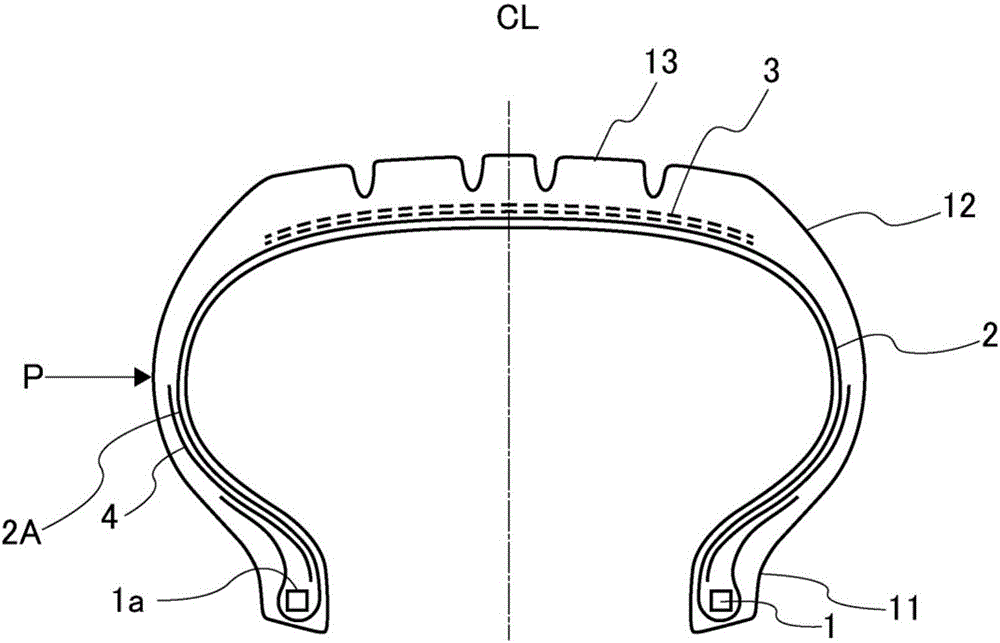
本發(fā)明涉及一種充氣輪胎(以下也簡稱為“輪胎”),更具體地,涉及使用可用于橡膠制品加強(qiáng)用途的橡膠-纖維復(fù)合體的充氣子午線輪胎。
背景技術(shù):
:傳統(tǒng)上,已經(jīng)對作為如輪胎等橡膠制品的加強(qiáng)材料的諸如有機(jī)纖維或金屬材料等材料作出了各種研究,并且已經(jīng)使用了這樣的材料。有機(jī)纖維之中,盡管由諸如聚丙烯(PP)-系樹脂等聚烯烴系樹脂形成的有機(jī)纖維是尚未被用于普通橡膠制品的纖維材料,但是根據(jù)本發(fā)明人的研究,由于此類有機(jī)纖維可以與橡膠熔著,由此消除了提供有機(jī)纖維和橡膠的粘接通常所需要的粘合劑組合物在有機(jī)纖維上的浸漬處理的步驟的需要、或提供由具有與通過浸漬處理形成的粘合層的有利的粘接性的涂覆橡膠形成的層的需要,可以省略為了確保粘接性的目的而放入其間的層。因此,由聚烯烴系樹脂形成的加強(qiáng)材料特別適用于實(shí)現(xiàn)用于輪胎的節(jié)約資源的薄的規(guī)格的需求。這里,在其熔點(diǎn)以上通過加熱熔化的纖維樹脂通過在界面處的相互作用粘著至橡膠稱為熔著(fusion)。然而,當(dāng)制造橡膠制品時,需要其中使橡膠硫磺交聯(lián)并且接合加強(qiáng)材料的硫化處理;并且為了引起硫磺交聯(lián)反應(yīng),通常需要在140℃以上的溫度下的熱處理。工業(yè)上,硫化通常在165至190℃的溫度下進(jìn)行以便通過減少硫化反應(yīng)的時間來控制加工成本。由于PP-系樹脂具有相對低的熔點(diǎn),所以當(dāng)PP-系樹脂簾線用于加強(qiáng)橡膠制品時,設(shè)想的是加強(qiáng)用纖維材料變?yōu)橥ㄟ^在硫化期間的加熱而在橡膠制品中熔化的熔融體。出于該原因,實(shí)際上,幾乎沒有研究過PP-系樹脂應(yīng)用到橡膠制品。關(guān)于使用具有由在中心的芯部和覆蓋芯部的外周的鞘部構(gòu)成的橫截面結(jié)構(gòu)的所謂的芯/鞘纖維作為加強(qiáng)構(gòu)件用的一種有機(jī)纖維已進(jìn)行各種研究。例如,專利文獻(xiàn)1公開了通過將由包括為樹脂的芯組分和為與橡膠熱熔著的熱塑性樹脂的鞘組分的芯/鞘纖維構(gòu)成的簾線嵌入未硫化橡膠中從而通過硫化將一體化而形成的簾線/橡膠復(fù)合體,所述樹脂選自聚酯、聚酰胺、聚乙烯醇、聚丙烯腈、人造絲和含雜環(huán)的聚合物中的至少一種?,F(xiàn)有技術(shù)文獻(xiàn)專利文獻(xiàn)專利文獻(xiàn)1:日本未經(jīng)審查的專利申請公布No.H10-6406(權(quán)利要求等)技術(shù)實(shí)現(xiàn)要素:發(fā)明要解決的問題此外,急需解決的一個環(huán)境問題是其中輪胎側(cè)部振動而在行駛期間產(chǎn)生噪音的現(xiàn)象。盡管輪胎側(cè)部的振動可以通過提供在輪胎側(cè)部中的如嵌入構(gòu)件等的加強(qiáng)層以解決該問題來抑制,但仍由于由覆膠的簾線層形成的正常的加強(qiáng)層常規(guī)需要浸漬處理或橡膠包覆而具有側(cè)部的厚度增加的缺點(diǎn)。因此,本發(fā)明的目的是通過使用可應(yīng)用于此類嵌入構(gòu)件等的加強(qiáng)材料借此可以得到目標(biāo)的加強(qiáng)性能而同時抑制厚度的增加來提供其中性能能夠改善而同時抑制厚度的增加的充氣輪胎。用于解決問題的方案如上所述,常規(guī)地,由于聚烯烴系樹脂例如PP-系樹脂具有相對低的熔點(diǎn),對橡膠制品的加強(qiáng)材料的應(yīng)用未進(jìn)行充分的研究。類似地,對芯/鞘纖維用作橡膠制品的加強(qiáng)材料時形成芯部的樹脂的應(yīng)用未進(jìn)行充分的研究,并且由于其中聚烯烴系樹脂如PP-系樹脂用于芯部的芯/鞘纖維推測在橡膠制品的硫化期間熔化,因此沒有其中這樣的芯/鞘纖維應(yīng)用于橡膠制品的先例。然而,本發(fā)明人實(shí)際研究發(fā)現(xiàn)了,即使當(dāng)PP簾線在硫化處理的加熱處理?xiàng)l件下在150℃至200℃、特別地約165℃至190℃的溫度下工業(yè)硫化時,在限制的硫化時間內(nèi)僅PP簾線的簾線強(qiáng)度一定程度地劣化,并且簾線的形狀或強(qiáng)度不會由于橡膠制品中的簾線的熔化而損失。因此,認(rèn)為的是其中芯部由具有高熔點(diǎn)的聚烯烴系樹脂制成和鞘部由具有低熔點(diǎn)的聚烯烴系樹脂制成并且進(jìn)行硫化而得到預(yù)定的簾線強(qiáng)度的芯/鞘纖維可用作橡膠制品的加強(qiáng)材料,并且特別地可用作嵌入構(gòu)件,雖然待使用的構(gòu)件不特別限制。從這樣的觀點(diǎn)出發(fā),本發(fā)明人進(jìn)一步研究發(fā)現(xiàn)了上述問題可以通過采用以下構(gòu)成來解決,由此完成了本發(fā)明。即,本發(fā)明的輪胎是包括如下的充氣輪胎:一對胎圈部;分別從所述一對胎圈部的輪胎徑向外側(cè)延續(xù)的一對側(cè)壁部;和在所述一對側(cè)壁部之間延伸而形成接地部的胎面部,并且包括由至少一層胎體簾布層形成的胎體層作為骨架,所述胎體簾布層在分別嵌入所述一對胎圈部的胎圈芯之間環(huán)狀延伸,其中至少在所述胎圈芯的輪胎徑向外側(cè)設(shè)置有加強(qiáng)層,所述加強(qiáng)層使用由芯/鞘型復(fù)合纖維(C)形成的加強(qiáng)材料,其中芯部由熔點(diǎn)為150℃以上的高熔點(diǎn)聚烯烴系樹脂(A)制成且鞘部由熔點(diǎn)為80℃以上且低于150℃的低熔點(diǎn)聚烯烴系樹脂(B)制成。根據(jù)本發(fā)明的輪胎中,所述加強(qiáng)材料的纖度優(yōu)選為100dtex至5,000dtex。根據(jù)本發(fā)明的輪胎中,通過將所述復(fù)合纖維(C)覆膠并硫化之后的斷裂拉伸強(qiáng)度優(yōu)選為29N/mm2以上。此外,根據(jù)本發(fā)明的輪胎中,優(yōu)選地,以所述加強(qiáng)材料的取向方向相對于所述輪胎徑向在30°至90°的范圍的方式設(shè)置所述加強(qiáng)層。仍進(jìn)一步,根據(jù)本發(fā)明的輪胎中,優(yōu)選地,在所述一對胎圈部之間延伸的所述胎體簾布層的主體部和胎圈填膠之間、并且在從所述胎圈芯的輪胎徑向外側(cè)端部到輪胎最大寬度位置的區(qū)域內(nèi)設(shè)置所述加強(qiáng)層。根據(jù)本發(fā)明的輪胎中,優(yōu)選地,由所述復(fù)合纖維(C)形成的加強(qiáng)材料沿一個方向取向并且覆膠。此外,根據(jù)本發(fā)明的輪胎中,優(yōu)選地,由所述復(fù)合纖維(C)形成的加強(qiáng)材料的纖維集合體的形式是單絲、或通過使10根以下的單絲成束而形成的簾線。發(fā)明的效果根據(jù)本發(fā)明,上述構(gòu)成使得可以實(shí)現(xiàn)通過使用可應(yīng)用于此類嵌入構(gòu)件等的加強(qiáng)材料借此可以得到目標(biāo)的加強(qiáng)性能而同時抑制厚度的增加來提供其中性能改善而同時抑制厚度的增加的充氣輪胎。附圖說明圖1是說明根據(jù)本發(fā)明的充氣輪胎的一個實(shí)例的示意性截面圖。圖2是說明根據(jù)本發(fā)明的充氣輪胎的另一個實(shí)例的示意性截面圖。圖3是說明根據(jù)本發(fā)明的充氣輪胎的又一個實(shí)例的示意性部分截面圖。圖4是說明根據(jù)本發(fā)明的充氣輪胎的又一個實(shí)例的示意性部分截面圖。圖5是說明根據(jù)本發(fā)明的充氣輪胎的又一個實(shí)例的示意性部分截面圖。