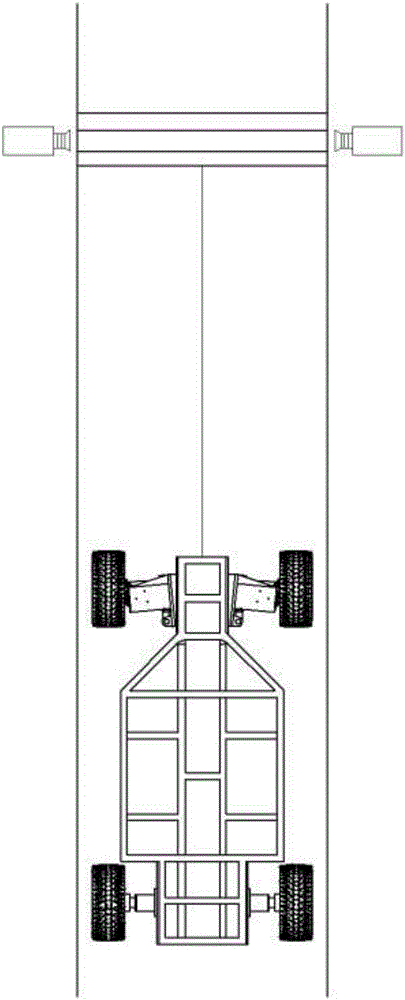
本發(fā)明涉及汽車零部件模擬試驗領域,具體涉及一種用于車輪模擬實況沖擊試驗的車輛及系統(tǒng)。
背景技術:
:目前在進行車輪模擬沖擊試驗時,往往采用臺架方法來進行徑向沖擊、13度沖擊等試驗,從而考察車輪在各種沖撞條件下的反應并判斷車輪是否符合汽車生產(chǎn)商及使用者的要求。臺架試驗是對現(xiàn)實駕駛條件的模擬,其模擬結果可能無法完全反映實際駕駛過程中遇到各種不理想路面的真實反應。為了提供交通事故條件下的車輛質量,整車廠商往往使用真車沖撞墻面等試驗來考察整車在交通事故下的表現(xiàn)。然而目前還沒有針對車輪等零部件在非事故條件下的考驗來進行試驗的方法和裝置。技術實現(xiàn)要素:為了在非事故條件下對車輪等零部件進行模擬實況沖擊試驗,本發(fā)明提供了一種用于車輪模擬實況沖擊試驗的車輛及系統(tǒng)。本領域的技術人員知道,在汽車的行駛過程中可能遭遇路面上的凸起物。該凸起物可能是泥土路面上的隆起部分、村道或鄉(xiāng)鎮(zhèn)道路上為農(nóng)業(yè)澆灌而鋪設的水管及護泥、小區(qū)或學校周邊鋪設的減速帶或者道路上出現(xiàn)的其他隆起物或者障礙物。汽車行駛過程中也可能遭遇凹陷,凹陷可能是泥土路面、瀝青路面和水泥路面上的凹陷部分,路面涂層型減速帶等等。汽車當行駛通過以上的路面結構時,車胎將對車輪造成一定的作用力。該作用力隨后通過軸和懸掛系統(tǒng)分散到車身。作為直接面對沖擊的汽車零部件,車輪在這一行駛事件中可能遭受損傷。作為車輪生產(chǎn)企業(yè),中信戴卡希望在更接近現(xiàn)實狀態(tài)的條件下進行車輪性能檢測。在本發(fā)明的一個方面,提供了一種用于車輪模擬實況沖擊試驗的車輛,所述的車輛由碰撞車輛總成(1)和測試的實車車輪及懸架系統(tǒng)(2)構成,其特征在于:所述的碰撞車輛總成(1)包括臺車車體(101)、砝碼及固定裝置(102)、后輪及輪軸總成(103)和牽引掛鉤適配機構(104);所述的臺車車體(101)中部設置有砝碼及固定裝置(102),在臺車車體(101)前部安裝有測試的實車車輪及懸架系統(tǒng)(2),臺車車體(101)后部安裝后輪及輪軸總成(103),并且臺車車體(101)底部固定有牽引掛鉤適配機構(104)。在本發(fā)明優(yōu)選的方面,所述的臺車車體(101)由方管鋼材焊接而成,并且其底部鋪設有鋼板。在本發(fā)明優(yōu)選的方面,所述的砝碼及固定裝置(102)包括位于固定到臺車車體(101)前部、中部和后部的砝碼,并且固定到臺車車體(101)前部、中部和后部的砝碼分別為50~200千克、50~400千克和50~200千克。在本發(fā)明進一步優(yōu)選的方面,所述的砝碼及固定裝置(102)中單塊的砝碼為直徑400mm,厚度50mm的圓柱體,中間有直徑60mm的通孔;單塊的砝碼通過固定桿固定到臺車車體(101),固定桿為長度500mm,M48的螺紋桿;固定桿底端通過螺紋固定在臺車底部車體上。