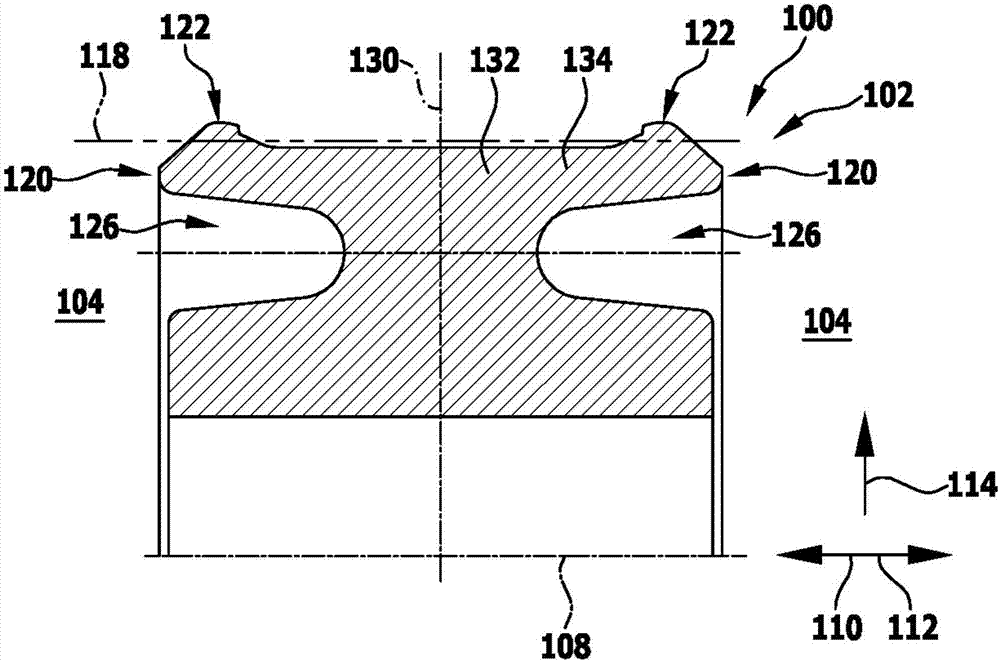
本發(fā)明涉及一種密封件,其特別是用作連桿密封、活塞密封和/或軸密封的密封件。
背景技術(shù):
:這種密封件例如由de102012112594a1已知。技術(shù)實現(xiàn)要素:本發(fā)明的任務(wù)在于提供一種密封件,其確??煽康拿芊庑Ч⒛軌蚝唵吻业统杀镜刂圃?。這一任務(wù)例如通過根據(jù)本發(fā)明的密封件得以實現(xiàn)??蔀橛欣氖?,密封件包括由熱塑性塑料材料制成的基體,其中,該基體在高壓工藝和/或高溫工藝中至少獲得其最終外形的一部分。替代地,可以設(shè)置為,密封件包括由熱塑性塑料材料制成的基體,其中,該基體在高壓工藝和/或高溫工藝中只獲得其最終外形的一部分。密封件,特別是密封件的基體,優(yōu)選接近最終外形地制造。最終外形特別是基體在密封件的使用狀態(tài)下或在待用狀態(tài)下所具有的形狀。最終外形還特別是基體在作為密封件的組成部分常規(guī)使用之前不需再進行進一步加工,例如不再進行表面改型的形狀??蔀橛欣氖牵w至少部分地或僅部分地具有通過高壓工藝和/或高溫工藝的成型體和/或完成體所具有的表面特性。可為有利的是,基體至少部分地或僅部分地具有通過注塑成型工藝的成型體和/或完成體所具有的表面特性。在本發(fā)明的一個實施方案中可以設(shè)置為,基體設(shè)計為基本上成環(huán)形?;w優(yōu)選包括一個或多個關(guān)于該環(huán)形的徑向上的內(nèi)密封段以及一個或多個徑向上的外密封段。為簡化起見,下文將以單數(shù)說明密封段。而在此當(dāng)然也可以始終設(shè)置多個具有單一或多個所述特征的密封段?;w可以例如設(shè)計為圓環(huán)形。徑向上的內(nèi)密封段優(yōu)選用于可動部件上的動態(tài)密封,特別是活塞、連桿或軸上的動態(tài)密封。徑向上的外密封段優(yōu)選用于密封裝置的殼體上的靜態(tài)密封??蔀橛欣氖牵瑥较蛏系膬?nèi)密封段和/或徑向上的外密封段在高壓工藝和/或高溫工藝中獲得其最終外形。在此可以設(shè)置為,只有徑向上的內(nèi)密封段或只有徑向上的外密封段或徑向上的內(nèi)密封段和徑向上的外密封段都在高壓工藝和/或高溫工藝中獲得其最終外形。替代地或補充地,可以設(shè)置為,徑向上的內(nèi)密封段和/或徑向上的外密封段通過再加工,例如切削加工而獲得各自的最終外形。在本發(fā)明的一個擴展方案中可以設(shè)置為,基體包括關(guān)于軸向彼此相反的兩端,這兩端特別是在密封件的使用狀態(tài)下與需相互分離的流體相接觸。僅一端具有或兩端都具有最終外形,優(yōu)選在高壓工藝和/或高溫工藝中獲得。替代地或補充地,可以設(shè)置為,僅一端是或兩端都是通過再加工,例如切削加工而獲得最終外形。一端或兩端優(yōu)選設(shè)置有一個或多個彈簧部件接納部,用以接納一個或多個彈簧部件??蔀橛欣氖?,基體包括特別是可注塑成型的熱塑性塑料材料,或由特別是可注塑成型的熱塑性塑料材料形成。該熱塑性塑料材料可以特別是氟類熱塑性材料,例如全氟化熱塑性塑料材料。基體優(yōu)選為注塑成型部件,特別是塑料注塑成型部件。密封件可以例如是彈簧支持的槽型圈。則該密封件就優(yōu)選包括一個或多個彈簧部件,該彈簧部件例如由彈簧鋼形成并至少大略具有環(huán)形形狀。一個或多個彈簧部件在此可以具有例如垂直于圓周方向的u形、v形或l形的橫截面。一個或多個彈簧部件優(yōu)選是自鎖的,特別是,一個或多個彈簧部件無需底切就能夠固定在密封件的彈簧部件接納部中。本發(fā)明還涉及密封件,特別是根據(jù)本發(fā)明的密封件作為連桿密封、活塞密封和/或軸密封的用途。密封件在此優(yōu)選應(yīng)用于燃料泵和/或活塞泵中兩個介質(zhì)腔的密封。根據(jù)本發(fā)明的用途優(yōu)選具有單個或多個關(guān)聯(lián)根據(jù)本發(fā)明的密封件所述的特征和/或優(yōu)點。本發(fā)明還涉及一種用于制造密封件的方法。在這一方面,本發(fā)明的任務(wù)在于,提供一種方法,借助該方法能夠簡單且低成本地制造可靠密封的密封件。根據(jù)本發(fā)明,這一任務(wù)通過根據(jù)本發(fā)明的方案的方法得以實現(xiàn)。該方法優(yōu)選包括:由熱塑性塑料材料制造密封件的基體,其中,該基體在高壓工藝和/或高溫工藝中至少獲得其最終外形的一部分或僅獲得其最終外形的一部分。根據(jù)本發(fā)明的方法優(yōu)選具有單個或多個關(guān)聯(lián)根據(jù)本發(fā)明的密封件和/或根據(jù)本發(fā)明的用途所述的特征和/或優(yōu)點??蔀橛欣氖?,高壓工藝包括沖壓工藝、加壓工藝、注塑成型工藝和/或壓鑄工藝。因此,基體優(yōu)選在沖壓工藝、加壓工藝、注射工藝和/或壓鑄工藝中至少獲得其最終外形的一部分或僅獲得其最終外形的一部分。替代地或補充地,可以設(shè)置為,高溫工藝包括熱沖壓工藝、熱壓工藝、注射工藝、澆鑄工藝、燒結(jié)工藝和/或熱成型工藝。因此,基體優(yōu)選在熱沖壓工藝、熱壓工藝、注射工藝、澆鑄工藝、燒結(jié)工藝和/或熱成型工藝中至少獲得其最終外形的一部分或僅獲得其最終外形的一部分??蔀橛欣氖?,密封件的基體在進行高壓工藝和/或高溫工藝之后僅進行局部的再加工。例如可以只在一側(cè)局部地再加工,特別是在軸向和/或徑向上的一側(cè)進行再加工。然而也可以設(shè)置為,在軸向上的兩側(cè)和/或在徑向上的兩側(cè)對基體進行再加工。基體優(yōu)選進行切削加工。替代地或補充地,可以設(shè)置為,為了進行再加工或作為再加工而涂裝基體。密封件的一個或多個密封段優(yōu)選通過對基體的加工制成。例如可以設(shè)置為,密封件的一個或多個動態(tài)密封段和/或密封件的一個或多個靜態(tài)密封段通過對基體的加工,特別是切削加工制成。用于接納一個或多個彈簧部件的一個或多個彈簧部件接納部優(yōu)選不進行再加工,而是優(yōu)選在高壓工藝和/或高溫工藝中獲得其最終外形。特別有利的可以是,基體由優(yōu)選可注塑成型的、部分氟化或全氟化的熱塑性塑料材料制成??梢栽O(shè)置為,基體由純ptfe(聚四氟乙烯)材料形成。熱塑性塑料(塑料材料)優(yōu)選能夠熔融加工。所使用的塑料優(yōu)選為共聚單體含量高于0.5重量%的tfe(四氟乙烯)共聚物。