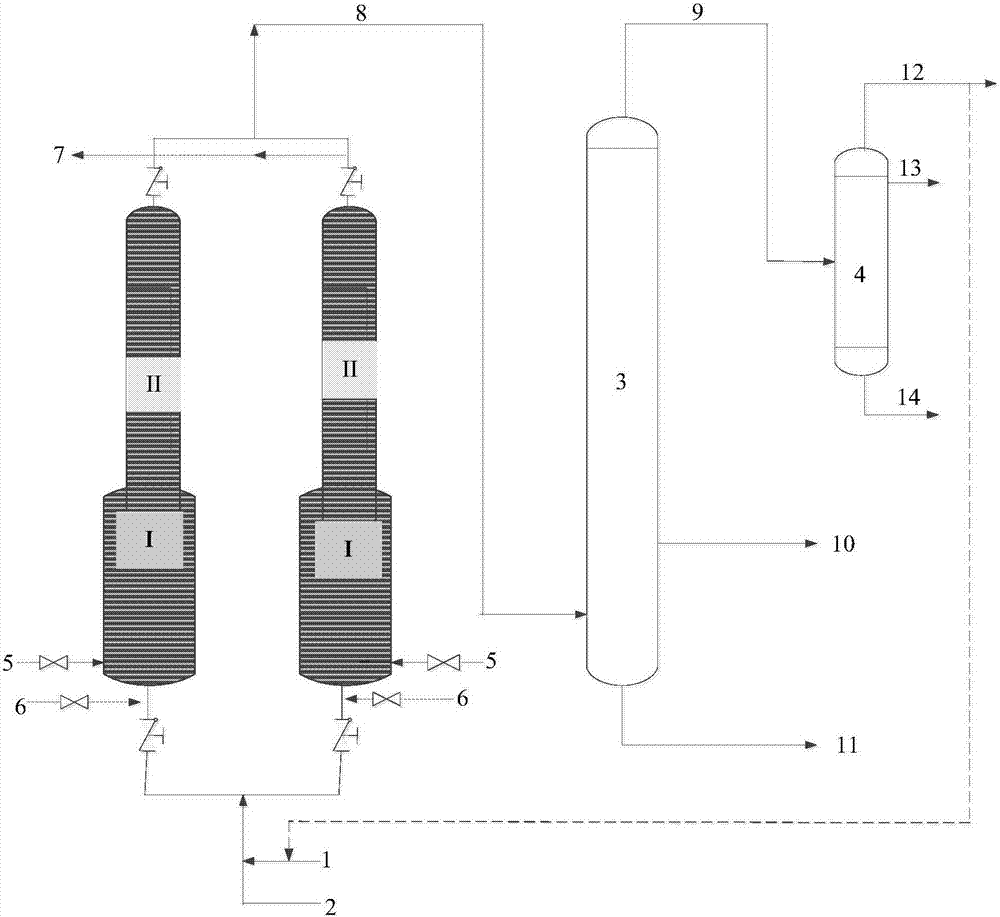
本發(fā)明涉及一種劣質原料油的加工方法和系統(tǒng)。
背景技術:
:隨著石油資源短缺和對高品質汽油、柴油以及低碳烯烴的需求日益增加,劣質原料油如煤液化油、油砂油以及劣質、重質石油等油品的加工技術越來越受到重視。劣質原料油、煤液化油、油砂油等,類似天然石油,但又比天然石油含有更多的不飽和烴,并含氮、硫和氧等非烴類有機化合物,不僅影響其二次加工利用,而且還影響產(chǎn)品汽油、柴油的顏色及安定性,硫、氮含量高。目前劣質原料油除了少量生產(chǎn)化學藥品外,大部分未經(jīng)二次加工而直接作為輕質燃料油銷售,因此有必要開發(fā)更多高效利用劣質原料油的技術。由于劣質原料油中氮、硫、氧等雜原子化合物含量較高,尤其是氮質量分數(shù)一般在1%~3%,不能直接作為催化裂化原料進行劣質原料油的輕質化,主要是因為氮化物特別是堿性氮化物在催化裂化反應過程中能和催化劑酸性中心作用而降低催化劑活性和選擇性,表現(xiàn)在產(chǎn)物分布上是生焦率增加,油漿增加,輕質油收率下降。arco公司指出,大多數(shù)催化裂化裝置可耐2000μg/g總氮和1000μg/g堿氮。通過采用高酸中心密度、稀土分子篩的抗氮裂化催化劑如rhz-200、lc-7、ccc-1、rhz-300,或者用酸性添加物作為氮的捕捉劑,催化裂化裝置也只能加工氮含量3000μg/g以下的進料。另外,劣質原料油膠質和烯烴含量較高。在催化裂化過程中,三分之一的膠質會生成焦炭,而烯烴較活潑,二者容易吸附在催化劑上覆蓋活性中心。雖然膠質氣化需要較高的溫度,但是反應溫度越高越容易生成焦炭。綜合以上因素,劣質原料油一般需要先加氫處理改質,以脫除氧、氮、硫等雜質,然后在煉廠按常規(guī)的煉油加工工藝加工成各種油品。美國專利us4342641公開了一種劣質原料油加工方法,先將全餾分劣質原料油進行加氫處理,得到的小于249℃的餾分直接作為噴氣燃料,得到的大于249℃的餾分再進行加氫裂化,以生產(chǎn)噴氣燃料;其中加氫處理分兩步進行,先用ni-mo含量低的催化劑進行預精制,再用ni-mo含量高的催化劑進行進一步精制。該方法加氫過程多,氫耗高,操作費用高,建設投資高。中國專利cn1067089a、cn102453546a與cn102465036a均公開了一種劣質原料油加氫分餾,加氫重油再催化裂解的加工方法,如中國專利cn1067089a所述,劣質原料油先經(jīng)過加氫處理得到加氫生成油,加氫生成油分離為加氫重油和輕質產(chǎn)品,加氫重油經(jīng)催化裂化后得到干氣、液化氣、汽油、柴油和催化重油,柴油和重循環(huán)油可返回加氫處理步驟;只是中國專利cn102465036a的劣質原料油加氫重油采用兩個提升管反應器進行催化裂解反應,而cn102453546a所得的加氫生成油與可選的減壓瓦斯油一起進入催化裂解裝置??傊?,劣質原料油進行加氫精制,精制得到的重油作為現(xiàn)有催化裂化技術的原料的加工方法,均可將劣質原料油轉化成輕質產(chǎn)品。劣質原料油加氫處理具有操作簡單、目的產(chǎn)品收率高、產(chǎn)品質量好且無三廢排放等優(yōu)點,為21世紀環(huán)境友好加工工藝。但是,劣質原料油中非烴化合物雜質在加氫處理中是有害物質,是所要除去或轉化的對象,但它本身卻是有用的化工原料,因此應考慮提取和利用;另外,如果劣質原料油氧含量較高,則影響加氫催化劑的壽命與效率。加氫技術目前僅有澳大利亞spp公司達到工業(yè)試驗階段,通過加氫精制生產(chǎn)超低硫輕質燃料油。非加氫處理主要是采用酸堿精制,如專利中國專利cn101967389a,酸堿精制不僅會產(chǎn)生大量難以處理的酸渣,污染環(huán)境,而且精制油收率低;雖然近年有些研究人員探索用單溶劑或多溶劑萃取精制法,如專利中國專利 cncn1746265a,但仍存在溶劑耗量較大,能耗高等問題。隨著環(huán)境保護要求的提高,國內(nèi)外對輕質燃料油燃燒尾氣的排放標準不斷提高,對車用輕質燃料油的硫、氮和芳烴含量的限制更低,所以采用非加氫處理法很難達到要求。因此,為了高效利用劣質原料油資源,滿足日益增長的輕質燃料油的需求,有必要開發(fā)一種將劣質原料油高效轉化為大量輕質且清潔的輕質燃料油的方法。技術實現(xiàn)要素:本發(fā)明的目的是提供一種劣質原料油的加工方法和系統(tǒng),在該系統(tǒng)上采用該方法進行加工劣質原料油能夠大幅度提高劣質原料油轉化率并降低干氣和焦炭產(chǎn)率,從而實現(xiàn)劣質原料油的清潔和高效利用。