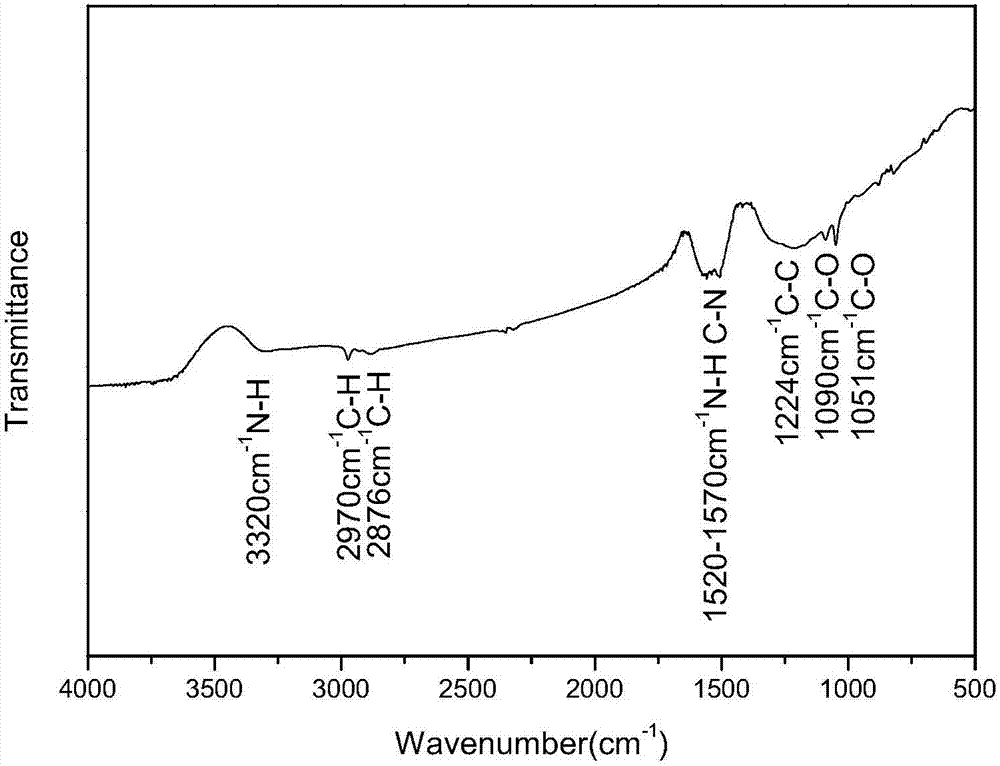
本發(fā)明屬于功能材料改性領(lǐng)域,具體涉及一種氨基化石墨烯的制備方法。
背景技術(shù):
:石墨烯作為一種新興的材料,由于其優(yōu)良的性能,從發(fā)現(xiàn)至今經(jīng)歷了迅猛的發(fā)展。石墨烯具有良好的導(dǎo)電性能、機(jī)械性能和光學(xué)性能,而且石墨烯的比表面積大,但是單層的石墨烯很難在水溶液中穩(wěn)定存在,容易發(fā)生團(tuán)聚,這一難題限制了石墨烯的發(fā)展應(yīng)用,所以開發(fā)一種分散性良好的親水性石墨烯成為一個棘手的問題。氨基化石墨烯不僅保留了石墨烯良好的導(dǎo)電性、機(jī)械性能和光學(xué)性能,還具有大的比表面積。此外,氨基基團(tuán)對重金屬有較好的吸附性,而且氨基化石墨烯可以在水溶液中穩(wěn)定存在,不易發(fā)生團(tuán)聚。將氨基化石墨烯應(yīng)用于水溶液中重金屬離子的檢測,不僅可以降低檢測下限,還可以提高檢測的靈敏度。但是,傳統(tǒng)的氨基化石墨烯工藝路線雖然操作簡單,但是得到的氨基含量偏低,不超過10.0wt%。而且在合成過程中使用的四氫呋喃、氯化亞砜等不僅對環(huán)境危害大,而且長期接觸對從業(yè)人員的身體健康造成不可逆轉(zhuǎn)的損害。傳統(tǒng)合成氨基化石墨烯方法中涉及到的球磨工藝,不僅會破壞石墨烯片層結(jié)構(gòu),而且機(jī)械方式摻入氨基致使大部分氨基以物理吸附的方式存在于產(chǎn)品中,只有很小一部分氨基以化學(xué)鍵的形式與石墨烯成鍵存在于產(chǎn)物中,此種方法得到的氨基化石墨烯的反應(yīng)活性位點會減少,不能達(dá)到預(yù)期效果。因此,尋求一種高效的合成氨基化石墨烯的工藝迫在眉睫。技術(shù)實現(xiàn)要素:本發(fā)明的目的在于提供一種避免石墨烯片層結(jié)構(gòu)破壞、出現(xiàn)團(tuán)聚,且氨基含量高的氨基化石墨烯的制備方法。本發(fā)明解決其技術(shù)問題所采用的技術(shù)方案是:一種氨基化石墨烯的制備方法,包括以下步驟:(1)將質(zhì)量比1:1的naoh和氯乙酸依次加入0.5~2mol·l-1氧化石墨烯水溶液中,在15-50℃下攪拌反應(yīng)3-12h,然后離心洗滌至離心液的ph值為7,得到羧基化石墨烯;(2)將羧基化石墨烯充分分散在水溶液中,配制成濃度為1mg·ml-1的羧基化石墨烯溶液,用氨水調(diào)ph值為10~12,室溫下攪拌6~12h,離心洗滌至洗液的ph值為7,得到酰胺基化石墨烯溶液,冷凍干燥得到酰氨基化石墨烯粉體;(3)將酰氨基化石墨烯粉體溶解在n-甲基吡咯烷酮中,加入三氯氧磷,反應(yīng)溫度保持40-100℃,攪拌3~15h,然后減壓蒸餾除去三氯氧磷,酰氨基化石墨烯脫水后得到氰基化石墨烯;(4)將氰基化石墨烯和催化劑混合,氰基化石墨烯與催化劑的質(zhì)量比1:1-1:10,混合后后按照100-300ml·min-1通入h2,反應(yīng)溫度為500~1000℃,恒溫保持3~10h,進(jìn)行催化加氫得到氨基化石墨烯。