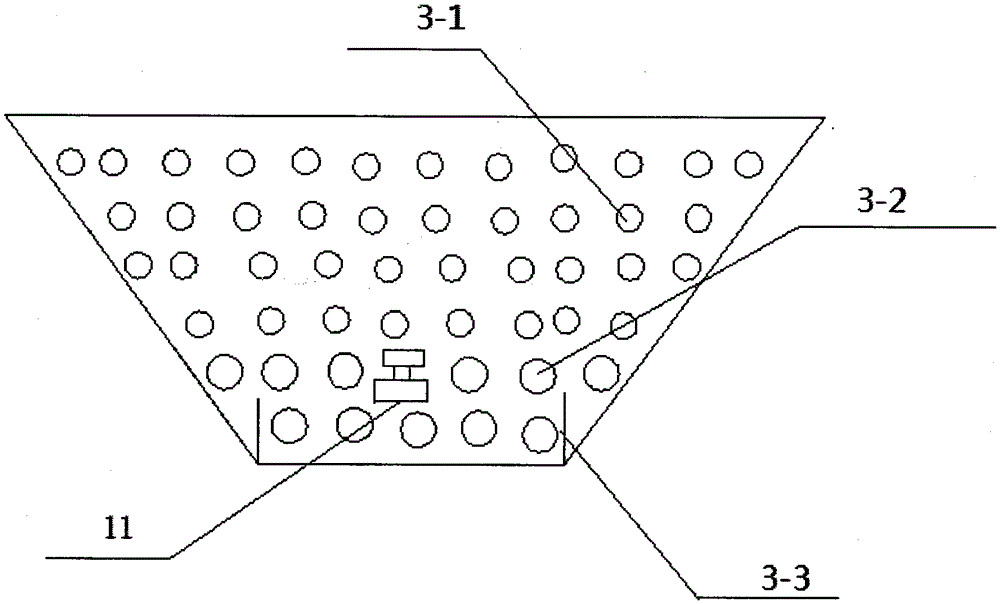
本發(fā)明屬于四氯化鈦制備技術領域,具體涉及制備四氯化鈦的裝置及方法。
背景技術:四氯化鈦是制造鈦白(二氧化鈦)、金屬鈦的一個重要中間體。鈦白被認為是目前世界上性能最好的一種白色顏料,廣泛應用于涂料、塑料、造紙、印刷油墨、化纖、橡膠、化妝品等工業(yè)。中國目前已經(jīng)是繼美國后第二大的鈦白粉消耗國,而且增長勢頭迅猛,潛力也非常大。目前鈦的用途發(fā)展也很快,已被廣泛應用于飛機、火箭、人造衛(wèi)星、宇宙飛船、艦艇、輕工、化工、紡織、醫(yī)療以及石油化工等領域。中國是鈦資源大國,我國的鈦資源主要集中在攀枝花地區(qū),其二氧化鈦(TiO2)的儲量達8.7億噸左右,占國內鈦儲量的90%以上?,F(xiàn)有四氯化鈦的制備是通過精鈦礦或富鈦料與氯氣在高溫下反應獲得,其生產(chǎn)工藝主要有兩種:(1)熔鹽氯化法,是將含鈦原料和焦炭混合物置入由KCl,NaCl,MgCl2熔鹽中,通入氯氣進行反應,該工藝的缺點是設備產(chǎn)能低、反應體積大,特別是廢液廢渣多,對環(huán)境污染大,已不滿足現(xiàn)代制造業(yè)的要求,正逐步被淘汰。(2)沸騰氯化法,沸騰氯化是將含鈦原料制備成一定分布的顆粒,并隨焦炭顆粒一起放入反應器中,通人氯氣使顆粒懸浮起來進行反應,該方法反應器效率高,沒有廢液產(chǎn)生,廢渣也很少,對環(huán)境的影響也較小,因而沸騰氯化是目前制備四氯化鈦的主要方法。該工藝的缺點是對原料品質要求很高,特別是鈣鎂氧化物含量要小于1%,這是由于沸騰氯化反應溫度通常在800~1000℃之間,當鈦渣中含有較多的鈣鎂氧化物時,將產(chǎn)生大量的氯化鈣、氯化鎂,而氯化鈣的熔點為714℃,氯化鎂的熔點為772℃,在800-1000℃的氯化反應器內氯化鈣和氯化鎂都呈液態(tài),粘結周圍的顆粒形成較大的聚團,破壞沸騰床的穩(wěn)定操作。但攀枝花鈦礦的品位較低,鈣鎂氧化物含量高,以攀枝花鈦精礦冶煉的高鈦渣CaO、MgO含量在7~11%,現(xiàn)有的沸騰氯化工藝還不能將低品位(鈣鎂含量高)的鈦原料直接用作沸騰氯化的原料。如何充分利用攀枝花地區(qū)的低品位鈦礦制備四氯化鈦,是急待解決的難題?,F(xiàn)有用低品位高鈦渣制備四氯化鈦的裝置及方法,如2003年11月12日公開的,公開號為CN1454849A的“用于含鈦礦物氯化制備四氯化鈦的裝置和方法”專利,公開是一種多級快速流化床和湍動流化床串聯(lián)的方式處理低品位高鈦渣工藝,即以含鈦礦物和石油焦為固體原料、以氯氣和氧氣為氣體原料,采用多級(3-10級)快速反應流化床和湍流流化床作為反應器,先進行高溫氯化反應,后經(jīng)冷卻,再進行一次固氣分離而制得成品。該專利主要有以下缺點:1)反應器結構復雜,需要的反應器數(shù)量較多,而且兩類反應器之間結構差異較大,設 備投資大,生產(chǎn)成本高。2)為了避免密度很小的焦炭顆粒被氣體攜帶出反應器,須采用顆粒直徑很大的焦炭顆粒,或者采用較小的操作氣速,這兩種情況都會降低反應的速率,影響反應器的效率,生產(chǎn)效率不高。3)湍動流化床與快速流化床的直徑相差較大,進出口之間有較大的傾角,固體顆粒,特別是對于由于表面有氯化鎂、氯化鈣而粘性較大的高鈦渣顆粒,容易在進出口粘結,造成系統(tǒng)操作的而不正常,影響產(chǎn)品的產(chǎn)量和質量;又如專利號為ZL200910103049.9的“一種半循環(huán)流化制備四氯化鈦的方法”,公開的方法是以低品位的高鈦渣和焦炭為固體原料,以氯氣和氮氣為氣體原料,采用循環(huán)流化床裝置,經(jīng)過高溫氯化反應,冷卻及氣固分離而將四氯化鈦產(chǎn)品。該方法的主要缺點是:1)循環(huán)流化床裝置較為復雜,所包含的流化床反應器包含了加熱段,高溫反應段以及頂部的冷卻分離段,結構復雜,操作不方便,設備投資大;2)為了促使聚團破碎,需要較高的氣速,為提高單程轉化率低需要很高的反應器;3)由于反應器在不同高度存在升溫和降溫,能量效率低。
技術實現(xiàn)要素:本發(fā)明的目的是:針對現(xiàn)有用低品位高鈦渣制備四氯化鈦的裝置及方法的不足,提供一種振動式內循環(huán)流化制備四氯化鈦的裝置及方法,本發(fā)明裝置具有結構緊湊,熱量利用高,生產(chǎn)效率高,產(chǎn)品質量好,操作方便且能有效處理鈣鎂含量高,粘性大的低品位鈦渣等特點,本發(fā)明方法是將物料加熱和高溫氯化反應耦合在一起,采用外循環(huán)流化床加熱,內流化床反應器反應的方法,具有反應溫度分布均勻,控制方便,鈦轉化率高等特點。本發(fā)明的機理:本發(fā)明采用振動式內循環(huán)流化氯化制備四氯化鈦的方法,反應物氯氣和鈦渣顆粒以及焦炭顆粒在流化床內部進行流化氯化反應,由于該反應屬于縮核反應:隨著反應的進行,氣固混合物在上行過程中,固體反應物顆粒的粒徑逐漸減小。