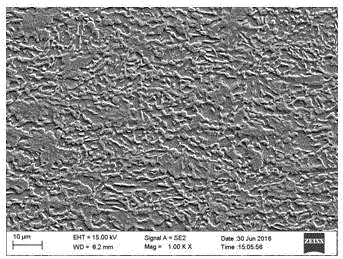
本發(fā)明涉及一種高強(qiáng)鋼板及其生產(chǎn)方法,尤其是一種一鋼多級的熱軋復(fù)相高強(qiáng)鋼板及其生產(chǎn)方法。
背景技術(shù):
:高強(qiáng)鋼分為傳統(tǒng)高強(qiáng)鋼(ConventionalHSS)和先進(jìn)高強(qiáng)鋼(AHSS);先進(jìn)高強(qiáng)度鋼,也稱為高級高強(qiáng)度鋼,其英文縮寫為AHSS(AdvancedHighStrengthSteel);AHSS主要包括雙相鋼(DP)、相變誘導(dǎo)塑性(TRIP)鋼、馬氏體(M)鋼、復(fù)相鋼(CP)、熱成形(HF)鋼和孿晶誘導(dǎo)塑性(TWIP)鋼等。先進(jìn)高強(qiáng)鋼是上個世紀(jì)70年代逐漸發(fā)展起來的新型鋼種,其強(qiáng)化手段與傳統(tǒng)的高強(qiáng)鋼有明顯的不同,傳統(tǒng)高強(qiáng)鋼主要通過固溶強(qiáng)化、相變強(qiáng)化、彌散強(qiáng)化和細(xì)晶強(qiáng)化等手段提高鋼板的強(qiáng)度從而達(dá)到所需性能,先進(jìn)高強(qiáng)鋼在傳統(tǒng)強(qiáng)化手段的基礎(chǔ)上,充分發(fā)揮了相變強(qiáng)化的作用,通過配合熱處理工藝手段,獲得馬氏體、貝氏體、鐵素體和殘余奧氏體的兩相或更多相的復(fù)相組織,使得各相充分發(fā)揮自身特點(diǎn)。隨著汽車等行業(yè)向節(jié)能、降耗、環(huán)保的輕量化方向發(fā)展,汽車用鋼面臨嚴(yán)峻的挑戰(zhàn),設(shè)計(jì)能滿足汽車多種零件性能要求的鋼種已成為汽車行業(yè)對鋼鐵行業(yè)的迫切要求,為了獲得強(qiáng)韌性能良好匹配的輕量化鋼板,同時滿足汽車產(chǎn)業(yè)多零件、多性能特點(diǎn),考慮鋼鐵企業(yè)生產(chǎn)組織特點(diǎn),通過采用一種成分體系實(shí)現(xiàn)多種性能的產(chǎn)品,適應(yīng)不同用戶零件的需求,成為鋼鐵企業(yè)亟待解決的問題?,F(xiàn)有技術(shù)中,公開號CN103045950A介紹了一種低合金高強(qiáng)韌性復(fù)相鋼及其熱處理方法,其主要是通過淬火工藝然后回火實(shí)現(xiàn)復(fù)相鋼組織,其采用較高的C含量,零件焊接性能較差。公開號CN103589954A介紹了一種一鋼多級的熱軋鋼板及其制造方法,其采用分段冷卻和不同卷取溫度實(shí)現(xiàn)不同強(qiáng)度級別,無法保證鋼卷性能的均勻性,而且低溫卷取時要實(shí)現(xiàn)自動控制,需增上低溫卷取高溫計(jì),對卷取設(shè)備能力要求也較高。公開號CN101225499A介紹了一種低合金超高強(qiáng)度復(fù)相鋼及其熱處理方法,其將工件奧氏體化后,需經(jīng)3次淬火/保溫處理,工序較復(fù)雜,淬火介質(zhì)較多,生產(chǎn)工況條件較差。公開號CN103667948A介紹了一種復(fù)相鋼及其制備方法,其添加了較高的P,可能會對材料的性能造成影響。技術(shù)實(shí)現(xiàn)要素:本發(fā)明要解決的技術(shù)問題是提供一種性能良好的一鋼多級的熱軋復(fù)相高強(qiáng)鋼板;本發(fā)明還提供了一種一鋼多級的熱軋復(fù)相高強(qiáng)鋼板的生產(chǎn)方法。