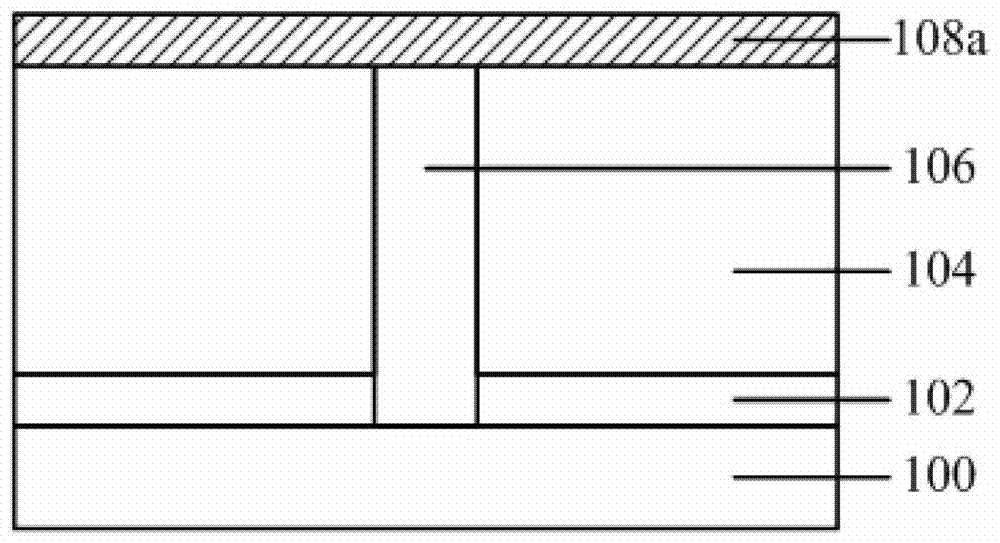
本發(fā)明涉及半導(dǎo)體制造技術(shù)領(lǐng)域,尤其涉及一種半導(dǎo)體結(jié)構(gòu)及其形成方法。
背景技術(shù):現(xiàn)今集成電路設(shè)計(jì)和制造領(lǐng)域所遇到的一個(gè)挑戰(zhàn)是如何降低信號傳輸RC延遲(ResistiveCapacitivedelay),對此,現(xiàn)在技術(shù)已經(jīng)采用的一種方法是將鋁金屬層替換為銅金屬層,降低金屬層串聯(lián)電阻;還有一種方法是降低金屬層之間的寄生電容,這可以通過在金屬層之間的介質(zhì)層中構(gòu)造多孔的(Porous)低介電常數(shù)(Lowk)材料或者空氣隙(AirGap)來實(shí)現(xiàn)?,F(xiàn)有工藝在金屬層周圍形成空氣隙時(shí),包括如下步驟:首先,在半導(dǎo)體襯底上形成層間介質(zhì)層;接著,形成貫穿所述層間介質(zhì)層的銅金屬層;再接著,去除位于銅金屬層之間的層間介質(zhì)層,從而在層間介質(zhì)層原占據(jù)的位置處形成開口;最后,在所述開口和銅金屬層上形成阻擋層,對所述開口進(jìn)行封口,以形成空氣隙。然而,通過完全去除銅金屬層之間的層間介質(zhì)層形成的空氣隙機(jī)械強(qiáng)度差,且銅金屬層易發(fā)生變形或者剝離,所形成半導(dǎo)體結(jié)構(gòu)的成品率較低,包括所形成半導(dǎo)體結(jié)構(gòu)的半導(dǎo)體器件電學(xué)性能較差。而且,由于所形成開口的直徑較大,在進(jìn)行封口時(shí),阻擋層易沉積到開口的底部和側(cè)壁,在開口內(nèi)形成一定厚度的阻擋層,由開口內(nèi)阻擋層所圍成的空氣隙較小,不利于半導(dǎo)體結(jié)構(gòu)在信號傳輸過程中RC延遲的降低。更多與上述技術(shù)方案相關(guān)的信息請參考公開號為CN1967800A的中國專利申請。
技術(shù)實(shí)現(xiàn)要素:本發(fā)明解決的問題是提供一種半導(dǎo)體結(jié)構(gòu)及其形成方法,增強(qiáng)了半導(dǎo)體結(jié)構(gòu)中包含空氣隙的層間介質(zhì)層的機(jī)械強(qiáng)度,以提高包括所述半導(dǎo)體結(jié)構(gòu)的半導(dǎo)體器件的電學(xué)性能。為解決上述問題,本發(fā)明提供了一種半導(dǎo)體結(jié)構(gòu)的形成方法,包括:提供半導(dǎo)體襯底;在所述半導(dǎo)體襯底上形成層間介質(zhì)層,并在所述層間介質(zhì)層中形成金屬層,所述金屬層的上表面與所述層間介質(zhì)層的上表面齊平;在所述層間介質(zhì)層和金屬層上形成包含納米孔洞的掩膜層;以所述掩膜層為掩模,刻蝕所述層間介質(zhì)層,在所述層間介質(zhì)層中形成管狀開口??蛇x的,所述掩膜層的材料為氧化鋁,形成包含納米孔洞的掩膜層包括:在所述層間介質(zhì)層和金屬層上形成鋁金屬層;對所述鋁金屬層進(jìn)行陽極氧化處理,形成包含納米孔洞的氧化鋁層。