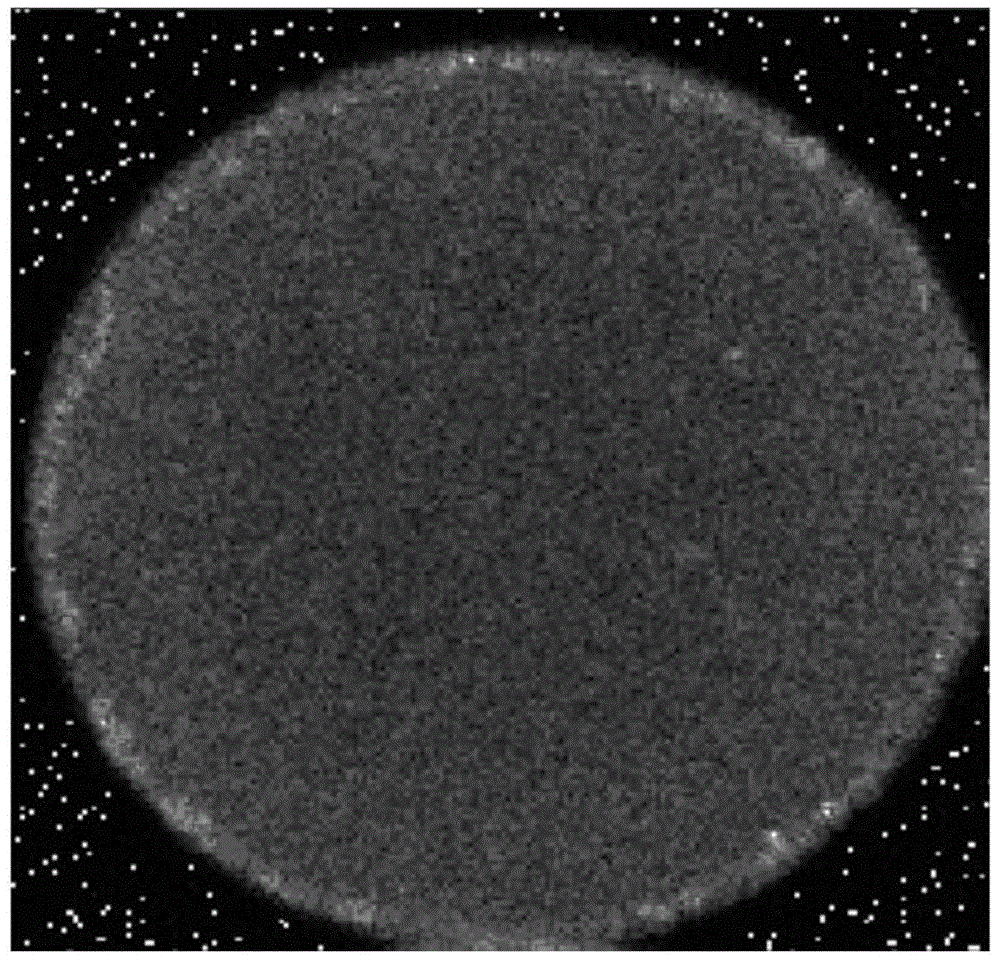
本發(fā)明屬于冶金制備領域,特別涉及一種高質(zhì)量鈦鋁合金靶材的制造方法。
背景技術:隨著現(xiàn)代機械加工業(yè)朝著高精度、高速切削、硬加工代研磨、干加工(無冷卻液)保護環(huán)境以及降低成本等方向發(fā)展,對刀具性能提出了相當高的要求。因此,開發(fā)各種耐磨性能優(yōu)越、能長時間進行穩(wěn)定加工的切削材料是必然的發(fā)展趨勢。以過渡族金屬碳化物、氮化物、硼化物和金剛石膜等為代表的硬質(zhì)涂層由于具有超硬和耐磨等特點,已在機械加工工具、模具和機械零件等方面獲得廣泛應用。物理氣相沉積(PhysicalVaporDeposition,PVD)是沉積硬質(zhì)涂層的主導技術,采用PVD方法制備的氮化鈦鋁(TiAlN)涂層是在二元涂層的基礎上發(fā)展起來的一種新型三元復合涂層,其硬度顯著高于TiN涂層,同時涂層的抗高溫氧化性、膜基結(jié)合強度、耐腐蝕性和耐磨性均得到提高。因此TiAlN被認為是較TiN更有前途的新型涂層材料,近年來受到廣泛關注。TiAlN涂層的膜料為鈦鋁合金。目前,制造鈦鋁合金靶材的方法有兩種,粉末燒結(jié)法和熔煉鑄造法:(1)粉末燒結(jié)法:如公開號為CN101214546A的中國專利申請中采用一定粒度的Ti粉和Al粉,或霧化的合金粉末,經(jīng)混粉,裝粉,冷等靜壓成型,脫氣,熱等靜壓或燒結(jié),再經(jīng)機加工制成成品。該方法的優(yōu)點是可制備組織均勻、細小的制件,且可實現(xiàn)制件的近凈成形,可有效解決鈦元素偏析問題;該方法的缺點是合金在制作過程中不僅易受間隙元素的污染,氣體雜質(zhì)(C、N、O)含量偏高,而且對粉末純度、粒度及性能要求較高,制備難度較大。(2)熔煉鑄造法:目前,熔煉鈦鋁合金的方法有以下幾種:1、真空感應熔煉。如專利號為01133475的中國專利申請中采用高純氧化鈣坩堝進行熔煉,通過添加1%~2%的金屬鈣進行脫氧,可生產(chǎn)出化學成份合格,雜質(zhì)含量低的鈦鋁合金。但是,在熔煉過程中活性金屬鈦、鋁均與坩堝材料反應,污染熔液,且添加金屬鈣也會引入大量鈣雜質(zhì)元素,無法滿足材料成分要求。2、真空電子束熔煉。該方法能較好的消除高密度和低密度夾雜,獲得細晶均質(zhì)鑄錠。但是該方法熔煉過程中鋁元素揮發(fā)大,成份不易控制。3、真空自耗電弧爐熔煉。該方法熔煉時金屬液滴滴入水冷坩堝后迅速凝固,不與坩堝材料反應,鑄錠密度較高,基本上不存疏松,但存在成分偏析,鑄錠中存在不熔物鈦。4、真空自耗凝殼爐熔煉。該方法亦可避免坩堝對金屬熔體的污染,且熔煉過程中存在均質(zhì)化過程,合金成分均勻,宏觀偏析少,由于采用重力鑄造的辦法,鑄錠內(nèi)部不可消除宏觀縮孔和疏松,成材率低。因此,目前的合金靶材制備領域需要一種結(jié)合上述真空自耗電弧爐熔煉工藝、真空自耗凝殼熔煉工藝的優(yōu)點,能夠得到鑄錠密度較高、縮孔較淺、成分均勻、無宏觀偏析的大尺寸鈦鋁合金錠坯的制備方法。
