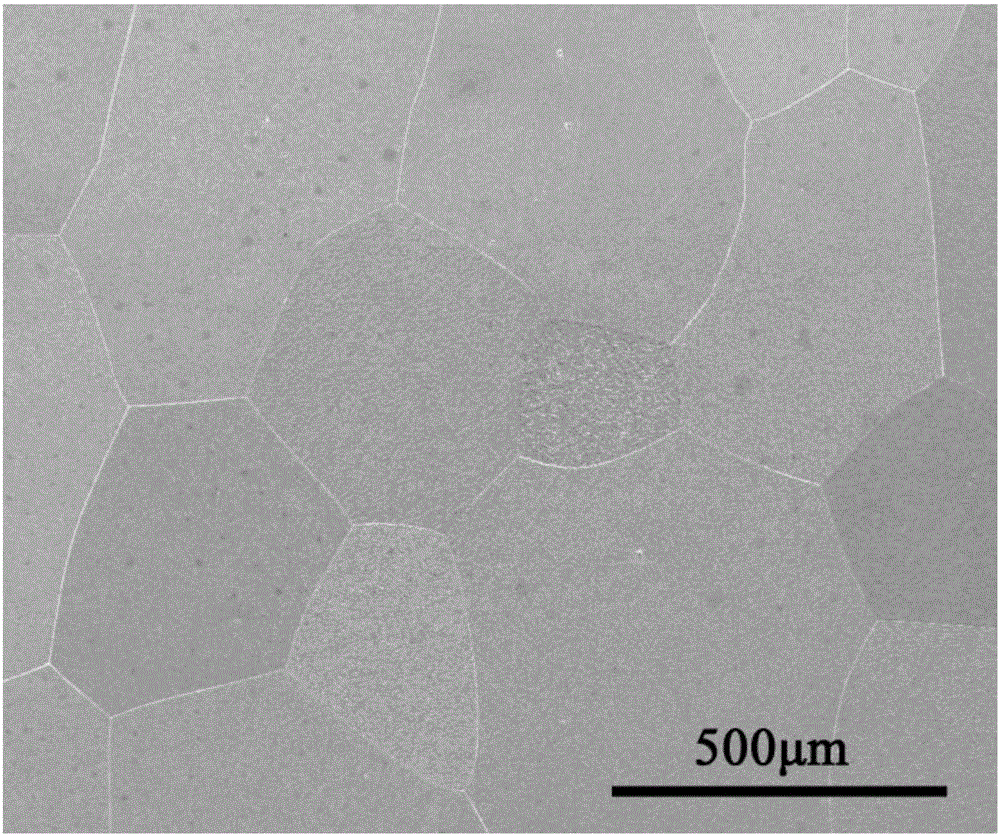
本發(fā)明涉及一種高致密、超高比重鎢合金的非自耗電弧熔煉制備方法。
背景技術(shù):
:鎢是一種非常重要的有色金屬,它具有高熔點(diǎn)、高密度、低熱膨脹系數(shù)、優(yōu)良的抗腐蝕性等一系列特性,通常被用于真空燈絲、焊接電極、配重材料、屏蔽材料、軍用穿甲材料及火箭噴管等,在電子工業(yè)、工程機(jī)械、醫(yī)療器械、武器裝備、航空航天等領(lǐng)域,其應(yīng)用范圍廣闊。鎢裸露于空氣中時(shí),在400℃發(fā)生輕微氧化,500~600℃迅速氧化成WO3,而WO3在高于800℃則會(huì)顯著升華,因此在鎢制備過程中要保證真空環(huán)境或惰性氣體保護(hù)。鎢的熔點(diǎn)為3410±20℃,是熔點(diǎn)最高的難熔金屬。由于熔點(diǎn)太高,造成高致密鎢及高比重致密鎢合金的制備非常困難,鎢合金的制備手段有:自耗、非自耗電弧熔煉,電子束熔煉,粉末冶金等。如“一種高鎢含量鎢合金的電弧熔煉方法”(申請公開號:CN102492863A)中提到鎢粉松裝密度低,電弧熔煉過程中極易被電弧壓力吹飛,采用傳統(tǒng)方法很難獲得鎢含量高于10%的均勻鎢合金,且經(jīng)其技術(shù)改進(jìn)后鎢含量高達(dá)40%的合金也已很難成功制備;同時(shí)由于自耗電弧熔煉的電極制備復(fù)雜增加了加工難度和電子束熔煉效率低、成本高等問題存在,限制了相關(guān)技術(shù)推廣。目前,一般在制備塊狀金屬鎢或高比重鎢合金時(shí)普遍采用粉末冶金方法(低于2500℃),由于鎢的熔點(diǎn)實(shí)在太高,目前所使用模具、坩堝、壓頭等材料的高溫高強(qiáng)極限性能很難超過2500℃(石墨制品可耐3000℃高溫,但強(qiáng)度不足、壽命短且會(huì)引入碳化物雜質(zhì)),制得的高比重鎢合金鎢含量很難超過98%(可對照表1),往往通過添加低熔點(diǎn)、低密度的合金元素來提高致密性,限制了其密度(或比重)的進(jìn)一步提高;本發(fā)明所用非自耗電弧熔煉技術(shù)是在確保加工效率情況下,制備高致密性、高比重鎢合金的的重要技術(shù)手段。技術(shù)實(shí)現(xiàn)要素:本發(fā)明所要解決的技術(shù)問題是:針對上述的技術(shù)現(xiàn)狀,提供一種高致密、超高比重鎢合金的非自耗電弧熔煉制備方法,該方法可以制備致密度高(98.1%~99.2%)的超高比重鎢合金(鎢比重含量達(dá)99.7%~99.9%,比重最高可達(dá)19.11)。本發(fā)明解決其技術(shù)問題采用以下的技術(shù)方案:本發(fā)明提供的鎢合金的非自耗電弧熔煉制備方法,包括以下步驟:(1)鎢粉的初步凈化:采用1~3mol/L稀鹽酸酸洗、電阻率≥2.0×106Ω·cm去離子水清洗和冷凍干燥的工藝,實(shí)現(xiàn)對鎢比重含量為≥98.5%的鎢粉的初步凈化,得到初步凈化的鎢粉;(2)冷壓成型及預(yù)制塊體制備:將初步凈化的鎢粉放入冷壓模具中,采用壓片機(jī)對其進(jìn)行冷壓成型,得到塊狀生坯;后經(jīng)高真空燒結(jié),獲得預(yù)制塊體;(3)抽真空、通氬氣:將預(yù)制塊體放入非自耗電弧熔煉爐結(jié)晶器熔池中,關(guān)閉爐門抽真空,當(dāng)真空度達(dá)到≤4Pa時(shí)往爐內(nèi)通氬氣,使?fàn)t內(nèi)壓強(qiáng)相對大氣壓強(qiáng)達(dá)到-0.04MPa,以防止樣品氧化和保證起弧正常;(4)電弧熔煉:引弧并調(diào)節(jié)熔煉功率對預(yù)制塊體進(jìn)行多次熔煉,最后一次重熔后,將預(yù)制塊體充分、快速冷卻至室溫再出爐,獲得高致密、超高比重鎢合金。