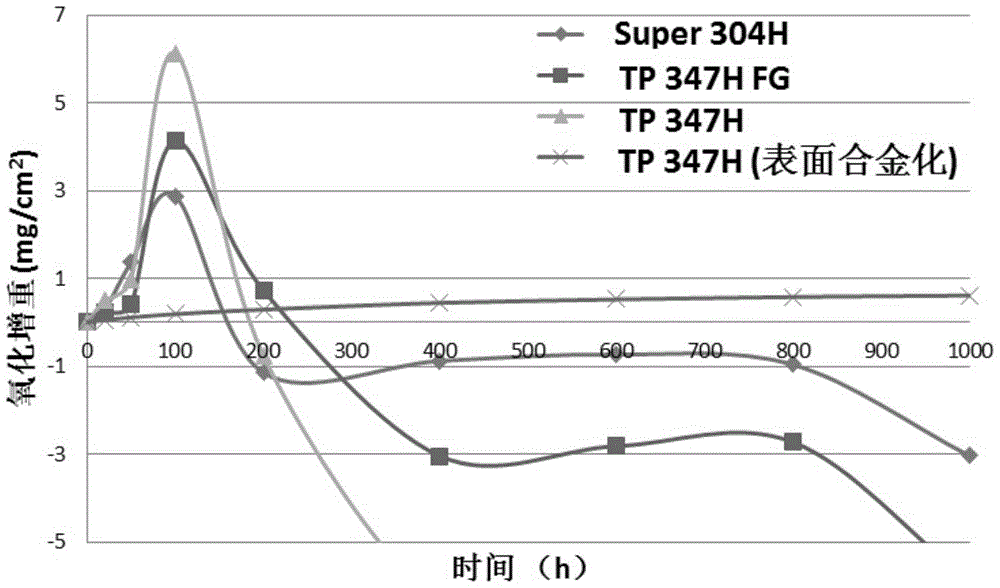
本發(fā)明屬于表面合金化及涂層技術(shù)領(lǐng)域,涉及一種鋼管表面合金化方法,具體涉及一種鍋爐過/再熱器用奧氏體不銹鋼管表面合金化方法。
背景技術(shù):過/再熱器部件是鍋爐中負(fù)責(zé)回收燃煤煙氣能量、加熱蒸汽、實現(xiàn)能量轉(zhuǎn)化的關(guān)鍵部件,是鍋爐中承受壓力最大、溫度最高、服役環(huán)境最苛刻的部分。奧氏體不銹鋼因具有足夠的高溫強(qiáng)度、持久強(qiáng)度、塑性、較好的抗氧化性能、沖擊性能、耐高溫蒸汽腐蝕以及耐煤灰磨損性能等,正越來越多的被作為鍋爐過/再熱器材料使用。包括TP304H,TP347H,Super304H,HR3C,NF709等。尤其隨著超超臨界技術(shù)的發(fā)展,奧氏體鋼是目前火電機(jī)組末級過/再熱器的首選材料之一。不銹鋼管的制作工藝決定了不銹鋼管的性能。目前,國內(nèi)外的鋼管生產(chǎn)企業(yè)對于火電機(jī)組鍋爐用奧氏體不銹鋼管的生產(chǎn)工藝主要由兩種制作工藝,分別為:1、熱軋(擠壓)的制作工藝。工藝流程包括圓管坯→加熱→熱擠壓→熱處理→冷拔→熱處理→矯直→酸洗→檢驗→標(biāo)記→入庫。2、冷軋的制作工藝。工藝流程圓管坯→穿孔→冷軋→熱處理→冷軋→熱處理→矯直→酸洗→檢驗→標(biāo)記→入庫。對于火電機(jī)組用的奧氏體不銹鋼管,兩種工藝在冷拔(軋)與矯直工序之間都需要進(jìn)行穩(wěn)定化熱處理工藝操作。研究表明,采用上述工藝制備的奧氏體不銹鋼管可滿足相關(guān)國標(biāo)要求。但奧氏體鋼作為鍋爐管道在服役過程中蒸汽側(cè)氧化膜具有雙層結(jié)構(gòu),內(nèi)層為Fe2Cr尖晶石層,外層為磁鐵礦層。由于粗晶奧氏體鋼與氧化皮熱膨脹系數(shù)差異大,氧化皮受較大層間力作用,比較容易剝落。流通管道內(nèi)剝落的氧化膜一方面會堵塞過、再熱器管從而引發(fā)爆管事故,另一方面被高流速蒸汽攜帶出過/再熱器(末級過熱器管內(nèi)流速19m/s,再熱器37m/s)并經(jīng)調(diào)門、噴嘴加速后損傷汽輪機(jī)高壓級和中壓級的前幾級葉片。尤其是大容量鍋爐受熱面熱負(fù)荷高、管徑相對大,管圈長管內(nèi)表面積大,新投產(chǎn)的高參數(shù)、大容量機(jī)組大量應(yīng)用奧氏體不銹鋼,這些機(jī)組在運(yùn)行在一萬小時后停機(jī)中高溫受熱面管內(nèi)產(chǎn)生氧化皮的脫落,約四萬小時左右頻繁發(fā)生奧氏體不銹鋼管內(nèi)壁由于氧化物脫落堵塞造成超溫爆管,大大降低了機(jī)組停運(yùn)行后的可靠性。目前,表面合金化技術(shù)的熱點研究議題之一,是尋求能克服現(xiàn)役超超臨界電站鍋爐奧氏體鋼管服役過程中所面臨的氧化/腐蝕問題的相關(guān)技術(shù),并希望提供現(xiàn)役耐熱鋼材料在更高的蒸汽參數(shù)機(jī)組(600-650℃)上繼續(xù)使用的途徑。