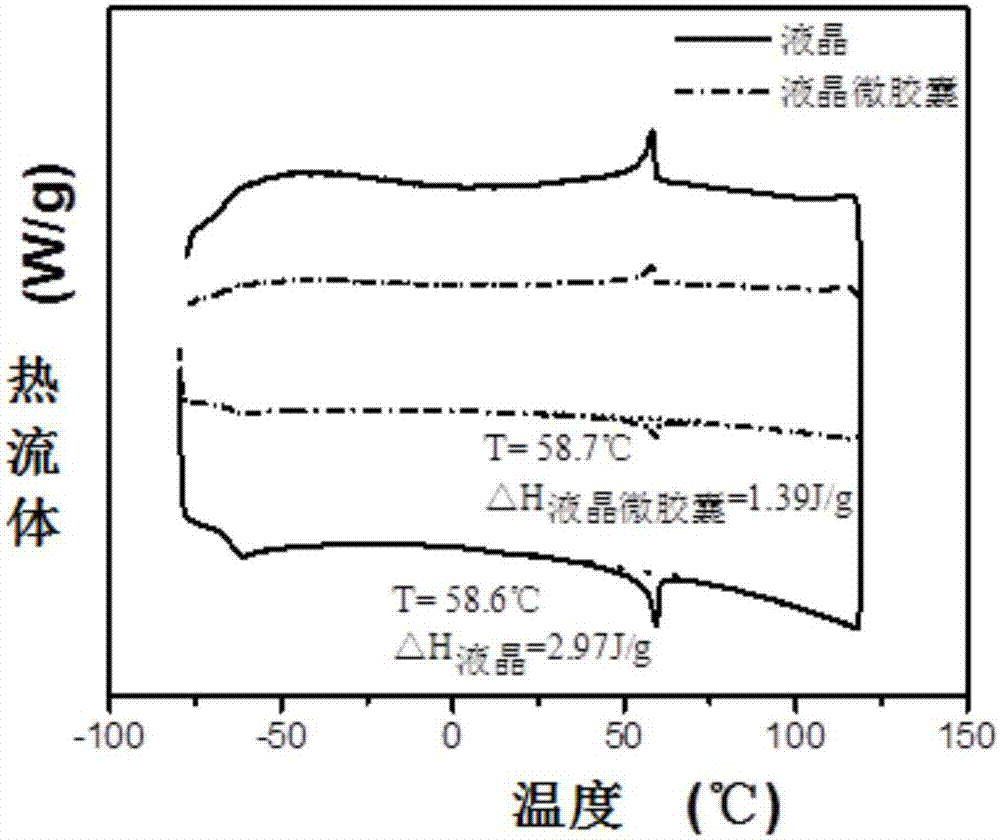
本發(fā)明屬于復(fù)合材料領(lǐng)域,涉及一種液晶微膠囊的制備方法及液晶微膠囊。
背景技術(shù):
:液晶是介于液態(tài)與結(jié)晶態(tài)之間的一種物質(zhì)狀態(tài),它除了兼有液體和晶體的某些性質(zhì),如流動(dòng)性、各向異性等,還具有特殊的理化與光電特性,因而成為當(dāng)今的科研熱點(diǎn)。聚合物分散液晶在全息存儲(chǔ)、顯示、梯度彩色光柵、調(diào)制激光等高科技領(lǐng)域具有廣泛的應(yīng)用前景。微膠囊是指利用天然或合成的高分子材料,將固體、液體或氣體物質(zhì)包裹成直徑5-300μm的微小膠囊。早在上世紀(jì)30年代,美國(guó)大西洋漁業(yè)公司便申請(qǐng)了在液體石蠟中制備含魚(yú)肝油明膠微膠囊的專(zhuān)利,該產(chǎn)品也成為了世界上第一個(gè)微膠囊產(chǎn)品。隨著科學(xué)技術(shù)的發(fā)展,新材料不斷涌現(xiàn),現(xiàn)在已知的微膠囊化方法約有一百多種,主要應(yīng)用于香精香料、食品、醫(yī)藥行業(yè)。將液晶材料微膠囊化可以顯著提高液晶材料的耐久性、延長(zhǎng)其使用壽命,擴(kuò)大其應(yīng)用范圍。目前用于液晶微膠囊的壁材主要是有機(jī)類(lèi)材料,包括各種聚合物,如苯乙烯、甲基丙烯酸酯類(lèi)、阿拉伯膠和明膠等。然而,用單純的聚合物的作為壁材的液晶微膠囊存在諸多問(wèn)題,比如壁材強(qiáng)度較低,應(yīng)用過(guò)程中易導(dǎo)致液晶材料滲出、微膠囊破裂等。謝淑云等人對(duì)制備液晶乳液快速微膠囊(CN85104765)的研究。而用親油親水兩種壁材雙層包封液晶,制備液晶微膠囊具有兩層壁材之間的相容性不好、包覆率低、體系復(fù)雜、使用有機(jī)溶劑多、內(nèi)層壁材明膠易分解等問(wèn)題,從而對(duì)產(chǎn)品的使用有限制。專(zhuān)利EP0204537通過(guò)乳液聚合技術(shù)形成液晶微膠囊,其以聚乙烯醇為殼層,近晶相液晶為芯材,形成多分散球形微膠囊。微膠囊的粒徑為0.3~100μm。而用此方法所制備的微膠囊形狀不規(guī)則,殼層為親水的聚乙烯醇,限制了其在油性體系中的應(yīng)用。專(zhuān)利US5976405通過(guò)溶脹聚合形成以向列型液晶為芯材的單分散微膠囊,其使用液晶、種子球和乙烯基單體為油相,與水形成乳液體系,通過(guò)自由基聚合形成聚合物顆粒,其中液晶被封裝在球形聚合物殼層中,這種顆粒的分散度為1.0到1.3。雖然其具有很好的單分散性,但是其反應(yīng)過(guò)程復(fù)雜,反應(yīng)時(shí)間長(zhǎng),對(duì)液晶和添加劑有嚴(yán)苛要求。俞書(shū)宏等人以明膠和阿拉伯膠為壁材制備的液晶微膠囊(高分材料科學(xué)與工程1999;15:115),由于具有的明膠和阿拉伯膠易分解,且對(duì)合成條件依賴(lài)性較高。李克軒等人制備的采用異氟爾酮二異氰酸酯(IPDI)為原料,采用界面聚合法制備的液晶微膠囊,由于原料毒性較強(qiáng),不利于大規(guī)模生產(chǎn)(液晶與顯示2012;27:583)。