具體地,所述步驟(1)中氧化石墨烯由化學(xué)氧化法制得,使用濃硫酸和濃磷酸體積比為1:1~10:1,氧化時間為1~10h;氧化石墨烯和氯乙酸的質(zhì)量比為1:5~1:15。具體地,所述步驟(3)中酰胺基化石墨烯的n-甲基吡咯烷酮溶液的濃度為1~5mg·ml-1;酰氨基化石墨烯與三氯氧磷的質(zhì)量比為1:1-1:10。具體地,所述步驟(4)中催化劑為ru-m-b/zro2,其中m=sc、ti、v、zn、fe、mn、co、ni、cu、cr、mo、y、zr、nb、tc、rh、pd、ag或cd。本發(fā)明具有以下有益效果:本發(fā)明方法制備的氨基化石墨烯可避免石墨烯片層的團(tuán)聚,有效防止在合成過程中氨基化石墨烯結(jié)構(gòu)的改變,本方法區(qū)別于機(jī)械球磨,可防止合成過程中石墨烯片層結(jié)構(gòu)的破壞。本發(fā)明制備的氨基化石墨烯中氨基的含量超過15.0wt%,最高可達(dá)到25.0wt%,而傳統(tǒng)方法合成的氨基化石墨烯中的氨基含量最高不超過10.0wt%。附圖說明圖1是本發(fā)明實施例8中制備的氨基化石墨烯的sem圖。圖2是本發(fā)明實施例8中制備的氨基化石墨烯的ftir圖。具體實施方式以下是本發(fā)明的具體實施例,對本發(fā)明的技術(shù)方案做進(jìn)一步描述,但是本發(fā)明的保護(hù)范圍并不限于這些實施例。凡是不背離本發(fā)明構(gòu)思的改變或等同替代均包括在本發(fā)明的保護(hù)范圍之內(nèi)。實施例1(1)氧化石墨烯的制備本發(fā)明中合成氧化石墨烯的方法為化學(xué)氧化法。本發(fā)明中氨基的來源為氧化石墨烯中的羧基,所以氧化石墨烯中的羧基含量直接影響氨基化石墨烯中氨基的摻雜量。因此,我們在合成氧化石墨烯的過程中,通過將濃硫酸改為濃硫酸與濃磷酸的混酸和延長氧化時間提高石墨的氧化程度,增加反應(yīng)活性位點。濃硫酸與濃磷酸的體積比為1:1,氧化時間為2h。(2)氨基化石墨烯的制備將氧化石墨烯在水溶液中分散均勻,濃度為1mol·l-1,然后加入質(zhì)量比為1:1的naoh和氯乙酸,氧化石墨烯與氯乙酸的質(zhì)量比為1:5,室溫25℃下攪拌5h,離心過濾洗滌得到羧基化石墨烯。將得到的羧基化石墨烯在水溶液中分散均勻后,配制成濃度為1mg·ml-1的羧基化石墨烯溶液,用氨水調(diào)ph值為12,在室溫下攪拌6h,離心洗滌至洗液的ph值為7,得到酰胺基化石墨烯溶液,冷凍干燥得到酰氨基化石墨烯粉體;將酰氨基化石墨烯在n-甲基吡咯烷酮中分散均勻,濃度為3mg·ml-1;然后將三氯氧磷以質(zhì)量比1:5加入,60℃反應(yīng)5h后減壓蒸餾去除三氯氧磷,酰氨基化石墨烯脫水生成氰基化石墨烯。