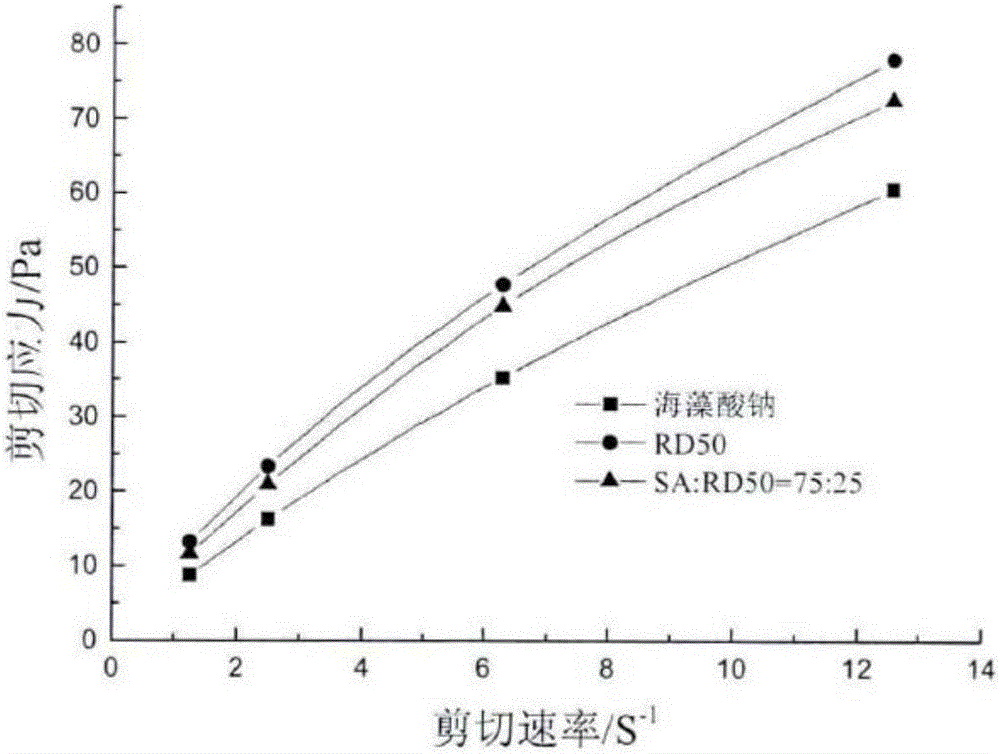
本發(fā)明涉及印染
技術(shù)領(lǐng)域:
,特別涉及一種滌、棉布的分散、活性染料二相法印花方法。
背景技術(shù):
::滌、棉織物是用滌綸纖維和棉纖維混紡紗線織成的各種織物,具有外觀挺刮、耐穿、耐用、尺寸穩(wěn)定、易洗快干等優(yōu)點(diǎn),適宜制作各種衣服。目前市場上絕大部分的滌、棉都是采用涂料印花,這對于大面積印花的手感及印花部分的刷洗牢度都不能達(dá)到客戶要求。為改善這種工藝,出現(xiàn)了分散/活性染料的印花工藝,分散/活性染料的印花工藝根據(jù)染料的不同,可分為兩大類,一相法和二相法。一相法也稱全料法,顧名思義,就是把分散染料、活性染料、堿劑及其他助劑全部放在一起制成色漿進(jìn)行印花、固色、水洗的工藝。此法是目前應(yīng)用最廣泛的方法,工藝比較簡單:一相法工藝流程:半成品—印花—烘干—固色一水洗—皂煮—水洗―烘干。常用的色漿處方如下:此工藝最需要注意的地方是由于色漿中含有堿劑,所以色漿不是很穩(wěn)定,而且高溫焙烘時部分碳酸氫鈉會分解,色漿中pH值升高,某些分散染料對堿不穩(wěn)定,容易發(fā)生色變,固色率低,甚至結(jié)構(gòu)發(fā)生變化,因此要選擇耐堿性良好的分散染料。此外,在堿劑的存在條件下滌棉織物經(jīng)高溫焙烘后,織物容易泛黃(主要是棉纖維),因此堿劑的用量要嚴(yán)格控制,且活性染料要選用熱穩(wěn)定好、固色率高的染料。二相法印花是色漿中不加堿劑,一般也不加尿素,先對分散染料進(jìn)行高溫焙烘固色,活性染料則在印后經(jīng)軋堿液進(jìn)行短蒸固色。兩相法印花適用于反應(yīng)性高的活性染料(如乙稀砜型、雙活性基型活性染料),借助濃堿的作用,在短時間內(nèi)高溫汽蒸的條件下進(jìn)行固色。常用的色漿處方如下:快速蒸化軋堿劑處方如下:兩相法印花的最主要優(yōu)點(diǎn)是色漿中不含堿劑,色漿穩(wěn)定,大大擴(kuò)大分散染料的選擇,色澤鮮艷,色光純正,白地沾污和織物泛黃都較好。同時大幅度降低尿素用量,減少污染。為防止印花后白地沾污的問題,還可以選用不耐堿的分散染料,后處理采用熱堿水洗工藝,破壞分散染料的浮色,防止沾污。兩相法的主要缺點(diǎn)是工藝流程長,色澤難以控制;同時后軋堿液容易引起花紋滲化。傳統(tǒng)法的軋液率為70—80%,活性染料固色不充分;帶液率太高,易造成花型滲化、不清晰。印染效果還受糊料和蒸化設(shè)備影響:印花原糊的作用是使色漿具有一定的粘度和流變性。它由親水性高分子物糊料調(diào)制而成,常用的糊料有淀粉、淀粉降解產(chǎn)物(白糊精與黃糊精)、淀粉醚衍生物、海藻酸鈉(或銨)、羥乙基皂莢膠、龍膠、纖維素醚、合成高分子化合物等。用水、火油與乳化劑制成的乳化糊,有時也用作印花原糊。印花原糊對色漿中的化學(xué)藥劑應(yīng)具有良好的穩(wěn)定性,不與染料發(fā)生作用,對纖維有一定的粘附力并易于從織物上洗去。