所述鎢粉的初步凈化的過程中,鎢粉經(jīng)酸洗和攪拌30~60min后,先除去上層清液,再用去離子水在攪拌下進(jìn)行清洗(pH≥4時(shí)為止),然后使用冷凍干燥設(shè)備在-10℃以下對鎢粉冷凍干燥12~24h。所述的冷壓成型,其工藝參數(shù)是:壓強(qiáng)為200~1000MPa,壓模時(shí)間為3~5min,環(huán)境溫度為室溫(25℃左右)。所述的高真空燒結(jié)采用熱壓燒結(jié),其工藝參數(shù)為:真空度≥10-3Pa,熱壓燒結(jié)壓力為30~200MPa,溫度1500~2000℃,保壓時(shí)間30~120min。所述的高真空燒結(jié)采用放電等離子體燒結(jié),其工藝參數(shù)為:真空度≥10-3Pa,燒結(jié)壓力10~80MPa,溫度1500~2000℃,保壓時(shí)間20~30min。所述電弧熔煉的過程中,引弧前應(yīng)檢查電弧爐冷卻循環(huán)水系統(tǒng)是否正常工作,確定循環(huán)水壓強(qiáng)為≥0.08MPa,保證設(shè)備正常運(yùn)行和熔煉后設(shè)備及樣品的充分、快速冷卻。所述電弧熔煉的過程中,應(yīng)調(diào)整非自耗電弧熔煉爐運(yùn)行參數(shù)引弧,并調(diào)整參數(shù)對預(yù)制塊體預(yù)熱、預(yù)熔和熔煉,預(yù)熱應(yīng)使樣品達(dá)到紅熱狀態(tài),預(yù)熔應(yīng)使樣品達(dá)到白熱狀態(tài),熔煉應(yīng)使樣品充分熔化,然后迅速滅弧,使樣品充分、快速冷卻,完成初步熔煉。本發(fā)明方法采用3~5次重熔,每次重熔后須再次預(yù)熔,且每次重熔后須翻轉(zhuǎn)試樣。所述電弧熔煉過程中,每次擊發(fā)電弧熔煉后必須冷卻充分,以保證電弧爐及樣品的充分、快速冷卻。本發(fā)明提供的上述鎢合金的非自耗電弧熔煉制備方法,所制備的高致密、超高比重鎢合金,其技術(shù)參數(shù)為:致密度98.1%~99.2%,鎢比重含量99.7%~99.9%,比重18.89~19.11。本發(fā)明制備的鎢合金,用于制備電子工業(yè)、核工業(yè)、航空航天及動(dòng)高壓物理領(lǐng)域中的元件。本發(fā)明與現(xiàn)有技術(shù)相比具有以下主要優(yōu)點(diǎn):1.涉及鎢粉凈化、預(yù)制塊體和合金熔煉三個(gè)部分,其工藝過程簡單,且實(shí)際操作中所使用原料(鎢粉)、試劑、用具等廉價(jià)易得,同時(shí)實(shí)驗(yàn)條件容易實(shí)現(xiàn),再現(xiàn)性強(qiáng)。2.采用先冷壓成型得到塊狀生坯,再經(jīng)高真空燒結(jié)的方式獲得預(yù)制塊體,對預(yù)制塊體進(jìn)行電弧熔煉的方法,很好解決了鎢粉松裝密度低,易被電弧壓力吹飛的問題;同時(shí)由于高真空燒結(jié)工藝可使預(yù)制塊體具備較高致密度,明顯降低了鎢合金的電弧熔煉難度和氣孔率。3.所采用的非自耗電弧熔煉技術(shù),其電極可重復(fù)使用,具有簡單易操作、加工效率高等特點(diǎn)。4.在保證高致密度(致密度為98.1%~99.2%)的情況下所制得的高致密、超高比重鎢合金,其鎢比重含量達(dá)到99.7%~99.9%,比重最高達(dá)19.11,參見表1,遠(yuǎn)高于市面上出現(xiàn)的93W、97W的鎢比重含量(93%、97%)和比重(17.6、18.5),可進(jìn)一步提升高鎢合金在射線防護(hù)、武器穿甲、及動(dòng)高壓物理中的應(yīng)用性能。表1中“超高比重鎢合金”為本發(fā)明所制鎢合金,通過對比不同國家、不同高鎢合金產(chǎn)品的比重含量及比重,可知本發(fā)明所得鎢合金性能優(yōu)勢明顯。5.所得鎢合金具有一定的提純效果,通過鎢粉初步凈化、高真空燒結(jié)及電弧熔煉協(xié)同凈化的方式進(jìn)行提純,參見表2,可獲得純度要求較高的鎢合金靶材、燈絲等材料,可在電子、能源領(lǐng)域得到廣泛應(yīng)用。