為了實現(xiàn)上述目的,本發(fā)明提供一種劣質原料油的加工方法,該方法包括:a、將含氫氣體與劣質原料油送入固定床反應器的臨氫吸附區(qū)中與吸附劑接觸并進行臨氫吸附反應,得到臨氫吸附產(chǎn)物;b、將步驟a中所得臨氫吸附產(chǎn)物送入所述固定床反應器的裂化區(qū)中與催化裂化催化劑接觸并進行催化裂化反應,得到催化裂化油氣。優(yōu)選地,該方法還包括:將步驟b中所得催化裂化油氣送入分餾裝置進行分餾處理,得到包括富氣的催化裂化產(chǎn)物;將所得富氣不經(jīng)過富氣壓縮機直接送入吸收穩(wěn)定裝置進行吸收穩(wěn)定處理。優(yōu)選地,所述含氫氣體包括氫氣和/或干氣,所述劣質原料油為選自頁巖油、煤液化油、油砂油、焦化蠟油、渣油、加氫渣油和脫瀝青油中的至少一種。優(yōu)選地,所述吸附劑與所述催化裂化催化劑為相同或者不同,并且各自獨立地包括1-50重量%的沸石、5-99重量%的無機氧化物和0-70重量%的粘 土。優(yōu)選地,所述沸石包括中孔沸石和/或大孔沸石,所述中孔沸石為選自zsm-5沸石、zsm-11沸石、zsm-12沸石、zsm-23沸石、zsm-35沸石、zsm-38沸石、zsm-48沸石和zrp沸石中的至少一種,所述大孔沸石為選自稀土y型沸石、稀土氫y沸石、高硅y型沸石和超穩(wěn)y型沸石中的至少一種;所述無機氧化物為氧化硅和/或氧化鋁;所述粘土為選自二氧化硅、高嶺土、多水高嶺土、蒙脫土、硅藻土、埃洛石、皂石、累托土、海泡石、凹凸棒石、水滑石和膨潤土中的至少一種。優(yōu)選地,所述臨氫吸附反應的條件包括:溫度為200-450℃,壓力為0.5-5.0兆帕,吸附時間為5-360秒,劑油重量比為(0.5-5.0):1,氫油體積比為100-1000;所述催化裂化反應的條件包括:溫度為460-540℃,壓力為0.5-5.0兆帕,油氣停留時間為10-600秒,劑油重量比為(5-10):1。優(yōu)選地,該方法還包括:將冷卻介質送入所述臨氫吸附區(qū)中進行控溫;所述冷卻介質為選自冷氫、水、汽油、柴油、回煉油和熔鹽中的至少一種。本發(fā)明還提供一種劣質原料油的加工系統(tǒng),其中,該加工系統(tǒng)包括設置有臨氫吸附區(qū)和裂化區(qū)的固定床反應器;所述臨氫吸附區(qū)與裂化區(qū)串聯(lián)并且流體連通,所述固定床反應器的臨氫吸附區(qū)一端設置有含氫氣體入口和劣質原料油入口,所述固定床反應器的裂化區(qū)一端設置有催化裂化油氣出口。優(yōu)選地,所述加工系統(tǒng)還包括分餾裝置和吸收穩(wěn)定裝置,所述分餾裝置的油氣入口與所述催化裂化油氣出口流體連通,所述分餾裝置的富氣出口與所述吸收穩(wěn)定裝置的富氣入口流體連通。優(yōu)選地,所述臨氫吸附區(qū)設置在所述裂化區(qū)的上方或所述裂化區(qū)設置在所述臨氫吸附區(qū)的上方。優(yōu)選地,所述加工系統(tǒng)包括至少兩個并列設置且可切換的固定床反應器。優(yōu)選地,所述固定床反應器為等徑固定床反應器或變徑固定床反應器,和/或所述固定床反應器為徑向固定床反應器、軸向固定床反應器或列管式固定床反應器。優(yōu)選地,所述固定床反應器為變徑固定床反應器,所述變徑固定床反應器中臨氫吸附區(qū)的直徑為裂化區(qū)的直徑的0.5-3.0倍,臨氫吸附區(qū)的長度為裂化區(qū)的長度的5-30%。優(yōu)選地,所述固定床反應器設置有冷卻介質入口,所述冷卻介質入口與所述臨氫吸附區(qū)直接流體連通或與設置在所述臨氫吸附區(qū)中的取熱盤管流體連通。本發(fā)明與現(xiàn)有技術相比具有下列技術效果:(1)劣質原料油可以不經(jīng)精制處理而直接進行加工處理,劣質原料油的加工流程短,氫耗低,并可實現(xiàn)長周期連續(xù)化生產(chǎn);(2)本發(fā)明采用“一器兩反”進行加工劣質原料油,即在一個反應器內(nèi)裝入相同或不同的劣質原料油吸附劑與催化裂化催化劑,這兩種催化劑在同一反應氛圍中協(xié)同完成劣質原料油吸附硫化物、堿性氮化物、重金屬和膠質等雜質以及劣質原料油催化裂化的功能,繼而可以在同一再生氛圍中同時恢復活性,這兩種催化劑也可以是一種催化劑,如催化裂化催化劑;(3)劣質原料油先吸附脫除硫化物、堿性氮化物、重金屬和膠質等極性物質再催化裂化,劣質原料油轉化率高,干氣與焦炭產(chǎn)率低,減少了裝置生焦,液體產(chǎn)品(液化氣+汽油+柴油)產(chǎn)率高;(4)劣質原料油在臨氫氛圍下進行吸附,更有利于吸附劑對劣質原料油中含硫、含氮和含氧化合物的吸附脫除,吸附劑與劣質原料油重量比降低,吸附時間短,液體產(chǎn)品硫、氮含量低且品質好;(5)加工系統(tǒng)在臨氫帶壓下操作,相應提高了進入吸收穩(wěn)定裝置的富氣的壓力,省卻了常規(guī)fcc工藝的富氣壓縮機,裝置能耗降低;(6)固定床反應器可以采用多臺反應器進行交替進行反應與再生,操作簡單。