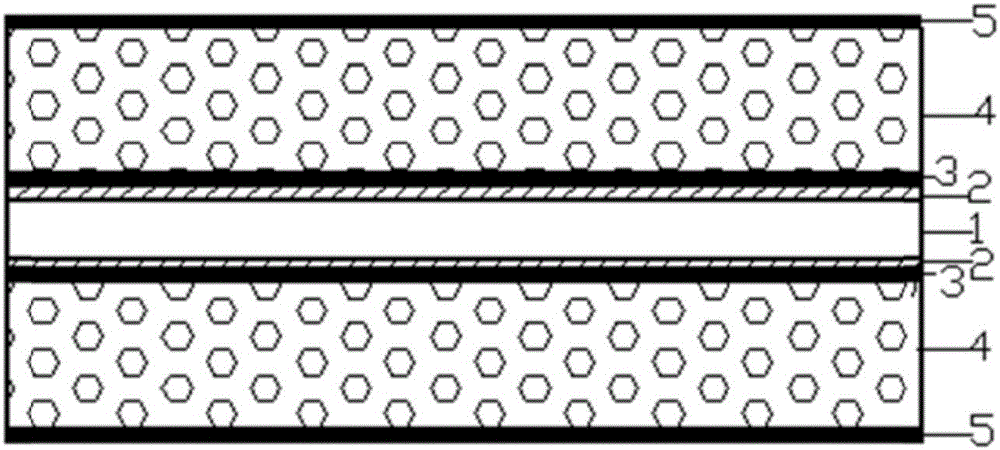
本發(fā)明涉及鋰離子電池
技術領域:
,具體涉及一種鋰離子電池復合負極極片及其制備方法、鋰離子電池。
背景技術:
:商品化的鋰離子電池以其能量密度高、循環(huán)壽命長、環(huán)境友好等特性廣泛應用于電動汽車、數(shù)碼電子、儲能等領域。隨著市場對鋰離子電池性能要求越來越高,鋰離子電池能量密度和安全性能的提高成為研發(fā)的熱點。目前,提高鋰離子電池安全的措施主要有:采用陶瓷隔膜、采用安全性電解液及其采用安全性能高的正負極材料,很少通過對負極極片表面改性提高鋰離子的安全性能。提高鋰離子電池能量密度的方法主要有:采用高容量、高壓實的正負極材料、采用高壓電解液及其優(yōu)化電池設計等措施提高能量密度,比如選用高容量的硅負極,但是由于采用硅材料作為負極材料存在膨脹率高(≥300%),使其極片上活性物質(zhì)與集流體的分離,造成容量衰減較快,使其難以產(chǎn)業(yè)化應用。而通過氣相沉積法將硅化合物沉積在集流體表面,不但可以降低材料的膨脹系數(shù),而且提高材料與集流體之間的接觸面積,降低內(nèi)阻?,F(xiàn)有技術中,CN104347842A公開了一種鋰離子二次電池復合負極片,包括金屬集流體和沉積在所述金屬集流體表面的第一負極活性層,以及涂敷設置在所述第一負極活性層表面的第二負極活性層,所述第一負極活性層為硅基活性材料層,所述硅基活性材料層的厚度為5nm~2μm,所述第二負極活性層的材料包括負極活性材料、粘結劑和導電劑,所述負極活性材料為碳素類負極材料和鈦酸鋰中的至少一種。并且進一步公開了所述硅基活性材料選自硅單質(zhì)、硅氧化物和硅合金中的一種。該復合負極片,由于較小厚度的硅基活性材料與電解液的直接接觸,緩沖硅基活性材料的體積膨脹,從而有效解決硅基活性材料因體積膨脹效應而易從集流體脫落的問題,延長鋰離子二次電池的循環(huán)使用壽命。但是硅材料本身的導電率低,使得該復合負極片的第一活性層和第二活性層之間的導電性差,降低了鋰離子電池的倍率性能。技術實現(xiàn)要素:本發(fā)明的目的是提供一種倍率性能更好的鋰離子電池復合負極極片。本發(fā)明還提供了一種鋰離子電池復合負極極片的制備方法,及使用上述極片的鋰離子電池。為了實現(xiàn)以上目的,本發(fā)明的鋰離子電池復合負極極片所采用的技術方案是:一種鋰離子電池復合負極極片,包括集流體、設置在集流體表面的硅材料層、設置在硅材料層表面的石墨烯層、設置在石墨烯層表面的活性物質(zhì)層;所述硅材料層的硅材料為SiB4、SiB6、Mg2Si、Ni2Si、TiSi2、CoSi2、CaSi2、MnSi2、SiC中的一種。本發(fā)明的鋰離子電池復合負極極片,通過在集流體表面設置硅材料層,可以提高硅材料與集流體之間的接觸面積,降低內(nèi)阻,提高其循環(huán)性能和能量密度;在硅材料層上設置石墨烯層,可以降低硅材料層在使用過程中的膨脹率,同時石墨烯的高導電性又可以提高極片的倍率性能。