CN104624124A公開(kāi)了一種液晶微膠囊及其制備方法。所述的制備方法包括:a)將乳化劑加入到水中獲得分散液,以該分散液作為水相;b)將液晶、單烯烴類(lèi)單體、多烯烴類(lèi)交聯(lián)劑以及引發(fā)劑混合均勻獲得混合物,以該混合物作為油相;c)將所述水相和所述油相混合,通過(guò)進(jìn)行乳化得到水包油的乳液;d)將所述乳液通過(guò)乳液聚合形成核殼結(jié)構(gòu)的液晶微膠囊;以及e)將所述液晶微膠囊通過(guò)離心分離和噴霧干燥得到液晶微膠囊的干粉。雖然該申請(qǐng)的方法改善了液晶微膠囊的包覆率,但是得到的液晶微膠囊的光學(xué)性能欠佳。因此,亟待一種能夠制備理化和光學(xué)性能更加優(yōu)異,并且工藝簡(jiǎn)單的液晶微膠囊的方法。有鑒于此,特提出本發(fā)明。技術(shù)實(shí)現(xiàn)要素:本發(fā)明的目的在于提供一種有機(jī)-無(wú)機(jī)復(fù)合殼層的液晶微膠囊的制備方法,目的是制備透光性好、機(jī)械強(qiáng)度高、耐化學(xué)腐蝕的液晶微膠囊,本發(fā)明的進(jìn)一步目的在于提供一種工藝簡(jiǎn)單、成本低,且便于控制結(jié)構(gòu)、可工業(yè)化生產(chǎn)的液晶微膠囊制備方法。本發(fā)明的另一重要目的旨在提供一種有機(jī)-無(wú)機(jī)聚合物復(fù)合殼層的液晶微膠囊,該液晶微膠囊殼層的強(qiáng)度和柔性得到了顯著的提高,穩(wěn)定性更好,具有較好的理化和光學(xué)性能,應(yīng)用前景廣闊。根據(jù)本發(fā)明的一個(gè)方面,提供一種液晶微膠囊的制備方法,包括水相、油相以及水包油的乳液的制備過(guò)程,其中,作為油相的混合物包括液晶、環(huán)氧樹(shù)脂單體、硅烷偶聯(lián)劑和油溶性環(huán)氧樹(shù)脂固化劑。CN104624124A公開(kāi)了一種以液晶、單烯烴類(lèi)單體、多烯烴類(lèi)交聯(lián)劑以及引發(fā)劑的混合物作為油相,而本申請(qǐng)的制備方法以液晶、環(huán)氧樹(shù)脂單體、硅烷偶聯(lián)劑以及油溶性環(huán)氧樹(shù)脂固化劑的混合物作為油相,不僅得到的液晶微膠囊透光性能得到提升,提供了一種性能優(yōu)異的光電材料;而且液晶微膠囊的成囊率和包覆率也得到了明顯的改善,提高了液晶微膠囊的制備效率和質(zhì)量。本發(fā)明所述的液晶微膠囊的制備方法用簡(jiǎn)單的工藝獲得透光性好、機(jī)械強(qiáng)度高、耐化學(xué)腐蝕的液晶微膠囊,而且還便于調(diào)控液晶微膠囊的結(jié)構(gòu),工序簡(jiǎn)單、易于實(shí)現(xiàn)工業(yè)化生產(chǎn),應(yīng)用前景好。優(yōu)選地,還包括水包油的乳液的聚合反應(yīng)過(guò)程,所述聚合反應(yīng)過(guò)程中加入水溶性環(huán)氧樹(shù)脂固化劑。優(yōu)選地,水相制備過(guò)程中添加的乳化劑以所述液晶100重量份計(jì)為5~30重量份;硅烷偶聯(lián)劑以所述液晶100重量份計(jì)為10~80重量份;環(huán)氧樹(shù)脂以所述液晶100重量份計(jì)為10~80重量份;水溶性環(huán)氧樹(shù)脂固化劑或油溶性環(huán)氧樹(shù)脂固化劑以所述液晶100重量份計(jì)為5~50重量份。