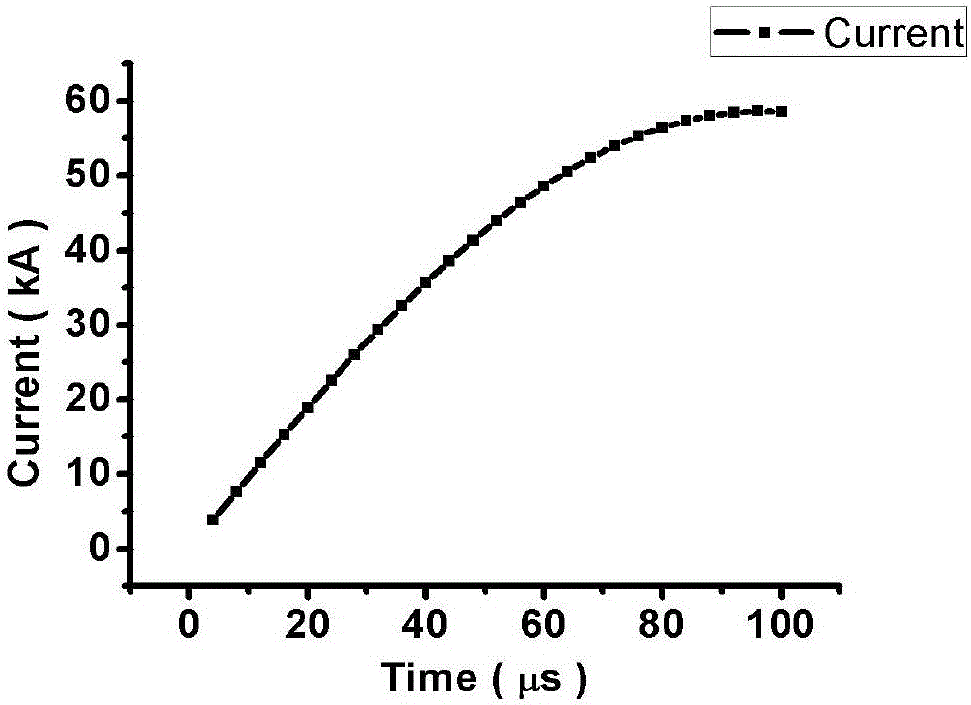
本發(fā)明屬于金屬成形制造
技術(shù)領(lǐng)域:
,更具體地,涉及一種勻壓力電磁成形的裝置、勻壓力線圈及其獲取方法。
背景技術(shù):
:電磁成形是變化的磁場與金屬材料中感應(yīng)渦流相互作用、產(chǎn)生瞬間電磁沖擊力而導(dǎo)致的一種高速變形,作為一種高能高速率成形技術(shù),電磁成形在提高鋁合金等輕質(zhì)合金材料成形制造水平、突破一些關(guān)鍵技術(shù)瓶頸方面潛力巨大。在電磁成形中,用于平板電磁成形的一般為平面螺旋線圈,但平面螺旋線圈在工件上產(chǎn)生的電磁力分布不均勻,制約了它的應(yīng)用范圍。勻壓力線圈作為一種新型線圈,能夠在工件上形成比較均勻的電磁力,成形效率比平螺旋線圈更高,在成形車門型腔、手機(jī)殼和燃料電池板等組件上具有顯著優(yōu)勢(shì),因此受到了廣泛的關(guān)注。圖1為勻壓力線圈原理圖,在線圈外面有一個(gè)凹形導(dǎo)電通道,導(dǎo)電通道和線圈之間絕緣良好并且和成形工件組成了一個(gè)封閉的回路。當(dāng)電容放電時(shí),在工作線圈中產(chǎn)生變化的電流,同時(shí)在外面的回路中感應(yīng)出方向相反的感應(yīng)電流。由于工件與導(dǎo)電通道形成了回路,因此工件中的感應(yīng)電流方向、大小相同,所受到的電磁力比較均勻,再加上感應(yīng)電流回路完全環(huán)繞線圈,所以磁場能量損失較小,效率較高。在目前有關(guān)勻壓力線圈的研究中,為了確保足夠的結(jié)構(gòu)強(qiáng)度,使線圈在電磁成形過程中不至于應(yīng)力過大而變形,常將銅塊或銅合金塊直接進(jìn)行切割得到線圈。這種方法通過線圈自身的強(qiáng)度來保證整體結(jié)構(gòu)的強(qiáng)度,因而得到的勻壓力線圈必須要有較厚的線圈橫截面,使得線圈中電流密度較小,進(jìn)而導(dǎo)致工件受到的電磁力較小,限制了線圈的成形效率。此外,將銅塊切割為勻壓力線圈形狀技術(shù)復(fù)雜、切割耗時(shí)較長。這些技術(shù)缺陷直接制約了勻壓力線圈的應(yīng)用以及相關(guān)領(lǐng)域的研究和發(fā)展。技術(shù)實(shí)現(xiàn)要素:針對(duì)現(xiàn)有技術(shù)的缺陷,本發(fā)明的目的在于提供一種勻壓力電磁成形的裝置,旨在解決現(xiàn)有技術(shù)中線圈的成形效率低的問題。本發(fā)明提供了一種勻壓力電磁成形的裝置,包括:導(dǎo)電通道、線圈和工件;U形導(dǎo)電通道設(shè)置在線圈的上方包圍線圈,工件設(shè)置在線圈的下方,工件與導(dǎo)電通道形成電流回路;線圈包括:導(dǎo)線,環(huán)氧板和加固材料;由環(huán)氧板構(gòu)成的骨架為導(dǎo)線提供支撐;加固材料設(shè)置在導(dǎo)線外側(cè)作為外加固層,用于提供足夠的強(qiáng)度;工作時(shí),受線圈中變化電流的影響,工件與導(dǎo)電通道中感應(yīng)出了渦流,形成了電流回路,且工件中的感應(yīng)電流方向、大小相同,則工件受到的電磁力比較均勻;由于線圈選用較薄的紫銅導(dǎo)線纏繞多層多匝而成,因此工件中所受電磁力更大,成形效率更高;為保證線圈強(qiáng)度,將加固材料分別沿著線圈導(dǎo)線繞制的方向和垂直于導(dǎo)線繞制的方向進(jìn)行纏繞加固,實(shí)現(xiàn)高強(qiáng)高效勻壓力電磁成形。