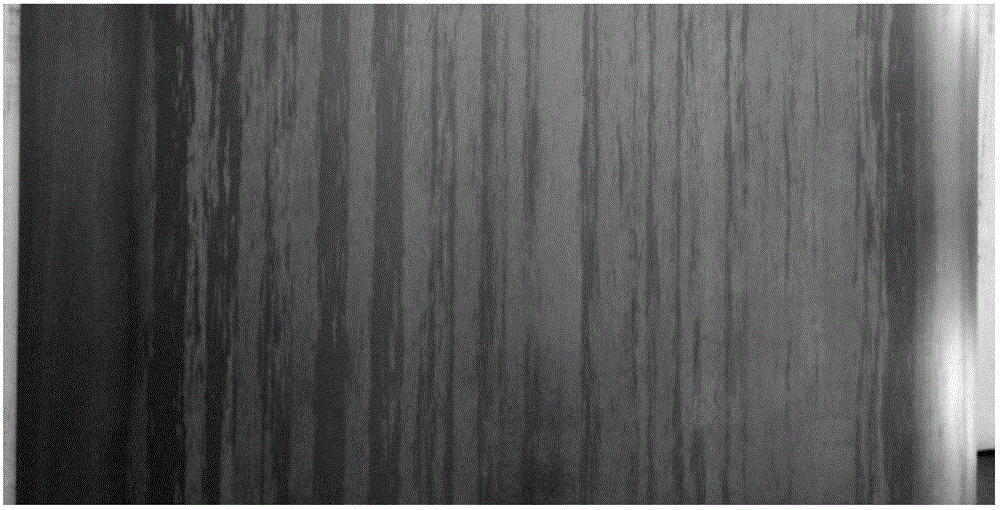
本發(fā)明涉及冶金行業(yè)帶鋼表面處理
技術(shù)領(lǐng)域:
,特別涉及一種用于減少熱軋帶鋼表面紅銹的熱軋方法。
背景技術(shù):
:隨著汽車(chē)工業(yè)朝著減重、節(jié)能和提高安全性方向的發(fā)展,高強(qiáng)汽車(chē)板在汽車(chē)上的應(yīng)用越來(lái)越廣泛,高強(qiáng)汽車(chē)板的應(yīng)用不僅可以節(jié)約鋼材,還能降低汽車(chē)油耗,是實(shí)現(xiàn)車(chē)身輕量化的重要材料。高強(qiáng)汽車(chē)板在進(jìn)行合金化設(shè)計(jì)時(shí),為了增強(qiáng)鋼材淬透性、提高成品強(qiáng)度,會(huì)添加一定量的Si元素,而Si元素的添加,例如DP、TRIP類(lèi)鋼種,會(huì)導(dǎo)致帶鋼表面極易產(chǎn)生紅銹缺陷(也稱(chēng)紅鱗缺陷)。紅銹主要是含Si鋼容易在加熱和軋制的過(guò)程中形成鐵橄欖石相Fe2SiO4,鐵橄欖石相Fe2SiO4在高溫是液態(tài)的侵入鋼鐵基體,當(dāng)溫度降下來(lái)固態(tài)Fe2SiO4容易形成FeO,且在空氣中形成紅色的Fe2O3。因?yàn)楦邷叵耂i元素會(huì)在帶鋼基體和氧化鐵皮層之間形成鐵橄欖石相(Fe2SiO4),在其凝固后會(huì)形成類(lèi)似錨狀形貌將FeO釘扎住,釘扎住的FeO很難在除鱗中被完全除掉。殘余的FeO在隨后的熱軋過(guò)程中破碎,與空氣中氧的接觸面積加大,導(dǎo)致生成呈紅色的Fe2O3。紅銹缺陷的形成機(jī)制及Si元素對(duì)氧化鐵皮生長(zhǎng)特性的影響研究比較充分,結(jié)論也已經(jīng)得到學(xué)術(shù)界一致的認(rèn)同,但是始終沒(méi)有找到有效的控制手段解決這一缺陷,極大地限制了高表面等級(jí)高Si類(lèi)高強(qiáng)汽車(chē)板的生產(chǎn)。技術(shù)實(shí)現(xiàn)要素:針對(duì)現(xiàn)有技術(shù)中的上述問(wèn)題,本發(fā)明的主要目的在于提供一種用于減少熱軋帶鋼表面紅銹的熱軋方法,抑制了紅銹的形成,提高了帶鋼的表面質(zhì)量。為了達(dá)到上述目的,本發(fā)明采用如下技術(shù)方案:一種用于減少熱軋帶鋼表面紅銹的熱軋方法,所述帶鋼熱軋方法包括如下步驟:將板坯加熱后出爐;依次經(jīng)過(guò)粗軋機(jī)組前的除鱗設(shè)備初除鱗和所述粗軋機(jī)組軋制;再將所述板坯經(jīng)精軋機(jī)組前的除鱗設(shè)備精除鱗和所述精軋機(jī)組軋制;冷卻,卷取;其中,所述板坯在加熱爐的在爐時(shí)間為160-220min,均熱時(shí)間20-40min;二加段出口溫度為1140-1160℃;出鋼溫度為1170-1210℃。作為進(jìn)一步的優(yōu)選,所述加熱爐內(nèi)各個(gè)加段的空氣過(guò)剩系數(shù)為≤0.97。