由表2可知,本發(fā)明所制鎢合金W元素含量達(dá)99.9%。附圖說明圖1是本發(fā)明的工藝流程圖。由圖1可以看出本發(fā)明工藝過程簡單,易操作。圖2是制備的高致密、超高比重鎢合金微觀形貌圖(經(jīng)一定濃度的鐵氰化鉀金相腐蝕)。由圖2可看出制備所得鎢合金組織均勻、致密、無明顯氣孔存在。具體實(shí)施方式本發(fā)明設(shè)計(jì)使用非自耗電弧熔煉方法,快速制備出高致密、超高比重鎢合金,同時(shí)制備過程中由于電弧熔煉溫度(高于鎢的熔點(diǎn))遠(yuǎn)高于粉末冶金燒結(jié)溫度,真空度較高,樣品中部分原始雜質(zhì)或制備過程中引入、生成的微量雜質(zhì)會(huì)在高溫下得到凈化,具有一定的提純作用。其主要工藝流程如下:首先使用稀鹽酸對鎢粉酸洗,去離子水清洗和冷凍干燥,完成鎢粉的初步凈化;經(jīng)冷壓成型制得塊狀生坯和高真空燒結(jié)獲得預(yù)制塊體,在保證爐內(nèi)真空度(≤4Pa)情況下,通入氬氣,使用非自耗電弧熔煉方法對樣品預(yù)熱、預(yù)熔、熔煉和重熔(3~5次),經(jīng)快速冷卻后獲得致密度高(98.1%~99.2%)的超高比重鎢合金(鎢比重含量最高可達(dá)99.9%,比重最高可達(dá)19.11)。下面結(jié)合實(shí)施例及附圖對本發(fā)明做進(jìn)一步說明,但并不局限于下面所述的內(nèi)容。實(shí)施例1制備致密度為99.2%的超高比重鎢合金(鎢比重含量為99.9%,比重為19.11)。其制備過程依次經(jīng)鎢粉酸洗、清洗、冷凍干燥處理,冷壓成型、高真空燒結(jié)獲得預(yù)制塊體,合金的非自耗電弧熔煉等獲得該鎢合金。其中,非自耗電弧熔煉的工藝過程又包括預(yù)熱、預(yù)熔、熔煉、多次重熔等。其具體步驟如下:1.鎢粉的酸洗、清洗與冷凍干燥處理:使用濃度為3mol/L的稀鹽酸對鎢比重含量占99.0%的鎢粉(粒徑為1~20μm)攪拌酸洗60min,后除去上層清洗液,使用電阻率≥2.0×106Ω·cm的去離子水進(jìn)行清洗至pH≥4為止,后使用冷凍干燥設(shè)備在-10℃以下對清洗后的鎢粉冷凍干燥24h。2.將鎢粉冷壓成型為生坯,經(jīng)高真空燒結(jié)獲得預(yù)制塊體:將步驟1中獲得的鎢粉裝入Cr12MoV模具中,使用壓片機(jī)在室溫(25℃左右)下冷壓成型,壓強(qiáng)為800MPa,壓模時(shí)間5min,獲得塊狀生坯;之后經(jīng)過高真空熱壓燒結(jié),真空度為10-3Pa,壓力為100MPa,溫度為1800℃,保壓時(shí)間為1h,獲得預(yù)制塊體。3.開通快速冷卻循環(huán)水,抽真空、通氬氣,做好非自耗電弧熔煉前的準(zhǔn)備工作:開通快速冷卻循環(huán)水,保證水壓≥0.08MPa,并將步驟2中獲得的預(yù)制塊體放入ACM-SO1非自耗熔煉爐中的結(jié)晶器熔池中,關(guān)閉爐門抽真空,當(dāng)真空度≤4Pa時(shí),往爐內(nèi)通氬氣,使?fàn)t內(nèi)壓強(qiáng)相對大氣壓強(qiáng)達(dá)到-0.04MPa(保證起弧正常),做好非自耗電弧熔煉前的準(zhǔn)備工作。4.高致密、超高比重鎢合金的非自耗電弧熔煉過程:將ACM-SO1非自耗電弧熔煉爐運(yùn)行參數(shù)調(diào)至20kV,100mA,引弧并對預(yù)制塊體預(yù)熱120s;而后在20kV,200mA條件下預(yù)熔90s;之后在20kV,250mA下進(jìn)行熔煉,待塊狀鎢坯充分熔化后(觀察鎢粉為液態(tài)時(shí)),迅速滅弧,并使其快速冷卻,完成初步熔煉。之后將試樣翻轉(zhuǎn),在20kV,200mA條件下重新預(yù)熔90s后,迅速在20kV,250mA條件下進(jìn)行5次重熔,且每次重熔冷卻后均需重新預(yù)熔和翻轉(zhuǎn)試樣,最后一次重熔后,待樣品冷卻至室溫(25℃左右)出爐,所得產(chǎn)品為鎢比重含量為99.9%、比重為19.11、致密度為99.2%的高致密超高比重鎢合金。