優(yōu)選的,所述硅材料層、石墨烯層和活性物質(zhì)層的厚度比為(0.5~2):(0.5~2):(80~150)。優(yōu)選的,集流體和硅材料層的厚度比為(8~15):(0.5~2)。所述集流體為銅網(wǎng)。所述銅網(wǎng)的厚度為10~12μm。所述銅網(wǎng)的孔隙率為30~60%。優(yōu)選的,所述活性物質(zhì)層由石墨、導電劑SP、LA132粘結劑組成。所述石墨、導電劑SP和LA132粘結劑的質(zhì)量比為95:1:4。優(yōu)選的,上述鋰離子電池復合負極極片還包括設置在活性物質(zhì)層表面的氧化鋁復合材料層。在活性物質(zhì)層表面再沉積一層氧化鋁復合材料,可以降低硅材料使用過程中造成的極片膨脹帶來的安全隱患,提高其安全性能。進一步優(yōu)選的,所述氧化鋁復合材料層與活性物質(zhì)層的厚度比為(1~5):(80~150)。進一步優(yōu)選的,所述氧化鋁復合材料層由氧化鋁、偏鋁酸鋰、粘結劑組成。偏鋁酸鋰中的鋰離子能夠提高大倍率條件下鋰離子的傳輸速率,并降低極片內(nèi)阻提高其倍率性能。更進一步優(yōu)選的,所述氧化鋁、偏鋁酸鋰、粘結劑的質(zhì)量比為(1~20):(1~5):(5~20)。所述粘結劑為PVDF粘結劑。本發(fā)明的鋰離子電池復合負極極片的制備方法所采用的技術方案為:一種上述的鋰離子電池復合負極極片的制備方法,包括以下步驟:1)將硅材料沉積在集流體表面,形成硅材料層,得到極片A;2)將石墨烯沉積在步驟1)所得的極片A表面,形成石墨烯層,得到極片B;3)將負極漿料涂覆在步驟2)所得的極片B表面,形成活性物質(zhì)層,得到極片C,即得。本發(fā)明的鋰離子電池復合負極極片的制備方法,沉積形成的硅材料層更致密,有助于提高本發(fā)明的鋰離子電池復合負極極片的循環(huán)性能和能量密度;并且工藝簡單,適于推廣應用。優(yōu)選的,步驟1)中,在集流體上沉積硅材料采用的是磁控濺射法或氣相沉積法;步驟2)中,在極片A上沉積石墨烯采用的是磁控濺射法或氣相沉積法。采用磁控濺射法或氣相沉積法將硅材料沉積在集流體表面,能夠進一步降低硅材料和集流體的接觸面積、降低內(nèi)阻,同時得到的硅材料層更致密,循環(huán)性能和能量密度更高;沉積得到的硅材料層的厚度較薄、一致性更高。優(yōu)選的,步驟1)中,所述集流體與硅材料層的厚度比為(8~15):(0.5~2)。所述集流體為銅網(wǎng)。所述銅網(wǎng)的厚度為10~12μm。銅網(wǎng)的孔隙率為30~60%。優(yōu)選的,步驟2)中,所述石墨烯層和硅材料層的厚度比為(0.5~2):(0.5~2)。步驟3)中,所述活性物質(zhì)層與石墨烯層的厚度比為(80~150):(0.5~2)。優(yōu)選的,步驟3)中,所述負極漿料的組成為石墨,導電劑SP、LA132粘結劑、二次蒸餾水。所述石墨、導電劑SP、LA132粘結劑和二次蒸餾水的質(zhì)量比為95:1:4:150。