作為進(jìn)一步的優(yōu)選,熱軋時(shí)采用如下的軋制計(jì)劃:在軋制輥期的前輥期,安排寬度≥1500mm,厚度≥4.0mm規(guī)格的低碳鋁鎮(zhèn)靜鋼或者車(chē)輪鋼普材料;在軋制輥期開(kāi)軋時(shí),安排3-5塊SS400作為燙輥材;安排≥15塊的厚規(guī)格SPHC以及≥6塊的厚規(guī)格耐候鋼作為過(guò)渡材;安排高Si鋼軋制,一個(gè)輥期的塊數(shù)≤20。作為進(jìn)一步的優(yōu)選,所述帶鋼為高Si鋼,所述高Si鋼的Si含量為1wt%~1.5wt%。作為進(jìn)一步的優(yōu)選,所述SPHC和耐候鋼的厚規(guī)格為≥4.0*1500mm。作為進(jìn)一步的優(yōu)選,所述高Si鋼軋制時(shí),裝鋼間距為1800mm。作為進(jìn)一步的優(yōu)選,所述初除鱗采用雙排除鱗,初除磷壓力為19-22Mpa。作為進(jìn)一步的優(yōu)選,所述粗軋共軋制6個(gè)道次,粗軋采用3+3軋制模式,保證除鱗道次≥4。作為進(jìn)一步的優(yōu)選,所述除鱗為第1道次,第3道次、第5道次和第6道次,除鱗水壓為19-22Mpa。。作為進(jìn)一步的優(yōu)選,粗軋出口溫度為980-1020℃。作為進(jìn)一步的優(yōu)選,所述精軋出口溫度為850-890℃。作為進(jìn)一步的優(yōu)選,所述精除鱗壓力為19-21Mpa。作為進(jìn)一步的優(yōu)選,所述精軋時(shí),前4機(jī)架使用上機(jī)次數(shù)≤3次的高速鋼輥,全部開(kāi)啟精軋工作輥的防剝落水。作為進(jìn)一步的優(yōu)選,所述冷卻時(shí),采用前段集中冷軋方式冷卻。本發(fā)明的有益效果是:(1)本發(fā)明通過(guò)優(yōu)化加熱爐內(nèi)板坯加熱的過(guò)程,縮短加熱過(guò)程的均熱段時(shí)間,降低出鋼溫度,使得橄欖石的硅酸鹽相形成困難,對(duì)板坯的粘附力降低,因而抑制了紅銹的形成,提高了帶鋼的表面質(zhì)量。(2)本發(fā)明通過(guò)對(duì)空氣過(guò)剩系數(shù)的控制,控制了爐子內(nèi)的氧含量,減少了鐵橄欖石相Fe2SiO4的生成。(3)本發(fā)明選取的軋制計(jì)劃,對(duì)鋼種厚度的要求確保了后續(xù)高Si鋼可以有較低的出鋼溫度;對(duì)寬度的要求確保了高Si鋼可以有較短的在爐時(shí)間。(4)常規(guī)的裝鋼間距較小1600mm或者更小,本發(fā)明采取大的裝鋼間距主要是確保高Si鋼具有較短的在爐時(shí)間。(5)本發(fā)明軋制過(guò)程中選擇的軋制模式、溫度控制以及除鱗控制等,防止了軋制過(guò)程中紅銹的形成,并且能對(duì)形成的紅銹進(jìn)行有效的消除。(6)本發(fā)明不需要對(duì)常規(guī)的除鱗設(shè)備(22Mpa以下)進(jìn)行改造;而且較低的出鋼溫度能夠降低能耗。附圖說(shuō)明圖1為本發(fā)明實(shí)施例用于減少熱軋帶鋼表面紅銹的熱軋方法的工藝流程圖。圖2為現(xiàn)有技術(shù)提供的熱軋帶鋼表面紅銹缺陷形貌圖。圖3為本發(fā)明實(shí)施例1得到的熱軋帶鋼表面紅銹缺陷形貌圖。圖4為本發(fā)明實(shí)施例3得到的熱軋帶鋼表面紅銹缺陷形貌圖。