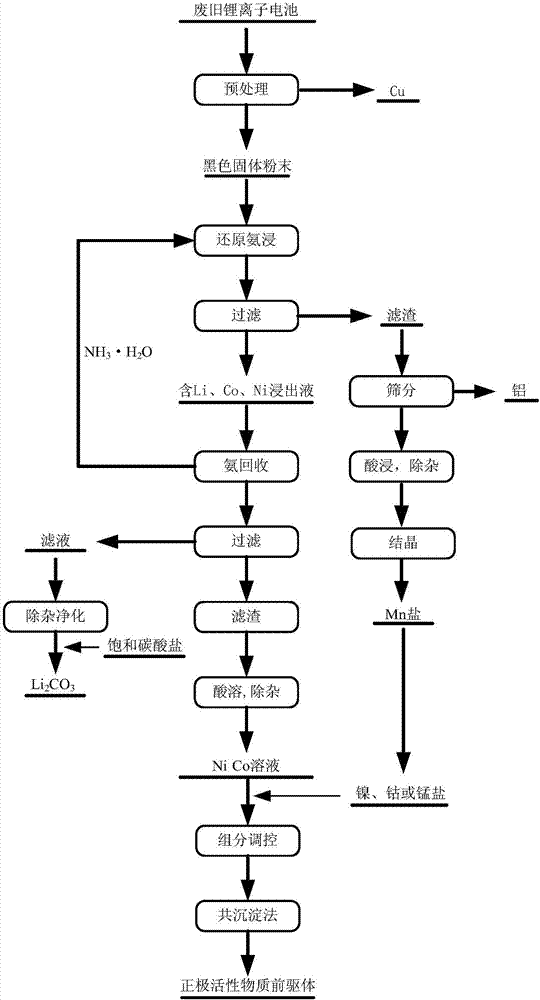
本發(fā)明屬于二次資源回收利用和循環(huán)經(jīng)濟(jì)
技術(shù)領(lǐng)域:
,涉及一種正極材料中金屬組分的選擇性浸出劑及回收方法,尤其涉及一種廢舊鋰離子電池正極材料中金屬組分的選擇性浸出劑及回收方法。
背景技術(shù):
:隨著鋰離子電池在手機(jī)、筆記本及數(shù)碼相機(jī)等便攜式電子產(chǎn)品等領(lǐng)域中的廣泛應(yīng)用,鋰離子電池的需求量不斷增加,其產(chǎn)量也在逐年增加,以中國(guó)為例,2010年的鋰電池產(chǎn)量有26.86億只,而2015年1~10月,全國(guó)共生產(chǎn)鋰離子電池43.75億只。根據(jù)工業(yè)需求和增長(zhǎng)量進(jìn)行估算,鋰離子電池的市場(chǎng)價(jià)值將由2015年的314億快速增長(zhǎng)至2020年的537億美元。根據(jù)國(guó)際技術(shù)聯(lián)合會(huì)itu(internationaltelecommunicationsunion)的信息,用于移動(dòng)電源設(shè)備的鋰離子電池(libs)和電動(dòng)汽車的鋰離子電池(libs)的壽命分別為2~3年和5~8年,因此,未來(lái)將會(huì)產(chǎn)生大量的廢舊鋰離子電池。鋰離子電池主要由正極材料(licoo2,ncm(linixcoymnzo2),nca(linixcoyalzo2),x+y+z=1,limn2o4,lifepo4等)、負(fù)極材料(石墨)、隔板(pp,pe)、電解液(lipf6,libf4,liclo4)以及外殼等組成。報(bào)廢后,若棄之于環(huán)境,廢舊鋰離子電池內(nèi)部的有機(jī)電解液(lipf6,libf4,liclo4)會(huì)污染大氣、水和土壤等;廢舊鋰離子電池內(nèi)部的重金屬會(huì)污染水和土壤等,并通過(guò)生物鏈危害人體。此外,廢舊鋰離子電池中含有大量有價(jià)金屬,以三元鋰離子電池正極報(bào)廢料為例,其中的金屬鋰、鈷、錳、鎳和鋁的含量分別為6.15%、18.65%、17.57%和7.86%。鈷和鎳是稀有的貴金屬,在自然界原礦的金屬含量很低,而金屬鋰則是一種戰(zhàn) 略金屬。因此,回收廢舊鋰離子電池不僅能夠避免其對(duì)環(huán)境和人類健康的風(fēng)險(xiǎn),還能夠獲得較好的經(jīng)濟(jì)效益。目前,國(guó)內(nèi)外對(duì)廢舊鋰離子電池的處理和有價(jià)金屬的回收開(kāi)展了許多的研究工作,提出了很多處理方法,主要包括濕法冶金、火法冶金和生物冶金技術(shù)。其中,由于濕法冶金技術(shù)具有金屬回收率高、回收產(chǎn)物純度高、產(chǎn)品附加值高等優(yōu)點(diǎn),使其成為廢舊鋰離子電池回收的研究熱點(diǎn)。cn103326088a將廢舊鋰離子電池經(jīng)過(guò)一系列的機(jī)械、熱處理和分選后得到含鎳鈷的正極材料,利用正極材料本身特點(diǎn)采用常壓h2so4加亞硫酸鈉浸出;浸出液加入鹽酸鹽調(diào)節(jié)ph值,加入氟化鹽進(jìn)行初步除去ca和mg;采用p204萃取除雜,除去fe、cu、zn、ca及mg等雜質(zhì),并用p507選擇性萃取進(jìn)行鎳鈷分離,制備得到fe、cu、zn、ca和mg均≤2.0mg/l高純硫酸鎳和高純硫酸鈷溶液。cn104157926a將濕法選擇性破碎得到的廢舊電池廢料經(jīng)過(guò)兩段堿浸除鋁,得到的濾渣在2mol/lh2so4與0.15mol/lna2s2o3的混合溶液中浸出,浸出液中加入10%nh4hco3調(diào)節(jié)ph除去浸出液中的鋁和銅,然后用naclo氧化沉淀鐵和錳;用25%的p507萃取分離鈷、鎳和鋰后反萃制得原料液,在naoh調(diào)節(jié)ph后,采用(nh4)2c2o4沉淀固相法直接合成licoo2粉體,利用回收的鈷資源制備的鈷酸鋰的首次充、放電比容量分別為143.8mah/g和140.0mah/g。cn104577247a將拆解后得到的電極片熱解、球磨后加入氫氧化鈉溶液選擇性溶鋁,濾渣加入1~3mol/l的鹽酸溶液反應(yīng)得到氫氧化鋁,上清液加入硫酸或者雙氧水中的一種進(jìn)行浸出反應(yīng),浸出液中加入氫氧化鈉或氯酸鈉中一種除鐵,并再次加入氫氧化鈉進(jìn)行二次除鋁和鐵,得到含鈷溶液;將得到的含鈷溶液萃取除雜,得到的萃取液通過(guò)p507萃取分離,將得到的含鈷溶液經(jīng)過(guò)反萃取得到純鈷溶液;將得到的純鈷溶液通過(guò)純水進(jìn)行結(jié)晶洗滌得到氯化鈷。