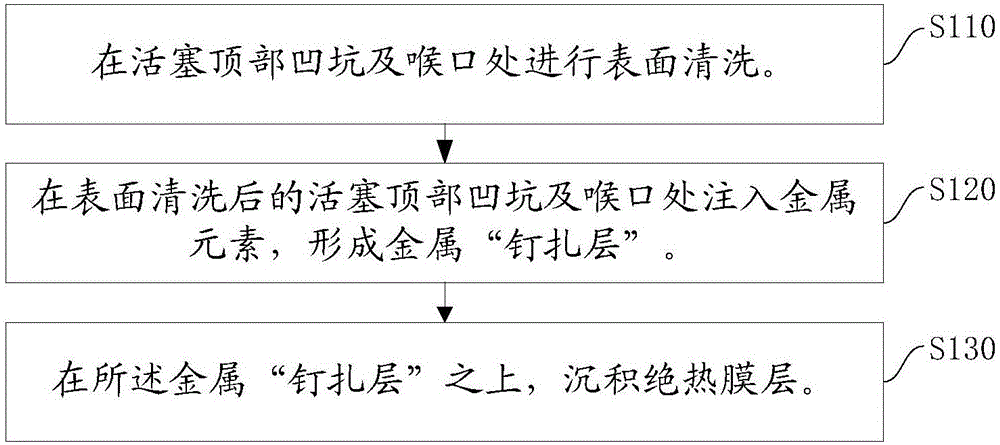
本發(fā)明涉及材料表面改性
技術(shù)領(lǐng)域:
,尤其涉及一種解決發(fā)動機活塞拉缸的方法。
背景技術(shù):
:活塞被稱為內(nèi)燃機的“心臟”,承受交變的機械負荷和熱負荷,是內(nèi)燃機中工作條件最惡劣的關(guān)鍵零部件之一,對其材料具有特殊的要求:熱膨脹系數(shù)小、密度小、傳熱導電性好、耐蝕性及耐磨性等。目前,國內(nèi)外車輛發(fā)動機均向高速和高功率密度的方向發(fā)展,其中,卡車柴油機的升功率提升了三倍,軍車柴油機的升功率提升速度更高。隨著內(nèi)燃機的大幅度強化,缸內(nèi)燃氣的最大爆發(fā)壓力逐漸升高,同時,缸內(nèi)燃氣溫度也大幅度升高,導致和燃氣直接接觸的活塞熱負荷迅速增加,即隨著發(fā)動機強化程度的提高,活塞的溫度也逐漸增高,而過高的溫度使得活塞材料強度降低,進而導致活塞的高溫強度和承載能力降低。高溫和高負荷等惡劣的工作環(huán)境,使得活塞成為疲勞失效較多的發(fā)動機零價之一,其可靠性成為制約整個發(fā)動機安全運行的重要目標。新材料技術(shù)是我國乃至全世界都非常重視的研究領(lǐng)域之一,從我國“863”計劃設(shè)立起,新材料技術(shù)就是其中的一個重要的研究領(lǐng)域,而材料表面改性技術(shù)是新材料技術(shù)研究的一個重要方向。通過合適的表面改性處理,可以顯著提高材料表面的多種性能,例如材料表面的光潔度、硬度、抗磨性、抗氧化、耐溫以及抗腐蝕等性能,從而顯著提高材料的使用壽命和工作效率,實現(xiàn)節(jié)約原材料、降低能源消耗等目的。技術(shù)實現(xiàn)要素:隨著內(nèi)燃機的大幅度強化,缸內(nèi)燃氣的最大爆發(fā)壓力逐漸升高,以及缸內(nèi)溫度的不斷升高,對活塞相關(guān)聯(lián)的關(guān)鍵部件穩(wěn)定、可靠性方面的要求越來越高,研制出高壽命、高穩(wěn)定性的活塞對內(nèi)燃機的發(fā)展顯得非常重要。鑒于此,為解決目前發(fā)動機存在的活塞拉缸的問題,本發(fā)明實施例提供了一種解決發(fā)動機活塞拉缸的方法,在活塞頂部凹坑及喉口處沉積絕熱膜層,用以阻止燃燒室熱量向活塞下的關(guān)鍵部件的傳導,解決活塞拉缸的問題。優(yōu)選地,所述在活塞頂部凹坑及喉口處沉積絕熱膜層包括:在活塞頂部凹坑及喉口處進行表面清洗;在表面清洗后的活塞頂部凹坑及喉口處注入金屬元素,形成金屬“釘扎層”;在所述金屬“釘扎層”之上,沉積絕熱膜層。進一步優(yōu)選地,利用金屬離子束對所述活塞頂部凹坑及喉口處進行表面清洗。進一步優(yōu)選地,金屬離子束所用金屬元素為Ti、Ni或Al。進一步優(yōu)選地,所述金屬元素為Ti、Ni或Al。進一步優(yōu)選地,所述絕熱膜層為Al2O3膜或TiC-DLC膜。進一步優(yōu)選地,所述絕熱膜層為TiC-DLC膜。進一步優(yōu)選地,注入金屬元素時的電壓為4-15V;注入金屬元素時的束流強度為1-15mA;注入金屬元素的劑量為1×1014-1×1017/cm2;注入金屬元素時的深度為70-120nm。