按照上述的含量進(jìn)行添加可以提高液晶微膠囊的包覆率和成囊率,并且所得的液晶微膠囊的機(jī)械強(qiáng)度更高,透光性更好,并且便于控制液晶微膠囊的大小勻稱(chēng)度和圓整性。并且采用所述的環(huán)氧樹(shù)脂單體與硅烷偶聯(lián)劑來(lái)獲取包裹液晶的殼層結(jié)構(gòu),硅烷偶聯(lián)劑水解聚合、環(huán)氧樹(shù)脂固化形成互穿的有機(jī)-無(wú)機(jī)聚合物復(fù)合殼體,該有機(jī)-無(wú)機(jī)聚合物復(fù)合殼體與液晶的相融合性好,提高了液晶微膠囊中液晶與包覆液晶的材料的相分離程度,并且有助于延長(zhǎng)液晶的存儲(chǔ)時(shí)間。另外,環(huán)氧樹(shù)脂單體與硅烷偶聯(lián)劑易于在液晶表面沉積并形成機(jī)械強(qiáng)度可靠的殼層,提高了成囊率和包覆率,而且所得的液晶微膠囊不易破損。本發(fā)明所述的液晶微膠囊的制備方法結(jié)合操作過(guò)程,具體包括下列步驟:1)將乳化劑溶于水中、調(diào)節(jié)pH進(jìn)行乳化,獲得分散液,以該分散液作為水相;2)將液晶、環(huán)氧樹(shù)脂單體、硅烷偶聯(lián)劑以及油溶性環(huán)氧樹(shù)脂固化劑混合均勻獲得混合物,以該混合物作為油相;3)將步驟2)得到的油相加入到步驟1)的水相中,進(jìn)行乳化后得到水包油的乳液;4)調(diào)節(jié)乳液的溫度,反應(yīng)一段時(shí)間,加入水溶性環(huán)氧樹(shù)脂固化劑,使其繼續(xù)反應(yīng)形成核殼結(jié)構(gòu)的液晶微膠囊;5)將所述液晶微膠囊離心分離、冷凍干燥得到液晶微膠囊的干粉。以上所述的步驟4)即為本發(fā)明所稱(chēng)的水包油的乳液的聚合反應(yīng)過(guò)程。優(yōu)選地,水相的pH為2~6或者8~13,更優(yōu)選pH為4.7~6或者8~11;采用以上所述的pH制備的液晶微膠囊大小均勻,圓整性好,并且每個(gè)液晶微膠囊的表面非常圓滑,透光性更好。優(yōu)選地,步驟4)的溫度調(diào)節(jié)為50~90℃,更優(yōu)選溫度為70~80℃,最優(yōu)選為76℃。發(fā)明人在實(shí)驗(yàn)研究過(guò)程中發(fā)現(xiàn):采用上述的溫度可以使液晶微膠囊的成囊率和包覆率可以同時(shí)達(dá)到較高值,并且所得的液晶微膠囊的透光性更好、機(jī)械強(qiáng)度更高。當(dāng)溫度調(diào)節(jié)為76℃時(shí),用于形成殼層的材料分子運(yùn)動(dòng)速度最適于成膜反應(yīng)的充分進(jìn)行,形成的殼層厚度和強(qiáng)度最合適,不易破囊,液晶微膠囊的成囊率提高,并且所得的液晶微膠囊的機(jī)械性能更好,耐化學(xué)腐蝕性最優(yōu);同時(shí),用于形成殼層的材料較易在液晶表面高效沉積率提高,液晶微膠囊的包覆率也得到進(jìn)一步改善。優(yōu)選地,步驟4)的反應(yīng)時(shí)間為1~24小時(shí),更優(yōu)選為8~12小時(shí)。