實(shí)施例2制備致密度為98.1%的超高比重鎢合金(鎢比重含量為99.7%,比重為18.89)。其制備過程依次經(jīng)鎢粉酸洗、清洗、冷凍干燥處理,冷壓成型、高真空燒結(jié)獲得預(yù)制塊體,合金的非自耗電弧熔煉等獲得該鎢合金。其中,非自耗電弧熔煉的工藝過程又包括預(yù)熱、預(yù)熔、熔煉、多次重熔等。其具體步驟如下:1.鎢粉的酸洗、清洗與冷凍干燥處理:使用濃度為3mol/L的稀鹽酸對鎢比重含量占98.5%的鎢粉(粒徑為1~20μm)攪拌酸洗30min,后除去上層清洗液,使用電阻率≥2.0×106Ω·cm的去離子水進(jìn)行清洗至pH≥4為止,后使用冷凍干燥設(shè)備在-10℃以下對清洗后的鎢粉冷凍干燥12h。2.將鎢粉冷壓成型為生坯,經(jīng)高真空燒結(jié)獲得預(yù)制塊體:將步驟1中獲得的鎢粉裝入Cr12MoV模具中,使用壓片機(jī)在室溫(25℃左右)下冷壓成型,壓強(qiáng)為1000MPa,壓模時(shí)間3min,獲得塊狀生坯;之后經(jīng)過高真空熱壓燒結(jié),真空度為10-3Pa,壓力為100MPa,溫度為1800℃,保壓時(shí)間為1h,獲得預(yù)制塊體。3.開通快速冷卻循環(huán)水,抽真空、通氬氣,做好非自耗電弧熔煉前的準(zhǔn)備工作:開通快速冷卻循環(huán)水,保證水壓≥0.08MPa,并將步驟2中獲得的預(yù)制塊體放入ACM-SO1非自耗熔煉爐中的結(jié)晶器熔池中,關(guān)閉爐門抽真空,當(dāng)真空度≤4Pa時(shí),往爐內(nèi)通氬氣,使?fàn)t內(nèi)壓強(qiáng)相對大氣壓強(qiáng)達(dá)到-0.04MPa(保證起弧正常),做好非自耗電弧熔煉前的準(zhǔn)備工作。4.高致密、超高比重鎢合金的非自耗電弧熔煉過程:將ACM-SO1非自耗電弧熔煉爐運(yùn)行參數(shù)調(diào)至20kV,100mA,引弧并對預(yù)制塊體預(yù)熱120s;而后在20kV,200mA條件下預(yù)熔90s;之后在20kV,250mA下進(jìn)行熔煉,待塊狀鎢坯充分熔化后(觀察鎢粉為液態(tài)時(shí)),迅速滅弧,并使其快速冷卻,完成初步熔煉。之后將試樣翻轉(zhuǎn),在20kV,200mA條件下重新預(yù)熔90s后,迅速在20kV,250mA條件下進(jìn)行3次重熔,且每次重熔冷卻后均需重新預(yù)熔和翻轉(zhuǎn)試樣,最后一次重熔后,待樣品冷卻至室溫(25℃左右)出爐,所得產(chǎn)品為鎢比重含量為99.7%、比重為18.89、致密度為98.1%的高致密超高比重鎢合金。實(shí)施例3制備致密度為99.0%的超高比重鎢合金(鎢比重含量為99.9%,比重為19.07)。其制備過程依次經(jīng)鎢粉酸洗、清洗、冷凍干燥處理,冷壓成型、高真空燒結(jié)獲得預(yù)制塊體,合金的非自耗電弧熔煉等獲得該鎢合金。其中,非自耗電弧熔煉的工藝過程又包括預(yù)熱、預(yù)熔、熔煉、多次重熔等。其具體步驟如下:1.鎢粉的酸洗、清洗與冷凍干燥處理:使用濃度為1mol/L的稀鹽酸對鎢比重含量占98.5%的鎢粉(粒徑為1~20μm)攪拌酸洗60min,后除去上層清洗液,使用電阻率≥2.0×106Ω·cm的去離子水進(jìn)行清洗至pH≥4為止,后使用冷凍干燥設(shè)備在-10℃以下對清洗后的鎢粉冷凍干燥24h。2.將鎢粉冷壓成型為生坯,經(jīng)高真空燒結(jié)獲得預(yù)制塊體:將步驟1中獲得的鎢粉裝入Cr12MoV模具中,使用壓片機(jī)在室溫(25℃左右)下冷壓成型,壓強(qiáng)為800MPa,壓模時(shí)間5min,獲得塊狀生坯;之后經(jīng)過高真空熱壓燒結(jié),真空度為10-3Pa,壓力為100MPa,溫度為1800℃,保壓時(shí)間為1h,獲得預(yù)制塊體。