進一步優(yōu)選地,沉積絕緣熱膜層時采用的是磁過濾陰極真空弧系統(tǒng)。進一步優(yōu)選地,所述絕熱膜層的厚度為20-30μm。相對于現(xiàn)有技術(shù),本發(fā)明實施例具有以下優(yōu)勢:1、在活塞頂部凹坑及喉口處沉積超厚絕熱膜層能夠非常方便的解決因熱量傳遞帶來的活塞部件以下各關(guān)鍵部件因熱膨脹系數(shù)不一致帶來的問題。2、在膜層制備技術(shù)方面:(a)通過對活塞基材進行高能量的金屬元素注入,使基材亞表面原子與注入金屬形成金屬-基材原子混合的“釘扎層”結(jié)構(gòu),這樣形成的“釘扎層”結(jié)構(gòu)與基底層乃至后續(xù)磁過濾沉積出的結(jié)構(gòu)性膜層的結(jié)合力都非常好,從而使其抗剝離強度得以增強;(b)相比磁控濺射、電子束蒸發(fā)等PVD沉積方法,磁過濾電弧沉積設(shè)備原子離化率非常高,大約在90%以上。由于原子離化率高,可使等離子體密度增加,成膜時大顆粒減少,有利于提高薄膜硬度、耐溫性、耐磨性、致密性以及膜基結(jié)合力等。附圖說明構(gòu)成本發(fā)明實施例部分的附圖是用來提供對本發(fā)明實施例的進一步理解,本發(fā)明的示意性實施例及其說明用于解釋本發(fā)明,并不構(gòu)成對本發(fā)明的限制。圖1為本發(fā)明實施例提供的在活塞頂部凹坑及喉口處沉積絕熱膜層的流程示意圖;圖2為本發(fā)明實施例提供的絕熱膜層結(jié)構(gòu)示意圖;圖3(a)為本發(fā)明實施例提供的Al2O3絕熱膜層實物圖;圖3(b)為本發(fā)明實施例提供的TiC-DLC絕熱膜層實物圖;圖4(a)為本發(fā)明實施例提供的Al2O3絕熱膜表面金相顯微圖;圖4(b)為本發(fā)明實施例提供的TiC-DLC絕熱膜表面金相顯微圖;圖5為本發(fā)明實施例提供的Al2O3和TiC-DLC絕熱膜熱循環(huán)測試時的熱電偶位置;圖6為本發(fā)明實施例提供的Al2O3、TiC-DLC絕熱膜與磷化活塞測溫點處加熱到100℃-250℃時所需時間對比圖;附圖標記說明:200—活塞基材;210—金屬清洗層;220—金屬“釘扎層”;230—絕熱膜層;具體實施方式下面通過附圖和實施例,對本發(fā)明的技術(shù)方案做進一步的詳細描述。應(yīng)當理解為這些實施例僅僅是用于更詳細具體地說明,但并不意于限制本發(fā)明的保護范圍。此外,還需要說明的是,本部分對本發(fā)明實驗中所使用到的材料以及試驗方法進行一般性的描述。雖然為實現(xiàn)本發(fā)明目的所使用的許多材料和操作方法是本領(lǐng)域公知的,但是本發(fā)明仍然在此作盡可能詳細描述。本領(lǐng)域技術(shù)人員清楚,在上下文中,如果未特別說明,本發(fā)明所用材料和操作方法是本領(lǐng)域公知的。實施例一為解決目前發(fā)動機存在的活塞拉缸的問題,本實施例提供了一種解決發(fā)動機活塞拉缸的方法,在活塞頂部凹坑及喉口處沉積絕熱膜層,用以阻止燃燒室熱量向活塞下的關(guān)鍵部件的傳導,解決活塞拉缸的問題。