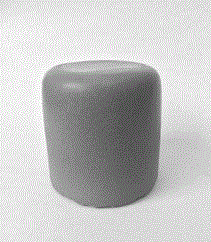
本發(fā)明涉及核工業(yè)領(lǐng)域,尤其是放射性污染廢機油水泥固化技術(shù)領(lǐng)域,該方法能夠用于核電行業(yè)放射性污染廢機油水泥固化。
背景技術(shù):在核工業(yè)領(lǐng)域,包括核設(shè)施和核電站運行過程中,會產(chǎn)生一定量的被放射性核素污染的廢機油。該類機油主要包括壓縮機油和真空泵油,這些有機介質(zhì)會與放射性核素會形成相對穩(wěn)定的絡(luò)合物,而絡(luò)合物的生成則增加了廢機油的處理難度。目前,國際上處理放射性有機廢液的方法主要包括焚燒法、高溫高壓處理方法、各種高級氧化方法等,然而前述方法工藝復(fù)雜、能耗高,對于設(shè)備要求苛刻,因此,難以實施。而我國國內(nèi)缺少放射性廢機油簡單易行的有效處理方法,核工業(yè)領(lǐng)域仍存放有一定量的放射性污染廢機油亟待處理。水泥固化法是將放射性污染廢機油水泥固化成固化體后,放入中低放固體廢物處置場的方法,其具有工藝簡單、能耗低、投資少、安全可靠,且水泥固化體具有耐輻照和自屏蔽效應(yīng)好等優(yōu)點。然而,放射性廢機油與水泥混合不能形成均勻的體系。如果將機油直接加入水泥中進行固化,機油將影響水泥水化反應(yīng)過程,并最終導(dǎo)致制成的水泥固化體性能達不到國家標準GB14569.1-2011要求。因此,目前迫切需要一種新的方法,以解決上述問題。
技術(shù)實現(xiàn)要素:本發(fā)明的發(fā)明目的在于:針對目前采用水泥固化法處理廢機油時,機油與水泥相容性差,難以獲得滿足國家標準GB14569.1-2011要求的包容廢機油水泥固化體的問題,提供一種放射性廢機油高強度水泥固化體的制備方法。本發(fā)明采用將機油與水乳化后進行水泥固化,同時在固化水泥配方中加入了粉煤灰、吸油樹脂、木質(zhì)纖維作為添加劑,加大水泥固化體的強度和降低放射性核素的浸出率。本發(fā)明能有效解決機油與水泥相容性問題,所制備的含有機物的水泥固化體性能優(yōu)于國家標準GB14569.1-2011要求。本發(fā)明設(shè)計合理,操作方便,工藝簡單,投資少,安全可靠,能夠滿足放射性廢機油的處理要求,對于處理放射性廢機油具有重要意義。為了實現(xiàn)上述目的,本發(fā)明采用如下技術(shù)方案:一種放射性廢機油高強度水泥固化體的制備方法,包括如下步驟:(1)制備均質(zhì)水包油乳液將乳化劑、機油、水混合后,高速攪拌,形成均質(zhì)水包油乳液;(2)制備水泥漿料將水泥、粉煤灰混勻后,向其中加水濕潤,形成水泥漿料;(3)制備水泥固化體將步驟1制備的均質(zhì)水包油乳液、步驟2制備的水泥漿料、吸油劑、水泥體增強劑混合,攪拌均勻,經(jīng)固化養(yǎng)護后,即得水泥固化體;所述步驟1中,機油、水、乳化劑的體積比為1~1.5:1~2:0.1~0.2;所述步驟2中,水泥、粉煤灰、水按質(zhì)量比是1:0.05~0.1:0.1~0.2;所述步驟3中,步驟1制備的均質(zhì)水包油乳液、步驟2中的水泥、吸油劑、水泥體增強劑的質(zhì)量比為0.35~0.50:1:0.01~0.15:0.01~0.1。所述步驟1中,乳化劑為司苯、吐溫、十二烷基苯磺酸鈉、十二烷基硫酸鈉、辛基酚聚氧乙烯醚中的兩種或兩種以上。