反應物從內流化床反應器頂部出口流出進入自由空域,由于自由空域直徑增大,氣體的表觀速度減小,攜帶的細顆粒被拋撒在振動分布板上,在振動器的振動下細顆粒穿過振動分布板上的細孔進入外循環(huán)流化床,與新加入的焦炭顆粒一起下流,從內流化床反應器壁上的回料口進入內流化床反應器,從而形成內循環(huán)流化氯化過程。從自由空域頂部出料管流出的氣體將攜帶極細小的粉塵通過直管進入高效旋風分離器,粉塵從旋風分離器下部固體顆粒出料口排出。設備底部設置有氧氣和氮氣混合氣體進料管,輸入的氧氣和焦炭顆粒進行燒炭反應,放出大量的熱量,可以為整個反應系統(tǒng)提供充分的熱量,輸入的氮氣維持外循環(huán)床內顆粒處于初始流化狀態(tài),便于顆粒向下流動。在內流化床反應器底部有氯氣進料管,攜帶鈦渣顆粒進入內流化床反應器,進行高溫氯化反應,制得四氯化鈦產(chǎn)品。實現(xiàn)本發(fā)明目的的技術方案是:一種振動式內循環(huán)流化制備四氯化鈦的裝置,主要包括外循環(huán)流化床、內流化床反應器、振動分布板和振動器、旋風分離器、氣體緩沖罐和氣體分 布板等。其特征是:所述外循環(huán)流化床、內流化床反應器、振動分布板、氣體緩沖罐、擋板、出料管、直管、進料管的材料均為不銹鋼材質或鈦合金材質。所述外循環(huán)流化床的形狀為頂端封閉的圓柱形殼體,所述圓柱形殼體的內徑為500~3000mm、長度為1000~5000mm、厚度為3~8mm。在所述圓柱形殼體內的上部高度為400~3000mm的空間為自由空域,設置自由空域用以焦炭固體原料的進料及從所述內流化床反應器流出的固體顆粒的沉降。在所述自由空域的圓周壁上,對稱地設置兩個孔徑為50~150mm的通孔(即焦炭固體原料入口),在所述焦炭固體原料入口外分別焊接一根長度為500~1500mm、與所述外循環(huán)流化床的殼體的夾角呈30°~70°、內徑與所述焦炭固體原料入口相匹配的焦炭顆粒進料管,以便焦炭固體原料能順利地輸入所述的外循環(huán)流化床內,并通過所述的振動分布板進入所述的內循環(huán)流化床反應器內。在所述圓柱形殼體的頂端面的圓心處(即位于所述自由空域的頂端圓心處)設置一孔徑為50~200mm的通孔(即出料口),在所述的出料口處焊接一根長度為1500~2000mm、內徑與所述出料口相匹配的出料管,并在所述出料管的另一端焊接一根長度為1000~5000mm、外徑為50~200mm、與所述出料管相垂直的直管,所述直管的另一端與所述旋風分離器的入口固接連通,以便所述外循環(huán)流化床輸出的經(jīng)過氯化反應后的混合氣體順利輸入所述的旋風分離器進行氣固分離。所述外循環(huán)流化床底端通過法蘭固接氣體分布板1,所述的氣體分布板1為厚度為1~10mm、外徑與所述的外循環(huán)流化床殼體的內徑相匹配、內徑與所述內循環(huán)流化床反應器殼體的內徑相匹配的圓環(huán)形陶瓷板,在所述的氣體分布板1上均勻設置開孔率為1%~10%、孔徑為0.5~2.5mm的通孔,以便所述的氮氣和氧氣的混合氣體均勻地輸入所述的外循環(huán)流化床的殼體內,所述氣體分布板1用于氧氣和氮氣混合氣體均勻分布。在所述外循環(huán)流化床的圓柱形殼體內的自由空域的下端處,焊接一振動分布板,以便焦炭固體顆粒通過所述振動分布板進入所述的外循環(huán)流化床內和所述的內流化床反應器內。所述內流化床反應器的形狀為兩端開口的圓柱形殼體,所述內流化床反應器殼體的頂端焊接在所述的振動分布板下部的外表面上。所述圓柱形殼體內徑為250~2500mm、長度為800~2000mm、厚度為3~8mm。在所述圓柱形殼體的下部的圓周壁上還均勻設置2~8個、孔徑為10~50mm的通孔(即顆?;亓峡?,以便經(jīng)所述振動分布板的焦炭固體原料順利進入所述的內流化床反應器內進行氯化反應。在所述圓柱形內流化床反應器殼體下部一側的壁上設置一孔徑為50~150mm的通孔(即鈦渣固體原料入口),在所述的通孔處焊接一根長度為200~800mm、與所述圓柱形內流化床反應器殼體的夾角呈30°~70°、內徑與所述鈦渣固體原料入口相匹配的鈦渣顆粒進料管,以便鈦渣固體原料順利進入所述的內循環(huán)流化床反應器內。 所述圓柱形內流化床反應器殼體底端通過法蘭固接氣體分布板2,所述的氣體分布板2為厚度為1~10mm、外徑與所述內流化床反應器殼體的內徑相匹配的圓盤形陶瓷板,在所述的氣體分布板2上均勻設置開孔率為1%~10%、孔徑為0.5~2.5mm的通孔,以便所述的氯氣氣體原料均勻地輸入所述圓柱形內流化床反應器殼體內。所述的振動分布板的形狀為兩端敞開的截錐形殼體,所述截錐形殼體的上頂面的內徑與所述外循環(huán)流化床殼體的內徑相匹配、下底面的內徑為100~1000mm、高度為300~1200mm、厚度為100~400mm。