圖6是說明根據(jù)本發(fā)明的充氣輪胎的又一個實(shí)例的示意性部分截面圖。圖7是說明根據(jù)本發(fā)明的充氣輪胎的又一個實(shí)例的示意性部分截面圖。圖8是說明根據(jù)本發(fā)明的充氣輪胎的又一個實(shí)例的示意性部分截面圖。圖9是說明根據(jù)本發(fā)明的充氣輪胎的又一個實(shí)例的示意性部分截面圖。圖10通過使用熒光顯微鏡觀察從根據(jù)本發(fā)明的實(shí)施例的測試輪胎取出的復(fù)合體的橡膠中的加強(qiáng)材料的截面而得到的照片。具體實(shí)施方式下文中,將參照附圖詳細(xì)地描述根據(jù)本發(fā)明的實(shí)施方案。圖1是說明根據(jù)本發(fā)明的充氣輪胎的一個實(shí)例的示意性截面圖。圖示的輪胎包括:一對胎圈部11;分別從一對胎圈部11的輪胎徑向外側(cè)延續(xù)的一對側(cè)壁部12;和在一對側(cè)壁部12之間延伸而形成接地部的胎面部13。圖示的輪胎包括由至少一層胎體簾布層形成的胎體層2作為骨架,該胎體簾布層在分別嵌入一對胎圈部11的胎圈芯1之間環(huán)狀延伸,并且包括由配置在骨架的冠部的輪胎徑向外側(cè)上的至少兩個帶束部構(gòu)成的帶束層3。盡管未示出,但氣密層設(shè)置在胎體層2的輪胎徑向內(nèi)側(cè)。圖中的符號5表示胎圈填膠。根據(jù)本發(fā)明的其他優(yōu)選實(shí)例的充氣輪胎的實(shí)例包括具有其中未埋設(shè)圖1中的胎圈填膠5的構(gòu)成的圖2中示出的輪胎。如圖所示,根據(jù)本發(fā)明的輪胎的特征在于:在至少胎圈芯1的輪胎徑向外側(cè)設(shè)置有加強(qiáng)層4,所述加強(qiáng)層4使用由芯/鞘型復(fù)合纖維(C)形成的加強(qiáng)材料,其中芯部由熔點(diǎn)為150℃以上的高熔點(diǎn)聚烯烴系樹脂(A)制成且鞘部由熔點(diǎn)為80℃以上且低于150℃的低熔點(diǎn)聚烯烴系樹脂(B)制成。通過至少在胎圈芯的輪胎徑向外側(cè),例如胎圈部11和側(cè)壁部12的至少一部分上,設(shè)置加強(qiáng)層4,抑制在輪胎側(cè)部的振動的產(chǎn)生,由此可以抑制在行駛期間的噪音的產(chǎn)生。在行駛期間的輪胎中,輪胎壁的振動的振幅越大,空氣振動,即在胎側(cè)表面上產(chǎn)生的行駛噪音越大。由于胎側(cè)表面的振動,特別地在輪胎周向上的振動通過配置這樣的加強(qiáng)層4由于復(fù)合纖維(C)的拉伸張力可以得到抑制,所以從胎側(cè)表面等產(chǎn)生的聲音降低,由此降低諸如通過噪音等噪音。由于根據(jù)本發(fā)明的加強(qiáng)層4的厚度小于由傳統(tǒng)的覆膠簾線層形成的加強(qiáng)層的厚度,所以沒有由于側(cè)部的厚度的增加而引起的缺點(diǎn)。此外,由于普通輪胎的輪胎側(cè)部在行駛期間的溫度為約60℃,所以根據(jù)本發(fā)明的使用具有相對低的熔點(diǎn)的聚烯烴系纖維的加強(qiáng)材料可應(yīng)用作橡膠構(gòu)件。仍進(jìn)一步,通過設(shè)置這樣的加強(qiáng)層4,也可以得到增加輪胎側(cè)部的剛性和改善操縱穩(wěn)定性(drivability)的效果。當(dāng)輪胎側(cè)部的所要求的剛性通過設(shè)置使用由芯/鞘型復(fù)合纖維(C)形成的加強(qiáng)材料的加強(qiáng)層4可以在不埋設(shè)胎圈填膠的情況下得到時,可以采用其中不埋設(shè)胎圈填膠的輪胎結(jié)構(gòu),這是由于可以得到輪胎耐久行駛中的充分的耐疲勞性。本發(fā)明中,加強(qiáng)層4可以設(shè)置在胎圈芯1的輪胎徑向外側(cè),借此根據(jù)本發(fā)明的降低噪音的預(yù)期的效果可以通過利用由加強(qiáng)層4中的復(fù)合纖維(C)負(fù)擔(dān)的張力改變在輪胎滾動期間的位移或應(yīng)變分布得到,并且也可以得到改善操縱穩(wěn)定性的效果。本發(fā)明中,例如,如圖1中所示,優(yōu)選地,加強(qiáng)層4配置在于一對胎圈部11之間延伸的胎體簾布層的主體部2A和胎圈填膠5之間,并且在胎圈芯1的輪胎徑向外側(cè)端部1a到輪胎最大寬度位置P的區(qū)域內(nèi),作為所謂的嵌入構(gòu)件。加強(qiáng)層4設(shè)置在此類范圍對于降低行駛期間的噪音是最有效的。圖3至5是說明根據(jù)本發(fā)明的充氣輪胎的其他實(shí)例的示意性部分截面圖。根據(jù)本發(fā)明的充氣輪胎的再一些其他實(shí)例包括圖6至8中示出的輪胎,其中不埋設(shè)胎圈填膠5、且具有圖3至5中的輪胎的構(gòu)成。本發(fā)明中,如圖3中所示,使用上述復(fù)合纖維(C)的加強(qiáng)層也可以配置在胎體層2與胎圈填膠5和胎圈芯1之間作為所謂的鋼絲圈外包布(flipper)24。鋼絲圈外包布24可以配置為圍繞胎圈芯1折返,以致輪胎寬度方向內(nèi)側(cè)端24i和輪胎寬度方向外側(cè)端24o都位于胎圈填膠5的輪胎徑向外側(cè)端5e的輪胎徑向外側(cè)。通過在此類范圍設(shè)置加強(qiáng)層24作為鋼絲圈外包布,可以得到降低在行駛期間的噪音和改善操縱穩(wěn)定性的效果。本發(fā)明中,如圖4中所示,加強(qiáng)層也可以配置在胎體簾布層的主體部2A和胎體簾布層的折返部2B外側(cè)作為所謂的胎跟加強(qiáng)層(chipper)34,所述胎體簾布層圍繞胎圈芯1沿輪胎寬度方向從內(nèi)側(cè)到外側(cè)折返并且沿輪胎寬度方向卷起以沿著主體部2A的端部2Be和胎體簾布層的折返部2B來包圍折返部2B。胎跟加強(qiáng)層34可以配置在從接近胎圈芯1到胎圈填膠5的輪胎徑向外側(cè)端5e的輪胎徑向外側(cè)的區(qū)域內(nèi)。通過在此類范圍設(shè)置加強(qiáng)層34作為胎跟加強(qiáng)層,可以得到降低在行駛期間的噪音和改善操縱穩(wěn)定性的效果。此外,本發(fā)明中,如圖5中所示,加強(qiáng)層可以配置在胎體層2的輪胎徑向內(nèi)側(cè)作為所謂的胎圈包布(chafer)44。胎圈包布44可以配置為圍繞胎圈芯1折返,以致輪胎寬度方向內(nèi)側(cè)端44i位于胎圈填膠5的輪胎徑向外側(cè)端5e的輪胎徑向外側(cè),以及輪胎寬度方向外側(cè)端44o位于胎圈芯1的輪胎徑向外側(cè)端部1a的輪胎徑向外側(cè)和胎圈填膠5的輪胎徑向外側(cè)端5e的輪胎徑向內(nèi)側(cè)。通過在此類范圍設(shè)置加強(qiáng)層44作為胎圈包布,可以得到降低在行駛期間的噪音和改善操縱穩(wěn)定性的效果。本發(fā)明中,即使當(dāng)使用上述復(fù)合纖維(C)的加強(qiáng)層配置在其中不埋設(shè)胎圈填膠5的如圖6至8中示出的輪胎中作為鋼絲圈外包布、胎跟加強(qiáng)層、或胎圈包布時,也可以得到降低在行駛期間的噪音和改善操縱穩(wěn)定性的效果。這是因?yàn)楫?dāng)本發(fā)明加強(qiáng)層的復(fù)合纖維(C)與胎體簾布層形成交叉層時,甚至在其中不埋設(shè)胎圈填膠5的輪胎的情況下,也可以將特別是在輪胎的扭轉(zhuǎn)方向上的靜態(tài)剛性維持為高的。仍進(jìn)一步,本發(fā)明中,如圖9中所示,加強(qiáng)層可以配置在從胎面部13到側(cè)壁部12的范圍作為冠部加強(qiáng)層54。在該情況下,在胎面部13上,帶束層3、覆蓋帶束層3的整個寬度的覆蓋層6、和覆蓋帶束層3的輪胎寬度方向端部的層狀層7以上述順序配置在胎體層2的冠部的輪胎徑向外側(cè),并且冠部加強(qiáng)層54配置在層狀層7的輪胎徑向外側(cè)以便埋設(shè)在胎面橡膠8中。