本發(fā)明所述的反應(yīng)時(shí)間是指步驟4)中的反應(yīng)一段時(shí)間和繼續(xù)反應(yīng)形成核殼的時(shí)間的總和。采用上述反應(yīng)時(shí)間進(jìn)行制備,可以進(jìn)一步提高液晶微膠囊的大小均勻度和圓整性,并且液晶微膠囊的穩(wěn)定性也得到改善。由于本發(fā)明對(duì)液晶材料的要求是油溶性且不參與聚合反應(yīng),基本上所有的小分子液晶材料均符合要求,優(yōu)選地,液晶選自溶致液晶或熱致液晶。優(yōu)選地,環(huán)氧樹(shù)脂單體選自雙酚A型的E-51、E-44、AG-80或E-42中任一種或幾種。優(yōu)選地,硅烷偶聯(lián)劑選自γ-氨丙基三乙氧基硅烷、γ-縮水甘油醚氧丙基三甲氧基硅烷、γ-(甲基丙烯酰氧)丙基三甲氧基硅烷或N-(β-氨乙基)-γ-氨丙基三甲(乙)氧基硅烷中的一種或幾種。優(yōu)選地,水溶性環(huán)氧樹(shù)脂固化劑選自二乙烯三胺、四乙烯五胺、三乙醇胺、2-乙基-4甲基咪唑、二甲氨基甲基苯酚或2,4,6-三(二甲氨基甲基)苯酚中的一種或幾種。優(yōu)選地,油溶性環(huán)氧樹(shù)脂固化劑為芐基二甲胺。以上的物質(zhì)材料可以提高液晶微膠囊的包覆率和成囊率,并且賦予液晶微膠囊更穩(wěn)定的理化性能。優(yōu)選地,水溶性環(huán)氧樹(shù)脂固化劑或油溶性環(huán)氧樹(shù)脂固化劑的添加量為環(huán)氧樹(shù)脂的5~20wt%。采用該添加量的水溶性環(huán)氧樹(shù)脂固化劑或油溶性環(huán)氧樹(shù)脂固化劑可以賦予液晶微膠囊更好的圓整性和透光性。優(yōu)選地,乳化劑選自十二烷基硫酸鈉、聚乙烯醇、苯乙烯-馬來(lái)酸酐交替共聚物的鈉鹽水解物或環(huán)氧樹(shù)脂-聚乙二醇共聚物中的一種或幾種,更優(yōu)選為聚乙烯醇或環(huán)氧樹(shù)脂-聚乙二醇共聚物中的一種或兩種;優(yōu)選地,乳化通過(guò)高速剪切乳化、超聲波細(xì)胞粉碎機(jī)或者膜乳化,或者通過(guò)先進(jìn)行高速剪切乳化再進(jìn)行膜乳化的方式進(jìn)行;更優(yōu)選地,高速剪切乳化速度在1500轉(zhuǎn)/分~25000轉(zhuǎn)/分,乳化時(shí)間為1~30分鐘;超聲波細(xì)胞粉碎機(jī)的功率為50W~200W,乳化時(shí)間為1~30分鐘;膜乳化過(guò)程中使用的微孔膜的孔徑為55nm~2μm。采用上述的優(yōu)選乳化方式可以提高液晶微膠囊的大小均勻度、圓整性(大部分呈完好的圓球狀),并且還可以提高液晶微膠囊的包覆率和成囊率。根據(jù)本發(fā)明的另一重要目的,提供一種液晶微膠囊,該膠囊的核為液晶材料,殼為通過(guò)環(huán)氧樹(shù)脂單體和硅烷偶聯(lián)劑聚合所得的互穿有機(jī)-無(wú)機(jī)聚合物復(fù)合殼層;所述液晶微膠囊通過(guò)如上所述任意一種制備方法獲得。優(yōu)選地,所述液晶微膠囊的粒徑為60nm~10μm。優(yōu)選地,所述液晶微膠囊中液晶的含量為1%~90%。采用所述的液晶含量可以確保液晶微膠囊的包覆率和成囊率,并且更符合實(shí)際應(yīng)用的需求,降低成本。優(yōu)選地,所述液晶微膠囊的包覆率為1%~95%,更優(yōu)選為47~95%,最優(yōu)選為95%。