所述截錐形殼體分為上部和下部,在所述截錐形殼體的上部(即占整個振動分布板長度的2/3)均勻設置孔徑為0.5~2mm、孔間距為2~6mm的小孔(即振動分布板上部小孔),以便較小的焦炭固體顆粒經(jīng)過所述小孔進入所述外循環(huán)流化床中進行物料循環(huán);在所述截錐形殼體下部(即占整個振動分布板長度的1/3)均勻設置孔徑為1~3mm、孔間距為3~10mm的大孔(即振動分布板下部大孔),以便較大的焦炭固體顆粒經(jīng)過所述大孔進入所述內流化床反應器內進行氯化反應。在所述截錐形殼體內的底端面上設置一兩端面均敞開的圓柱形殼體的擋板,所述擋板的高度為20~50mm、厚度為5~8mm、內徑與所述截錐形殼體的底面內徑相匹配,用以阻擋所述振動分布板中下滑的焦炭固體顆粒,防止過多焦炭固體顆粒直接進入所述內流化床反應器內。在所述的振動分布板內放置一振動器,所述振動器為市購的、振動壓力為0.1~0.35MPa的倉壁式振動器,通過調整振動頻率和功率,賦予所述振動分布板上顆粒更高的能量,促使焦炭固體顆粒通過所述振動分布板的細孔進入所述外循環(huán)流化床內和所述內流化床反應器中。所述的氣體緩沖罐為厚度為3~10mm的、一小一大的兩個開口頂面和封閉底面的截錐形殼體。兩個所述的截錐形殼體組裝成一個同軸心的容器,所述的小的截錐形殼體(即氣體緩沖罐2)的長度為200~1500mm、開口頂面的內徑與所述內流化床反應器殼體的內徑相匹配、封閉底面的內徑為150~1200mm,所述的氣體緩沖罐2與所述的圓盤形氣體分布板2通過法蘭固接所述內流化床反應器底端,在所述的氣體緩沖罐2的封閉底面的軸心處,設置一孔徑為50~120mm的通孔(即氯氣原料進料口),在所述通孔處焊接一管徑與所述的氯氣原料進料口相匹配、總長度為400~2100mm的直角形氣體進料管2,以便順利地將氯氣氣體原料輸入所述的氣體緩沖罐2內,保證氯氣氣體原料持續(xù)穩(wěn)定地輸入所述的內流化床反應器內,所述氣體緩沖罐2用于氯氣氣體的緩沖。所述的大的截錐形殼體(即氣體緩沖罐1)的長度為500~2000mm、頂面開口的內徑與所述外循環(huán)流化床殼體的內徑相匹配、封面底面的內徑為300~2000mm,所述氣體緩沖罐1與所述的圓環(huán)形氣體分布板1通過法蘭固接所述外循環(huán)流化床底端,并在所述的氣體緩沖罐1的截錐形殼體的外壁上的同一高度均勻焊接4~6個鞍型支架或支撐式支架或掩護式支架固定在地面上。在所述氣體緩沖罐1的封閉底面的軸心處,設 置一孔徑為50~150mm的通孔(即氯氣和氮氣的混合氣體的進料口),在所述混合氣體進料口處焊接一根長度為100~500mm、管徑與所述混合氣體進料口相匹配的氣體進料管1,以便將所述的混合氣體持續(xù)穩(wěn)定地輸入所述的氣體緩沖罐1內,所述氣體緩沖罐1用于氧氣和氮氣混合氣體的緩沖;并在所述氣體緩沖罐1的側壁上并對應于所述氣體進料管2的出口處,設置一孔徑與所述進料管2的外徑相匹配的通孔,以便所述的氣體進料管2伸出所述的氣體緩沖罐1外,保證讓氯氣氣體原料順利輸入到所述的氣體緩沖罐2內。所述的旋風分離器為市售的常規(guī)產(chǎn)品,從所述的外循環(huán)流化床的自由空域頂部流出的攜帶極細小的粉塵的氣體通過所述的直管進入所述的旋風分離器,進行氣固分離,收集從所述旋風分離器下部的固體顆粒出料口排出的粉塵,經(jīng)分離后再循環(huán)利用,收集從所述旋風分離器上部的氣體出口排出的氣體,經(jīng)冷卻后得到四氯化鈦產(chǎn)品,并收集濾出的剩余氣體,經(jīng)處理后可再利用,以免污染大氣。一種振動式內循環(huán)流化制備四氯化鈦的方法,以低品位的鈣鎂含量高的高鈦渣和焦炭為固體原料,以氧氣,氮氣及氯氣為氣體原料,利用本發(fā)明裝置,經(jīng)過氯化反應和冷卻及氣固分離而制得成品。所述的具體步驟如下:(1)原料處理以低品位的鈣鎂含量高的高鈦渣(簡稱高鈦渣)和焦炭為固體原料,以氧氣和氮氣及氯氣為氣體原料,先對所述的固體原料分別通過0.7~21目的分離篩進行分篩,并按高鈦渣顆粒的平均粒徑∶焦炭顆粒的平均粒徑之比1∶0.8~1.2,和按高鈦渣顆粒的質量∶焦炭顆粒的質量比為1∶0.3~3的比例備料,然后分別對高鈦渣顆粒和焦炭顆粒進行加熱,加熱至固體顆粒溫度為400~600℃,備用。對所述氣體原料中的氯氣進行加熱至300~500℃,備用;對氧氣和氮氣先按氧氣∶氮氣的體積比為1∶0.1~0.5的比例進行混合,再對混合氣體進行加熱至100~300℃,備用。(2)氯化反應第(1)步完成后,將第(1)步處理后的原料,分別輸入到本發(fā)明的裝置中,即焦炭顆粒以1.8~540kg/h的速度從所述裝置的焦炭顆粒進料管輸入,通過所述裝置振動分布板進入所述裝置的外循環(huán)流化床內和內流化床反應器中;高鈦渣顆粒以36~180kg/h的速度從所述裝置的鈦渣顆粒進料管輸入到所述的內流化床反應器中;氯氣以0.5~3.5m/s的速度從所述裝置的氣體緩沖罐2底面的氣體進料管2輸入到所述的內流化床反應器中,氧氣和氮氣的混合氣體以0.2~1.5m/s的速度從所述裝置的氣體緩沖罐1底面的氣體進料管1輸入到所述的外循環(huán)流化床中。