本發(fā)明的其他特征和優(yōu)點將在隨后的具體實施方式部分予以詳細說明。附圖說明附圖是用來提供對本發(fā)明的進一步理解,并且構成說明書的一部分,與下面的具體實施方式一起用于解釋本發(fā)明,但并不構成對本發(fā)明的限制。在附圖中:圖1是包括本發(fā)明加工方法的一種具體實施方式的流程示意圖,也是包括本發(fā)明加工系統(tǒng)的一種具體實施方式的結構示意圖;圖2是包括本發(fā)明加工方法的另一種具體實施方式的流程示意圖,也是包括本發(fā)明加工系統(tǒng)的另一種具體實施方式的結構示意圖。附圖標記說明i臨氫吸附區(qū)ii裂化區(qū)1含氫氣體2劣質原料油3分餾裝置4吸收穩(wěn)定裝置5冷卻介質6再生氣體7煙氣8催化裂化油氣9富氣10柴油11油漿12干氣13液化氣14汽油具體實施方式以下結合附圖對本發(fā)明的具體實施方式進行詳細說明。應當理解的是,此處所描述的具體實施方式僅用于說明和解釋本發(fā)明,并不用于限制本發(fā)明。本發(fā)明提供一種劣質原料油的加工方法,該方法包括:a、將含氫氣體與劣質原料油送入固定床反應器的臨氫吸附區(qū)i中與吸附劑接觸并進行臨氫 吸附反應,得到臨氫吸附產(chǎn)物;b、將步驟a中所得臨氫吸附產(chǎn)物送入所述固定床反應器的裂化區(qū)ii中與催化裂化催化劑接觸并進行催化裂化反應,得到催化裂化油氣。本發(fā)明的發(fā)明人經(jīng)過多年的研究意外地發(fā)現(xiàn),劣質原料油中的含氮化合物、含硫化合物和含氧化合物等可以通過吸附脫除,而催化裂化催化劑本身也可以作為吸附劑;特別是在臨氫氛圍下,吸附時間短,更有利于吸附劑對劣質原料油中含硫化合物、含氮化合物、含氧化合物及金屬的吸附脫除,使劣質原料油的轉化率高,液體產(chǎn)品硫、氮含量低,品質好。根據(jù)本發(fā)明,該方法還可以包括:將步驟b中所得催化裂化油氣送入分餾裝置3進行分餾處理,得到包括富氣的催化裂化產(chǎn)物;將所得富氣不經(jīng)過富氣壓縮機直接送入吸收穩(wěn)定裝置4進行吸收穩(wěn)定處理?,F(xiàn)有常規(guī)催化裂化裝置反應和分餾系統(tǒng)在0.1-0.25mpa壓力下進行操作,而吸收穩(wěn)定裝置需在1.1mpa以上的壓力下進行操作,因此常規(guī)催化裂化裝置必須設置富氣壓縮機對來自分餾裝置的富氣進行壓縮提壓,本發(fā)明反應系統(tǒng)在臨氫帶壓(0.5-5.0mpa)下操作,相應提高了富氣進入吸收穩(wěn)定裝置的壓力,可省卻常規(guī)fcc工藝中的富氣壓縮機,從而降低裝置能耗和成本投入。分餾裝置得到富氣、柴油和油漿,分餾裝置(分餾塔)頂部的富氣可以不經(jīng)富氣壓縮機壓縮直接進入吸收穩(wěn)定裝置進一步進行產(chǎn)品分離,得到干氣、液化氣和汽油等。汽油或柴油等餾程可以按實際需要進行調整,不僅限于全餾程汽油或柴油。根據(jù)本發(fā)明,含氫氣體是本領域技術人員所熟知的,既可以作為氫源使用,也可以作為劣質原料油輸送氣體使用,其組成本發(fā)明沒有特別限制,例如,所述含氫氣體可以包括氫氣和/或干氣,也可以包括氮氣和水蒸氣等非含氫介質,非含氫介質不含有或含有微量的氧氣,氧氣在含氫氣體中的體積分數(shù)不大于1%;劣質原料油為本領域技術人員所公知,可以為選自頁巖油、 煤液化油、油砂油、焦化蠟油、渣油、加氫渣油和脫瀝青油中的至少一種,相對密度可以為0.8-1.1,可以富含烷烴、芳烴和部分烯烴,碳氫元素重量比可以為7-9,并且氮、硫和氧等非烴類有機化合物含量較高,氮含量可以為0.5%-5%,硫含量可以為0.5%-10%,氧含量可以為0.5%-20%。本發(fā)明中,所述劣質原料油可以先經(jīng)過預熱后送入反應器中進行反應,所述預熱的溫度可以為150-400℃,優(yōu)選為200-350℃。根據(jù)本發(fā)明,吸附劑和催化裂化催化劑是本領域技術人員所熟知的,所述吸附劑與所述催化裂化催化劑可以為相同或者不同,所述催化裂化催化劑的微反應活性可以為40-70,優(yōu)選為45-65。催化裂化催化劑的組成可以包括:沸石、無機氧化物和任選的粘土;吸附劑和催化裂化催化劑具體組成與裝填量,既取決于劣質原料油氮含量和脫氮要求,又取決于催化裂化反應條件,例如,所述吸附劑和催化裂化催化劑可以各自獨立地包括1-50重量%的沸石、5-99重量%的無機氧化物和0-70重量%的粘土。