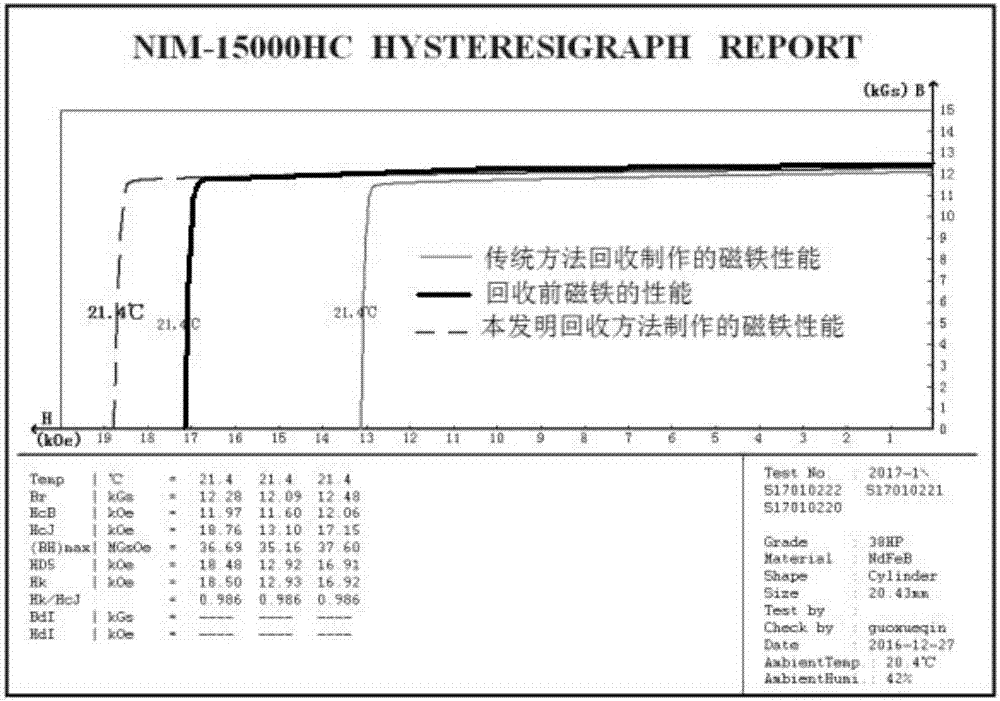
本發(fā)明涉及磁性材料制備工藝,尤其涉及一種利用燒結釹鐵硼廢料制作高性能釹鐵硼的方法。
背景技術:
:燒結釹鐵硼作為目前綜合磁性能最好,性價比最高的永磁材料,自問世以來,被廣泛運用于汽車,電子,電動,能源,醫(yī)療,信息技術等領域,被業(yè)界稱之為磁王。近幾年來,隨著燒結釹鐵硼新的技術新工藝的不斷發(fā)展,燒結釹鐵硼的綜合磁性能逐步提高,燒結釹鐵硼在整個永磁市場份額也大大提升,近年來,各個領域對燒結釹鐵硼的需求總量以每年20%以上的增速不斷攀升。但另一方面,釹鐵硼的廣泛運用帶來對稀土資源的巨大消耗,伴隨著一些產(chǎn)品的報廢產(chǎn)生的釹鐵硼廢料也越來越多,釹鐵硼制造企業(yè)中各個工序產(chǎn)生的不良品也具有較大的量,如果能將這些報廢的磁體和不良品回收利用,可減少稀土資源的大量浪費。而目前釹鐵硼廢料最常見的回收辦法是對廢料進行破碎后氧化焙燒,然后溶解到酸液中再對稀土進行分離和提取,此種方法存在著工藝復雜,對環(huán)境污染嚴重,回收率低等缺點。如果能將回收的釹鐵硼磁體直接用作制作新磁體的原材料進行回收利用,釹鐵硼的磁體的回收工序大大簡化,回收利用率也將大大提高。目前在利用回收的釹鐵硼磁體制作新的磁體時,由于回收磁體表面存在氧化層,在磁體破碎過程中磁體也會吸氧,造成最終制作的新磁體的矯頑力較低,新磁體的致密度低造成剩磁也較低。技術實現(xiàn)要素:針對上述技術問題,本發(fā)明提供了一種利用燒結釹鐵硼廢料制作高性能釹鐵硼的方法。本發(fā)明提供的技術方案為:一種利用燒結釹鐵硼廢料制作高性能釹鐵硼的方法,在進行氫爆處理時加入甩片,甩片成分為(dyndx)(coycuzfe)0.84,其中x取值為0.25-0.3,y取值為10-20,z取值為2-4,添加甩片的重量比例為1-5%。優(yōu)選的是,所述的利用燒結釹鐵硼廢料制作高性能釹鐵硼的方法中,進行燒結之前,向經(jīng)氫爆處理的廢料中添加dyh3,且添加dyh3的重量比例為0.2-0.5%。優(yōu)選的是,所述的利用燒結釹鐵硼廢料制作高性能釹鐵硼的方法中,燒結溫度為1020-1070℃,保溫時間為6-12h。優(yōu)選的是,所述的利用燒結釹鐵硼廢料制作高性能釹鐵硼的方法,其具體包括以下步驟:步驟(1)對燒結釹鐵硼廢料進行前處理,制成磁體塊;步驟(2)對磁體塊進行所述氫爆處理,制成粗粉;步驟(3)對粗粉進行機械粉碎,添加固體添加劑,再進行氣流磨研磨成平均粒度為2.8-3.2μm的細粉,向細粉中添加液態(tài)潤滑劑,并按所述添加dyh3的重量比例向細粉中添加dyh3;步驟(4)待加入dyh3的細粉鈍化后,壓制成壓坯,并進行等靜壓處理;步驟(5)燒結,回火。優(yōu)選的是,所述的利用燒結釹鐵硼廢料制作高性能釹鐵硼的方法中,所述步驟(2)中,所述氫爆處理具體包括:先抽真空,待真空度達到1pa以下后停止抽真空,再充入氫氣使壓力達到正壓0.066-0.098mpa,并進行冷卻,當吸氫達到飽和以后,再抽真空并加熱到480-600℃進行脫氫。