印花色漿的粘度決定于原糊的性質(zhì),印花時如果色漿粘度下降太多則難以印得精細(xì)的線條,粘度太大則色漿不易通過篩網(wǎng)的細(xì)孔。蒸化亦稱汽蒸。印上色漿的織物經(jīng)烘干后進(jìn)行蒸化。蒸汽在織物上冷凝,使織物溫度升高、纖維和糊料溶脹、染料溶解并上染,有些染料在蒸化過程中還發(fā)生化學(xué)反應(yīng)。印花染料由于糊料的存在,上染過程較為復(fù)雜,蒸化時間要比軋染的蒸化時間長。蒸化設(shè)備有三種:①高壓汽蒸箱:將織物懸掛在支架上,推入箱體進(jìn)行蒸化;②連續(xù)蒸化機(jī):把織物成環(huán)狀懸掛在長環(huán)上,長環(huán)緩緩前進(jìn),連續(xù)蒸化;③各種快速蒸化機(jī)。汽蒸箱和懸掛式連續(xù)蒸化機(jī)適用于蠶絲織物、針織物和合成纖維織物。汽蒸箱在密閉條件下進(jìn)行蒸化,但不能連續(xù)生產(chǎn)。蒸化條件隨染料和纖維性質(zhì)而異。對還原染料的印花織物蒸化時,應(yīng)將蒸化室中的空氣驅(qū)除。分散染料的滌綸印花織物,可在密閉汽蒸箱中以130℃左右進(jìn)行蒸化,或在常壓下用175℃左右的過熱蒸汽蒸化,也可在200℃左右過熱空氣焙烘固色。對于上述任一技術(shù)條件進(jìn)行改善創(chuàng)新,均可對印花效果造成較大影響,現(xiàn)有技術(shù)中?!队∪尽?2006No.7)作者:賈景文,王玉民:滌棉織物分散/活性兩相法印花工藝,此文章公開了分散/活性兩相法印花工藝條件,優(yōu)選了染料和固色堿劑,與全料法印花工藝相比,前者固色率高,色牢度可提高0.5~1級,生產(chǎn)易控制;提出兩相法印花中軋堿高溫快速蒸化的技術(shù)關(guān)鍵是設(shè)備,并給出兩次皂洗的工藝條件,以解決白地沾污問題。其工藝條件:白布預(yù)定形(溫度190℃、車速45m/min)→印花→焙烘(195℃、60s)→軋堿快速蒸化→皂洗(第一次)→皂洗(第二次)→拉幅上軟(溫度170℃,車速45m/min)→預(yù)縮。工藝處方如下:(1)印花處方/g·kg-1與變性淀粉混合糊適量(2)快速蒸化軋堿劑處方/g·L-1軋液率50%~60%,蒸化130~135℃×50s。再如,現(xiàn)有技術(shù)中,中國專利公開號CN104562800A(2015.04.29)公開滌棉織物印花工藝,工藝流程如下:預(yù)定形:白布預(yù)定形溫度190℃,車速45m/min。印花:印花處方:分散染料30-40g/kg、雷瑪素活性染料40-45g/kg、防染鹽S10-15g/kg、檸檬酸10-15g/kg,將上述配方與變性淀粉混合糊混合組成印花色漿印花。烘焙:烘培溫度195℃,時間1min。軋堿快速蒸化:軋堿劑處方:純堿150g/L、食鹽100g/L、碳酸鉀100g/L、36波美度燒堿100mL/L,軋液率50%-60%,蒸化溫度130-135℃,蒸化時間50s。