技術實現(xiàn)要素:針對現(xiàn)有技術的不足,本發(fā)明的目的在于提供一種鈦鋁合金靶材的真空自耗電弧爐和凝殼爐復合熔煉方法。該方法具有合金成份控制準確,鈦、鋁元素分布均勻,顯微組織晶粒細小,無坩堝污染,氣體雜質(zhì)含量低,無皮下氣泡、裂紋等鑄造缺陷的優(yōu)點。本發(fā)明的目的是通過以下技術方案實現(xiàn)的:一種高質(zhì)量鈦鋁合金靶材的制備方法,先進行真空自耗電弧爐熔煉,再進行真空自耗凝殼爐熔煉制備鈦鋁合金,依次包括配料步驟、烘料步驟、電極壓制步驟、電極焊接步驟、真空自耗電弧爐熔煉步驟、和真空自耗凝殼爐熔煉步驟,其中:在所述烘料步驟中,將配好的原料海綿鈦和金屬鋁進行烘烤處理,得到烘烤好的原料;在所述電極壓制步驟中,將所述烘烤好的原料進行壓制處理,得到電極;在所述電極焊接步驟中,將所述電極進行焊接處理,得到焊接好的電極;在所述真空自耗電弧爐熔煉步驟中,將所述焊接好的電極進行真空自耗電弧爐熔煉處理,得到真空自耗電弧爐熔煉后的錠坯;在所述真空自耗凝殼爐熔煉步驟中,將所述真空自耗電弧爐熔煉后的電極進行真空自耗凝殼爐熔煉處理,得到真空自耗凝殼爐熔煉后的鑄錠。進一步地,在所述配料步驟中,按鈦鋁合金成分設計要求分別稱取0級海綿鈦和純度高于99.99%的金屬鋁,其中所述鈦鋁合金按重量百分比由以下元素組成Ti:60~70%,Al:40~30%。進一步地,在所述烘料步驟中,所述烘烤溫度為140~200℃,所述烘烤時間為4~6h,所述真空烘箱的真空度為500~5000Pa。進一步地,在所述電極壓制步驟中,將烘烤好的金屬鋁置于電極中心,電極外圍由烘烤好的海綿鈦包裹;電極壓制的模具材料為碳素工具鋼,尺寸為D140*300mm。進一步地,在所述電極焊接步驟中,將5~7根電極進行焊接處理;所述焊接處理采用鎢極氬弧焊,焊接材料為純鈦焊絲。進一步地,在所述真空自耗電弧爐熔煉步驟中,首先使真空感應爐的真空度保持為0.01~0.08Pa,再以4000~6000A的電流送電熔煉,電壓控制在32~35V,熔煉完后繼續(xù)保持真空度在0.05~0.1Pa,隨爐冷卻至300~400℃出爐;采用的結(jié)晶器為水冷銅坩堝。進一步地,在所述真空自耗凝殼爐熔煉步驟中,模具除氣的溫度為500~600℃,烘烤時間為8~12h;真空凝殼爐的真空度保持在0.01~0.08Pa,再以16000~20000A的電流進行熔煉,熔煉電壓控制在32~40V;澆鑄完后保持爐內(nèi)真空度在在0.05~0.1Pa,隨爐冷卻至室溫后出爐;所述模具為石墨模具。本發(fā)明相比現(xiàn)有技術具有如下有益效果:1、在本發(fā)明的方法的各個步驟之間相互協(xié)同作用、環(huán)環(huán)相扣,確保了產(chǎn)品的質(zhì)量:原材料經(jīng)真空烘干以確保原材料干燥且不被氧化;由于海綿鈦和金屬鋁的熔點相差較大,制備電極時將金屬鋁塊置于電極的中心,可以防止電極在熔煉過程中電極的塌陷;采用水冷銅坩堝進行真空自耗電弧爐熔煉時,單個熔滴滴入水冷銅坩堝后迅速凝固,可以避免鈦鋁合金熔液與坩堝材料反應;采用真空自耗凝殼爐熔煉時,由于水冷銅坩堝與金屬熔體之間存在一層由金屬熔體凝固而形成的固體殼層,避免了坩堝對金屬熔體的污染,且真空自耗凝殼熔煉工藝鑄造縮孔淺、鑄錠密度較高,可解決真空自耗電弧爐熔煉大尺寸鈦鋁合金錠坯時,存在很深縮孔,成材率低的問題。