冠部加強(qiáng)層54可以具有與覆蓋層6大致相同的寬度,并且可以例如,通過將多個由上述芯/鞘型復(fù)合纖維(C)形成的加強(qiáng)材料定向且埋設(shè)在橡膠中而形成的條帶沿輪胎寬度方向彼此間隔開、基本上沿輪胎周向螺旋地卷繞來設(shè)置。通過在此類范圍設(shè)置加強(qiáng)層54作為冠部加強(qiáng)層,可以得到改善耐久性的效果。本發(fā)明中,加強(qiáng)層4可以以加強(qiáng)材料的纖維軸向是任意的方向的方式來設(shè)置,并且優(yōu)選地以加強(qiáng)材料的取向方向相對于輪胎徑向基本上在30°至90°的范圍的方式設(shè)置,并且更優(yōu)選地以加強(qiáng)材料的取向方向相對于輪胎徑向基本上在45°至90°的范圍的方式設(shè)置。特別優(yōu)選地,加強(qiáng)層4以加強(qiáng)材料的取向方向相對于輪胎徑向基本上90°即在輪胎周向上的方式設(shè)置。關(guān)于降低噪音的效果,由于輪胎側(cè)部在輪胎橫向上的振動可以通過加強(qiáng)材料的拉伸張力來抑制,輪胎周向或輪胎徑向都得到高效果;然而,對比輪胎周向和輪胎徑向的兩種情況,當(dāng)加強(qiáng)層4以加強(qiáng)材料的取向方向在輪胎周向上的方式配置時得到更高的效果。這認(rèn)為是因?yàn)?,為了抑制由于在胎體簾布層簾線之間的空間增加而引起的位移,因?yàn)檩喬サ奶ンw簾布層簾線沿輪胎徑向設(shè)置,所以輪胎周向的情況是更有效的。關(guān)于操縱穩(wěn)定性的改善,在由借助通過當(dāng)由在胎圈芯之間環(huán)狀延伸的胎體簾布層形成的橡膠層填充有空氣時的內(nèi)壓施加的張力支撐的空氣膜形成的輪胎結(jié)構(gòu)中,期望:當(dāng)由于膜的面外方向上的凹凸的變動或屈曲造成的輪胎側(cè)部的胎體簾布層簾線之間的位移得到抑制且小時,從胎圈部到胎面部加強(qiáng)的胎體簾布層簾線的取向較少地擾亂。由于當(dāng)簾線的取向較少地擾亂時,其中在操縱車輛期間的操縱力等將應(yīng)力從車輪通過胎體簾布層傳遞至接觸地面的輪胎胎面部的過程中由于胎體簾布層簾線的取向的擾亂而應(yīng)力較為不可能傳遞的狀況更為改善,期待涉及操縱如操縱力等的應(yīng)力在膜的面內(nèi)方向的傳遞的改善,并且認(rèn)為改善了操縱穩(wěn)定性如操縱響應(yīng)性。由于特別有效地抑制胎體簾布層簾線之間的位移,加強(qiáng)層優(yōu)選沿輪胎周向配置。根據(jù)本發(fā)明的加強(qiáng)材料由其中芯部由熔點(diǎn)為150℃以上的高熔點(diǎn)聚烯烴系樹脂(A)制成且鞘部由熔點(diǎn)為80℃以上且低于150℃的低熔點(diǎn)聚烯烴系樹脂(B)制成的芯/鞘型復(fù)合纖維(C)形成。熔點(diǎn)根據(jù)JIS-K-7121通過DSC方法測量。由于用于本發(fā)明中的芯/鞘型復(fù)合纖維(C)的鞘部由低熔點(diǎn)聚烯烴系樹脂(B)制成,所以芯/鞘型復(fù)合纖維(C)有利地同時實(shí)現(xiàn)以下功能:復(fù)合纖維可以通過當(dāng)應(yīng)用于橡膠制品的加強(qiáng)時的熱熔著而直接粘著至橡膠;以及在芯部的樹脂即使在硫化處理的加熱下也不熔化的情況下可以維持簾線的拉伸剛性。當(dāng)加強(qiáng)材料如由聚烯烴系樹脂形成的纖維不是具有根據(jù)本發(fā)明的芯/鞘結(jié)構(gòu)的復(fù)合纖維等時,例如,當(dāng)加強(qiáng)材料是單一組成的單絲簾線時,不能得到本發(fā)明的效果。如上所述,對于由單一組成的聚烯烴系樹脂形成的傳統(tǒng)的單絲簾線難以同時實(shí)現(xiàn)自相矛盾的功能:加強(qiáng)材料可以通過當(dāng)應(yīng)用于橡膠制品的加強(qiáng)時的熱熔著而直接粘著至橡膠;以及即使在硫化處理中的加熱下也不使樹脂熔化的情況下可以維持簾線的拉伸剛性。然而,由于根據(jù)本發(fā)明的加強(qiáng)材料由其中芯部由熔點(diǎn)為150℃以上的高熔點(diǎn)聚烯烴系樹脂(A)制成且鞘部由熔點(diǎn)為80℃以上且低于150℃的低熔點(diǎn)聚烯烴系樹脂(B)制成的芯/鞘型復(fù)合纖維(C)形成,所以加強(qiáng)材料可以同時實(shí)現(xiàn)以下功能:加強(qiáng)材料可以通過與鞘部的樹脂熱熔著而直接粘著至橡膠;以及因?yàn)楹熅€的芯部的樹脂不熔化而維持作為加強(qiáng)材料的拉伸剛性。由于將根據(jù)本發(fā)明的加強(qiáng)材料覆膠以形成橡膠-纖維復(fù)合體并且這樣的橡膠-纖維復(fù)合體不需要其中當(dāng)與橡膠復(fù)合時傳統(tǒng)用于粘接輪胎簾線的如間苯二酚·福爾馬林·膠乳(RFL)粘合劑等的粘合劑組合物附著于復(fù)合體的浸漬處理,可以簡化粘接處理步驟。當(dāng)有機(jī)纖維和橡膠在加強(qiáng)輪胎的應(yīng)用等中通過使用粘合劑組合物粘接在一起時,通常需要將有機(jī)纖維用涂覆纖維用橡膠(膠清橡膠(SkimRubber))涂覆以確保粘接強(qiáng)度。然而,本發(fā)明的加強(qiáng)材料與胎側(cè)膠、或胎面橡膠等之間的強(qiáng)粘著力可以通過熱熔著直接獲得而不用涂覆纖維用橡膠的介入。當(dāng)有機(jī)纖維用涂覆纖維用橡膠涂覆時,需要確保涂覆的厚度在橡膠涂層不破損的程度下,因此,涂覆厚度的橡膠的重量增加,這反過來通常否定了有助于成本效率的改善的減少輪胎的重量的需求。然而,對于本發(fā)明中的粘接處理沒有這樣的限制,因此,可以提供與根據(jù)加強(qiáng)部分的橡膠種類如側(cè)胎面橡膠的復(fù)合體而沒有附加的負(fù)面影響如涂覆纖維用橡膠的重量的增加。另一方面,盡管在此類芯/鞘型復(fù)合纖維(C)中,芯部由高熔點(diǎn)聚烯烴系樹脂(A)制成,但是芯部即使在如上所述的橡膠的硫化處理中也不熔化。在本發(fā)明人的研究中,根據(jù)本發(fā)明的芯/鞘型復(fù)合纖維(C)在作為高于一般工業(yè)硫化條件的溫度的195℃下硫化15分鐘,觀察埋設(shè)入硫化橡膠中的簾線的截面,并且本發(fā)明人發(fā)現(xiàn)了,雖然鞘部的低熔點(diǎn)聚烯烴系樹脂(B)的圓形截面通過熔化而變形,但芯部的高熔點(diǎn)聚烯烴系樹脂(A)的圓形截面的形狀在芯/鞘復(fù)合體紡絲之后仍維持,并且簾線不變成完全的熔融體,以及纖維斷裂強(qiáng)度維持為150N/mm2以上。如上所述,本發(fā)明人發(fā)現(xiàn)了,當(dāng)簾線芯部的樹脂的熔點(diǎn)為150℃以上時,獲得其中即使當(dāng)簾線在橡膠制品的硫化期間于195℃下進(jìn)行加熱處理時簾線既不熔化也不斷裂的根據(jù)本發(fā)明的橡膠加強(qiáng)材料。據(jù)認(rèn)為維持了簾線材料的強(qiáng)度并且甚至在如上所述的樹脂的固有熔點(diǎn)的加工溫度下簾線也具有耐熱性,這是因?yàn)椴幌窀鶕?jù)其中熔點(diǎn)在沒有限制樹脂的形狀的情況下測量的JIS-K7121等的方法中,由于埋設(shè)入橡膠中的簾線在長度恒定的情況下硫化,并且簾線處于其中纖維不收縮的恒定長度限制的條件,其熔點(diǎn)變得比樹脂的固有熔點(diǎn)高。公開了這樣的纖維在其中作為纖維材料在特定狀況下的熱現(xiàn)象的纖維不收縮的"恒定長度限制"測量條件下可具有高的熔點(diǎn)(第二版,纖維手冊,1994年3月25日發(fā)行,編者:TheSocietyofFiberScienceandTechnology,日本,出版社:MaruzenCo.,Ltd.,第207頁第13行)。