所述步驟2中,水泥為普通硅酸鹽水泥、鋁酸鹽水泥、火山灰水泥中的一種或多種。作為優(yōu)選,所述步驟1中,機油、水、乳化劑的體積比為1~1.5:1:0.1。作為優(yōu)選,所述步驟2中,水泥、粉煤灰、水按質(zhì)量比是1:0.05~0.1:0.1。所述吸油劑為吸油樹脂,所述水泥體增強劑為木質(zhì)纖維。一種放射性廢機油高強度水泥固化體的制備方法,包括如下步驟:(a)制備均質(zhì)水包油乳液將乳化劑、機油、水混合后,高速攪拌,形成均質(zhì)水包油乳液;(b)制備水泥漿料將水泥、粉煤灰、吸油劑、水泥體增強劑混勻后,向其中加水濕潤,形成水泥漿料;(c)制備水泥固化體將步驟a制備的均質(zhì)水包油乳液、步驟b制備的水泥漿料混合,攪拌均勻,經(jīng)固化養(yǎng)護后,即得水泥固化體;所述步驟a中,機油、水、乳化劑的體積比為1~1.5:1~2:0.1~0.2;所述步驟c中,水泥固化體中各組分的質(zhì)量比為均質(zhì)水包油乳液:水泥:粉煤灰:吸油劑:水泥體增強劑=0.30~0.50:1:0.05~0.1:0.01~0.15:0.01~0.1。作為優(yōu)選,所述步驟c中,水泥固化體中各組分的質(zhì)量比為均質(zhì)水包油乳液:水泥:粉煤灰:吸油劑:水泥體增強劑=0.42:1:0.05:0.03:0.01。針對前述問題,本申請?zhí)峁┮环N放射性廢機油高強度水泥固化體的制備方法。本發(fā)明中,首先利用乳化劑將機油與水乳化形成水包油型乳液(即均質(zhì)水包油乳液),然后制備水泥漿料、固化,得到水泥固化體。經(jīng)過實際測定,本發(fā)明中所獲得水泥固化體的機油包容量大于15%,固化體抗壓強度大,最大達12.6MPa,顯著優(yōu)于現(xiàn)有技術(shù),其它各方面指標均滿足國家標準GB14569.1-2011要求。本發(fā)明可用于核工業(yè)中低水平放射性污染廢機油的固化處理,有效降低放射性廢物管理的安全隱患,具有重要的意義。附圖說明本發(fā)明將通過例子并參照附圖的方式說明,其中:圖1為實施例8所制備的樣品圖。圖2為實施例9所制備的樣品圖。圖3為采用現(xiàn)有方法制備的廢油乳液圖。圖4為采用現(xiàn)有方法制備的固化體圖。具體實施方式本說明書中公開的所有特征,或公開的所有方法或過程中的步驟,除了互相排斥的特征和/或步驟以外,均可以以任何方式組合。本說明書中公開的任一特征,除非特別敘述,均可被其他等效或具有類似目的的替代特征加以替換。即,除非特別敘述,每個特征只是一系列等效或類似特征中的一個例子而已。實施例1將廢機油、乳化劑和水按體積比1:0.1:1.0的比例充分攪拌后,形成機油乳化液。將普通硅酸鹽水泥、粉煤灰、吸油樹脂、木質(zhì)纖維按質(zhì)量比1:0.05:0.03:0.01攪拌均勻后,形成水泥漿料。將上述水泥漿料與廢機油乳化液按質(zhì)量比1:0.5攪拌均勻,經(jīng)固化養(yǎng)護后,得到的水泥固化體強度為8.9MPa。實施例2將廢機油、乳化劑和水按體積比1:0.1:1的比例充分攪拌后,形成機油乳化液。將普通硅酸鹽水泥、粉煤灰、水、吸油樹脂、木質(zhì)纖維按質(zhì)量比1:0.05:0.1:0.03:0.01攪拌均勻后,形成水泥漿料。將上述水泥漿料與廢機油乳化液按質(zhì)量比1:0.5攪拌均勻,經(jīng)固化養(yǎng)護后,得到的水泥固化體強度為11.3MPa。