皂洗:先用冷水洗,再用3-5g/L的硫酸溶液酸洗,接著用含皂洗劑MR3g/L的溶液進(jìn)行第一次皂洗,皂洗溫度90℃,最后用含燒堿3g/L、皂洗劑MR3g/L的溶液進(jìn)行第二次皂洗;熱水洗:用40-50℃的熱水清洗織物。烘干。又如,現(xiàn)有技術(shù)中,中國專利公開號CN105113296A(2015.12.02)公開了一種印花糊料及其制備方法,印花糊料,包括以下組分且100g印花糊料中各組分的質(zhì)量為:羥乙基皂莢膠:5-10g;乳化劑:2-3g;火油:70-75g;尿素:5-6g;水:余量。再如、現(xiàn)有技術(shù)中,中國專利公開號CN105696379A(2016.06.22)公開了一種活性染料印花糊料及其制備方法和應(yīng)用,按照質(zhì)量百分比由以下組分構(gòu)成:海泡石10%-20%,煤油6%-12%,乳化劑0.8%-1.6%,尿素8%-12%,防染鹽S2%-4%,純堿2%-4%,余量為水,以上組分含量總量為100%?,F(xiàn)有技術(shù)中的滌棉分散活性染料全相法印花,由于堿劑的加入,使得分散與活性染料的利用率較低,且穩(wěn)定性較差。為解決這種技術(shù)問題,需要出現(xiàn)一種使用方便,通過刮印含有堿劑與尿素的糊料,經(jīng)過二次印花涂布再進(jìn)行常溫常壓汽蒸的方式,從而達(dá)到對活性染料的固色,提高染料的適應(yīng)性、固色率,以及防沾污性均顯著提高的一種滌、棉布的分散、活性染料二相法印花方法。技術(shù)實(shí)現(xiàn)要素::本發(fā)明的目的在于克服現(xiàn)有技術(shù)中存在的缺點(diǎn),提供一種使用方便,通過刮印含有堿劑與尿素的糊料,經(jīng)過二次印花涂布再進(jìn)行常溫常壓汽蒸的方式,從而達(dá)到對活性染料的固色,提高染料的適應(yīng)性、固色率,以及防沾污性均顯著提高的一種滌、棉布的分散、活性染料二相法印花方法。為了實(shí)現(xiàn)上述目的,本發(fā)明提供了一種滌、棉布的分散、活性染料二相法印花方法,其中,包括如下步驟:A、色漿與原糊的制備B、印花C、高溫蒸化D、第二次刮印涂布E、常溫蒸化F、二次水洗定型。進(jìn)一步的,色漿制備包括預(yù)配軟水和增稠劑的步驟:配制增稠劑時用電機(jī)攪拌至透明狀,然后靜置過夜使其充分膨化,配制色漿時,染料先用水溶解,然后再加增稠劑,配置軟水:100g六偏磷酸鈉1.2g水98.8g;配置增稠劑:100g尿素Xg防染鹽S1.3gNaHCO3Yg海藻酸鈉8g軟水Zg;配置色漿:100g增稠劑78g活性染料xg分散染料yg冷水zg。進(jìn)一步的,原糊的制備:將海藻酸鈉、RD50分別加入到52-65攝氏度蒸餾水,攪拌至透明狀,靜置過夜,使這兩種基本糊料充分膨化,兩種基本原糊按質(zhì)量比混合得海藻混合糊,海藻酸鈉:RD50為100-0:0-100進(jìn)行混合。