這些方法雖然 能得到純度較高的產(chǎn)品,但回收過(guò)程需要繁雜的除雜工藝,增加了生產(chǎn)過(guò)程的成本,浸出劑不能腐蝕性強(qiáng),不能循環(huán)利用。目前國(guó)內(nèi)外公開(kāi)了許多廢舊鋰離子電池處理的專利或研究成果,基本采用了酸性介質(zhì)在有添加劑存在的情況下同時(shí)浸出廢舊鋰離子電池中的多種有價(jià)金屬元素,得到一種同時(shí)含有多種金屬離子的溶液,然后再除雜、分離提取,工藝流程較長(zhǎng)。實(shí)際物料中金屬組分復(fù)雜,酸浸的選擇性差,必然導(dǎo)致很多雜質(zhì)金屬離子進(jìn)入溶液,因此除雜工藝復(fù)雜,金屬損耗大。另一方面,酸的腐蝕性大,介質(zhì)不能循環(huán)使用,使回收的成本增加。廢舊鋰離子電池中金屬鋰、鈷和鎳為緊缺戰(zhàn)略金屬,具有很高的資源價(jià)值。如果浸出過(guò)程中選擇合適的工藝,選擇性浸出金屬鋰、鈷和鎳等價(jià)值較高的金屬,而價(jià)值較低的金屬如鋁和鐵等則以其他方式回收,可極大的簡(jiǎn)化生產(chǎn)過(guò)程,降低成本和投資??傊?,目前為止還沒(méi)有一種能夠?qū)崿F(xiàn)廢舊鋰離子電池正極材料中有價(jià)金屬的選擇性浸出及浸出劑循環(huán)使用的回收技術(shù)。技術(shù)實(shí)現(xiàn)要素:針對(duì)現(xiàn)有技術(shù)存在的不足,為解決廢舊鋰離子電池回收工藝長(zhǎng)、除雜工藝復(fù)雜及浸出劑不可循環(huán)使用等問(wèn)題,本發(fā)明的目的在于提供一種正極材料中金屬組分的選擇性浸出劑及回收方法,所述浸出劑能夠選擇性浸出價(jià)值較高的li、ni和co溶液,且浸出效率較高,消除了后續(xù)回收工序中雜質(zhì)對(duì)li、co和ni元素提取的影響,便于正極材料中有價(jià)金屬的回收處理。為達(dá)此目的,本發(fā)明采用以下技術(shù)方案:本發(fā)明的目的之一在于提供一種正極材料中金屬組分的選擇性浸出劑,所述浸出劑為含有還原劑、銨鹽和氨水中的任意兩種或三種的溶液,所述還原劑 為堿性條件下具有還原性的物質(zhì),所述浸出劑中氨水的濃度為0~10mol/l,銨根離子的濃度為0~8mol/l,還原劑的濃度為0~2mol/l。所述選擇性浸出劑中氨水、銨根離子和還原劑中至多一種物質(zhì)的濃度為0。所述浸出劑中氨水的濃度為0~10mol/l,如0.1mol/l、0.2mol/l、0.5mol/l、0.8mol/l、1mol/l、1.2mol/l、1.5mol/l、2mol/l、3mol/l、4mol/l、5mol/l、6mol/l、7mol/l、8mol/l、9mol/l或9.5mol/l等,優(yōu)選為0~4mol/l;銨根離子的濃度為0~6mol/l,如0.2mol/l、0.5mol/l、0.8mol/l、1mol/l、1.5mol/l、2mol/l、2.5mol/l、3mol/l、3.5mol/l、4mol/l、4.5mol/l、5mol/l或5.5mol/l等,優(yōu)選為2~4mol/l;還原劑的濃度為0~2mol/l,如0.2mol/l、0.5mol/l、0.8mol/l、1.0mol/l、1.2mol/l、1.5mol/l或1.8mol/l等,優(yōu)選為0.1~1mol/l。所述還原劑為亞硫酸鹽、亞硫酸氫鹽、硫代硫酸鹽、硫酸亞鐵、鐵粉、二氧化硫、葡萄糖、硼氫化鈉、硼氫化鉀或水合肼中的任意一種或至少兩種的組合,典型但非限制性的組合如:亞硫酸鹽與亞硫酸氫鹽,硫代硫酸鹽、硫酸亞鐵與鐵粉,二氧化硫與葡萄糖,硼氫化鈉、硼氫化鉀與水合肼,硫代硫酸鹽、硫酸亞鐵、鐵粉與二氧化硫。優(yōu)選地,所述的亞硫酸鹽、亞硫酸氫鹽或硫代硫酸鹽中的陽(yáng)離子獨(dú)立地為鈉離子、鉀離子或銨根離子中任意一種或至少兩種的組合,典型但非限制性的組合如鈉離子與鉀離子,鈉離子與銨根離子,鈉離子、鉀離子與銨根離子。優(yōu)選地,所述銨鹽為硫酸銨、硫酸氫銨、碳酸銨、碳酸氫銨、氯化銨、硝酸銨或乙酸銨中的任意一種或至少兩種的組合。典型但非限制性的組合如:硫酸銨與硫酸氫銨,碳酸銨、碳酸氫銨與氯化銨,硝酸銨與乙酸銨,硫酸氫銨、碳酸銨、碳酸氫銨與氯化銨,碳酸氫銨、氯化銨、硝酸銨與乙酸銨。優(yōu)選地,所述銨鹽為硫酸銨和硫酸氫銨的組合,或碳酸銨和碳酸氫銨的組 合。