與實施例1相比,實施例2在制備水泥漿料的過程中,加入部分水,使水泥漿料濕潤,其能夠有效減少水泥漿料與廢機油乳化液接觸時,破乳現(xiàn)象的產(chǎn)生,最終顯著提高水泥固化體的強度。實施例3將廢機油、乳化劑和水按體積比1.0:0.1:1的比例充分攪拌后,形成機油乳化液。將普通硅酸鹽水泥、粉煤灰、水按質(zhì)量比1:0.05:0.1攪拌均勻后,形成水泥漿料。將上述水泥漿料與機油乳化液、吸油樹脂、木質(zhì)纖維按質(zhì)量比1:0.5:0.025:0.008攪拌均勻,經(jīng)固化養(yǎng)護后,得到的水泥固化體強度為11.2MPa。實施例3與實施例2相比,吸油樹脂與木質(zhì)纖維的添加順序不同,但兩者的實驗結(jié)果無明顯差異。這表明:吸油樹脂與木質(zhì)纖維先添加于水泥漿料中或最后添加,不會對水泥固化體本身產(chǎn)生影響。實施例4將廢機油、乳化劑和水按體積比1.0:0.1:1.5的比例充分攪拌后,形成機油乳化液。將普通硅酸鹽水泥、粉煤灰、水、吸油樹脂、木質(zhì)纖維按質(zhì)量比1:0.05:0.1:0.03:0.01攪拌均勻后,形成水泥漿料。將上述水泥漿料與機油乳化液按質(zhì)量比1:0.45攪拌均勻,經(jīng)固化養(yǎng)護后,得到的水泥固化體強度為12.5MPa。實施例5將廢機油、乳化劑和水按體積比1.3:0.1:1的比例充分攪拌后,形成機油乳化液。將普通硅酸鹽水泥、粉煤灰、水、吸油樹脂、木質(zhì)纖維按質(zhì)量比1:0.05:0.1:0.03:0.01攪拌均勻后,形成水泥漿料。將上述水泥漿料與廢機油乳化液按質(zhì)量比1:0.5攪拌均勻,得到的水泥固化體強度為9.3MPa。對比實施例1將廢機油、乳化劑和水按體積比2:0.1:1的比例充分攪拌后,形成機油乳化液。將普通硅酸鹽水泥、粉煤灰、水、吸油樹脂、木質(zhì)纖維按質(zhì)量比1:0.05:0.1:0.03:0.01攪拌均勻后,形成水泥漿料。將上述水泥漿料與廢機油乳化液按質(zhì)量比1:0.5攪拌均勻,得到的水泥固化體強度為6.8MPa,該過程攪拌相對困難,上層少許浮油。通過實施例4、5與對比實施例1的比較,能夠看出:采用本申請技術(shù)方案之外的方案,其固化強度難以滿足相關(guān)的要求,不能用于放射性廢機油的水泥固化處理。實施例6將廢機油、乳化劑和水按體積比1.3:0.1:1的比例充分攪拌后,形成機油乳化液。將普通硅酸鹽水泥、粉煤灰、水、吸油樹脂、木質(zhì)纖維按質(zhì)量比1:0.05:0.1:0.03:0.01攪拌均勻后,形成水泥漿料。將上述水泥漿料與廢機油乳化液按質(zhì)量比1:0.4攪拌均勻,得到的水泥固化體強度為8.0MPa。本實施例中,乳化劑采用十二烷基苯磺酸鈉與辛基酚聚氧乙烯醚復(fù)配而成。實施例7將廢機油、乳化劑和水按體積比1.3:0.1:1的比例充分攪拌后,形成機油乳化液。將普通硅酸鹽水泥、粉煤灰、水、吸油樹脂、木質(zhì)纖維按質(zhì)量比1:0.05:0.1:0.03:0.01攪拌均勻后,形成水泥漿料。將上述水泥漿料與廢機油乳化液按質(zhì)量比1:0.55攪拌均勻,得到的水泥固化體強度為7.3MPa。養(yǎng)護后,該固化體上層有少許乳化液干燥的跡象。實施例8將廢機油、乳化劑和水按體積比1.3:0.1:1的比例充分攪拌后,形成機油乳化液。