圖5為本發(fā)明實(shí)施例6得到的熱軋帶鋼表面紅銹缺陷形貌圖。具體實(shí)施方式本申請(qǐng)實(shí)施例通過(guò)提供一種用于減少熱軋帶鋼表面紅銹的熱軋方法,有效的消除了帶鋼表面嚴(yán)重紅銹缺陷,防止了鐵橄欖石相Fe2SiO4(紅銹)在加熱爐內(nèi)的形成;進(jìn)一步的,也能夠抑制其在軋制過(guò)程中的形成,并且在形成之后也能夠消除紅銹,提高了帶鋼的表面質(zhì)量。本申請(qǐng)實(shí)施例中的技術(shù)方案為解決上述紅銹的問(wèn)題,具體思路如下:本申請(qǐng)實(shí)施例用于減少熱軋帶鋼表面紅銹的熱軋方法,如圖1所示,所述帶鋼熱軋方法包括如下步驟:步驟101:將板坯加熱后出爐;步驟102:依次經(jīng)過(guò)粗軋機(jī)組前的除鱗設(shè)備初除鱗和所述粗軋機(jī)組軋制;步驟103:再將所述板坯經(jīng)精軋機(jī)組前的除鱗設(shè)備精除鱗和所述精軋機(jī)組軋制;步驟104:冷卻,卷取得鋼卷;其中,板坯在加熱爐在爐時(shí)間為160-220min,均熱時(shí)間20-40min;二加段出口溫度為1140-1160℃;出鋼溫度為1170-1210℃。出鋼溫度比正常生產(chǎn)降低了60-90℃,是現(xiàn)場(chǎng)實(shí)際生產(chǎn)摸索的防止紅銹的出鋼溫度;出鋼溫度較低,其是為了防止高Si鋼鐵表面在加熱爐形成鐵橄欖石相Fe2SiO4(熔點(diǎn)1173℃);在爐時(shí)間較短,其是為了減少鐵橄欖石相Fe2SiO4的形成量,防止液態(tài)的侵入鋼鐵表面基體;二加段溫度的限制是為了確保鋼坯在出鋼之前較長(zhǎng)時(shí)間在低溫段(1173℃以下)。為了更好的理解上述技術(shù)方案,下面將結(jié)合說(shuō)明書(shū)附圖以及具體的實(shí)施方式對(duì)上述技術(shù)方案進(jìn)行詳細(xì)的說(shuō)明。實(shí)施例1:以CR420/780DP為例(高Si雙相鋼),規(guī)格5.0*1050mm。熔煉成分(wt.%)見(jiàn)下表1:表1CSiMnP≤S≤Alt含量0.08-0.101.10-1.201.9-2.00.0200.0250.010-0.060本申請(qǐng)實(shí)施例1用于減少熱軋帶鋼表面紅銹的熱軋方法,包括如下步驟:步驟101:將板坯加熱后出爐;步驟102:依次經(jīng)過(guò)粗軋機(jī)組前的除鱗設(shè)備初除鱗和所述粗軋機(jī)組軋制;步驟103:再將所述板坯經(jīng)精軋機(jī)組前的除鱗設(shè)備精除鱗和所述精軋機(jī)組軋制;步驟104:冷卻,卷取得鋼卷;其中,板坯在加熱爐在爐時(shí)間為175min,均熱時(shí)間20-40min;二加段出口溫度為1153℃;出鋼溫度為1206℃。編排軋制計(jì)劃時(shí),前輥期安排5.0*1600mm規(guī)格380CL;軋制輥期安排4塊SS00燙輥,然后安排20塊4.5*1540mm規(guī)格SPHC,在軋制計(jì)劃的中前期中,前面軋制17塊SS400,然后安排7塊4.5*1100mm規(guī)格SPA-H,隨后安排15塊5.0*1050mm規(guī)格CR420/780DP。