更進(jìn)一步地,導(dǎo)線為任意橫截面積(不小于最小橫截面積)的紫銅導(dǎo)線。更進(jìn)一步地,當(dāng)導(dǎo)線的厚度小于透入深度時(shí),導(dǎo)線越薄電流密度越大,感應(yīng)產(chǎn)生的電流密度也越大,工件上所受電磁力越大,成形效率更高;其中,電流在銅上的透入深度f為電流頻率,μ為磁導(dǎo)率,γ為電導(dǎo)率。更進(jìn)一步地,導(dǎo)線的橫截面積其中,ΔT為銅導(dǎo)線最大溫升,ρ1為銅的電阻率,c為比熱容,ρ2為銅的質(zhì)量密度,trise為線圈電流波形第一個(gè)上升沿時(shí)間,I(t)為線圈電流與時(shí)間的關(guān)系,t為時(shí)間。更進(jìn)一步地,加固材料沿著導(dǎo)線繞制的方向和垂直于導(dǎo)線繞制的方向分別進(jìn)行纏繞加固。更進(jìn)一步地,加固材料為玻璃纖維或柴龍(zylon)。本發(fā)明提供了一種勻壓力線圈的獲取方法,包括下述步驟:(1)將環(huán)氧板固定在繞線機(jī)上,并將銅導(dǎo)線按照預(yù)先設(shè)置的最小匝間距纏繞在環(huán)氧軸心上;(2)采用W19環(huán)氧樹脂,并按照胺的用量(phr)=胺當(dāng)量×環(huán)氧值來配置固化劑,將配置好的環(huán)氧樹脂固化劑涂抹在纏繞好的導(dǎo)線上;其中,phr指每100份樹脂所需固化劑的質(zhì)量份數(shù),胺當(dāng)量=胺的相對(duì)分子量÷胺中活潑氫的個(gè)數(shù),環(huán)氧值指100g環(huán)氧樹脂中所含環(huán)氧基團(tuán)的物質(zhì)的量;(3)涂抹完環(huán)氧樹脂后,根據(jù)仿真時(shí)線圈所受最大強(qiáng)度選擇加固材料,并將加固材料在線圈上均勻的纏繞一層;(4)重復(fù)步驟(2),在加固材料上均勻的涂抹環(huán)氧樹脂,完成一層導(dǎo)線的繞制;(5)重復(fù)步驟(1)-(4),完成多層多匝勻壓力線圈的繞制。更進(jìn)一步地,所述加固材料為極限強(qiáng)度為4.9GPa的S-2玻璃纖維。更進(jìn)一步地,在步驟(3)中,沿著導(dǎo)線繞制方向與垂直于導(dǎo)線繞制方向分別在線圈上均勻的纏繞一層。本發(fā)明提供了一種基于上述的獲取方法得到的勻壓力線圈,包括:導(dǎo)線,環(huán)氧板和加固材料;由環(huán)氧板構(gòu)成的骨架為導(dǎo)線提供支撐;加固材料設(shè)置在導(dǎo)線外側(cè)作為外加固層,用于提供足夠的強(qiáng)度。