其中,沸石可以為中孔沸石和/或任選的大孔沸石,中孔沸石可以占沸石總重量的80-100重%,優(yōu)選占90重%-100重%;大孔沸石可以占沸石總重量的0-20重%,優(yōu)選占0重%-10重%。所述中孔沸石可以為zsm系列沸石和/或zrp沸石,優(yōu)選自zsm-5沸石、zsm-11沸石、zsm-12沸石、zsm-23沸石、zsm-35沸石、zsm-38沸石、zsm-48沸石和zrp沸石中的至少一種,也可以包括其它類似結構的沸石。有關zsm-5沸石更為詳盡的描述可以參見美國專利us3,702,886,有關zrp沸石更為詳盡的描述可以參見美國專利us5,232,675。所述大孔沸石可以為y系列沸石,可以包括稀土y型沸石(rey)、稀土氫y沸石(rehy)、超穩(wěn)y型沸石(可以由不同方法得到)和高硅y型沸石中的至少一種。所述無機氧化物一般作為粘接劑,可以為氧化硅(sio2)和/或氧化鋁(al2o3),以干基重量計,無機氧化物中氧化硅可以占50重-90重%,氧化鋁可以占10重-50重%。所述粘土作為基質(即載體),可以為選 自二氧化硅、高嶺土、多水高嶺土、蒙脫土、硅藻土、埃洛石、皂石、累托土、海泡石、凹凸棒石、水滑石和膨潤土中的至少一種。優(yōu)選情況下,可以采用鐵、鈷、鎳等過渡金屬元素組分對上述大孔、中孔沸石、無機氧化物和粘土等進行改性。所述固定床反應器的臨氫吸附區(qū)的吸附劑與裂化區(qū)的催化裂化催化劑可以各自采取不同形狀,如球狀、條狀或三葉草狀的顆粒狀,或者網(wǎng)狀、蜂窩狀以及纖維狀;催化劑的平均粒徑與反應器直徑相關,以球狀為例,一般在2-8mm,優(yōu)選為3-6mm。根據(jù)本發(fā)明,臨氫吸附反應和催化裂化反應是本領域技術人員所熟知的,例如,所述臨氫吸附反應的條件可以包括:溫度為200-450℃,優(yōu)選為250-400℃,壓力為0.5-5.0兆帕,優(yōu)選為1.0-4.0兆帕,吸附時間為5-360秒,優(yōu)選為10-240秒,劑油重量比為(0.5-5.0):1,優(yōu)選為(1-4):1,氫油體積比為100-1000,優(yōu)選為300-800;所述催化裂化反應的條件可以包括:溫度為460-540℃,優(yōu)選為480-530℃,壓力為0.5-5.0兆帕,優(yōu)選為1.0-4.0兆帕,油氣停留時間為10-600秒,優(yōu)選為20-600秒,劑油重量比為(5-10):1,優(yōu)選為(5.5-8):1。根據(jù)本發(fā)明,臨氫吸附區(qū)i與裂化區(qū)ii的劃分可以在反應器底部或頂部注入冷卻介質,通過引入冷卻介質,將固定床反應器分為臨氫吸附區(qū)i與裂化區(qū)ii,將臨氫吸附和催化裂化工藝有機結合,從而實現(xiàn)劣質原料油臨氫吸附和催化裂化,并且提高劣質原料油轉化能力。因此該方法還可以包括:將冷卻介質送入所述臨氫吸附區(qū)i中進行控溫;所述冷卻介質可以為選自冷氫、水、汽油、柴油、回煉油和熔鹽中至少一種;冷卻介質可以直接注入反應器,或通過在反應器內(nèi)布置取熱盤管等使得催化劑與冷卻介質換熱,從而控制臨氫吸附區(qū)溫度。本發(fā)明還提供一種劣質原料油的加工系統(tǒng),其中,該加工系統(tǒng)包括設置有臨氫吸附區(qū)i和裂化區(qū)ii的固定床反應器;所述臨氫吸附區(qū)i與裂化區(qū)ii 串聯(lián)并且流體連通,所述固定床反應器的臨氫吸附區(qū)i一端設置有含氫氣體入口和劣質原料油入口,所述固定床反應器的裂化區(qū)ii一端設置有催化裂化油氣出口。根據(jù)本發(fā)明的一種具體實施方式,所述加工系統(tǒng)還可以包括分餾裝置3和吸收穩(wěn)定裝置4,所述分餾裝置3的油氣入口可以與所述催化裂化油氣出口流體連通,所述分餾裝置3的富氣出口可以與所述吸收穩(wěn)定裝置4的富氣入口流體連通?,F(xiàn)有常規(guī)催化裂化裝置反應和分餾裝置一般在0.1-0.25mpa壓力下進行操作,而吸收穩(wěn)定裝置需在1.1mpa以上的壓力下進行,因此常規(guī)催化裂化裝置必須設置富氣壓縮機對來自分餾裝置的富氣進行壓縮提壓,本發(fā)明加工系統(tǒng)在臨氫帶壓(0.5-5.0mpa)下操作,相應提高了富氣進入吸收穩(wěn)定裝置的壓力,可省卻常規(guī)fcc工藝中富氣壓縮機,從而降低裝置能耗。根據(jù)本發(fā)明的具體實施方式,所述臨氫吸附區(qū)i可以設置在所述裂化區(qū)ii的上方(如圖1所示)或所述裂化區(qū)ii可以設置在所述臨氫吸附區(qū)i的上方(如圖2所示)。