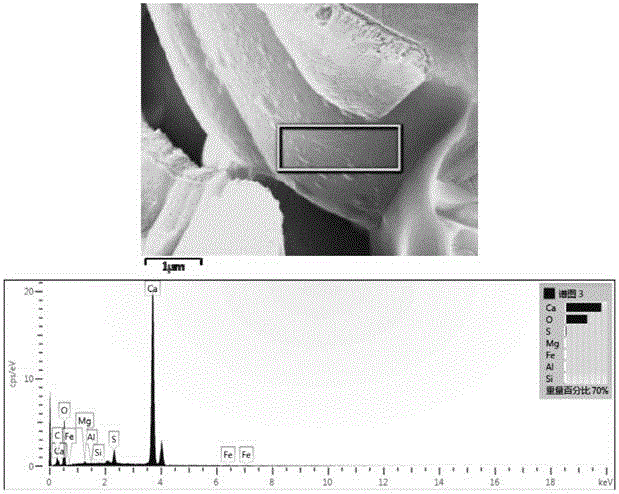
本發(fā)明涉及混凝土補償收縮添加劑領域,具體的是涉及一種水泥自應力膨脹熟料。特別地,本發(fā)明涉及一種主要成分為CaO和CaSO4的水泥自應力膨脹熟料以及該膨脹熟料的制作方法。
背景技術:
:膨脹劑指的是一種用于水泥的外加劑,在水泥凝結硬化時,膨脹劑體積膨脹,起補償收縮、張拉鋼筋產生預應力以及充分填充水泥間隙的作用。膨脹劑的主要類別包括:明礬石膨脹劑、硫鋁酸鈣膨脹劑、氧化鈣膨脹劑、鐵屑膨脹劑、氧化鎂膨脹劑、氧化鈣-硫鋁酸鈣復合膨脹劑等。鋼筋混凝土硬化時產生裂縫的原因較為復雜。通常認為,混凝土干縮和冷縮是產生裂縫的主要原因。因此,較為理想的是,在混凝土中摻入能達到補償其收縮的膨脹劑。膨脹劑加入到普通混凝土中,加水后生成大量膨脹結晶水化物-水化硫鋁酸鈣(即鈣釩石),使混凝土產生適度膨脹,在鋼筋鄰位的約束下,在結構中建立0.2~0.7MPa預壓應力,這一預壓應力可大致抵消混凝土在硬化過程中產生的收縮拉應力,同時,推遲了收縮的產生過程。當混凝土開始收縮時,其抗拉力已足以抵抗收縮應力,從而防止或減少混凝土收縮開裂。而且產生的鈣礬石使混凝土更加致密,從而大大提高了混凝土結構的抗裂防滲性能。目前,國內外一致采用膨脹劑配制的補償收縮混凝土來代替普通混凝土解決建筑物裂滲的問題?;炷僚蛎泟V泛應用于地下防水防滲工程、超長結構以及各類大型的混凝土施工工程,是防止混凝土收縮開裂的有效技術之一。國內現(xiàn)有的膨脹劑大多都是屬于以硫鋁酸鈣或氧化鈣復合硫鋁酸鈣為主要膨脹源的鈣釩石型膨脹劑。氧化鈣作為一種膨脹熟料最先是在日本發(fā)明并推廣應用的,硫鋁酸鈣主要是由中國建材研究總院研制出并最早在國內推廣并應用。后來隨著復合膨脹劑的出現(xiàn),選擇氧化鈣、硫鋁酸鈣、MgO等膨脹源,復合成單源、多源 膨脹劑。經過多年的市場應用發(fā)現(xiàn),相同化學組分的礦物不經過煅燒作為膨脹劑時活性很低,只有通過煅燒形成膨脹熟料,才能將膨脹劑的膨脹性能大幅提高。膨脹熟料顯然已成為膨脹劑的核心材料。然而此類熟料與水泥熟料的礦物組成十分接近,雖然可以通過調整熟料的礦物組成來改變對水的需求量,但還是需有必要的水發(fā)生水化反應,才能滿足對水泥建材的膨脹補償收縮效果。因此,膨脹熟料作為水泥建材添加劑的核心材料與水泥的匹配性顯得尤為重要。水泥建材收縮通常分為四個階段:塑性收縮、化學自收縮、溫度收縮和干燥收縮。作為以無機礦物組成的膨脹熟料,其膨脹能發(fā)揮太早會損失在水泥建材的塑性階段,而水泥建材在中后期的干燥收縮則會因缺水無法形成膨脹。所以,化學自收縮和溫度收縮兩個階段是造成水泥建材開裂及耐久的關鍵時期,也是膨脹材料可發(fā)揮作用的主要階段。MgO類型膨脹劑的膨脹主要發(fā)生在水泥建材收縮的中后期,不能滿足補償需求。目前市場上的一些膨脹劑的水化速度較快、膨脹期短、放熱集中,其有效膨脹會較大程度的損失在塑性收縮階段,并且在塑性階段大幅度提高溫度,會加快溫度提升和早期的水泥化學反應,在水泥建材強度還未足夠形成時就形成高膨脹,因此會影響建材的安定性。