圖1為本發(fā)明實施例提供的在活塞頂部凹坑及喉口處沉積絕熱膜層的流程示意圖,圖2為本發(fā)明實施例提供的絕熱膜層結(jié)構(gòu)示意圖。如圖1所示,所述方法包括:S110,在活塞頂部凹坑及喉口處進行表面清洗。在一個示例中,利用金屬離子束對所述活塞頂部凹坑及喉口處進行表面清洗,形成基底層。優(yōu)選地,采用磁過濾陰極真空弧(filteredcathodicvacuumarc,F(xiàn)CVA)系統(tǒng)在活塞頂部凹坑及喉口處進行金屬離子束表面清洗。如圖2所示,在活塞基材200處進行表面清洗,形成基底層,即金屬清洗層210。本步驟可選地,表面清洗時所用金屬元素為Ti、Ni或Al,能更好的與活塞基材結(jié)合。需要說明的是,在清洗過程中,F(xiàn)CVA系統(tǒng)的負壓在400-1000V,清洗時的金屬離子束流強度為300-1000mA。S120,在表面清洗后的活塞頂部凹坑及喉口處注入金屬元素,形成金屬“釘扎層”.在一個示例中,利用金屬蒸汽真空弧(Metalvaporvacuumarc,MVVA)離子源向基底層注入金屬元素,形成金屬“釘扎層”。即,利用高能金屬離子注入基底,能夠形成金屬和基底材料的混合層,提高其表面后續(xù)膜層與基底的結(jié)合力。如圖2所示,在金屬清洗層210上注入金屬元素,形成金屬“釘扎層”220。需要指出的是,注入的金屬元素可采用Ti、Ni或Al。作為一種可選實施方式,注入金屬元素的過程中,注入電壓為4-15kV,束流強度為1-15mA,注入劑量為1×1014-1×1017/cm2,注入深度為70-120nm。S130,在所述金屬“釘扎層”之上,沉積絕熱膜層。在一個示例中,采用磁過濾陰極真空弧(filteredcathodicvacuumarc,F(xiàn)CVA)系統(tǒng)在基底“釘扎層”表面,磁過濾沉積,同時通入反應(yīng)氣體,得到絕熱膜層。如圖2所示,在金屬“釘扎層”220上面沉積得到絕熱膜層230。在本步驟中,可選地,絕熱膜層為Al2O3膜或TiC摻雜DLC(類金剛)薄膜等,即絕熱膜可以為Al2O3膜或TiC-DLC膜等,且絕熱膜層的厚度為20-30μm。進一步可選的,絕熱膜層為TiC-DLC膜。本實施例提供的解決發(fā)動機活塞拉缸的方法,主要是通過FCVA系統(tǒng)利用金屬離子束Ti、Al或Ni中的一種元素對活塞頂部凹坑及喉口處進行表面清洗,之后通過(MEVVA系統(tǒng)注入的Ti、Al或Ni中的一種元素在基底上制備金屬“釘扎層”,最后通過FCVA系統(tǒng)沉積超厚絕熱膜層構(gòu)成了整個膜層的主體結(jié)構(gòu),同時厚度在20-30μm;該結(jié)構(gòu)膜層利用金屬離子注入系統(tǒng)形成了金屬混合“釘扎層”,使后續(xù)沉積膜層與基底材料有著非常好的結(jié)合強度;同時選擇了絕熱效果好的膜層,使其沉積在活塞頂部凹坑及喉口超厚具有明顯的隔熱效果,同時阻止了燃燒室的相對高溫向活塞頂部以下關(guān)鍵部件的熱傳導,明顯減小其熱膨脹量,同時可直接避免因膨脹系數(shù)不一致帶來的各種問題。