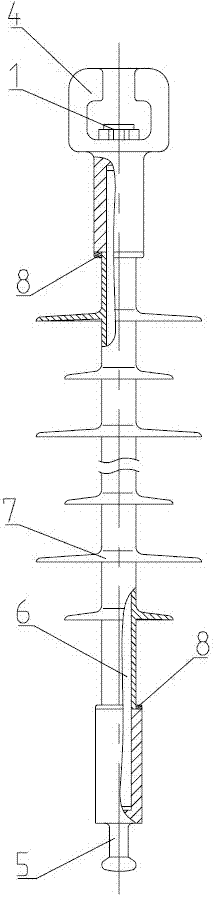
本發(fā)明屬于電力線路輸變電使用的復(fù)合絕緣子,具體說是涉一種復(fù)合絕緣子的制造方法。
背景技術(shù):已經(jīng)成熟的復(fù)合絕緣子配方的物理機(jī)械性能和生產(chǎn)工藝已經(jīng)基本滿足復(fù)合絕緣子的技術(shù)要求。但在實(shí)際制造過程中,關(guān)鍵工藝控制稍有不嚴(yán)謹(jǐn),即導(dǎo)致復(fù)合絕緣子電氣性能的不穩(wěn)定。據(jù)山東電力集團(tuán)公司對(duì)一次停電事故的分析,足以說明復(fù)合絕緣子內(nèi)部缺陷的存在,而在常規(guī)檢驗(yàn)、試驗(yàn)中是難以發(fā)現(xiàn)的。該公司所轄的一條500KV交流電力線路上使用的是由德外進(jìn)口的交流棒形復(fù)合懸式絕緣子,對(duì)其中兩支故障絕緣子退網(wǎng)檢查發(fā)現(xiàn),故障點(diǎn)處復(fù)合護(hù)套有孔眼,并與內(nèi)絕緣件粘接不牢固,在吸潮、積污、腐蝕、起痕多重作用下,致使復(fù)合護(hù)套快速劣化,內(nèi)絕緣件斷裂,導(dǎo)致全線停電,不得不將該線路絕緣子全部提前更換。另據(jù)國家絕緣子標(biāo)準(zhǔn)化技術(shù)委員會(huì)在修訂GB/T19519-2004《標(biāo)稱電壓高于1000V的交流架空線路用復(fù)合絕緣子—定義、試驗(yàn)方法及驗(yàn)收準(zhǔn)則》前言中也做了以下提示“我國十多年的運(yùn)行經(jīng)驗(yàn)表明,絕緣子金屬附件高壓端界面密封的破壞,是導(dǎo)致絕緣子破壞的主要原因,應(yīng)引起使用本標(biāo)準(zhǔn)各方的注意?!比绾蜗龔?fù)合絕緣子的潛在缺陷,充分發(fā)揮利用復(fù)合絕緣子的優(yōu)特點(diǎn)成為重要課題。再匯總各方面信息的基礎(chǔ)上,本發(fā)明人進(jìn)行了深入的研究,提出了本
技術(shù)實(shí)現(xiàn)要素:。發(fā)明內(nèi)容本發(fā)明要解決的技術(shù)問題是為了克服目前復(fù)合絕緣子壽命前期運(yùn)行正常,中后期出現(xiàn)質(zhì)量隱患,導(dǎo)致停電事故,提前報(bào)廢而提出的一種復(fù)合絕緣子制造方法。為解決上述技術(shù)問題,本發(fā)明包括以下步驟:A、將內(nèi)絕緣件與頭部金屬附件及尾部金屬附件裝配連接;B、將連接在一起的上述組件進(jìn)行表面清潔處理;C、在清潔處理后的內(nèi)絕緣件表面及與內(nèi)絕緣件相臨近的頭部金屬附件與尾部金屬附件的局部外表面噴涂一層偶聯(lián)劑,靜置30-60min,待偶聯(lián)劑呈無濕狀附著于內(nèi)絕緣件表面,再刷涂一層偶聯(lián)劑,靜置1-4h;D、將刷涂偶聯(lián)劑后的組件置入溫升至140±5℃的加熱干燥裝置內(nèi)保溫待用;E、將上述組件與復(fù)合硅橡膠置入預(yù)熱后模具型腔內(nèi),在150-205℃溫度條件下,硫化700-1800S后,打開模具型腔,取出復(fù)合絕緣子,常溫冷卻;F、將復(fù)合絕緣子電壓端和絕緣端界面余料清理干凈,用同型號(hào)常溫硫化硅橡膠沿界面縫隙壓縫注入,在所有端部界面形成無間隙密封。