2、本發(fā)明利用真空自耗電弧爐熔煉工藝鑄錠密度較高,縮孔較淺的優(yōu)勢,和利用真空自耗凝殼熔煉工藝合金成分比較均勻,無宏觀偏析的優(yōu)勢,將兩種熔煉工藝復合在一起,成功地制備了大尺寸鈦鋁合金錠坯。3、本發(fā)明與現(xiàn)有技術相比具有合金成份控制準確,鈦、鋁元素分布均勻,宏觀偏析少,無坩堝污染,氣體雜質(zhì)含量低,無皮下氣泡、裂紋、中心縮孔等鑄造缺陷的優(yōu)點。上述優(yōu)點具體如下:成分控制精確,主成分偏差≤0.5wt%,錠坯內(nèi)部沒有鈦元素偏析,合金中外來夾雜Ca≤0.005wt%,氣體含量較低(O≤0.08wt%,N≤0.01wt%,C≤0.015wt%),錠坯內(nèi)部探傷無內(nèi)部氣孔、微裂紋、疏松等缺陷。附圖說明圖1是本發(fā)明實施例1制得的合金鑄錠切片的超聲波探傷圖。圖2是本發(fā)明實施例2制得的合金鑄錠切片的超聲波探傷圖。圖3是本發(fā)明實施例3制得的合金鑄錠切片的超聲波探傷圖。圖4是本發(fā)明對比例2制得的合金鑄錠內(nèi)部缺陷的掃描電鏡圖。圖5是本發(fā)明對比例3制得的合金線切割后鑄錠內(nèi)部的缺陷圖。圖6是本發(fā)明對比例4制得的合金鑄錠切片的超聲波探傷圖。圖7是本發(fā)明對比例5制得的合金鑄錠切片的超聲波探傷圖。具體實施方式下面結(jié)合具體實施例對本發(fā)明進行詳細說明,但本發(fā)明并不限于此。本發(fā)明采用水冷銅坩堝進行真空自耗電弧爐熔煉、再采用石墨模具進行真空自耗凝殼爐熔煉制備鈦鋁合金,高質(zhì)量鈦鋁合金錠坯的制備方法中依次包括配料步驟、烘料步驟、電極壓制步驟、電極焊接步驟、真空自耗電弧爐熔煉步驟、真空自耗凝殼爐熔煉步驟,其中:一、配料步驟:是按照鈦鋁合金成分設計要求,分別稱取塊狀的海綿鈦和塊狀的金屬鋁;作為一種優(yōu)選實施方式,配料步驟是按鈦鋁合金成分設計要求,分別稱取0級海綿鈦和純度高于99.99%的金屬鋁,其中鈦鋁合金按重量百分比由以下元素組成:Ti:60-70%,Al:30-40%。比如,Al的重量百分比可以控制在32%、34%、36%、38%等;二、烘料步驟:將配好的原料海綿鈦和金屬鋁進行烘烤處理,得到烘烤好的原料;具體來說,是將配好的原料金屬鋁和海綿鈦分別放入真空烘,烘烤溫度為不低于140℃,烘烤時間為不少于4小時,然后隨爐降溫不高于40℃取出待用;上述方法可以示例性地描述為:在烘料步驟中,將配好的原料放入真空烘箱中,在140℃、160℃、180℃或200℃的條件下保溫4h、5h或6h,然后隨爐降溫至15℃、20℃、30℃或40℃取出待用;優(yōu)選地,在烘料步驟中,烘烤溫度為140~200℃,烘烤時間為4~6h。