優(yōu)選的,上述鋰離子電池復合負極極片的制備方法,還包括在步驟3)所得的極片C上涂覆氧化鋁復合漿料,形成氧化鋁復合材料層。所述氧化鋁復合材料層與活性物質(zhì)層的厚度比為(1~5):(80~150)。所述氧化鋁復合漿料的組成為氧化鋁,偏鋁酸鋰,粘結劑和溶劑。以質(zhì)量計,氧化鋁:偏鋁酸鋰:粘結劑:溶劑=(1~20):(1~5):(5~20):100。所述粘結劑為PVDF粘結劑。所述溶劑為NMP溶劑。所述氧化鋁復合漿料的粘度為200~2000mPa·s。本發(fā)明的技術方案還在于:一種采用上述的鋰離子電池復合負極極片的鋰離子電池。本發(fā)明的鋰離子電池,采用上述鋰離子電池復合負極極片,具有更好的循環(huán)性能、更低的內(nèi)阻和更高的倍率性能;同時有更高的安全性能。附圖說明圖1為鋰離子電池復合負極極片的結構示意圖,其中,1-集流體,2-硅材料層,3-石墨烯層,4-活性物質(zhì)層,5-氧化鋁復合材料層。具體實施方式以下結合具體實施方式對本發(fā)明的技術方案作進一步說明。實施例1本實施例的鋰離子電池復合負極極片,如圖1所示,包括集流體1和沿遠離集流體方向上依次設置的硅材料層2、石墨烯層3、活性物質(zhì)層4和氧化鋁材料層5,即在集流體1表面設置硅材料層2,在硅材料層2表面設置石墨烯層3,在石墨烯層3表面設置活性物質(zhì)層4,在活性物質(zhì)層4表面設置氧化鋁材料層5。集流體為銅網(wǎng),厚度為10μm,孔隙率為50%;集流體、硅材料層、石墨烯層、活性物質(zhì)層和氧化鋁材料層的厚度比為10:1:1:120:3;所述硅材料為SiB4;所述活性物質(zhì)層由人造石墨、導電劑SP、LA132粘結劑組成,人造石墨、導電劑SP、LA132粘結劑的質(zhì)量比為95:1:4;所述氧化鋁材料層由氧化鋁、偏鋁酸鋰、PVDF粘結劑組成,氧化鋁、偏鋁酸鋰、PVDF粘結劑的質(zhì)量比為10:3:15。本實施例的鋰離子電池復合負極極片的制備方法,包括以下步驟:1)負極漿料和氧化鋁復合漿料的制備負極漿料的制備:稱取LA132粘結劑40g添加到1500g的二次蒸餾水中,攪拌均勻,然后添加10g導電劑SP分散均勻,再分三批加入950g人造石墨分散均勻,得到負極漿料;氧化鋁復合漿料的制備:取氧化鋁10g,偏鋁酸鋰3g,PVDF粘結劑15g加入100mLNMP溶劑中,采用高速分散機攪拌得到粘度為1000mPa·s的氧化鋁復合漿料;2)通過磁控濺射法將硅材料沉積在集流體兩面,分別形成硅材料層,得到極片A;3)通過氣相沉積法將石墨烯沉積在步驟2)所得的極片A的兩面,形成石墨烯層,得到極片B;4)通過噴涂技術將負極漿料涂覆在步驟3)所得的極片B的兩面,干燥,形成活性物質(zhì)層,得到極片C;5)通過噴涂技術將步驟1)所得的氧化鋁復合漿料涂覆在步驟4)所得的極片C的兩個表面,干燥形成氧化復合材料層,即得。實施例2本實施例的鋰離子電池復合負極極片,包括集流體和沿遠離集流體方向上依次設置的硅材料層、石墨烯層、活性物質(zhì)層和氧化鋁材料層,即在集流體表面設置硅材料層,在硅材料層表面設置石墨烯層,在石墨烯層表面設置活性物質(zhì)層,在活性物質(zhì)層表面設置氧化鋁材料層。