通過在此量級范圍內(nèi)的共聚單體含量,能夠在不削弱材料的機械強度的同時降低聚合物鏈的分子量,從而降低熔融粘度并使通過注塑成型的加工成為可能。共聚單體優(yōu)選從全氟烷基乙烯基醚,特別是全氟甲基乙烯基醚、六氟丙烯和全氟(2,2-二甲基-1,3-二氧雜環(huán)戊烯)中選擇。根據(jù)不同的共聚單體含量,全氟化熱塑性塑料涉及所謂的可熔融加工的ptfe(共聚單體含量至約3重量%),涉及pfa(作為共聚單體的全氟烷基乙烯基醚含量高于約3重量%)、mfa(作為共聚單體的全氟甲基乙烯基醚含量高于約3重量%)或fep(作為共聚單體的六氟丙烯含量高于約3重量%)。tfe共聚物也可以包括不同的共聚單體。也可能的是,全氟化熱塑性塑料包括各種tfe共聚物的混合物?;w的材料可以部分地或基本上完全地由全氟化熱塑性塑料形成。替代地或補充地,材料可以包括一種或多種填充料,特別是顏料、減少摩擦的添加劑和/或提高熱穩(wěn)定性的添加劑,以進一步優(yōu)化密封件的性能并適應(yīng)各種需求。密封件特別是適用于高壓燃料泵中的活塞的密封或用于制動系統(tǒng)(abs、esp等)的活塞泵中的活塞的密封。熱塑性塑料材料還可以特別是耐高溫和/或耐化學(xué)性的熱塑性材料,特別是peek、peak、pei等,和/或包括上述材料中的一種或多種的復(fù)合材料。特別是,通過在注塑成型工藝中制造密封件的基體,可以達到熱塑性塑料材料的高抗變形性,從而特別是最終實現(xiàn)在較高的壓力下的密封。高壓工藝特別是高壓改型工藝。高溫工藝優(yōu)選為高溫改型工藝和/或高溫改造工藝。可以設(shè)置為,高壓工藝和/或高溫工藝為制造基體的工序或僅有的工序。替代地,可以設(shè)置為,為制造基體進行其他工序。為制造密封件的基體,可以例如設(shè)置為,熱塑性塑料材料在擠出成型工藝,特別是ram擠出成型(柱塞擠出成型)工藝中進行預(yù)制,接著通過研磨以及銑削、車削或其他切削加工形成最終外形。還可以設(shè)置為,密封件的基體通過以下工序制造:擠出成型熱塑性塑料材料,特別是熔融擠出成型熱塑性塑料材料;研磨;在自動車床中進行切削加工;熱沖壓;cnc再加工(數(shù)控再加工),特別是用于制造內(nèi)輪廓,例如一個或多個徑向上的內(nèi)密封段??梢栽O(shè)置為,密封件的基體通過車削加工和/或切削加工至少獲得其最終外形的一部分或僅獲得其最終外形的一部分或完全獲得其最終外形。例如可以設(shè)置為,在成型步驟之后對基體的在密封件的安裝狀態(tài)下靠近可動部件的內(nèi)側(cè)或下側(cè)進行再加工。特別是可以通過車削加工和/或切削加工形成和/或再加工一個或多個密封緣和/或凹陷部。車削加工和/或切削加工可以例如使用能夠在軸向和徑向上移動的工具進行,該工具根據(jù)待生成的基體內(nèi)輪廓,在軸向上和徑向上沿著該基體運行。此外可以設(shè)置為,車削加工和/或切削加工例如使用這樣的工具進行,該工具包括與待生成的基體內(nèi)輪廓互補的加工緣,特別是加工刀口。該工具優(yōu)選能夠在徑向上從內(nèi)向外抵靠基體運行,特別是在加工步驟中無軸向移動地完成期望的內(nèi)輪廓。在另一實施方案中可以設(shè)置為,通過以下工序制造密封件的基體:壓制坯件;進行燒結(jié)過程;熱沖壓;cnc加工,特別是用于制造內(nèi)輪廓,例如一個或多個徑向上的內(nèi)密封段。還可以例如通過以下工序制造密封件的基體:壓制坯件;進行燒結(jié)過程;基體的cnc加工,特別是用于制造外輪廓和/或內(nèi)輪廓,例如用于制造一個或多個徑向上的內(nèi)密封段和/或一個或多個徑向上的外密封段。此外,還可以通過以下工序制造密封件的基體:?;牧希辉谟糜谥圃旎w的注塑成型工藝中使用該原材料;如有必要,對基體進行再加工,特別是進行cnc加工,以制造內(nèi)輪廓,例如一個或多個徑向上的內(nèi)密封段。如有必要,已完成的基體可以與密封件的其他部件相連接或組裝并最后一同包裝。密封唇的幾何形狀對密封件的密封性和耐久性具有決定性的影響。因此,選擇最佳的幾何形狀是密封件的制造中的重大挑戰(zhàn)。例如,具有優(yōu)選唇厚度和優(yōu)選唇定位角的唇幾何形狀、彈簧力以及密封件剖面與可動部件的直徑(特別是活塞桿直徑)的重疊,這些因素共同產(chǎn)生了對于動態(tài)密封性來說非常重要的徑向力。借助該徑向力,動態(tài)密封唇以其密封緣施壓在可動部件上。該徑向力對于密封區(qū)域的表面壓力分布的調(diào)節(jié)十分重要,并且還對這種密封件的使用壽命具有決定性的影響。過高的徑向力導(dǎo)致密封件加劇磨損并相應(yīng)地導(dǎo)致該密封件過早地失效。相反,過小的徑向力則導(dǎo)致密封件的密封性的欠缺。徑向力的最優(yōu)調(diào)節(jié)所產(chǎn)生的密封緣區(qū)域的表面壓力分布使得被拖拉開的潤滑油膜盡可能好地恢復(fù)。該表面壓力分布取決于密封唇整體的幾何形狀、密封緣的幾何形狀、彈簧部件的幾何形狀和彈簧特性以及由密封件的磨損和變形引起的上述幾何形狀和彈簧特性的一時的變化。另一個挑戰(zhàn)在于,當(dāng)選擇應(yīng)用注塑成型工藝制造密封件的至少一個區(qū)段時,在該成型工藝中雙動密封件的脫模。最佳配置的密封唇和密封緣幾何形狀可能在內(nèi)芯的脫模過程中,在模具內(nèi)的溫度下劇烈變形。出于這一原因,就必須改變密封唇/密封緣的內(nèi)部幾何形狀,以便無需過度損傷密封緣就能夠進行脫模。對此,多種措施已經(jīng)被證明是有利的。特別是,對以往的幾何形狀的脫模過程的有限元模擬得出了驚人的發(fā)現(xiàn)。令人驚訝的是,已經(jīng)證實,在脫模過程中重要的是徑向力在密封緣上的分布。本
發(fā)明內(nèi)容中的所有信息都是為了優(yōu)選在密封件的一個橫截面上更簡單地說明密封件的幾何形狀,該橫截面在穿過對稱軸延伸的平面內(nèi)。因此,可能的一維的和/或點相關(guān)的信息在求整個密封件的內(nèi)插法中得出線或曲線,特別是環(huán)形曲線。可能的二維的和/或線相關(guān)或曲線相關(guān)的信息因此在求整個密封件的內(nèi)插法中得出面,特別是環(huán)形面??赡艿亩S的和/或面相關(guān)的信息因此在求整個密封件的內(nèi)插法中得出空間,特別是環(huán)形空間。例如有利的是,對于每個密封緣來說,密封緣和在軸向上向內(nèi)鄰接該密封緣的凹處之間的距離至少大致相等。距離在本