另外,烘料過程中優(yōu)選使真空烘箱的真空度為500-5000Pa,比如為1000Pa、1300Pa、1600Pa、2000Pa、2300Pa、2500Pa、3000Pa、3400Pa、3800Pa、4200Pa、4600Pa等。三、電極壓制步驟:將烘烤好的原料進行壓制處理,得到電極;具體來說,是將經(jīng)烘烤的原料海綿鈦和金屬鋁放入市售的專用的四柱電極壓制機的模具內(nèi),壓制成電極,壓機的公稱力為10000KN;該模具的材料可以為碳素工具鋼,尺寸為D140*300mm;金屬鋁要求置于電極中心,外圍由海綿鈦包裹。四、電極焊接步驟:將5~7根電極進行焊接處理,得到焊接好的電極;具體來說,焊接處理中,采用鎢極氬弧焊,焊接材料為純鈦焊絲,將5~7根電極焊接在一起。五、真空自耗電弧爐熔煉步驟:將焊接好的電極進行真空自耗電弧爐熔煉處理,得到真空自耗電弧爐熔煉后的錠坯;具體來說,是采用650kg真空自耗電極電弧爐進行熔煉,配備直徑為¢150-¢220mm的鑄錠使用的水冷銅坩堝;首先使真空自耗電極電弧爐的真空度保持在0.1Pa以下,以不低于3000A的電流將焊接好的電極進行熔煉,熔煉電壓控制在30V以上,待25-30分鐘后停爐冷卻,并保持爐內(nèi)真空度在不大于0.1Pa,隨爐冷卻至400℃以下出爐;上述方法可以示例性地描述為:在真空自耗電弧爐熔煉步驟中,首先使真空電弧爐的真空度保持在0.01Pa、0.04Pa、0.05Pa、0.06Pa、0.07Pa、0.08Pa或0.1Pa,再以3000A、4000A或5000A的電功率流送電,待25min、28min或30min后停爐冷卻,并保持爐內(nèi)真空度在0.05Pa、0.08Pa或0.1Pa,隨爐冷卻至400℃、350℃、300℃或200℃出爐。優(yōu)選地,在真空自耗電弧爐熔煉步驟中,首先使真空感應爐的真空度保持為0.01~0.08Pa,以4000~6000A的電流進行熔煉,熔煉電壓為32~35V,待28~32分鐘后停爐冷卻,并保持爐內(nèi)真空度為0.05~0.1Pa,隨爐冷卻至300~400℃出爐。六、真空自耗凝殼爐熔煉步驟:將真空自耗電弧爐熔煉后的電極進行真空自耗凝殼爐熔煉處理,得到真空自耗凝殼爐熔煉后的鑄錠;具體來說,是采用150kg真空自耗電極凝殼爐進行熔煉,配備高純石墨模具進行澆鑄;首先將石墨模具在真空烘箱內(nèi)進行除氣處理,加熱溫度為不低于500℃,烘烤時間大于6h;將烘烤后的石墨模具置于真空凝殼爐內(nèi)的旋轉(zhuǎn)盤上,并用鐵絲將石墨模具固定住,使?jié)驳揽趯适>咧行?;然后使真空凝殼爐的真空度保持在0.1Pa以下,以不低于15000A的電流將真空自耗電弧爐熔煉后的鑄錠作為電極進行熔煉,熔煉電壓控制在30V以上,待6~8分鐘后停止供電,啟動自動澆注系統(tǒng)進行澆鑄;澆鑄完后保持爐內(nèi)真空度在不低于1Pa,隨爐冷卻至室溫后出爐;上述方法可以示例性地描述為:在真空自耗凝殼爐熔煉步驟中,首先將石墨模具在真空烘箱內(nèi)進行除氣處理