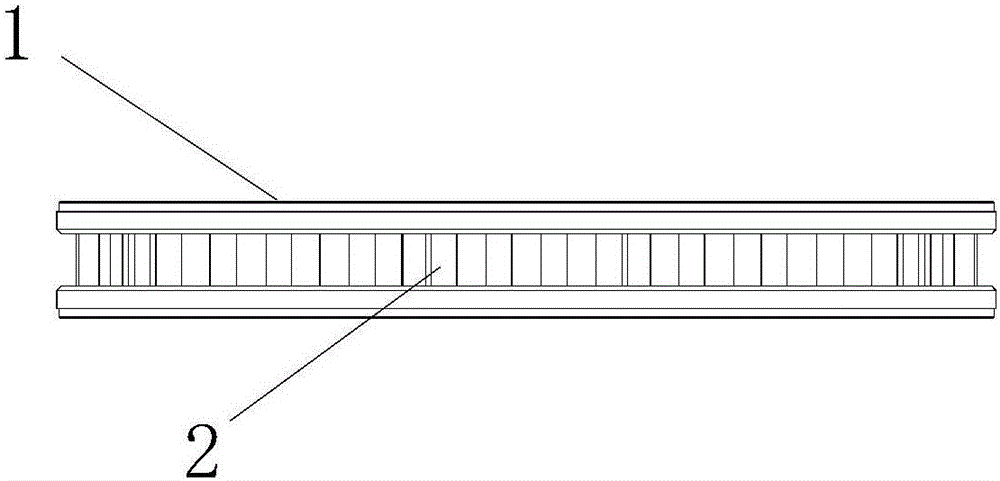
本發(fā)明涉及一種軸裝制動(dòng)盤的生產(chǎn)方法及應(yīng)用該方法的軸裝制動(dòng)盤,特別是一種城市快軌列車、鐵路客車和高速動(dòng)車組列車用軸裝制動(dòng)盤制造過(guò)程中防止產(chǎn)品質(zhì)量分布不均的方法及應(yīng)用該方法的軸裝制動(dòng)盤。
背景技術(shù):
:目前,城市快軌列車、鐵路客車和高速動(dòng)車組列車的基礎(chǔ)制動(dòng)均采用盤形制動(dòng)裝置,盤形制動(dòng)裝置的作用是在車輛實(shí)施制動(dòng)時(shí),使閘片垂直壓緊軸裝制動(dòng)盤的兩個(gè)摩擦面產(chǎn)生摩擦力,由此產(chǎn)生制動(dòng)力矩,將車輛運(yùn)動(dòng)時(shí)的動(dòng)能和勢(shì)能轉(zhuǎn)化為熱能,從而達(dá)到使車輛減速或停車的目的。因此制動(dòng)盤是將列車動(dòng)能和勢(shì)能通過(guò)摩擦轉(zhuǎn)化成熱能的關(guān)鍵部件。目前使用的軸裝制動(dòng)盤的結(jié)構(gòu)是由上下兩個(gè)薄片圓環(huán)中間聯(lián)接上多個(gè)圓柱形散熱筋組成,薄片圓環(huán)的外側(cè)面作為摩擦面,因此在鑄造過(guò)程中現(xiàn)有的做法是使用上箱、下箱將鑄件從中間分型由上下兩個(gè)半型腔合起來(lái)形成整體,且上箱、下箱的分型面處在制動(dòng)盤的中間,雖然這樣工藝較為簡(jiǎn)單,但是在實(shí)際操作過(guò)程中輕微的錯(cuò)型錯(cuò)芯經(jīng)常發(fā)生,一旦產(chǎn)生錯(cuò)型錯(cuò)芯,雖然外輪廓尺寸可以通過(guò)機(jī)加工來(lái)滿足圖紙尺寸要求,但中間的散熱筋根本無(wú)法處理,致使產(chǎn)品質(zhì)量分布不均,檢驗(yàn)時(shí)無(wú)法通過(guò)動(dòng)平衡檢測(cè)而成為廢品。技術(shù)實(shí)現(xiàn)要素:為克服上述現(xiàn)有技術(shù)中存在的問(wèn)題,本發(fā)明提供一種易于實(shí)現(xiàn)、避免鑄造時(shí)的錯(cuò)型錯(cuò)芯影響軸裝制動(dòng)盤質(zhì)量的生產(chǎn)方法,以及使用該方法制造的軸裝制動(dòng)盤。本發(fā)明的技術(shù)方案為:一種軸裝制動(dòng)盤的生產(chǎn)方法,所述軸裝制動(dòng)盤鑄造過(guò)程中,將所述軸裝制動(dòng)盤整體設(shè)置在下箱內(nèi),上箱只保留所述軸裝制動(dòng)盤的摩擦面外側(cè)的加工余量頂和冒口,將上箱、下箱的分型面設(shè)置在所述軸裝制動(dòng)盤的摩擦面的外側(cè)的所述加工余量頂處,可以避免錯(cuò)型錯(cuò)芯對(duì)所述軸裝制動(dòng)盤中間的散熱筋和摩擦面造成影響;同時(shí)將摩擦面外側(cè)的加工余量頂都設(shè)計(jì)成錐面,增大了鑄件變形的阻力,使鑄件保持穩(wěn)定收縮,冷卻完成后,將所述加工余量頂加工成平面。