使所述的焦炭顆粒在所述外循環(huán)流化床下行中與所述的氧氣和氮氣混合氣體逆流接觸反應,利用反應放出的熱量加熱焦炭顆粒,使焦炭顆粒達到1000~1300℃,所得到的高溫 焦炭顆粒從所述內流化床反應器壁上的顆粒回料口進入所述的內流化床反應器內,用以保持所述內流化床反應器內部溫度為800~1100℃;從所述的氣體進料管2輸入的氯氣和從所述鈦渣顆粒進料管進入的鈦渣顆粒在所述的內流化床反應器內進行高溫氯化反應;隨反應的進行,氣固混合物在上行過程中,固體反應物顆粒粒徑逐漸減小,進入所述外循環(huán)流化床內上部的自由空域,氣體表觀速度減小,攜帶的細顆粒被拋灑在所述振動分布板上,在所述振動器振動下較小顆粒穿過所述振動分布板上部小孔進入所述外循環(huán)流化床內,與新進料的焦炭顆粒一起下流,經(jīng)過所述的顆?;亓峡谶M入所述內流化床反應器內,從而形成內循環(huán)流化氯化過程;所述氯化反應后產(chǎn)生的并攜帶有少量粉塵的氣體通過所述的外循環(huán)流化床上部的自由空域和出料管及直管輸入所述裝置的旋風分離器中。所述的裝置在運行中的壓力為0.1~0.35MPa。(3)氣固分離第(2)步完成后,在所述裝置的旋風分離器中,對第(2)步氯化反應產(chǎn)生的帶有少量粉塵的氣體,進行氣固分離,收集在所述旋風分離器上部的氣體出口濾出的氣體,自然冷卻后得到四氯化鈦產(chǎn)品,并收集濾出的剩余氣體,經(jīng)處理后可再利用以免污染大氣;收集從所述旋風分離器下部的固體顆粒出料口濾出的粉塵,經(jīng)分離后再利用。本發(fā)明采用上述技術方案,主要有以下效果1本發(fā)明裝置采用的振動式內循環(huán)流化床,進料的焦炭顆粒通過顆?;亓峡谠谕庋h(huán)流化床和內流化床反應器內進行物料循環(huán)并和進料的氣體接觸反應,使得幾種物料良性接觸且得到充分的利用,避免了過多物料的損失,節(jié)約成本,生產(chǎn)效率進一步提高,氣固兩相處于流化狀態(tài),避免了顆粒間相互粘結形成的較大的聚團,破壞振動式內循環(huán)流化床的穩(wěn)定操作;其次,本發(fā)明裝置利用振動可以將附著在振動分布板上的顆粒松動,而傾斜的出口板有利于粘性顆粒流動,防止顆粒黏附在振動分布板上。2本發(fā)明裝置中振動分布板上開有不同大小的細孔,可以通過振動將顆粒分級,細顆粒先從振動分布板上部小孔流出,從外循環(huán)流化床以初始流化狀態(tài)緩慢流下,而較大的顆粒從振動分布板下部大孔流出,沿內流化床反應器壁向下流動,這樣可以阻止粘性顆粒黏附在內流化床反應器內壁,起到阻粘作用。3本發(fā)明裝置采用旋風分離器出口排渣不影響反應系統(tǒng)的操作,因而系統(tǒng)可以連續(xù)、穩(wěn)定、長期工作,且產(chǎn)品質量高,適用于大規(guī)模的工業(yè)生產(chǎn)。4本發(fā)明裝置的反應器結構緊湊,易于操作、檢修,降低了生產(chǎn)成本。5本發(fā)明方法采用部分焦炭氧化產(chǎn)生熱量滿足反應所需熱量,這樣供熱體系與反應體系耦合在一個裝置內,并采用熱容量大的固體焦炭顆粒為熱介質,提高料熱量的使用效率。6本發(fā)明方法操作方便且能充分利用低品位鈣鎂含量高粘性大鈦渣,將物料加熱和高溫氯化反應耦合在一起,采用外循環(huán)流化床加熱,內流化床反應器反應的方法,反應溫度分布均勻,控制方便,鈦轉化率高。本發(fā)明可廣泛應用于利用鈦礦制備四氯化鈦,特別適用于利用低品位的鈣鎂含量高的高鈦渣制備四氯化鈦。附圖說明圖1為本發(fā)明裝置的結構示意圖;圖2為圖1中放大的振動分布板的結構示意圖。圖中:1外循環(huán)流化床,1-1外循環(huán)流化床壁,1-2焦炭顆粒進料管,1-3鈦渣顆粒進料管,2內循環(huán)流化床反應器,2-1內流化床反應器壁,2-2顆?;亓峡?,3振動分布板,3-1振動分布板上部小孔,3-2振動分布板下部大孔,3-3擋板,4出料管,5直管,6旋風分離器,6-1氣體出口,6-2閥門,6-3固體顆粒出料口,7鈦渣顆粒,8-1氣體分布板2,8-2氣體分布板1,9-1氣體緩沖罐2,9-2氣體進料管2,9-3氣體進料罐1,9-4氣體進料管1,10焦炭顆粒,11振動器。具體實施方式下面結合具體實施方式,進一步說明本發(fā)明。實施例1如圖1、2所示,一種振動式內循環(huán)流化制備四氯化鈦的裝置。主要包括外循環(huán)流化床、內流化床反應器、振動分布板和振動器、旋風分離器、氣體緩沖罐和氣體分布板等。