,以單數(shù)形式出現(xiàn)的詞包括復(fù)數(shù)形式,反之亦然。另外,除非特別說明,那么任何實施例的全部或一部分可結(jié)合任何其它實施例的全部或一部分來使用。當(dāng)前第1頁12