另一種軸裝制動(dòng)盤的生產(chǎn)方法,包括具體如下步驟:A、通過(guò)計(jì)算機(jī)模擬軟件對(duì)所述軸裝制動(dòng)盤的鑄造工藝和鑄造模具進(jìn)行模擬分析,將軸裝制動(dòng)盤整體設(shè)置在下箱內(nèi),上箱只保留軸裝制動(dòng)盤的摩擦面外側(cè)的加工余量頂和冒口,將上箱、下箱的分型面設(shè)置在軸裝制動(dòng)盤的摩擦面外側(cè)的加工余量頂處;將所述軸裝制動(dòng)盤摩擦面外側(cè)的加工余量頂都設(shè)計(jì)成錐形并確定其厚度。B、制定所述制動(dòng)盤的鑄造工藝。C、根據(jù)步驟A的模擬分析結(jié)果,制作鑄造模具,所述摩擦面外側(cè)的加工余量頂符合步驟A中模擬分析的結(jié)果。D、制作型芯,合箱,熔煉澆鑄,冷卻凝固,打箱落砂。E、對(duì)鑄件進(jìn)行粗加工和熱處理,去除摩擦面的加工余量頂。F、對(duì)鑄件進(jìn)行調(diào)質(zhì)處理和精加工。進(jìn)一步,在步驟C中,所述鑄造模具設(shè)計(jì)為一型兩件,用一個(gè)澆注系統(tǒng)一次澆注兩個(gè)鑄件,提高生產(chǎn)效率的同時(shí),也滿足了鑄件順序凝固的工藝需要,符合鑄件順序凝固的溫度梯度要求,以獲得更好的產(chǎn)品內(nèi)在質(zhì)量。進(jìn)一步,所述加工余量頂?shù)暮穸炔怀^(guò)10mm,保證加工效果的同時(shí),減少材料的浪費(fèi)。在進(jìn)行模擬分析前,首先對(duì)鑄件需要達(dá)到的技術(shù)要求做分析,根據(jù)技術(shù)要求模擬制動(dòng)盤的鑄造工藝和鑄造模具。本發(fā)明選用的模擬軟件包括適用于材料加工工程及制造領(lǐng)域中的任何模擬軟件,如Magma、ProCast、NovaCast、AnyCast、Flow3D、華鑄CAE、Ansys、Abaqus、Marc等。打開(kāi)模擬軟件,建立實(shí)體模型,在模型上劃分網(wǎng)格,設(shè)定參數(shù),進(jìn)行模擬分析;根據(jù)模擬結(jié)果調(diào)試參數(shù),然后使用新的參數(shù)再次進(jìn)行模擬分析;經(jīng)過(guò)不斷的調(diào)試參數(shù),得到能夠達(dá)到鑄件技術(shù)要求的鑄造工藝和鑄造模具。本發(fā)明通過(guò)計(jì)算在滿足鑄件正常的順序凝固不受影響,將鑄件的整體設(shè)置在下箱內(nèi),而不是對(duì)稱設(shè)置在上箱、下箱內(nèi),所述上箱內(nèi)僅保留摩擦面外側(cè)的加工余量頂和冒口,即使生產(chǎn)時(shí)產(chǎn)生輕微錯(cuò)型錯(cuò)芯,僅會(huì)影響摩擦面的加工余量頂,避免影響所述軸裝制動(dòng)盤中間的散熱筋和摩擦面,進(jìn)而使機(jī)加工后的產(chǎn)品形成均勻的摩擦環(huán)厚度,完全通過(guò)動(dòng)平衡測(cè)試。一種軸裝制動(dòng)盤,該軸裝制動(dòng)盤采用上述方法制得。所制備的軸裝制動(dòng)盤在澆注時(shí),將所述軸裝制動(dòng)盤整體設(shè)置在下箱內(nèi),上箱只保留所述軸裝制動(dòng)盤的摩擦面外側(cè)的加工余量頂和冒口,將上箱、下箱的分型面設(shè)置在所述軸裝制動(dòng)盤的摩擦面的外側(cè)的所述加工余量頂處;同時(shí)將摩擦面外側(cè)的加工余量頂設(shè)計(jì)成錐面,在鑄造過(guò)程中即使出現(xiàn)錯(cuò)型錯(cuò)芯,也不會(huì)影響所述軸裝制動(dòng)盤的摩擦面和散熱筋,摩擦面使用錐形加工余量頂,增大了鑄件變形的阻力,使鑄件保持穩(wěn)定收縮,最大限度保證制動(dòng)盤盤環(huán)動(dòng)平衡檢測(cè)的通過(guò)率。