其特征是:所述外循環(huán)流化床、內流化床反應器、振動分布板、氣體緩沖罐、擋板、出料管、直管、進料管的材料均為不銹鋼材質。所述外循環(huán)流化床1的形狀為頂端封閉的圓柱形殼體,所述圓柱形殼體設置的內徑為1800mm、長度為3000mm、厚度為5mm。在所述圓柱形殼體內的上部高度1700mm的空間為自由空域,設置自由空域用以焦炭固體原料的進料及從所述內流化床反應器2流出的固體顆粒的沉降。在所述自由空域的圓周壁上,對稱地設置兩個孔徑為100mm的通孔(即焦炭固體原料入口),在所述焦炭固體原料入口外分別焊接一根長度為1000mm、與所述外循環(huán)流化床1的殼體的夾角呈50°、內徑與所述焦炭固體原料入口相匹配的焦炭顆粒進料管1-2,以便焦炭固體原料能順利地輸入所述的外循環(huán)流化床1內,并通過所述的振動分布板3進入所述的內循環(huán)流化床反應器2內。在所述圓柱形殼體的頂端面的圓心處,即位于所述自由空域的頂端圓心處,設置一孔徑為120mm的通孔(即出料口),在所述的出料口處焊接一根長度為 1000mm、內徑與所述出料口相匹配的出料管4,并在所述出料管4的另一端焊接一根長度為3000mm、外徑為120mm、與所述出料管4相垂直的直管5。所述直管5的另一端與所述旋風分離器6的入口固接連通,以便所述外循環(huán)流化床1輸出的經(jīng)過氯化反應后的混合氣體順利輸入所述的旋風分離器6進行氣固分離。所述外循環(huán)流化床1底端通過法蘭固接氣體分布板18-2,所述的氣體分布板18-2為厚度為5.5mm、外徑與所述的外循環(huán)流化床1殼體的內徑相匹配、內徑與所述內循環(huán)流化床反應器2殼體的內徑相匹配的圓環(huán)形陶瓷板。在所述的氣體分布板18-2上均勻設置開孔率為0.05、孔徑為1.5mm的通孔,以便所述的氮氣和氧氣的混合氣體均勻地輸入所述的外循環(huán)流化床1的殼體內,所述氣體分布板18-2用于氧氣和氮氣混合氣體均勻分布。在所述外循環(huán)流化床1的圓柱形殼體內的自由空域的下端處,焊接一振動分布板3,以便焦炭固體顆粒通過所述振動分布板3進入所述的外循環(huán)流化床1內和所述的內流化床反應器2內。所述內流化床反應器2的形狀為兩端開口的圓柱形殼體,所述內流化床反應器2殼體的頂端焊接在所述的振動分布板3下部的外表面上,所述圓柱形殼體內徑為1350mm,長度為1400mm,厚度為5mm。在所述圓柱形殼體的下部的圓周壁上還均勻設置5個,孔徑為30mm的通孔(即顆粒回料口2-2),以便經(jīng)所述振動分布板3的焦炭固體原料順利進入所述的內流化床反應器2內進行氯化反應。在所述圓柱形內流化床反應器2殼體下部一側的壁上設置一孔徑為100mm的通孔(即鈦渣固體原料入口),在所述的通孔處焊接一根長度為500mm、與所述圓柱形內流化床反應器2殼體的夾角呈50°、內徑與所述鈦渣固體原料入口相匹配的鈦渣顆粒進料管1-3,以便鈦渣固體原料順利進入所述的內循環(huán)流化床反應器2內。所述圓柱形內流化床反應器2殼體底端通過法蘭固接氣體分布板28-1,所述的氣體分布板28-1為長度為厚度為5.5mm、外徑與所述內流化床反應器2殼體的內徑相匹配的圓盤形陶瓷板,在所述的氣體分布板28-1上均勻設置開孔率為0.05、孔徑為1.5mm的通孔,以便所述的氯氣氣體原料均勻地輸入所述圓柱形內流化床反應器2殼體內。所述的振動分布板3的形狀為兩端敞開的截錐形殼體,所述截錐形殼體的上頂面的內徑與所述外循環(huán)流化床1殼體的內徑相匹配、下底面的內徑為550mm、高度為750mm、厚度為250mm,所述截錐形殼體分為上部和下部,在所述截錐形殼體的上部(即占整個振動分布板3長度的2/3),均勻設置孔徑為1.2mm、孔間距為4mm的小孔(即振動分布板上部小孔3-1),以便較小的焦炭固體顆粒經(jīng)過所述小孔進入所述外循環(huán)流化床1中進行物料循環(huán)。在所述截錐形殼體下部(即占整個振動分布板3長度的1/3),均勻設置孔徑為2mm、孔間距為6.5mm的大孔(即振動分布板下部大孔3-2),以便較大的焦炭固體顆粒經(jīng)過所述大孔進入所述內流化床反應器2內進行氯化反應。在所述截錐形殼體內的底端面上設置一兩端面均敞開的圓柱 形殼體的擋板3-3,所述擋板3-3的高度為35mm、厚度為6.5mm、內徑與所述截錐形殼體的底面內徑相匹配,用以阻擋所述振動分布板3中下滑的焦炭固體顆粒,防止過多焦炭固體顆粒直接進入所述內流化床反應器2內。在所述的振動分布板3內放置一振動器11,所述振動器11為市購的、振動壓力為0.22MPa的倉壁式振動器,通過調整振動頻率和功率,賦予所述振動分布板上顆粒更高的能量,促使焦炭固體顆粒通過所述振動分布板3的細孔進入所述外循環(huán)流化床1內和所述內流化床反應器2中。