優(yōu)選的是,所述的利用燒結釹鐵硼廢料制作高性能釹鐵硼的方法中,所述步驟(3)中,所述固體添加劑包括硬脂酸鋅、硬脂酸鈣、聚乙二醇辛烷中的一種或多種。優(yōu)選的是,所述的利用燒結釹鐵硼廢料制作高性能釹鐵硼的方法中,所述液態(tài)潤滑劑包括甲酯類、醇類、液態(tài)石蠟等中的一種或多種。優(yōu)選的是,所述的利用燒結釹鐵硼廢料制作高性能釹鐵硼的方法中,所述步驟(4)中,所述等靜壓處理過程中,氧含量控制在0.5%以下,取向磁場為1.5t,壓坯密度3.6-4.2g/cm3,等靜壓壓力150-250mpa。優(yōu)選的是,所述的利用燒結釹鐵硼廢料制作高性能釹鐵硼的方法中,所述步驟(5)中,所述燒結過程具體包括:先將溫度升至250℃,保溫,之后繼續(xù)將溫度升至650℃,保溫,再繼續(xù)將溫度升至850℃,保溫,繼續(xù)將溫度升至1020-1070℃,保溫6-12個小時;所述回火過程具體包括:一級回火溫度為900℃,保溫時間為4-5h,之后先將溫度升至比二級回火溫度高15℃的位置,然后經(jīng)過2h降溫至二級回火溫度,并保溫3-4h,所述二級回火溫度460-620℃;所述燒結和回火過程中升溫速率為5-7℃/min。優(yōu)選的是,所述的利用燒結釹鐵硼廢料制作高性能釹鐵硼的方法中,所述步驟(1)具體包括:對燒結釹鐵硼廢料進行退磁處理,退磁過程中,在真空度小于0.01pa的情況下,升溫到380-420℃,經(jīng)保溫3-8h后充氬氣到50kpa,并送風將磁體冷卻到室溫;進行拋光去電鍍處理和去表面氧化層處理;再進行機械破碎處理,控制破碎環(huán)境中氧含量小于1%,破碎后的磁體塊直徑小于2cm,破碎后的磁體塊密封儲存,并充氮氣保護。本發(fā)明所述的利用燒結釹鐵硼廢料制作高性能釹鐵硼的方法在氫爆處理過程中加入了甩片,克服了用回收的燒結釹鐵硼磁體直接制備新的磁體氧含量高,致密化低,矯頑力低等缺點,改善了釹鐵硼磁體的性能。另外,本發(fā)明還在進行燒結之前,添加了一定量的dyh3,進一步改善了釹鐵硼磁體的性能。附圖說明圖1為實施例一中利用該燒結釹鐵硼廢料制備的磁體的性能曲線,燒結釹鐵硼廢料的性能曲線以及采用傳統(tǒng)方法(即不添加晶界改善相和dyh3)將燒結釹鐵硼廢料制成的磁體的性能曲線的對比圖;圖2為實施例二中利用該燒結釹鐵硼廢料制備的磁體的性能曲線,燒結釹鐵硼廢料的性能曲線以及采用傳統(tǒng)方法(即不添加晶界改善相和dyh3)將燒結釹鐵硼廢料制成的磁體的性能曲線的對比圖。具體實施方式下面結合附圖對本發(fā)明做進一步的詳細說明,以令本領域技術人員參照說明書文字能夠據(jù)以實施。本發(fā)明提供一種利用燒結釹鐵硼廢料制作高性能釹鐵硼的方法,在進行氫爆處理時加入甩片,甩片成分為(dyndx)(coycuzfe)0.84,其中x取值為0.25-0.3,y取值為10-20,z取值為2-4,添加甩片的重量比例為1-5%。在氫爆處理時,如不加上述甩片,部分稀土相會進入到主相中,導致稀土相過少,影響最終制備的磁體的矯頑力。添加了上述甩片后,甩片作為晶界改善相,可以增加稀土相,進而提高最終制備的磁體的矯頑力。