為更好的理解本發(fā)明提供的技術(shù)方案,下面,結(jié)合附圖說明,以在塞頂部凹坑及喉口處沉積Al2O3以及TiC-DLC兩種絕熱膜層為例,詳細的介紹本發(fā)明的基于離子束技術(shù)解決發(fā)動機活塞拉缸的方法,并對沉積的兩種絕熱膜層進行性能分析。實施例二在活塞頂部凹坑及喉口處沉積Al2O3絕熱膜層。實施步驟如下:S110,金屬清洗層210制備Al沉積:將活塞基材200固定于樣品臺,轉(zhuǎn)動樣品至沉積靶位,開始沉積,即對活塞基材200進行表面清洗,獲得金屬清洗層210。沉積弧源為純度99%的Al弧源,沉積條件為:真空度1×10-3-6×10-3Pa,沉積弧流:100-120A,磁場電流:1.4-2.4A,弧流:380-440mA,負壓:400V-1000V,占空比50%-100%,沉積時間3-60S,磁過濾管道為90°過濾。S120,金屬“釘扎層“220制備:注入:轉(zhuǎn)動至注入靶位開始注入,即在金屬清洗層210之上注入金屬離子,獲得金屬“釘扎層”220。注入離子源為純度99.9%的純Ti,注入條件為:真空度1×10-3-6×10-3Pa,注入弧壓:50-70V,注入電壓:6-10kV,弧流:3-6mA,注入劑量1×1014-1×1015Ti/cm2。S130,Al2O3超厚絕熱層230制備:Al2O3膜沉積:在220之上沉積Al2O3膜230,沉積條件為:沉積弧源為純度99%的Al弧源,真空度:1×10-2-6×10-2Pa,沉積弧流:100-120A,磁場電流:1.4-2.4A,弧流:180-240mA,負壓:150V-350V,占空比50%-100%,氧氣進氣量20-100sccm,沉積厚度為20-30μm。圖3(a)為本實施例制備的Al2O3絕熱膜層實物圖。后續(xù)對其進行性能測試和分析。實施例三在活塞頂部凹坑及喉口處沉積TiC-DLC絕熱層。實施步驟如下:S110,金屬清洗層210制備:Ti沉積:將活塞基材200固定于樣品臺,轉(zhuǎn)動樣品至沉積靶位開始沉積。沉積弧源為純度99%的Ti弧源,沉積條件為:真空度1×10-3-6×10-3Pa,沉積弧流:100-110A,磁場電流:1.4-2.4A,弧流:380-440mA,負壓:-400V-1000V,占空比50%-100%,沉積時間3-60S,磁過濾管道為90°過濾。S120,金屬“釘扎層”220制備:注入:轉(zhuǎn)動至注入靶位開始注入。注入離子源為純度99.9%的純Ti,注入條件為:真空度1×10-3-6×10-3Pa,注入弧壓:50-70V,注入電壓:6-10kV,弧流:3-6mA,注入劑量1×1014-1×1015Ti/cm2。S130,TiC-DLC超厚絕熱層230制備:TiC-DLC膜沉積:在220之上沉積TiC-DLC膜230,沉積條件為:沉積弧源為純度99%的Ti弧源,真空度:1×10-2-6×10-2Pa,沉積弧流:100-120A,磁場電流:3.4-5.0A,弧流:180-240mA,負壓:150V-350V,占空比10%-100%,乙炔氣進氣量200-300sccm,沉積厚度為20-30μm。圖3(b)為本實施例制備的TiC-DLC絕熱膜層實物圖,后續(xù)對其進行性能測試和分析。