所述的氣體緩沖罐為厚度為6.5mm的、一小一大的兩個開口頂面、封閉底面的截錐形殼體,兩個所述的截錐形殼體組裝成一個同軸心的容器,所述的小的截錐形殼體(即氣體緩沖罐29-1)的長度為900mm、開口頂面的內徑與所述內流化床反應器2殼體的內徑相匹配、封閉底面的內徑為700mm,所述的氣體緩沖罐29-1與所述的圓盤形氣體分布板28-1通過法蘭固接在所述內流化床反應器2底端,在所述的氣體緩沖罐29-1的封閉底面的軸心處,設置一孔徑為80mm的通孔(即氯氣原料進料口),在所述通孔處焊接一管徑與所述的氯氣原料進料口相匹配、總長度為1250mm的直角形氣體進料管29-2,以便順利地將氯氣氣體原料輸入所述的氣體緩沖罐29-1內,保證氯氣氣體原料持續(xù)穩(wěn)定地輸入所述的內流化床反應器2內,所述氣體緩沖罐29-1用于氯氣氣體的緩沖。所述的大的截錐形殼體(即氣體緩沖罐19-3)的長度為1250mm,頂面開口的內徑與所述外循環(huán)流化床1殼體的內徑相匹配,封面底面的內徑為1200mm,所述氣體緩沖罐19-3與所述的圓環(huán)形氣體分布板18-2通過法蘭固接在所述外循環(huán)流化床1底端,并在所述的氣體緩沖罐19-3的截錐形殼體的外壁上的同一高度均勻焊接5個支撐式支架固定在地面上。在所述氣體緩沖罐19-3的封閉底面的軸心處,設置一孔徑為100mm的通孔(即氯氣原料進料口),在所述混合氣體進料口處焊接一根長度為300mm、管徑與所述混合氣體進料口相匹配的氣體進料管19-4,以便將所述的混合氣體持續(xù)穩(wěn)定地輸入所述的氣體緩沖罐19-3內,所述氣體緩沖罐19-3用于氧氣和氮氣混合氣體的緩沖;并在所述氣體緩沖罐19-3的側壁上并對應于所述氣體進料管29-2的出口處,設置一孔徑與所述進料管29-2的外徑相匹配的通孔,以便所述的氣體進料管29-2伸出所述的氣體緩沖罐19-3外,讓氯氣氣體原料順利輸入。所述的旋風分離器6為市售的常規(guī)產(chǎn)品,從所述的外循環(huán)流化床1的自由空域頂部流出的攜帶極細小的粉塵的氣體通過所述的直管5進入所述的旋風分離器6,進行氣固分離,收集從所述旋風分離器6下部的固體顆粒出料口6-3排出的粉塵,經(jīng)分離后再循環(huán)利用,收集從所述旋風分離器上部的氣體出口6-1排出的氣體,經(jīng)冷卻后得到四氯化鈦產(chǎn)品,并收集濾出的剩余氣體,經(jīng)處理后可再利用,以免污染大氣。實施例2一種振動式內循環(huán)流化制備四氯化鈦的裝置,同實施例1,其中:所述外循環(huán)流化床1的內徑為500mm、長度為1000mm、厚度為3mm,在所述圓柱形殼體內的自由空域上部高度為400mm,所述自由空域的圓周壁上的兩個通孔(即焦炭固體原料入口)的孔徑為50mm。在所述焦炭固體原料入口外分別焊接一根長度為500mm、與所述外循環(huán)流化床1的殼體的夾角呈30°、內徑與所述焦炭固體原料入口相匹配的焦炭顆粒進料管1-2。在所述圓柱形殼體的頂端面的圓心處的通孔(即出料口)的孔徑為50mm,在所述的出料口處焊接一根長度為1500mm、內徑與所述出料口相匹配的出料管4,并在所述出料管4的另一端焊接一根長度為1000mm、外徑為50mm、與所述出料管4相垂直的直管5。所述的氣體分布板18-2為厚度為1mm。在所述的氣體分布板18-2上均勻設置開孔率為0.01、孔徑為0.5mm的通孔。所述內流化床反應器2圓柱形殼體的內徑為250mm、長度為800mm、厚度為3mm,所述圓柱形殼體的下部的圓周壁上還均勻設置2個、孔徑為10mm的通孔(即顆?;亓峡?-2)。在所述圓柱形內流化床反應器2殼體下部一側的壁上設置一孔徑為50mm的通孔(即鈦渣固體原料入口),在所述的通孔處焊接一根長度為200mm、與所述圓柱形內流化床反應器2殼體的夾角呈30°、內徑與所述鈦渣固體原料入口相匹配的鈦渣顆粒進料管1-3。述圓柱形內流化床反應器2殼體底端通過法蘭固接在氣體分布板28-1上,所述的氣體分布板28-1為厚度為1mm、外徑與所述內流化床反應器2殼體的內徑相匹配的圓盤形陶瓷板。所述的氣體分布板28-1上均勻設置開孔率為0.01、孔徑為0.5mm的通孔。所述的振動分布板3的下底面的內徑為100mm、高度為300mm、厚度為100mm。在所述振動分布板的上部均勻設置孔徑為0.5mm、孔間距為2mm的小孔(即振動分布板上部小孔3-1)。在所述振動分布板的下部均勻設置孔徑為1mm、孔間距為3mm的大孔(即振動分布板下部大孔3-2)。所述擋板3-3的高度為20mm、厚度為5mm。所述振動器11為振動壓力為0.1MPa的倉壁式振動器。所述的氣體緩沖罐為厚度為3mm的一小一大的兩個截錐形殼體,氣體緩沖罐29-1的長度為200mm、封閉底面的內徑為150mm。在所述的氣體緩沖罐29-1的封閉底面的軸心處,設置一孔徑為50mm的通孔(即氯氣原料進料口),在所述通孔處焊接一管徑與所述的氯氣原料進料口相匹配、總長度為400mm的直角形氣體進料管29-2。氣體緩沖罐19-3的長度為500mm、封面底面的內徑為300mm。