在一個優(yōu)選的實施例中,所述的利用燒結釹鐵硼廢料制作高性能釹鐵硼的方法中,進行燒結之前,向經(jīng)氫爆處理的廢料中添加dyh3,且添加dyh3的重量比例為0.2-0.5%。在燒結過程中dyh3中的h會還原氧,進而降低料中的氧含量,從而提高最終制備的磁體的矯頑力。而dy則作為稀土成分,進入稀土相中,同時改善最終制備磁體的矯頑力。但dyh3的用量不宜過大,過大則導致最終制備磁體的剩磁降低。在一個優(yōu)選的實施例中,所述的利用燒結釹鐵硼廢料制作高性能釹鐵硼的方法中,燒結溫度為1020-1070℃,保溫時間為6-12h。經(jīng)研究,加入dyh3后,燒結溫度為1020-1070℃,保溫時間為6-12h,可以促使dyh3-的h分離出來,與料中所含氧進行反應。在一個優(yōu)選的實施例中,所述的利用燒結釹鐵硼廢料制作高性能釹鐵硼的方法,其具體包括以下步驟:步驟(1)對燒結釹鐵硼廢料進行前處理,制成磁體塊;步驟(2)對磁體塊進行所述氫爆處理,制成粗粉;步驟(3)對粗粉進行機械粉碎,添加固體添加劑,再進行氣流磨研磨成平均粒度為2.8-3.2μm的細粉,向細粉中添加液態(tài)潤滑劑,并按所述添加dyh3的重量比例向細粉中添加dyh3;步驟(4)待加入dyh3的細粉鈍化后,壓制成壓坯,并進行等靜壓處理;步驟(5)燒結,回火。在一個優(yōu)選的實施例中,所述的利用燒結釹鐵硼廢料制作高性能釹鐵硼的方法中,所述步驟(2)中,所述氫爆處理具體包括:先抽真空,待真空度達到1pa以下后停止抽真空,再充入氫氣使壓力達到正壓0.066-0.098mpa,并進行冷卻,當吸氫達到飽和以后,再抽真空并加熱到480-600℃進行脫氫。具體地,氫爆時先對氫爆爐進行抽真空,真空度達到1pa以下后關閉真空系統(tǒng),向氫爆爐內(nèi)充入氫氣使氫爆爐內(nèi)壓力達到正壓0.066-0.098mpa,并通冷卻水對反應釜進行冷卻,當吸氫達到飽和以后,對爐體進行抽真空并加熱到480-600℃進行脫氫。在一個優(yōu)選的實施例中,所述的利用燒結釹鐵硼廢料制作高性能釹鐵硼的方法中,所述步驟(3)中,所述固體添加劑包括硬脂酸鋅、硬脂酸鈣、聚乙二醇辛烷中的一種或多種。固體添加劑在氣流磨過程中,具有潤滑作用,避免已經(jīng)達到粒度的粉末顆粒重新團聚在一起,改善粉末的分散性,使最終研磨的粉末粒度分布均勻。粒度分布越均勻,最終制備磁體的綜合性能越好。具體地,氫爆后的粗粉經(jīng)過中碎機機械粉碎后,添加300-500ppm固體添加劑,之后在三維混粉機里混粗粉90-120min。將混完的粗粉經(jīng)過氣流磨研磨到平均粒度為2.8-3.2um的釹鐵硼細粉,氣流磨制粉工藝為,加氧量為0ppm(即在氣流磨過程中盡量避免加氧),研磨氣體壓力為0.4-0.5mpa,分級輪轉速4600-4950rpm。在一個優(yōu)選的實施例中,所述的利用燒結釹鐵硼廢料制作高性能釹鐵硼的方法中,所述液態(tài)潤滑劑包括甲酯類、醇類、液態(tài)石蠟等中的一種或多種。具體地,將細粉加入0.1-0.2%液態(tài)潤滑劑,添加0.2-0.5%的dyh3粉末,用v形混粉機混粉60-180min,將混完后的細粉裝入密封的金屬粉罐內(nèi),充氮氣保護。