為解決上述技術(shù)問題,本發(fā)明化學(xué)成分的重量百分含量為:C0.08~0.15%,Mn1.80~3.00%,S≤0.015%,P≤0.025%,Si0.50~1.00%,Als0.020~0.060%,Cr0.40~1.0%,Ti0.010~0.040%,Mo0.10~0.30%,N≤0.007%,其余為鐵和不可避免的雜質(zhì)。本發(fā)明所述鋼板的金相組織為鐵素體+貝氏體+殘余奧氏體、鐵素體+馬氏體+貝氏體+殘余奧氏體或鐵素體+馬氏體+殘余奧氏體。本發(fā)明方法包括加熱、熱軋、冷卻、卷取和退火工序,所述鋼板化學(xué)成分的重量百分含量如上所述;所述熱軋工序:精軋開軋溫度為1030~1100℃,終軋溫度為800~900℃;所述退火工序:退火溫度為600~1000℃,保溫2~8h,然后隨爐冷卻或空冷。本發(fā)明所述退火工序選用下述工藝模式:Ⅰ、退火溫度為600~650℃,保溫2~8h,然后隨爐冷卻,得到700MPa級鐵素體+貝氏體+殘余奧氏體的復(fù)相高強(qiáng)鋼板;Ⅱ、退火溫度為650~700℃,保溫2~8h,然后隨爐冷卻,得到800MPa級的鐵素體+貝氏體+殘余奧氏體的復(fù)相高強(qiáng)鋼板;Ⅲ、退火溫度為700℃~750℃,保溫2~4h隨爐冷卻或保溫4~8h空冷,得到900MPa級的鐵素體+貝氏體+殘余奧氏體的復(fù)相高強(qiáng)鋼板;Ⅳ、退火溫度為800℃~900℃,保溫2~3h隨爐冷卻或保溫3~8h空冷,得到1000MPa級的鐵素體+馬氏體+貝氏體+殘余奧氏體的復(fù)相高強(qiáng)鋼板;Ⅴ、退火溫度為900℃~1000℃,保溫2~3h隨爐冷卻或保溫3~8h空冷,得到1100MPa級的鐵素體+馬氏體+殘余奧氏體的復(fù)相高強(qiáng)鋼板。本發(fā)明所述加熱工序:將鋼坯加熱至1200~1300℃,保溫2.5~4h,板坯頭尾溫差≤20℃。本發(fā)明所述冷卻工序:采用“U”型冷卻控制,帶鋼頭部20~30米的溫度比中部高10~30℃,尾部40~80米的溫度比中部高20~40℃。本發(fā)明所述卷取工序:卷取溫度為500~700℃,卷取機(jī)單位張力為35~42N/mm2,張力分配為20~40%,熱卷在芯軸停留0.5~2.5min后進(jìn)行卸卷。本發(fā)明方法設(shè)計(jì)構(gòu)思為:將板坯采用熱軋+退火工藝,實(shí)現(xiàn)不同的金相組織,達(dá)到不同強(qiáng)度級別復(fù)相鋼產(chǎn)品的需求;熱軋工序?yàn)楸WC長度方向力學(xué)性能的均勻,在熱軋步驟的冷卻過程中,帶鋼頭部20~30米的溫度比中部高10~30℃,尾部40~80米的溫度比中部高20~40℃。本發(fā)明方法主要應(yīng)用相組織轉(zhuǎn)變的原理,生產(chǎn)控制難度小,采用一種成分體系生產(chǎn)多種性能的產(chǎn)品,適應(yīng)不同用戶零件的需求,可產(chǎn)生極大的經(jīng)濟(jì)效益。本發(fā)明方法所述卷取工序?yàn)楸WC產(chǎn)品卷型質(zhì)量,滿足酸洗工序上卷要求,采用上述單位張力、張力分配以及熱卷在芯軸停留時間的限定。