所述包覆率在數(shù)值上與焓值保有率、芯材含量一致。所述芯材含量可通過(guò)熔融焓或結(jié)晶焓來(lái)計(jì)算,計(jì)算方法如下:壁材含量=(1一芯材含量)×100%其中,△Hm0為液晶材料的相轉(zhuǎn)變點(diǎn)熱焓,△Hm為所得到的液晶微膠囊的相轉(zhuǎn)變點(diǎn)熱焓。本發(fā)明制備方法具有廣泛的適應(yīng)性,可制備一系列不同壁層材質(zhì)的液晶微膠囊,并且液晶微膠囊的組成和殼層是可控的,其粒徑在50nm~10μm內(nèi)可調(diào),制備過(guò)程中通過(guò)本發(fā)明所述的高速剪切乳化速度和時(shí)間、超聲波細(xì)胞破碎儀的功率及時(shí)間、以及改變膜乳化中的膜孔徑等,實(shí)現(xiàn)對(duì)液晶微膠囊粒徑大小的控制,并且改變液晶與殼層材料的投料比可以獲得更高的液晶包覆率。本發(fā)明液晶微膠囊的制備方法具有下列優(yōu)點(diǎn):1、與傳統(tǒng)的液晶微膠囊的制備方法不同,本發(fā)明采用界面誘導(dǎo)相分離技術(shù),不會(huì)污染液晶,包覆率高,原料的轉(zhuǎn)化率高;2、使用安全、廉價(jià)的原料,工藝簡(jiǎn)單,操作方便,成本低;3、通過(guò)硅烷偶聯(lián)劑水解聚合、環(huán)氧樹(shù)脂固化形成互穿的有機(jī)-無(wú)機(jī)聚合物復(fù)合殼體,液晶微膠囊和包覆液晶微膠囊的材料的相融合性好;4、液晶微膠囊的表面可以引入各類(lèi)功能性硅烷偶聯(lián)劑,拓展其應(yīng)用范圍。根據(jù)本發(fā)明方法制備的液晶微膠囊具有核殼結(jié)構(gòu),其核為小分子液晶,殼為通過(guò)硅烷偶聯(lián)劑水解聚合、環(huán)氧樹(shù)脂類(lèi)固化而成的有機(jī)-無(wú)機(jī)聚合物復(fù)合殼層,其具有以下優(yōu)點(diǎn):1、透光性好、機(jī)械強(qiáng)度高、耐化學(xué)腐蝕強(qiáng);2、提高了液晶微膠囊中液晶與包覆液晶的材料的相分離程度、儲(chǔ)存液晶時(shí)間長(zhǎng);3、所述液晶微膠囊的包覆率可自由調(diào)控,包覆率高達(dá)95%。附圖說(shuō)明圖1表示實(shí)施例1所制備的液晶微膠囊的偏光顯微鏡圖;圖2表示實(shí)施例1所制備的液晶微膠囊的差示掃描量熱儀(DSC)升降溫曲線;圖3表示實(shí)施例2所制備的液晶微膠囊的掃描電鏡(SEM)圖;圖4表示實(shí)施例2所制備的液晶微膠囊的差示掃描量熱儀(DSC)升降溫曲線;圖5表示實(shí)施例3所制備的液晶微膠囊的透射電鏡(TEM)圖;圖6表示實(shí)施例3所制備的液晶微膠囊的差示掃描量熱儀(DSC)升降溫曲線。具體實(shí)施方式下面結(jié)合具體實(shí)施例,進(jìn)一步闡述本發(fā)明。應(yīng)當(dāng)理解這些實(shí)施例僅用于說(shuō)明本發(fā)明而不用于限制本發(fā)明的保護(hù)范圍。此外,在閱讀了本發(fā)明所公開(kāi)或者教導(dǎo)的內(nèi)容之后,本領(lǐng)域技術(shù)人員可以對(duì)本發(fā)明做各種修改和/或改進(jìn),這些修改或者改進(jìn)的形式都同樣落于本發(fā)明的權(quán)利要求書(shū)所限定的范圍內(nèi)。