在本發(fā)明優(yōu)選的方面,所述的測試的實車車輪及懸架系統(tǒng)(2)包括測試車輪輪胎(201)、輪轂軸承(202)、轉向節(jié)(203)、阻尼器及彈簧(204)、轉向拉桿(205)、控制臂(206)和懸架固定背板(207);測試車輪輪胎(201)、輪轂軸承(202)、轉向節(jié)(203)、阻尼器及彈簧(204)、轉向拉桿(205)和控制臂(206)按照真車的裝配方式進行裝配;控制臂(206)和阻尼器及彈簧(204)分別固定到懸架固定背板(207);懸架固定背板(207)固定到臺車車體(101)。在本發(fā)明進一步優(yōu)選的方面,所述的輪轂軸承(202)、轉向節(jié)(203)、阻尼器及彈簧(204)、轉向拉桿(205)和控制臂(206)是待測車輪輪胎(201)真車裝配配套的部件。在本發(fā)明的另一個方面,還提供了一種用于車輪模擬實況沖擊試驗的系統(tǒng),所述的系統(tǒng)包括前文所述的用于車輪模擬實況沖擊試驗的車輛、路面(3)、高頻照明設施(4)、標準障礙物塊(5)、高速攝像機(6)、牽引電機及鋼纜(7);牽引電機及鋼纜(7)的牽引電機固定到路面(3)的第一端并且與鋼纜的第一端固定,鋼纜的另一端固定到車輪模擬實況沖擊試驗的車輛的牽引掛鉤適配機構(104);前文所述的用于車輪模擬實況沖擊試驗的車輛位于路面(3)的第一端;標準障礙物塊(5)固定到路面(3)的第二端;高速攝像機(6)安裝到路面(3)側面,標準障礙物塊(5)上方;高頻照明設施(4)安裝到標準障礙物塊(5)的上方。在本發(fā)明的另一個方面,還提供了使用前文所述的用于車輪模擬實況沖擊試驗的系統(tǒng)來進行車輪模擬實況沖擊試驗的方法,其包括步驟:(A)將待測車輪輪胎(201)所對應的真車的裝配條件下的輪轂軸承(202)、轉向節(jié)(203)、阻尼器及彈簧(204)、轉向拉桿(205)和控制臂(206)組裝到實車車輪及懸架系統(tǒng)(2),并且通過懸架固定背板(207)固定到臺車車體(101);(B)按照待測車輪輪胎(201)所對應的真車的車重,在臺車車體(101)前部、中部和后部固定砝碼,構成砝碼及固定裝置(102);(C)對安裝好的用于車輪模擬實況沖擊試驗的車輛進行前輪定位校正,以保證其在牽引電機及鋼纜(7)的驅動下沿著直線運動;(D)將安裝好的用于車輪模擬實況沖擊試驗的車輛移動到路面(3)的第一端,并且固定到牽引電機及鋼纜(7);(E)在路面(3)設置標準障礙物塊(5);(F)開啟高頻照明設施(4)和高速攝像機(6);(G)通過牽引電機及鋼纜(7)牽引用于車輪模擬實況沖擊試驗的車輛;(H)車輪通過障礙物塊時,高速攝像機錄像,然后減速停車;(I)檢查車輪變形情況。在本發(fā)明一個具體的方面,在步驟(F)中,牽引使得用于車輪模擬實況沖擊試驗的車輛速度為40-80km/h。在本發(fā)明一個具體的方面,牽引使得用于車輪模擬實況沖擊試驗的車輛速度為64kM/h,所使用的輪胎為205/55R16型號輪胎,輪胎的胎壓為200kPa,滿載前軸重為900kg,后軸重820kg。本發(fā)明的用于車輪模擬實況沖擊試驗的車輛及系統(tǒng)的優(yōu)點在于,通過使用通配型的碰撞臺車,使得可以使用一套設備來滿足多種車輪的測試需求,從而避免針對每一款車輪使用相應的真車來進行試驗。