所述A步驟中的內(nèi)絕緣件為瓷件或玻璃件,所述的內(nèi)絕緣件與頭部金屬附件及尾部金屬附件通過水泥膠合劑固定連接在一起。所述A步驟中的內(nèi)絕緣件為芯棒,所述的內(nèi)絕緣件與頭部金屬附件及尾部金屬附件經(jīng)外力壓縮金屬附件壓裝在一起。所述B步驟中進(jìn)行表面清潔處理,首先是用氣或風(fēng)流將界面結(jié)合部預(yù)留冷熱緩沖縫隙內(nèi)的膠合劑渣粒及內(nèi)絕緣件表面浮塵吹拂干凈,再將組件置入清洗劑內(nèi)浸泡3-5min,在一定外力下進(jìn)行清洗,清潔后組件在干燥清潔環(huán)境下自然晾干。所述D步驟中保溫時(shí)間為40-240min。所述E步驟中硫化成型壓力為0.4-1.2MN。所述E步驟中復(fù)合絕緣子在復(fù)合成型過程中,模具經(jīng)3-7次啟閉,釋放排氣。所述F步驟中所述端部界面形成無間隙密封為T型狀搭接密封,密封層厚度大于復(fù)合護(hù)套厚度1-3mm。本發(fā)明制造方法的優(yōu)點(diǎn)效果是:1、將復(fù)合絕緣子內(nèi)絕緣件在包封硫化硅橡膠前進(jìn)行清潔處理,并對(duì)噴刷各一層偶聯(lián)劑后的內(nèi)絕緣件進(jìn)行預(yù)熱,同時(shí)達(dá)到排潮和激活偶聯(lián)劑活性成分的雙重作用。2、在復(fù)合絕緣子包封后成型前進(jìn)行不少于3-7次的壓縮氣體排放,保證了復(fù)合傘套表面光滑致密,真正體現(xiàn)出硅橡膠憎水和憎水遷移的特點(diǎn),提高了復(fù)合絕緣子的性能恢復(fù)和自潔能力,同時(shí)消除了內(nèi)絕緣件與復(fù)合硅橡膠傘套間經(jīng)常出現(xiàn)的孔眼和氣泡,使得內(nèi)絕緣件與復(fù)合傘套無間隙的牢固粘接,達(dá)到了粘接強(qiáng)度大于硅橡膠自身的抗撕裂強(qiáng)度,阻斷了電弧沿內(nèi)絕緣件與復(fù)合傘套間不規(guī)則捷徑到達(dá)絕緣端金屬附件的通道,防止了復(fù)合絕緣子的內(nèi)部閃絡(luò),進(jìn)而確保和提高了復(fù)合絕緣子的電氣性能。3、通過對(duì)復(fù)合絕緣子端部界面的T形密封,阻塞了端部吸潮的通道,消除了潮氣對(duì)復(fù)合絕緣子內(nèi)部的膠合劑、偶聯(lián)劑及內(nèi)絕緣件的水解侵害,也降低了電壓端吸潮、積污、放電的蝕損。經(jīng)大于國家標(biāo)準(zhǔn)的溫差90K的3次15min冷熱溫度循環(huán)試驗(yàn),密封界面無脫落、裂紋和變形,與未經(jīng)試驗(yàn)的產(chǎn)品密封界面比較毫無差異。極大地提高了復(fù)合絕緣子應(yīng)有的電氣性能和設(shè)計(jì)運(yùn)行壽命。附圖說明下面結(jié)合附圖對(duì)本發(fā)明的具體實(shí)施方式作進(jìn)一步詳細(xì)描述:圖1為本發(fā)明一種實(shí)施例的結(jié)構(gòu)示意圖;圖2為本發(fā)明另一種實(shí)施例的結(jié)構(gòu)示意圖。具體實(shí)施方式圖1所示為一種盤式復(fù)合絕緣子,該絕緣子是在內(nèi)絕緣件6頭部外表面及內(nèi)腔中通過水泥膠合劑3固定粘接有頭部金屬附件4及尾部金屬附件5。