對(duì)鋼種厚度要求是確保后續(xù)高Si鋼CR420/780DP具有較低的出鋼溫度;對(duì)寬度的要求主要是確保高Si鋼具有較短的在爐時(shí)間。以易軋制且質(zhì)量要求較低的鋼種編為燙輥材;過(guò)渡材是通過(guò)燙輥材盡快過(guò)渡到主軋材;過(guò)渡材是為盡快適應(yīng)主軋材而編制的過(guò)渡材,以適應(yīng)主軋材的上產(chǎn)難度,即有足夠的余地調(diào)整好板形,使軋輥熱凸度趨于穩(wěn)定等??刂萍訜釥t內(nèi)各段空氣過(guò)剩系數(shù)為0.95,空氣過(guò)剩系數(shù)控制是為了控制爐子內(nèi)的氧含量,減少鐵橄欖石相Fe2SiO4的生成。圖3為本發(fā)明實(shí)施例1得到的熱軋帶鋼表面紅銹缺陷形貌圖。其與圖2現(xiàn)有技術(shù)提供的熱軋帶鋼表面紅銹缺陷形貌圖相比,本發(fā)明實(shí)施例1得到的熱軋帶鋼表面的紅銹缺陷明顯改善。實(shí)施例2:以鋼種TRIP590為例,規(guī)格3.25*1341mm。熔煉成分(wt.%)見(jiàn)下表2。表2本申請(qǐng)實(shí)施例2用于減少熱軋帶鋼表面紅銹的熱軋方法,包括如下步驟:步驟101:將板坯加熱后出爐;步驟102:依次經(jīng)過(guò)粗軋機(jī)組前的除鱗設(shè)備初除鱗和所述粗軋機(jī)組軋制;步驟103:再將所述板坯經(jīng)精軋機(jī)組前的除鱗設(shè)備精除鱗和所述精軋機(jī)組軋制;步驟104:冷卻,卷取得鋼卷;其中,鋼坯在加熱爐內(nèi)總在爐平均時(shí)間210min,均熱時(shí)間20-40min,二加段末溫度1160℃,出鋼溫度為1189℃。軋制計(jì)劃編排:前輥期安排,4.5*1700mm規(guī)格SPHC低碳鋁鎮(zhèn)靜鋼;軋制輥期安排,先5塊SS00燙輥,接著安排18塊4.5*1652mm規(guī)格SPHC,然后安排7塊4.5*1300mm規(guī)格SPA-H,隨后安排19塊3.25*1341mm規(guī)格TRIP590。所述高Si鋼TRIP590軋制時(shí),裝鋼間距為1800mm。常規(guī)的裝鋼間距較小1600mm或者更小,大的裝鋼間距主要是確保高Si鋼較短的在爐時(shí)間。所述步驟101中,控制所述加熱爐內(nèi)各段空氣過(guò)剩系數(shù)為0.94。實(shí)施例3本申請(qǐng)實(shí)施例3用于減少熱軋帶鋼表面紅銹的熱軋方法,包括如下步驟:步驟101:將板坯加熱后出爐;步驟102:依次經(jīng)過(guò)粗軋機(jī)組前的除鱗設(shè)備初除鱗和所述粗軋機(jī)組軋制;步驟103:再將所述板坯經(jīng)精軋機(jī)組前的除鱗設(shè)備精除鱗和所述精軋機(jī)組軋制;步驟104:冷卻,卷取得鋼卷;其中,板坯在加熱爐在爐時(shí)間為175min,均熱時(shí)間30min;二加段出口溫度為1153℃;出鋼溫度為1206℃。