這使得試驗成本大為降低,同時還確保了試驗狀態(tài)接近真車狀態(tài),能較好地模擬真車遇見障礙物的過程中的表現(xiàn)。附圖說明以下,結合附圖來詳細說明本發(fā)明的實施方案,其中:圖1是本發(fā)明的實施例1的用于車輪模擬實況沖擊試驗的系統(tǒng)的組成示意圖;圖2是本發(fā)明的實施例1的用于車輪模擬實況沖擊試驗的系統(tǒng)的俯視圖;圖3是本發(fā)明的實施例1的碰撞臺車的側視圖;圖4是本發(fā)明的實施例1的碰撞臺車的后視圖;圖5是本發(fā)明的實施例1的碰撞臺車的俯視圖;圖6是本發(fā)明的實施例1的碰撞臺車的立體圖;圖7是本發(fā)明的實施例1的碰撞臺車的立體組裝狀態(tài)圖;圖8是本發(fā)明的實施例1的測試的實車車輪及懸架系統(tǒng)(2)的結構示意圖;圖9是本發(fā)明的實施例1的測試的實車車輪及懸架系統(tǒng)(2)的裝配示意圖;圖10是本發(fā)明的實施例2的凸起障礙物的結構示意圖;圖11是本發(fā)明的實施例2的凹陷障礙物的結構示意圖;圖中:1-碰撞車輛總成、2-測試的實車車輪及懸架系統(tǒng)、3-路面、4-高頻照明設施、5-標準障礙物塊、6-高速攝像機、7-牽引電機及鋼纜、101-臺車車體、102-砝碼及固定裝置、103-后輪及輪軸總成、104-牽引掛鉤適配機構、201-測試車輪輪胎、202-輪轂軸承、203-轉向節(jié)、204-阻尼器及彈簧、205-轉向拉桿、206-控制臂、207-懸架固定背板、1001-凸起障礙物塊、1002-三軸力傳感器、1003-傳感器底座、1005-凸起障礙物塊的槽溝、1101-凹陷障礙物塊、1102-三軸力傳感器、1103-傳感器底座和1105-凹陷障礙物塊的槽溝。具體實施方式實施例1:用于車輪模擬實況沖擊試驗的車輛和系統(tǒng)在本實施例中,圖1中各系統(tǒng)單元組成了車輪和懸架系統(tǒng)的實況沖擊試驗的設備,主要由碰撞車輛總成(1)、測試的實車車輪及懸架系統(tǒng)(2)、標準50m~200m跑道(3)、高頻照明設施(4)、標準障礙物塊(5)、高速攝像機(6)、牽引電機及鋼纜(7)組成。碰撞臺車、車輪及懸架系統(tǒng)的總成示意圖由臺車車體(101)、砝碼及固定裝置(102)、后輪及輪軸總成(103)、牽引掛鉤適配機構(104)和車輪懸架總成(2)構成。車體(101)由方管鋼材焊接而成,底部鋪設有鋼板,鋼板上布置了6個用于固定砝碼固定桿的孔。實際測試時,通過調整每一個砝碼固定桿上的砝碼數(shù)量,實現(xiàn)對整車前輪負重和后輪負重,以及整車重心位置的精確控制調整。在車體的底部,設有牽引掛鉤適配機構(104)。砝碼及固定裝置(102)由砝碼塊、固定桿、鎖定螺母三部分組成。其中單塊的砝碼為直徑400mm,厚度50mm的圓柱體,中間有直徑60mm的通孔。固定桿長度為500mm,M48的螺紋桿,底端通過螺紋固定在臺車底部車體上。鎖定螺母為自制的M48外六方螺母。后輪及輪軸總成(103)由后車輪、輪軸總結兩部分組成,通過螺栓緊固在車體上。車輪和輪胎可任意選用(因測試主要是評估前輪,而后輪只起協(xié)助行駛的作用),輪軸為自制。