本發(fā)明提供的浸出劑來(lái)源范圍廣,原料價(jià)格便宜,能夠高效地(浸出效率達(dá)90%以上)選擇性浸出正極材料中價(jià)值較高的li、ni和co,用于回收正極材料中的li、co和ni,能夠分別回收鋰、鎳和鈷與浸出劑,避免后續(xù)回收工序中雜質(zhì)對(duì)li、co和ni元素提取的影響;且回收成本低,對(duì)設(shè)備的腐蝕性小,能夠避免現(xiàn)有技術(shù)采用無(wú)機(jī)酸對(duì)環(huán)境可能造成的二次污染。本發(fā)明的目的之二在于提供一種回收正極材料中金屬組分的方法,所述方法包括如下步驟:(1)將正極材料在浸出劑中浸出,固液分離后,得到含鋰、鎳和鈷的浸出液與含錳和鋁的濾渣,所述的浸出劑為含有還原劑、銨鹽和氨水中的任意兩種或三種的溶液,所述還原劑為堿性條件下具有還原性的物質(zhì);(2)含鋰、鎳和鈷的浸出液經(jīng)汽提精餾實(shí)現(xiàn)氨的回收和重金屬氨絡(luò)合物的解絡(luò)合,脫氨后的浸出液經(jīng)固液分離得到含鋰溶液和含鎳和鈷的濾渣。所述方法在步驟(2)之后還進(jìn)行如下步驟:(3)將含鎳和鈷的濾渣溶解,除雜,得到含鎳和鈷的溶液,調(diào)節(jié)含鎳和鈷的溶液中鎳、鈷和錳的摩爾比,使其符合分子式linixcoymn1-x-yo2中ni、co和mn的摩爾比,其中x>0,y>0,且x+y<1,得到前驅(qū)體溶液,之后,利用前驅(qū)體溶液制備活性物質(zhì)前驅(qū)體;(4)利用步驟(2)中得到的含鋰溶液制備,并將鋰鹽和步驟(3)中制備的活性物質(zhì)前驅(qū)體制備得到正極活性物質(zhì)。本發(fā)明提供的方法所采用的浸出劑為含有還原劑的氨-銨溶液,浸出劑來(lái)源范圍廣,原料價(jià)格便宜,對(duì)設(shè)備的腐蝕性小,選擇性好,有利于有價(jià)金屬li、co和ni的富集,消除了后續(xù)回收工序中雜質(zhì)對(duì)li、co和ni元素提取的影響, 便于廢舊鋰離子電池有價(jià)金屬的回收處理;且可以通過(guò)目前工業(yè)上成熟的氨回收技術(shù)回收氨水,可實(shí)現(xiàn)浸出劑的循環(huán)使用;不僅節(jié)約了成本,同時(shí)避免了現(xiàn)有技術(shù)采用無(wú)機(jī)酸對(duì)環(huán)境可能造成的二次污染。步驟(1)所述的正極材料為鋰離子電池正極材料,優(yōu)選為廢舊鋰離子電池中的正極材料。優(yōu)選地,步驟(1)所述正極材料為磷酸鐵鋰、鈷酸鋰、鎳鈷錳三元材料、鎳鈷鋁三元材料、錳酸鋰或鎳酸鋰中的任意一種或至少兩種的組合。所述鎳鈷錳三元材料是指含有鎳、鈷和錳三種元素的材料,所述鎳鈷鋁三元材料為含有鎳、鈷和鋁三種元素的材料。典型但非限制性的正極材料組合如,磷酸鐵鋰與鈷酸鋰,鎳鈷錳三元材料與鎳鈷鋁三元材料,錳酸鋰與鎳酸鋰,磷酸鐵鋰、鈷酸鋰與鎳鈷錳三元材料,鎳鈷鋁三元材料、錳酸鋰與鎳酸鋰,磷酸鐵鋰、鈷酸鋰、鎳鈷錳三元材料與鎳鈷鋁三元材料,錳酸鋰、磷酸鐵鋰、鈷酸鋰與鎳鈷錳三元材料。優(yōu)選地,步驟(1)所述正極材料由鋰離子電池經(jīng)預(yù)處理得到,所述預(yù)處理為機(jī)械分離法、物理溶解法或熱處理法中的任意一種或至少兩種的組合。典型但非限制性的組合如機(jī)械分離法與物理溶解法,機(jī)械分離法與熱處理法,機(jī)械分離法、物理溶解法和熱處理法。步驟(1)所述浸出劑中氨水的濃度為0~10mol/l,如0.1mol/l、0.2mol/l、0.5mol/l、0.8mol/l、1mol/l、1.2mol/l、1.5mol/l、2mol/l、3mol/l、4mol/l、5mol/l、6mol/l、7mol/l、8mol/l、9mol/l或9.5mol/l等,優(yōu)選為0~4mol/l,銨根離子的濃度為0~6mol/l,如0.2mol/l、0.5mol/l、0.8mol/l、1mol/l、1.5mol/l、2mol/l、2.5mol/l、3mol/l、3.5mol/l、4mol/l、4.5mol/l、5mol/l或5.5mol/l等,優(yōu)選為2~4mol/l,還原劑的濃度為0~2mol/l,如0.2mol/l、 0.5mol/l、0.8mol/l、1.0mol/l、1.2mol/l、1.5mol/l或1.8mol/l等,優(yōu)選為0.1~1mol/l。所述浸出劑中氨水、銨根離子和還原劑中至多一種物質(zhì)的濃度為0。優(yōu)選地,步驟(1)所述還原劑為亞硫酸鹽、亞硫酸氫鹽、硫代硫酸鹽、硫酸亞鐵、鐵粉、二氧化硫、葡萄糖、硼氫化鈉、硼氫化鉀或水合肼中的任意一種或至少兩種的組合,典型但非限制性的組合如:亞硫酸鹽與亞硫酸氫鹽,硫代硫酸鹽、硫酸亞鐵與鐵粉,二氧化硫與葡萄糖,硼氫化鈉、硼氫化鉀與水合肼,硫代硫酸鹽、硫酸亞鐵、鐵粉與二氧化硫。