在一個優(yōu)選的實施例中,所述的利用燒結釹鐵硼廢料制作高性能釹鐵硼的方法中,所述步驟(4)中,所述等靜壓處理過程中,氧含量控制在0.5%以下,取向磁場為1.5t,壓坯密度3.6-4.2g/cm3,等靜壓壓力150-250mpa。具體地,將混完的細粉鈍化24h后,采用全密封自動壓機壓制成方塊壓坯,采用真空封裝機將壓坯封裝后用等靜壓機進行等靜壓處理,壓機氧含量控制在0.5%以下,取向磁場能達到1.5t,壓坯密度3.6-4.2g/cm3,等靜壓壓力150-250mpa。在一個優(yōu)選的實施例中,所述的利用燒結釹鐵硼廢料制作高性能釹鐵硼的方法中,所述步驟(5)中,所述燒結過程具體包括:先將溫度升至250℃,保溫,之后繼續(xù)將溫度升至650℃,保溫,再繼續(xù)將溫度升至850℃,保溫,繼續(xù)將溫度升至1020-1070℃,保溫6-12個小時;所述回火過程具體包括:一級回火溫度為900℃,保溫時間為4-5h,之后先將溫度升至比二級回火溫度高15℃的位置,然后經(jīng)過2h降溫至二級回火溫度,并保溫3-4h,所述二級回火溫度460-620℃;所述燒結和回火過程中升溫速率為5-7℃/min。具體地,將經(jīng)過等靜壓處理的壓坯在手套箱剪料后,采用真空燒結后在900℃進行一級回火,并在460-620℃進行二級回火。所述燒結溫度為1020-1070℃,保溫時間為6-12h,燒結過程中要分別經(jīng)過250℃,650℃,850℃的保溫平臺,以保證燒結過程中,能夠充分的脫氣以及致密化,且保證所有毛坯的燒結的一致性。一級回火保溫時間為4-5h,二級回火要求先升溫到t+15℃(t為二級回火保溫溫度),然后經(jīng)過2h降溫到t,保溫3-4h,所述燒結回火過程都必須在真空狀態(tài)下,升溫速率5-7℃/min,冷卻方式為充氬氣冷卻。在一個優(yōu)選的實施例中,所述的利用燒結釹鐵硼廢料制作高性能釹鐵硼的方法中,所述步驟(1)具體包括:對燒結釹鐵硼廢料進行退磁處理,退磁過程中,在真空度小于0.01pa的情況下,升溫到380-420℃,經(jīng)保溫3-8h后充氬氣到50kpa,并送風將磁體冷卻到室溫;進行拋光去電鍍處理和去表面氧化層處理;再進行機械破碎處理,控制破碎環(huán)境中氧含量小于1%,破碎后的磁體塊直徑小于2cm,破碎后的磁體塊密封儲存,并充氮氣保護。具體地,回收的磁體為燒結釹鐵硼磁體,對磁體的成分、微觀結構、性能牌號、表面鍍層無特殊要求。對于帶磁性的燒結釹鐵硼磁體需首先進行退磁處理,退磁方法為在真空熱處理爐中,在真空度小于0.01pa的情況下,將爐溫經(jīng)過1h升溫到380-420℃,經(jīng)保溫3-8h后充氬氣到50kpa,并開風機將磁體冷卻到室溫。之后將退磁后的磁體在金屬拋丸機里進行拋光去電鍍處理和去表面氧化層處理,拋光時間可根據(jù)實際情況選擇10-60min,拋光后的磁體儲存在干燥密封的塑料袋里。接下來,將拋光后的磁體在5h內(nèi)進行機械破碎處理,機械破碎可在氮氣氣氛保護下的顎式破碎機里進行,要求破碎機中氧含量小于1%,破碎后的磁體塊要求直徑小于2cm,破碎后的磁體塊要求儲存在密封的粉罐里,并充氮氣保護。