將氰基化石墨烯與催化劑ru-cr-b/zro2以質(zhì)量比1:3混合,然后通入h2,控制在100ml·min-1,反應(yīng)溫度控制為600℃,反應(yīng)時間為3h,氰基化石墨烯加氫后生成氨基化石墨烯。本實施例中氨基化石墨烯的氨基含量為15.8wt%。實施例2(1)氧化石墨烯的制備本發(fā)明中合成氧化石墨烯的方法為化學(xué)氧化法。本發(fā)明中氨基的來源為氧化石墨烯中的羧基,所以氧化石墨烯中的羧基含量直接影響氨基化石墨烯中氨基的摻雜量。因此,我們在合成氧化石墨烯的過程中,通過將濃硫酸改為濃硫酸與濃磷酸的混酸和延長氧化時間提高石墨的氧化程度,增加反應(yīng)活性位點。濃硫酸與濃磷酸的體積比為3:1,氧化時間為5h。(2)氨基化石墨烯的制備將氧化石墨烯在水溶液中分散均勻,濃度為0.5mol·l-1,然后加入質(zhì)量比為1:1的naoh和氯乙酸,氧化石墨烯與氯乙酸的質(zhì)量比為1:10,15℃下攪拌8h,離心過濾洗滌得到羧基化石墨烯。將得到的羧基化石墨烯在水溶液中分散均勻后,配制成濃度為1mg·ml-1的羧基化石墨烯溶液,用氨水調(diào)ph值為11,在室溫下攪拌7h,離心洗滌至洗液的ph值為7,得到酰胺基化石墨烯溶液,冷凍干燥得到酰氨基化石墨烯粉體;將酰氨基化石墨烯在n-甲基吡咯烷酮中分散均勻,濃度為5mg·ml-1;然后將三氯氧磷以質(zhì)量比1:1加入,50℃反應(yīng)3h后減壓蒸餾去除三氯氧磷,酰氨基化石墨烯脫水生成氰基化石墨烯。將氰基化石墨烯與催化劑ru-ti-b/zro2以質(zhì)量比1:7混合,然后通入h2,控制在200ml·min-1,反應(yīng)溫度控制為700℃,反應(yīng)時間為7h,氰基化石墨烯加氫后生成氨基化石墨烯。本實施例中氨基化石墨烯的氨基含量為17.5wt%。實施例3(1)氧化石墨烯的制備本發(fā)明中合成氧化石墨烯的方法為化學(xué)氧化法。本發(fā)明中氨基的來源為氧化石墨烯中的羧基,所以氧化石墨烯中的羧基含量直接影響氨基化石墨烯中氨基的摻雜量。因此,我們在合成氧化石墨烯的過程中,通過將濃硫酸改為濃硫酸與濃磷酸的混酸和延長氧化時間提高石墨的氧化程度,增加反應(yīng)活性位點。濃硫酸與濃磷酸的體積比為8:1,氧化時間為3h。(2)氨基化石墨烯的制備將氧化石墨烯在水溶液中分散均勻,濃度為2mol·l-1,然后加入質(zhì)量比為1:1的naoh和氯乙酸,氧化石墨烯與氯乙酸的質(zhì)量比為1:15,30℃下攪拌12h,離心過濾洗滌得到羧基化石墨烯。