目前市場上廣泛應用的硫鋁型膨脹劑則由于膨脹率太低不能形成對混凝土有效地收縮補償。傳統(tǒng)的硫鋁酸鈣或氧化鈣復合硫鋁酸鈣膨脹劑存在一個更大的隱患是二次鈣礬石形成(secondanzsubstguentettringiteformation,SEF)帶來的危害。所謂二次鈣礬石形成,是指在膨脹劑產生膨脹作用之后,再次發(fā)生的鈣礬石形成。在二次鈣礬石形成以前,已經發(fā)生過一次鈣礬石形成過程,此次鈣礬石形成(可以稱為第一次鈣礬石形成)是硫鋁酸鈣類膨脹劑起作用的主要原因。對于第一次鈣礬石形成,由無水硫鋁酸鈣形成鈣礬石的化學反應為:C4A3S+8CaSO4+6CaO+96H2O→3C3A·3CaSO4·32H2O,其中C4A3S代表:無水硫鋁酸鈣(3Ca.3Al2O3.CaSO4);C3A代表鋁酸三鈣(3CaO.Al2O3)。在第一次鈣礬石形成過程中,只要保證充足的外部供水,無水硫酸鈣本身體積將膨脹為原來的9倍以上,從而達到補償混凝土收縮的效果。該第一次鈣礬石形成過程的膨脹會補償混凝土的收縮,顯然是有利的。而二次鈣礬 石形成指的是后期在砂漿和混凝土孔、裂縫、界面中由于存在含鋁的物質例如氧化鋁,所以會二次析出鈣礬石。該二次鈣礬石的形成會帶來鈣礬石延遲膨脹(DEF),該DEF現(xiàn)象出現(xiàn)在混凝土中的鈣礬石遇高溫或長期干燥分解脫水后,又遇到水,例如降水、管道漏水等,而形成第二次膨脹,這時的膨脹對混凝土是極其有害的,此時混凝土基本處于脆性狀態(tài),會經受不住DEF形成的膨脹壓力,由此導致水泥開裂,這也是最致命的開裂,將會導致混凝土全面劣化,因此需要避免形成二次鈣礬石。為此,本文減少或不引入形成二次鈣礬石的原料,例如鋁、氧化鋁,同時煅燒形成特定的核殼結構,由此減少鈣礬石的形成,避免混凝土遇水發(fā)生二次膨脹。技術實現(xiàn)要素:本發(fā)明所要提供的是一種膨脹劑熟料,該膨脹劑熟料膨脹能高,是膨脹的核心材料,能夠補償水泥建材的收縮,同時大幅度控制鈣礬石延遲膨脹(DEF)隱患。本發(fā)明的發(fā)明人深入研究后,發(fā)現(xiàn)通過提供CaO與含CaSO4的重量比為1:(0.15~0.67)的含CaO與含CaSO4的原料,煅燒后形成主要構成或基本構成為CaO和CaSO4的特定結構的膨脹劑熟料,能夠提供改善的膨脹效果,同時減少鈣礬石延遲膨脹(DEF)隱患。本發(fā)明提供一種水泥自應力膨脹熟料的制備方法,包括:a)按照CaO、CaSO4的重量比為1:(0.15~0.67),提供含CaO的原料和含CaSO4的原料,得到主要組成,優(yōu)選基本組成為含CaO和CaSO4的原料的原料混合物;b)將該原料混合物在約1250℃~1500℃煅燒例如20~60分鐘,形成以CaO為核、CaSO4為殼的核-殼結構膨脹熟料。具體地,物料在流動下被高溫熱源進行交互煅燒(其中,所述交互煅燒即為:物料流動方向與火焰噴射方向相反,也即頂火煅燒),形成CaSO4作為液相與CaO作為固相結合的核-殼結構。