采用上述技術(shù)方案所產(chǎn)生的有益效果在于:本發(fā)明滿足用戶對不同強(qiáng)度級別的要求,具有力學(xué)性能均勻,烘烤硬化性能良好等特點(diǎn)。本發(fā)明方法在不改變冶煉成分的前提下,通過熱軋+退火工藝來滿足用戶對不同強(qiáng)度級別的要求,采用不同的退火工藝實(shí)現(xiàn)鐵素體+貝氏體+殘余奧氏體、鐵素體+馬氏體+貝氏體+殘余奧氏體、鐵素體+馬氏體+殘余奧氏體等不同組織類別的產(chǎn)品,抗拉強(qiáng)度級別覆蓋700~1200MPa,屈服強(qiáng)度550~1000MPa,延伸率>10%,烘烤硬化值BH2>50MPa的復(fù)相鋼產(chǎn)品。本發(fā)明通過合理的成分設(shè)計(jì)采用一種成分體系,通過控制退火工序不同的組織類別實(shí)現(xiàn)不同強(qiáng)度級別復(fù)相鋼,滿足鋼鐵企業(yè)采用一種成分滿足不同用戶的特殊需求,產(chǎn)品卷力學(xué)性能均勻,烘烤硬化性能良好,滿足用戶對小批量、不同強(qiáng)度級別樣片的需求。附圖說明下面結(jié)合附圖和具體實(shí)施方式對本發(fā)明作進(jìn)一步詳細(xì)的說明。圖1為實(shí)施例1中1100MPa級鐵素體-馬氏體-少量殘余奧氏體熱軋鋼板典型金相組織;圖2為實(shí)施例8中1000MPa級鐵素體-馬氏體-少量貝氏體-少量殘余奧氏體熱軋鋼板典型金相組織;圖3為實(shí)施例14中900MPa級鐵素體-貝氏體-少量殘余奧氏體熱軋鋼板典型金相組織;圖4為實(shí)施例20中800MPa級鐵素體-貝氏體-少量殘余奧氏體熱軋鋼板典型金相組織;圖5為實(shí)施例23中700MPa級鐵素體-貝氏體-少量殘余奧氏體熱軋鋼板典型金相組織。具體實(shí)施方式本一鋼多級的熱軋復(fù)相高強(qiáng)鋼板及其生產(chǎn)方法采用下述工藝步驟:(1)煉鋼和澆鑄工序:出鋼鋼水化學(xué)成分的重量百分比為:C0.08~0.15%,Mn1.80~3.00%,S≤0.015%,P≤0.025%,Si0.50~1.00%,Als0.020~0.060%,Cr0.40~1.0%,Ti0.010~0.040%,Mo0.10~0.30%,N≤0.007%,其余為鐵和不可避免的雜質(zhì)。澆鑄時采用全程氬氣保護(hù)澆鑄,鋼水過熱度為20~35℃,應(yīng)用動態(tài)輕壓下,結(jié)晶器液面波動穩(wěn)定控制在±2mm內(nèi)。(2)加熱工序:澆鑄得到的鋼坯加熱至1200~1300℃,保溫2.5~4h,爐后除鱗溫度>1120℃,板坯頭尾溫差≤20℃。(3)熱軋工序:精軋開軋溫度為1030~1100℃,終軋溫度為800~900℃。(4)冷卻工序:采用“U”型冷卻控制,帶鋼頭部20~30米的溫度比中部高10~30℃,尾部40~80米的溫度比中部高20~40℃。采用“U”型冷卻主要考慮熱卷卷取后頭尾空冷溫降快,頭尾部性能較高,在二級模型里可以設(shè)定卷取溫度頭尾部升溫模式。(5)卷取工序:卷取溫度為500~700℃,卷取時的單位張力為35~42N/mm2,張力分配為20~40%,熱卷在芯軸停留0.5~2.5min后進(jìn)行卸卷,得到厚度規(guī)格為1.8~12.0mm的熱軋鋼板。