編排軋制計(jì)劃時(shí),前輥期安排5.0*1600mm規(guī)格380CL;軋制輥期安排4塊SS00燙輥,然后安排20塊4.5*1540mm規(guī)格SPHC,在軋制計(jì)劃的中前期中,前面軋制17塊SS400,然后安排7塊4.5*1100mm規(guī)格SPA-H,隨后安排15塊5.0*1050mm規(guī)格CR420/780DP。所述步驟101中,控制加熱爐內(nèi)各段空氣過(guò)剩系數(shù)為0.95。所述步驟102中,所述初除鱗采用雙排除鱗,除鱗壓力為19Mpa。除鱗壓力是為了確保形成的Fe2SiO4去除。圖4為本發(fā)明實(shí)施例3得到的熱軋帶鋼表面紅銹缺陷形貌圖。其與圖2現(xiàn)有技術(shù)提供的熱軋帶鋼表面紅銹缺陷形貌圖相比,本發(fā)明實(shí)施例3得到的熱軋帶鋼表面的紅銹缺陷明顯改善。實(shí)施例4本申請(qǐng)實(shí)施例3用于減少熱軋帶鋼表面紅銹的熱軋方法,包括如下步驟:步驟101:將板坯加熱后出爐;步驟102:依次經(jīng)過(guò)粗軋機(jī)組前的除鱗設(shè)備初除鱗和所述粗軋機(jī)組軋制;步驟103:再將所述板坯經(jīng)精軋機(jī)組前的除鱗設(shè)備精除鱗和所述精軋機(jī)組軋制;步驟104:冷卻,卷取得鋼卷;其中,鋼坯在加熱爐內(nèi)總在爐平均時(shí)間210min,均熱時(shí)間20-40min,二加段末溫度1160℃,出鋼溫度為1189℃。軋制計(jì)劃編排:前輥期安排,4.5*1700mm規(guī)格SPHC低碳鋁鎮(zhèn)靜鋼;軋制輥期安排,先5塊SS00燙輥,接著安排18塊4.5*1652mm規(guī)格SPHC,然后安排7塊4.5*1300mm規(guī)格SPA-H,隨后安排19塊3.25*1341mm規(guī)格TRIP590。所述高Si鋼TRIP590軋制時(shí),裝鋼間距為1800mm。常規(guī)的裝鋼間距較小1600mm或者更小,大的裝鋼間距主要是確保高Si鋼較短的在爐時(shí)間。所述步驟101中,控制所述加熱爐內(nèi)各段空氣過(guò)剩系數(shù)為0.94。所述步驟102中,所述初除鱗采用雙排除鱗,除鱗壓力為20.1Mpa。所述步驟103中,調(diào)整所述粗軋共軋制6個(gè)道次,粗軋采用3+3軋制模式,保證除鱗道次≥4;除鱗水壓保證在19.5Mpa左右。軋制模式3+3軋制時(shí)間較短,減少軋制過(guò)程中鋼坯表面氧化,防止Fe2SiO4形成,除鱗道次和壓力是為了確保形成的紅銹的消除。實(shí)施例5本申請(qǐng)實(shí)施例5用于減少熱軋帶鋼表面紅銹的熱軋方法,包括如下步驟:步驟101:將板坯加熱后出爐;步驟102:依次經(jīng)過(guò)粗軋機(jī)組前的除鱗設(shè)備初除鱗和所述粗軋機(jī)組軋制;步驟103:再將所述板坯經(jīng)精軋機(jī)組前的除鱗設(shè)備精除鱗和所述精軋機(jī)組軋制;步驟104:冷卻,卷取得鋼卷;其中,鋼坯在加熱爐內(nèi)總在爐平均時(shí)間210min,均熱時(shí)間20-40min,二加段末溫度1160℃,出鋼溫度為1189℃。軋制計(jì)劃編排:前輥期安排,4.5*1700mm規(guī)格SPHC低碳鋁鎮(zhèn)靜鋼;軋制輥期安排,先5塊SS00燙輥,接著安排18塊4.5*1652mm規(guī)格SPHC,然后安排7塊4.5*1300mm規(guī)格SPA-H,隨后安排19塊3.25*1341mm規(guī)格TRIP590。