發(fā)明內(nèi)容和所附權(quán)利要求中特別是:(i)沿著平行于密封唇的遠離至少一個密封緣的上邊或上表面延伸的方向的距離,或者(ii)沿著垂直于密封唇的遠離至少一個密封緣的上邊或上表面延伸的方向的距離,或者(iii)沿著平行于密封件的對稱軸延伸的方向的距離,即在軸向上的距離,或者(iv)沿著垂直于密封件的對稱軸延伸的方向的距離,即在徑向上的距離。凹處在本
發(fā)明內(nèi)容和所附權(quán)利要求中特別是:(i)密封唇內(nèi)的凹陷部的一個位置,該位置在局部與對稱軸之間關(guān)于徑向的距離最大,或者(ii)密封唇內(nèi)的凹陷部的一個位置,該位置在局部與密封唇的上邊或上表面之間特別是關(guān)于密封唇的厚度方向的距離最小,或者(iii)該凹陷部整體。例如,軸向上的外密封緣和在軸向上向內(nèi)鄰接該密封緣的凹處之間的距離可以為至少約0.5mm,優(yōu)選至少約0.6mm。此外,軸向上的外密封緣和在軸向上向內(nèi)鄰接該密封緣的凹處之間的距離可以為最大約1.5mm,優(yōu)選最大約1.0mm,特別是最大約0.9mm,例如為約0.8mm。例如,軸向上的內(nèi)密封緣和在軸向上向內(nèi)鄰接該密封緣的凹處之間的距離可以為至少約0.5mm,優(yōu)選至少約0.6mm。此外,軸向上的內(nèi)密封緣和在軸向上向內(nèi)鄰接該密封緣的凹處之間的距離可以為最大約2.5mm,優(yōu)選最大約1.0mm,特別是最大約0.9mm,例如為約0.8mm。在軸向上向內(nèi)鄰接密封緣的凹處特別是在密封件從注塑成型模具中脫模時起作用的底切。密封緣和在軸向上向內(nèi)鄰接該密封緣的凹處之間的距離特別是密封緣的斜邊(flanken)長度。例如,一個密封唇或所有密封唇的相鄰的密封緣的斜邊長度彼此相差最高約15%,優(yōu)選最高約5%??蔀橛欣氖?,軸向上的內(nèi)密封緣的斜邊長度小于軸向上的外密封緣的斜邊長度,例如相差至少約0.05mm,特別是至少約0.1mm,和/或相差最高約0.2mm,特別是最高約0.15mm。以這種方式,徑向力可以例如在密封件脫模時,暫時較強地施壓于第一密封緣。該第一密封緣在軸向上更靠外側(cè)設(shè)置,并比軸向內(nèi)側(cè)的第二密封緣更為柔韌。因此,盡管負載暫時增強,第一密封緣優(yōu)選并不怎么有塑性變形的危險。此外,可以設(shè)置為,軸向上的外密封緣的斜邊長度小于軸向上的內(nèi)密封緣的斜邊長度,例如相差至少約0.05mm,特別是至少約0.1mm,和/或相差最高約0.2mm,特別是最高約0.15mm。一邊由密封緣的在軸向上向內(nèi)鄰接該密封緣的斜邊、另一邊由密封件的對稱軸所圍成的密封緣角優(yōu)選對于每個密封緣來說至少大致大小相等。一個密封唇或所有密封唇的相鄰的密封緣的密封緣角優(yōu)選彼此相差最高約15%,優(yōu)選最高約5%。軸向上的外密封緣優(yōu)選為第一密封緣。軸向上的內(nèi)密封緣優(yōu)選為第二密封緣,特別是當(dāng)外密封緣和內(nèi)密封緣之間沒有設(shè)置其他密封緣時。通過選擇適當(dāng)?shù)男边呴L度和/或密封緣角,施加于兩個密封緣的徑向負載在脫模過程中優(yōu)選均勻地且更長時間地分布于兩個密封緣。由此,在脫模時,兩個密封緣優(yōu)選同時提升并重新下降??蓜硬考闹睆絻?yōu)選為至少約4mm,例如至少約5mm,和/或最大約18mm,例如最大約13mm??蓜硬考貏e是活塞桿。令人驚訝地,已經(jīng)表明,在面對強制脫模時,密封緣處的較小的半徑比較大的半徑更為敏感。較大的半徑相應(yīng)地比較小的半徑更容易脫模。經(jīng)過脫模,密封緣經(jīng)受了一定程度的塑性變形,這是因為脫模時的溫度高,而材料在該溫度下通常不具有足以完整保持形狀的高強度。半徑就可能由于塑性變形而扭曲。特別是在滿足以下參數(shù)時可得到可靠的密封效果,并同時具有良好的脫模行為:軸向上的內(nèi)密封緣的密封緣半徑優(yōu)選為至少約0.1mm,特別是至少約0.15mm,例如約0.2mm。軸向上的內(nèi)密封緣的密封緣半徑優(yōu)選為最大約0.5mm,特別是最大約0.25mm。軸向上的外密封緣的密封緣半徑優(yōu)選為至少約0.1mm,特別是至少約0.15mm,例如為約0.2mm。軸向上的外密封緣的密封緣半徑優(yōu)選為最大約0.5mm,特別是最大約0.25mm。軸向上的內(nèi)凹陷部的曲率半徑優(yōu)選為至少約0.1mm,特別是至少約0.15mm,例如為約0.2mm。軸向上的外凹陷部(位于兩個密封緣之間)的曲率半徑優(yōu)選為最大約0.3mm,特別是最大約0.25mm。對于實現(xiàn)良好的脫模來說,在燃料泵的密封系統(tǒng)中證明有效的密封唇幾何形狀有可能證實為過于穩(wěn)定和/或過于剛性的,尤其是在使用可注塑成型的氟化熱塑性塑料時,因為這種材料相比于基于ptfe的材料具有較高的剛度。業(yè)已證明有利的是,軸向上的內(nèi)密封緣的內(nèi)側(cè)上的最窄處的密封唇厚度為至少約0.4mm,優(yōu)選至少約0.5mm,例如為約0.6mm。還可以設(shè)置為,軸向上的內(nèi)密封緣的內(nèi)側(cè)上的最窄處的密封唇厚度為最大約1.0mm,優(yōu)選最大約0.7mm??蔀橛欣氖?,軸向上的內(nèi)密封緣和軸向上的外密封緣之間的最窄處的密封唇厚度為至少約0.3mm,優(yōu)選至少約0.4mm,例如為約0.5mm。還可以設(shè)置為,軸向上的內(nèi)密封緣和軸向上的外密封緣之間的最窄處的密封唇厚度為最大約0.9mm,優(yōu)選最大約0.6mm。業(yè)已證明,特別是在使用優(yōu)選的原料(材料)時,由于較高的剛度和強度,上述厚度可以足以能夠例如在燃料泵的工作壓力下可靠地密封。此外,為了使密封件能夠無損脫模,上述厚度可以是必需的。密封唇角優(yōu)選為一邊由密封唇的遠離至少一個密封緣的上表面或上邊、另一邊由對稱軸所圍成的角。在基體特別是準備好用于接納和/或固定一個或多個,特別是兩個彈簧部件的完成狀態(tài)下,一個或兩個密封唇的密封唇角例如為至少約2°,優(yōu)選至少約3°,特別是為約5°。在基體特別是準備好用于容納和/或固定一個或多個,特別是兩個彈簧部件的完成狀態(tài)下,一個或兩個密封唇的密封唇角例如為最大約12°,優(yōu)選最大約10°,特別是為約8°。在基體特別是準備好用于容納和/或固定一個或多個,特別是兩個彈簧部件的完成狀態(tài)之后,接下來的是密封件優(yōu)選在容納和/或固定一個或多個,特別是兩個彈簧部件后的待安裝狀態(tài),在該狀態(tài)下,密封件已制成并準備好用于安裝在設(shè)備內(nèi)。