在本發(fā)明一個優(yōu)選的實施方式中,步驟a)中CaO與CaSO4的重量比為1:(0.45~0.55);在本發(fā)明另一個優(yōu)選的實施方式中,步驟a)中CaO與CaSO4的重量比為1:(0.45~0.50),其中最優(yōu)選的重量比為1:0.46-1:0.48。作為提供含CaO的原料可以為,但不限于:含有CaCO3的天然礦物、 含有CaCO3的工業(yè)廢棄物或循環(huán)利用物,例如石灰石、霰石、方解石、白堊、石灰?guī)r、大理石、石灰華等;或者含有Ca(OH)2的天然礦物、工業(yè)循環(huán)利用物,例如熟石灰、消石灰、電石渣等。該含有CaCO3的天然礦物、工業(yè)循環(huán)利用物中CaO含量大于40%重量,優(yōu)選大于55%重量;含有Ca(OH)2的天然礦物、工業(yè)循環(huán)利用物,其CaO含量大于55%重量,優(yōu)選大于70%重量。作為提供含CaSO4的原料可以為,但不限于:含有無結晶水的CaSO4礦物、含有CaSO4的工業(yè)循環(huán)利用物,例如天然硬石膏、二水石膏、半水石膏、脫硫石膏、磷石膏等;或者含結晶水的CaSO4的礦物、工業(yè)循環(huán)利用物。所述含有無結晶水CaSO4礦物、工業(yè)循環(huán)利用物,其CaSO4含量大于60%重量,優(yōu)選大于80%重量;含結晶水的CaSO4的礦物、工業(yè)循環(huán)利用物中的CaSO4含量優(yōu)選大于50%重量,更優(yōu)選大于70%重量的物質。煅燒溫度可以在約1250℃~1500℃的范圍內進行選擇。溫度的選擇應該使得在該煅燒溫度下,CaO為固態(tài),而CaSO4至少部分處于熔融狀態(tài),從而能夠在煅燒后獲得CaSO4與CaO結合的核-殼結構產品。優(yōu)選的,步驟b)中的高溫煅燒溫度為1400~1450℃。更加優(yōu)選的,步驟b)中的高溫煅燒溫度為約1450℃。在上述煅燒溫度范圍內,步驟b)中核-殼結構形成過程中,CaSO4為至少部分為熔融的液態(tài),CaO基本保持為固態(tài),從而使得至少部分處于熔融狀態(tài)的CaSO4包覆在CaO表面,形成CaO內核-CaSO4外殼的核-殼結構膨脹熟料顆粒。優(yōu)選的,步驟b)之后還包括冷卻的步驟c),所述冷卻步驟例如可以采用篦冷機冷卻,即將煅燒后的膨脹劑熟料在出窯30~60分鐘后,冷卻至50~100℃。對煅燒的時間可以不作特別的限定,只要保證CaSO4包裹在CaO表面,形成核-殼結構膨脹劑顆粒即可。優(yōu)選的,步驟b)中煅燒時間為30~60分鐘。優(yōu)選地,步驟b)或步驟c)之后還包括粉磨步驟d),粉磨至所述熟料比表面積大于180m2/kg,一般在200m2/kg至500m2/kg,或者是在250m2/kg至450m2/kg,或者是在300m2/kg至400m2/kg。粉磨可以使得本文的膨脹熟料能夠根據需要,具有更好的膨脹性能。所述粉磨可以采用球磨、立磨或輥磨等方式。在煅燒過程中,由于進行交互煅燒,物料一直處于相互運動狀態(tài),所以所形成的膨脹熟料具有多層核-殼結構,研磨后的顆粒仍為具有核-殼結 構的膨脹熟料顆粒。