車輪和懸架系統(tǒng)總成。由測試車輪輪胎(201)、輪轂軸承(202)、轉向節(jié)(203)、阻尼器及彈簧(204)、轉向拉桿(205)、控制臂(206)、懸架固定背板(207)組成。輪轂軸承(202)、轉向節(jié)(203)、阻尼器及彈簧(204)、轉向拉桿(205)、控制臂(206)均為2015款大眾高爾夫1.4T車的原車配件,購自本地汽配城。具體的連接方式為:轉向節(jié)(203)與阻尼器及彈簧(204)、轉向拉桿(205)、控制臂(206)、懸架固定背板(207)按實際裝車的裝配關系組成懸架系統(tǒng),將輪轂軸承安裝在轉向節(jié)上,安裝方式等同與在原車上的裝配關系。將測試車輪和裝車用原裝輪胎組織到一起,充氣至胎壓200kPa后,通過螺栓固定在輪轂軸承上,等同于車輛上的裝配。實施例2:車輪模擬實況沖擊試驗本實施例按照以下的步驟來進行:1.確定試驗需求。對2015款大眾高爾夫1.4T車型左前位置車輪進行64km/h下模擬實況沖擊路面凸起障礙物標準塊試驗。2.確定試驗參數(shù)。沖擊速度=64kM/h;輪胎=205/55R16;胎壓=200kPa;滿載前軸重為900kg,后軸重820kg。3.準備懸架總成。在市場上(汽配城)采購高爾夫車型的輪轂軸承、轉向節(jié)、阻尼器及螺旋彈簧、轉向拉桿、控制臂等懸架零部件。按原車裝配參數(shù)設計制成懸架固定背板。將其以等效于原車懸架裝配的方式組成試驗臺車用懸架系統(tǒng)。4.懸架與臺車車體裝配。用螺釘將組建好的懸架系統(tǒng)通過背板上的螺孔固定在臺車車體上。5.取全新的測試車輪樣品,裝胎,充氣并做動平衡。用等同于車輛上的安裝方式將車輪輪胎總成安裝到懸架輪轂軸承上。6.對安裝好前輪和懸架的試驗臺車總成進行前輪定位校正,以保障其能按直線行駛。7.將臺車移動至發(fā)車區(qū),連接牽引掛鉤。8.設定好燈光和攝像系統(tǒng)。保證車輛在碰撞的時刻他們能正常工作。9.牽引系統(tǒng)通過掛鉤牽引車輛加速至64km/h。10.車輪通過障礙物塊時,高速攝像機錄像,然后減速停車。11.檢查車輪變形情況。其中,固定障礙物包括凹陷障礙物或者凸起障礙物。凹陷障礙物由凹陷障礙物塊(1101)、三軸力傳感器(1102)、傳感器底座(1103)和凹陷障礙物塊的槽溝(1105)構成,其特征在于:所述的凹陷障礙物塊的槽溝(1105)位于路面(1104)上;傳感器底座(1103)安放在凹陷障礙物塊的槽溝(1105)的底部;三軸力傳感器(1102)的一端安裝在傳感器底座(1103)的上表面,另一端安裝到凹陷障礙物塊(1101)的下表面;所述的凹陷障礙物塊(1101)沿凹陷障礙物塊的槽溝(1105)的長度方向的橫截面具有梯形的凹陷;并且,所述的凹陷障礙物塊(1101)設置為當安裝完畢后,凹陷的梯形的底邊和路面(1104)平齊。所述的凹陷障礙物塊(1101)沿凹陷障礙物塊的槽溝(1105)的長度方向的橫截面的等腰梯形部分的長底邊長度為1400mm,短底邊長度為100mm,梯形的高度為120mm,凹陷障礙物塊(1101)的頂部寬度為1600mm。