將得到的羧基化石墨烯在水溶液中分散均勻后,配制成濃度為1mg·ml-1的羧基化石墨烯溶液,用氨水調(diào)ph值為10,在室溫下攪拌8h,離心洗滌至洗液的ph值為7,得到酰胺基化石墨烯溶液,冷凍干燥得到酰氨基化石墨烯粉體;將酰氨基化石墨烯在n-甲基吡咯烷酮中分散均勻,濃度為4mg·ml-1;然后將三氯氧磷以質(zhì)量比1:7加入,40℃反應(yīng)8h后減壓蒸餾去除三氯氧磷,酰氨基化石墨烯脫水生成氰基化石墨烯。將氰基化石墨烯與催化劑ru-zn-b/zro2以質(zhì)量比1:1混合,然后通入h2,控制在150ml·min-1,反應(yīng)溫度控制為500℃,反應(yīng)時間為10h,氰基化石墨烯加氫后生成氨基化石墨烯。本實施例中氨基化石墨烯的氨基含量為15.9wt%。實施例4(1)氧化石墨烯的制備本發(fā)明中合成氧化石墨烯的方法為化學(xué)氧化法。本發(fā)明中氨基的來源為氧化石墨烯中的羧基,所以氧化石墨烯中的羧基含量直接影響氨基化石墨烯中氨基的摻雜量。因此,我們在合成氧化石墨烯的過程中,通過將濃硫酸改為濃硫酸與濃磷酸的混酸和延長氧化時間提高石墨的氧化程度,增加反應(yīng)活性位點。濃硫酸與濃磷酸的體積比為10:1,氧化時間為7h。(2)氨基化石墨烯的制備將氧化石墨烯在水溶液中分散均勻,濃度為1.5mol·l-1,然后加入質(zhì)量比為1:1的naoh和氯乙酸,氧化石墨烯與氯乙酸的質(zhì)量比為1:8,40℃下攪拌7h,離心過濾洗滌得到羧基化石墨烯。將得到的羧基化石墨烯在水溶液中分散均勻后,配制成濃度為1mg·ml-1的羧基化石墨烯溶液,用氨水調(diào)ph值為12,在室溫下攪拌10h,離心洗滌至洗液的ph值為7,得到酰胺基化石墨烯溶液,冷凍干燥得到酰氨基化石墨烯粉體;將酰氨基化石墨烯在n-甲基吡咯烷酮中分散均勻,濃度為1mg·ml-1;然后將三氯氧磷以質(zhì)量比1:10加入,100℃反應(yīng)15h后減壓蒸餾去除三氯氧磷,酰氨基化石墨烯脫水生成氰基化石墨烯。將氰基化石墨烯與催化劑ru-fe-b/zro2以質(zhì)量比1:10混合,然后通入h2,控制在300ml·min-1,反應(yīng)溫度控制為900℃,反應(yīng)時間為5h,氰基化石墨烯加氫后生成氨基化石墨烯。本實施例中氨基化石墨烯的氨基含量為21.4wt%。實施例5(1)氧化石墨烯的制備本發(fā)明中合成氧化石墨烯的方法為化學(xué)氧化法。本發(fā)明中氨基的來源為氧化石墨烯中的羧基,所以氧化石墨烯中的羧基含量直接影響氨基化石墨烯中氨基的摻雜量。因此,我們在合成氧化石墨烯的過程中,通過將濃硫酸改為濃硫酸與濃磷酸的混酸和延長氧化時間提高石墨的氧化程度,增加反應(yīng)活性位點。濃硫酸與濃磷酸的體積比為5:1,氧化時間為1h。(2)氨基化石墨烯的制備將氧化石墨烯在水溶液中分散均勻,濃度為1mol·l-1,然后加入質(zhì)量比為1:1的naoh和氯乙酸,氧化石墨烯與氯乙酸的質(zhì)量比為1:12,50℃下攪拌3h,離心過濾洗滌得到羧基化石墨烯。