所述劣質原料油進入固定床反應器的臨氫吸附區(qū)i,可以根據(jù)臨氫吸附區(qū)的設置,采用下進料也可以采用上進料;如果采用下進料,劣質原料油從固定床反應器底部進入臨氫吸附區(qū),隨著含氫氣體由下向上流動;如果劣質原料油采用上進料,劣質原料油隨著含氫氣體由上向下流動;劣質原料油進入臨氫吸附區(qū)i,先在具有氮化物吸附功能的吸附劑上吸附脫除其中堿性氮化物等雜質。例如,如圖2所示,在該具體實施方式中,固定床反應器采用下進料,且固定床反應器的下段設置為臨氫吸附區(qū)i,從而使臨氫吸附區(qū)i位于裂化區(qū)ii的下方。根據(jù)本發(fā)明,如圖1-2所示,為了方便固定床反應器中催化劑的再生,所述加工系統(tǒng)可以包括至少兩個并列設置且可切換的固定床反應器,可以并列聯(lián)接且在平行方向或垂直方向布置,所述固定床反應器中的一個反應器內(nèi) 催化劑失活時,將反應切換到其它反應器中進行,同時將催化劑失活的固定床反應器中的失活催化劑再生,待生催化劑經(jīng)氮氣或蒸汽汽提脫除其內(nèi)部吸附的油氣后升溫,與再生氣體接觸,實現(xiàn)再生;再生后的再生催化劑循環(huán)使用,從而實現(xiàn)連續(xù)生產(chǎn)。將催化劑失活的固定床反應器中的失活催化劑再生,在再生過程中,再生氣體可以為選自空氣、氧氣和含氧氣體中的至少一種,再生溫度可以為550-700℃,優(yōu)選為600-650℃。再生后的催化劑最好經(jīng)冷卻后再使用。根據(jù)本發(fā)明,固定床反應器是本領域技術人員所熟知的,例如可以為等徑固定床反應器或變徑固定床反應器,優(yōu)選為變徑固定床反應器,和/或所述固定床反應器可以為徑向固定床反應器、軸向固定床反應器或列管式固定床反應器,優(yōu)選為軸向列管式固定床反應器。如果固定床反應器臨氫吸附區(qū)i擴徑,則能夠強化劣質原料油中氮化物、膠質等的吸附脫除。一種具體實施方式,所述固定床反應器為變徑固定床反應器,所述變徑固定床反應器中臨氫吸附區(qū)i的直徑可以為裂化區(qū)ii的直徑的0.5-3.0倍,優(yōu)選為1.0-2.0倍,臨氫吸附區(qū)i的長度可以為裂化區(qū)ii的長度的5-30%,優(yōu)選為10-20%。所述臨氫吸附區(qū)和裂化區(qū)是指反應器內(nèi)能夠進行臨氫吸附反應和催化裂化反應的空間,并不包括反應器本身。根據(jù)本發(fā)明,臨氫吸附區(qū)i與裂化區(qū)ii的劃分可以在反應器底部或頂部注入冷卻介質,因此所述固定床反應器可以設置有冷卻介質入口,所述冷卻介質入口可以與所述臨氫吸附區(qū)i直接流體連通或可以與設置在所述臨氫吸附區(qū)i中的取熱盤管流體連通。當冷卻介質從固定床反應器底部注入時,則臨氫吸附區(qū)i位于固定床反應器下部,裂化區(qū)ii則位于固定床反應器上部;當冷卻介質從固定床反應器頂部注入時,則臨氫吸附區(qū)i位于固定床反應器上部,裂化區(qū)ii則位于固定床反應器下部。下面將通過具體實施方式來進一步說明本發(fā)明,但是本發(fā)明并不因此而 受到任何限制。例如圖1所示,加工系統(tǒng)包括平行放置的兩個并聯(lián)的固定床反應器,兩個并聯(lián)的固定床反應器中反應與再生交替進行,從而實現(xiàn)連續(xù)的劣質原料油加工。在兩個并聯(lián)的固定床反應器中,固定床反應器上段設置為臨氫吸附區(qū)i,并在臨氫吸附區(qū)i內(nèi)設置取熱盤管并采用熔鹽作為冷卻介質,以吸附脫除劣質原料油中的堿性氮化物、硫化物、含氧化合物、重金屬和膠質等雜質等,隨后劣質原料油下行進入裂化區(qū)ii進行催化裂化反應。其工藝流程如下:劣質原料油2進入固定床反應器的臨氫吸附區(qū)i上部,隨著含氫氣體1由上至下流動,在吸附劑上進行臨氫吸附反應,吸附脫除其中堿性氮化物、硫化物、含氧化合物、膠質和重金屬等雜質;臨氫吸附產(chǎn)物隨之下行進入裂化區(qū)ii,逐步接觸高溫高活性的催化裂化催化劑進行催化裂化反應;生成的油氣8進入分餾裝置3進行分餾處理得到柴油10、油漿11,分餾裝置塔頂富氣9不經(jīng)富氣壓縮機壓縮直接進入吸收穩(wěn)定裝置4進一步進行產(chǎn)品分離,得到干氣12、液化氣13和汽油14等產(chǎn)品,油漿11根據(jù)需要選擇回煉或不回煉,干氣12根據(jù)需要選擇部分循環(huán)回臨氫吸附區(qū)i作為含氫氣體。下面將通過實施例來進一步說明本發(fā)明,但是本發(fā)明并不因此而受到任何限制。