在密封件的待安裝狀態(tài)下,特別是由于彈簧部件的作用,密封唇角比在基體的完成狀態(tài)下優(yōu)選增大至少約1°,例如至少約2°,特別是增大約3°。在密封件的待安裝狀態(tài)下,特別是由于彈簧部件的作用,密封唇角比在基體的完成狀態(tài)下優(yōu)選增大最多約10°,例如最多約6°,特別是增大約3°。密封唇角的減小降低了脫模時的徑向力,因為通過把密封唇調(diào)正,實現(xiàn)了成型裝置和密封件之間較小的底切。若將該角度改為0°(密封唇的內(nèi)輪廓平行于軸;密封唇的遠離至少一個密封緣的上表面或上邊平行于對稱軸),則密封件與可動部件的重疊面較小,在彈簧部件相同的情況下徑向力也同樣較小。如果基體例如在第一步驟中,特別是在注塑成型步驟中所獲得的第一形狀的密封唇角為約3°或更小,就可能需要進行基體的再加工。例如可能在注塑成型步驟之后需要密封唇的再加工(也稱為密封唇的校準),以便特別是實現(xiàn)所需的密封唇或密封緣與可動部件的重疊和/或施加于可動部件的擠壓效果。這種再加工可以冷進行或優(yōu)選在提升的溫度下進行,以便特別是例如在使用含氟聚合物時克服形狀記憶效果。特別是在將密封件用于燃料泵的密封時,密封唇優(yōu)選分別具有兩個或多個密封緣。在這些密封緣之間優(yōu)選設(shè)置有凹處,該凹處應(yīng)當(dāng)有助于密封件的潤滑。因此,該凹處優(yōu)選用作潤滑劑存貯處,并應(yīng)能容納足夠的體積,從而能夠維持潤滑,和/或在出現(xiàn)瞬時較高的泄露量時,能夠暫時儲存一定量的燃料或機油。深的凹處提供了較大的存貯空間,然而也可能在例如通過注塑成型工藝制造密封件時阻礙脫模。特別是,深的凹處可能在脫模時導(dǎo)致密封緣的劇烈的塑性變形。凹處的深度優(yōu)選為密封緣和在軸向上向內(nèi)鄰接該密封緣的凹處之間的高度差。該高度差在此特別是沿著垂直于密封唇的遠離至少一個密封緣的上邊或上表面延伸的方向的距離??蔀橛欣氖牵芊饩壓驮谳S向上向內(nèi)鄰接該密封緣的凹處之間的高度差為至少約0.1mm,優(yōu)選至少約0.15mm,例如至少約0.2mm。此外,可為有利的是,密封緣和在軸向上向內(nèi)鄰接該密封緣的凹處之間的高度差為最大約0.4mm,優(yōu)選最大約0.3mm,例如最大約0.25mm。該高度差也可以稱為存貯處深度。密封唇或密封緣的所有上述特征和優(yōu)點可以既涉及靜態(tài)密封段的一個或多個密封唇和/或密封緣,又涉及動態(tài)密封段的一個或多個密封唇和/或密封緣。靜態(tài)密封段的密封唇優(yōu)選關(guān)于垂直于對稱軸延伸的橫向中心平面相互鏡像對稱。動態(tài)密封段的密封唇優(yōu)選關(guān)于垂直于對稱軸的橫向中心平面相互鏡像對稱。動態(tài)密封段的密封唇優(yōu)選作用在彼此相反的方向上。動態(tài)密封段的兩個密封唇的所有密封緣優(yōu)選在徑向上向內(nèi)突出和/或起作用。密封件特別是雙動密封件。熱塑性塑料材料優(yōu)選能夠如下制造或如下制造:可為有利的是,熱塑性塑料是特別是能夠借助復(fù)合設(shè)備制造或借助復(fù)合設(shè)備制造的復(fù)合材料。復(fù)合設(shè)備優(yōu)選包括擠出機,特別是螺桿擠出機,例如雙螺桿擠出機。為了確保所期望的材料參數(shù),必須特別是精確地開環(huán)控制和/或閉環(huán)控制螺桿轉(zhuǎn)速、螺桿幾何形狀、原材料的混合比和溫度變化過程。熱塑性塑料材料的生產(chǎn)優(yōu)選遵循一種或多種以下加工條件,特別是所有以下加工條件:材料“碳纖維”特別是炭精纖維。可為有利的是,熱塑性塑料材料的含氟聚合物含量按其質(zhì)量和/或其體積計為至少約85%,優(yōu)選至少約90%,例如為約94%。此外可以設(shè)置為,熱塑性塑料材料的含氟聚合物含量按其質(zhì)量和/或其體積計為最高約99%,優(yōu)選最高約96%,例如為約94%??蔀橛欣氖牵瑹崴苄运芰喜牧系奶祭w維含量按其質(zhì)量和/或其體積計為至少約0.5%,優(yōu)選至少約2%,例如為約4%。此外可以設(shè)置為,熱塑性塑料材料的碳纖維含量按其質(zhì)量和/或其體積計為最高約10%,優(yōu)選最高約6%,例如為約4%。可為有利的是,熱塑性塑料材料的石墨含量按其質(zhì)量和/或其體積計為至少約0.5%,優(yōu)選至少約1.5%,例如為約2%。此外可以設(shè)置為,熱塑性塑料材料的石墨含量按其質(zhì)量和/或其體積計為最高約6%,優(yōu)選最高約4%,例如為約2%。以上述方式獲得的熱塑性塑料材料優(yōu)選用于制造一個或多個密封件。為此,該熱塑性塑料材料優(yōu)選在符合一個或多個以下加工條件,特別是所有以下加工條件的前提下進行進一步加工,特別是通過注塑成型工藝制成所期望的形狀:參數(shù)單位數(shù)值原料名稱-vm3050螺桿直徑mm25塑化單元的連續(xù)區(qū)域內(nèi)的溫度:c1℃350±20c2℃365±20c3℃370±20c4℃375±20c5℃380±20模具溫度℃245±20塑化體積cm315.6注射速度cm3/s30注射壓力bar1200±100保壓壓力bar160保壓時間s6剩余冷卻時間s15上述名為vm3050的熱塑性塑料材料在其用于制造密封件時的突出特性與其他原料的比較如下表所示:術(shù)語“大約”或“近似”優(yōu)選表示特定值的最大偏差為至多10%,特別是至多5%,例如至多1%。附圖說明本發(fā)明的其它優(yōu)選特征和/或優(yōu)點是以下描述和實施例的示意圖的對象。其中:圖1示出了密封件的基體的縱截面示意圖,其中該基體僅部分地具有其最終外形;圖2示出了基體的對應(yīng)圖1的示意圖,其中為了完成外輪廓而對該基體進行過加工;圖3示出了密封件的對應(yīng)圖1的示意圖,該密封件包括已完成的基體和兩個彈簧部件;圖4示出了密封件的密封唇的縱截面示意圖,在該密封件中設(shè)置有具有引導(dǎo)區(qū)段的中央?yún)^(qū)段;圖5示出了密封件的密封唇的對應(yīng)圖4的圖示,其中該密封件不包括引導(dǎo)區(qū)段;圖6示出了密封唇的對應(yīng)圖4的圖示,用以圖解密封唇的密封緣的半徑以及密封唇內(nèi)的凹處的半徑;圖7示出了密封唇的對應(yīng)圖4的圖示,用以圖解密封唇厚度;圖8示出了密封唇的對應(yīng)圖4的圖示,用以圖解密封唇角;以及圖9示出了密封唇的對應(yīng)圖4的圖示,用以圖解底切深度和密封唇的存貯處的存貯處深度。