再次,下述實(shí)施例中所使用的實(shí)驗(yàn)方法如無(wú)特殊說(shuō)明,均為常規(guī)方法;下述實(shí)例中所用的材料、試劑等,如無(wú)特殊說(shuō)明,均可從商業(yè)途徑得到。實(shí)施例1本實(shí)施例中使用環(huán)氧樹(shù)脂-聚乙二醇共聚物作為乳化劑。1)將3.3wt%的環(huán)氧樹(shù)脂-聚乙二醇共聚物水溶液2g加入到48g水中,用鹽酸調(diào)節(jié)pH值到3.5,此溶液作為水相;2)將1g液晶、0.15gγ-縮水甘油醚氧丙基三甲氧基硅烷和1gE-51混合,超聲分散使它們混合均勻后作為油相;3)將上述水相和油相相混合,采用超聲細(xì)胞破碎儀在200w的功率下超聲乳化2分鐘,得到水包油的乳液;4)將上述水包油的乳液轉(zhuǎn)移至提前預(yù)熱的反應(yīng)釜中,以300轉(zhuǎn)/分機(jī)械攪拌,70℃下反應(yīng)約3小時(shí),隨著聚合反應(yīng)的進(jìn)行,硅烷偶聯(lián)劑緩慢的在油水界面溶膠凝膠形成最初的殼層;升溫到80℃加入0.013g四乙烯五胺(水溶性環(huán)氧樹(shù)脂固化劑),反應(yīng)12個(gè)小時(shí),E-51(環(huán)氧樹(shù)脂單體)在界面上與水溶性環(huán)氧樹(shù)脂固化劑接觸并固化,逐漸形成穩(wěn)定的核殼結(jié)構(gòu),形成液晶微膠囊;5)離心分離、冷凍干燥,得到液晶微膠囊的干粉。上述方法制備的液晶微膠囊的粒徑在300nm~1μm之間,尺寸均勻、可控、圓整性較好;制備所得的液晶微膠囊的包覆率為47%。實(shí)施例2本實(shí)施例中使用苯乙烯馬來(lái)酸酐交替共聚物的鈉鹽水解物(購(gòu)買(mǎi)自沙多瑪(sartomer)公司)作為乳化劑。1)將10wt%的苯乙烯馬來(lái)酸酐交替共聚物的鈉鹽3g加入到47g水中,用氨水調(diào)節(jié)pH值到9,此溶液作為水相;2)將2g液晶、0.25gγ-縮水甘油醚氧丙基三甲氧基硅烷和1.5gE-51混合,超聲分散使它們混合均勻后作為油相;3)將上述水相和油相混合,用平均孔徑為55nm的微孔膜進(jìn)行膜乳化,得到水包油的乳液,;4)將上述水包油的乳液轉(zhuǎn)移至提前預(yù)熱的反應(yīng)釜中,通入非活性氣體-氮?dú)猓?00轉(zhuǎn)/分機(jī)械攪拌,70℃下反應(yīng)約3小時(shí),隨著聚合反應(yīng)的進(jìn)行,硅烷偶聯(lián)劑緩慢的在油水界面溶膠凝膠形成最初的殼層;升溫到80℃加入0.12g三乙烯四胺(水溶性環(huán)氧樹(shù)脂固化劑),反應(yīng)12個(gè)小時(shí),環(huán)氧樹(shù)脂在界面上與固化劑接觸并固化,逐漸形成穩(wěn)定的核殼結(jié)構(gòu),形成液晶微膠囊;5)通過(guò)離心分級(jí)實(shí)現(xiàn)均勻性和尺寸控制,冷凍干燥得到液晶微膠囊的干粉。上述制備方法制備的核殼結(jié)構(gòu)的液晶微膠囊的粒徑在200nm~500nm之間,尺寸均勻、可控,圓整性和透光性好;制備所得的液晶微膠囊的包覆率為72%。實(shí)施例3本實(shí)施例中使用環(huán)氧樹(shù)脂-聚乙二醇共聚物作為乳化劑。