(6)退火工序根據(jù)產(chǎn)品需求選用下述工藝模式:Ⅰ、退火溫度為600~650℃,保溫2~8h,然后隨爐冷卻至室溫,經(jīng)后續(xù)的酸洗工序后,得到700MPa級的鐵素體+貝氏體+殘余奧氏體的復(fù)相高強(qiáng)鋼板,其中鐵素體的體積分?jǐn)?shù)為65~85%,硬相為貝氏體;Ⅱ、退火爐內(nèi)退火溫度為650~700℃,保溫2~8h,然后隨爐冷卻至室溫;經(jīng)后續(xù)的酸洗工序后,得到800MPa級的鐵素體+貝氏體+殘余奧氏體的復(fù)相高強(qiáng)鋼板,其中鐵素體的體積分?jǐn)?shù)為55~75%,硬相為貝氏體;Ⅲ、退火溫度為700℃~750℃,保溫2~4h后隨爐冷卻至室溫,或保溫4~8h后空冷至室溫;經(jīng)后續(xù)的酸洗工序后,得到900MPa級的鐵素體+貝氏體+殘余奧氏體的復(fù)相高強(qiáng)鋼板,其中鐵素體的體積分?jǐn)?shù)為35~55%,硬相為馬氏體和貝氏體;Ⅳ、退火溫度為800℃~900℃,保溫2~3h后隨爐冷卻至室溫,或保溫3~8h后空冷至室溫;經(jīng)后續(xù)的酸洗工序后,得到1000MPa級的鐵素體+馬氏體+貝氏體+殘余奧氏體的復(fù)相高強(qiáng)鋼板,其中鐵素體的體積分?jǐn)?shù)為25~45%,硬相為馬氏體和貝氏體;Ⅴ、退火溫度為900℃~1000℃,保溫2~3h后隨爐冷卻至室溫,或保溫3~8h后空冷至室溫;經(jīng)后續(xù)的酸洗工序后,得到1100MPa級的鐵素體+馬氏體+殘余奧氏體的復(fù)相高強(qiáng)鋼板,其中鐵素體的體積分?jǐn)?shù)為20~35%,硬相為馬氏體。(7)酸洗工序:退火卷開卷破鱗后進(jìn)入酸洗槽,酸洗速度為60~120m/min,保證去除鋼板表面氧化鐵皮;酸洗后即可得到所述的復(fù)相高強(qiáng)鋼板,其抗拉強(qiáng)度級別覆蓋700~1200MPa,屈服強(qiáng)度550~1000MPa,延伸率>10%,烘烤硬化值BH2>50MPa。實(shí)施例1:本一鋼多級的熱軋復(fù)相高強(qiáng)鋼板具體生產(chǎn)工藝如下所述。(1)煉鋼和澆鑄:出鋼鋼水化學(xué)成分的重量百分比為:C0.10%,Mn2.5%,S0.012%,P0.025%,Si0.8%,Als0.04%,Cr0.60%,Ti0.015%,Mo0.10%,N0.005%,其余為鐵和不可避免的雜質(zhì),澆鑄步驟中,鋼水過熱度為30℃;應(yīng)用動態(tài)輕壓下,結(jié)晶器液面波動穩(wěn)定控制在±2mm內(nèi)。(2)加熱工序:板坯加熱至1270~1300℃,保溫3.0h,爐后除鱗溫度1130℃,板坯頭尾溫差≤20℃。(3)熱軋工序:精軋開軋溫度1040±10℃,終軋溫度為890±10℃,軋制鋼板厚度為8.0mm。(4)冷卻工序:采用“U”型冷卻控制,頭20米+10℃,尾部40米+20℃。(5)卷取工序:卷取溫度為610±10℃,卷取單位張力采用38N/mm2,張力分配為20%,熱卷在芯軸停留2min后進(jìn)行卸卷。(6)退火工序:退火溫度為950℃,在該溫度保溫4h,然后出爐空冷至室溫。(7)酸洗工序:酸洗速度為60m/min。本實(shí)施例所得金相組織為鐵素體-馬氏體-少量殘余奧氏體,典型金相組織見圖1,復(fù)相高強(qiáng)鋼板的性能指標(biāo)見表4。實(shí)施例2:本一鋼多級的熱軋復(fù)相高強(qiáng)鋼板具體生產(chǎn)工藝如下所述。