然而,之前從未知道關(guān)于適合于加強(qiáng)橡膠制品用的樹脂材料的發(fā)現(xiàn):其中推測在根據(jù)JIS方法的樹脂熔點(diǎn)或更高的溫度下變成熔融體的根據(jù)本發(fā)明的聚烯烴系樹脂材料和簾線材料在對應(yīng)于橡膠硫化過程的溫度下研究,以及該材料通過熱熔著直接粘著至橡膠,同時,芯部的樹脂即使在硫化過程的加熱下也不熔化。由于上述芯/鞘型復(fù)合纖維(C)由均通過聚烯烴系樹脂制成的芯部和鞘部形成,所以不像其中不同種類的樹脂用于芯部和鞘部的情況,在芯/鞘聚合物界面的粘合力強(qiáng),并且得到關(guān)于芯部/鞘部之間的界面剝離的充分的耐剝離反應(yīng)力,由此可以長時間地展現(xiàn)復(fù)合纖維的充分的性能。此外,根據(jù)本發(fā)明的加強(qiáng)材料可以在不用浸漬處理或橡膠涂覆的情況下與橡膠熔著,由此特別是當(dāng)根據(jù)本發(fā)明的橡膠-纖維復(fù)合體用于加強(qiáng)輪胎時的薄的規(guī)格而有助于輪胎的輕量化。用于本發(fā)明中的高熔點(diǎn)聚烯烴系樹脂(A)可以具有150℃以上、優(yōu)選160℃以上的熔點(diǎn)。當(dāng)高熔點(diǎn)聚烯烴系樹脂(A)的熔點(diǎn)小于150℃時,復(fù)合纖維(C)的芯部熔化并且變形從而在橡膠制品的硫化期間變成薄的,或者纖維樹脂的分子的取向劣化,由此未得到充分的加強(qiáng)性能。用于本發(fā)明中的低熔點(diǎn)聚烯烴系樹脂(B)的熔點(diǎn)的下限可以在80℃以上的范圍,優(yōu)選為125℃以上,并且進(jìn)一步優(yōu)選為130℃以上。當(dāng)?shù)腿埸c(diǎn)聚烯烴系樹脂(B)的熔點(diǎn)小于80℃時,熔融樹脂的粘度變得太低,并且在硫化期間的熱流動性變得太高。生成其中鞘部的厚度由于硫化期間的壓力而變薄的部分,并且在粘合測試等中的應(yīng)變應(yīng)力集中于鞘部的樹脂薄的部分,由此在這樣的部分中的斷裂很可能會出現(xiàn)。因此,低熔點(diǎn)聚烯烴系樹脂(B)的熔點(diǎn)需要為80℃以上。當(dāng)?shù)腿埸c(diǎn)聚烯烴系樹脂(B)的熔點(diǎn)為125℃以上時,橡膠和低熔點(diǎn)聚烯烴系樹脂熱熔著,同時,硫化交聯(lián)反應(yīng)可以對橡膠組合物在作為可工業(yè)上用于已添加硫磺和硫化促進(jìn)劑的橡膠組合物的硫化處理溫度的130℃以上的溫度下進(jìn)行,這是優(yōu)選的。當(dāng)?shù)腿埸c(diǎn)聚烯烴系樹脂(B)的熔點(diǎn)為130℃以上時,低熔點(diǎn)聚烯烴系樹脂(B)的鞘樹脂的強(qiáng)度變高,并且當(dāng)剝離橡膠和鞘部的復(fù)合體時,鞘部的樹脂的耐斷裂性變高,由此橡膠和鞘部的復(fù)合體的粘接強(qiáng)度變高,這是更優(yōu)選的。在其中硫化溫度設(shè)定為170℃以便工業(yè)上減少硫化時間的情況下,當(dāng)?shù)腿埸c(diǎn)聚烯烴系樹脂(B)的熔點(diǎn)的上限小于150℃時,由于低熔點(diǎn)聚烯烴系樹脂(B)的熱流動性可以得到在于作為高溫的175℃以上的硫化溫度下的硫化早期階段與橡膠組合物的相容性。當(dāng)?shù)腿埸c(diǎn)聚烯烴系樹脂(B)的熔點(diǎn)小于145℃時,可以得到在于普通的硫化溫度下的硫化早期階段與橡膠組合物的相容性,這是優(yōu)選的。低熔點(diǎn)聚烯烴系樹脂(B)優(yōu)選為具有低熔點(diǎn)的樹脂和具有高軟化溫度的樹脂。因?yàn)檫@樣意味著熔點(diǎn)越低,即使當(dāng)加工溫度低時,樹脂也越可能熔著,雖然樹脂甚至在高溫下也不太可能軟化,這是優(yōu)選的特征??捎米鞲呷埸c(diǎn)聚烯烴系樹脂(A)和低熔點(diǎn)聚烯烴系樹脂(B)的聚烯烴系樹脂的具體實(shí)例包括聚乙烯、聚丙烯、聚1-丁烯、聚3-甲基-1-丁烯、聚1-戊烯、聚1-己烯、聚4-甲基-1-戊烯、聚1-辛烯、聚1-癸烯、聚1-十二碳烯、聚1-十四碳烯、聚1-十六碳烯、聚1-十八碳烯、聚1-二十碳烯、聚苯乙烯、聚對甲基苯乙烯、聚異丙基苯乙烯、和聚叔丁基苯乙烯。其中,熔點(diǎn)為150℃以上的結(jié)晶性聚丙烯優(yōu)選用于高熔點(diǎn)聚烯烴系樹脂(A),并且結(jié)晶性聚丙烯的實(shí)例包括丙烯均聚物、乙烯-丙烯無規(guī)共聚物和乙烯-丙烯嵌段共聚物。高結(jié)晶性丙烯均聚物是特別優(yōu)選的。對于低熔點(diǎn)聚烯烴系樹脂(B),可以適當(dāng)?shù)厥褂镁郾┗蚓垡蚁┑鹊木酆衔铩⒒蚱浠旌衔?,或通過可與聚丙烯共聚的組分和聚丙烯共聚而形成的聚丙烯系共聚物樹脂等等。對于高熔點(diǎn)聚烯烴系樹脂(A)和低熔點(diǎn)聚烯烴系樹脂(B)的組合,從芯部和鞘部之間有利的相容性的觀點(diǎn)出發(fā),優(yōu)選的是熔點(diǎn)為150℃以上的結(jié)晶性丙烯均聚物用于芯部的高熔點(diǎn)聚烯烴系樹脂(A),并且通過可與聚丙烯共聚的組合和聚丙烯共聚而形成的聚丙烯系共聚物樹脂如乙烯-丙烯共聚物或乙烯-丁烯-丙烯三元共聚物用于鞘部的低熔點(diǎn)聚烯烴系樹脂(B)。聚丙烯系共聚物樹脂中的共聚用單體的共聚形式的實(shí)例包括無規(guī)共聚物和嵌段共聚物,這是優(yōu)選的,因?yàn)樵黾恿嗽谂c橡膠的界面的粘接性??膳c聚丙烯共聚的共聚用單體的實(shí)例包括α-烯烴、非共軛二烯和可與其他聚丙烯共聚的單體。用作共聚用單體的單體不限于一種,并且可以優(yōu)選使用其中使用兩種以上的單體的多組分共聚物如三元共聚物。α-烯烴的實(shí)例包括其中碳原子數(shù)為2或4至20個的那些,具體地是乙烯、1-丁烯、1-戊烯、1-己烯、1-辛烯、1-庚烯、4-甲基-戊烯-1、4-甲基-己烯-1、和4,4-二甲基戊烯-1。非共軛二烯的實(shí)例包括5-乙叉基-2-降冰片烯、二環(huán)戊二烯和1,4-己二烯。特別地,優(yōu)選的是將非共軛二烯引入乙烯和丙烯作為第三組分,這是因?yàn)楫?dāng)含有乙烯-丙烯-二烯共聚物(EPDM)的組分時,含有了在與待粘接的橡膠的界面處具有粘著性且具有由于硫磺的共硫化性的組分。丙烯系共聚物樹脂的制造方法的實(shí)例包括淤漿聚合,氣相聚合,或者使用烯烴聚合催化劑如齊格勒催化劑或茂金屬催化劑的液相本體聚合,以及作為聚合方法,可以使用任何間歇聚合和連續(xù)聚合。低熔點(diǎn)聚烯烴系樹脂(B)是作為本發(fā)明中定義的熔點(diǎn)范圍的樹脂組合物的聚烯烴系樹脂的組合物或乙烯-丙烯無規(guī)共聚物,所述聚烯烴系樹脂例如是聚乙烯或聚丙烯的均聚物,并且這些的混合樹脂組合物已知具有相分離的結(jié)構(gòu)。為了促進(jìn)通過添加由軟鏈段和硬鏈段形成的嵌段共聚物而造成的各相之間的界面的相容性,可以使用增容劑。這些增容劑優(yōu)選包括具有在為芯組分的高熔點(diǎn)聚烯烴系樹脂(A)和為鞘組分的低熔點(diǎn)聚烯烴系樹脂(B)之間的界面的粘接性的鏈段、或者具有與鞘組分和待粘著的橡膠中含有的苯乙烯·丁二烯橡膠(SBR)、丁二烯橡膠(BR)、丁基橡膠(IIR)和具有聚異戊二烯結(jié)構(gòu)的天然橡膠(IR)等的分子結(jié)構(gòu)的相互作用的鏈段,這是因?yàn)閷Υ持南鹉z的粘接性改善。此類增容劑的實(shí)例包括苯乙烯-丁二烯系聚合物、聚苯乙烯-聚(乙烯/丙烯)系嵌段共聚物、苯乙烯-異戊二烯系嵌段聚合物、以及其中苯乙烯和丁二烯的這些嵌段共聚物的雙鍵被氫化的完全氫化或部分氫化的聚合物。苯乙烯-丁二烯系聚合物的具體實(shí)例包括苯乙烯-二烯聚合物(SBS)、苯乙烯-乙烯·丁二烯共聚物(SEB)、苯乙烯-乙烯·丁二烯-苯乙烯共聚物(SEBS)、苯乙烯-丁二烯·丁烯-苯乙烯共聚物(SBBS)、和部分氫化的苯乙烯-異戊二烯·丁二烯-苯乙烯共聚物。