為對超厚絕熱層性能進行說明,這里可參照圖圖4(a)和圖4(b)、圖5及圖6,其分別為Al2O3絕熱膜層和TiC-DLC絕熱膜層的表面光學形貌圖、活塞截面及熱電偶安裝位置圖,以及500次熱沖擊循環(huán)試驗結(jié)果示意圖,需要說明的是,作為對比,對活塞進行磷化處理,圖6中還包括磷化活塞測量點的熱沖擊循環(huán)試驗結(jié)果。并對Al2O3、TiC-DLC超厚絕熱膜層進行硬度測試,測試過程中,其載荷為100g,其總體的顯微硬度結(jié)果如表1所示。表1實施例二和實施例三提供的Al2O3和TiC-DLC絕熱膜的顯微硬度值測試點12345平均硬度Al2O3硬度/HV183614671776168016201675.8TiC-DLC硬度/HV212322002100209023232167.2結(jié)合表1可知,Al2O3超厚絕熱層顯微硬度可達1675.8HV,TiC-DLC膜層的顯微硬度可達2167.2HV。圖6為超厚絕熱層500次熱沖擊循環(huán)試驗結(jié)果示意圖,本試驗方法按照Q/LE107.093-2010《活塞熱疲勞試驗規(guī)范》進行。熱電偶安裝位置及測量點的分布見圖5,其中,A點為熱偶安裝位置及測量點。從試驗分析結(jié)果可以看出:(1)燃燒室表面經(jīng)過物理氣相沉積處理的G4700B活塞經(jīng)過500次熱沖擊循環(huán)試驗后,滲透層未出現(xiàn)脫落現(xiàn)象;(2)燃燒室表面物理氣相沉積處理的活塞與表面理化處理的活塞在加熱100℃-250℃同一溫度段下,在加熱同一段溫度下,燃燒室表面經(jīng)過物理氣相沉積TiC-DLC處理的活塞比表面磷化的活塞加熱時間均長40S以上,沉積超厚Al2O3膜層的活塞加熱時間比磷化活塞延時20S,說明物理氣相沉積TiC-DLC和Al2O3能夠起到很好的隔熱效果。本發(fā)明提供的解決發(fā)動機活塞拉缸的方法,主要是通過FCVA系統(tǒng)利用金屬離子束對活塞頂部凹坑及喉口處進行表面清洗,之后通過MEVVA系統(tǒng)注入金屬元素在基底上制備金屬“釘扎層”,使后續(xù)沉積膜層與基底材料有著非常好的結(jié)合強度,從而使其抗剝離強度得以增強;此外,沉積膜層具有明顯的隔熱效果,阻止了燃燒室的相對高溫向活塞頂部以下關(guān)鍵部件的熱傳導,明顯減小其熱膨脹量,同時可直接避免因膨脹系數(shù)不一致帶來的各種問題。需要說明的是,盡管本發(fā)明已進行了一定程度的描述,明顯地,在不脫離本發(fā)明的精神和范圍的條件下,可進行各個條件的適當變化。可以理解為本發(fā)明不限于所述實施方案,而歸于權(quán)利要求的范圍,其包括所述每個因素的等同替換。以上所述的具體實施方式,對本發(fā)明的目的、技術(shù)方案和有益效果進行了進一步詳細說明,所應(yīng)理解的是,以上所述僅為本發(fā)明的具體實施方式而已,并不用于限定本發(fā)明的保護范圍,凡在本發(fā)明的精神和原則之內(nèi),所做的任何修改、等同替換、改進等,均應(yīng)包含在本發(fā)明的保護范圍之內(nèi)。當前第1頁1 2 3