發(fā)明的技術(shù)效果:(1)本發(fā)明的軸裝制動(dòng)盤生產(chǎn)方法,相對(duì)于現(xiàn)有技術(shù),在制造過(guò)程中,將軸裝制動(dòng)盤整體設(shè)置在下箱內(nèi),上箱只保留軸裝制動(dòng)盤的摩擦面的加工余量頂和冒口,避免因錯(cuò)型錯(cuò)芯對(duì)軸裝制動(dòng)盤的摩擦面和散熱筋造成影響;(2)將軸裝制動(dòng)盤的摩擦面外側(cè)的加工余量頂設(shè)計(jì)成錐面,增大了鑄件變形的阻力,使鑄件保持穩(wěn)定收縮;(3)冷卻成型后通過(guò)機(jī)加工將軸裝制動(dòng)盤的摩擦面的加工余量頂加工成平面,對(duì)鑄件結(jié)構(gòu)形狀沒(méi)有任何影響,只需在加工過(guò)程中增加少量的加工時(shí)間,最大限度保證了產(chǎn)品動(dòng)平衡檢測(cè)通過(guò)率;(4)采用一型兩件的鑄造模具,用一個(gè)澆注系統(tǒng)一次澆注兩個(gè)鑄件,提高生產(chǎn)效率的同時(shí),也滿足了鑄件順序凝固的工藝需要,符合鑄件順序凝固的溫度梯度要求,以獲得更好的產(chǎn)品內(nèi)在質(zhì)量。附圖說(shuō)明下面結(jié)合說(shuō)明書(shū)附圖對(duì)本發(fā)明作進(jìn)一步詳細(xì)說(shuō)明:圖1是現(xiàn)有軸裝制動(dòng)盤的產(chǎn)品結(jié)構(gòu)示意圖;圖2是圖1的左視圖;圖3是本發(fā)明一種軸裝制動(dòng)盤的生產(chǎn)方法的工藝流程圖;圖4是本發(fā)明軸裝制動(dòng)盤的毛坯結(jié)構(gòu)示意圖;圖5是本發(fā)明的生產(chǎn)方法合箱的示意圖;圖6是圖5中A的局部放大圖。圖中:摩擦面1,散熱筋2,加工余量頂3,上箱4,下箱5。具體實(shí)施方式實(shí)施例1以時(shí)速250km/h的高速列車鑄鋼軸裝制動(dòng)盤(外徑為610mm,內(nèi)徑為240mm)為例,其鑄造方法的工藝流程如圖3所示,其按照先后順序包括以下步驟:A、通過(guò)計(jì)算機(jī)模擬軟件對(duì)軸裝制動(dòng)盤的鑄造工藝和鑄造模具進(jìn)行模擬分析,將軸裝制動(dòng)盤整體設(shè)置在下箱5內(nèi),上箱4內(nèi)只保留軸裝制動(dòng)盤的摩擦面外側(cè)的加工余量頂和冒口,將上箱4、下箱5的分型面設(shè)置在軸裝制動(dòng)盤的摩擦面外側(cè)的加工余量頂處;將上箱4內(nèi)軸裝制動(dòng)盤的摩擦面外側(cè)的加工余量頂3設(shè)計(jì)成錐形,加工余量頂?shù)腻F面厚度為7mm(其他實(shí)施例可以是5mm、6mm、8mm、9mm、10mm等);將下箱5內(nèi)軸裝制動(dòng)盤的另一個(gè)摩擦面外側(cè)的加工余量頂設(shè)計(jì)成錐形,加工余量頂?shù)腻F面厚度為5mm(其他實(shí)施例可以是6mm、7mm、8mm、9mm、10mm等);將上箱4、下箱5的分型面設(shè)置在軸裝制動(dòng)盤的摩擦面外側(cè)的加工余量頂處。B、制定所述軸裝制動(dòng)盤的鑄造工藝。