進(jìn)一步的,印花處方g/L如下,其中,分散染料為雙酯型的分散染料,不耐堿;活性染料為一氯均三嗪型染料。進(jìn)一步的,第二次刮印的處方g/L如下:進(jìn)一步的,第二次刮印(含有尿素與堿劑的原糊),①第二次刮印基本原糊采用全海藻。②第二次刮印漿的粘度控制在3000-4000dpa.s.③第二次刮印時進(jìn)布不能起皺,反面羅紋輥開幅及控制好工藝車速。④控制好活性基本糊涂布時磁棒及刮刀壓力。進(jìn)一步的,兩次蒸化條件如下,高溫蒸化180℃,8min,常溫蒸化102℃,8min。進(jìn)一步的,二次水洗為皂洗:第一次皂洗工序:軋酸,條件:5g/L醋酸,PH值5.5-6;→多格水洗→皂洗,皂洗劑ALX2g/L,溫度90℃,整體車速為35-40m/min;第二次皂洗:三格堿洗,燒堿2g/L,皂洗劑ALX2g/L,→皂洗→三格熱水洗→烘干。進(jìn)一步的,二相法印花后的水洗必須先進(jìn)行軋酸清洗,然后再進(jìn)行軋堿皂洗與皂蒸。經(jīng)試驗(yàn),在第一次水洗時進(jìn)行軋酸水洗,可以減少活性染料的沾色,而第二次水洗時,在2g/l燒堿溶液中加入2g/l皂洗劑,95℃洗滌2min白地的白度會大大提高。而對于全相法印花,由于染料的選擇問題,首先分散染料不能采用不耐堿的分散染料,所以對于分散染料的棉相沾色不能很好的洗除。從而造成滌棉織物的色澤萎暗、陳舊,浮色可達(dá)30%到50%,濕摩擦牢度顯著下降。所以對于滌棉織物中棉相沾色來說,浮色越容易去除干凈,則其織物的印花鮮艷度則越高。本發(fā)明的優(yōu)點(diǎn)為:使用方便,通過刮印含有堿劑與尿素的糊料,經(jīng)過二次印花涂布再進(jìn)行常溫常壓汽蒸的方式,從而達(dá)到對活性染料的固色,提高染料的適應(yīng)性、固色率,以及防沾污性均顯著提高,本發(fā)明與印花方法與國內(nèi)外的對比如下:本發(fā)明二相法印花的工藝流程為:印花(制漿是分散與活性染料同漿配制,其中不加尿素與堿劑色漿中只含有軟水劑與防還原劑)→高溫焙烘(180℃X8min分散染料發(fā)色)→第二次刮印(含有尿素與堿劑的色漿,其色漿中不含任何染料)→常溫常壓汽蒸(102℃X8min)→加酸、冷流水洗、堿洗或皂洗→后整理→成品歐洲國家的傳統(tǒng)二相印花為:印花(制漿是分散與活性染料同漿配制,其中不加尿素與堿劑色漿中只含有軟水劑與防還原劑)→高溫焙烘(195℃X60S,分散染料發(fā)色)→軋堿快速蒸化(軋余率50%-60%,蒸化130℃-135℃X50S,快速軋堿處方為36Be.燒堿100ml/l,純堿150g/l,食鹽100g/l,碳酸鉀100g/l)→第一次皂洗→第二次皂洗→后整理→成品。我國現(xiàn)在一相法印花為:印花(制漿時分散與活性染料同漿配制,加入適量的尿素與適量的堿劑。軟水劑與防還原劑一并加入)→先焙烘,后汽蒸(焙烘180℃X4min,蒸化為102℃X5-6min。)→水洗及皂洗→后整理→成品??