1)將3.3wt%的環(huán)氧樹(shù)脂-聚乙二醇共聚物水溶液2.5g加入到47.5g水中,用鹽酸調(diào)節(jié)pH值到4.7,此溶液作為水相;2)將1g液晶、0.1gγ-氨丙基三乙氧基硅烷和0.3gE-51混合,超聲分散使它們混合均勻后作為油相;3)將上述水相和油相混合,采用超聲細(xì)胞破碎儀在300w的功率下超聲乳化2分鐘,得到水包油的乳液;4)將上述水包油的乳液轉(zhuǎn)移至提前預(yù)熱的反應(yīng)釜中,通入非活性氣體-氮?dú)?,?00轉(zhuǎn)/分機(jī)械攪拌,70℃下反應(yīng)約6小時(shí),隨著聚合反應(yīng)的進(jìn)行,硅烷偶聯(lián)劑緩慢的在油水界面溶膠凝膠形成最初的殼層;升溫到80℃加入0.01g四乙烯五胺(水溶性環(huán)氧樹(shù)脂固化劑),反應(yīng)10個(gè)小時(shí),環(huán)氧樹(shù)脂單體在界面上與固化劑接觸并固化,逐漸形成穩(wěn)定的核殼結(jié)構(gòu),形成液晶微膠囊;5)離心分離,冷凍干燥得到液晶微膠囊的干粉。上述制備方法制備的核殼結(jié)構(gòu)的液晶微膠囊的粒徑在150nm~300nm之間,尺寸均勻、可控,圓整性和透光性好;制備所得的液晶微膠囊的包覆率為84%。實(shí)施例4本實(shí)施例中使用苯乙烯馬來(lái)酸酐交替共聚物的鈉鹽水解物(購(gòu)買(mǎi)自沙多瑪(sartomer)公司)作為乳化劑。1)將10wt%的苯乙烯馬來(lái)酸酐交替共聚物的鈉鹽3g加入到47g水中,用氨水調(diào)節(jié)pH值到10,此溶液作為水相;2)將2g液晶、0.25gγ-縮水甘油醚氧丙基三甲氧基硅烷和1gE-51混合,超聲分散使它們混合均勻后作為油相;3)將上述水相和油相混合,采用高速攪拌機(jī)在25000轉(zhuǎn)/分的轉(zhuǎn)速下剪切乳化3分鐘后,得到水包油的乳液,得到水包油的乳液;4)將該上述水包油的乳液轉(zhuǎn)移至提前預(yù)熱的反應(yīng)釜中,通入非活性氣體-氮?dú)猓?00轉(zhuǎn)/分機(jī)械攪拌,76℃下反應(yīng)約8小時(shí),隨著聚合反應(yīng)的進(jìn)行,硅烷偶聯(lián)劑緩慢的在油水界面溶膠凝膠形成最初的殼層;升溫到90℃加入0.12g三乙烯四胺(水溶性環(huán)氧樹(shù)脂固化劑),反應(yīng)12個(gè)小時(shí),環(huán)氧樹(shù)脂單體在界面上與固化劑接觸并固化,逐漸形成穩(wěn)定的核殼結(jié)構(gòu),形成液晶微膠囊;5)通過(guò)離心分級(jí)實(shí)現(xiàn)均勻性和尺寸控制,冷凍干燥得到液晶微膠囊的干粉。上述制備方法制備的核殼結(jié)構(gòu)的液晶微膠囊的粒徑在60nm~300nm之間,尺寸均勻、可控,圓整性和透光性好;制備所得的液晶微膠囊的包覆率為92%。實(shí)施例5本實(shí)施例中使用環(huán)氧樹(shù)脂-聚乙二醇共聚物作為乳化劑。