本實(shí)施例中,內(nèi)絕緣件6為瓷件或玻璃件,整體呈盤狀,頭部金屬附件4為鐵帽,鐵帽中設(shè)有鎖緊銷1,尾部金屬附件5為鋼腳,內(nèi)絕緣件6的盤口處延伸出鐵帽徑向邊緣,鋼腳頂部與內(nèi)絕緣件6頂部內(nèi)壁之間設(shè)有墊片2,鋼腳底部伸出內(nèi)絕緣件6,水泥膠合劑3位于鐵帽口沿以內(nèi)及內(nèi)絕緣件6下部口沿以上部位。在內(nèi)絕緣件6的外表面設(shè)有復(fù)合護(hù)套7,該復(fù)合護(hù)套7徑向頂面內(nèi)側(cè)與鐵帽邊緣相接并包覆鐵帽內(nèi)腔與內(nèi)絕緣件6頭部外表面之間的水泥膠合劑3,復(fù)合護(hù)套7徑向底面內(nèi)側(cè)延伸至鋼腳并包覆內(nèi)絕緣件內(nèi)腔與鋼腳之間的水泥膠合劑3,該復(fù)合護(hù)套7為硅橡膠材料,成型后該復(fù)合護(hù)套7整體呈盤狀或傘翼狀。在復(fù)合護(hù)套7徑向頂面內(nèi)側(cè)與鐵帽邊緣以及復(fù)合護(hù)套徑向底面與鋼腳之間的端部界面的界面縫隙處設(shè)有密封膠層8,該密封膠層8用同型號(hào)常溫硫化硅橡膠沿界面縫隙壓縫注入,密封膠層8與復(fù)合護(hù)套7成一體結(jié)構(gòu),在所有端部界面形成無間隙密封,并且端部界面形成的無間隙密封為T型狀搭接密封。制作該盤式復(fù)合絕緣子時(shí),包括以下步驟:A、將內(nèi)絕緣件與頭部金屬附件及尾部金屬附件裝配連接,即將內(nèi)絕緣件與頭部金屬附件及尾部金屬附件通過水泥膠合劑固定連接在一起,連接后的組件經(jīng)機(jī)械負(fù)荷和電氣試驗(yàn)轉(zhuǎn)入下流程,內(nèi)絕緣件為瓷件或玻璃件。B、將連接在一起的上述組件進(jìn)行表面清潔處理,首先是用氣或風(fēng)流將界面結(jié)合部預(yù)留冷熱緩沖縫隙內(nèi)的膠合劑渣粒及內(nèi)絕緣件表面浮塵吹拂干凈,再將組件置入清洗劑內(nèi)浸泡3-5min,在一定外力下進(jìn)行清洗,如刷洗或攪動(dòng)清洗,重點(diǎn)是將內(nèi)絕緣件表面清洗,清潔后組件在干燥清潔環(huán)境下自然晾干。C、在清潔處理后的內(nèi)絕緣件表面及與內(nèi)絕緣件相臨近的頭部金屬附件與尾部金屬附件的局部外表面噴涂一層偶聯(lián)劑,即在內(nèi)絕緣件表面、鐵帽口沿處內(nèi)外表面及鋼腳水泥膠合劑以下的直桿段外表面噴涂一層偶聯(lián)劑,靜置30-60min,待偶聯(lián)劑呈無濕狀附著于內(nèi)絕緣件表面,再刷涂一層偶聯(lián)劑,靜置1-4h。D、將刷涂偶聯(lián)劑后的組件置入溫升至140±5℃的加熱干燥裝置內(nèi)保溫40-240min待用,該過程達(dá)到排潮和激活偶聯(lián)劑活性成分的雙重作用。E、將上述組件與復(fù)合硅橡膠置入預(yù)熱后模具型腔內(nèi),在150-205℃溫度條件下,硫化成型壓力為0.4-1.2MN,復(fù)合成型過程中,模具經(jīng)3-7次啟閉,釋放排氣,復(fù)合絕緣子進(jìn)入包封硫化成型狀態(tài)。硫化700-1800S后,打開模具型腔,取出復(fù)合絕緣子,常溫冷卻。實(shí)際操作時(shí),先將硫化成型設(shè)備的溫度預(yù)設(shè)至155-200±5℃,硫化時(shí)間預(yù)設(shè)至700-1800S,硫化成型壓力預(yù)設(shè)至0.4-1.2MN,閉合上下加熱板,開啟加溫裝置,對(duì)復(fù)合絕緣子模具進(jìn)行加溫。