3.開通快速冷卻循環(huán)水,抽真空、通氬氣,做好非自耗電弧熔煉前的準(zhǔn)備工作:開通快速冷卻循環(huán)水,保證水壓≥0.08MPa,并將步驟2中獲得的預(yù)制塊體放入ACM-SO1非自耗熔煉爐中的結(jié)晶器熔池中,關(guān)閉爐門抽真空,當(dāng)真空度≤4Pa時(shí),往爐內(nèi)通氬氣,使?fàn)t內(nèi)壓強(qiáng)相對大氣壓強(qiáng)達(dá)到-0.04MPa(保證起弧正常),做好非自耗電弧熔煉前的準(zhǔn)備工作。4.高致密、超高比重鎢合金的非自耗電弧熔煉過程:將ACM-SO1非自耗電弧熔煉爐運(yùn)行參數(shù)調(diào)至20kV,100mA,引弧并對預(yù)制塊體預(yù)熱120s;而后在20kV,200mA條件下預(yù)熔90s;之后在20kV,250mA下進(jìn)行熔煉,待塊狀鎢坯充分熔化后(觀察鎢粉為液態(tài)時(shí)),迅速滅弧,并使其快速冷卻,完成初步熔煉。之后將試樣翻轉(zhuǎn),在20kV,200mA條件下重新預(yù)熔90s后,迅速在20kV,250mA條件下進(jìn)行4次重熔,且每次重熔冷卻后均需重新預(yù)熔和翻轉(zhuǎn)試樣,最后一次重熔后,待樣品冷卻至室溫(25℃左右)出爐,所得產(chǎn)品為鎢比重含量為99.9%、比重為19.07、致密度為99.0%的高致密超高比重鎢合金。實(shí)施例4制備致密度為98.5%的超高比重鎢合金(鎢比重含量為99.9%,比重為18.97)。其制備過程依次經(jīng)鎢粉酸洗、清洗、冷凍干燥處理,冷壓成型、高真空燒結(jié)獲得預(yù)制塊體,合金的非自耗電弧熔煉等獲得該鎢合金。其中,非自耗電弧熔煉的工藝過程又包括預(yù)熱、預(yù)熔、熔煉、多次重熔等。其具體步驟如下:1.鎢粉的酸洗、清洗與冷凍干燥處理:使用濃度為3mol/L的稀鹽酸對鎢比重含量占99.5%的鎢粉(粒徑為1~20μm)攪拌酸洗30min,后除去上層清洗液,使用電阻率≥2.0×106Ω·cm的去離子水進(jìn)行清洗至pH≥4為止,后使用冷凍干燥設(shè)備在-10℃以下對清洗后的鎢粉冷凍干燥12h。2.將鎢粉冷壓成型為生坯,經(jīng)高真空燒結(jié)獲得預(yù)制塊體:將步驟1中獲得的鎢粉裝入Cr12MoV模具中,使用壓片機(jī)在室溫(25℃左右)下冷壓成型,壓強(qiáng)為1000MPa,壓模時(shí)間3min,獲得塊狀生坯;之后經(jīng)過高真空熱壓燒結(jié),真空度為10-3Pa,壓力為100MPa,溫度為1500℃,保壓時(shí)間為1h,獲得預(yù)制塊體。3.開通快速冷卻循環(huán)水,抽真空、通氬氣,做好非自耗電弧熔煉前的準(zhǔn)備工作:開通快速冷卻循環(huán)水,保證水壓≥0.08MPa,并將步驟2中獲得的預(yù)制塊體放入ACM-SO1非自耗熔煉爐中的結(jié)晶器熔池中,關(guān)閉爐門抽真空,當(dāng)真空度≤4Pa時(shí),往爐內(nèi)通氬氣,使?fàn)t內(nèi)壓強(qiáng)相對大氣壓強(qiáng)達(dá)到-0.04MPa(保證起弧正常),做好非自耗電弧熔煉前的準(zhǔn)備工作。4.高致密、超高比重鎢合金的非自耗電弧熔煉過程:將ACM-SO1非自耗電弧熔煉爐運(yùn)行參數(shù)調(diào)至20kV,100mA,引弧并對預(yù)制塊體預(yù)熱60s;而后在20kV,200mA條件下預(yù)熔60s;之后在20kV,300mA下進(jìn)行熔煉,待塊狀鎢坯充分熔化后(觀察鎢粉為液態(tài)時(shí)),迅速滅弧,并使其快速冷卻,完成初步熔煉。