聚苯乙烯-聚(乙烯/丙烯)系嵌段聚合物的實(shí)例包括聚苯乙烯-聚(乙烯/丙烯)嵌段共聚物(SEP)、聚苯乙烯-聚(乙烯/丙烯)嵌段-聚苯乙烯(SEPS)、聚苯乙烯-聚(乙烯/丁烯)嵌段-聚苯乙烯(SEBS)、和聚苯乙烯-聚(乙烯-乙烯/丙烯)嵌段-聚苯乙烯(SEEPS)。苯乙烯-異戊二烯系嵌段聚合物的實(shí)例包括聚苯乙烯-聚異戊二烯-聚苯乙烯共聚物(SIS)。除了上述由軟鏈段和硬鏈段形成的嵌段共聚物之外,低熔點(diǎn)聚烯烴系樹脂(B)可以含有交聯(lián)至聚丙烯系共聚物的熱塑性橡膠(TPV),或JISK6418中記載的熱塑性彈性體的分類中的"其他熱塑性彈性體(TPZ)"等,以用于提高與待粘著的橡膠組合物的界面的粘接性的目的。這些可以將部分或高度交聯(lián)的橡膠微細(xì)分散至低熔點(diǎn)聚烯烴系樹脂(B)的熱塑性樹脂組合物的基質(zhì)的連續(xù)相中。交聯(lián)的熱塑性橡膠的實(shí)例包括丙烯腈-丁二烯橡膠、天然橡膠、環(huán)氧化天然橡膠、丁基橡膠和乙烯·丙烯·二烯橡膠。其他熱塑性彈性體(TPZ)的實(shí)例包括間同立構(gòu)的-1,2-聚丁二烯樹脂和反式-聚異戊二烯樹脂。此外,向根據(jù)本發(fā)明的聚烯烴系樹脂中,可以在本發(fā)明的效果或在紡絲期間的操作性等不顯著讓步以便增加其他特性如耐氧化性的程度下添加通常添加至聚烯烴系樹脂的添加劑。對于此類添加劑組分,用作聚烯烴樹脂用的添加劑的各種傳統(tǒng)已知的添加劑如成核劑、抗氧化劑、中和劑、光穩(wěn)定劑、紫外線吸收劑、潤滑劑、抗靜電劑、填料、金屬鈍化劑、過氧化物、抗菌殺菌劑、或熒光增白劑、或其他添加劑可以使用。添加劑的具體實(shí)例包括,如成核劑,2,2-亞甲基-雙(4,6-二叔丁基苯基)磷酸鈉、滑石、山梨糖醇系化合物如1,3,2,4-二(對甲基亞芐基)山梨糖醇、和羥基-二-叔丁基苯甲酸鋁??寡趸瘎┑膶?shí)例包括酚系抗氧化劑如三-(3,5-二叔丁基-4-羥基芐基)異氰脲酸酯、1,1,3-三(2-甲基-4-羥基-5-叔丁基苯基)丁烷、十八烷基-3-(3,5-二叔丁基-4-羥基苯基)丙酸酯、季戊四醇基-四{3-(3,5-二叔丁基-4-羥基苯基)丙酸酯}、1,3,5-三甲基-2,4,6-三(3,5-二叔丁基-4-羥基芐基)苯、3,9-雙[2-{3-(3-叔丁基-4-羥基-5-甲基苯基)丙酰氧基}-1,1-二甲基乙基]-2,4,8,10-四氧雜螺[5,5]十一烷、和1,3,5-三(4-叔丁基3-羥基-2,6-二甲基芐基)異氰脲酸。磷系抗氧化劑的實(shí)例包括三(混合的,單-和二-壬基苯基亞磷酸酯)、三(2,4-二叔丁基苯基)亞磷酸酯、4,4'-亞丁基雙(3-甲基-6-叔丁基苯基-二-十三烷基)亞磷酸酯、1,1,3-三(2-甲基-4-二-十三烷基亞磷酸酯-5-叔丁基苯基)丁烷、雙(2,4-二叔丁基苯基)季戊四醇-二亞磷酸酯、四(2,4-二叔丁基苯基)-4,4'-亞聯(lián)苯基二亞磷酸酯、四(2,4-二叔丁基-5-甲基苯基)-4,4'-亞聯(lián)苯基二亞磷酸酯、和雙(2,6-二叔丁基-4-甲基苯基)季戊四醇-二亞磷酸酯。硫系抗氧化劑的實(shí)例包括二硬脂基硫代二丙酸酯、二肉豆蔻基硫代二丙酸酯、和季戊四醇-四-(3-月桂基硫代丙酸酯)。中和劑的實(shí)例包括硬脂酸鈣、硬脂酸鋅和水滑石。受阻胺系穩(wěn)定劑的實(shí)例包括琥珀酸二甲酯和1-(2-羥乙基)-4-羥基-2,2,6,6-四甲基哌啶的縮聚物,四(1,2,2,6,6-五-4-哌啶基)1,2,3,4-丁烷四羧酸酯,雙(1,2,2,6,6-五甲基-4-哌啶基)癸二酸酯,N,N-雙(3-氨基丙基)乙二胺·2,4-雙{N-丁基-N-(1,2,2,6,6-五甲基-4-哌啶基)氨基}-6-氯-1,3,5-三嗪縮合物,雙(2,2,6,6-四甲基-4-哌啶基)癸二酸酯,聚[{6-(1,1,3,3-四甲基丁基)亞氨基-1,3,5-三嗪-2,4-二基}{(2,2,6,6-四甲基-4-哌啶基)亞氨基}六亞甲基{2,2,6,6-四甲基-4-哌啶基}亞氨基],和聚[(6-嗎啉代-s-三嗪-2,4-二基)[(2,2,6,6-四甲基-4-哌啶基)亞氨基]六亞甲基{(2,2,6,6-四甲基-4-哌啶基)亞氨基}]。潤滑劑的實(shí)例包括高級脂肪酸酰胺,如油酸酰胺、硬脂酸酰胺、山萮酸酰胺、或乙烯雙硬脂酰胺;硅油;和高級脂肪酸酯。抗靜電劑的實(shí)例包括高級脂肪酸的甘油酯,烷基二乙醇胺,烷基二乙醇酰胺,和烷基二乙醇酰胺的脂肪酸單酯。填料的實(shí)例包括無機(jī)顆粒狀載體如蒙皂石族,蛭石族,或云母族,例如氧化鋁、二氧化硅-氧化鋁、氯化鎂、碳酸鈣、滑石、蒙脫石、鋅蒙脫石(zakonite)、貝得石、綠脫石、皂石、鋰蒙脫石、硅鎂石、斑脫土、或帶云母;和多孔有機(jī)載體,例如聚丙烯、聚乙烯、聚苯乙烯、苯乙烯-二乙烯基苯共聚物、或丙烯酸類共聚物。例如,在其中鞘部的耐斷裂性不充分并且在鞘部中產(chǎn)生裂紋致破損的情況下,這些填料可以作為用于當(dāng)鞘部粘接至待粘著的橡膠時加強(qiáng)鞘部的填料添加。紫外線吸收劑的實(shí)例包括2-羥基-4-正辛氧基二苯甲酮、2-(2'-羥基-3',5'-二叔丁基苯基)-5-氯苯并三唑、和2-(2'-羥基-3'-叔丁基-5'-甲基苯基)-5-氯苯并三唑。光穩(wěn)定劑的實(shí)例包括正十六烷基-3,5-二叔丁基-4-羥基苯甲酸酯、2,4-二叔丁基苯基-3',5'-二叔丁基-4'-羥基苯甲酸酯、雙(2,2,6,6-四甲基-4-哌啶基)癸二酸酯、琥珀酸二甲基-2-(4-羥基-2,2,6,6-四甲基-1-哌啶基)乙醇酯縮合物、聚{[6-〔(1,1,3,3-四甲基丁基)氨基〕-1,3,5-三嗪-2,4-二基]〔(2,2,6,6-四甲基-4-哌啶基)亞氨基〕六亞甲基〔(2,2,6,6-四甲基-4-哌啶基)亞氨基〕}、和N,N'-雙(3-氨基丙基)乙二胺-2,4-雙〔N-丁基-N-(1,2,2,6,6-五甲基-4-哌啶基)氨基〕-6-氯-1,3,5-三嗪縮合物。本發(fā)明中,更適當(dāng)?shù)?,聚丙烯系樹脂均用于高熔點(diǎn)聚烯烴系樹脂(A)和低熔點(diǎn)聚烯烴系樹脂(B)。例如,由于聚丙烯樹脂具有0.91的比重,聚丙烯樹脂由于其低比重而可以有利地減輕輪胎的重量。當(dāng)PP-系樹脂用作構(gòu)成芯部的高熔點(diǎn)聚烯烴系樹脂(A)時,盡管PP-系樹脂的模量比傳統(tǒng)用于輪胎簾線的高彈性簾線如尼龍、聚酯或芳綸的低,但其彈性模量在傳統(tǒng)的簾線和橡膠的那些之間,由此可以將PP-系樹脂提供給在輪胎制造期間接受張力的橡膠制品,這通過傳統(tǒng)的輪胎簾線尚未實(shí)現(xiàn)。例如,在諸如輪胎等橡膠制品中,存在如下的工藝:其中裝配由橡膠或涂覆的簾線材料形成的構(gòu)件,將成型的未硫化的原形如生胎放入模具中,并且將成型的未硫化的原形通過高溫·高壓蒸汽使用稱為氣囊的橡膠球狀壓縮設(shè)備從內(nèi)側(cè)壓向模具。在該工藝中,當(dāng)提供給成型的未硫化的原形如生胎的簾線的模量太高時,簾線各材料的延伸率在加壓過程中通過高溫和高壓蒸汽變大的部分中不延伸,并且作為所謂的"切螺紋(cuttingthread)"(切割塊狀物如粘土的螺紋等)從而割斷橡膠,這使得難以提供這樣的簾線給輪胎。特別地,當(dāng)輪胎周向上的簾線配置在輪胎側(cè)部上從而以不具有自由端的環(huán)形形狀連接時,大的擴(kuò)張力通過高溫·高壓蒸汽加壓很可能被施加至簾線,因此,可伸展的材料如PP-系樹脂是優(yōu)選的。聚丙烯系樹脂,與傳統(tǒng)用于輪胎簾線的尼龍、聚酯或芳綸等相比,具有如下的性能:其中在張力沿簾線方向在其中制造橡膠制品的硫化過程的加熱期間施加這樣的情況下,當(dāng)簾線方向上的拉伸應(yīng)變大時,蠕變出現(xiàn),并且樹脂更加可能被拉出,而當(dāng)簾線方向上的拉伸應(yīng)變小時,樹脂在簾線方向上熱收縮,由此簾線松弛較不可能出現(xiàn),這是優(yōu)選的。