將得到的羧基化石墨烯在水溶液中分散均勻后,配制成濃度為1mg·ml-1的羧基化石墨烯溶液,用氨水調(diào)ph值為11,在室溫下攪拌11h,離心洗滌至洗液的ph值為7,得到酰胺基化石墨烯溶液,冷凍干燥得到酰氨基化石墨烯粉體;將酰氨基化石墨烯在n-甲基吡咯烷酮中分散均勻,濃度為2mg·ml-1;然后將三氯氧磷以質(zhì)量比1:4加入,90℃反應(yīng)12h后減壓蒸餾去除三氯氧磷,酰氨基化石墨烯脫水生成氰基化石墨烯。將氰基化石墨烯與催化劑ru-mn-b/zro2以質(zhì)量比1:5混合,然后通入h2,控制在250ml·min-1,反應(yīng)溫度控制為1000℃,反應(yīng)時間為8h,氰基化石墨烯加氫后生成氨基化石墨烯。本實施例中氨基化石墨烯的氨基含量為22.5wt%。實施例6(1)氧化石墨烯的制備本發(fā)明中合成氧化石墨烯的方法為化學(xué)氧化法。本發(fā)明中氨基的來源為氧化石墨烯中的羧基,所以氧化石墨烯中的羧基含量直接影響氨基化石墨烯中氨基的摻雜量。因此,我們在合成氧化石墨烯的過程中,通過將濃硫酸改為濃硫酸與濃磷酸的混酸和延長氧化時間提高石墨的氧化程度,增加反應(yīng)活性位點。濃硫酸與濃磷酸的體積比為2:1,氧化時間為10h。(2)氨基化石墨烯的制備將氧化石墨烯在水溶液中分散均勻,濃度為1.5mol·l-1,然后加入質(zhì)量比為1:1的naoh和氯乙酸,氧化石墨烯與氯乙酸的質(zhì)量比為1:10,35℃下攪拌10h,離心過濾洗滌得到羧基化石墨烯。將得到的羧基化石墨烯在水溶液中分散均勻后,配制成濃度為1mg·ml-1的羧基化石墨烯溶液,用氨水調(diào)ph值為10,在室溫下攪拌12h,離心洗滌至洗液的ph值為7,得到酰胺基化石墨烯溶液,冷凍干燥得到酰氨基化石墨烯粉體;將酰氨基化石墨烯在n-甲基吡咯烷酮中分散均勻,濃度為4mg·ml-1;然后將三氯氧磷以質(zhì)量比1:3加入,80℃反應(yīng)10h后減壓蒸餾去除三氯氧磷,酰氨基化石墨烯脫水生成氰基化石墨烯。將氰基化石墨烯與催化劑ru-nb-b/zro2以質(zhì)量比1:5混合,然后通入h2,控制在300ml·min-1,反應(yīng)溫度控制為800℃,反應(yīng)時間為9h,氰基化石墨烯加氫后生成氨基化石墨烯。本實施例中氨基化石墨烯的氨基含量為18.9wt%。實施例7(1)氧化石墨烯的制備本發(fā)明中合成氧化石墨烯的方法為化學(xué)氧化法。本發(fā)明中氨基的來源為氧化石墨烯中的羧基,所以氧化石墨烯中的羧基含量直接影響氨基化石墨烯中氨基的摻雜量。因此,我們在合成氧化石墨烯的過程中,通過將濃硫酸改為濃硫酸與濃磷酸的混酸和延長氧化時間提高石墨的氧化程度,增加反應(yīng)活性位點。濃硫酸與濃磷酸的體積比為4:1,氧化時間為8h。(2)氨基化石墨烯的制備將氧化石墨烯在水溶液中分散均勻,濃度為1.2mol·l-1,然后加入質(zhì)量比為1:1的naoh和氯乙酸,氧化石墨烯與氯乙酸的質(zhì)量比為1:7,20℃下攪拌9h,離心過濾洗滌得到羧基化石墨烯。