,加熱溫度為500℃、800℃、1000℃,烘烤時間為7h、9h、11h;使真空凝殼爐的真空度保持在0.05Pa、0.06Pa、0.07Pa、0.08Pa、0.09Pa,以15000A、17000A、18000A、21000A的電流進行熔煉;優(yōu)選地,在真空自耗凝殼爐熔煉步驟中,首先將石墨模具在真空烘箱內(nèi)進行除氣處理,加熱溫度為500~600℃,烘烤時間為8~12h;真空凝殼爐的真空度保持在0.01~0.08Pa,再以16000-20000A的電流進行熔煉,熔煉電壓控制在32~40V,待5~8分鐘后停爐進行澆鑄;澆鑄完后保持爐內(nèi)真空度在在0.05~0.1Pa,隨爐冷卻至室溫后出爐。以下三個實施例是按照本發(fā)明鈦鋁合金靶材真空自耗電弧爐和真空自耗凝殼爐復合熔煉方法,分別制備了3爐鈦鋁合金。實施例1本實施例制備的鈦鋁合金靶材按重量百分比由以下元素組成:Ti64%,Al36%。制造方法如下:(1)配料:按上述合金成分設計分別稱取0級海綿鈦和純度高于99.99%的金屬鋁;(2)烘料:將稱好的原材料鈦和鋁放入真空烘箱(真空度為5000Pa)中,在140℃條件下保溫5h,隨爐降溫至35℃取出待用;(3)壓電極:將鋁塊用鋁箔包好,將海綿鈦分為兩部分,先往四柱電極壓制機的模具內(nèi)倒入一部分海綿鈦,然后將鋁塊包放入模具內(nèi),最后將剩余的海綿鈦倒入模具內(nèi);(3)壓電極:將鋁塊用鋁箔包好,將海綿鈦分為兩部分,先往四柱電極壓制機的模具內(nèi)倒入一部分海綿鈦,然后將鋁塊包放入模具內(nèi),最后將剩余的海綿鈦倒入模具內(nèi);該四柱電極壓制機為市售產(chǎn)品;(4)焊接電極:采用鎢極氬弧焊將7根壓制好的電極首尾在一起,焊接的材料是純鈦焊絲;(5)真空自耗電弧爐熔煉:采用650kg真空自耗電極電弧爐進行熔煉,配備直徑為¢190mm的水冷銅坩堝;首先使真空自耗電極電弧爐的真空度保持在0.05Pa,以5000A的電流對焊接好的電極進行熔煉(熔煉后的液體滴入結(jié)晶器——水冷銅坩堝中)熔煉電壓控制在32V,待30分鐘后停爐冷卻,并保持爐內(nèi)真空度在0.08Pa,隨爐冷卻至400℃出爐;(6)錠坯扒皮:采用型號為CD6140A的車床對真空電弧爐熔煉后的錠坯進行扒皮處理:該錠坯冷卻后自動收縮,與水冷銅坩堝分離,從表皮往錠坯中心3~4mm的部分通過車加工消除掉;(7)真空自耗凝殼爐熔煉:采用150kg真空自耗電極凝殼爐進行熔煉,配備高純石墨模具進行澆鑄;首先將石墨模具在真空烘箱內(nèi)進行除氣處理,加熱溫度為550℃,烘烤時間為10h;將烘烤后的石墨模具置于真空凝殼爐內(nèi),并用鐵絲將石墨模具固定住,使?jié)驳揽趯适>咧行?;然后使所述真空凝殼爐的真空度保持在0.08Pa,以20000A的電流對上一步得到的錠坯作為電極進行熔煉(熔煉后的液體滴入結(jié)晶器中),熔煉電壓控制在35V,待5分鐘后停止供電,啟動自動澆注系統(tǒng)進行澆鑄(將熔煉得到的合金液通過澆道口流入石墨模具內(nèi));澆鑄完后保持爐內(nèi)真空度在0.07Pa,隨爐冷卻至室溫后出爐,得到相應的合金鑄錠;(8)機加工步驟:對上一步得到的合金鑄錠按照圖紙進行機加工,清洗后得到所需要的成品靶材。