具體地,關(guān)于通過模具在硫化之后制造的橡膠制品的設(shè)計的形狀,該性能使得容易制造具有設(shè)計的形狀的橡膠制品,因?yàn)楹熅€本身與即使當(dāng)提供的簾線在未硫化的原形的成型和制造時松弛或移位時的輪胎的形狀一致地延伸或收縮,這是優(yōu)選的。此外,由于聚丙烯系樹脂是撓性的并且其結(jié)晶度不是太高,甚至推測通過在壓縮輸入下因疲勞相對大幅劣化的單絲簾線的強(qiáng)度的劣化也被抑制,這是有利的。關(guān)于本發(fā)明中的復(fù)合纖維(C)中的芯部和鞘部的比例,復(fù)合纖維(C)中的芯部的比例優(yōu)選為10至95質(zhì)量%。當(dāng)芯部的比例太低時,復(fù)合纖維(C)的強(qiáng)度會劣化并且不會獲得充分的加強(qiáng)性能。特別地,當(dāng)芯部的比例為50質(zhì)量%以上時,可以改善加強(qiáng)性能,這是優(yōu)選的。另一方面,當(dāng)芯部的比例太高時,復(fù)合纖維(C)的芯部很可能由于鞘部的比例太低而露出,并且不會獲得充分的對橡膠的粘接性。本發(fā)明中,高熔點(diǎn)聚烯烴系樹脂(A)的熔體流動指數(shù)(熔體流動速率,MFR)(MFR1)和低熔點(diǎn)聚烯烴系樹脂(B)的熔體流動指數(shù)(MFR2)都不特別限制,只要它們在其中紡絲是可行的范圍即可,并且優(yōu)選為0.3至100g/10min。高熔點(diǎn)聚烯烴系樹脂(A)的熔體流動指數(shù)(熔體流動速率,MFR)(MFR1)優(yōu)選為選自0.3至15g/10min、更優(yōu)選為0.5至10g/10min、特別優(yōu)選為1至5g/10min的范圍的指數(shù)。這是因?yàn)?,?dāng)高熔點(diǎn)聚烯烴系樹脂(A)的MFR在上述范圍時,得到有利的紡絲卷取性(pinningtake-upproperty)和拉伸性,并且芯部的高熔點(diǎn)聚烯烴系樹脂(A)的熔融體在其中制造橡膠制品的硫化過程的加熱下不流動,由此維持簾線的形式。低熔點(diǎn)聚烯烴系樹脂(B)的熔體流動指數(shù)(MFR2)優(yōu)選為5g/10min以上,更優(yōu)選為5至70g/10min,特別優(yōu)選為5至30g/10min。為了增加鞘部的低熔點(diǎn)聚烯烴系樹脂(B)的熱熔著性(thermalfusibility),具有高M(jìn)FR的樹脂是優(yōu)選的,因?yàn)檫@樣的樹脂在與待粘著的橡膠的間隙內(nèi)可以流動并且填充。另一方面,當(dāng)MFR太高時,在其中接近待配置的復(fù)合纖維(C)存在諸如簾布層簾線或胎圈芯等其他加強(qiáng)構(gòu)件、以及涂覆復(fù)合纖維(C)的橡膠具有間隙的情況下,低熔點(diǎn)聚烯烴系樹脂(B)的熔融體可在簾布層簾線或胎圈芯的纖維材料的表面上潤濕鋪展,因此MFR特別優(yōu)選為70g/10min以下。當(dāng)MFR為30g/10min以下時,當(dāng)待粘著的橡膠剝離時鞘部的樹脂的耐斷裂性變高,由此樹脂強(qiáng)固地粘著至橡膠,這是進(jìn)一步優(yōu)選的。MFR(g/10min)的值是根據(jù)JIS-K-7210的。對于聚丙烯系樹脂材料的熔體流動速率,可以使用在230℃的溫度、21.18N(2160g)的負(fù)荷下測量的值;對于聚乙烯系樹脂材料的熔體流動速率,可以使用在190℃的溫度、21.18N(2160g)的負(fù)荷下測量的值。本發(fā)明中,復(fù)合纖維(C)的加強(qiáng)材料的纖維集合體的形式不特別限制,并且優(yōu)選為單絲或通過使10根以下的單絲成束而形成的簾線,并且進(jìn)一步優(yōu)選為單絲簾線。這是因?yàn)?,?dāng)本發(fā)明中的復(fù)合纖維(C)的纖維集合體為通過使10根以上的單絲成束而形成的簾線、加捻的簾線、無紡布或織物的纖維形式時,因?yàn)楫?dāng)纖維集合體在橡膠中硫化時構(gòu)成鞘部的低熔點(diǎn)聚烯烴系樹脂(B)熔化,并且熔融體相互滲透從而在一些情況下在橡膠制品中形成大塊異物,長絲相互熔著。當(dāng)這樣的異物生成時,在使用輪胎時由于滾動引起的應(yīng)變,裂紋從橡膠制品中的大塊異物起發(fā)展,并且可以造成分裂。因?yàn)樵撛?,?dāng)復(fù)合纖維(C)在橡膠制品中形成纖維集合體時,可以成束的長絲的數(shù)量越大,橡膠越不可能在簾線之間滲透,并且大塊異物越可能形成,因此通常,待成束的長絲的數(shù)量優(yōu)選為10根以下。復(fù)合纖維(C)優(yōu)選以單絲的纖維形式作為諸如充氣輪胎的鋼絲圈外包布等加強(qiáng)材料提供給輪胎側(cè)壁部,這是由于抑制由于輪胎側(cè)部的胎體簾布層簾線之間的空間的增加而造成的位移的效果提高,并且改善諸如操作響應(yīng)性等操縱穩(wěn)定性。這是因?yàn)?,在與輪胎側(cè)部的胎體簾布層簾線交叉的加強(qiáng)材料使用非加捻的單絲的情況下,與由多根長絲形成的加捻的簾線相比,在其中多根長絲的加捻結(jié)構(gòu)打開或關(guān)閉的纖維中的形式?jīng)]有變化,因此,當(dāng)胎體簾布層簾線之間的間隙增加或減少時的位移小。本發(fā)明中,加強(qiáng)材料的纖度即纖維粗細(xì)優(yōu)選在100dtex至5,000dtex的范圍。當(dāng)加強(qiáng)材料的纖維粗細(xì)小于100dtex時,簾線很可能由于其低強(qiáng)度而斷裂。特別地在輪胎的情況下,為了抑制在當(dāng)制造輪胎時的各種過程的加工期間的簾線斷裂,加強(qiáng)材料的纖維粗細(xì)更優(yōu)選為500dtex以上。加強(qiáng)材料的纖維粗細(xì)的上限不特別限定,只要加強(qiáng)材料可以提供給如輪胎等橡膠制品的各構(gòu)件,并且優(yōu)選為5,000dtex以下,特別優(yōu)選為4,000dtex以下。這是因?yàn)?,在單絲簾線的情況下,當(dāng)纖維粗細(xì)在紡絲期間大時,在加工期間的成本效率劣化,因?yàn)榧徑z速度降低,此外,因?yàn)楫?dāng)膠絲(thread)圍繞如線筒等繞線工具卷繞時,膠絲由于膠絲的厚度大而難以彎曲,由此劣化操作性。本發(fā)明中的纖維粗細(xì)意味著在使用單絲的情況下對于單一的單絲和在使用成束的單絲的情況下對于通過使單絲成束而形成的簾線測量的纖維尺寸(根據(jù)JISL0101)。此外,對于用于根據(jù)本發(fā)明的橡膠-纖維復(fù)合體的涂覆橡膠,可以使用根據(jù)待加強(qiáng)的橡膠制品和待施加的涂覆橡膠的位置酌情選擇的橡膠種類,但是不特別限于此。橡膠種類優(yōu)選為含有在其主鏈包括雙鍵的二烯橡膠的橡膠組合物,特別優(yōu)選為進(jìn)一步含有硫磺系硫化劑的橡膠組合物。二烯橡膠的實(shí)例包括天然橡膠、異戊二烯橡膠、丁二烯橡膠、丁苯橡膠和氯丁橡膠。二烯橡膠優(yōu)選為包括天然橡膠和丁二烯橡膠的橡膠組合物。由復(fù)合纖維(C)形成的加強(qiáng)材料的長度適當(dāng)?shù)貫?0mm以上,并且越長越優(yōu)選。當(dāng)由復(fù)合纖維(C)形成的加強(qiáng)材料的長度小到小于10mm時,在與橡膠一體化的情況下使諸如與橡膠的混煉和擠出等方法成必要,這使得難以使加強(qiáng)材料沿一個方向取向并且覆膠。短纖維和長纖維之間的差異對應(yīng)于纖維的端部作為自由端的作用和纖維的端部作為固定端的作用之間的差異。因?yàn)槔w維越長,通過適當(dāng)?shù)嘏渲孟鹉z-纖維復(fù)合體,作為長纖維的特征的拉伸承受能力可以越好地改善,目標(biāo)性能可以在諸如輪胎等橡膠制品中容易地獲得。