本發(fā)明還提供一種水泥自應力膨脹熟料,該水泥自應力膨脹熟料為核-殼結構,上述核-殼結構水泥自應力膨脹熟料可以采用上述水泥自應力膨脹熟料的制備方法來制備。優(yōu)選,煅燒后上述熟料顆粒的直徑為300μm以下,一般為200μm以下,更一般是2-100μm,特別地是2-20μm,使用時避免混凝土開裂。該熟料顆粒為晶體顆粒,所述晶體顆粒主要由CaO內核和CaSO4外殼組成,外殼厚度為0.1-5μm,優(yōu)選0.1-3μm,更優(yōu)選為0.05-2μm。主要由CaO內核和CaSO4外殼形成的膨脹劑熟料分別以CaO、SO3為基礎計算,其化學組成為CaO≥70wt%,優(yōu)選≥80wt%,更優(yōu)選≥85%、還更優(yōu)選≥90%;SO3≥7wt%,優(yōu)選大于≥10wt%,更優(yōu)選≥15%,其余為原料帶入的不可避免的雜質,膨脹劑熟料的總量為100%重量。雜質包括,但不限于:Al2O3、Fe2O3和/或MgO等,該雜質中Al2O3≤1%重量,優(yōu)選≤0.08%重量,更優(yōu)選≤0.05%重量,還更優(yōu)選≤0.02%重量;Fe2O3≤0.5%重量,優(yōu)選≤0.3%重量,更優(yōu)選≤0.2%重量;MgO≤5.0%重量。采用本發(fā)明的技術方案,相對于本領域已有的硫鋁酸鈣類膨脹劑具有明顯的技術優(yōu)勢。本發(fā)明具體實施方式部分的數(shù)據將表明,本發(fā)明的水泥自應力膨脹熟料具有較高的膨脹性能,且其膨脹性能與水泥建材相匹配,減少了材料的有效膨脹損失,相同的膨脹率摻量更低。根據本發(fā)明提供的水泥自應力膨脹熟料制備方法,在熟料燒結原料中無需添加常用的礦化劑,例如含F(xiàn)e、Mg等的礦化劑,進一步減小了熟料中其它物質對水泥建材的影響,穩(wěn)定發(fā)揮膨脹能,在鋼筋約束條件下能使水泥建材產生1~3MPa的自應力,逐步產生膨脹壓力抵抗水泥建材自身收縮,從而抑制砂漿、混凝土開裂,提高水泥建材的耐久性。更加驚奇的是,本發(fā)明的水泥自應力膨脹熟料有效地解決了鈣礬石延遲膨脹(DEF)帶來的棘手問題。如前所述,無水硫鋁酸鈣形成鈣礬石的化學反應是硫鋁酸鈣類膨脹劑起作用的主要因素,因而本領域已有的硫鋁酸鈣類膨脹劑/膨脹熟料都需要添加含鋁的原料,以在最終產品中生成無水硫鋁酸鈣。也就是說,本領域在本發(fā)明提出之前,已經形成了一種技術上的共識,硫鋁酸鈣類膨脹劑/膨脹熟料沒有足夠量的鋁的添加不可能取得良好的膨脹效果。然而,不局限于理論,發(fā)明人發(fā)現(xiàn)鋁的引入造成了后期延遲膨脹(DEF)的危害,DEF的發(fā)生需要同時滿足三個條件:1)漿體 或混凝土中需要額外添加鋁源,存在一定量的硫和鋁,通常為1%重量以上;2)漿體或混凝土中存在鈣礬石析出的空間;3)漿體或混凝土中能夠得到充足的水供應。其中第2)項和第3)項條件在很多應用場合都是無法避免的。根據傳統(tǒng)觀點,硫和鋁都是硫鋁酸鈣類膨脹劑/膨脹熟料所必須的組分,缺一不可。