C、根據(jù)步驟A的模擬分析結(jié)果,制作鑄造模具,摩擦面外側(cè)的加工余量頂符合步驟A中模擬分析的結(jié)果;其中,上箱4內(nèi)加工余量頂?shù)腻F面厚度為7mm,下箱5內(nèi)加工余量頂?shù)腻F面厚度為5mm。D、制作型芯,合箱,熔煉澆鑄,冷卻凝固,打箱落砂。E、對(duì)鑄件進(jìn)行粗加工和熱處理,去除摩擦面外側(cè)的加工余量頂。F、對(duì)鑄件進(jìn)行調(diào)質(zhì)處理和精加工。選用ProCast模擬軟件對(duì)鑄造工藝和鑄造模具進(jìn)行模擬分析。根據(jù)最佳模擬結(jié)果,制定實(shí)際的鑄造工藝流程和實(shí)際的鑄造模具。在軸裝制動(dòng)盤的鑄造過(guò)程中,金屬液進(jìn)入型腔的方式、位置、流速等各個(gè)參數(shù)均要符合模擬結(jié)果;鑄造模具中澆鑄系統(tǒng)和補(bǔ)縮系統(tǒng)的位置、形狀、尺寸、冒口數(shù)量及形狀等各個(gè)參數(shù)也均要符合模擬結(jié)果。鑄造模具設(shè)計(jì)成一型兩件的鑄造模具,用一個(gè)澆注系統(tǒng)一次澆注兩個(gè)鑄件,提高生產(chǎn)效率。上箱4內(nèi)加工余量頂?shù)腻F面厚度為7mm(其余實(shí)施例可以是5mm、6mm、8mm、9mm、10mm等),下箱5內(nèi)的加工余量頂?shù)腻F面厚度為5mm(其他實(shí)施例可以是6mm、7mm、8mm、9mm、10mm等);上箱4、下箱5的分型面處在摩擦面1的外側(cè);完成制作型芯,合箱,熔煉澆鑄工序后,冷卻定型,打箱落砂后對(duì)制動(dòng)盤進(jìn)行機(jī)加工,去除摩擦面外側(cè)的加工余量頂3,再對(duì)軸裝制動(dòng)盤進(jìn)行后續(xù)精加工及檢測(cè)。上箱4面需要放置補(bǔ)縮冒口方便渣氣上浮至冒口內(nèi),能更好的保證鑄件的內(nèi)在質(zhì)量,因此上箱4內(nèi)的加工余量頂?shù)暮穸却笥谙孪?內(nèi)的厚度。對(duì)制得的制動(dòng)盤進(jìn)行無(wú)損檢測(cè),同時(shí)滿足超聲探傷II級(jí)和磁粉探傷I級(jí)的檢驗(yàn)要求,檢測(cè)合格的軸裝制動(dòng)盤配對(duì)進(jìn)行輪對(duì)動(dòng)平衡檢驗(yàn),檢驗(yàn)合格率100%,使用該工藝前后尺寸檢驗(yàn)合格率、動(dòng)平衡檢測(cè)合格率數(shù)據(jù)的對(duì)比見(jiàn)表1。表1試驗(yàn)組與對(duì)比組檢驗(yàn)合格率數(shù)據(jù)項(xiàng)目例數(shù)尺寸一次檢驗(yàn)合格量加工后尺寸合格量動(dòng)平衡檢測(cè)合格量試驗(yàn)組100669494對(duì)比組100267646顯然,上述實(shí)施例僅僅是為清楚地說(shuō)明本發(fā)明所作的舉例,而并非是對(duì)本發(fā)明的實(shí)施方式的限定。對(duì)于所屬領(lǐng)域的普通技術(shù)人員來(lái)說(shuō),在上述說(shuō)明的基礎(chǔ)上還可以做出其它不同形式的變化或變動(dòng)。這里無(wú)需也無(wú)法對(duì)所有的實(shí)施方式予以窮舉。而這些屬于本發(fā)明的精神所引伸出的顯而易見(jiàn)的變化或變動(dòng)仍處于本發(fā)明的保護(hù)范圍之中。當(dāng)前第1頁(yè)1 2 3