之后將試樣翻轉(zhuǎn),在20kV,200mA條件下重新預(yù)熔60s后,迅速在20kV,300mA條件下進(jìn)行3次重熔,且每次重熔冷卻后均需重新預(yù)熔和翻轉(zhuǎn)試樣,最后一次重熔后,待樣品冷卻至室溫(25℃左右)出爐,所得產(chǎn)品為鎢比重含量為99.9%、比重為18.97,致密度為98.5%的高致密超高比重鎢合金。實(shí)施例5制備致密度為99.1%的超高比重鎢合金(鎢比重含量為99.9%,比重為19.09)。其制備過程依次經(jīng)鎢粉酸洗、清洗、冷凍干燥處理,冷壓成型、高真空燒結(jié)獲得預(yù)制塊體,合金的非自耗電弧熔煉等獲得該鎢合金。其中,非自耗電弧熔煉的工藝過程又包括預(yù)熱、預(yù)熔、熔煉、多次重熔等。其具體步驟如下:1.鎢粉的酸洗、清洗與冷凍干燥處理:使用濃度為3mol/L的稀鹽酸對鎢比重含量占99.0%的鎢粉(粒徑為1~20μm)攪拌酸洗60min,后除去上層清洗液,使用電阻率≥2.0×106Ω·cm的去離子水進(jìn)行清洗至pH≥4為止,后使用冷凍干燥設(shè)備在-10℃以下對清洗后的鎢粉冷凍干燥12h。2.將鎢粉冷壓成型為生坯,經(jīng)高真空燒結(jié)獲得預(yù)制塊體:將步驟1中獲得的鎢粉裝入Cr12MoV模具中,使用壓片機(jī)在室溫(25℃左右)下冷壓成型,壓強(qiáng)為200MPa,壓模時(shí)間3min,獲得塊狀生坯;之后經(jīng)過高真空熱壓燒結(jié),真空度為10-3Pa,壓力為30MPa,溫度為2000℃,保壓時(shí)間為2h,獲得預(yù)制塊體。3.開通快速冷卻循環(huán)水,抽真空、通氬氣,做好非自耗電弧熔煉前的準(zhǔn)備工作:開通快速冷卻循環(huán)水,保證水壓≥0.08MPa,并將步驟2中獲得的預(yù)制塊體放入ACM-SO1非自耗熔煉爐中的結(jié)晶器熔池中,關(guān)閉爐門抽真空,當(dāng)真空度≤4Pa時(shí),往爐內(nèi)通氬氣,使?fàn)t內(nèi)壓強(qiáng)相對大氣壓強(qiáng)達(dá)到-0.04MPa(保證起弧正常),做好非自耗電弧熔煉前的準(zhǔn)備工作。4.高致密、超高比重鎢合金的非自耗電弧熔煉過程:將ACM-SO1非自耗電弧熔煉爐運(yùn)行參數(shù)調(diào)至20kV,100mA,引弧并對預(yù)制塊體預(yù)熱90s;而后在20kV,200mA條件下預(yù)熔120s;之后在20kV,280mA下進(jìn)行熔煉,待塊狀鎢坯充分熔化后(觀察鎢粉為液態(tài)時(shí)),迅速滅弧,并使其快速冷卻,完成初步熔煉。之后將試樣翻轉(zhuǎn),在20kV,200mA條件下重新預(yù)熔120s后,迅速在20kV,280mA條件下進(jìn)行3次重熔,且每次重熔冷卻后均需重新預(yù)熔和翻轉(zhuǎn)試樣,最后一次重熔后,待樣品冷卻至室溫(25℃左右)出爐,所得產(chǎn)品為鎢比重含量為99.9%、比重為19.09、致密度為99.1%的高致密超高比重鎢合金。實(shí)施例6制備致密度為98.8%的超高比重鎢合金(鎢比重含量為99.9%,比重為19.03)。其制備過程依次經(jīng)鎢粉酸洗、清洗、冷凍干燥處理,冷壓成型、高真空燒結(jié)獲得預(yù)制塊體,合金的非自耗電弧熔煉等獲得該鎢合金。其中,非自耗電弧熔煉的工藝過程又包括預(yù)熱、預(yù)熔、熔煉、多次重熔等。其具體步驟如下:1.鎢粉的酸洗、清洗與冷凍干燥處理:使用濃度為3mol/L的稀鹽酸對鎢比重含量占99.0%的鎢粉(粒徑為1~20μm)攪拌酸洗60min,后除去上層清洗液,使用電阻率≥2.0×106Ω·cm的去離子水進(jìn)行清洗至pH≥4為止,后使用冷凍干燥設(shè)備在-10℃以下對清洗后的鎢粉冷凍干燥12h。2.將鎢粉冷壓成型為生坯,經(jīng)高真空燒結(jié)獲得預(yù)制塊體:將步驟1中獲得的鎢粉裝入Cr12MoV模具中,使用壓片機(jī)在室溫(25℃左右)下冷壓成型,壓強(qiáng)為200MPa,壓模時(shí)間3min,獲得塊狀生坯;之后經(jīng)過高真空熱壓燒結(jié),真空度為10-3Pa,壓力為30MPa,溫度為2000℃,保壓時(shí)間為30min,獲得預(yù)制塊體。