在道路上設置的凹坑中,將障礙物、三軸力傳感器、傳感器底板按上述連接方式固定,用一定速度的車輛去通過障礙物,設置在障礙物底下的四個三軸力學傳感器連接高速數(shù)字采集儀,能得到?jīng)_擊過程中的力學曲線,通過對四個傳感器進行數(shù)學耦合,計算出障礙物的受的合力,即為沖擊力。凸起障礙物由凸起障礙物塊(1001)、三軸力傳感器(1002)、傳感器底座(1003)和凸起障礙物塊的槽溝(1005)構成,其特征在于:所述的凸起障礙物塊的槽溝(1005)位于路面(1004)上;傳感器底座(1003)安放在凸起障礙物塊的槽溝(1005)的底部;三軸力傳感器(2)的一端安裝在傳感器底座(1003)的上表面,另一端安裝到凸起障礙物塊(1001)的下表面;所述的凸起障礙物塊(1001)沿凸起障礙物塊的槽溝(1005)的長度方向的橫截面在上部為梯形;并且,所述的凸起障礙物塊(1001)設置為當安裝完畢后,梯形的底邊和路面平齊。所述的凸起障礙物塊(1001)沿凸起障礙物塊的槽溝(1005)的長度方向的橫截面的等腰梯形部分的長底邊長度為430mm,短底邊長度為100mm,梯形的高度為80mm。所述的凸起障礙物塊(1001)沿凸起障礙物塊的槽溝(1005)的長度方向的橫截面下部為矩形,矩形的尺寸為430×70mm。在道路上設置的凹坑中,將障礙物、三軸力傳感器、傳感器底板按上述連接方式固定。用一定速度的車輛去通過障礙物,設置在障礙物底下的四個三軸力傳感器連接高速數(shù)字采集儀,能得到?jīng)_擊過程中的力學曲線,通過對四個傳感器進行數(shù)學耦合,計算出障礙物的受的合力。對比例1:車輪的臺架試驗選擇與實施例2中同款車輪一只,裝胎205/55R16充氣,按QC/T991-2015行業(yè)標準規(guī)定的試驗方法,對車輪進行90°沖擊試驗,能量選擇為E2級。測得車輪受最大沖擊力是=56.1KN,輪緣變形量是8.63mm。對比例2:車輪的真車試驗對2015款大眾高爾夫1.4T車型實車的左前位置車輪進行80km/h下模擬實況沖擊路面凸起障礙物標準塊試驗。為了保證安全提前在車身內部安裝防翻滾架,試車駕駛員穿安全服佩戴頭盔。測試路面上放置凸起標準障礙物塊。車輛前軸重調整至900kg,后軸重820kg。駕駛車輛在64km/h速度下,使左前輪通過標準障礙物塊,測得沖擊力為37.7kN。沖擊完成后卸下車輪,發(fā)現(xiàn)車輪輪輞變形量為1.1mm。實施例3:車輪變形試驗結果實施例2和對比例1~2選擇了同樣的標準障礙物塊具有可比性。將實施例2、對比例1~2中測得的試驗數(shù)據(jù)放入表1進行比較,發(fā)現(xiàn)模擬實車沖擊系統(tǒng)(實施例2)較臺架試驗(對比例1)更加接近實際車輛行駛中撞擊結果(對比例2)。表1實施例2與對比例1~2的試驗結果試驗組測得沖擊力(KN)測得變形量(mm)實施例236.01.5對比例156.18.63對比例237.71.1從試驗結果可以看出,臺架試驗與真車試驗存在著很大的差異,主要是因為臺架試驗時無法把車輛懸架安裝上,沖擊力只能全部由車輪來吸收。而實施例2用等效車輛裝配的方式把車輪及懸架安裝在一臺模擬車輛上,進行沖擊試驗的效果已非常的接近對比例2的實際車輛沖擊情況。當前第1頁1 2 3