相應(yīng)的,本發(fā)明還提供了一種半導(dǎo)體結(jié)構(gòu),包括:半導(dǎo)體襯底;位于所述半導(dǎo)體襯底上的層間介質(zhì)層;位于所述層間介質(zhì)層中的金屬層,所述金屬層的上表面與所述層間介質(zhì)層的上表面齊平;其中,所述層間介質(zhì)層中形成有管狀開口。可選的,所述半導(dǎo)體結(jié)構(gòu)還包括:位于所述層間介質(zhì)層和金屬層上的掩膜層,所述掩膜層中形成有與所述管狀開口對應(yīng)的納米孔洞。與現(xiàn)有技術(shù)相比,本發(fā)明技術(shù)方案具有以下優(yōu)點(diǎn):在半導(dǎo)體襯底上的層間介質(zhì)層中形成金屬層之后,在金屬層和層間介質(zhì)層上形成包含納米孔洞的掩膜層,然后以掩膜層為掩模,刻蝕所述層間介質(zhì)層,形成貫穿層間介質(zhì)層厚度的管狀開口。之后,通過在掩膜層上形成阻擋層,對所述管狀開口進(jìn)行封口,在層間介質(zhì)層中形成空氣隙。由于管狀孔洞在與掩膜層表面平行方向上橫截面的直徑較小,阻擋層不易沉積于管狀開口內(nèi)部,所形成的空氣隙較大,有效降低了層間介質(zhì)層的介電常數(shù),降低了所形成半導(dǎo)體結(jié)構(gòu)在信號傳輸過程中的RC延遲。而且,由于空氣隙與金屬層之間還保留部分層間介質(zhì)層,空氣隙的機(jī)械強(qiáng)度較大,位于層間介質(zhì)層中的金屬層不易變形或者剝離,所形成半導(dǎo)體結(jié)構(gòu)的成品率高,最終提高了包含所形成半導(dǎo)體結(jié)構(gòu)的半導(dǎo)體器件的性能。附圖說明圖1為本發(fā)明半導(dǎo)體結(jié)構(gòu)的形成方法一個(gè)實(shí)施方式的流程示意圖;圖2~圖5為本發(fā)明半導(dǎo)體結(jié)構(gòu)的形成方法一個(gè)實(shí)施例的示意圖。具體實(shí)施方式為使本發(fā)明的上述目的、特征和優(yōu)點(diǎn)能夠更加明顯易懂,下面結(jié)合附圖對本發(fā)明的具體實(shí)施方式做詳細(xì)的說明。在下面的描述中闡述了很多具體細(xì)節(jié)以便于充分理解本發(fā)明,但是本發(fā)明還可以采用其它不同于在此描述的其它方式來實(shí)施,因此本發(fā)明不受下面公開的具體實(shí)施例的限制。正如
背景技術(shù):部分所述,現(xiàn)有通過去除銅金屬層之間層間介質(zhì)層形成的空氣隙機(jī)械強(qiáng)度差,銅金屬層易發(fā)生變形或者剝離,導(dǎo)致包含所形成半導(dǎo)體結(jié)構(gòu)的半導(dǎo)體器件性能較差。而且,在層間介質(zhì)層被完全去除之后,所形成開口的直徑較大,形成阻擋層時(shí),阻擋層易沉積于開口內(nèi)部而導(dǎo)致所形成的空氣隙較小,不利于半導(dǎo)體結(jié)構(gòu)RC延遲的降低。