3.開通快速冷卻循環(huán)水,抽真空、通氬氣,做好非自耗電弧熔煉前的準(zhǔn)備工作:開通快速冷卻循環(huán)水,保證水壓≥0.08MPa,并將步驟2中獲得的預(yù)制塊體放入ACM-SO1非自耗熔煉爐中的結(jié)晶器熔池中,關(guān)閉爐門抽真空,當(dāng)真空度≤4Pa時(shí),往爐內(nèi)通氬氣,使?fàn)t內(nèi)壓強(qiáng)相對大氣壓強(qiáng)達(dá)到-0.04MPa(保證起弧正常),做好非自耗電弧熔煉前的準(zhǔn)備工作。4.高致密、超高比重鎢合金的非自耗電弧熔煉過程:將ACM-SO1非自耗電弧熔煉爐運(yùn)行參數(shù)調(diào)至20kV,100mA,引弧并對預(yù)制塊體預(yù)熱90s;而后在20kV,200mA條件下預(yù)熔120s;之后在20kV,280mA下進(jìn)行熔煉,待塊狀鎢坯充分熔化后(觀察鎢粉為液態(tài)時(shí)),迅速滅弧,并使其快速冷卻,完成初步熔煉。之后將試樣翻轉(zhuǎn),在20kV,200mA條件下重新預(yù)熔120s后,迅速在20kV,280mA條件下進(jìn)行4次重熔,且每次重熔冷卻后均需重新預(yù)熔和翻轉(zhuǎn)試樣,最后一次重熔后,待樣品冷卻至室溫(25℃左右)出爐,所得產(chǎn)品為鎢比重含量為99.9%、比重為19.03、致密度為98.8%的高致密超高比重鎢合金。實(shí)施例7制備致密度為98.6%的超高比重鎢合金(鎢比重含量為99.9%,比重為18.99)。其制備過程依次經(jīng)鎢粉酸洗、清洗、冷凍干燥處理,冷壓成型、高真空燒結(jié)獲得預(yù)制塊體,合金的非自耗電弧熔煉等獲得該鎢合金。其中,非自耗電弧熔煉的工藝過程又包括預(yù)熱、預(yù)熔、熔煉、多次重熔等。其具體步驟如下:1.鎢粉的酸洗、清洗與冷凍干燥處理:使用濃度為3mol/L的稀鹽酸對鎢比重含量占99.0%的鎢粉(粒徑為1~20μm)攪拌酸洗60min,后除去上層清洗液,使用電阻率≥2.0×106Ω·cm的去離子水進(jìn)行清洗至pH≥4為止,后使用冷凍干燥設(shè)備在-10℃以下對清洗后的鎢粉冷凍干燥12h。2.將鎢粉冷壓成型為生坯,經(jīng)高真空燒結(jié)獲得預(yù)制塊體:將步驟1中獲得的鎢粉裝入Cr12MoV模具中,使用壓片機(jī)在室溫(25℃左右)下冷壓成型,壓強(qiáng)為800MPa,壓模時(shí)間5min,獲得塊狀生坯;之后經(jīng)過高真空放電等離子燒結(jié),真空度為10-3Pa,壓力為10MPa,溫度為2000℃,保壓時(shí)間為30min,獲得預(yù)制塊體。3.開通快速冷卻循環(huán)水,抽真空、通氬氣,做好非自耗電弧熔煉前的準(zhǔn)備工作:開通快速冷卻循環(huán)水,保證水壓≥0.08MPa,并將步驟2中獲得的預(yù)制塊體放入ACM-SO1非自耗熔煉爐中的結(jié)晶器熔池中,關(guān)閉爐門抽真空,當(dāng)真空度≤4Pa時(shí),往爐內(nèi)通氬氣,使?fàn)t內(nèi)壓強(qiáng)相對大氣壓強(qiáng)達(dá)到-0.04MPa(保證起弧正常),做好非自耗電弧熔煉前的準(zhǔn)備工作。4.高致密、超高比重鎢合金的非自耗電弧熔煉過程:將ACM-SO1非自耗電弧熔煉爐運(yùn)行參數(shù)調(diào)至20kV,100mA,引弧并對預(yù)制塊體預(yù)熱90s;而后在20kV,200mA條件下預(yù)熔120s;之后在20kV,280mA下進(jìn)行熔煉,待塊狀鎢坯充分熔化后(觀察鎢粉為液態(tài)時(shí)),迅速滅弧,并使其快速冷卻,完成初步熔煉。