將普通硅酸鹽水泥、粉煤灰、水、吸油樹脂、木質(zhì)纖維按質(zhì)量比1:0.1:0.1:0.07:0.05攪拌均勻后,形成水泥漿料。將上述水泥漿料與廢機油乳化液按質(zhì)量比1:0.5攪拌均勻,得到的水泥固化體強度為8.3MPa。對比實施例2將廢機油、乳化劑和水按體積比2:0.1:1的比例充分攪拌后,形成機油乳化液。將普通硅酸鹽水泥、粉煤灰、水、吸油樹脂、木質(zhì)纖維按質(zhì)量比1:0.1:0.1:0.15:0.1攪拌均勻后,形成水泥漿料。將上述水泥漿料與廢機油乳化液按質(zhì)量比1:0.5攪拌均勻,得到的水泥固化體強度為7.8MPa,該過程漿料攪拌相對困難。實施例9將廢機油、乳化劑和水按體積比1.3:0.1:1的比例充分攪拌后,形成機油乳化液。將火山灰水泥、粉煤灰、水、吸油樹脂、木質(zhì)纖維按質(zhì)量比1:0.05:0.1:0.03:0.01攪拌均勻后,形成水泥漿料。將上述水泥漿料與廢機油乳化液按質(zhì)量比1:0.5攪拌均勻,得到的水泥固化體強度為12.6MPa。實施例10將廢機油、乳化劑和水按體積比1.3:0.1:1的比例充分攪拌后,形成機油乳化液。將鋁酸鹽水泥、粉煤灰、水、吸油樹脂、木質(zhì)纖維按質(zhì)量比1:0.05:0.1:0.03:0.01攪拌均勻后,形成水泥漿料。將上述水泥漿料與廢機油乳化液按質(zhì)量比1:0.5攪拌均勻得到的水泥固化體強度為8.6MPa。同時,申請人對上述實施例所得到的水泥固化體進行了測定,測定結(jié)構(gòu)如表1所示。表1獲得水泥固化體性能指標從表1的結(jié)果抗壓看出,本發(fā)明中制備的廢機油水泥固化體,抗壓強度較高,浸出率較低,滿足國家標準要求,具有較好的應(yīng)用前景。對比實驗一經(jīng)過檢索,申請人發(fā)現(xiàn)中國專利ZL201010534138.1(簡稱在先申請)公開了一種放射性有機廢液水泥固化的方法,該專利與本發(fā)明的方法較為類似。為此,申請人依照中國專利ZL201010534138.1中提供的方法及配方,進行了廢機油固化的驗證實驗。實驗過程及結(jié)果如下:①乳化實驗過程:將機油、常見復(fù)配乳化劑、水以體積比為1:(0.8~1):(0.15~0.3)混合,該比例條件下機油較難以形成均一的油水乳液,乳化后機油與水分層明顯。②固化實驗過程:將上述機油水混合液與水泥、沸石、石灰與常用水泥促凝劑CaCl2按專利(專利申請?zhí)枺?01010534138.1)公布配方比例進行固化。其中,圖3為采用在先申請制備的廢油乳液圖,圖4為采用該方法制備的固化體圖,通過圖3、4可以看出:油水不能均一乳液,固化體強度及28天后強度都不能滿足國標要求。實驗表明,該固化過程中,機油水混合液與水泥仍然難以相容,攪拌困難,最后形成的固化體強度及其它性能不能滿足國家標準GB14569.1-2011要求,因此,該專利方法不適用于放射性廢機油的水泥固化。通過對比可以看出,本發(fā)明能夠有效實現(xiàn)放射性廢機油的水泥固化,所制備的固化體具有較高的機械強度,且機油包容量大于15%,其他各項指標均滿足國家標準GB14569.1-2011的要求。本發(fā)明并不局限于前述的具體實施方式。本發(fā)明擴展到任何在本說明書中披露的新特征或任何新的組合,以及披露的任一新的方法或過程的步驟或任何新的組合。