將得到的羧基化石墨烯在水溶液中分散均勻后,配制成濃度為1mg·ml-1的羧基化石墨烯溶液,用氨水調(diào)ph值為12,在室溫下攪拌9h,離心洗滌至洗液的ph值為7,得到酰胺基化石墨烯溶液,冷凍干燥得到酰氨基化石墨烯粉體;將酰氨基化石墨烯在n-甲基吡咯烷酮中分散均勻,濃度為3mg·ml-1;然后將三氯氧磷以質(zhì)量比1:8加入,70℃反應(yīng)6h后減壓蒸餾去除三氯氧磷,酰氨基化石墨烯脫水生成氰基化石墨烯。將氰基化石墨烯與催化劑ru-cu-b/zro2以質(zhì)量比1:8混合,然后通入h2,控制在200ml·min-1,反應(yīng)溫度控制為800℃,反應(yīng)時間為6h,氰基化石墨烯加氫后生成氨基化石墨烯。本實施例中氨基化石墨烯的氨基含量為20.7wt%。實施例8(1)氧化石墨烯的制備本發(fā)明中合成氧化石墨烯的方法為化學(xué)氧化法。本發(fā)明中氨基的來源為氧化石墨烯中的羧基,所以氧化石墨烯中的羧基含量直接影響氨基化石墨烯中氨基的摻雜量。因此,我們在合成氧化石墨烯的過程中,通過將濃硫酸改為濃硫酸與濃磷酸的混酸和延長氧化時間提高石墨的氧化程度,增加反應(yīng)活性位點。濃硫酸與濃磷酸的體積比為10:1,氧化時間為5h。(2)氨基化石墨烯的制備將氧化石墨烯在水溶液中分散均勻,濃度為1.5mol·l-1,然后加入質(zhì)量比為1:1的naoh和氯乙酸,氧化石墨烯與氯乙酸的質(zhì)量比為1:15,25℃下攪拌7h,離心過濾洗滌得到羧基化石墨烯。將得到的羧基化石墨烯在水溶液中分散均勻后,配制成濃度為1mg·ml-1的羧基化石墨烯溶液,用氨水調(diào)ph值為12,在室溫下攪拌5h,離心洗滌至洗液的ph值為7,得到酰胺基化石墨烯溶液,冷凍干燥得到酰氨基化石墨烯粉體;將酰氨基化石墨烯在n-甲基吡咯烷酮中分散均勻,濃度為4mg·ml-1;然后將三氯氧磷以質(zhì)量比1:5加入,60℃反應(yīng)7h后減壓蒸餾去除三氯氧磷,酰氨基化石墨烯脫水生成氰基化石墨烯。將氰基化石墨烯與催化劑ru-co-b/zro2以質(zhì)量比1:5混合,然后通入h2,控制在200ml·min-1,反應(yīng)溫度控制為600℃,反應(yīng)時間為5h,氰基化石墨烯加氫后生成氨基化石墨烯。本實施例中制備的氨基化石墨烯的sem圖如圖1所示,ftir圖如圖2所示。本實施例中氨基化石墨烯的氨基含量為25.0wt%。實施例9-19步驟與實施例8相同,僅將催化劑ru-co-b/zro2中的co分別替換為sc、v、ni、y、zr、mo、tc、rh、pd、ag、cd,最終制備的氨基化石墨烯的氨基含量如下表:實施例910111213141516171819催化劑中mscvniyzrmotcrhpdagcd氨基含量wt%19.216.817.616.920.221.817.815.415.617.122.3當(dāng)前第1頁12