針對上述缺陷,本發(fā)明提供了一種半導(dǎo)體結(jié)構(gòu)的形成方法,在銅金屬層形成之后,在層間介質(zhì)層和金屬層上形成包含納米孔洞的掩膜層,然后以掩膜層為掩模對層間介質(zhì)層進(jìn)行刻蝕,在層間介質(zhì)層中形成若干管狀開口,由于管狀開口在與掩膜層表面平行方向上橫截面的直徑較小,通過形成阻擋層對管狀開口進(jìn)行封口時(shí),阻擋層不易沉積于管狀開口內(nèi)部,使形成于介質(zhì)層中的空氣隙較大。而且,由于空氣隙形成于層間介質(zhì)層中,所形成空氣隙的機(jī)械強(qiáng)度較大,位于層間介質(zhì)層中的金屬層也不易變形或者剝離,提高了所形成半導(dǎo)體結(jié)構(gòu)的成品率,包含所形成半導(dǎo)體結(jié)構(gòu)的半導(dǎo)體器件的性能較佳。下面結(jié)合附圖進(jìn)行詳細(xì)說明。參考圖1,為本發(fā)明半導(dǎo)體結(jié)構(gòu)的形成方法一個(gè)實(shí)施方式的流程示意圖,包括:步驟S11,提供半導(dǎo)體襯底;步驟S12,在所述半導(dǎo)體襯底上由下至上依次形成停止層和層間介質(zhì)層;步驟S13,形成貫穿所述層間介質(zhì)層和停止層的金屬層;步驟S14,在所述層間介質(zhì)層和金屬層上形成鋁金屬層;步驟S15,對所述鋁金屬層進(jìn)行陽極氧化處理,形成包含納米孔洞的氧化鋁層;步驟S16,以所述掩膜層為掩模,刻蝕所述層間介質(zhì)層,在所述層間介質(zhì)層中形成管狀開口;步驟S17,進(jìn)行清洗工藝;步驟S18,在包含納米孔洞的氧化鋁層上形成阻擋層。參考圖2~圖5,通過具體實(shí)施例對本發(fā)明半導(dǎo)體結(jié)構(gòu)的形成方法做進(jìn)一步說明。參考圖2,提供半導(dǎo)體襯底100,并在所述半導(dǎo)體襯底100上由下至上依次形成停止層102和層間介質(zhì)層104。本實(shí)施例中,所述半導(dǎo)體襯底100的材料可為單晶硅或單晶硅鍺,或者單晶摻碳硅;或者還可以包括其它的材料,本發(fā)明對此不做限制。此外,所述半導(dǎo)體襯底100中形成有器件結(jié)構(gòu)(圖未示),所述器件結(jié)構(gòu)可以為半導(dǎo)體前段工藝中形成的器件結(jié)構(gòu),例如MOS晶體管等。所述停止層102用于防止后續(xù)形成的金屬層中原子擴(kuò)散。具體的,當(dāng)所述金屬層的材料為銅時(shí),所述停止層102的材料可為含碳氮化硅。所述層間介質(zhì)層104的材料為低k材料或者超低k材料。繼續(xù)參考圖2,形成貫穿所述層間介質(zhì)層104和停止層102的金屬層106。本實(shí)施例中,所述金屬層106的材料可為銅。但需要說明的是,本發(fā)明并不限制所述金屬層106的材料。具體的,形成金屬層106可包括如下步驟:在所述層間介質(zhì)層104上形成光刻膠層(圖未示),所述光刻膠層中形成有與所述金屬層106位置和形狀對應(yīng)的光刻圖形;以所述光刻膠層為掩模,沿光刻圖形刻蝕所述層間介質(zhì)層104和停...