待硫化成型設(shè)備達(dá)到預(yù)設(shè)溫度,且保溫達(dá)到30min以上,將組件與復(fù)合硅橡膠置入模具型腔內(nèi)。在復(fù)合絕緣子包封后成型前進(jìn)行不少于3-7次的壓縮氣體排放,保證了復(fù)合傘套表面光滑致密,真正體現(xiàn)出硅橡膠憎水和憎水遷移的特點(diǎn),提高了復(fù)合絕緣子的性能恢復(fù)和自潔能力,同時(shí)消除了內(nèi)絕緣件與復(fù)合硅橡膠傘套間經(jīng)常出現(xiàn)的孔眼和氣泡,使得內(nèi)絕緣件與復(fù)合傘套無間隙的牢固粘接,達(dá)到了粘接強(qiáng)度大于硅橡膠自身的抗撕裂強(qiáng)度,阻斷了電弧沿內(nèi)絕緣件與復(fù)合傘套間不規(guī)則捷徑到達(dá)絕緣端金屬附件的通道,防止了復(fù)合絕緣子的內(nèi)部閃絡(luò),進(jìn)而確保和提高了復(fù)合絕緣子的電氣性能。F、將復(fù)合絕緣子電壓端和絕緣端界面余料清理干凈,用同型號(hào)常溫硫化硅橡膠沿界面縫隙壓縫注入,在所有端部界面形成無間隙密封,該端部界面形成無間隙密封優(yōu)選采用T型狀搭接密封,密封層厚度大于復(fù)合護(hù)套厚度1-3mm,由此制得盤式復(fù)合絕緣子。前述復(fù)合護(hù)套厚度及密封層厚度是指該處垂直于內(nèi)絕緣件表面處的厚度(下同)。通過對(duì)復(fù)合絕緣子端部界面的T形密封,阻塞了端部吸潮的通道,消除了潮氣對(duì)復(fù)合絕緣子內(nèi)部的膠合劑、偶聯(lián)劑及內(nèi)絕緣件的水解侵害,也降低了電壓端吸潮、積污、放電的蝕損。經(jīng)大于國家標(biāo)準(zhǔn)的溫差90K的3次15min冷熱溫度循環(huán)試驗(yàn),密封界面無脫落、裂紋和變形,與未經(jīng)試驗(yàn)的產(chǎn)品密封界面比較毫無差異。極大地提高了復(fù)合絕緣子應(yīng)有的電氣性能和設(shè)計(jì)運(yùn)行壽命。利用該方法制作的盤式復(fù)合絕緣子,通過對(duì)復(fù)合絕緣子內(nèi)絕緣件及與內(nèi)絕緣件相臨近的頭部金屬附件與尾部金屬附件的局部外表面的高度清潔處理,使得偶聯(lián)劑的附著力增強(qiáng),又加之采用噴刷相結(jié)合的涂敷方式,偶聯(lián)劑能在內(nèi)絕緣件表面形成完整的粘接膜層,進(jìn)而提高了內(nèi)絕緣件與復(fù)合硅橡膠全面粘接的強(qiáng)度。另外,復(fù)合絕緣子硫化成型前的氣體排放,消除了復(fù)合護(hù)套內(nèi)的氣體,進(jìn)而防止了孔眼的出現(xiàn)(因孔眼是氣泡未貫通或破裂后形成的),對(duì)復(fù)合絕緣子外絕緣的加強(qiáng)起到了至關(guān)重要的作用。再就對(duì)復(fù)合絕緣子端部界面的密封進(jìn)行了大的改進(jìn),由傳統(tǒng)的密封圈有隙套封和涂抹密封膜層蓋封改由壓縫注膠放射延伸搭接,增加密封層厚度的密封方式,降低了因復(fù)合絕緣子端部界面破壞導(dǎo)致停電事故的概率,對(duì)于保證電網(wǎng)安全運(yùn)行,提高供電和用電的經(jīng)濟(jì)效益,都產(chǎn)生了積極的效果。