實施例和對比例的產(chǎn)品檢測方法為:反應產(chǎn)物被n2帶入-10℃的液收瓶中進行氣液分離,氣體產(chǎn)物收集完成由agilent6890gc(tcd檢測器)在線分析組成;液體產(chǎn)物收集后離線稱重,分別進行模擬蒸餾和汽油單體烴分析(采用ripp81-90試驗方法進行測試),汽油和柴油的餾分切割點分別為221℃和343℃;生焦催化劑卸出后在multiea2000碳硫分析儀上進行焦炭分析(采用ripp106-90試驗方法進行測試),所有產(chǎn)物質量加和計算物料平衡,臨氫吸附產(chǎn)物和汽油中硫氮含量采用ripp62-90試驗方法和ripp63-90試驗方法進行測定。金屬含量采用ripp124-90試驗方法進行測定。本發(fā)明的ripp試驗方法選自《石油化工分析方法(ripp試驗方法)》,楊翠定等編,科學出版社,1990。實施例和對比例中所用的劣質原料油為頁巖油(a)與渣油(b),其性質如表1所示。實施例和對比例中所用的催化劑制備方法如下所示:1)、將20gnh4cl溶于1000g水中,向此溶液中加入100g(干基)晶化產(chǎn)品dasy沸石(齊魯石化公司催化劑廠生產(chǎn),晶胞大小為2.445-2.448nm,稀土含量(以re2o3計)=2.0重%),在90℃交換0.5h后,過濾得濾餅;將4.0gh3po4(濃度85%)與5.4gco(no3)2·6h2o溶于90g水中,與濾餅混合浸漬后烘干,接著在550℃溫度下焙燒處理2小時得到含磷和鈷的大孔沸石,化學元素組成為:0.1na2o·5.1al2o3·2.4p2o5·1.5co2o3·3.8re2o3·88.1sio2。2)、用250kg脫陽離子水將75.4kg多水高嶺土(蘇州瓷土公司工業(yè)產(chǎn)品,固含量71.6m%)打漿,再加入54.8kg擬薄水鋁石(山東鋁廠工業(yè)產(chǎn)品,固含量63m%),用鹽酸將其ph調至2-4,攪拌均勻,在60-70℃下靜置老化1小時,保持ph為2-4,將溫度降至60℃以下,加入41.5kg鋁溶膠(齊魯石化公司催化劑廠產(chǎn)品,al2o3含量為21.7m%),攪拌40分鐘,得到混合漿液。3)、將步驟1)制備的含磷和鈷的大孔沸石(干基為33.8kg)以及mfi結構中孔zrp-1沸石(齊魯石化公司催化劑廠工業(yè)產(chǎn)品,sio2/al2o3=30,干基為3.0kg)加入到步驟2)得到的混合漿液中,攪拌均勻,并加入適量特種粘合劑、結構助劑及造孔劑,混合后放于粘合機中,加入適量水,充分攪拌均勻,在空氣中放置4小時,用滾球機滾球成形放置24小時后,于干燥箱中120℃烘干3小時后,用磷酸二氫銨溶液(磷含量為1m%)洗滌,洗去游離na+,再次干燥即得催化劑記為cat-1(平均粒徑在4~6mm)。該催化劑的組成為4.1重%mfi結構中孔沸石、20.6重%含磷和鈷的dasy沸石、 29.4重%擬薄水鋁石、5.5重%鋁溶膠和余量高嶺土。其性質列于表2。實施例1該實施例按照圖1的流程進行試驗,頁巖油a作為催化裂化的原料,在小型連續(xù)再生固定床反應器上進行試驗,并聯(lián)兩個反應器平行放置,反應器上部擴徑(臨氫吸附區(qū)i的內(nèi)徑為0.03米,長度為0.15米,裂化區(qū)ii的直徑為0.02米,長度為2.30米)并設置取熱盤管采用熔鹽作為冷卻介質冷卻吸附劑;采用cat-1催化劑同時作為吸附劑和催化裂化催化劑,cat-1平衡劑的微反應活性(mat)為62。頁巖油a經(jīng)300℃預熱后進入固定床反應器擴徑的臨氫吸附區(qū)i頂部,在反應壓力4.5mpa下,隨著氫氣體積分數(shù)85%的干氣(其余為甲烷、乙烷與乙烯等)作為含氫氣體由上向下流動,h2/原料油的體積比為400,在吸附溫度400℃、催化劑與劣質原料油的重量比4.0、吸附時間為10.0秒的條件下進行臨氫吸附反應,脫除劣質原料油中堿性氮化物、硫化物和重金屬等雜質;臨氫吸附產(chǎn)物隨之下行進入裂化區(qū)ii,在500℃、催化劑與臨氫吸附產(chǎn)物的重量比5.5、反應時間60秒條件下發(fā)生催化裂化反應;生成的油氣進入分餾裝置得到柴油和油漿,分餾裝置塔頂?shù)母粴獠唤?jīng)富氣壓縮機壓縮直接進入吸收穩(wěn)定裝置進一步進行產(chǎn)品分離,得到干氣、液化氣和汽油等產(chǎn)物,油漿回煉比為0.1。反應一定時間后,待生催化劑汽提脫除其內(nèi)部吸附的油氣后,采用空氣作為再生氣體,在再生溫度620℃下與待生催化劑接觸進行再生;再生后的再生催化劑循環(huán)使用。操作條件和產(chǎn)品分布列于表3。