梢园l(fā)現(xiàn):1、本發(fā)明通過刮印含有堿劑與尿素的糊料,通過二次印花涂布再進(jìn)行常溫常壓汽蒸的方式,從而達(dá)到對活性染料的固色。2,對于全相法印花,此二相法印花對于染料的適應(yīng)性、分散染料的固色率都在很大的提高,并且工藝操作簡便。3,通過采用雙酯型分散染料,對于滌棉印花的沾污性要比全相法印花好得多,對于活性染料,此方法可以采用目前工廠使用的染料,而不需要另外采用乙烯砜結(jié)構(gòu)的染料。附圖說明:圖1為本發(fā)明原糊的隨剪切速率變化的粘度曲線圖2為本發(fā)明原糊的流變曲線。具體實(shí)施方式:下面結(jié)合附圖,對本發(fā)明進(jìn)行說明。本發(fā)明的整體工藝為:印花(制漿是分散與活性染料同漿配制,其中不加尿素與堿劑色漿中只含有軟水劑與防還原劑)→高溫焙烘(180℃X8min分散染料發(fā)色)→第二次刮印(含有尿素與堿劑的色漿,其色漿中不含任何染料)→常溫常壓汽蒸(102℃X8min)→加酸、冷流水洗、堿洗或皂洗→后整理→成品。其具體的關(guān)鍵部分如下,包括如下步驟:A、色漿與原糊的制備B、印花C、高溫蒸化D、第二次刮印涂布E、常溫蒸化F、二次水洗定型。進(jìn)一步的,色漿制備包括預(yù)配軟水和增稠劑的步驟:配制增稠劑時用電機(jī)攪拌至透明狀,然后靜置過夜使其充分膨化,配制色漿時,染料先用水溶解,然后再加增稠劑,配置軟水:100g六偏磷酸鈉1.2g水98.8g;配置增稠劑:100g尿素Xg防染鹽S1.3gNaHCO3Yg海藻酸鈉8g軟水Zg;配置色漿:100g增稠劑78g活性染料xg分散染料yg冷水zg。進(jìn)一步的,原糊的制備:將海藻酸鈉、SP980分別加入到52-65攝氏度軟水,攪拌至透明狀,靜置過夜,使這兩種基本糊料充分膨化,兩種基本原糊按質(zhì)量比混合得海藻混合糊,海藻酸鈉:RD50為100-0:0-100進(jìn)行混合。進(jìn)一步的,印花處方g/L如下,其中,分散染料為雙酯型的分散染料,不耐堿;活性染料為一氯均三嗪型染料。進(jìn)一步的,第二次刮印的處方g/L如下:進(jìn)一步的,第二次刮印(含有尿素與堿劑的原糊),①第二次刮印基本原糊采用全海藻。②第二次刮印漿的粘度控制在3000-4000dpa.s.③第二次刮印時進(jìn)布不能起皺,反面羅紋輥開幅及控制好工藝車速。④控制好活性基本糊涂布時磁棒及刮刀壓力。進(jìn)一步的,兩次蒸化條件如下,高溫蒸化180℃,8min,常溫蒸化102℃,8min。進(jìn)一步的,二次水洗為皂洗:第一次皂洗工序:軋酸,條件:5g/L醋酸,PH值5.5-6;→多格水洗→皂洗,皂洗劑ALX2g/L,溫度90℃,整體車速為35-40m/min;第二次皂洗:三格堿洗,燒堿2g/L,皂洗劑ALX2g/L,→皂洗→三格熱水洗→烘干。進(jìn)一步的,二相法印花后的水洗必須先進(jìn)行軋酸清洗,然后再進(jìn)行軋堿皂洗與皂蒸。經(jīng)試驗(yàn),在第一次水洗時進(jìn)行軋酸水洗,可以減少活性染料的沾色,而第二次水洗時,在2g/l燒堿溶液中加入2g/l皂洗劑,95℃洗滌2min白地的白度會大大提高。