通過本發(fā)明所構(gòu)思的以上技術(shù)方案,與現(xiàn)有技術(shù)相比,由于采用環(huán)氧板作為內(nèi)支撐;在繞制工藝上纏繞加固材料進(jìn)行外加固,并分別沿著導(dǎo)線繞制方向和垂直于導(dǎo)線繞制方向纏繞,在各個(gè)方向上為線圈提供了充足的強(qiáng)度,極大的提高了線圈的整體強(qiáng)度,譬如S-2玻璃纖維極限強(qiáng)度為4.9GPa左右,遠(yuǎn)大于各種銅類的極限強(qiáng)度。且在本發(fā)明中,由于單匝導(dǎo)線更薄,最大限度的降低了集膚效應(yīng)的影響,節(jié)省的空間用于繞制的多層線圈具有更高的成形效率。結(jié)構(gòu)更靈活,可以根據(jù)實(shí)際需要采用任意橫截面積(不小于最小橫截面積)的銅導(dǎo)線繞制任意匝數(shù)與層數(shù)的線圈。本發(fā)明采用銅導(dǎo)線繞制線圈的方式更加簡單,高效。附圖說明圖1是勻壓力線圈的原理示意圖;圖2是一次采用勻壓力線圈進(jìn)行電磁成形實(shí)驗(yàn)的電流時(shí)間關(guān)系圖;圖3是三種線圈在工件上正中心一點(diǎn)處產(chǎn)生的電磁力大小對(duì)比圖;圖4是本發(fā)明所述的一種單層勻壓力線圈橫截面示意圖。在所有附圖中,其中:1為導(dǎo)電通道,2為線圈,3為工件,2-1為導(dǎo)線,2-2為環(huán)氧板,2-3為玻璃纖維。具體實(shí)施方式為了使本發(fā)明的目的、技術(shù)方案及優(yōu)點(diǎn)更加清楚明白,以下結(jié)合附圖及實(shí)施例,對(duì)本發(fā)明進(jìn)行進(jìn)一步詳細(xì)說明。應(yīng)當(dāng)理解,此處所描述的具體實(shí)施例僅僅用以解釋本發(fā)明,并不用于限定本發(fā)明。針對(duì)上述問題,本發(fā)明提供了一種具有高強(qiáng)度的繞制勻壓力線圈的方法,旨在解決現(xiàn)有技術(shù)中線圈電流密度較小、成形效率較低、線圈加工復(fù)雜以及加工時(shí)間較長的技術(shù)問題。本發(fā)明中,為了提高成形效率,不再采用銅塊切割獲取勻壓力線圈,而是選用較薄的紫銅導(dǎo)線(單玻璃絲包聚酰亞胺薄膜繞包扁銅線)纏繞形成多層多匝的勻壓力線圈;同時(shí),由于薄導(dǎo)線自身強(qiáng)度較低無法承受電磁成形過程中的電磁力,選用特定的加固材料作為外加固,環(huán)氧板作為內(nèi)支撐來提高線圈整體的強(qiáng)度。根據(jù)電磁感應(yīng)定律,工件上所受到的電磁力為:其中為工件中的感應(yīng)電流,為線圈在工件處產(chǎn)生的磁場與工件內(nèi)渦流在同一點(diǎn)產(chǎn)生的磁場矢量和。感應(yīng)電流密度越大,工件上所受電磁力也就越大,成形效率越高。根據(jù)集膚效應(yīng),電流在銅上的透入深度為:其中,f為電流頻率,μ為磁導(dǎo)率,γ為電導(dǎo)率。對(duì)于電磁成形而言,以一次典型的電磁成形實(shí)驗(yàn)為例,線圈內(nèi)電流大小如圖2所示,μ銅=μ0=4π×10-7H/m,γ銅=5.8×107S/m,帶入式(2)得透入深度為1.33mm。