圖2所示為一種棒式復(fù)合絕緣子,該絕緣子是在內(nèi)絕緣件6兩端經(jīng)外力壓縮將頭部金屬附件4及尾部金屬附件5壓裝在內(nèi)絕緣件6兩端部。本實(shí)施例中,內(nèi)絕緣件6為芯棒,頭部金屬附件4為鐵帽,鐵帽中設(shè)有鎖緊銷1,尾部金屬附件5為鋼腳。即將頭部金屬附件4及尾部金屬附件5用壓接機(jī)壓裝在芯棒兩端部。在內(nèi)絕緣件6的外表面及與內(nèi)絕緣件6兩端相接的頭部金屬附件4及尾部金屬附件5內(nèi)端外表面設(shè)有復(fù)合護(hù)套7,即該復(fù)合護(hù)套7一端與鐵帽內(nèi)端相接并包覆鐵帽內(nèi)端頭,復(fù)合護(hù)套7另一端與鋼腳內(nèi)端相接并包覆鋼腳內(nèi)端頭,該復(fù)合護(hù)套7為硅橡膠材料,成型后該復(fù)合護(hù)套7整體呈串接的盤狀或傘翼狀。在復(fù)合護(hù)套7兩端與鐵帽及鋼腳的端部界面處設(shè)有密封膠層8,該密封膠層8用同型號(hào)常溫硫化硅橡膠沿界面縫隙壓縫注入,密封膠層8與復(fù)合護(hù)套7成一體結(jié)構(gòu),在所有端部界面形成無間隙密封,并且端部界面形成的無間隙密封為T型狀搭接密封。制作該棒式復(fù)合絕緣子時(shí),包括以下步驟:A、將內(nèi)絕緣件與頭部金屬附件及尾部金屬附件裝配連接,即將內(nèi)絕緣件兩端經(jīng)外力壓縮將頭部金屬附件及尾部金屬附件壓裝在內(nèi)絕緣件兩端部,連接后的組件經(jīng)機(jī)械負(fù)荷和電氣試驗(yàn)轉(zhuǎn)入下流程,內(nèi)絕緣件為芯棒。B、將連接在一起的上述組件進(jìn)行表面清潔處理,首先是用氣或風(fēng)流將界面結(jié)合部預(yù)留冷熱緩沖縫隙及內(nèi)絕緣件表面浮塵吹拂干凈,再將組件置入清洗劑內(nèi)浸泡3-5min,在一定外力下進(jìn)行清洗,如刷洗或攪動(dòng)清洗,重點(diǎn)是將內(nèi)絕緣件表面清洗,清潔后組件在干燥清潔環(huán)境下自然晾干。C、在清潔處理后的內(nèi)絕緣件表面及與內(nèi)絕緣件兩端相接的頭部金屬附件及尾部金屬附件內(nèi)端外表面噴涂一層偶聯(lián)劑,即在內(nèi)絕緣件表面、鐵帽與內(nèi)絕緣件相接的內(nèi)端外表面及鋼腳與內(nèi)絕緣件相接的內(nèi)端外表面噴涂一層偶聯(lián)劑,靜置30-60min,待偶聯(lián)劑呈無濕狀附著于內(nèi)絕緣件表面,再刷涂一層偶聯(lián)劑,靜置1-4h。D、將刷涂偶聯(lián)劑后的組件置入溫升至140±5℃的加熱干燥裝置內(nèi)保溫40-240min待用,該過程達(dá)到排潮和激活偶聯(lián)劑活性成分的雙重作用。E、將上述組件與復(fù)合硅橡膠置入預(yù)熱后模具型腔內(nèi),在150-205℃溫度條件下,硫化成型壓力為0.4-1.2MN,復(fù)合成型過程中,模具經(jīng)3-7次啟閉,釋放排氣,復(fù)合絕緣子進(jìn)入包封硫化成型狀態(tài)。硫化700-1800S后,打開模具型腔,取出復(fù)合絕緣子,常溫冷卻。