為了進一步說明本發(fā)明的技術方案,提供以下實施例。實施例一1、對一批44m的不良品進行回收,廢料尺寸為11*7*32mm,原始磁性能br=13.6kgs;hcj=14.8koe,未充磁和電鍍。2、將上述磁體廢料在金屬拋丸機里進行拋光去表面氧化層處理,拋光時間為30min,拋光后的磁體儲存在干燥密封的塑料袋里。3、拋光后的磁體在5h內(nèi)進行機械破碎處理,機械破碎在氮氣氣氛保護下的顎式破碎機里進行,破碎機中氧含量小于1%,破碎后的磁體塊要求直徑小于2cm,破碎后的磁體塊儲存在密封的粉罐里,并充氮氣保護。4、將步驟3機械破碎后的磁體小塊放入氫爆爐氫爆處理,氫爆要加入一定比例的晶界相改善的甩片,添加晶界改善相甩片的重量比例為2%,晶界改善相甩片成分為(dynd0.27)(co16cu3fe)0.84。氫爆時先對氫爆爐進行抽真空,真空度達到1pa以下后關閉真空系統(tǒng),向氫爆爐內(nèi)充入氫氣使氫爆爐內(nèi)壓力達到正壓0.066-0.098mpa,并通冷卻水對反應釜進行冷卻,當吸氫達到飽和以后,對爐體進行抽真空并加熱到580℃進行脫氫。5、將步驟4氫爆后的粗粉,經(jīng)過中碎機機械粉碎后,添加350ppm固體添加劑硬脂酸鋅,在三維混粉機里混粗粉120min。6、將步驟5混完的粗粉經(jīng)過氣流磨研磨到平均粒度為2.8-3.0um的釹鐵硼細粉,氣流磨制粉工藝為,加氧量為0ppm,研磨氣體壓力為0.45mpa,分級輪轉速4800rpm。7、將步驟6制得的釹鐵硼細粉加入0.15%液態(tài)潤滑劑,所用的液態(tài)潤滑劑為甲酯類和醇類的混合物,并添加0.35%的dyh3粉末,用v形混粉機混粉60min,將混完后的細粉裝入密封的金屬粉罐內(nèi),充氮氣保護。8、將步驟7混完的細粉鈍化24h后,采用全密封自動壓機壓制成方塊壓坯,采用真空封裝機將壓坯封裝后用等靜壓機進行等靜壓處理,壓機氧含量控制在0.5%以下,取向磁場能達到1.5t,壓坯密度3.8g/cm3,等靜壓壓力200mpa。9、將步驟8經(jīng)過等靜壓處理的壓坯在手套箱剪料后,采用真空燒結后在900℃進行一級回火,并在520℃進行二級回火。所述燒結溫度為1050℃,保溫時間為8h,燒結過程中要分別經(jīng)過250℃,650℃,850℃的保溫平臺,以保證燒結過程中,能夠充分的脫氣以及致密化,且保證所有毛坯的燒結的一致性。一級回火保溫時間為4-5h,二級回火要求先升溫到535℃,然后經(jīng)過2h降溫到520℃,保溫4h,所述燒結回火過程都必須在真空狀態(tài)下,升溫速率5℃/min,冷卻方式為充氬氣冷卻。圖1中從左向右依次為本實施例利用該燒結釹鐵硼廢料制備的磁體的性能曲線,燒結釹鐵硼廢料的性能曲線以及采用傳統(tǒng)方法(即不添加晶界改善相和dyh3)將燒結釹鐵硼廢料制成的磁體的性能曲線。從圖1中可以看出,本實施例制備的磁體的矯頑力明顯大于燒結釹鐵硼廢料和傳統(tǒng)方法制備的磁體。下表是原始磁體的性能,采用傳統(tǒng)方法(即不添加晶界改善相和dyh3)回收的磁體和本方法制備的磁體性能對比列表。