集流體為銅網(wǎng),厚度為10μm,孔隙率為30%;集流體、硅材料層、石墨烯層、活性物質(zhì)層和氧化鋁材料層的厚度比為8:0.5:0.5:80:1。所述硅材料為Mg2Si;所述活性物質(zhì)層由人造石墨、導電劑SP、LA132粘結劑組成,人造石墨、導電劑SP、LA132粘結劑的質(zhì)量比為95:1:4;所述氧化鋁材料層由氧化鋁、偏鋁酸鋰、PVDF粘結劑組成,氧化鋁、偏鋁酸鋰、PVDF粘結劑的質(zhì)量比為1:1:5。本實施例的鋰離子電池復合負極極片的制備方法,包括以下步驟:1)負極漿料和氧化鋁復合漿料的制備負極漿料的制備:稱取LA132粘結劑40g添加到1500g的二次蒸餾水中,攪拌均勻,然后添加10g導電劑SP分散均勻,再分三批加入950g人造石墨分散均勻,得到負極漿料;氧化鋁復合漿料的制備:取氧化鋁1g,偏鋁酸鋰1g,PVDF粘結劑5g加入100mLNMP溶劑中,采用高速分散機攪拌得到粘度為200mPa·s的氧化鋁復合漿料;2)通過磁控濺射法將硅材料沉積在集流體的兩面,形成硅材料層,得到極片A;3)通過氣相沉積法將石墨烯沉積在步驟2)所得的極片A的兩面,形成石墨烯層,得到極片B;4)通過噴涂技術將負極漿料涂覆在步驟3)所得的極片B的兩面,干燥,形成活性物質(zhì)層,得到極片C;5)通過噴涂技術將步驟1)所得的氧化鋁復合漿料涂覆在步驟4)所得的極片C的兩個表面,干燥形成氧化復合材料層,即得。實施例3本實施例的鋰離子電池復合負極極片,包括集流體和沿遠離集流體方向上依次設置的硅材料層、石墨烯層、活性物質(zhì)層和氧化鋁材料層,即在集流體表面設置硅材料層,在硅材料層表面設置石墨烯層,在石墨烯層表面設置活性物質(zhì)層,在活性物質(zhì)層表面設置氧化鋁材料層。集流體為銅網(wǎng),厚度為10μm,孔隙率為60%;集流體、硅材料層、石墨烯層、活性物質(zhì)層和氧化鋁材料層的厚度比為15:2:2:150:5。所述硅材料為TiSi2;所述活性物質(zhì)層由人造石墨、導電劑SP、LA132粘結劑組成,人造石墨、導電劑SP、LA132粘結劑的質(zhì)量比為95:1:4;所述氧化鋁材料層由氧化鋁、偏鋁酸鋰、PVDF粘結劑組成,氧化鋁、偏鋁酸鋰、PVDF粘結劑的質(zhì)量比為20:5:20。本實施例的鋰離子電池復合負極極片的制備方法,包括以下步驟:1)負極漿料和氧化鋁復合漿料的制備負極漿料的制備:稱取LA132粘結劑40g添加到1500g的二次蒸餾水中,攪拌均勻,然后添加10g導電劑SP分散均勻,再分三批加入950g人造石墨分散均勻,得到負極漿料;氧化鋁復合漿料的制備:取氧化鋁20g,偏鋁酸鋰5g,PVDF粘結劑20g加入100mLNMP溶劑中,采用高速分散機攪拌得到粘度為2000mPa·s的氧化鋁復合漿料;2)通過磁控濺射法將硅材料沉積在集流體上,形成硅材料層,得到極片A;3)通過氣相沉積法將石墨烯沉積在步驟2)所得的極片A的兩面,形成石墨烯層,得到極片B;4)通過噴涂技術將負極漿料涂覆在步驟3)所得的極片B的兩面,干燥,形成活性物質(zhì)層,得到極片C;5)通過噴涂技術將步驟1)所得的氧化鋁復合漿料涂覆在步驟4)所得的極片C的兩面,干燥形成氧化復合材料層,即得。