優(yōu)選地,步驟(1)所述的亞硫酸鹽、亞硫酸氫鹽或硫代硫酸鹽中的陽(yáng)離子獨(dú)立地為鈉離子、鉀離子或銨根離子中任意一種或至少兩種的組合,典型但非限制性的組合如鈉離子與鉀離子,鈉離子與銨根離子,鈉離子、鉀離子與銨根離子。優(yōu)選地,步驟(1)所述銨鹽為硫酸銨、硫酸氫銨、碳酸銨、碳酸氫銨、氯化銨、硝酸銨或乙酸銨中的任意一種或至少兩種的組合。典型但非限制性的組合如:硫酸銨與硫酸氫銨,碳酸銨、碳酸氫銨與氯化銨,硝酸銨與乙酸銨,硫酸氫銨、碳酸銨、碳酸氫銨與氯化銨,碳酸氫銨、氯化銨、硝酸銨與乙酸銨。優(yōu)選地,步驟(1)所述銨鹽為硫酸銨和硫酸氫銨的組合,或碳酸銨和碳酸氫銨的組合。步驟(1)所述正極材料與選擇性浸出劑的固液比為5~200g·l-1,如10g·l-1、20g·l-1、30g·l-1、40g·l-1、50g·l-1、60g·l-1、80g·l-1、85g·l-1、95g·l-1、100g·l-1、110g·l-1、120g·l-1、130g·l-1、150g·l-1、180g·l-1或190g·l-1等,優(yōu)選為10~50g·l-1。優(yōu)選地,步驟(1)所述浸出在15~100℃條件下進(jìn)行,如20℃、30℃、40℃、50℃、60℃、70℃、80℃、90℃或95℃等,優(yōu)選為50~90℃。優(yōu)選地,步驟(1)所述浸出在攪拌條件下進(jìn)行,攪拌的速率為100~2000rpm,如200rpm、300rpm、500rpm、800rpm、1000rpm、1200rpm、1500rpm或1800rpm等。優(yōu)選地,步驟(1)所述浸出的時(shí)間為30~480min,如40min、50min、80min、100min、130min、150min、180min、200min、230min、250min、280min、310min、320min、350min、380min、400min、420min或450min等,優(yōu)選為120~300min。本發(fā)明提供的正極材料的選擇性浸出方法能夠選擇性的提取金屬價(jià)值較高的金屬鋰、鎳和鈷,通過(guò)調(diào)節(jié)還原劑含量、氨濃度、銨鹽濃度及浸出的時(shí)間和溫度,控制浸出液中雜質(zhì)金屬離子的含量,避免了現(xiàn)有技術(shù)中對(duì)浸出液中各種金屬進(jìn)行分離提出的復(fù)雜流程,實(shí)現(xiàn)了有價(jià)金屬的選擇性分離。優(yōu)選地,步驟(1)所述含錳和鋁的濾渣經(jīng)如下方法回收錳和鋁:將含錳和鋁的濾渣篩分,得到金屬鋁和含錳沉淀物,含錳沉淀物經(jīng)酸溶解,除雜,結(jié)晶,得到錳鹽。所述酸溶解、除雜和結(jié)晶均為本領(lǐng)域常規(guī)的操作,本領(lǐng)域技術(shù)人員可輕易從含錳沉淀物制得錳鹽。步驟(2)所述汽提精餾在蒸氨塔中進(jìn)行。所述汽提精餾為本領(lǐng)域中常規(guī)的操作,本領(lǐng)域技術(shù)人員可輕易進(jìn)行。優(yōu)選地,步驟(2)所述含鋰溶液中ni、co、mn、fe和al的含量均≤0.5ppm,如含量為0.4ppm、0.3ppm、0.2ppm、0.1ppm或0.05ppm等。汽提精餾能夠?qū)崿F(xiàn)氨的回收和重金屬氨絡(luò)合物的解絡(luò)合,溶液經(jīng)過(guò)蒸氨后,得到金屬ni、co以及雜質(zhì)mn、fe和al在溶液中殘余均≤0.5ppm的高純含鋰溶液。步驟(3)所述調(diào)節(jié)含鎳和鈷的溶液中鎳、鈷和錳的摩爾比具體為:向含鎳和鈷的溶液中添加水溶性鎳鹽、鈷鹽或者錳鹽中一種或至少兩種的組合。添加 的鎳鹽、鈷鹽或錳鹽的量根據(jù)含鎳和鈷的溶液中鎳和鈷的含量以及目標(biāo)活性物質(zhì)前驅(qū)體的組成確定。優(yōu)選地,所述錳鹽來(lái)源于步驟(1)所述含錳和鋁的濾渣中的錳。優(yōu)選地,步驟(3)利用共沉淀法將前驅(qū)體溶液制備成活性物質(zhì)前驅(qū)體。采用共沉淀法制備活性物質(zhì)前驅(qū)體為本領(lǐng)域常規(guī)的操作。優(yōu)選地,步驟(4)所述利用鋰溶液制備鋰鹽具體為:向含鋰溶液中加入水溶性飽和碳酸鹽和/或通入co2后,固液分離,得到純度達(dá)99%以上的碳酸鋰。優(yōu)選地,所述的水溶性飽和碳酸鹽中的陽(yáng)離子獨(dú)立地為鈉離子、鉀離子或銨根離子中的任意一種或至少兩種的組合。典型但非限制性的組合如鈉離子與鉀離子,鈉離子與銨根離子,鉀離子與銨根離子,鈉離子、鉀離子與銨根離子。