相同或功能相當(dāng)?shù)牟考谌扛綀D中標記為相同的標號。具體實施方案圖1至圖3所示的、整體以100標記的密封件的實施方案例如是高壓泵102的組成部分,并且用于可動部件106區(qū)域內(nèi)的兩個介質(zhì)腔104之間的密封??蓜硬考?06可以例如是高壓泵102的活塞??蓜硬考?06特別是穿過密封件100??蓜硬考?06和密封件100在此都優(yōu)選旋轉(zhuǎn)對稱地圍繞對稱軸108。對稱軸108特別是平行于可動部件106的和密封件100的縱軸110。密封件100和可動部件106在安裝狀態(tài)下具有共同的對稱軸108。縱軸110優(yōu)選定義軸向112。垂直于軸向112的方向為徑向114。借助密封件100優(yōu)選在軸向112上將介質(zhì)腔104相互隔開。密封件100優(yōu)選經(jīng)由兩個動態(tài)密封段116,在徑向114上向內(nèi)鄰接可動部件106。密封件100在徑向114上向外鄰接高壓泵102的殼體118。密封件100在自身的安裝狀態(tài)下相對于殼體118固定。因此,密封件100的對應(yīng)兩個介質(zhì)腔104的兩個密封區(qū)域120除包括動態(tài)密封段116之外,還包括抵靠殼體118的兩個靜態(tài)密封段122。動態(tài)密封段116用于密封件100和相對于密封件100運動的、特別是沿著軸向112滑動的部件106之間的動態(tài)密封。為了達到增強的密封效果,可以設(shè)置密封件100的一個或多個彈簧部件124。該一個或多個彈簧部件124特別是能夠設(shè)置在或設(shè)置在一個或多個彈簧部件接納部126中。借助一個或多個彈簧部件124特別是能夠?qū)⒁粋€或多個動態(tài)密封段116壓緊在可動部件106上。替代地或補充地,可以設(shè)置為,借助一個或多個彈簧部件124能夠?qū)⒁粋€或多個靜態(tài)密封段122壓緊在高壓泵102的殼體118上。彈簧部件124特別是設(shè)計為環(huán)形,例如圓環(huán)形,并具有例如v形或u形的橫截面。每個動態(tài)密封段116優(yōu)選包括一個密封唇127,每個該密封唇具有一個、兩個或多于兩個密封緣128。每個密封唇127和/或每個密封緣128優(yōu)選設(shè)計為基本上成環(huán)形且基本上旋轉(zhuǎn)對稱地圍繞對稱軸108。每個密封唇127的密封緣128在此優(yōu)選設(shè)置為與密封件100的橫向中心平面130相距不同的距離,該橫向中心平面垂直于密封件100的縱軸110延伸。密封件100特別是包括基體132,該基體優(yōu)選由熱塑性塑料材料一體成型?;w132特別是包括一個或多個動態(tài)密封段116、一個或多個靜態(tài)密封段122和一個或多個彈簧部件接納部126?;w132例如可以如下制造:基體132的坯件134例如可以通過注塑成型工藝制造?;w132的坯件134在此僅部分地具有其最終的外形。特別是,在坯件134的制造過程中僅完成彈簧部件接納部126。而密封段116、122則必須特別是通過切削加工,例如cnc加工來進行再加工,以完成基體132。特別是通過比較圖1至圖3可知,在此例如可以首先加工外輪廓,以完成徑向外側(cè)的靜態(tài)密封段122。接著就可以進行徑向內(nèi)側(cè)的加工,以完成動態(tài)密封段116。可以替代地設(shè)置為,坯件134例如通過注塑成型工藝這樣制成,即,靜態(tài)密封段122和彈簧部件接納部126經(jīng)過注塑成型過程之后都已具有最終的外形。此后,只有徑向內(nèi)側(cè)區(qū)域仍必須進行機械再加工,以完成動態(tài)密封段116。特別是,一方面在高壓工藝和/或高溫工藝,例如注塑成型工藝中制成坯件134,另一方面僅在局部進行后處理以完成基體132,通過這樣的組合,能夠特別有效率且低成本地制造基體132并由此制造整個密封件100。圖4示出了密封件100的一個替代實施方案的動態(tài)密封段116的密封唇127的放大的截面圖。該密封件100的密封唇127與圖3所示的密封件100的實施方案的密封唇127的不同之處基本上在于其幾何形狀。為了詳細說明該密封唇127的幾何形狀,首先詳細說明密封唇127的各個部件和該密封唇區(qū)域:密封唇127是從基體132的中央?yún)^(qū)段140稍微傾斜于軸向112延伸的、并且在徑向114上向內(nèi)輕微突出的基體132的區(qū)段。密封唇127在此包括在密封件100的安裝狀態(tài)下靠近可動部件106的下邊142,以及在密封件100的安裝狀態(tài)下遠離可動部件106的上邊144。上邊144在橫截面中基本上是平的。在立體觀察密封件100時,該上邊144特別是具有截錐外形。在密封唇127的下邊142上設(shè)置有一個或多個,例如兩個突出部146。該突出部146在其在徑向114上向內(nèi)突出的端部上形成密封唇127的密封緣128。斜邊148在軸向112上向內(nèi),即向著基體132的中央?yún)^(qū)段140的方向分別鄰接密封緣128。在每個斜邊148的遠離各個密封緣128的一側(cè)上設(shè)置有密封唇127的凹處150或凹陷部152。由此,一個凹處150特別是設(shè)置在形成密封緣128的兩個突出部146之間。另一個凹處150優(yōu)選形成在軸向112上的內(nèi)密封緣128i和基體132的中央?yún)^(qū)段140之間。由圖4可知,基體132的中央?yún)^(qū)段140可以包括引導(dǎo)區(qū)段154。該引導(dǎo)區(qū)段154優(yōu)選具有平行于對稱軸108延伸的表面,并在密封件100的使用狀態(tài)下用于在可動部件106側(cè)移的情況下支撐和/或引導(dǎo)可動部件106。引導(dǎo)區(qū)段154與對稱軸108之間的距離在此優(yōu)選大于可動部件106的半徑rb。密封唇127的外密封緣128a形成第一密封緣128。密封唇127的內(nèi)密封緣128i形成第二密封緣128。由圖4可知,外密封緣128a和在軸向112上向內(nèi)鄰接該外密封緣128a的凹處150相互間存在軸向間距aaa,該軸向間距例如至少近似地對應(yīng)內(nèi)密封緣128i和在軸向112上向內(nèi)鄰接該內(nèi)密封緣128i的凹處150之間的軸向間距aai。