(1)煉鋼和澆鑄:出鋼鋼水化學(xué)成分的重量百分比為:C0.08%,Mn1.80%,S0.006%,P0.012%,Si1.0%,Als0.045%,Cr0.80%,Ti0.035%,Mo0.3%,N0.006%,其余為鐵和不可避免的雜質(zhì),澆鑄步驟中,鋼水過熱度為25℃;應(yīng)用動態(tài)輕壓下,結(jié)晶器液面波動穩(wěn)定控制在±2mm內(nèi)。(2)加熱工序:板坯加熱至1250~1270℃,保溫2.5h,爐后除鱗溫度1135℃,板坯頭尾溫差≤20℃。(3)熱軋工序:精軋開軋溫度1090±10℃,終軋溫度為870±10℃,軋制鋼板厚度為1.8mm。(4)冷卻工序:采用“U”型冷卻控制,頭30米+20℃,尾部80米+40℃。(5)卷取工序:卷取溫度為670±10℃,卷取單位張力采用42N/mm2,張力分配為30%,熱卷在芯軸停留2.5min后進(jìn)行卸卷。(6)退火工序:退火溫度為910℃,在該溫度保溫8h,然后出爐空冷至室溫。(7)酸洗工序:酸洗速度為120m/min。本實(shí)施例所得金相組織為鐵素體-馬氏體-少量殘余奧氏體,復(fù)相高強(qiáng)鋼板的性能指標(biāo)見表4。實(shí)施例3-7:本一鋼多級的熱軋復(fù)相高強(qiáng)鋼板具體生產(chǎn)工藝如下所述。除步驟(6)退火工序之外,其余同實(shí)施例1;步驟(6)退火工序的具體工藝見表1。表1:實(shí)施例3-7的退火工藝實(shí)施例3實(shí)施例4實(shí)施例5實(shí)施例6實(shí)施例7退火溫度/℃10009009009501000保溫時間/h35322.5冷卻方式出爐空冷出爐空冷隨爐冷卻隨爐冷卻隨爐冷卻實(shí)施例3-7所得金相組織為鐵素體-馬氏體-少量殘余奧氏體,復(fù)相高強(qiáng)鋼板的性能指標(biāo)見表4。實(shí)施例8:本一鋼多級的熱軋復(fù)相高強(qiáng)鋼板具體生產(chǎn)工藝如下所述。(1)煉鋼和澆鑄:出鋼鋼水化學(xué)成分的重量百分比為:C0.15%,Mn3.0%,S0.006%,P0.025%,Si0.5%,Als0.045%,Cr1.0%,Ti0.01%,Mo0.15%,N0.007%,其余為鐵和不可避免的雜質(zhì),澆鑄步驟中,鋼水過熱度為35℃;應(yīng)用動態(tài)輕壓下,結(jié)晶器液面波動穩(wěn)定控制在±2mm內(nèi)。(2)加熱工序:板坯加熱至1200~1230℃,保溫3.5h,爐后除鱗溫度1150℃,板坯頭尾溫差≤20℃。(3)熱軋工序:精軋開軋溫度1070±10℃,終軋溫度為860±10℃,軋制鋼板厚度為4.5mm。(4)冷卻工序:采用“U”型冷卻控制,頭30米+15℃,尾部60米+25℃。(5)卷取工序:卷取溫度為570±10℃,卷取單位張力采用40N/mm2,張力分配為25%,熱卷在芯軸停留2.0min后進(jìn)行卸卷。(6)退火工序:退火溫度為860℃,在該溫度保溫2h,然后爐冷至室溫。(7)酸洗工序:酸洗速度為80m/min。本實(shí)施例所得金相組織為鐵素體-馬氏體-少量貝氏體-少量殘余奧氏體,典型金相組織見圖2,復(fù)相高強(qiáng)鋼板的性能指標(biāo)見表4。實(shí)施例9:本一鋼多級的熱軋復(fù)相高強(qiáng)鋼板具體生產(chǎn)工藝如下所述。