原始磁體傳統(tǒng)方法回收磁體本發(fā)明方法回收的磁體br(kgs)13.613.213.4hcj(koe)14.812.616.5實施例二1、對一批38h不良品進行回收,廢料尺寸為d19.8*3mm,原始磁性能br=12.5kgs;hcj=17.1koe,未充磁,電鍍ni-cu-ni。2、將上述磁體廢料在金屬拋丸機里進行拋光去電鍍和表面氧化層處理,拋光時間為60min,拋光后的磁體儲存在干燥密封的塑料袋里。3、拋光后的磁體在5h內(nèi)進行機械破碎處理,機械破碎在氮氣氣氛保護下的顎式破碎機里進行,破碎機中氧含量小于1%,破碎后的磁體塊要求直徑小于2cm,破碎后的磁體塊儲存在密封的粉罐里,并充氮氣保護。4、將步驟3機械破碎后的磁體小塊放入氫爆爐氫爆處理,氫爆要加入一定比例的晶界相改善的甩片,添加晶界改善相甩片的重量比例為2%,晶界改善相甩片成分為(dynd0.27)(co16cu3fe)0.84。氫爆時先對氫爆爐進行抽真空,真空度達到1pa以下后關閉真空系統(tǒng),向氫爆爐內(nèi)充入氫氣使氫爆爐內(nèi)壓力達到正壓0.066-0.098mpa,并通冷卻水對反應釜進行冷卻,當吸氫達到飽和以后,對爐體進行抽真空并加熱到580℃進行脫氫。5、將步驟4氫爆后的粗粉,經(jīng)過中碎機機械粉碎后,添加500ppm固體添加劑硬脂酸鋅,在三維混粉機里混粗粉120min;6、將步驟5混完的粗粉經(jīng)過氣流磨研磨到平均粒度為2.8-3.0um的釹鐵硼細粉,中所述氣流磨制粉工藝為,加氧量為0ppm,研磨氣體壓力為0.45mpa,分級輪轉速4900rpm。7、將步驟6制得的釹鐵硼細粉加入0.05%液態(tài)潤滑劑,所用的液態(tài)潤滑劑哪位甲酯類,醇類的混合物,并添加0.5%的dyh3粉末,用v形混粉機混粉120min,將混完后的細粉裝入密封的金屬粉罐內(nèi),充氮氣保護。8、將步驟7混完的細粉鈍化24h后,采用全密封自動壓機壓制成方塊壓坯,采用真空封裝機將壓坯封裝后用等靜壓機進行等靜壓處理,壓機氧含量控制在0.5%以下,取向磁場能達到1.5t,壓坯密度3.9g/cm3,等靜壓壓力200mpa。9、將步驟8經(jīng)過等靜壓處理的壓坯在手套箱剪料后,采用真空燒結后在900℃進行一級回火,并在560℃進行二級回火。所述燒結溫度為1040℃,保溫時間為6h,燒結過程中要分別經(jīng)過250℃,650℃,850℃的保溫平臺,以保證燒結過程中,能夠充分的脫氣以及致密化,且保證所有毛坯的燒結的一致性。一級回火保溫時間為4-5h,二級回火要求先升溫到575℃(,然后經(jīng)過2h降溫到560℃,保溫3.5h,所述燒結回火過程都必須在真空狀態(tài)下,升溫速率5℃/min,冷卻方式為充氬氣冷卻。圖2中從左向右依次為本發(fā)明利用該燒結釹鐵硼廢料制備的磁體的性能曲線,燒結釹鐵硼廢料的性能曲線以及采用傳統(tǒng)方法(即不添加晶界改善相和dyh3)將燒結釹鐵硼廢料制成的磁體的性能曲線。從圖2中可以看出,本實施例制備的磁體的矯頑力明顯大于燒結釹鐵硼廢料和傳統(tǒng)方法制備的磁體。下表是原始磁體的性能,采用傳統(tǒng)方法(即不添加晶界改善相和dyh3)回收的磁體和本方法制備的磁體性能對比列表。