從表3可以看出,頁巖油a先進行臨氫吸附再催化裂化,頁巖油a吸附脫硫率55重%,脫氮率85重%,脫金屬率50重%;頁巖油a臨氫吸附后再催化裂化,頁巖油a的轉化率68.2重%,油漿產(chǎn)率6.0重%,干氣產(chǎn)率3.8重%,焦炭產(chǎn)率10.7重%,液體產(chǎn)品收率高達79.5重%,其中汽油產(chǎn)率高達 37.5重%,丙烯產(chǎn)率5.2重%;產(chǎn)品汽油硫含量143.1ppm,氮含量98.3ppm。對比例1該對比例以頁巖油a作為原料,以cat-1為吸附劑和催化裂化催化劑,平衡劑mat=62,在實施例1的小型固定床催化裂化裝置上進行試驗,不同于實施例1的是:將含氫氣體替換為不含氫的水蒸氣,反應器壓力為0.25mpa,且不注入冷卻介質,而頁巖油a與水蒸汽直接注入固定床反應器的上部,即頁巖油a與催化劑順流而下,頁巖油a不經(jīng)吸附直接進行催化裂化反應;反應后,分餾裝置塔頂富氣經(jīng)富氣壓縮機壓縮提壓至1.2~1.6mpa后進入吸收穩(wěn)定裝置進一步進行產(chǎn)品分離,油漿回煉比為0.2。操作條件和產(chǎn)品分布列于表3。從表3可以看出,頁巖油a不經(jīng)吸附直接進行催化裂化反應,頁巖油轉化率65.8重%,油漿產(chǎn)率7.6重%,干氣產(chǎn)率4.6重%,焦炭產(chǎn)率14.3重%,液體產(chǎn)品收率73.5重%,其中汽油產(chǎn)率30.5重%,丙烯產(chǎn)率為5.1重%;產(chǎn)品汽油硫含量降低318.0ppm,氮含量655.2ppm。從表3的數(shù)據(jù)可以看出,采用本發(fā)明的方法進行處理頁巖油a,頁巖油轉化能力高,回煉比低,頁巖油a轉化率提高2.4個百分點,且油漿產(chǎn)率低了1.6個百分點,而干氣與焦炭產(chǎn)率低,干氣+焦炭產(chǎn)率低了4.4個百分點,液體產(chǎn)品收率提高了6.0個百分點,產(chǎn)品汽油硫含量降低174.9ppm,氮含量降低556.9ppm。實施例2該實施例按照圖2的流程進行試驗,渣油b作為催化裂化的原料,在小型連續(xù)再生固定床反應器上進行試驗,并聯(lián)兩個反應器平行放置,反應器底部擴徑(臨氫吸附區(qū)i的內(nèi)徑為0.03米,長度為0.30米,裂化區(qū)ii的直徑 為0.02米,長度為1.15米),并設置取熱盤管采用熔鹽作為冷卻介質冷卻催化劑;采用cat-1催化劑同時作為吸附劑和催化裂化催化劑,cat-1平衡劑的微反應活性(mat)為64。渣油b經(jīng)260℃預熱后進入固定床反應器擴徑的臨氫吸附區(qū)i底部,在反應壓力1.5mpa下,隨著氫氣體積分數(shù)70%的加氫尾氣與部分干氣的混合氣體作為含氫氣體由下向上流動,h2/原料油的體積比為200,在吸附溫度300℃、催化劑與渣油的重量比1.0、吸附時間為150秒條件下進行臨氫吸附反應,脫除堿性氮化物、硫化物和重金屬等雜質;渣油隨之上行進入裂化區(qū)ii,在495℃、催化劑與臨氫吸附產(chǎn)物的重量比5.5、反應時間240秒條件下一起發(fā)生催化裂化反應;生成的油氣進入分餾裝置得到柴油、油漿,分餾裝置塔頂富氣不經(jīng)富氣壓縮機壓縮直接進入吸收穩(wěn)定裝置進一步進行產(chǎn)品分離,得到干氣、液化氣和汽油等產(chǎn)物,干氣根據(jù)需要部分循環(huán)回臨氫吸附區(qū)i作為含氫氣體,油漿不回煉。反應一定時間后,待生催化劑汽提脫除其內(nèi)部吸附的油氣后,采用空氣作為再生氣體,在再生溫度600℃下與待生劑接觸進行再生;再生后的再生劑循環(huán)使用。操作條件和產(chǎn)品分布列于表4。從表4可以看出,渣油b先進行臨氫吸附再催化裂化,渣油b吸附脫硫率60重%,脫氮率70重%,脫金屬率為40重%;渣油b進行臨氫吸附后再催化裂化,渣油的轉化率(100%-柴油收率-油漿收率)為69.4重%,油漿產(chǎn)率5.0重%,干氣產(chǎn)率4.0重%,焦炭產(chǎn)率11.5重%,液體產(chǎn)品收率(液化氣收率+汽油收率+柴油收率)高達79.5重%,其中汽油產(chǎn)率高達38.5重%,丙烯產(chǎn)率為4.8重%;產(chǎn)品汽油硫含量175.2ppm,氮含量24.4ppm。對比例2該對比例以渣油b作為原料,以cat-1為吸附劑和催化裂化催化劑,平衡劑mat=64,在實施例2的小型固定床催化裂化裝置上進行試驗,不同 于實施例2的是:將含氫氣體替換為不含氫的水蒸氣,反應器壓力為0.15mpa,且不注入冷卻介質,而渣油b與水蒸汽直接注入固定床反應器的反應區(qū)下部,即渣油b不經(jīng)吸附在非臨氫氛圍下直接進行催化裂化反應;反應后,分餾裝置塔頂富氣經(jīng)富氣壓縮機壓縮提壓至1.2~1.6mpa后進入吸收穩(wěn)定裝置進一步進行產(chǎn)品分離,油漿回煉比0.1。