因此對(duì)于多層線圈,當(dāng)導(dǎo)線厚度大于透入深度時(shí),多出來的部分不但對(duì)成形沒有幫助,反而使得內(nèi)層導(dǎo)線離工件更遠(yuǎn),降低成形效率;當(dāng)導(dǎo)線厚度小于透入深度時(shí),導(dǎo)線越薄,電流密度越大,因而感應(yīng)產(chǎn)生的電流密度也越大,工件上所受電磁力越大,成形效率更高。為了證實(shí)采用薄銅導(dǎo)線繞制的線圈成形效率更高,此處對(duì)線圈橫截面尺寸為4mm×1mm的單層線圈,4mm×4mm的單層線圈與4mm×1mm的雙層線圈進(jìn)行分析,線圈匝數(shù)均為16匝,匝間距均為0.5mm。3種線圈電感求得如表1所示,在160μF、10kV電源下對(duì)線圈放電(線路電阻10mΩ,線路電感5μH),得到的工件上中心點(diǎn)的電磁力隨時(shí)間變化的曲線圖如圖3所示,由圖3可知4mm×1mm的雙層線圈在工件上產(chǎn)生的電磁力最大,4mm×4mm的單層線圈在工件上產(chǎn)生的電磁力最小,因此本文提出的采用薄銅導(dǎo)線繞制的多層線圈成形效率更高。表1不同橫截面線圈電感值4mm×1mm,一層4mm×4mm,一層4mm×1mm,雙層電感(μH)5.013.9817.6然而,薄銅導(dǎo)線并不是越薄越好,考慮到發(fā)熱問題,薄銅導(dǎo)線的溫升不能超過規(guī)定值,因此導(dǎo)線的橫截面積不能低于某一特定值。銅導(dǎo)線的溫度指數(shù)根據(jù)其包含的聚酰亞胺薄膜和粘結(jié)漆的溫度指數(shù)來決定,取其中最低的溫度指數(shù)。根據(jù)方程組(3):可得導(dǎo)線的截面積的表達(dá)式(4):其中,R為導(dǎo)線電阻,ρ1為電阻率,L為導(dǎo)線長度,A為導(dǎo)線橫截面積,Q為導(dǎo)線產(chǎn)生的熱量,I為導(dǎo)線內(nèi)電流大小,t為通流時(shí)間,ΔT為導(dǎo)線溫升,c為導(dǎo)線材料比熱容,m為導(dǎo)線質(zhì)量,ρ2為導(dǎo)線材料質(zhì)量密度。考慮到單玻璃絲包聚酰亞胺薄膜繞包扁銅線耐受溫度為155℃,因此在室溫條件下,溫升ΔT≤130℃,其他常數(shù)如銅導(dǎo)線電阻率ρ1=1.75×10-8Ω·m,,比熱容c=0.39×103J/(kg·℃),紫銅質(zhì)量密度ρ2=8.92×103kg/m3。根據(jù)圖2的電流數(shù)據(jù),對(duì)式(4)做定積分,可得:因此,電磁繞組線最小橫截面積為2.62。為實(shí)現(xiàn)上述目的,按照上述思想,提供了一種具有高強(qiáng)度的用于電磁成形的勻壓力線圈獲取方法,具體可以通過勻壓力電磁成形的裝置來實(shí)現(xiàn)勻壓力線圈的獲取,其中勻壓力電磁成形的裝置包括:導(dǎo)電通道1、線圈2、工件3;導(dǎo)電通道1設(shè)置在線圈2的上方,工件3設(shè)置在線圈2的下方,與導(dǎo)電通道形成電流回路;線圈2由導(dǎo)線2-1,環(huán)氧板2-2,加固材料2-3組成,環(huán)氧板2-2固定在導(dǎo)線內(nèi)層作為支撐,導(dǎo)線可以采用任意截面積(不小于最小橫截面積)的紫銅導(dǎo)線,而不是必須采用銅塊進(jìn)行切割,加固材料在導(dǎo)線外層作為外加固層,為了對(duì)線圈提供足夠的強(qiáng)度,加固材料需分別沿著導(dǎo)線繞制的方向和垂直于導(dǎo)線繞制的方向分別進(jìn)行纏繞加固。