(1)煉鋼和澆鑄:出鋼鋼水化學(xué)成分的重量百分比為:C0.10%,Mn2.5%,S0.012%,P0.025%,Si0.8%,Als0.04%,Cr0.60%,Ti0.015%,Mo0.10%,N0.005%,其余為鐵和不可避免的雜質(zhì),澆鑄步驟中,鋼水過熱度為30℃;應(yīng)用動態(tài)輕壓下,結(jié)晶器液面波動穩(wěn)定控制在±2mm內(nèi)。(2)加熱工序:板坯加熱至1230~1250℃,保溫3.5h,爐后除鱗溫度1150℃,板坯頭尾溫差≤20℃。(3)熱軋工序:精軋開軋溫度1070±10℃,終軋溫度為870±10℃,軋制鋼板厚度為3.0mm。(4)冷卻工序:采用“U”型冷卻控制,頭20米+10℃,尾部40米+20℃。(5)卷取工序:卷取溫度為690±10℃,卷取單位張力采用40N/mm2,張力分配為20%,熱卷在芯軸停留1.5min后進(jìn)行卸卷。(6)退火工序:退火溫度為900℃,在該溫度保溫8h,然后空冷至室溫。(7)酸洗工序:酸洗速度為120m/min。本實(shí)施例所得金相組織為鐵素體-馬氏體-少量貝氏體-少量殘余奧氏體,復(fù)相高強(qiáng)鋼板的性能指標(biāo)見表4。實(shí)施例10-13:本一鋼多級的熱軋復(fù)相高強(qiáng)鋼板具體生產(chǎn)工藝如下所述。除步驟(6)退火工序之外,其余同實(shí)施例8;步驟(6)退火工序的具體工藝見表4。表2:實(shí)施例10-13的退火工藝實(shí)施例10實(shí)施例11實(shí)施例12實(shí)施例13退火溫度/℃800840900800保溫時間/h6332.5冷卻方式出爐空冷出爐空冷隨爐冷卻隨爐冷卻實(shí)施例10-13所得金相組織為鐵素體-馬氏體-少量貝氏體-少量殘余奧氏體,復(fù)相高強(qiáng)鋼板的性能指標(biāo)見表4。實(shí)施例14:本一鋼多級的熱軋復(fù)相高強(qiáng)鋼板具體生產(chǎn)工藝如下所述。(1)煉鋼和澆鑄:出鋼鋼水化學(xué)成分的重量百分比為:C0.15%,Mn3.0%,S0.006%,P0.025%,Si0.5%,Als0.045%,Cr1.0%,Ti0.01%,Mo0.15%,N0.007%,其余為鐵和不可避免的雜質(zhì),澆鑄步驟中,鋼水過熱度為35℃;應(yīng)用動態(tài)輕壓下,結(jié)晶器液面波動穩(wěn)定控制在±2mm內(nèi)。(2)加熱工序:板坯加熱至1270~1300℃,保溫4h,爐后除鱗溫度1125℃,板坯頭尾溫差≤20℃。(3)熱軋工序:精軋開軋溫度1070±10℃,終軋溫度為820±10℃,軋制鋼板厚度為2.5mm。(4)冷卻工序:采用“U”型冷卻控制,頭30米+15℃,尾部70米+20℃。(5)卷取工序:卷取溫度為600±10℃,卷取單位張力采用40N/mm2,張力分配為25%,熱卷在芯軸停留2.5min后進(jìn)行卸卷。(6)退火工序:退火溫度為720℃,在該溫度保溫2h,然后爐冷至室溫。(7)酸洗工序:酸洗速度為100m/min。本實(shí)施例所得金相組織為鐵素體-貝氏體-少量殘余奧氏體,典型金相組織見圖3,復(fù)相高強(qiáng)鋼板的性能指標(biāo)見表4。實(shí)施例15:本一鋼多級的熱軋復(fù)相高強(qiáng)鋼板具體生產(chǎn)工藝如下所述。