間距aaa優(yōu)選在約0.5mm至約2.5mm之間,例如在約0.5mm至約1.5mm之間,特別是在約0.6mm至約1mm之間。間距aaa和間距aai都優(yōu)選涉及密封唇127的相關(guān)位置相互間在軸向112上的距離。通過適當(dāng)選擇間距aaa和aai,可以例如在通過注塑成型工藝制造密封件時,使該密封件100盡可能無損地從(未示出的)成型裝置中脫模。特別是,可以在進行外密封緣128a區(qū)域的脫模時,使密封唇127在徑向114上向外彎曲,從而也使得形成內(nèi)密封緣128i的突出部146盡可能無破壞地進行脫模。在脫模時,優(yōu)選使外密封緣128a和內(nèi)密封緣128i基本上均勻地在徑向114上向外移動。由此作用在密封唇127上的力就可以優(yōu)選均勻地傳遞和吸收。圖5所示的密封件100的密封唇127的替代實施方案與圖4所示的實施方案的不同之處基本上在于,中央?yún)^(qū)段140不具有引導(dǎo)區(qū)段154。因此,在密封件100的安裝狀態(tài)下,中央?yún)^(qū)段140和可動部件106之間的距離am大于圖4所示的密封件100的實施方案中的相應(yīng)距離。除此之外,圖5所示的實施方案在構(gòu)造和功能方面與圖4所示的實施方案一致,從而就此而言參照后者的上述說明。圖6示出了密封緣128的半徑r和凹處150的半徑r。合適的半徑選擇特別是影響在通過注塑成型工藝制成密封件之后,該密封件100的脫模。密封緣128的半徑r和凹處150的半徑r優(yōu)選選擇為至少大致大小相近。該半徑例如在約0.1mm和約0.5mm之間,特別是為約0.2mm。然而也可以設(shè)置彼此不同的半徑r。例如,密封緣128的半徑r可以大于或小于凹處150的半徑r。特別是由圖7可知,密封唇127優(yōu)選設(shè)計為,位于中央?yún)^(qū)段140和內(nèi)密封緣128i的斜邊148之間的凹處150或凹陷部152區(qū)域的密封唇厚度d1大于位于兩個密封緣128i、128a之間的、設(shè)置在這兩個密封緣之間的凹處150或凹陷部152區(qū)域的密封唇厚度d2。密封唇厚度d1、d2在此分別為密封唇127的上邊144和每個凹處150或凹陷部152之間的最小距離??梢栽O(shè)置為,密封唇厚度d1例如在約0.4mm至約1mm之間,特別是在約0.5mm至約0.7mm之間,優(yōu)選為約0.6mm。另外可以設(shè)置為,密封唇厚度d2在約0.3mm至約0.7mm之間,特別是為約0.5mm。密封唇127在此特別是設(shè)計為,當(dāng)可動部件106的半徑rb例如在約2mm至9mm之間,特別是在約2.5mm至約6.5mm之間時,可確保該可動部件106上的最優(yōu)密封效果。特別是由圖8可知,密封唇127傾斜于軸向112且傾斜于徑向114地從密封件100的基體132的中央?yún)^(qū)段140突出。在基體132的完成狀態(tài)下,在安裝彈簧部件124之前,一邊由密封唇127的上邊144、另一邊由對稱軸108所圍成的密封唇角α優(yōu)選為在約3°和約10°之間。在密封件100的待安裝狀態(tài)下,即在安裝上彈簧部件124之后,該密封唇角α可以增大例如約1°至3°??梢栽O(shè)置為,在制造基體132時,先選擇較小的密封唇角α。例如可以在通過注塑成型工藝制造基體132時,先設(shè)置密封唇角α為0°。則密封唇127的上邊144就基本上平行于對稱軸108延伸。為了確保密封件100的最優(yōu)密封效果,在通過注塑成型工藝制成基體132之后,優(yōu)選進行該基體132的再加工或再處理。在此,特別是可以設(shè)置為,通過冷變形或通過在加熱密封唇127和/或整個基體132之后或過程中的變形使密封唇127改型,特別是為獲得大于約3°的密封唇角α。圖9一方面示出了底切深度t,由于密封唇127的幾何形狀,在密封件100脫模時必須克服該底切深度。兩個密封緣128之間的底切深度t在此優(yōu)選小于基體132的中央?yún)^(qū)段140區(qū)域的底切深度t,和/或小于設(shè)置于中央?yún)^(qū)段140和內(nèi)密封緣128i的斜邊148之間的凹處150和/或凹陷部152區(qū)域的底切深度t。由于必須克服底切深度t這一事實,密封件100從注塑成型模具中的脫模特別是強制脫模。由圖9還可以看出,密封唇127優(yōu)選具有用于容納介質(zhì),例如燃料或機油的存貯處156。通過將流經(jīng)外密封緣128a的介質(zhì)容納在存貯處156中,可以借助該存貯處156特別是至少暫時地抵消密封件在密封唇127區(qū)域的泄露。通過密封緣128和/或斜邊148的合適的幾何形狀,可以特別是在可動部件106進行軸向運動時,逐漸將容納的介質(zhì)送回相鄰的介質(zhì)腔104中。存貯處深度td優(yōu)選為位于兩個密封緣128之間的凹處150和穿過兩個密封緣128延伸的直線之間的最小距離。存貯處深度td優(yōu)選在約0.1mm至約0.4mm之間,特別是在約0.15mm和約0.25mm之間。圖4至圖9所述的密封唇127的參數(shù)優(yōu)選針對密封件100的動態(tài)密封段116的密封唇127。此外,可以設(shè)置為,所述的值和參數(shù)適用于兩個動態(tài)密封段116的兩個密封唇127。特別是可以設(shè)置為,在所有上述實施方案中,密封件100設(shè)計為關(guān)于橫向中心平面130鏡像對稱。此外,在每個所述實施方案中,密封件100優(yōu)選設(shè)計為圍繞對稱軸108旋轉(zhuǎn)對稱。優(yōu)選實施方案可以如下:1.密封件(100),其用于填充有第一介質(zhì)的第一介質(zhì)腔(104)和填充有第二介質(zhì)的第二介質(zhì)腔(104)之間在可動部件(106)區(qū)域的密封,該可動部件穿過該密封件(100)或能夠穿過該密封件,并能夠沿著該可動部件(106)的縱軸(110)滑動和/或能夠沿著該縱軸(110)旋轉(zhuǎn),其中,密封件(100)包括基體(132),該基體具有兩個抵靠或能夠抵靠可動部件(106)的動態(tài)密封段(116),其中,每個動態(tài)密封段(116)具有密封唇(127),其中,每個密封唇(127)分別包括一個、兩個或更多個密封緣(128),其中,基體(132)優(yōu)選由部分氟化或全氟化的熱塑性塑料材料形成,并且特別是在高壓工藝和/或高溫工藝中至少獲得其最終外形的一部分或只獲得其最終外形的一部分。2.