但是,本發(fā)明的發(fā)明人意外地發(fā)現(xiàn),事實并不是如現(xiàn)有技術所認知的那樣,不添加額外的鋁源,僅用CaO和CaSO4,煅燒后得到的核-殼結構水泥自應力膨脹熟料,能夠獲得良好的膨脹效果,同時由于最終產品中缺乏足夠量的鋁,成功地避免了長期以來困擾技術人員的DEF危害。附圖說明圖1:傳統(tǒng)的CSA熟料結構的顯微圖圖2:純氧化鈣膨脹熟料煅燒后的結構顯微圖圖3:根據本發(fā)明的一個實施方式氧化鈣與硫酸鈣按照1:0.5重量比,在約1450℃下煅燒得到的核-殼結構硫鈣膨脹熟料結構顯微圖圖4:根據本發(fā)明的一個實施方式制備的核-殼結構硫鈣膨脹熟料表面形貌圖及表面附近材料的元素分析圖圖5:根據本發(fā)明的一個實施方式制備的核-殼結構硫鈣膨脹熟料不完整包覆表面形貌圖及該部位的元素分析圖具體實施方式為使本發(fā)明的目的、技術方案和優(yōu)點更加清楚,下面將結合本發(fā)明附圖、實施例,對本發(fā)明的技術方案進行進一步描述。顯然,所描述的實施例是本發(fā)明的一部分實施例,而不是全部的實施例。基于所描述的本發(fā)明的實施例,本領域普通技術人員在無需創(chuàng)造性勞動的前提下所獲得的所有其他技術方案,都屬于本發(fā)明保護的范圍。除非特別聲明,本文中的比例一般指重量比。實施例1CaO、CaSO4混合比例的確定以CaO為主要膨脹成分、CaSO4為液相成分,按照CaO、CaSO4的不同重量比例,準備提供CaO、CaSO4的原料,并充分混合上述原料,得到混合物;將上述混合物在約1450℃高溫煅燒40分鐘,形成CaSO4包覆CaO的核-殼結構硫鈣膨脹熟料。保持其它條件不變的情況下,改變CaO、CaSO4之 間的重量比例,測試獲得熟料在水中/空氣中的限制膨脹率(體積),得到如下表的結果:表1實施例2煅燒溫度的確定按照CaO、CaSO4為1:0.50的重量比,準備提供CaO、CaSO4的原料。充分混合上述原料后,得到混合物;將上述混合物在不同的溫度高溫煅燒約60分鐘,形成CaSO4包覆CaO的核-殼結構硫鈣膨脹熟料。保持其它條件不變的情況下,改變煅燒溫度,測試獲得熟料在水中/空氣中的限制膨脹率(體積),得到如下表的結果:表2實施例3產品形貌的表征用與實施例1和2相同的方法,區(qū)別在于按照CaO、CaSO4為1:0.50的重量比例,在約1450℃下煅燒,得到CaSO4包覆CaO的核-殼結構硫鈣膨脹熟料。采用掃描電鏡(日本電子:JSM6510LV)獲得的膨脹熟料的顯微結構,如圖3所示。作為對比,圖1和圖2同時分別給出了傳統(tǒng)CSA熟料和煅燒CaO的顯微結構。由圖1-3可見,傳統(tǒng)CSA熟料呈現(xiàn)出明顯的六方棱柱結構,這是硫鋁酸鈣的典型結構,純氧化鈣煅燒后則為較光滑的橢球型,本發(fā)明的CaSO4包覆CaO的核-殼結構硫鈣膨脹熟料外貌與前兩者都有較大區(qū)別,首先其不具有六方棱柱結構,表明其中不存在硫鋁酸鈣;其次顆粒之間粘連較明顯,不像純氧化鈣煅燒后形成明顯分離的顆粒,這是由于熔融狀態(tài)的硫酸鈣將顆粒之間的空隙進行了填充。EDS微觀分析表明核-殼結構硫鈣膨脹熟料中,具有膨脹劑顆粒,顆粒粒徑在2-20μm之間,硫酸鈣的包覆厚度在0.35μm左右。