實(shí)際操作時(shí),先將硫化成型設(shè)備的溫度預(yù)設(shè)至155-200±5℃,硫化時(shí)間預(yù)設(shè)至700-1800S,硫化成型壓力預(yù)設(shè)至0.4-1.2MN,閉合上下加熱板,開啟加溫裝置,對(duì)復(fù)合絕緣子模具進(jìn)行加溫。待硫化成型設(shè)備達(dá)到預(yù)設(shè)溫度,且保溫達(dá)到30min以上,將組件與復(fù)合硅橡膠置入模具型腔內(nèi)。在復(fù)合絕緣子包封后成型前進(jìn)行不少于3-7次的壓縮氣體排放,保證了復(fù)合傘套表面光滑致密,真正體現(xiàn)出硅橡膠憎水和憎水遷移的特點(diǎn),提高了復(fù)合絕緣子的性能恢復(fù)和自潔能力,同時(shí)消除了內(nèi)絕緣件與復(fù)合硅橡膠傘套間經(jīng)常出現(xiàn)的孔眼和氣泡,使得內(nèi)絕緣件與復(fù)合傘套無間隙的牢固粘接,達(dá)到了粘接強(qiáng)度大于硅橡膠自身的抗撕裂強(qiáng)度,阻斷了電弧沿內(nèi)絕緣件與復(fù)合傘套間不規(guī)則捷徑到達(dá)絕緣端金屬附件的通道,防止了復(fù)合絕緣子的內(nèi)部閃絡(luò),進(jìn)而確保和提高了復(fù)合絕緣子的電氣性能。F、將復(fù)合絕緣子電壓端和絕緣端界面余料清理干凈,用同型號(hào)常溫硫化硅橡膠沿界面縫隙壓縫注入,在所有端部界面形成無間隙密封,該端部界面形成無間隙密封優(yōu)選采用T型狀搭接密封,密封層厚度大于復(fù)合護(hù)套厚度1-3mm,由此制得棒式復(fù)合絕緣子。通過對(duì)復(fù)合絕緣子端部界面的T形密封,阻塞了端部吸潮的通道,消除了潮氣對(duì)復(fù)合絕緣子內(nèi)部的膠合劑、偶聯(lián)劑及內(nèi)絕緣件的水解侵害,也降低了電壓端吸潮、積污、放電的蝕損。經(jīng)大于國家標(biāo)準(zhǔn)的溫差90K的3次15min冷熱溫度循環(huán)試驗(yàn),密封界面無脫落、裂紋和變形,與未經(jīng)試驗(yàn)的產(chǎn)品密封界面比較毫無差異。極大地提高了復(fù)合絕緣子應(yīng)有的電氣性能和設(shè)計(jì)運(yùn)行壽命。利用該方法制作的棒式復(fù)合絕緣子,通過對(duì)復(fù)合絕緣子內(nèi)絕緣件及與內(nèi)絕緣件兩端相接的頭部金屬附件及尾部金屬附件內(nèi)端的局部外表面的高度清潔處理,使得偶聯(lián)劑的附著力增強(qiáng),又加之采用噴刷相結(jié)合的涂敷方式,偶聯(lián)劑能在內(nèi)絕緣件表面形成完整的粘接膜層,進(jìn)而提高了內(nèi)絕緣件與復(fù)合硅橡膠全面粘接的強(qiáng)度。另外,復(fù)合絕緣子硫化成型前的氣體排放,消除了復(fù)合護(hù)套內(nèi)的氣體,進(jìn)而防止了孔眼的出現(xiàn)(因孔眼是氣泡未貫通或破裂后形成的),對(duì)復(fù)合絕緣子外絕緣的加強(qiáng)起到了至關(guān)重要的作用。再就對(duì)復(fù)合絕緣子端部界面的密封進(jìn)行了大的改進(jìn),由傳統(tǒng)的密封圈有隙套封和涂抹密封膜層蓋封改由壓縫注膠放射延伸搭接,增加密封層厚度的密封方式,降低了因復(fù)合絕緣子端部界面破壞導(dǎo)致停電事故的概率,對(duì)于保證電網(wǎng)安全運(yùn)行,提高供電和用電的經(jīng)濟(jì)效益,都產(chǎn)生了積極的效果。