操作條件和產(chǎn)品分布列于表4。從表4可以看出,渣油b不經(jīng)吸附在非臨氫氛圍下直接進行催化裂化反應,渣油的轉化率66.5重%,油漿產(chǎn)率7.0重%,干氣產(chǎn)率4.5重%,焦炭產(chǎn)率12.6重%,液體產(chǎn)品收率75.9重%,其中汽油產(chǎn)率35.2重%,丙烯產(chǎn)率為4.3重%;產(chǎn)品汽油硫含量438.0ppm,氮含量81.4ppm。從表4的數(shù)據(jù)可以看出,采用本發(fā)明的方法進行處理渣油b,渣油b轉化能力高,回煉比低,渣油轉化率提高2.9個百分點,且油漿產(chǎn)率低了2.0個百分點,而干氣與焦炭產(chǎn)率低,干氣+焦炭產(chǎn)率低了1.6個百分點,液體產(chǎn)品收率提高了3.6個百分點;產(chǎn)品汽油硫含量降低262.8ppm,氮含量降低57.0ppm。表1本發(fā)明實施例和對比例所使用的劣質原料油的性質劣質原料油名稱頁巖油渣油編號ab密度(20℃),千克/米3928942.7100℃運動粘度,毫米2/秒9.0362.8殘?zhí)?,重?.16.5凝點,℃2433瀝青質,重%1.32.4膠質,重%35.713.0元素組成碳,重%83.2886.62氫,重%11.6512.07硫,重%0.530.73氮,重%2.340.37氧,重%2.20.21金屬含量,ppm鐵11.011.2鎳6.67.6鈣0.18.5釩<0.18.2鈉1.31.2餾程,℃初餾點30534030%41042150%510558表2本發(fā)明實施例和對比例所使用的催化劑cat-1催化劑編號cat-1沸石類型中孔和大孔沸石化學組成,重%氧化硅52.7氧化鋁42.0氧化鈉0.30氧化鈷1.6稀土3.4形狀球形粒徑,毫米4~6表觀密度,kg/m3620孔體積,毫升/克0.35比表面積,米2/克260~300側壓強度,n/cm2>100表3為本發(fā)明實施例1和對比例1的操作條件和產(chǎn)品分布項目實施例1對比例1原料油頁巖油a頁巖油a進料方式臨氫吸附區(qū)進料裂化區(qū)進料催化劑名稱cat-1cat-1平衡劑活性(mat)6262回煉比0.10.2反應器頂壓力,mpa4.50.25臨氫吸附區(qū)操作條件原料預熱溫度,℃300300吸附溫度,℃400/h2/原料油的體積比400/吸附時間,s10.0/催化劑/原料油的重量比4.0/脫氮率,重%85.0/脫硫率,重%55.0/脫金屬率,重%50.0/裂化區(qū)操作條件反應區(qū)下部溫度,℃500500反應區(qū)中部溫度,℃505505反應區(qū)上部溫度,℃515515催化劑/原料油的重量比5.55.5油氣停留時間,s6060水蒸氣/總原料的重量比0.50.5產(chǎn)品分布,重%干氣3.84.6液化氣16.216.4丙烯5.25.1汽油37.530.5柴油25.826.6油漿6.07.6焦炭10.714.3合計100.0100.0轉化率,重%68.265.8液體產(chǎn)品收率,重%79.573.5汽油品質硫含量,ppm143.1318.0氮含量,ppm98.3655.2表4為本發(fā)明實施例2和對比例2的操作條件和產(chǎn)品分布實施例2對比例2原料油渣油b渣油b進料方式臨氫吸附區(qū)進料裂化區(qū)進料催化劑名稱cat-1cat-1平衡劑活性(mat)6464回煉比00.1反應器頂壓力,mpa1.50.15臨氫吸附區(qū)操作條件原料預熱溫度,℃280280h2/原料油的體積比200/吸附溫度,℃300/吸附時間,s150/催化劑/原料油的重量比1.0/脫氮率,重%70.0/脫硫率,重%60.0脫金屬率,重%40.0/裂化區(qū)操作條件反應區(qū)下部溫度,℃495495反應區(qū)中部溫度,℃500500反應區(qū)上部溫度,℃505505催化劑/原料油的重量比5.55.5油氣停留時間,s240240水蒸氣/總原料的重量比0.50.5產(chǎn)品分布,重%干氣4.04.5液化氣15.414.2丙烯4.84.3汽油38.535.2柴油25.626.5油漿5.07.0焦炭11.512.6合計100.0100.0轉化率,重%69.466.5液體產(chǎn)品收率,重%79.575.9汽油品質硫含量,ppm175.2438.0氮含量,ppm24.481.4當前第1頁12