金屬表面合金化技術(shù)是通過擴(kuò)散工藝改變基體金屬表面層的成分和組織以保護(hù)基體金屬的防護(hù)技術(shù)。這種技術(shù)能夠在不影響合金基體性能的前提下,改善和滿足服役環(huán)境對合金表面功能的特殊要求。近年來,國外正在研發(fā)的技術(shù)主要包括高/低溫粉末改性滲鋁技術(shù)、腔道噴涂技術(shù)等。歐洲的“CoatingsforSupercriticalSteamCycles”(SUPERCOAT)研究項目主要采取了在耐熱鋼表面進(jìn)行700℃?zhèn)鹘y(tǒng)熱擴(kuò)散滲鋁的方法。然而傳統(tǒng)熱擴(kuò)散滲鋁方法存在制備效率低、能耗高等諸多問題,難以在鍋爐管道等大型構(gòu)件上經(jīng)濟(jì)性的實施。另外,傳統(tǒng)熱擴(kuò)散滲鋁通常需保溫數(shù)個小時才能實現(xiàn),增加了熱加工步驟和成本。納米技術(shù)的發(fā)展帶動了表面合金化的進(jìn)展。美國科學(xué)家以純鐵氮化為對象的研究表明:金屬表面納米化能夠加速其表面合金化進(jìn)程。進(jìn)一步研究發(fā)現(xiàn)低碳鋼表面納米化后,600℃時滲鋁層η-Fe2Al5的生長速率是原來的3倍,這一結(jié)果為解決耐熱鋼低溫滲鋁效率低下的問題提供了方案。但必須注意的是,滲層仍為η-Fe2Al5相,因而其存在的力學(xué)性能問題仍未能由表面納米化的方法解決。同時,鍋爐管道的表面納米化處理在技術(shù)可行性與成本方面還有待商榷。此外,對于內(nèi)徑較小的鍋爐管道來說,要對其內(nèi)壁作噴丸納米化處理,技術(shù)上也是一種挑戰(zhàn)。在國內(nèi),研究人員對鍋爐過/再熱器管道表面合金化技術(shù)也有一定程度的研究。西安熱工院早期采用了熱浸滲鋁技術(shù),在鍋爐管道表面形成了以FeAl為主相的合金化層,顯著提高了管道抗煙氣腐蝕能力,并在馬頭電廠得到了示范應(yīng)用。但是,受熱浸滲鋁工藝所限,能處理的管子比較短(2~3米),大大增加了施工中的焊接量,因而未能得到推廣。中國科學(xué)院金屬研究所發(fā)明了一種大氣條件下無保護(hù)氣氛或保護(hù)層的料漿高速滲鋁方法。該法將工件表面沉積滲鋁料漿,在無保護(hù)氣氛和保護(hù)層下直接對工件加熱,可以在工件表層獲得一定厚度的富鋁層。但對鍋爐使用的超長管內(nèi)壁實施此工藝,工藝性和可行性尚待確認(rèn)。