根據(jù)實施方案1的密封件(100),其特征在于,基體(132)是注塑成型部件,和/或由可注塑成型的、部分氟化或全氟化的熱塑性塑料材料形成。3.根據(jù)實施方案1或2的密封件(100),其特征在于,軸向(112)上的外密封緣(128)和在軸向(112)上向內(nèi)鄰接該密封緣(128)的凹處之間的距離(a)為至少約0.5mm,優(yōu)選至少約0.6mm。4.根據(jù)實施方案1至3中任一項的密封件(100),其特征在于,軸向(112)上的外密封緣(128)和在軸向(112)上向內(nèi)鄰接該密封緣(128)的凹處(150)之間的距離(a)為最大約1.5mm,優(yōu)選最大約1.0mm,特別是最大約0.9mm,例如為約0.8mm。5.根據(jù)實施方案1至4中任一項的密封件(100),其特征在于,軸向(112)上的內(nèi)密封緣(128)和在軸向(112)上向內(nèi)鄰接該密封緣(128)的凹處(150)之間的距離(a)為至少約0.5mm,優(yōu)選至少約0.6mm。6.根據(jù)實施方案1至5中任一項的密封件(100),其特征在于,軸向(112)上的內(nèi)密封緣(128)和在軸向(112)上向內(nèi)鄰接該密封緣(128)的凹處(150)之間的距離(a)為最大約2.5mm,優(yōu)選最大約1.0mm,特別是最大約0.9mm,例如為約0.8mm。7.根據(jù)實施方案1至6中任一項的密封件(100),其特征在于,一個密封唇(127)或所有密封唇(127)的相鄰的密封緣(128)的兩個斜邊長度彼此相差最高約15%,優(yōu)選最高約5%。8.根據(jù)實施方案1至7中任一項的密封件(100),其特征在于,軸向(112)上的內(nèi)密封緣(128)的斜邊長度小于軸向(112)上的外密封緣(128)的斜邊長度,例如相差至少約0.05mm,特別是至少約0.1mm,和/或相差最高約0.2mm,特別是最高約0.15mm。9.根據(jù)實施方案1至8中任一項的密封件(100),其特征在于,軸向(112)上的外密封緣(128)的斜邊長度小于軸向(112)上的內(nèi)密封緣(128)的斜邊長度,例如相差至少約0.05mm,特別是至少約0.1mm,和/或相差最高約0.2mm,特別是最高約0.15mm。10.根據(jù)實施方案1至9中任一項的密封件(100),其特征在于,一邊由密封緣(128)的在軸向(112)上向內(nèi)鄰接該密封緣(128)的斜邊(148)、另一邊由密封件(100)的對稱軸(108)所圍成的密封緣角優(yōu)選對于每個密封緣(128)來說至少大致大小相等,其中,一個密封唇(127)或所有密封唇(127)的相鄰的密封緣(128)的密封緣角優(yōu)選彼此相差最高約15%,優(yōu)選最高約5%。11.根據(jù)實施方案1至10中任一項的密封件(100),其特征在于,可動部件(106)的直徑優(yōu)選為至少約4mm,例如至少約5mm,和/或最大約18mm,例如最大約13mm。12.根據(jù)實施方案1至11中任一項的密封件(100),其特征在于,軸向(112)上的內(nèi)密封緣(128)的密封緣半徑和/或軸向(112)上的外密封緣(128)的密封緣半徑為至少約0.1mm,特別是至少約0.15mm,例如為約0.2mm。13.根據(jù)實施方案1至12中任一項的密封件(100),其特征在于,軸向(112)上的內(nèi)密封緣(128)的密封緣半徑和/或軸向(112)上的外密封緣(128)的密封緣半徑為最大約0.5mm,特別是最大約0.25mm。14.根據(jù)實施方案1至13中任一項的密封件(100),其特征在于,軸向(112)上的內(nèi)密封緣(128)的內(nèi)側(cè)上的最窄處的密封唇厚度(d)為至少約0.4mm,優(yōu)選至少約0.5mm,例如為約0.6mm。15.根據(jù)實施方案1至14中任一項的密封件(100),其特征在于,軸向(112)上的內(nèi)密封緣(128)的內(nèi)側(cè)上的最窄處的密封唇厚度(d)為最大約1.0mm,優(yōu)選最大約0.7mm。16.根據(jù)實施方案1至15中任一項的密封件(100),其特征在于,軸向(112)上的內(nèi)密封緣(128)和軸向(112)上的外密封緣(128)之間的最窄處的密封唇厚度(d)為至少約0.3mm,優(yōu)選至少約0.4mm,例如為約0.5mm。17.根據(jù)實施方案1至16中任一項的密封件(100),其特征在于,軸向(112)上的內(nèi)密封緣(128)和軸向(112)上的外密封緣(128)之間的最窄處的密封唇厚度(d)為最大約0.9mm,優(yōu)選最大約0.6mm。18.根據(jù)實施方案1至17中任一項的密封件(100),其特征在于,在基體(132)的完成狀態(tài)下,一個或兩個密封唇(127)的密封唇角例如為至少約2°,優(yōu)選至少約3°,特別是為約5°。19.根據(jù)實施方案1至18中任一項的密封件(100),其特征在于,在基體(132)的完成狀態(tài)下,一個或兩個密封唇(127)的密封唇角例如為最大約12°,優(yōu)選最大約10°,特別是為約8°。20.根據(jù)實施方案1至19中任一項的密封件(100),其特征在于,密封緣(128)和在軸向(112)上向內(nèi)鄰接該密封緣(128)的凹處之間的高度差和/或密封唇(127)的存貯處深度為至少約0.1mm,優(yōu)選至少約0.15mm,例如至少約0.2mm。21.根據(jù)實施方案1至20中任一項的密封件(100),其特征在于,密封緣(128)和在軸向(112)上向內(nèi)鄰接該密封緣(128)的凹處之間的高度差和/或密封唇(127)的存貯處深度為最大約0.4mm,優(yōu)選最大約0.3mm,例如最大約0.25mm。22.特別是根據(jù)實施方案1至21中任一項的密封件(100),其用于填充有第一介質(zhì)的第一介質(zhì)腔(104)和填充有第二介質(zhì)的第二介質(zhì)腔(104)之間在可動部件(106)區(qū)域的密封,該可動部件穿過該密封件(100)或能夠穿過該密封件,并能夠沿著該可動部件(106)的縱軸(110)滑動和/或能夠沿著該縱軸(110)旋轉(zhuǎn),其中,密封件(100)包括基體(132),該基體具有兩個抵靠或能夠抵靠可動部件(106)的動態(tài)密封段(116),其中,每個動態(tài)密封段(116)具有密封唇(127),其中,每個密封唇(127)分別包括一個、兩個或更多個密封緣(128),其中,基體(132)由可注塑成型的、部分氟化或全氟化的熱塑性塑料材料形成。