優(yōu)選地,步驟(4)所述鋰鹽和活性物質(zhì)前驅(qū)體通過(guò)高溫固相反應(yīng)法制備正極活性物質(zhì),所述的高溫固相反應(yīng)溫度為800~900℃,如810℃、820℃、830℃、850℃、860℃、870℃、880℃或890℃等。所述高溫固相反應(yīng)為本領(lǐng)域常規(guī)的操作。作為優(yōu)選的技術(shù)方案,所述正極材料中金屬組分的回收方法包括如下步驟:(1)將正極材料在選擇性浸出劑中浸出,固液分離后,得到含鋰、鎳和鈷的浸出液與含錳和鋁的濾渣,并回收濾渣中的錳和鋁,其中,所述浸出劑為含有還原劑、銨鹽和氨水中的任意兩種或三種的溶液,所述還原劑為堿性條件下具有還原性的物質(zhì),所述浸出劑中氨水的濃度為0~10mol/l,銨根離子的濃度為0~8mol/l,還原劑的濃度為0~2mol/l,所述正極材料與選擇性浸出劑的固液比為5~200g·l-1,所述浸出在15~100℃、攪拌速率為100~2000rpm的條件下進(jìn)行,所述浸出的時(shí)間為30~480min;(2)含鋰、鎳和鈷的浸出液經(jīng)汽提精餾實(shí)現(xiàn)氨的回收和重金屬氨絡(luò)合物的 解絡(luò)合,脫氨后的浸出液經(jīng)固液分離得到含鋰溶液和含鎳和鈷的濾渣,向含鋰溶液中加入水溶性飽和碳酸鹽和/或通入co2后,固液分離,得到純度達(dá)99%以上的碳酸鋰;(3)將含鎳和鈷的濾渣溶解,除雜,得到含鎳和鈷的溶液,調(diào)節(jié)含鎳和鈷的溶液中鎳、鈷和錳的摩爾比,使其符合分子式linixcoymn1-x-yo2中ni、co和mn的摩爾比,其中x>0,y>0,且x+y<1,得到前驅(qū)體溶液,之后,利用前驅(qū)體溶液通過(guò)共沉淀法制備活性物質(zhì)前驅(qū)體,其中,調(diào)節(jié)含鎳和鈷的溶液中鎳、鈷和錳的摩爾比使用的錳源部分或全部來(lái)源于步驟(1)回收的錳;(4)利用步驟(2)中回收得到的鋰鹽和步驟(3)中制備的活性物質(zhì)前驅(qū)體通過(guò)高溫固相反應(yīng)制備得到正極活性物質(zhì)。與現(xiàn)有技術(shù)相比,本發(fā)明的有益效果為:(1)本發(fā)明提供的選擇性浸出劑實(shí)現(xiàn)了正極材料中金屬組分li、ni和co的選擇性浸出,且浸出效率較高,可達(dá)90%以上;(2)本發(fā)明提供的正極材料中金屬組分的選擇性浸出回收方法,避免了現(xiàn)有技術(shù)中浸出液中各種金屬組分分離提純的復(fù)雜流程,簡(jiǎn)化了工藝流程,且氨水可循環(huán)使用,降低了生產(chǎn)成本,適合大規(guī)模工業(yè)化使用;(3)本發(fā)明提供的正極材料中金屬組分的選擇性浸出回收方法制備的碳酸鋰純度達(dá)99%,全面高效利用了正極材料中的金屬元素,減少了廢舊鋰離子電池對(duì)環(huán)境的污染。附圖說(shuō)明圖1為本發(fā)明一種實(shí)施方式提供的廢舊鋰離子電池中金屬組分的選擇性浸出及回收的工藝流程圖。具體實(shí)施方式下面結(jié)合附圖并通過(guò)具體實(shí)施方式來(lái)進(jìn)一步說(shuō)明本發(fā)明的技術(shù)方案。領(lǐng)域的技術(shù)人員應(yīng)該明了,所述的實(shí)施例僅僅是幫助理解本發(fā)明,不應(yīng)視為對(duì)本發(fā)明的具體限制。一種廢舊鋰離子電池中金屬組分的選擇性浸出及回收工藝,如圖1所示,所述工藝包括如下步驟:(1)廢舊鋰離子電池經(jīng)預(yù)處理后得到含正極材料的粉料;將粉料加入到含還原劑的氨/銨溶液進(jìn)行選擇性浸出反應(yīng),固液分離后,得到含鋰、鎳和鈷的浸出液與含錳和鋁的濾渣,回收含錳和鋁的濾渣中的錳和鋁;(2)利用汽提精餾回收含鋰、鎳和鈷的浸出液中的氨并循環(huán)使用,脫氨后的含鋰、鎳和鈷的浸出液經(jīng)固液分離后,得到含鋰溶液和含鎳和鈷的濾渣,回收含鋰溶液中的鋰;(3)含鎳和鈷的濾渣溶解除雜后,得到含鎳和鈷的溶液,調(diào)節(jié)溶液中ni、co和mn的摩爾比,使其符合分子式linixcoymn1-x-yo2(其中0<x,0<y,且0<x+y<1)中ni、co和mn的摩爾比,得到前驅(qū)體溶液,利用前驅(qū)體溶液采用共沉淀法制備正極活性物質(zhì)前驅(qū)體;(4)利用步驟(2)中回收得到的鋰鹽和步驟(3)中制備的正極活性物質(zhì)前驅(qū)體制備鋰離子電池正極活性物質(zhì)。實(shí)施例1一種正極材料的選擇性浸出劑,所述浸出劑為含有氨水、硫酸銨和亞硫酸鈉的溶液,其中c(nh3)=4mol/l,c(nh4+)=4mol/l,亞硫酸鈉的濃度為1mol/l。