之后將試樣翻轉(zhuǎn),在20kV,200mA條件下重新預(yù)熔120s后,迅速在20kV,280mA條件下進(jìn)行4次重熔,且每次重熔冷卻后均需重新預(yù)熔和翻轉(zhuǎn)試樣,最后一次重熔后,待樣品冷卻至室溫(25℃左右)出爐,所得產(chǎn)品為鎢比重含量為99.9%、比重為18.99、致密度為98.6%的高致密超高比重鎢合金。實(shí)施例8制備致密度為98.4%的超高比重鎢合金(鎢比重含量為99.9%,比重為18.95)。其制備過程依次經(jīng)鎢粉酸洗、清洗、冷凍干燥處理,冷壓成型、高真空燒結(jié)獲得預(yù)制塊體,合金的非自耗電弧熔煉等獲得該鎢合金。其中,非自耗電弧熔煉的工藝過程又包括預(yù)熱、預(yù)熔、熔煉、多次重熔等。其具體步驟如下:1.鎢粉的酸洗、清洗與冷凍干燥處理:使用濃度為3mol/L的稀鹽酸對鎢比重含量占99.0%的鎢粉(粒徑為1~20μm)攪拌酸洗60min,后除去上層清洗液,使用電阻率≥2.0×106Ω·cm的去離子水進(jìn)行清洗至pH≥4為止,后使用冷凍干燥設(shè)備在-10℃以下對清洗后的鎢粉冷凍干燥12h。2.將鎢粉冷壓成型為生坯,經(jīng)高真空燒結(jié)獲得預(yù)制塊體:將步驟1中獲得的鎢粉裝入Cr12MoV模具中,使用壓片機(jī)在室溫(25℃左右)下冷壓成型,壓強(qiáng)為1000MPa,壓模時(shí)間3min,獲得塊狀生坯;之后經(jīng)過高真空放電等離子燒結(jié),真空度為10-3Pa,壓力為80MPa,溫度為1500℃,保壓時(shí)間為20min,獲得預(yù)制塊體。3.開通快速冷卻循環(huán)水,抽真空、通氬氣,做好非自耗電弧熔煉前的準(zhǔn)備工作:開通快速冷卻循環(huán)水,保證水壓≥0.08MPa,并將步驟2中獲得的預(yù)制塊體放入ACM-SO1非自耗熔煉爐中的結(jié)晶器熔池中,關(guān)閉爐門抽真空,當(dāng)真空度≤4Pa時(shí),往爐內(nèi)通氬氣,使?fàn)t內(nèi)壓強(qiáng)相對大氣壓強(qiáng)達(dá)到-0.04MPa(保證起弧正常),做好非自耗電弧熔煉前的準(zhǔn)備工作。4.高致密、超高比重鎢合金的非自耗電弧熔煉過程:將ACM-SO1非自耗電弧熔煉爐運(yùn)行參數(shù)調(diào)至20kV,100mA,引弧并對預(yù)制塊體預(yù)熱90s;而后在20kV,200mA條件下預(yù)熔120s;之后在20kV,280mA下進(jìn)行熔煉,待塊狀鎢坯充分熔化后(觀察鎢粉為液態(tài)時(shí)),迅速滅弧,并使其快速冷卻,完成初步熔煉。之后將試樣翻轉(zhuǎn),在20kV,200mA條件下重新預(yù)熔120s后,迅速在20kV,280mA條件下進(jìn)行4次重熔,且每次重熔冷卻后均需重新預(yù)熔和翻轉(zhuǎn)試樣,最后一次重熔后,待樣品冷卻至室溫(25℃左右)出爐,所得產(chǎn)品為鎢比重含量為99.9%、比重為18.95、致密度為98.4%的高致密超高比重鎢合金。表1不同高比重鎢合金樣品信息及比重對照表序號樣品名稱或合金牌號國別元素成分工藝手段比重1超高比重鎢合金中國W電弧熔煉18.89~19.11297W中國W、Ni、Fe粉末冶金18.5393W中國W、Ni、Fe粉末冶金17.64GW-1中國W、Ni、Fe及其他粉末冶金18.05SD-180美國W、Ni、Fe及其他粉末冶金18.06WHA-A日本W(wǎng)、Ni、Fe及其他粉末冶金18.07GW-2S中國W、Ni、Fe及其他粉末冶金18.08Malloyry3950美國W、Ni、Fe及其他粉末冶金18.09GW-3S中國W、Ni、Fe及其他粉末冶金17.010橡樹嶺公司W(wǎng)-Ni-Fe美國W、Ni、Fe及其他粉末冶金17.011A-123奧地利W、Ni、Fe及其他粉末冶金17.612WHA-C日本W(wǎng)、Ni、Fe及其他粉末冶金18.0表2高致密超高比重鎢合金元素含量ICP測試對照表當(dāng)前第1頁1 2 3