本實施例制備的合金鑄錠的性能參見表1。本實施例制備的合金鑄錠切片的超聲波探傷圖參見圖1,無皮下氣泡。實施例2本實施例制備的鈦鋁合金靶材按重量百分比由以下元素組成:Ti60%,Al40%。制造方法如下:(1)配料:按上述合金成分設計分別稱取0級海綿鈦和純度高于99.99%的金屬鋁;(2)烘料:將稱好的原材料鈦和鋁放入真空烘箱(真空度為5000Pa)中,在140℃條件下保溫4h,隨爐降溫至38℃取出待用;(3)壓電極:將鋁塊用鋁箔包好,將海綿鈦分為兩部分,先往四柱電極壓制機的模具內(nèi)倒入一部分海綿鈦,然后將鋁塊包放入模具內(nèi),最后將剩余的海綿鈦倒入模具內(nèi);該四柱電極壓制機為市售產(chǎn)品;(4)焊接電極:采用鎢極氬弧焊將6根壓制好的電極首尾在一起,焊接的材料是純鈦焊絲;(5)真空自耗電弧爐熔煉:采用650kg真空自耗電極電弧爐進行熔煉,配備直徑為¢190mm的水冷銅坩堝;首先使真空自耗電極電弧爐的真空度保持在0.06Pa,以4000A的電流對焊接好的電極進行熔煉(熔煉后的液體滴入結(jié)晶器——水冷銅坩堝中),熔煉電壓控制在33V左右,待32分鐘后停爐冷卻,并保持爐內(nèi)真空度在0.09Pa,隨爐冷卻至350℃以下出爐;(6)錠坯扒皮:采用型號為CD6140A的車床對真空電弧爐熔煉后的錠坯進行扒皮處理:該錠坯冷卻后自動收縮,與水冷銅坩堝分離,從表皮往錠坯中心3~4mm的部分通過車加工消除掉;(7)真空自耗凝殼爐熔煉:采用150kg真空自耗電極凝殼爐進行熔煉,配備高純石墨模具進行澆鑄;首先將石墨模具在真空烘箱內(nèi)進行除氣處理,加熱溫度為500℃,烘烤時間為12h;將烘烤后的石墨模具置于真空凝殼爐內(nèi),并用鐵絲將石墨模具固定住,使?jié)驳揽趯适>咧行?。然后使所述真空凝殼爐的真空度保持在0.08Pa,以16000A的電流對上一步得到的錠坯作為電極進行熔煉(熔煉后的液體滴入結(jié)晶器中),熔煉電壓控制在34V,待8分鐘后停止供電,啟動自動澆注系統(tǒng)進行澆鑄(將熔煉得到的合金液通過澆道口流入石墨模具內(nèi));澆鑄完后保持爐內(nèi)真空度在0.09Pa,隨爐冷卻至室溫后出爐,得到相應的合金鑄錠;(8)機加工步驟:對上一步得到的合金鑄錠按照圖紙進行機加工,清洗后得到所需要的成品靶材。本實施例制備的合金鑄錠的性能參見表1。采用與實施例1中相同的超聲波探傷檢驗方法對實施例2制備的錠坯進行檢驗,鑄錠切片的超聲波探傷圖參見圖2,無皮下氣泡。實施例3本實施例制備的鈦鋁合金靶材按重量百分比由以下元素組成:Ti70%,Al30%。