(1)煉鋼和澆鑄:出鋼鋼水化學(xué)成分的重量百分比為:C0.08%,Mn1.80%,S0.006%,P0.012%,Si1.0%,Als0.060%,Cr0.80%,Ti0.035%,Mo0.2%,N0.006%,其余為鐵和不可避免的雜質(zhì),澆鑄步驟中,鋼水過熱度為25℃;應(yīng)用動態(tài)輕壓下,結(jié)晶器液面波動穩(wěn)定控制在±2mm內(nèi)。(2)加熱工序:板坯加熱至1250~1270℃,保溫2.5h,爐后除鱗溫度1145℃,板坯頭尾溫差≤20℃。(3)熱軋工序:精軋開軋溫度1090±10℃,終軋溫度為870±10℃,軋制鋼板厚度為6.0mm。(4)冷卻工序:采用“U”型冷卻控制,頭20米+20℃,尾部60米+30℃。(5)卷取工序:卷取溫度為550±10℃,卷取單位張力采用38N/mm2,張力分配為30%,熱卷在芯軸停留1.5min后進(jìn)行卸卷。(6)退火工序:退火溫度為700℃,在該溫度保溫7h,然后空冷室溫。(7)酸洗工序:酸洗速度為80m/min。本實(shí)施例所得金相組織為鐵素體-貝氏體-少量殘余奧氏體,復(fù)相高強(qiáng)鋼板的性能指標(biāo)見表4。實(shí)施例16-19:本一鋼多級的熱軋復(fù)相高強(qiáng)鋼板具體生產(chǎn)工藝如下所述。除步驟(6)退火工序之外,其余同實(shí)施例14;步驟(6)退火工序的具體工藝見表4。表3:實(shí)施例16-19的退火工藝實(shí)施例16實(shí)施例17實(shí)施例18實(shí)施例19退火溫度/℃750730700750保溫時間/h4834冷卻方式出爐空冷出爐空冷隨爐冷卻隨爐冷卻實(shí)施例16-19所得金相組織為鐵素體-貝氏體-少量殘余奧氏體,復(fù)相高強(qiáng)鋼板的性能指標(biāo)見表4。實(shí)施例20:本一鋼多級的熱軋復(fù)相高強(qiáng)鋼板具體生產(chǎn)工藝如下所述。(1)煉鋼和澆鑄工序:出鋼鋼水化學(xué)成分的重量百分比為:C0.08%,Mn1.80%,S0.010%,P0.018%,Si1.0%,Als0.045%,Cr0.80%,Ti0.04%,Mo0.3%,N0.006%,其余為鐵和不可避免的雜質(zhì),澆鑄步驟中,鋼水過熱度為20℃;應(yīng)用動態(tài)輕壓下,結(jié)晶器液面波動穩(wěn)定控制在±2mm內(nèi)。(2)加熱工序:板坯加熱至1200~1230℃,保溫2.8h,爐后除鱗溫度1135℃,板坯頭尾溫差≤20℃。(3)熱軋工序:精軋開軋溫度1090±10℃,終軋溫度為870±10℃,軋制鋼板厚度為10.0mm。(4)冷卻工序:采用“U”型冷卻控制,頭25米+15℃,尾部50米+20℃。(5)卷取工序:卷取溫度為510±10℃,卷取單位張力采用38N/mm2,張力分配為35%,熱卷在芯軸停留1.5min后進(jìn)行卸卷。(6)退火工序:退火溫度為650℃,在該溫度保溫6h,然后爐冷至室溫。(7)酸洗工序:酸洗速度為80m/min。本實(shí)施例所得金相組織為鐵素體-貝氏體-少量殘余奧氏體,典型金相組織見圖4,復(fù)相高強(qiáng)鋼板的性能指標(biāo)見表4。實(shí)施例21:本一鋼多級的熱軋復(fù)相高強(qiáng)鋼板具體生產(chǎn)工藝如下所述。(1)煉鋼和澆鑄:出鋼鋼水化學(xué)成分的重量百分比為:C0.12%,Mn2.0%,S0.015%,P0.025%,Si0.7%,Als0.02%,Cr0.60%,Ti0.03%,Mo0.10%,N0.005%,其余為鐵和不可避免的雜質(zhì),澆鑄步驟中,鋼水過熱度為30℃;應(yīng)用動態(tài)輕壓下,結(jié)晶器液面波動穩(wěn)定控制在±2mm內(nèi)。