原始磁體傳統(tǒng)方法回收磁體本發(fā)明方法回收的磁體br(kgs)12.512.112.3hcj(koe)17.213.118.8實施例三1、對一批42uh不良品進行回收,廢料尺寸為50*20*1.8mm,原始磁性能br=13.1kgs;hcj=24.2koe,未充磁,表面磷化處理。2、將上述磁體廢料在金屬拋丸機里進行拋光去電鍍和表面氧化層處理,拋光時間為30min,拋光后的磁體儲存在干燥密封的塑料袋里。3、拋光后的磁體在5h內(nèi)進行機械破碎處理,機械破碎在氮氣氣氛保護下的顎式破碎機里進行,破碎機中氧含量小于1%,破碎后的磁體塊要求直徑小于2cm,破碎后的磁體塊儲存在密封的粉罐里,并充氮氣保護。4、將步驟3機械破碎后的磁體小塊放入氫爆爐氫爆處理,氫爆要加入一定比例的晶界相改善的甩片,添加晶界改善相甩片的重量比例為1%,晶界改善相甩片成分為(dynd0.25)(co10cu2fe)0.84。氫爆時先對氫爆爐進行抽真空,真空度達到1pa以下后關閉真空系統(tǒng),向氫爆爐內(nèi)充入氫氣使氫爆爐內(nèi)壓力達到正壓0.066-0.098mpa,并通冷卻水對反應釜進行冷卻,當吸氫達到飽和以后,對爐體進行抽真空并加熱到500℃進行脫氫。5、將步驟4氫爆后的粗粉,經(jīng)過中碎機機械粉碎后,添加350ppm固體添加劑硬脂酸鋅,在三維混粉機里混粗粉120min;6、將步驟5混完的粗粉經(jīng)過氣流磨研磨到平均粒度為2.8-2.9um的釹鐵硼細粉,中所述氣流磨制粉工藝為,加氧量為0ppm,研磨氣體壓力為0.45mpa,分級輪轉速4800rpm。7、將步驟6制得的釹鐵硼細粉加入0.15%液態(tài)潤滑劑,所用的液態(tài)潤滑劑哪位甲酯類,醇類的混合物,并添加0.2%的dyh3粉末,用v形混粉機混粉180min,將混完后的細粉裝入密封的金屬粉罐內(nèi),充氮氣保護。8、將步驟7混完的細粉鈍化24h后,采用全密封自動壓機壓制成方塊壓坯,采用真空封裝機將壓坯封裝后用等靜壓機進行等靜壓處理,壓機氧含量控制在0.5%以下,取向磁場能達到1.5t,壓坯密度3.8g/cm3,等靜壓壓力200mpa。9、將步驟8經(jīng)過等靜壓處理的壓坯在手套箱剪料后,采用真空燒結后在900℃進行一級回火,并在500℃進行二級回火。所述燒結溫度為1055℃,保溫時間為10h,燒結過程中要分別經(jīng)過250℃,550℃,850℃的保溫平臺,以保證燒結過程中,能夠充分的脫氣以及致密化,且保證所有毛坯的燒結的一致性。一級回火保溫時間為4-5h,二級回火要求先升溫到515℃(,然后經(jīng)過2h降溫到500℃,保溫4h,所述燒結回火過程都必須在真空狀態(tài)下,升溫速率5℃/min,冷卻方式為充氬氣冷卻。下表是原始磁體的性能,采用傳統(tǒng)方法(即不添加晶界改善相和dyh3)回收的磁體和本方法制備的磁體性能對比列表。原始磁體傳統(tǒng)方法回收磁體本發(fā)明方法回收的磁體br(kgs)13.112.813hcj(koe)24.220.325.6實施例四1、對一批48sh不良品進行回收,廢料尺寸為55*43*32mm,原始磁性能br=13.9kgs;hcj=19.3koe,未充磁,表面無鍍層。