制造方法如下:(1)配料:按上述合金成分設計分別稱取0級海綿鈦和純度高于99.99%的金屬鋁;(2)烘料:將稱好的原材料鈦和鋁放入真空烘箱(真空度為5000Pa)中,在145℃條件下保溫5h,隨爐降溫至37℃取出待用;(3)壓電極:鋁塊用鋁箔包好,海綿鈦分為兩部分,先往四柱電極壓制機的模具內(nèi)倒入一部分海綿鈦,然后將鋁塊包放入模具內(nèi),最后將剩余的海綿鈦倒入模具內(nèi);該四柱電極壓制機為市售產(chǎn)品;(4)焊接電極:采用鎢極氬弧焊將5根壓制好的電極首尾在一起,焊接的材料是純鈦焊絲;(5)真空自耗電弧爐熔煉:采用650kg真空自耗電極電弧爐進行熔煉,配備直徑為¢190mm的水冷銅坩堝;首先使真空自耗電極電弧爐的真空度保持在0.07Pa,以6000A的電流進行熔煉(熔煉后的液體滴入結(jié)晶器——水冷銅坩堝中),熔煉電壓控制在32V左右,待28分鐘后停爐冷卻,并保持爐內(nèi)真空度在0.07Pa,隨爐冷卻至300℃出爐;(6)錠坯扒皮:采用型號為CD6140A的車床對真空電弧爐熔煉后的錠坯進行扒皮處理:該錠坯冷卻后自動收縮,與水冷銅坩堝分離,從表皮往錠坯中心3~4mm的部分通過車加工消除掉;(7)真空自耗凝殼爐熔煉:采用150kg真空自耗電極凝殼爐進行熔煉,配備高純石墨模具進行澆鑄;首先將石墨模具在真空烘箱內(nèi)進行除氣處理,加熱溫度為600℃,烘烤時間為8h;將烘烤后的石墨模具置于真空凝殼爐內(nèi),并用鐵絲將石墨模具固定住,使?jié)驳揽趯适>咧行?;然后使所述真空凝殼爐的真空度保持在0.06Pa,以18000A的電流對上一步得到的錠坯作為電極進行熔煉(熔煉后的液體滴入結(jié)晶器中),熔煉電壓控制在32V,待6.5分鐘后停止供電,啟動自動澆注系統(tǒng)進行澆鑄(將熔煉得到的合金液通過澆道口流入石墨模具內(nèi));澆鑄完后保持爐內(nèi)真空度在0.06Pa,隨爐冷卻至室溫后出爐,得到相應的合金鑄錠;(8)機加工步驟:對上一步得到的合金鑄錠按照圖紙進行機加工,清洗后得到所需要的成品靶材。本實施例制備的合金鑄錠的性能參見表1。采用與實施例1中相同的超聲波探傷檢驗方法對實施例3制備的錠坯進行檢驗,鑄錠切片的超聲波探傷圖參見圖3,無皮下氣泡。為了進一步說明本發(fā)明的優(yōu)點,下面列舉了四個對比例。對比例1本對比例制備的鈦鋁合金靶材按重量百分比由以下元素組成:Ti64%,Al36%。制造方法為粉末燒結(jié)法,具體如下:(1)粉末制備:采用霧化干燥方法制得符合上述成分配比要求的鈦鋁合金粉末,平均粒徑為135μm;(2)冷等靜壓:將混合好的粉末裝入冷等靜壓模具中,在2噸壓力下壓制35min;(3)脫氣:將冷等靜壓坯放入預先備好的鐵包套中,置于脫氣爐中進行脫氣處理,脫氣溫度為420℃,脫氣時間為20h;(4)熱等靜壓燒結(jié):將脫氣完畢的包套放入熱等靜壓設備中壓制燒結(jié),溫度為1200℃,時間4h,壓力為120MPa;本對比例制備的合金靶材的性能參見表1。對比例2本實施例制備的鈦鋁合金靶材按重量百分比由以下元素組成:Ti64%,Al36%。