技術(shù)實現(xiàn)要素:本發(fā)明的目的在于克服上述現(xiàn)有技術(shù)的缺點,提供了一種鍋爐過/再熱器用奧氏體不銹鋼管表面合金化方法,該方法可以實現(xiàn)鍋爐過/再熱器用奧氏體不銹鋼管表面的合金化。為達(dá)到上述目的,本發(fā)明所述的鍋爐過/再熱器用奧氏體不銹鋼管表面合金化方法的具體操作為:對需要合金化的鍋爐過/再熱器用奧氏體不銹鋼管表面依次進(jìn)行料漿涂覆、烘干硬化及高溫?zé)Y(jié),其中,料漿由滲劑及粘結(jié)劑混合而成,滲劑與粘結(jié)劑的比例為80-120g∶100mL;所述烘干硬化的具體操作為:將料漿涂覆處理后的鍋爐過/再熱器用奧氏體不銹鋼管在室溫下放置1-5小時,然后再100-300℃的溫度下烘干硬化1-5小時;所述高溫?zé)Y(jié)的具體操作為:將經(jīng)過烘干硬化后的鍋爐過/再熱器用奧氏體不銹鋼管在850-920℃的溫度下熱處理30min-5h。所述滲劑由鋁粉、硅粉及鉻粉組成,其中,鋁粉、硅粉及鉻粉的質(zhì)量占滲劑的總質(zhì)量的比例分別為30-60%、15-45%及25-55%。所述粘結(jié)劑由濃度為10%-30%的磷酸鹽水溶液與鉻酐混合而成,其中,粘結(jié)劑中鉻酐所占質(zhì)量為1%-10%。所述鍋爐過/再熱器用奧氏體不銹鋼管表面涂覆的料漿的厚度為30-500微米。本發(fā)明具有以下有益效果:本發(fā)明所述的鍋爐過/再熱器用奧氏體不銹鋼管表面合金化方法在對鍋爐過/再熱器用奧氏體不銹鋼管表面合金化過程中,先分別依次對需要合金化的鍋爐過/再熱器用奧氏體不銹鋼管表面依次進(jìn)行料漿涂覆、烘干硬化及高溫?zé)Y(jié),所述漿料由滲劑及粘結(jié)劑混合而成,滲劑與粘結(jié)劑的比例為80-120g∶100mL,從而實現(xiàn)鍋爐過/再熱器用奧氏體不銹鋼管表面的合金化,可以使經(jīng)合金化的鍋爐過/再熱器用奧氏體不銹鋼管表面達(dá)到完成抗氧化級,操作簡單、方便。附圖說明圖1為本發(fā)明的實施例一中處理后的鍋爐過/再熱器用奧氏體不銹鋼管表面的截面圖;圖2為本發(fā)明的實施例一中處理后的鍋爐過/再熱器用奧氏體不銹鋼管表面在750℃純蒸汽環(huán)境中的氧化動力學(xué)曲線。具體實施方式下面結(jié)合附圖及實施例對本發(fā)明做進(jìn)一步詳細(xì)描述:實施例一對TP347H鋼管表面進(jìn)行合金化,本發(fā)明所述的鍋爐過/再熱器用奧氏體不銹鋼管表面合金化方法的具體操作為:對需要合金化的鍋爐過/再熱器用奧氏體不銹鋼管表面依次進(jìn)行料漿涂覆、烘干硬化及高溫?zé)Y(jié),其中,料漿由滲劑及粘結(jié)劑混合而成,滲劑與粘結(jié)劑的比例為100g∶100mL;所述烘干硬化的具體操作為:將料漿涂覆處理后的鍋爐過/再熱器用奧氏體不銹鋼管在室溫下放置3小時,然后再200℃的溫度下烘干硬化2小時;所述高溫?zé)Y(jié)的具體操作為:將經(jīng)過烘干硬化后的鍋爐過/再熱器用奧氏體不銹鋼管在890℃的溫度下熱處理1h。所述滲劑由鋁粉、硅粉及鉻粉組成,其中,鋁粉、硅粉及鉻粉的質(zhì)量占滲劑的總質(zhì)量的比例分別為60%、15%及25%。