而對于全相法印花,由于染料的選擇問題,首先分散染料不能采用不耐堿的分散染料,所以對于分散染料的棉相沾色不能很好的洗除。從而造成滌棉織物的色澤萎暗、陳舊,浮色可達(dá)30%到50%,濕摩擦牢度顯著下降。所以對于滌棉織物中棉相沾色來說,浮色越容易去除干凈,則其織物的印花鮮艷度則越高。試驗(yàn)1:配置4%海藻酸鈉、4%RD50原糊和混合原糊(4%海藻酸鈉:4%RD50=75:25)隨著剪切速率變化的粘度曲線如圖1所示,流變曲線如圖2所示。海藻酸鈉、RD50原糊及拼混原糊均屬于假塑性流體,拼混原糊的流變性與RD50的流變性相近。這表明在海藻酸鈉糊中加入少量的RD50糊就能很好的改善海藻酸鈉糊的流變性。RD50隨著剪切速度的增加,粘度急劇降低,與SA相比假塑性更強(qiáng),結(jié)構(gòu)粘度更大。海藻酸鈉隨著剪切速率的增大,粘度下降程度不大,與RD50相比,更接近牛頓流體。海藻酸鈉的剪切應(yīng)力與剪切速率基本呈線性關(guān)系,接近牛頓流體,粘彈性比RD50糊差。故本發(fā)明優(yōu)選在海藻酸鈉與RD50的比例為75:25或者70:30或者80:20,或者85:15。海藻酸鈉為SA。試驗(yàn)2:糊料的抱水性就是糊料的水合能力,是指該糊料的膨潤性、吸水性及耐稀釋性。糊料的抱水性強(qiáng)弱與否,對于活性染料汽蒸固色過程有很大的影響。汽蒸過程中,水在抱水性差的糊料中可自由移動,產(chǎn)生滲化現(xiàn)象;而抱水性太強(qiáng)的糊料,汽蒸過程中會吸收過量的水分,同樣可能產(chǎn)生滲化現(xiàn)象。海藻酸鈉為SA。如下表各原糊的抱水性由大到小依次為,RD50>混合糊>SA。半小時的上升高度均在0.1-0.2cm之間,各原糊均能滿足生產(chǎn)要求。試驗(yàn)3:采用活性RedPB-BR、YellowPB-6G活性染料用不同糊料對棉織物進(jìn)行印花,印花織物正、反面的K/S值和滲透率如下表織物表面K/S值和滲透率變化趨勢是一致的:RD50糊的表面得色量最高,混合糊次之,SA表面得色量最差;RD50糊的滲透性最好,SA次之,混合糊的滲透率最差。試驗(yàn)4:SA、RD50和混合糊料配制的色裝印花后織物的耐摩擦色牢度和耐洗色牢度等級。試驗(yàn)5:SA、RD50和混合糊印花皂洗后的印花織物在50%DMF水溶液中處理前后的K/S值及固色率情況??梢园l(fā)現(xiàn)三個印花體系的固色率都大于97%,比較試驗(yàn)一:本發(fā)明的二相法分散/活性工藝印花,因色漿中不含堿劑與尿素,在印花時,只是在色漿中加入了相應(yīng)的活性與分散染料,然后對分散染料進(jìn)行高溫焙烘,蒸化溫度為180℃,時間為8-10分鐘,由于色漿中沒有尿素、堿劑,所以在高溫焙烘時,對分散染料的染深性沒有影響。表一,分散染料在堿性條件下色變與上染率的比較+表示不發(fā)生色變,-表示發(fā)生色變;√表示上色率正常,X表示上色率下降。