1)將3.3wt%的環(huán)氧樹(shù)脂-聚乙二醇共聚物水溶液2g加入到48g水中,用鹽酸調(diào)節(jié)pH值到6,此溶液作為水相;2)將1g液晶、0.15gγ-縮水甘油醚氧丙基三甲氧基硅烷和0.2gE-51混合,超聲分散使它們混合均勻后作為油相;3)將上述水相和油相相混合,采用高速攪拌機(jī)在10000轉(zhuǎn)/分的轉(zhuǎn)速下剪切乳化30分鐘,再使用孔徑為2μm的微孔膜進(jìn)行膜乳化,得到水包油的乳液;4)將上述水包油的乳液轉(zhuǎn)移至提前預(yù)熱的反應(yīng)釜中,以500轉(zhuǎn)/分機(jī)械攪拌,70℃下反應(yīng)約3小時(shí),隨著聚合反應(yīng)的進(jìn)行,硅烷偶聯(lián)劑緩慢的在油水界面溶膠凝膠形成最初的殼層;升溫到80℃加入0.013g四乙烯五胺(水溶性環(huán)氧樹(shù)脂固化劑),反應(yīng)12個(gè)小時(shí),E-51(環(huán)氧樹(shù)脂單體)在界面上與水溶性環(huán)氧樹(shù)脂固化劑接觸并固化,逐漸形成穩(wěn)定的核殼結(jié)構(gòu),形成液晶微膠囊;5)離心分離、冷凍干燥,得到液晶微膠囊的干粉。上述方法制備的液晶微膠囊的粒徑在600nm~5μm之間,尺寸均勻、可控、圓整性較好;制備所得的液晶微膠囊的包覆率為95%。試驗(yàn)例1本試驗(yàn)采用如下所述的不同液晶微膠囊制備成相同尺寸的液晶元件,其中液晶元件的制備方法一致,然后在同樣的測(cè)試條件下,分別測(cè)試了各元件的透射率。樣品1:本發(fā)明實(shí)施例1所得的液晶微膠囊制備而成的液晶元件;樣品2:本發(fā)明實(shí)施例2所得的液晶微膠囊制備而成的液晶元件;樣品3:本發(fā)明實(shí)施例4所得的液晶微膠囊制備而成的液晶元件;樣品4:按照CN85104765的實(shí)施例1所得的液晶微膠囊制備而成的液晶元件;樣品5:按照CN201310548072.5的實(shí)施例1所得的液晶微膠囊制備而成的液晶元件。測(cè)試所得的實(shí)驗(yàn)數(shù)據(jù)具體如下表所示。樣品編號(hào)透射率(%)187285390470559由上述實(shí)驗(yàn)數(shù)據(jù)可以看出,本申請(qǐng)的制備方法獲得的液晶微膠囊制備成液晶元件后具有更加優(yōu)異的透光性能,能夠更好地應(yīng)用于光電
技術(shù)領(lǐng)域:
。以上是節(jié)選自發(fā)明人所做的大量實(shí)施例的部分內(nèi)容,為節(jié)省篇幅起見(jiàn),不便窮舉本發(fā)明技術(shù)方案所述的全部?jī)?nèi)容,但是其已經(jīng)能夠?qū)Ρ景l(fā)明的內(nèi)容進(jìn)行了清楚的闡述。以上所述的內(nèi)容僅是本發(fā)明的較佳實(shí)施例而已,并非對(duì)本發(fā)明作任何形式上的限制,雖然本發(fā)明已以較佳實(shí)施例揭露如上,然而并非用以限定本發(fā)明,任何熟悉本專(zhuān)利的技術(shù)人員在不脫離本發(fā)明技術(shù)方案范圍內(nèi),當(dāng)可利用上述提示的技術(shù)內(nèi)容作出些許更動(dòng)或修飾為等同變化的等效實(shí)施例,但凡是未脫離本發(fā)明技術(shù)方案的內(nèi)容,依據(jù)本發(fā)明的技術(shù)實(shí)質(zhì)對(duì)以上實(shí)施例所作的任何簡(jiǎn)單修改、等同變化與修飾,均仍屬于本發(fā)明方案的范圍內(nèi)。當(dāng)前第1頁(yè)1 2 3