所述粘結(jié)劑由濃度為30%的磷酸鹽水溶液與鉻酐混合而成,其中,粘結(jié)劑中鉻酐所占質(zhì)量為10%。所述鍋爐過/再熱器用奧氏體不銹鋼管表面涂覆的料漿的厚度為150微米。實施例二本發(fā)明所述的鍋爐過/再熱器用奧氏體不銹鋼管表面合金化方法的具體操作為:對需要合金化的鍋爐過/再熱器用奧氏體不銹鋼管表面依次進(jìn)行料漿涂覆、烘干硬化及高溫?zé)Y(jié),其中,料漿由滲劑及粘結(jié)劑混合而成,滲劑與粘結(jié)劑的比例為80g∶100mL;所述烘干硬化的具體操作為:將料漿涂覆處理后的鍋爐過/再熱器用奧氏體不銹鋼管在室溫下放置1小時,然后再300℃的溫度下烘干硬化1小時;所述高溫?zé)Y(jié)的具體操作為:將經(jīng)過烘干硬化后的鍋爐過/再熱器用奧氏體不銹鋼管在920℃的溫度下熱處理30min。所述滲劑由鋁粉、硅粉及鉻粉組成,其中,鋁粉、硅粉及鉻粉的質(zhì)量占滲劑的總質(zhì)量的比例分別為30%、45%及25%。所述粘結(jié)劑由濃度為10%的磷酸鹽水溶液與鉻酐混合而成,其中,粘結(jié)劑中鉻酐所占質(zhì)量為1%。所述鍋爐過/再熱器用奧氏體不銹鋼管表面涂覆的料漿的厚度為30微米。實施例三本發(fā)明所述的鍋爐過/再熱器用奧氏體不銹鋼管表面合金化方法的具體操作為:對需要合金化的鍋爐過/再熱器用奧氏體不銹鋼管表面依次進(jìn)行料漿涂覆、烘干硬化及高溫?zé)Y(jié),其中,料漿由滲劑及粘結(jié)劑混合而成,滲劑與粘結(jié)劑的比例為120g∶100mL;所述烘干硬化的具體操作為:將料漿涂覆處理后的鍋爐過/再熱器用奧氏體不銹鋼管在室溫下放置5小時,然后再100℃的溫度下烘干硬化5小時;所述高溫?zé)Y(jié)的具體操作為:將經(jīng)過烘干硬化后的鍋爐過/再熱器用奧氏體不銹鋼管在850℃的溫度下熱處理30min。所述滲劑由鋁粉、硅粉及鉻粉組成,其中,鋁粉、硅粉及鉻粉的質(zhì)量占滲劑的總質(zhì)量的比例分別為30%、15%及55%。所述粘結(jié)劑由濃度為15%的磷酸鹽水溶液與鉻酐混合而成,其中,粘結(jié)劑中鉻酐所占質(zhì)量為5%。所述鍋爐過/再熱器用奧氏體不銹鋼管表面涂覆的料漿的厚度為500微米。實施例四本發(fā)明所述的鍋爐過/再熱器用奧氏體不銹鋼管表面合金化方法的具體操作為:對需要合金化的鍋爐過/再熱器用奧氏體不銹鋼管表面依次進(jìn)行料漿涂覆、烘干硬化及高溫?zé)Y(jié),其中,料漿由滲劑及粘結(jié)劑混合而成,滲劑與粘結(jié)劑的比例為90g∶100mL;所述烘干硬化的具體操作為:將料漿涂覆處理后的鍋爐過/再熱器用奧氏體不銹鋼管在室溫下放置3小時,然后再150℃的溫度下烘干硬化2小時;所述高溫?zé)Y(jié)的具體操作為:將經(jīng)過烘干硬化后的鍋爐過/再熱器用奧氏體不銹鋼管在880℃的溫度下熱處理1h。所述滲劑由鋁粉、硅粉及鉻粉組成,其中,鋁粉、硅粉及鉻粉的質(zhì)量占滲劑的總質(zhì)量的比例分別為40%、25%及35%。