根據(jù)本發(fā)明的橡膠-纖維復(fù)合體中,由復(fù)合纖維(C)形成的加強(qiáng)材料優(yōu)選沿一個方向取向并且覆膠。通過使由復(fù)合纖維(C)形成的加強(qiáng)材料沿一個方向取向來待使用,施加至橡膠的張力可以由加強(qiáng)材料負(fù)擔(dān),并且可以獲得當(dāng)將材料應(yīng)用于加強(qiáng)輪胎的應(yīng)用時改善耐切割性的效果、或分散輪胎中的應(yīng)力的效果等。當(dāng)張力通過利用作為纖維的固有性能的各向異性而由加強(qiáng)材料負(fù)擔(dān)時,橡膠的使用量可以通過利用纖維軸向上的強(qiáng)度而減少,由此可以獲得通過輪胎由于其輕量化造成的改善每英里汽油消耗量(gasmileage)的效果。根據(jù)本發(fā)明的復(fù)合體中的加強(qiáng)材料的打緯密度(endcount)優(yōu)選為每5mm寬度0.5至20根。當(dāng)打緯密度太小時,不會獲得充分的加強(qiáng)效果,而當(dāng)打緯密度太大時,簾線的間隔變小,并且當(dāng)簾線相互接觸時,鞘部的低熔點(diǎn)聚烯烴系樹脂(B)在加熱下在纖維之間潤濕鋪展并且熔著的現(xiàn)象可易于出現(xiàn),這是不優(yōu)選的。根據(jù)本發(fā)明的復(fù)合體可以在每一個加強(qiáng)部分中以一層或多層設(shè)置,只要在制造待加強(qiáng)的橡膠制品時不出現(xiàn)問題即可,并且待設(shè)置的層的數(shù)量不特別限制。如上所述,根據(jù)本發(fā)明的橡膠-纖維復(fù)合體可以適當(dāng)?shù)赜糜诩訌?qiáng)諸如輪胎等各種橡膠制品,并且可以得到目標(biāo)的加強(qiáng)性能而同時抑制橡膠制品的厚度的增加。特別地,當(dāng)根據(jù)本發(fā)明的復(fù)合體用于加強(qiáng)輪胎時,與作為通過維持輪胎內(nèi)壓承擔(dān)輪胎的強(qiáng)度的骨架相比,復(fù)合體作為出于通過抑制輪胎的振動或聲音而改善輪胎等的操縱穩(wěn)定性、改善耐切割性、或改善降低輪胎變形期間的應(yīng)變的效果的目的與骨架材料一起使用的嵌入構(gòu)件更有用。通過將根據(jù)本發(fā)明的加強(qiáng)材料覆膠形成的橡膠-纖維復(fù)合體在硫化之后的斷裂拉伸強(qiáng)度適當(dāng)?shù)貫?9N/mm2以上,更適當(dāng)?shù)貫?0N/mm2以上,并且進(jìn)一步適當(dāng)?shù)貫?50N/mm2以上,并且斷裂拉伸強(qiáng)度越高,復(fù)合體越優(yōu)選。從輪胎中挖出的簾線的纖維強(qiáng)度適當(dāng)?shù)貫?.0cN/dtex以上,并且進(jìn)一步適當(dāng)?shù)貫?.7cN/dtex以上。關(guān)于根據(jù)本發(fā)明的復(fù)合纖維(C)的鞘部,盡管鞘部與橡膠熔著且在橡膠的加工期間的硫化溫度下熱變形,芯部也難以熱變形,因此,復(fù)合纖維(C)在纖維軸向上不熔斷。因?yàn)樵撛颍巯N系樹脂部分沿著纖維軸向連續(xù)地提供,由此得到29N/mm2以上的斷裂強(qiáng)度。通過這樣做,這樣的復(fù)合體變?yōu)榫哂谐浞值睦w維軸向上的橡膠斷裂強(qiáng)度的各向異性材料,因此,其中提供這樣的復(fù)合體的橡膠制品可以得到諸如承擔(dān)特定方向上的應(yīng)變等的功能。當(dāng)斷裂拉伸強(qiáng)度小于29N/mm2時,不會得到硫化之后的橡膠制品的充分的加強(qiáng)性能。即使在其中根據(jù)本發(fā)明的橡膠-纖維復(fù)合體在待加強(qiáng)的橡膠制品的期望位置上提供、然后在150℃至200℃的一般硫化溫度下硫化的情況下,也可以獲得充分的加強(qiáng)性能。因?yàn)樵撛颍@樣的復(fù)合體可以展現(xiàn)作為諸如輪胎等橡膠制品的加強(qiáng)材料的充分的加強(qiáng)性能,所述加強(qiáng)材料例如如上所述的加強(qiáng)胎圈部和側(cè)壁部的應(yīng)用如插件(insert)、鋼絲圈外包布、胎跟加強(qiáng)層和胎圈包布以及加強(qiáng)胎面部如冠部加強(qiáng)層的應(yīng)用。根據(jù)本發(fā)明的輪胎可以在生胎成型時通過將上述根據(jù)本發(fā)明的復(fù)合體配置在胎圈部11、側(cè)壁部12和胎面部13當(dāng)中的待加強(qiáng)的期望區(qū)域上、然后根據(jù)傳統(tǒng)方法在150℃至190℃的硫化溫度下進(jìn)行硫化3至50分鐘來制造。具體地,例如,當(dāng)在胎圈部11或側(cè)壁部12中以加強(qiáng)材料的纖維軸向?yàn)檩喬ブ芟虻姆绞皆O(shè)置加強(qiáng)層4時,可以提供復(fù)合體而形成沿輪胎徑向的螺旋地卷繞的結(jié)構(gòu)。例如,當(dāng)在胎面部13中以加強(qiáng)材料的纖維軸向?yàn)檩喬ブ芟虻姆绞皆O(shè)置加強(qiáng)層4時,可以提供形成沿輪胎周向的螺旋地卷繞的結(jié)構(gòu)的復(fù)合體。實(shí)施例下文中,通過實(shí)施例的方式更詳細(xì)地描述本發(fā)明。[乙烯-丙烯共聚物的制造](1)固體催化劑的前體混合物的合成在乙烯-丙烯共聚物的制造中,首先,關(guān)于Ti-Mg固體催化劑的前體的合成,裝配有滴液漏斗和攪拌器的1-升燒瓶的內(nèi)部用氮?dú)庵脫Q,然后,400mL己烷、103g四乙氧基硅烷和11g四丁氧基鈦放入該燒瓶中,并且將混合物在30℃下攪拌1小時。接下來,向混合物中,在維持燒瓶的溫度在5℃下的同時通過使用滴液漏斗經(jīng)3小時滴加250mL濃度為2.1mol/L的丁基氯化鎂的二丁基醚溶液。滴液完成之后,將混合物在5℃下攪拌1小時,然后在20℃下攪拌1小時,接著過濾。生成的固體首先用350mL甲苯反復(fù)洗滌3次,接下來,將300mL甲苯添加至其中來使其淤漿化,接著減壓干燥以除去溶劑,由此獲得棕色的固體催化劑組分的前體。(2)Ti-Mg固體催化劑的合成裝配有滴液漏斗和攪拌器的100mL燒瓶的內(nèi)部用氮?dú)庵脫Q,然后,35mL甲苯、72g四氯硅烷、和47.5g鄰苯二甲酸二(2-乙基己酯)放入該燒瓶中。7g在(1)中合成的固體催化劑組分的前體進(jìn)給入該燒瓶中,接著在105℃下攪拌3小時。其后,將攪拌后的混合物通過過濾進(jìn)行固液分離,并且將過濾和分離的固體用500mL甲苯在95℃下洗滌3次,接著添加300mL甲苯。其后,將混合物的溫度升高至70℃,然后65g四氯化鈦添加至其中,接著在105℃下攪拌1小時。接下來,進(jìn)行固液分離,并且將所得固體在95℃下用500mL甲苯反復(fù)洗滌6次。其后,將混合物在室溫下用500mL己烷洗滌2次,并且將洗滌后的固體干燥,由此獲得71g固體催化劑組分。(3)乙烯-丙烯共聚物的制造向裝配有攪拌器的1升容積的不銹鋼高壓釜中,稱入100g氯化鈉,并且將高壓釜的壓力在85℃下減壓且將高壓釜真空干燥。其后,將高壓釜的內(nèi)部用氬氣置換并且在常壓、60℃下穩(wěn)定化,然后添加丙烯直至0.25MPa,隨后,添加乙烯以致乙烯的量為40質(zhì)量%直至0.84MPa。其后,將6mL戊烷、1毫摩爾三乙基鋁和52.1mg在(2)中制備的Ti-Mg固體催化劑組分的混合物放入氬氣加壓的高壓釜從而開始聚合。在開始聚合之后,提供乙烯的量為40質(zhì)量%的乙烯和丙烯的混合物氣體,同時將單體分壓在63℃下調(diào)節(jié)至0.84MPa,并且持續(xù)攪拌4小時來聚合。在聚合完成之后,將所生成的產(chǎn)物從高壓釜中取出,1升水添加至其中,接著攪拌1小時,然后進(jìn)行過濾來真空干燥,由此獲得30g乙烯-丙烯共聚物。