對于二相法印花則不產(chǎn)生上述分散染料的色變與上染率變化的問題。二相法能提高染料的固著上染率,其色牢度可較全相法提高0.5-1級。表二,二相法印花與全相法印花活性染料上染率的比較活性染料全相法上染率二相法上染率活性黃PX-6GN70%90%活性黃P-2RN72%91%雅可素紅P-4B70%90%活性紅K-3B65%85%活性橙K-7R66%86%英彩克隆翠藍(lán)P-GR55%70.5%活性藍(lán)K-GRS60%78%雅可素艷藍(lán)P-3R58%76%雅可素藏青P-2R60%78%英彩克隆黑P-SG60%78%活性黑KN-B55%70%二相法印花時活性染料的上染率基本上與全棉活性印花時活性染料的上染率相同,而滌棉布全相法印花時,由于分散染料與活性染料同漿,色漿中含有1%-1.5%的堿劑,這就造成了分散染料的色變與分散染料上染率下降的。而二相法印花時,色漿中只含有染料及間硝基苯磺酸鈉。分散染料的上染基本上不受影響。表三,全相法印花與二相法印花織物的各項(xiàng)牢度比較試驗(yàn)二,本發(fā)明二相法印花的工藝流程為:印花(制漿是分散與活性染料同漿配制,其中不加尿素與堿劑色漿中只含有軟水劑與防還原劑)→高溫焙烘(180℃X8min分散染料發(fā)色)→第二次刮印(含有尿素與堿劑的色漿,其色漿中不含任何染料)→常溫常壓汽蒸(102℃X8min)→冷流水洗、堿洗或皂洗→后整理→成品。而歐洲國家的傳統(tǒng)二相印花為:印花(制漿是分散與活性染料同漿配制,其中不加尿素與堿劑色漿中只含有軟水劑與防還原劑)→高溫焙烘(195℃X60S,分散染料發(fā)色)→軋堿快速蒸化(軋余率50%-60%,蒸化130℃-135℃X50S,快速軋堿處方為36Be.燒堿100ml/l,純堿150g/l,食鹽100g/l,碳酸鉀100g/l)→第一次皂洗→第二次皂洗→后整理→成品。我國現(xiàn)在一相法印花為:印花(制漿時分散與活性染料同漿配制,加入適量的尿素與適量的堿劑。軟水劑與防還原劑一并加入)→先焙烘,后汽蒸(焙烘180℃X4min,蒸化為102℃X5-6min。)→水洗及皂洗→后整理→成品。分散/活性全相法與二相法印花的區(qū)別:綜上,本發(fā)明使用方便,通過刮印含有堿劑與尿素的糊料,經(jīng)過二次印花涂布再進(jìn)行常溫常壓汽蒸的方式,從而達(dá)到對活性染料的固色,提高染料的適應(yīng)性、固色率,以及防沾污性均顯著提高,具體為,1、本發(fā)明通過刮印含有堿劑與尿素的糊料,通過二次印花涂布再進(jìn)行常溫常壓汽蒸的方式,從而達(dá)到對活性染料的固色。2,對于全相法印花,此二相法印花對于染料的適應(yīng)性、分散染料的固色率都在很大的提高,并且工藝操作簡便。3,通過采用雙酯型分散染料,對于滌棉印花的沾污性要比全相法印花好得多,對于活性染料,此方法可以采用目前工廠使用的染料,而不需要另外采用乙烯砜結(jié)構(gòu)的染料。當(dāng)前第1頁1 2 3