制造方法為真空感應熔煉法,具體如下:(1)配料:按上述合金成分設計分別稱取0級海綿鈦和純度高于99.99%的金屬鋁;(2)烘料:將稱好的原材料鈦和鋁放入真空烘箱(真空度為5000Pa)中,在140℃條件下保溫5h,隨爐降溫至36℃取出待用;(3)裝爐:將烘烤后的原料(即爐料)中的金屬鋁放入25Kg真空感應爐CaO坩堝的底部,然后將海綿鈦松裝于金屬鋁的上部;(4)合金熔化:首先使真空感應爐的真空度保持為0.08Pa,再以13KW的電功率送電,待14分鐘后充入0.2atm的氬氣,然后加大送電功率至38KW,使原料快速熔化,以縮短合金液與坩堝的接觸時間,待送電12分鐘后合金熔化,熔化后合金液的最高溫度為1580℃;(5)降溫澆鑄:停電降溫28s,在合金液溫度為1520℃時進行澆鑄,從而得到合金鑄錠。本實施例制備的合金鑄錠的性能參見表1。采用與實施例1中相同的超聲波探傷檢驗方法對實施例2制備的錠坯進行檢驗,發(fā)現(xiàn)鑄錠切片中存在氣孔及鈦的富集等缺陷,經(jīng)過磨、拋處理,在掃描電鏡下觀察的氣孔缺陷及富鈦區(qū)參見圖4。圖中長方框體圈出的區(qū)域表示富鈦區(qū)域,中間的柱狀表示氣孔缺陷。對比例3本實施例制備的鈦鋁合金靶材按重量百分比由以下元素組成:Ti64%,Al36%。制造方法為冷坩堝、真空懸浮爐熔煉鑄造法,具體如下:(1)配料:按上述合金成分設計分別稱取0級海綿鈦和純度高于99.99%的金屬鋁;(2)壓電極:將海綿鈦和金屬鋁塊壓制成與水冷銅坩堝尺寸相適應的電極塊;(3)裝爐:將電極塊放入真空懸浮爐的水冷銅坩堝內(nèi);(4)合金熔化:首先使真空懸浮爐的真空度保持為0.03Pa,通電升溫,輸出電流為150A,輸出功率為45~55kW,使電極塊迅速熔化,熔煉時間7~10min;(5)降溫澆鑄:停電降溫60s,在合金液溫度為1650℃時進行自動澆鑄,從而得到合金鑄錠。本對比例制備的合金鑄錠的性能參見表1。采用線切割的方式將錠坯內(nèi)部切開,如圖5中長方框體圈出的區(qū)域所示,可以看到在距離錠坯底部1/3及其以上部分內(nèi)部存在嚴重的中心縮孔,疏松等缺陷,鑄錠切面圖參見圖5。對比例4該對比例省略了實施例1中的烘料步驟,其他與實施例1相同。本對比例制備的合金鑄錠的性能參見表1。采用與實施例1中相同的超聲波探傷檢驗方法對對比例3制備的錠坯進行檢驗,鑄錠切片的超聲波探傷圖參加圖6,圖中圈出的區(qū)域為內(nèi)部氣孔,尺寸為1~3mm。對比例5該對比例省略了實施例1中的扒皮步驟,其他與實施例1相同。本對比例制備的合金鑄錠的性能參見表1。采用與實施例1中相同的超聲波探傷檢驗方法對對比例4制備的錠坯進行檢驗,鑄錠切片的超聲波探傷圖參見圖7。圖中圈出的區(qū)域為內(nèi)部氣孔和夾雜物聚集區(qū)。表1:本發(fā)明實施例與對比例產(chǎn)品的性能表如表1所示,實施例1-3的合金靶材成分控制精確,主成分偏差≤0.5wt%,合金中外來夾雜Ca≤0.005wt%,氣體含量較低:C≤0.015wt%,N≤0.01wt%,O≤0.08wt%;而對比例1、2、5的合金靶材外來夾雜稍高:Ca≥0.01wt%,對比例1、2、4、5的氣體含量稍高:C≥0.017wt%,N≥0.01wt%,O≥0.07wt%。