所述粘結(jié)劑由濃度為12%的磷酸鹽水溶液與鉻酐混合而成,其中,粘結(jié)劑中鉻酐所占質(zhì)量為4%。所述鍋爐過/再熱器用奧氏體不銹鋼管表面涂覆的料漿的厚度為100微米。實施例五本發(fā)明所述的鍋爐過/再熱器用奧氏體不銹鋼管表面合金化方法的具體操作為:對需要合金化的鍋爐過/再熱器用奧氏體不銹鋼管表面依次進(jìn)行料漿涂覆、烘干硬化及高溫?zé)Y(jié),其中,料漿由滲劑及粘結(jié)劑混合而成,滲劑與粘結(jié)劑的比例為110g∶100mL;所述烘干硬化的具體操作為:將料漿涂覆處理后的鍋爐過/再熱器用奧氏體不銹鋼管在室溫下放置4小時,然后再250℃的溫度下烘干硬化4小時;所述高溫?zé)Y(jié)的具體操作為:將經(jīng)過烘干硬化后的鍋爐過/再熱器用奧氏體不銹鋼管在910℃的溫度下熱處理3h。所述滲劑由鋁粉、硅粉及鉻粉組成,其中,鋁粉、硅粉及鉻粉的質(zhì)量占滲劑的總質(zhì)量的比例分別為50%、20%及30%。所述粘結(jié)劑由濃度為22%磷酸鹽水溶液與鉻酐混合而成,其中,粘結(jié)劑中鉻酐所占質(zhì)量為6%。所述鍋爐過/再熱器用奧氏體不銹鋼管表面涂覆的料漿的厚度為180微米。實施例六本發(fā)明所述的鍋爐過/再熱器用奧氏體不銹鋼管表面合金化方法的具體操作為:對需要合金化的鍋爐過/再熱器用奧氏體不銹鋼管表面依次進(jìn)行料漿涂覆、烘干硬化及高溫?zé)Y(jié),其中,料漿由滲劑及粘結(jié)劑混合而成,滲劑與粘結(jié)劑的比例為95g∶100mL;所述烘干硬化的具體操作為:將料漿涂覆處理后的鍋爐過/再熱器用奧氏體不銹鋼管在室溫下放置3.5小時,然后再220℃的溫度下烘干硬化3.5小時;所述高溫?zé)Y(jié)的具體操作為:將經(jīng)過烘干硬化后的鍋爐過/再熱器用奧氏體不銹鋼管在910℃的溫度下熱處理2.5h。所述滲劑由鋁粉、硅粉及鉻粉組成,其中,鋁粉、硅粉及鉻粉的質(zhì)量占滲劑的總質(zhì)量的比例分別為30%、30%及40%。所述粘結(jié)劑由濃度為25%的磷酸鹽水溶液與鉻酐混合而成,其中,粘結(jié)劑中鉻酐所占質(zhì)量為9%。所述鍋爐過/再熱器用奧氏體不銹鋼管表面涂覆的料漿的厚度為250微米。圖1為合金化層的截面形貌,由圖可知,合金化層厚度為90微米,主要由內(nèi)外兩層組成,外層含少量孔洞及氧化物夾雜,涂層中平均Al含量33%,Si含量8%,Cr含量12%,其余為Fe,圖2為幾種合金在750℃下純蒸汽環(huán)境中的氧化動力學(xué)曲線,可以發(fā)現(xiàn),TP347H,TP347HFG,Super304H合金均出現(xiàn)了氧化失重,表明氧化膜發(fā)生了剝落現(xiàn)象,而表面合金化的TP347H具有最低的氧化速率,氧化增重趨勢符合拋物線規(guī)律,在此條件下,達(dá)到了完全抗氧化級。