一種廢舊鋰離子電池中金屬組分的選擇性浸出及回收方法,包括如下步驟:(1)將廢舊鋰離子電池直接破碎后篩分,除去銅之后,得到粉料,其金屬組成如表1所示:表1電極粉料的金屬組成金屬alfelinicomn含量(%)3.339.103.1012.5312.676.70取5g電極粉加入到盛有100ml含有氨水、硫酸銨和亞硫酸鈉混合溶液的三口燒瓶中,所述的三口燒瓶中亞硫酸鈉的濃度為1mol/l,將所述的三口燒瓶置于恒溫油浴鍋中,控制反應(yīng)溫度為90℃,攪拌速率為900rpm,反應(yīng)時(shí)間為300min。當(dāng)達(dá)到預(yù)設(shè)反應(yīng)時(shí)間后,用針管取2ml樣品,分析樣品的金屬成分,計(jì)算出金屬的浸出率。待反應(yīng)結(jié)束后,將浸出混合溶液過(guò)濾,洗滌濾渣三次,得到含li、ni和co的浸出液和含錳濾渣,含錳濾渣首先篩分,得到金屬鋁和篩下物,篩下物溶解后,除去溶液中的雜質(zhì)鐵和少量的鋁,然后結(jié)晶制備錳鹽。在本實(shí)施例條件下,當(dāng)反應(yīng)時(shí)間為300min時(shí),得到金屬li、ni和co的浸出率分別為99.35%、95.78%和91.32%,而金屬al、mn和fe的浸出率僅為1.79%、0.49%和0.38%,即含還原劑的氨水-銨鹽溶液浸出鋰離子電池電極粉時(shí),實(shí)現(xiàn)了有價(jià)金屬li、ni和co的選擇性浸出。以硫酸氫銨、碳酸銨、碳酸氫銨、氯化銨、硝酸銨或乙酸銨中的任意一種或至少兩種的組合,或硫酸銨與硫酸氫銨的組合,或碳酸銨與碳酸氫銨的組合代替硫酸銨,以亞硫酸氫鹽、硫代硫酸鹽、硫酸亞鐵、鐵粉、二氧化硫、葡萄糖、硼氫化鈉、硼氫化鉀或水合肼中的任意一種或至少兩種的組合代替硫代硫酸鈉,按上述步驟浸出相同的電極粉,li、ni和co的浸出率均可高于99%、90%和90%,而金屬al、mn與fe的浸出率分別為0.5~2.6%、0.4~1.9%與0.2~1.5%, 可以實(shí)現(xiàn)有價(jià)金屬li、ni和co的選擇性浸出。(2)向步驟(1)得到的含li、ni和co的浸出液中加入堿性物質(zhì),將其ph調(diào)節(jié)至12.5以上,然后將溶液引入汽提塔蒸氨系統(tǒng)回收氨,浸出液中的重金屬鎳和鈷與溶液中氫氧根結(jié)合生產(chǎn)沉淀,金屬鋰留在溶液中,蒸氨后固液分離,得到ni、co、al、mn和fe的含量均≤0.5ppm的高純含鋰溶液和含鎳和鈷的濾渣,向含鋰溶液中加入飽和碳酸鹽溶液,回收溶液中的金屬鋰,制備的碳酸鋰的純度達(dá)到99%;(3)將含鎳和鈷的濾渣經(jīng)酸溶除雜后,得到含鎳和鈷的溶液,根據(jù)溶液中的元素組成及含量,向其中加入鎳鹽、鈷鹽或者錳鹽中一種或至少兩種,以調(diào)節(jié)溶液中的ni、co或mn中的一種或者至少兩中元素的含量,使ni、co和mn的摩爾比符合分子式linixcoymn1-x-yo2中ni、co和mn的摩爾比,得到前驅(qū)體溶液,所述錳鹽部分或全部來(lái)源于步驟(1)所述含錳濾渣制得的錳鹽;利用前驅(qū)體溶液通過(guò)工業(yè)上較成熟的共沉淀法制備得到正極活性物質(zhì)前驅(qū)體;(4)將步驟(2)回收的鋰鹽和步驟(3)制備的正極活性物質(zhì)前驅(qū)體通過(guò)工業(yè)上成熟的固相反應(yīng)制備分子式為linixcoymn1-x-yo2的鋰離子電池正極活性物質(zhì)。實(shí)施例2一種正極材料的選擇性浸出劑,所述浸出劑為含有氨水、硫酸銨和亞硫酸氫鈉的溶液,其中c(nh3)=4mol/l,c(nh4+)=2mol/l,亞硫酸鈉的濃度為0.1mol/l。一種廢舊鋰離子電池中金屬組分的選擇性浸出及回收方法,包括如下步驟:(1)將廢舊鋰離子電池機(jī)械破碎、400~800℃熱處理30~300min,篩分去除金屬cu之后,得到黑色電極粉料,其金屬組成如表2所示;表2電極粉料的金屬組成金屬alfelinicomn含量(%)4.258.153.2611.5312.6710.70取1g電極粉加入到盛有100ml含有氨水、硫酸銨和亞硫酸氫鈉混合溶液的三口燒瓶中,所述的三口燒瓶中亞硫酸氫鈉的濃度為0.1mol/l,將所述的三口燒瓶置于恒溫油浴鍋中,控制反應(yīng)溫度為50℃,攪拌速率為100rpm,反應(yīng)時(shí)間為300min。當(dāng)達(dá)到預(yù)設(shè)反應(yīng)時(shí)間后,用針管取2ml樣品,分析樣品的金屬成分,計(jì)算出金屬的浸出率。待反應(yīng)結(jié)束后,將浸出混合溶液過(guò)濾,洗滌濾渣三次,得到含有l(wèi)i、ni和co的浸出液和含錳濾渣,采用實(shí)施例1中步驟(1)所述的方法回收含錳濾渣中的錳。