2、將上述磁體廢料在金屬拋丸機里進行拋光去電鍍和表面氧化層處理,拋光時間為60min,拋光后的磁體儲存在干燥密封的塑料袋里。3、拋光后的磁體在5h內(nèi)進行機械破碎處理,機械破碎在氮氣氣氛保護下的顎式破碎機里進行,破碎機中氧含量小于1%,破碎后的磁體塊要求直徑小于2cm,破碎后的磁體塊儲存在密封的粉罐里,并充氮氣保護。4、將步驟3機械破碎后的磁體小塊放入氫爆爐氫爆處理,氫爆要加入一定比例的晶界相改善的甩片,添加晶界改善相甩片的重量比例為1%,晶界改善相甩片成分為(dynd0.3)(co20cu4fe)0.84。氫爆時先對氫爆爐進行抽真空,真空度達到1pa以下后關閉真空系統(tǒng),向氫爆爐內(nèi)充入氫氣使氫爆爐內(nèi)壓力達到正壓0.066-0.098mpa,并通冷卻水對反應釜進行冷卻,當吸氫達到飽和以后,對爐體進行抽真空并加熱到500℃進行脫氫。5、將步驟4氫爆后的粗粉,經(jīng)過中碎機機械粉碎后,添加350ppm固體添加劑硬脂酸鋅,在三維混粉機里混粗粉120min;6、將步驟5混完的粗粉經(jīng)過氣流磨研磨到平均粒度為2.8-3.0um的釹鐵硼細粉,中所述氣流磨制粉工藝為,加氧量為0ppm,研磨氣體壓力為0.45mpa,分級輪轉速4850rpm。7、將步驟6制得的釹鐵硼細粉加入0.15%液態(tài)潤滑劑,所用的液態(tài)潤滑劑哪位甲酯類,醇類的混合物,并添加0.5%的dyh3粉末,用v形混粉機混粉120min,將混完后的細粉裝入密封的金屬粉罐內(nèi),充氮氣保護。8、將步驟7混完的細粉鈍化24h后,采用全密封自動壓機壓制成方塊壓坯,采用真空封裝機將壓坯封裝后用等靜壓機進行等靜壓處理,壓機氧含量控制在0.5%以下,取向磁場能達到1.5t,壓坯密度3.85g/cm3,等靜壓壓力200mpa。9、將步驟8經(jīng)過等靜壓處理的壓坯在手套箱剪料后,采用真空燒結后在900℃進行一級回火,并在520℃進行二級回火。所述燒結溫度為1058℃,保溫時間為10h,燒結過程中要分別經(jīng)過250℃,550℃,850℃的保溫平臺,以保證燒結過程中,能夠充分的脫氣以及致密化,且保證所有毛坯的燒結的一致性。一級回火保溫時間為4-5h,二級回火要求先升溫到535℃(,然后經(jīng)過2h降溫到520℃,保溫4h,所述燒結回火過程都必須在真空狀態(tài)下,升溫速率5℃/min,冷卻方式為充氬氣冷卻。下表是原始磁體的性能,采用傳統(tǒng)方法(即不添加晶界改善相和dyh3)回收的磁體和本方法制備的磁體性能對比列表。原始磁體傳統(tǒng)方法回收磁體本發(fā)明方法回收的磁體br(kgs)13.913.613.8hcj(koe)19.317.921.1盡管本發(fā)明的實施方案已公開如上,但其并不僅僅限于說明書和實施方式中所列運用,它完全可以被適用于各種適合本發(fā)明的領域,對于熟悉本領域的人員而言,可容易地實現(xiàn)另外的修改,因此在不背離權利要求及等同范圍所限定的一般概念下,本發(fā)明并不限于特定的細節(jié)和這里示出與描述的圖例。當前第1頁12