(2)加熱工序:板坯加熱至1240~1270℃,保溫3.0h,爐后除鱗溫度1130℃,板坯頭尾溫差≤15℃。(3)熱軋工序:精軋開軋溫度1040±10℃,終軋溫度為810±10℃,軋制鋼板厚度為12.0mm。(4)冷卻工序:采用“U”型冷卻控制,頭30米+30℃,尾部40米+20℃。(5)卷取工序:卷取溫度為650±10℃,卷取單位張力采用35N/mm2,張力分配為40%,熱卷在芯軸停留0.5min后進(jìn)行卸卷。(6)退火工序:退火溫度為660℃,在該溫度保溫8h,然后爐冷至室溫。(7)酸洗工序:酸洗速度為80m/min。本實(shí)施例所得金相組織為鐵素體-貝氏體-少量殘余奧氏體,復(fù)相高強(qiáng)鋼板的性能指標(biāo)見表4。實(shí)施例22:本一鋼多級的熱軋復(fù)相高強(qiáng)鋼板具體生產(chǎn)工藝如下所述。除步驟(6)退火工序之外,其余同實(shí)施例20;步驟(6)退火工序的具體工藝為:退火溫度為700℃,在該溫度保溫2h,然后爐冷至室溫。本實(shí)施例所得金相組織為鐵素體-貝氏體-少量殘余奧氏體,復(fù)相高強(qiáng)鋼板的性能指標(biāo)見表4。實(shí)施例23:本一鋼多級的熱軋復(fù)相高強(qiáng)鋼板具體生產(chǎn)工藝如下所述。(1)煉鋼和澆鑄:出鋼鋼水化學(xué)成分的重量百分比為:C0.15%,Mn3.0%,S0.006%,P0.020%,Si0.5%,Als0.045%,Cr0.4%,Ti0.01%,Mo0.15%,N0.007%,其余為鐵和不可避免的雜質(zhì),澆鑄步驟中,鋼水過熱度為35℃;應(yīng)用動態(tài)輕壓下,結(jié)晶器液面波動穩(wěn)定控制在±2mm內(nèi)。(2)加熱工序:板坯加熱至1220~1250℃,保溫3.0h,爐后除鱗溫度1145℃,板坯頭尾溫差≤20℃。(3)熱軋工序:精軋開軋溫度1070±10℃,終軋溫度為860±10℃,軋制鋼板厚度為9.5mm。(4)冷卻工序:采用“U”型冷卻控制,頭25米+15℃,尾部60米+35℃。(5)卷取工序:卷取溫度為670±10℃,卷取單位張力采用35N/mm2,張力分配為25%,熱卷在芯軸停留1.0min后進(jìn)行卸卷。(6)退火工序:退火溫度為620℃,在該溫度保溫8h,然后爐冷至室溫。(7)酸洗工序:酸洗速度為80m/min。本實(shí)施例所得金相組織為鐵素體-貝氏體-少量殘余奧氏體,典型金相組織見圖5,復(fù)相高強(qiáng)鋼板的性能指標(biāo)見表4。實(shí)施例24-25:本一鋼多級的熱軋復(fù)相高強(qiáng)鋼板具體生產(chǎn)工藝如下所述。除步驟(6)退火工序之外,其余同實(shí)施例23。實(shí)施例24的步驟(6)退火工序的具體工藝為:退火溫度為600℃,在該溫度保溫5h,然后爐冷至室溫。實(shí)施例25的步驟(6)退火工序的具體工藝為:退火溫度為650℃,在該溫度保溫2h,然后爐冷至室溫。實(shí)施例24-25所得金相組織為鐵素體-貝氏體-少量殘余奧氏體,復(fù)相高強(qiáng)鋼板的性能指標(biāo)見表4。表4:各實(shí)施例所得復(fù)相高強(qiáng)鋼板的性能指標(biāo)當(dāng)前第1頁1 2 3