在本發(fā)明實(shí)施例中,用于磁體繞制的加固材料可以有多種,具體可以為玻璃纖維或柴龍(zylon)等。在本發(fā)明實(shí)施例中,多層多匝勻壓力線圈獲取方法具體包括如下步驟:(1)將環(huán)氧板固定在繞線機(jī)上,由于匝間距越小,工件上的受力越均勻,再加上銅導(dǎo)線外層的漆包線厚度為0.25mm,因此將銅導(dǎo)線按照0.5mm的最小匝間距纏繞在環(huán)氧軸心上;(2)選用用于緊固線圈的W19環(huán)氧樹脂,按照胺的用量(phr)=胺當(dāng)量×環(huán)氧值配置固化劑(W19環(huán)氧樹脂及其固化劑配比如表2所示),其中phr指每100份樹脂所需固化劑的質(zhì)量份數(shù),胺當(dāng)量=胺的相對(duì)分子量÷胺中活潑氫的個(gè)數(shù),環(huán)氧值指100g環(huán)氧樹脂中所含環(huán)氧基團(tuán)的物質(zhì)的量。隨后將配置好的環(huán)氧樹脂均勻的涂抹在纏繞好的導(dǎo)線上;(3)涂抹完環(huán)氧樹脂后,根據(jù)仿真時(shí)線圈所受最大強(qiáng)度選擇加固材料,常用加固材料及其強(qiáng)度如表3所示。隨后將加固材料沿著導(dǎo)線繞制方向與垂直于導(dǎo)線繞制方向分別在線圈上均勻的纏繞一層;(4)重復(fù)步驟(2),在加固材料上均勻的涂抹環(huán)氧樹脂,完成一層導(dǎo)線的繞制;(5)重復(fù)步驟(1)-(4),完成多層多匝勻壓力線圈的繞制。表2W19環(huán)氧樹脂及其固化劑配比表3用于線圈加固的加固材料S-2玻璃纖維柴龍(Zylon)抗拉強(qiáng)度(GPa)4.95.8彈性模量(GPa)87280延展率(%)42.5總體而言,本發(fā)明所構(gòu)思的以上技術(shù)方案與現(xiàn)有技術(shù)相比,有如下優(yōu)點(diǎn):(1)線圈強(qiáng)度更高,在結(jié)構(gòu)設(shè)計(jì)方面采用環(huán)氧板作為內(nèi)支撐;在繞制工藝上纏繞加固材料進(jìn)行外加固,并分別沿著導(dǎo)線繞制方向和垂直于導(dǎo)線繞制方向纏繞,在各個(gè)方向上為線圈提供了充足的強(qiáng)度,極大的提高了線圈的整體強(qiáng)度,譬如S-2玻璃纖維極限強(qiáng)度為4.9GPa左右,遠(yuǎn)大于各種銅類的極限強(qiáng)度。(2)線圈成形效率更高。由于單匝導(dǎo)線更薄,最大限度的降低了集膚效應(yīng)的影響,節(jié)省的空間用于繞制的多層線圈具有更高的成形效率。結(jié)構(gòu)更靈活。可以根據(jù)實(shí)際需要采用任意橫截面積(不小于最小橫截面積)的銅導(dǎo)線繞制任意匝數(shù)與層數(shù)的線圈。(3)線圈加工簡單。相比于采用銅塊進(jìn)行線切割,采用銅導(dǎo)線繞制線圈的方式更加簡單,高效。