在本實(shí)施例條件下,當(dāng)反應(yīng)時(shí)間為300min時(shí),金屬li、ni和co的浸出率分別為99.21%、93.60%和90.20%,而金屬al、mn和fe的浸出率僅為1.54%、0.56%和0.49%,即含還原劑的氨水-銨鹽溶液浸出鋰離子電池電極粉時(shí),實(shí)現(xiàn)了有價(jià)金屬li、ni和co的選擇性浸出。以硫酸氫銨、碳酸銨、碳酸氫銨、氯化銨、硝酸銨或乙酸銨中的任意一種或至少兩種的組合,或硫酸銨與硫酸氫銨的組合,或碳酸銨與碳酸氫銨的組合代替硫酸銨,以亞硫酸鹽、硫代硫酸鹽、硫酸亞鐵、鐵粉、二氧化硫、葡萄糖、硼氫化鈉、硼氫化鉀或水合肼中的任意一種或至少兩種的組合代替亞硫酸氫鈉,按上述步驟浸出相同的電極粉,li、ni和co的浸出率均可高于99%、90%和88%,而金屬al、mn與fe的浸出率分別為0.3~2.4%、0.5~1.6%與0.4~1.5%,因此,可以實(shí)現(xiàn)有價(jià)金屬li、ni、co的選擇性浸出。步驟(2)、(3)和(4)同實(shí)施例1中的步驟(2)、(3)和(4)。當(dāng)所述浸出劑中氨水的濃度為0.1~3mol/l,如0.2mol/l、0.3mol/l、0.5mol/l、0.8mol/l、1mol/l、1.5mol/l、2mol/l或2.5mol/l;銨根離子的濃度為2.5~3.5mol/l,如2.8mol/l、3mol/l、3.2mol/l或3.4mol/l等;亞硫酸鈉的濃度為0.2~0.9mol/l,如0.3mol/l、0.4mol/l、0.5mol/l、0.7mol/l或0.8mol/l時(shí),將所述浸出劑用于回收與實(shí)施例2相同的廢舊鋰離子電池中的金屬組分,回收工藝條件也與實(shí)施例2中的工藝條件相同,當(dāng)反應(yīng)時(shí)間為300min時(shí),金屬li、ni和co的浸出率分別為99.52%、95.20%和92.15%,而金屬al、mn和fe的浸出率僅為1.44%、0.53%和0.41%,即含還原劑的氨水-銨鹽溶液浸出鋰離子電池電極粉時(shí),實(shí)現(xiàn)了有價(jià)金屬li、ni和co的選擇性浸出。實(shí)施例3一種正極材料的選擇性浸出劑,所述浸出劑為含有氨水和硫酸銨的溶液,其中c(nh3)=6mol/l,c(nh4+)=2mol/l。一種廢舊鋰離子電池中金屬組分的選擇性浸出及回收方法,包括如下步驟:(1)將廢舊鋰離子電池在400~600℃熱處理30~300min,破碎篩分得到電極粉料,其金屬組成如表3所示:表3電極粉的金屬組成金屬alfelinicomn含量(%)5.225.313.1613.5311.678.70取0.5g電極粉加入到盛有100ml含有氨水和硫酸銨混合溶液的三口燒瓶中,所述的三口燒瓶中所述混合溶液中不含有還原劑,將所述的三口燒瓶置于恒溫油浴鍋中,控制反應(yīng)溫度為15℃,攪拌速率為100rpm,反應(yīng)時(shí)間為30min。當(dāng)達(dá)到預(yù)設(shè)反應(yīng)時(shí)間后,用針管取2ml樣品,分析樣品的金屬成分,計(jì)算 出金屬的浸出率。待反應(yīng)結(jié)束后,將浸出混合溶液過(guò)濾,洗滌濾渣三次,得到含有l(wèi)i、ni和co的浸出液和含錳濾渣,采用實(shí)施例1步驟(1)所述的方法回收含錳濾渣中的錳。在本實(shí)施例條件下,當(dāng)反應(yīng)時(shí)間為30min時(shí),得到金屬li、ni和co的浸出率分別為49.5%、35.40%和32.10%,而金屬al、mn和fe的浸出率僅為5.34%、4.76%和6.24%,即不含還原劑的氨水-銨鹽溶液浸出鋰離子電池電極粉時(shí),實(shí)現(xiàn)了有價(jià)金屬li、ni和co的選擇性浸出。以硫酸氫銨、碳酸銨、碳酸氫銨、氯化銨、硝酸銨或乙酸銨中的任意一種或至少兩種的組合,或硫酸銨與硫酸氫銨的組合,或碳酸銨與碳酸氫銨的組合代替硫酸銨,按上述步驟浸出相同的電極粉,li、ni、co的浸出率均可高于45%、30%和30%,而金屬al、mn與fe的浸出率分別為3.0~10.0%、5~10%與4~11%,可以實(shí)現(xiàn)有價(jià)金屬li、ni和co的選擇性浸出。步驟(2)、(3)和(4)同實(shí)施例1中的步驟(2)、(3)和(4)。實(shí)施例4一種正極材料的選擇性浸出劑,所述浸出劑為含有氨水和硫代硫酸鈉的溶液,其中c(nh3)=10mol/l,c(nh4+)=0mol/l,硫代硫酸鈉的濃度為2mol/l。