實施例4核-殼結構用與實施例1和2類似的方法,按照CaO、CaSO4為1:0.25的重量比,在月1450℃下煅燒,得到CaSO4包覆CaO的核-殼結構硫鈣膨脹熟料。將得到的核-殼結構硫鈣膨脹熟料分別對包覆完整的材料表面部分和不完整包覆的材料部位進行了元素分析表征,場發(fā)射掃描電鏡(日本電子:JSM7100F)照片及元素分析圖譜見圖4-5。對包覆完整的材料表面部分的元素分析結果見下表:表3元素線類型表觀濃度k比值wt%wt%SigmaOK線系15.220.0512144.810.44MgK線系0.230.001510.370.07AlK線系0.050.000330.070.05SiK線系0.270.002160.360.06SK線系4.240.036575.130.11CaK線系40.280.3599348.840.41FeK線系0.270.002720.420.15總量100.00對CaO內核具有不完整包覆的材料表面部位進行元素分析,結果見下表:表4元素線類型表觀濃度k比值wt%wt%SigmaOK線系10.200.0343236.870.61MgK線系0.210.001400.350.08AlK線系0.030.000220.050.06SiK線系0.020.000150.030.06SK線系1.880.016172.320.10CaK線系48.790.4359060.290.60FeK線系0.060.000570.090.19總量100.00將上面兩個表的結果進行對比分析可知,從包覆完整的材料表面到不完整包覆的材料部位,Ca從48.84%提高到60.29%,O從44.81%降至36.87%,而S從5.13%降至2.32%,由此可以確認,氧化鈣內核表面包裹了硫酸鈣層,本發(fā)明的熟料為CaSO4包覆CaO的核-殼結構。實施例5與現(xiàn)有技術膨脹劑的比較下表將本發(fā)明的CaSO4包裹CaO的核-殼結構硫鈣膨脹熟料(簡稱為CCS)的鈣硫鋁比例、限制膨脹率等與現(xiàn)有技術已有的水泥膨脹劑進行了對比:表5如上表所示,現(xiàn)有技術已有的硫鋁酸鈣型膨脹劑,原料中都需要加入較大量的鋁,如前所述,大量鋁的存在可能導致后期的二次鈣礬石形成,從而造成延遲膨脹,導致存在混凝土開裂的風險。相反,本發(fā)明的CaSO4包裹CaO的核-殼結構硫鈣膨脹熟料不加入鋁源,極大地降低了二次鈣礬石形成帶來的隱患。從膨脹率來看,本發(fā)明的CaSO4包覆CaO的核-殼結構硫鈣膨脹熟料7天時水中限制膨脹率為0.141%-0.173%,空氣中21天的限制膨脹率為0.05%-0.10%,都接近HCSA(高性能混凝土膨脹劑)的數(shù)據,大大優(yōu)于UEA(UnitedExpansingAgent,簡寫UEA,它是以硫酸鋁、氧化鋁、硫酸鋁鉀等為主要多種膨脹源)和CSA(硫鋁酸鈣類膨脹劑)。因此,本發(fā)明的CaSO4包覆CaO的核-殼結構硫鈣膨脹熟料不需要加入鋁源,不但省略了原材料、降低了成本、簡化了工藝流程,而且還能達到與現(xiàn)有技術中最好的膨脹劑相仿的膨脹效果。當前第1頁1 2 3