在所述的氣體緩沖罐19-3的截錐形殼體的外壁上的同一高度均勻焊接4個鞍型支架固定在地面上,在所述氣體緩沖罐19-3的封閉底面的軸心處,設置一孔徑為50mm的通孔(即氯氣和氮氣的混合氣體的進料口),在所述混合氣體進料口處焊接一根長度為100mm的氣體進料管19-4。實施例3一種振動式內循環(huán)流化制備四氯化鈦的裝置,同實施例1,其中:所述外循環(huán)流化床、內流化床反應器、振動分布板、氣體緩沖罐、擋板、出料管、直管、進料管的材料均為鈦合金材質。所述外循環(huán)流化床1的內徑為3000mm、長度為5000mm、厚度為8mm,所述圓柱形殼體內的上部自由空域的高度為3000mm,所述自由空域的圓周壁上的通孔(即焦炭固體原料入口)的孔徑為150mm,在所述焦炭固體原料入口外分別焊接一根長度為1500mm、與所述外循環(huán)流化床1的殼體的夾角呈70°的焦炭顆粒進料管1-2。在所述圓柱形殼體的頂端面的圓心處,設置一孔徑為200mm的通孔(即出料口),在所述的出料口處焊接一根長度為2000mm的出料管4,并在所述出料管4的另一端焊接一根長度為5000mm、外徑為200mm、與所述出料管4相垂直的直管5。所述的氣體分布板18-2為厚度為10mm的圓環(huán)形陶瓷板,在所述的氣體分布板18-2上均勻設置開孔率為0.1、孔徑為2.5mm的通孔。所述內流化床反應器2的內徑為2500mm、長度為2000mm、厚度為8mm,在所述圓柱形殼體的下部的圓周壁上均勻設置8個、孔徑為50mm的通孔(即顆?;亓峡?-2),在所述內流化床反應器2殼體下部一側的壁上設置一孔徑為150mm的通孔(即鈦渣固體原料入口),在所述的通孔處焊接一根長度為800mm、與所述圓柱形內流化床反應器2殼體的夾角呈70°的鈦渣顆粒進料管1-3。所述的氣體分布板28-1為長度為厚度為10mm的圓盤形陶瓷板,在所述的氣體分布板28-1上均勻設置開孔率為0.1,孔徑為2.5mm的通孔。所述振動分布板3的下底面的內徑為1000mm、高度為1200mm、厚度為400mm。所述振動分布板3的上部均勻設置孔徑為2mm、孔間距為6mm的小孔(即振動分布板上部小孔3-1),在所述振動分布板3下部(即占整個振動分布板3長度的1/3),均勻設置孔徑為3mm、孔間距為10mm的大孔(即振動分布板下部大孔3-2),所述擋板3-3的高度為50mm、厚度為8mm。所述振動器11為振動壓力為0.35MPa的倉壁式振動器。所述的氣體緩沖罐為厚度為10mm的一小一大的兩個截錐形殼體。氣體緩沖罐29-1的長度為1500mm,封閉底面的內徑為1200mm,在所述的氣體緩沖罐29-1的封閉底面的軸心處,設置一孔徑為120mm的通孔(即氯氣原料進料口),在所述通孔處焊接一管徑與所述的氯氣原料進料口相匹配、總長度為2100mm的直角形氣體進料管29-2。氣體緩沖罐19-3的長度為2000mm,封面底面的內徑為2000mm。在所述的氣體緩沖罐19-3的截錐形殼體的外壁上的同一高度均勻焊接6掩護式支架固定在地面上,在所述氣體緩沖罐19-3的封閉底面的軸心處,設置一孔徑為150mm的通孔(即氯氣和氮氣的混合氣體的進料口),在所述混合氣體進料口處焊接一根長度為500mm的氣體進料管19-4。實施例4一種振動式內循環(huán)流化制備四氯化鈦的方法,以低品位的鈣鎂含量高的高鈦渣和焦炭為固體原料,以氧氣,氮氣及氯氣為氣體原料,利用本發(fā)明裝置,經(jīng)過氯化反應和冷卻及氣固分離而制得成品。所述的具體步驟如下:(1)原料處理以低品位的鈣鎂含量高的高鈦渣(簡稱高鈦渣)和焦炭為固體原料,以氧氣和氮氣及氯氣為氣體原料,先對所述的固體原料分別通過11目的分離篩進行分篩,并按高鈦渣顆粒的平均粒徑∶焦炭顆粒的平均粒徑之比1∶1,和按高鈦渣顆粒的質量∶焦炭顆粒的質量比為1∶1.65的比例備料,然后分別對高鈦渣顆粒和焦炭顆粒進行加熱,加熱至固體顆粒溫度都為500℃,備用,對所述氣體原料中的氯氣進行加熱至400℃,備用,對氧氣和氮氣先按氧氣∶氮氣的體積比為1∶0.3的比例進行混合,再對混合氣體進行加熱至200℃,備用。(2)氯化反應第(1)步完成后,將第(1)步處理后的原料,分別輸入到本發(fā)明的裝置中,即焦炭顆粒以271kg/h的速度從所述裝置的焦炭顆粒進料管1-2輸入,通過所述裝置的振動分布板3進入所述裝置的外循環(huán)流化床1內和所述裝置的內流化床反應器2中,高鈦渣顆粒以110kg/h的速度從所述裝置的鈦渣顆粒進料管1-3輸入到所述的內流化床反應器2中,氯氣以2m/s的速度從所述裝置的氣體緩沖罐29-1底面的氣體進料管29-2輸入到所述的內流化床反應器2中,氧氣和氮氣的混合氣體以0.8m/s的速度從所述裝置的氣體緩沖罐19-3底面的氣體進料管19-4輸入到所述的外循環(huán)流化床1中。