所得乙烯-丙烯共聚物在230℃下的MFR值為13g/10min,熔融峰溫度(熔點(diǎn))為132℃。[芯/鞘型復(fù)合纖維和覆膠簾線的單絲的制造]將下表2中列出的芯/鞘型復(fù)合纖維的單絲沿一個方向取向并且覆膠從而制造橡膠-纖維復(fù)合體。作為單絲的打緯密度的條件,采用每5mm寬度6根。作為材料的熱塑性樹脂,使用下表1中列出的樹脂(PP-1、PP-2、PP-3、TPE-1、TPE-2、PE-1),將其使用真空干燥器干燥。兩個的單軸擠出機(jī)用于芯材料和鞘材料,并且使用具有1.5mm孔的芯/鞘型復(fù)合體紡絲噴絲頭,熔融紡絲在19.5g/min的芯組分的排出量、13.0g/min的鞘組分的排出量、和70m/min的紡絲速度下進(jìn)行,以致鞘/芯比率的質(zhì)量比為4:6。其后,在98℃的熱水浴中進(jìn)行拉伸從而得到4.0-倍,并且熔融紡絲在270℃的芯部的紡絲溫度和240℃的鞘部的紡絲溫度下進(jìn)行,由此獲得具有下表2中示出的纖度的芯/鞘型復(fù)合體單絲。[表1]<實(shí)施例1至7,比較例1>使用195/55R15的輪胎尺寸,制造了實(shí)施例1的充氣輪胎,其包括:一對胎圈部;分別從一對胎圈部11的輪胎徑向外側(cè)延續(xù)的一對側(cè)壁部;和在一對側(cè)壁部之間延伸而形成接地部的胎面部。該測試輪胎包括由一層胎體簾布層形成的胎體層作為骨架,并且包括由配置在胎體層的冠部的輪胎徑向外側(cè)上的兩個帶束部構(gòu)成的帶束層。如圖1中所示,在測試輪胎的胎體簾布層的主體部和胎圈填膠之間,在每5mm寬度6根的打緯密度下、在具有45mm的從胎圈芯的輪胎徑向外側(cè)端部到輪胎最大寬度位置P的寬度的側(cè)壁部的區(qū)域中以加強(qiáng)材料的取向方向基本上在輪胎周向上的方式設(shè)置下表2中列出的芯/鞘單絲作為上述橡膠-纖維復(fù)合體的芯/鞘復(fù)合纖維。制造輪胎中的硫化條件是在189℃的硫化溫度下11min。實(shí)施例2至7和比較例1中,除了采用使用所得的具有如下表2示出的纖度的芯/鞘型復(fù)合體單絲、通過改變排出量、同時保持基于質(zhì)量比的鞘/芯比率為4:6的橡膠-纖維復(fù)合體之外,實(shí)施例2至7和比較例1的充氣輪胎以與實(shí)施例1的類似的方式制造。<實(shí)施例8>實(shí)施例8中,除了采用使用所得的具有如下表2示出的纖度的芯/鞘型復(fù)合體單絲、通過改變排出量、同時保持基于質(zhì)量比的鞘/芯比率為4:6的橡膠-纖維復(fù)合體,以及以加強(qiáng)材料的取向方向相對于輪胎徑向基本上為45°的方式設(shè)置上述橡膠-纖維復(fù)合體之外,實(shí)施例8的充氣輪胎以與實(shí)施例1的類似的方式制造。<傳統(tǒng)例>除了具有相同厚度且不包括加強(qiáng)材料的橡膠構(gòu)件代替上述橡膠-纖維復(fù)合體配置以外,傳統(tǒng)例的充氣輪胎以與實(shí)施例1的類似的方式制造。將各實(shí)施例中的所得的測試輪胎切開從而從內(nèi)部取出橡膠-纖維復(fù)合體,并且測量其斷裂拉伸強(qiáng)度。將各所得的測試輪胎安裝至實(shí)際車輛,并且車輛在測試過程中行駛來測量通過噪音。這些結(jié)果在表2中組合列出。關(guān)于通過將橡膠從實(shí)施例和比較例的各測試輪胎取出的復(fù)合體剝離而得到的加強(qiáng)材料的表面的橡膠附著狀態(tài),根據(jù)下表3進(jìn)行評級等級的確定從而確認(rèn)橡膠附著率(覆膠)。將所得測試輪胎安裝至實(shí)際車輛,并且車輛在測試過程中行駛來通過駕駛員的感觀評價來評價操縱穩(wěn)定性。結(jié)果中,將其中不配置加強(qiáng)材料的傳統(tǒng)例設(shè)定為標(biāo)準(zhǔn)(±0),并且與傳統(tǒng)例的差異通過具有"+"或"-"的數(shù)值表示。具有"+"的數(shù)值越大,性能越優(yōu)異。[表2]*1)比較例1中,由于輪胎在轉(zhuǎn)鼓試驗(yàn)中破損,所以未進(jìn)行輪胎試驗(yàn)。*2)根據(jù)JISL1013的化學(xué)纖維長絲紗線試驗(yàn)方法進(jìn)行密度和纖度的測量。[表3]橡膠附著率(橡膠附著)的評級涂覆橡膠相對于長絲表面積的面積比A大于80%至100%B大于60%至80%C大于40%至60%D大于20%至40%E0%至20%如在上述表2中列出的,在其中使用預(yù)定的芯/鞘型復(fù)合纖維的橡膠-纖維復(fù)合體作為加強(qiáng)材料至少配置在從胎圈芯起的輪胎徑向的外側(cè)區(qū)域上的各實(shí)施例的測試輪胎中,確認(rèn)了,與其中不配置加強(qiáng)材料的傳統(tǒng)例的測試輪胎相比,行駛期間的噪音降低,同時,獲得改善操縱穩(wěn)定性的效果。實(shí)施例1至8任一個的橡膠附著評級是A至C,與具有與芯組分大致相同的高熔點(diǎn)的164℃熔點(diǎn)的聚丙烯聚合物單絲的橡膠附著評級E相比,粘接狀態(tài)確認(rèn)為更有利的。如圖10的照片中所示的,在從實(shí)施例1的測試輪胎中取出的復(fù)合體的橡膠內(nèi)的加強(qiáng)材料的截面通過熒光顯微鏡觀察,從而發(fā)現(xiàn)了,在鞘部流體化且變形的同時,芯部不熔化。這里,圖10是通過使用熒光顯微鏡觀察從實(shí)施例的測試輪胎中取出的復(fù)合體的橡膠內(nèi)的加強(qiáng)材料的截面而得到的照片。圖10中,周向區(qū)域G是復(fù)合體的硫化橡膠,并且在附圖的中心的橢圓形區(qū)域PH是芯/鞘纖維(C)的芯部的高熔點(diǎn)聚烯烴系樹脂(A)的部分。在為硫化橡膠的周向區(qū)域G與為芯部的樹脂部分的附圖的中心的橢圓形區(qū)域PH之間的區(qū)域PL是鞘部的低熔點(diǎn)聚烯烴系樹脂(B)的熔融層。該照片中,鞘部是本發(fā)明中定義的低熔點(diǎn)聚烯烴系樹脂(B),并且發(fā)現(xiàn)了鞘部在由模具和氣囊形成的硫化設(shè)備中在硫化期間通過高溫·高壓蒸汽從內(nèi)側(cè)壓向模具從而使鞘部的低熔點(diǎn)聚烯烴系樹脂(B)通過加熱變?yōu)槿廴隗w,導(dǎo)致變形,其中形態(tài)通過加壓模具壓縮的力而變形,并且流體化的樹脂潤濕鋪展從而填充橡膠與纖維之間的間隙,由此通過熔化獲得強(qiáng)的粘接。與變形的鞘部相比,芯部維持橢圓形式,且是本發(fā)明中定義的高熔點(diǎn)聚烯烴系樹脂(A),因此不熔化為熔融體,并且如實(shí)施例中所示,維持纖維斷裂強(qiáng)度。因此,發(fā)現(xiàn)了橡膠制品的加強(qiáng)材料所需要的簾線剛性的功能未喪失。因此,通過本發(fā)明中定義的芯/鞘纖維(C),熱熔著性和簾線強(qiáng)度的保持二者都可以在橡膠制品的硫化條件下實(shí)現(xiàn),因此,可以提供完全未出現(xiàn)的適合于加強(qiáng)橡膠制品的手段。附圖標(biāo)記說明1胎圈芯1a胎圈芯的輪胎徑向外側(cè)端部2胎體層2A胎體簾布層的主體部2B胎體簾布層的折返部2Be胎體簾布層的折返部的端部3帶束層4加強(qiáng)層5胎圈填膠5e胎圈填膠的輪胎徑向外側(cè)端6覆蓋層7層狀層8胎面橡膠11胎圈部12側(cè)壁部13胎面部24鋼絲圈外包布24i鋼絲圈外包布的輪胎寬度方向內(nèi)側(cè)端24o鋼絲圈外包布的輪胎寬度方向外側(cè)端34胎跟加強(qiáng)層44胎圈包布44i胎圈包布的輪胎寬度方向內(nèi)側(cè)端44o胎圈包布的輪胎寬度方向外側(cè)端54冠部加強(qiáng)層G復(fù)合體的硫化橡膠PH芯部的高熔點(diǎn)聚烯烴系樹脂PL鞘部的低熔點(diǎn)聚烯烴系樹脂當(dāng)前第1頁1 2 3