實施例4本實施例的鋰離子電池復合負極極片,包括集流體和沿遠離集流體方向上依次設置的硅材料層、石墨烯層、活性物質(zhì)層,即在集流體表面設置硅材料層,在硅材料層表面設置石墨烯層,在石墨烯層表面設置活性物質(zhì)層。集流體為銅網(wǎng),厚度為12μm,孔隙率為50%;集流體、硅材料層、石墨烯層、活性物質(zhì)層的厚度比為12:1.5:1.5:80。所述硅材料為CoSi2;所述活性物質(zhì)層由天然石墨、導電劑SP、LA132粘結劑組成,天然石墨、導電劑SP、LA132粘結劑的質(zhì)量比為95:1:4。本實施例的鋰離子電池復合負極極片的制備方法,包括以下步驟:1)負極漿料的制備負極漿料的制備:稱取LA132粘結劑40g添加到1500g的二次蒸餾水中,攪拌均勻,然后添加10g導電劑SP分散均勻,再分三批加入950g人造石墨分散均勻,得到負極漿料;2)通過磁控濺射法將硅材料沉積在集流體的兩面上,形成硅材料層,得到極片A;3)通過氣相沉積法將石墨烯沉積在步驟2)所得的極片A的兩面,形成石墨烯層,得到極片B;4)通過噴涂技術將負極漿料涂覆在步驟3)所得的極片B的兩面,干燥,形成活性物質(zhì)層,得到極片C,即得。實施例5本實施例的鋰離子電池復合負極極片,包括集流體和在集流體一面沿遠離集流體方向上依次設置的硅材料層、石墨烯層、活性物質(zhì)層和氧化鋁材料層,即在集流體的一面設置硅材料層,在硅材料層表面設置石墨烯層,在石墨烯層表面設置活性物質(zhì)層,在活性物質(zhì)層表面設置氧化鋁材料層。集流體為銅網(wǎng),厚度為8μm,孔隙率為50%;集流體、硅材料層、石墨烯層、活性物質(zhì)層和氧化鋁材料層的厚度比為8:1.8:1.2:150:4。所述硅材料為SiC;所述活性物質(zhì)層由天然石墨、導電劑SP、LA132粘結劑組成,天然石墨、導電劑SP、LA132粘結劑的質(zhì)量比為95:1:4;所述氧化鋁材料層由氧化鋁、偏鋁酸鋰、PVDF粘結劑組成,氧化鋁、偏鋁酸鋰、PVDF粘結劑的質(zhì)量比為15:2:10。本實施例的鋰離子電池復合負極極片的制備方法,包括以下步驟:1)負極漿料和氧化鋁復合漿料的制備負極漿料的制備:稱取LA132粘結劑40g添加到1500g的二次蒸餾水中,攪拌均勻,然后添加10g導電劑SP分散均勻,再分三批加入950g人造石墨分散均勻,得到負極漿料;氧化鋁復合漿料的制備:取氧化鋁15g,偏鋁酸鋰2g,PVDF粘結劑10g加入100mLNMP溶劑中,采用高速分散機攪拌得到粘度為1000mPa·s的氧化鋁復合漿料;2)通過磁控濺射法將硅材料沉積在集流體上,形成硅材料層,得到極片A;3)通過氣相沉積法將石墨烯沉積在步驟2)所得的極片A的一面,形成石墨烯層,得到極片B;4)通過噴涂技術將負極漿料涂覆在步驟3)所得的極片B的石墨烯層表面,干燥,形成活性物質(zhì)層,得到極片C;5)通過噴涂技術將步驟1)所得的氧化鋁復合漿料涂覆在步驟4)所得的極片C的活性物質(zhì)層表面,干燥形成氧化復合材料層,即得。