使所述的焦炭顆粒在所述外循環(huán)流化床1下行中與所述的氧氣和氮氣混合氣體逆流接觸反應,利用反應放出的熱量加熱焦炭顆粒,使焦炭顆粒達到1200℃,所得到的高溫焦炭顆粒從所述內流化床反應器壁2-1上的顆?;亓峡?-2進入所述的內流化床反應器2內,用以保持所述內流化床反應器2內部溫度為950℃,從所述的氣體進料管29-2輸入的氯氣和從所述鈦渣顆粒進料管1-3進入的鈦渣顆粒在所述的內流化床反應器2內進行高溫氯化反應,隨反應的進行,氣固混合物在上行過程中,固體反應物顆粒粒徑逐漸減小,進入所述外循環(huán)流化床1內上部的自由空域,氣體表觀速度減小,攜帶的細顆粒被拋灑在所述振動分布板3上,在所述振動器11振動下較小顆粒穿過所述振動分布板上部小孔3-1進入所述外循環(huán)流化床1內,與新進料的焦炭顆粒一起下流,經(jīng)過所述顆粒回料口2-2進入所述內流化床反應器2內,從而形成內循環(huán)流化氯化過程,所述氯化反應后產(chǎn)生的并攜帶有少量粉塵的氣體通過所述的外循環(huán)流化床1上部的自由空域和出料管4及直管5輸入所述裝置的旋風分離器6中,所述裝置在運行中的壓力為0.22MPa。(3)氣固分離第(2)步完成后,在所述裝置的旋風分離器6中,對第(2)步氯化反應產(chǎn)生的帶有少量粉塵的氣體,進行氣固分離,收集在所述旋風分離器6上部的氣體出口6-1濾出的氣體,自然冷卻后得到四氯化鈦產(chǎn)品,并收集濾出的剩余氣體,經(jīng)處理后可再利用以免污染大氣;收集從所述旋風分離器6下部的固體顆粒出料口6-3濾出的粉塵,經(jīng)分離后再利用。最后經(jīng)測定,含鈦礦物的氯化率達到99%,經(jīng)精制工序后,得到純度為99%(質量分數(shù))的四氯化鈦。實施例5一種振動式內循環(huán)流化制備四氯化鈦的方法,同實施例4,其中:第(1)步中,對所述的固體原料分別通過0.7目的分離篩進行分篩,高鈦渣顆粒的平均粒徑∶焦炭顆粒的平均粒徑之比1∶0.8,高鈦渣顆粒的質量∶焦炭顆粒的質量比為1∶0.3的比例備料,分別加熱高鈦渣顆粒和焦炭顆粒至溫度都為400℃,對所述氣體原料中的氯氣進行加熱至300℃,對氧氣和氮氣先按氧氣∶氮氣的體積比為1∶0.1的比例進行混合,再對混合氣體進行加熱至100℃。第(2)步中,焦炭顆粒以1.8kg/h的速度從所述裝置的焦炭顆粒進料管1-2輸入,高鈦渣顆粒以36kg/h的速度從所述裝置的鈦渣顆粒進料管1-3輸入到內流化床反應器2中,氯氣以0.5m/s的速度從所述裝置的氣體緩沖罐29-1底面的氣體進料管29-2輸入到內流化床反應器2中,氧氣和氮氣的混合氣體以0.2m/s的速度從所述裝置的氣體緩沖罐19-3底面的氣體進料管19-4輸入到外循環(huán)流化床1中。利用焦炭顆粒與所述的氧氣和氮氣混合氣體反應放出的熱量加熱焦炭顆粒達到1000℃,用以保持所述內流化床反應器2內部溫度為800℃,本發(fā)明裝置在運行中的壓力為0.1MPa。第(3)步中,收集在所述旋風分離器6上部的氣體出口6-1濾出的氣體,自然冷卻后得到四氯化鈦產(chǎn)品;收集從所述旋風分離器6下部的固體顆粒出料口6-3濾出的粉塵,經(jīng)分離后再利用。最后經(jīng)測定,含鈦礦物的氯化率達到96%,經(jīng)精制工序后,得到純度為97%(質量分數(shù))的四氯化鈦。實施例6一種振動式內循環(huán)流化制備四氯化鈦的方法,同實施例4,其中:第(1)步中,先對所述的固體原料分別通過21目的分離篩進行分篩,并按高鈦渣顆粒的平均粒徑∶焦炭顆粒的平均粒徑之比1∶1.2,和按高鈦渣顆粒的質量∶焦炭顆粒的質量比為1∶3的比例備料,分別加熱高鈦渣顆粒和焦炭顆粒至溫度都為600℃。對所述氣體原料中的氯氣進行加熱至500℃,對氧氣和氮氣先按氧氣∶氮氣的體積比為1∶0.5的比例進行混合,再 對混合氣體進行加熱至300℃。第(2)步中,焦炭顆粒以540kg/h的速度從所述裝置的焦炭顆粒進料管1-2輸入,高鈦渣顆粒以180kg/h的速度從所述裝置的鈦渣顆粒進料管1-3輸入到所述裝置的內流化床反應器2中,氯氣以3.5m/s的速度從所述裝置的氣體緩沖罐29-1底面的氣體進料管29-2輸入到所述的內流化床反應器2中,氧氣和氮氣的混合氣體以1.5m/s的速度從所述裝置的氣體緩沖罐19-3底面的氣體進料管19-4輸入到所述的外循環(huán)流化床1中。利用焦炭顆粒與所述的氧氣和氮氣混合氣體反應放出的熱量加熱焦炭顆粒達到1300℃,保持所述內流化床反應器2內部溫度為1100℃,所述裝置在運行中的壓力為0.35MPa。第(3)步中,收集在所述旋風分離器6上部的氣體出口6-1濾出的氣體,自然冷卻后得到四氯化鈦產(chǎn)品;收集從所述旋風分離器6下部的固體顆粒出料口6-3濾出的粉塵,經(jīng)分離后再利用。最后經(jīng)測定,含鈦礦物的氯化率達到97%,經(jīng)精制工序后,得到純度為98%(質量分數(shù))的四氯化鈦。