為了使本發(fā)明的目的、技術(shù)方案及優(yōu)點(diǎn)更加清楚明白,以下結(jié)合圖4及具體實(shí)施例進(jìn)一步詳細(xì)說明如下:如圖4所示,為本發(fā)明實(shí)施例提供的一種雙層勻壓力線圈橫截面示意圖,其中導(dǎo)線2-1為銅導(dǎo)線,加固材料2-3為玻璃纖維,圖中由環(huán)氧板2-2構(gòu)成的骨架為導(dǎo)線提供支撐。以該雙層勻壓力線圈為例,線圈具體繞制過程如下:步驟一:將環(huán)氧板固定在繞線機(jī)上,將銅導(dǎo)線按照設(shè)定好的匝間距纏繞在環(huán)氧軸心上。步驟二:選用W19環(huán)氧樹脂,按表2中比例要求配好固化劑,若固化劑太少,則環(huán)氧樹脂無法固化,隨后纏繞的玻璃纖維無法緊固在線圈上,使線圈強(qiáng)度降低;若固化劑太多,則在繞制線圈的過程中環(huán)氧樹脂便已固化,影響線圈的制作過程。將配好固化劑的環(huán)氧樹脂均勻地涂抹在纏繞好的導(dǎo)線上,由于環(huán)氧樹脂分子鏈中固有的極性羥基和醚鍵的存在,使其對(duì)各種物質(zhì)具有很高的粘附力,再加上固化時(shí)環(huán)氧樹脂的收縮性低,產(chǎn)生的內(nèi)應(yīng)力小,這也有助于提高粘附強(qiáng)度;此外,在環(huán)氧樹脂固化之前,由于環(huán)氧/固化劑體系存在大量帶有極性或強(qiáng)極性官能基的低分子化合物,此時(shí)它們的電氣性能都很差,隨著固化反應(yīng)的進(jìn)行,活性基團(tuán)大量消耗,分子量逐漸增大,以至三度交聯(lián)網(wǎng)逐漸形成,在這個(gè)過程中,它們的電絕緣能力得到了極大的提高。因此固化之后的環(huán)氧樹脂粘附性強(qiáng)并且介電性能良好,能夠很好地固定住線圈導(dǎo)線并提供足夠的絕緣強(qiáng)度。步驟三:涂抹完環(huán)氧樹脂后,再沿著導(dǎo)線繞制方向和垂直于導(dǎo)線繞制方向上均勻纏繞一層玻璃纖維,使玻璃纖維能夠均勻地在各個(gè)方向上為線圈提供機(jī)械強(qiáng)度并保證線圈表面平整。步驟四:交替重復(fù)步驟二與步驟三若干次,次數(shù)根據(jù)具體實(shí)驗(yàn)中線圈所需承受的最大電磁力決定。若次數(shù)太少,會(huì)導(dǎo)致強(qiáng)度不夠線圈脹裂;若次數(shù)太多,則由于玻璃纖維層過厚使得線圈導(dǎo)線與工件間距離過遠(yuǎn)而降低成形效率;5-8次,以提供足夠的機(jī)械強(qiáng)度。步驟五:在玻璃纖維上均勻的涂抹環(huán)氧樹脂,保證玻璃纖維完全粘附在導(dǎo)線上。到此一層導(dǎo)線便繞制完成。步驟六:重復(fù)步驟一至五,完成第二層導(dǎo)線的繞制。本領(lǐng)域的技術(shù)人員容易理解,以上所述僅為本發(fā)明的較佳實(shí)施例而已,并不用以限制本發(fā)明,凡在本發(fā)明的精神和原則之內(nèi)所作的任何修改、等同替換和改進(jìn)等,均應(yīng)包含在本發(fā)明的保護(hù)范圍之內(nèi)。當(dāng)前第1頁1 2 3