一種廢舊鋰離子電池中金屬組分的選擇性浸出及回收方法,包括如下步驟:(1)將廢舊鋰離子電池拆解后得到負(fù)有正極材料的鋁箔,用n-甲基吡咯烷酮超聲處理鋁箔片,固液分離后得到沉淀,將沉淀在600~800℃灼燒3~5h得到黑色電極粉,其金屬組成如表4所示:表4電極粉的金屬組成取20g電極粉加入到盛有100ml含有氨水和硫代硫酸鈉混合溶液的三口燒瓶中,所述的三口燒瓶中硫代硫酸鈉的濃度為2mol/l,將所述的三口燒瓶置于恒溫油浴鍋中,控制反應(yīng)溫度為100℃,攪拌速率為2000rpm,反應(yīng)時(shí)間為120min。當(dāng)達(dá)到預(yù)設(shè)反應(yīng)時(shí)間后,用針管取2ml樣品,分析樣品的金屬成分,計(jì)算出金屬的浸出率。待反應(yīng)結(jié)束后,將浸出混合溶液過(guò)濾,洗滌濾渣三次,得到含有l(wèi)i、ni和co的浸出液和含錳濾渣,采用實(shí)施例1步驟(1)所述的方法回收含錳濾渣中的錳。在本實(shí)施例條件下,當(dāng)反應(yīng)時(shí)間為120min時(shí),得到金屬li、ni和co的浸出率分別為89.21%、73.60%和70.20%,而金屬mn的浸出率僅為0.42%,即含還原劑的氨水溶液浸出鋰離子電池電極粉時(shí),實(shí)現(xiàn)了有價(jià)金屬li、ni和co的選擇性浸出。以亞硫酸氫鹽、硫代硫酸鹽、硫酸亞鐵、鐵粉、二氧化硫、葡萄糖、硼氫化鈉、硼氫化鉀或水合肼中的任意一種或至少兩種的組合代替硫代硫酸鈉,按上述步驟浸出相同的電極粉,li、ni和co的浸出率均可高于99%、85%和70%以上,而金屬mn的浸出率為0.3~1.0%,可以實(shí)現(xiàn)有價(jià)金屬li、ni和co的選擇性浸出。步驟(2)、(3)和(4)同實(shí)施例1中的步驟(2)、(3)和(4)。實(shí)施例5一種正極材料的選擇性浸出劑,所述浸出劑為含有硫酸銨和硫代硫酸鈉的溶液,硫代硫酸鈉的濃度為2mol/l。一種廢舊鋰離子電池中金屬組分的選擇性浸出及回收方法,包括如下步驟:(1)將廢舊鋰離子電池拆解后得到負(fù)有正極材料的鋁箔,鋁箔在400~600℃灼燒0.5~5h后篩分得到電極粉料,其金屬組成如表5所示:表5電極粉料的金屬組成金屬allinicomn含量(%)1.257.0119.5318.6718.42取10g電極粉加入到盛有100ml含有硫酸銨和硫代硫酸鈉混合溶液的三口燒瓶中,所述的三口燒瓶中硫代硫酸鈉的濃度為2mol/l,將所述的三口燒瓶置于恒溫油浴鍋中,控制反應(yīng)溫度為90℃,攪拌速率為2000rpm,反應(yīng)時(shí)間為480min。當(dāng)達(dá)到預(yù)設(shè)反應(yīng)時(shí)間后,用針管取2ml樣品,分析樣品的金屬成分,計(jì)算出金屬的浸出率。待反應(yīng)結(jié)束后,將浸出混合溶液過(guò)濾,洗滌濾渣三次,得到含有l(wèi)i、ni和co的浸出液和含錳濾渣,采用實(shí)施例1步驟(1)所述的方法回收含錳濾渣中的錳。在本實(shí)施例條件下,當(dāng)反應(yīng)時(shí)間為480min時(shí),得到金屬li、ni和co的浸出率分別為99.21%、93.60%和90.20%,而金屬al和mn的浸出率僅為3.40%和2.42%,即含還原劑的銨鹽溶液浸出鋰離子電池電極粉時(shí),實(shí)現(xiàn)了有價(jià)金屬li、ni和co的選擇性浸出。以硫酸氫銨、碳酸銨、碳酸氫銨、氯化銨、硝酸銨或乙酸銨中的任意一種或至少兩種的組合,或硫酸銨與硫酸氫銨的組合,或碳酸銨與碳酸氫銨的組合代替硫酸銨,以亞硫酸氫鹽、硫代硫酸鹽、硫酸亞鐵、鐵粉、二氧化硫、葡萄糖、硼氫化鈉、硼氫化鉀或水合肼中的任意一種或至少兩種的組合代替硫代硫酸鈉,按上述步驟浸出相同的電極粉,li、ni和co的浸出率均可高于98%、92%和90%,而金屬al和mn的浸出率分別為2~5%、2~5%,可以實(shí)現(xiàn)有價(jià)金屬li、 ni和co的選擇性浸出。步驟(2)、(3)和(4)同實(shí)施例1中的步驟(2)、(3)和(4)。申請(qǐng)人聲明,以上所述僅為本發(fā)明的具體實(shí)施方式,但本發(fā)明的保護(hù)范圍并不局限于此,所屬
技術(shù)領(lǐng)域:
的技術(shù)人員應(yīng)該明了,任何屬于本
技術(shù)領(lǐng)域:
的技術(shù)人員在本發(fā)明揭露的技術(shù)范圍內(nèi),可輕易想到的變化或替換,均落在本發(fā)明的保護(hù)范圍和公開(kāi)范圍之內(nèi)。當(dāng)前第1頁(yè)12