所述高Si鋼TRIP590軋制時(shí),裝鋼間距為1800mm。常規(guī)的裝鋼間距較小1600mm或者更小,大的裝鋼間距主要是確保高Si鋼較短的在爐時(shí)間。所述步驟101中,控制所述加熱爐內(nèi)各段空氣過(guò)剩系數(shù)為0.96。所述步驟102中,所述初除鱗采用雙排除鱗,除鱗壓力為21.8Mpa。所述步驟103中,調(diào)整所述粗軋共軋制6個(gè)道次,粗軋采用3+3軋制模式,保證除鱗道次≥4;所述精除鱗水壓為21.5Mpa。所述除鱗為第1道次,第3道次、第4道次和第6道次。所述步驟103中,粗軋出口溫度為1015℃,粗軋出口溫度是為了控制進(jìn)入精軋的溫度,減少后續(xù)氧化鐵皮的形成。實(shí)施例6本申請(qǐng)實(shí)施例6用于減少熱軋帶鋼表面紅銹的熱軋方法,包括如下步驟:步驟101:將板坯加熱后出爐;步驟102:依次經(jīng)過(guò)粗軋機(jī)組前的除鱗設(shè)備初除鱗和所述粗軋機(jī)組軋制;步驟103:再將所述板坯經(jīng)精軋機(jī)組前的除鱗設(shè)備精除鱗和所述精軋機(jī)組軋制;步驟104:冷卻,卷取得鋼卷;其中,板坯在加熱爐在爐時(shí)間為175min,均熱時(shí)間30min;二加段出口溫度為1153℃;出鋼溫度為1206℃。編排軋制計(jì)劃時(shí),前輥期安排5.0*1600mm規(guī)格380CL;軋制輥期安排4塊SS00燙輥,然后安排20塊4.5*1540mm規(guī)格SPHC,在軋制計(jì)劃的中前期中,前面軋制17塊SS400,然后安排7塊4.5*1100mm規(guī)格SPA-H,隨后安排15塊5.0*1050mm規(guī)格CR420/780DP。所述步驟101中,控制加熱爐內(nèi)各段空氣過(guò)剩系數(shù)為0.95。所述步驟102中,所述初除鱗采用雙排除鱗,除鱗壓力為20.1Mpa。所述步驟103中,調(diào)整所述粗軋共軋制6個(gè)道次,粗軋采用3+3軋制模式,保證除鱗道次≥4;所述精除鱗水壓為19.5Mpa。所述除鱗為第1道次,第3道次、第5道次和第6道次。所述步驟103中,粗軋出口溫度為980-1020℃,粗軋出口溫度是為了控制進(jìn)入精軋的溫度,減少后續(xù)氧化鐵皮的形成。所述精軋出口溫度為878℃。所述精除鱗壓力19.2Mpa。所述步驟103中,所述精軋時(shí),前4機(jī)架使用上機(jī)次數(shù)2次的高速鋼輥,開(kāi)啟F1-F4精軋工作輥的防剝落水。這樣是為了防止軋制表面正常,防止軋制表面粗糙。所述步驟104中,所述冷卻時(shí),采用前段集中冷軋方式冷卻。圖5為本發(fā)明實(shí)施例6得到的熱軋帶鋼表面紅銹缺陷形貌圖,其與圖2、圖3、圖4提供的熱軋帶鋼表面紅銹缺陷形貌圖相比,本發(fā)明實(shí)施例6得到的熱軋帶鋼表面的紅銹缺陷明顯改善,表面質(zhì)量最好。在本發(fā)明實(shí)施例中,以CR420/780DP鋼為例,分別根據(jù)本發(fā)明實(shí)施例6的減少紅銹缺陷的方法應(yīng)用于熱連軋產(chǎn)線上進(jìn)行了批量化實(shí)施,取得了預(yù)想中的效果。