實施例6本實施例的鋰離子電池,分別采用實施例1~5的鋰離子電池復合負極極片為負極片,磷酸鐵鋰為正極,隔膜采用復PP隔膜,LiPF6/EC+DEC(體積比1:1)為電解液,并采用疊片方式制備出鋰離子電芯,并經(jīng)過干燥、封裝、注液、化成定容等工序制備出鋰離子電池E1、E2、E3、E4和E5。對比例本對比例的鋰離子電池的制備方法包括如下步驟:1)將石墨漿料通過涂布機涂覆在10μm銅網(wǎng)上,涂覆厚度為200μm,制備出負極極片;2)以步驟1)所得的負極極片為負極,磷酸鐵鋰為正極,隔膜采用復PP隔膜,LiPF6/EC+DEC(體積比1:1)為電解液,并采用疊片方式制備出鋰離子電芯,并經(jīng)過干燥、封裝、注液、化成定容等工序制備出鋰離子電池F1。實驗例1循環(huán)性能測試:分別以1.0C/1.0C的倍率,溫度為25±3℃,進行鋰離子電池循環(huán)測試,同時根據(jù)鋰離子電池放電容量,質(zhì)量計算出E1、E2、E3、E4、E5和F1鋰離子電池的質(zhì)量能量密度,結果見表1。表1實施例與對比例電池的循環(huán)性能和能量密度比較由表1可以看出,實施例1~5與對比例制備出的鋰離子電池相比,循環(huán)性能得到明顯提高,其原因為采用磁控濺射法或氣相沉積法將硅材料噴涂在集流體表面,其硅材料與集流體之間的結合更緊密,內(nèi)阻更小,同時可以降低硅材料在使用過程中的膨脹,提高其循環(huán)性能。同時也可以看出,實施例制備的鋰離子電池復合負極極片中有高容量硅材料,可以降低石墨的使用量,即在集流體表面的活性物質(zhì)涂覆厚度更薄。實施例中,活性物質(zhì)涂覆厚度為(80~150)μm,而相同容量的石墨負極材料涂覆厚度為200μm,因此鋰離子電池的能量密度得到提高。實驗例2直流內(nèi)阻及其安全性能測試:直流內(nèi)阻測試方法參考《FreedomCAR電池測試手冊》,安全性能測試為針刺短路實驗,測試方法見UL2054安全標準測試標準。結果見下表2。表2采用實施例和對比例制備出電池性能比較項目電池編號直流內(nèi)阻(mΩ)安全性系數(shù)實施例1E14.189/10實施例2E24.228/10實施例3E34.248/10實施例4E44.588/10實施例5E54.658/10對比例1F16.985/10從表2可以看出,相對于對比例,采用實施例1~5的復合負極極片的鋰離子電池具有較低的直流內(nèi)阻、高的安全性系數(shù)。原因在于:本發(fā)明制備出的鋰離子電池復合負極極片上設置氧化鋁復合材料層,在電池溫度異常時,可以提高負極材料表面的耐高溫性能,并降低其與隔膜接觸部分的熱收縮,并提高其安全性能。同時氧化鋁復合材料層中具有提高鋰離子傳遞速率的偏鋁酸鋰物質(zhì),可以提高大倍率條件下鋰離子的傳遞速率,從而降低其內(nèi)阻。當前第1頁1 2 3