23.根據(jù)實施方案1至23中任一項的密封件(100),其特征在于,密封件(100)的基體(132)通過車削加工和/或切削加工至少獲得其最終外形的一部分或只獲得其最終外形的一部分或完全獲得其最終外形。24.根據(jù)實施方案1至23中任一項的密封件(100),其特征在于,在成型步驟之后對在密封件(100)的安裝狀態(tài)下靠近可動部件(106)的基體(132)的內(nèi)側(cè)或下側(cè)(142)進行再加工。25.根據(jù)實施方案1至24中任一項的密封件(100),其特征在于,熱塑性塑料材料的含氟聚合物含量按其質(zhì)量和/或其體積計為至少約85%,優(yōu)選至少約90%,例如為約94%。26.根據(jù)實施方案1至25中任一項的密封件(100),其特征在于,熱塑性塑料材料的含氟聚合物含量按其質(zhì)量和/或其體積計為最高約99%,優(yōu)選最高約96%,例如為約94%。27.根據(jù)實施方案1至26中任一項的密封件(100),其特征在于,熱塑性塑料材料的碳纖維含量按其質(zhì)量和/或其體積計為至少約0.5%,優(yōu)選至少約2%,例如為約4%。28.根據(jù)實施方案1至27中任一項的密封件(100),其特征在于,熱塑性塑料材料的碳纖維含量按其質(zhì)量和/或其體積計為最高約10%,優(yōu)選最高約6%,例如為約4%。29.根據(jù)實施方案1至28中任一項的密封件(100),其特征在于,熱塑性塑料材料的石墨含量按其質(zhì)量和/或其體積計為至少約0.5%,優(yōu)選至少約1.5%,例如為約2%。30.根據(jù)實施方案1至29中任一項的密封件(100),其特征在于,熱塑性塑料材料的石墨含量按其質(zhì)量和/或其體積計為最高約6%,優(yōu)選最高約4%,例如為約2%。31.高壓泵(102),其包括至少一個根據(jù)實施方案1至30中任一項的密封件(100)。32.根據(jù)實施方案31的高壓泵(102)用于將燃料噴射進內(nèi)燃機。33.根據(jù)實施方案1至30中任一項的密封件(100)用作連桿密封、活塞密封和/或軸密封,特別是用于燃料泵和/或活塞泵中的應(yīng)用。34.使用可注塑成型的、部分氟化或全氟化的熱塑性塑料材料制造密封件(100),特別是根據(jù)實施方案1至30中任一項的密封件(100)。35.用于制造密封件(100),特別是根據(jù)實施方案1至30中任一項的密封件(100)的方法,其包括:由部分氟化或全氟化的熱塑性塑料材料制造密封件(100)的基體(132),其中,該基體(132)特別是在高壓工藝和/或高溫工藝中優(yōu)選至少獲得其最終外形的一部分或只獲得其最終外形的一部分。36.根據(jù)實施方案35的方法,其特征在于,高壓工藝包括沖壓工藝、加壓工藝、注射工藝和/或壓鑄工藝。37.根據(jù)實施方案35或36的方法,其特征在于,高溫工藝包括熱沖壓工藝、熱壓工藝、注射工藝、澆鑄工藝、燒結(jié)工藝和/或熱成型工藝。38.根據(jù)實施方案35至37中任一項的方法,其特征在于,密封件(100)的基體(132)在進行高壓工藝和/或高溫工藝之后僅局部地進行再加工。39.根據(jù)實施方案35至38中任一項的方法,其特征在于,基體(132)完全或局部地進行切削加工和/或涂裝。40.根據(jù)實施方案35至39中任一項的方法,其特征在于,密封件(100)的一個或多個密封段(116、122),特別是密封緣(128)通過對基體(132)的機械加工,特別是切削加工而制成。41.根據(jù)實施方案35至40中任一項的方法,其特征在于,基體(132)在注塑成型步驟中獲得第一形狀,在該形狀中,動態(tài)密封段(116)的一個或兩個密封唇(127)的密封唇角為約3°或更小。42.根據(jù)實施方案41的方法,其特征在于,將基體(132)再加工為,特別是熱再加工和/或機械再加工為,動態(tài)密封段(116)的一個或兩個密封唇(127)的密封唇角增大到約3°以上,例如至少增大到約5°。43.特別是根據(jù)實施方案35至42中任一項的方法,用于制造密封件(100),特別是根據(jù)實施方案1至30中任一項的密封件(100),該方法包括:由可注塑成型的、部分氟化或全氟化的熱塑性塑料材料制造密封件(100)的基體(132)。44.根據(jù)實施方案35至43中任一項的方法,其特征在于,密封件(100)的基體(132)通過車削加工和/或切削加工至少獲得其最終外形的一部分或只獲得其最終外形的一部分或完全獲得其最終外形。45.根據(jù)實施方案35或44的方法,其特征在于,在成型步驟之后對在密封件(100)的安裝狀態(tài)下靠近可動部件(106)的基體(132)的內(nèi)側(cè)或下側(cè)(142)進行再加工。46.根據(jù)實施方案35至45中任一項的方法,其特征在于,通過車削加工和/或切削加工形成和/或再加工一個或多個密封緣(128)和/或凹陷部(152)和/或凹處(150)。47.根據(jù)實施方案46的方法,其特征在于,車削加工和/或切削加工使用能夠在軸向和徑向上移動的工具進行,該工具根據(jù)待生成的基體(100)的內(nèi)輪廓,在軸向上和徑向上沿著該基體運行。48.根據(jù)實施方案46或47的方法,其特征在于,車削加工和/或切削加工使用這樣的工具進行,該工具包括與待生成的基體(100)的內(nèi)輪廓互補的加工緣,特別是加工刀口。49.根據(jù)實施方案48的方法,其特征在于,該工具在徑向上從內(nèi)向外抵靠基體(100)運行,特別是在加工步驟中無軸向移動地完成期望的基體(132)的內(nèi)輪廓。50.根據(jù)實施方案35至49中任一項的方法,其特征在于,作為復(fù)合材料的熱塑性塑料材料由(按重量和/或體積計)約94%的含氟聚合物、約4%的碳纖維和約2%的石墨制成。51.根據(jù)實施方案35至50中任一項的方法,其特征在于,熱塑性塑料材料在復(fù)合設(shè)備的塑化單元的連續(xù)區(qū)域內(nèi)相繼地達到以下溫度:80±20℃、340±20℃、360±20℃、365±20℃、350±20℃、340±20℃。52.根據(jù)實施方案35至51中任一項的方法,其特征在于,熱塑性塑料材料在用于制造密封件(100)的注塑成型設(shè)備的塑化單元的連續(xù)區(qū)域內(nèi)相繼地達到以下溫度:350±20℃、365±20℃、370±20℃、375±20℃、380±20℃。當(dāng)前第1頁12