同時(shí)根據(jù)不采用本發(fā)明的去除缺陷的方法,也進(jìn)行同等量的生產(chǎn),然后進(jìn)行表面質(zhì)量判斷,表面質(zhì)量判級(jí)系統(tǒng)中,1級(jí)最優(yōu)、4級(jí)最差,而導(dǎo)致熱軋帶鋼表面質(zhì)量降級(jí)的主要原因就是紅銹缺陷。根據(jù)判定系統(tǒng),分別對(duì)采用本發(fā)明減少紅銹缺陷的方法和沒(méi)有采用本發(fā)明的方法所制備的熱軋帶鋼進(jìn)行判斷,沒(méi)有采用本發(fā)明減少紅銹缺陷的方法所制備的熱軋帶鋼表面等級(jí)比例分別見(jiàn)表1,采用本發(fā)明實(shí)施例6減少紅銹缺陷的方法所制備的熱軋帶鋼表面等級(jí)比例分別見(jiàn)表2。表1表2從表1和表2可以看出,采用本發(fā)明后該鋼種的1級(jí)和2級(jí)表面比例分別大幅度提高到了25%和60%。本申請(qǐng)實(shí)施例中提供的一個(gè)或多個(gè)技術(shù)方案,至少具有如下技術(shù)效果或優(yōu)點(diǎn):(1)本發(fā)明通過(guò)優(yōu)化加熱爐內(nèi)板坯加熱的過(guò)程,縮短加熱過(guò)程的均熱段時(shí)間,降低出鋼溫度,使得橄欖石的硅酸鹽相形成困難,對(duì)板坯的粘附力降低,因而抑制了紅銹的形成,提高了帶鋼的表面質(zhì)量。(2)本發(fā)明通過(guò)對(duì)空氣過(guò)剩系數(shù)的控制,控制了爐子內(nèi)的氧含量,減少了鐵橄欖石相Fe2SiO4的生成。(3)本發(fā)明選取的軋制計(jì)劃,對(duì)鋼種厚度的要求確保了后續(xù)高Si鋼可以有較低的出鋼溫度;對(duì)寬度的要求確保了高Si鋼可以有較短的在爐時(shí)間。(4)常規(guī)的裝鋼間距較小1600mm或者更小,本發(fā)明采取大的裝鋼間距主要是確保高Si鋼具有較短的在爐時(shí)間。(5)本發(fā)明軋制過(guò)程中選擇的軋制模式、溫度控制以及除鱗控制等,防止了軋制過(guò)程中紅銹的形成,并且能對(duì)形成的紅銹進(jìn)行消除。(6)本發(fā)明不需要對(duì)常規(guī)的除鱗設(shè)備(22Mpa以下)進(jìn)行改造;而且較低的出鋼溫度能夠降低能耗。盡管已描述了本發(fā)明的優(yōu)選實(shí)施例,但本領(lǐng)域內(nèi)的技術(shù)人員一旦得知了基本創(chuàng)造性概念,則可對(duì)這些實(shí)施例作出另外的變更和修改。所以,所附權(quán)利要求意欲解釋為包括優(yōu)選實(shí)施例以及落入本發(fā)明范圍的所有變更和修改。顯然,本領(lǐng)域的技術(shù)人員可以對(duì)本發(fā)明進(jìn)行各種改動(dòng)和變型而不脫離本發(fā)明的精神和范圍。這樣,倘若本發(fā)明的這些修改和變型屬于本發(fā)明權(quán)利要求及其等同技術(shù)的范圍之內(nèi),則本發(fā)明也意圖包含這些改動(dòng)和變型在內(nèi)。當(dāng)前第1頁(yè)1 2 3