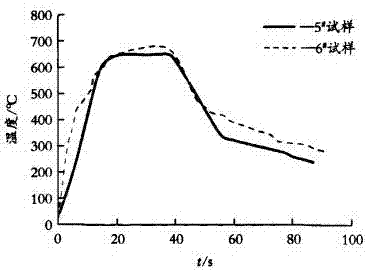
本發(fā)明涉及電泳涂料領域,尤其涉及一種熱防護電泳涂料;相應地,本發(fā)明還涉及一種熱防護電泳涂料的制備方法;相應地,本發(fā)明還涉及一種熱防護電泳涂膜。
背景技術:
:環(huán)氧樹脂類電泳涂料作為熱防護涂料,將該種涂料涂于工件表面,由于在爐頭工作時會產(chǎn)生較大的熱效應。這時,采用熱防護電泳涂料涂覆在爐頭形成涂膜可以很好保護爐頭工件,確保爐頭的正常工作?,F(xiàn)有普通環(huán)氧樹脂類的電泳涂料是包括樹脂以及填料組成的一種復合材料,配方中的固體顆粒粒徑一般達到80μm,當使用電泳涂裝技術將涂料粘附在工件形成涂膜后,由于樹脂對調(diào)料產(chǎn)生的浸潤能力不足,在350℃以上高溫加熱之后,表層的涂膜會出現(xiàn)較為明顯的龜裂以及粗糙等問題,這極大地影響到其工作性能。同時,普通環(huán)氧樹脂類電泳涂料涂層在350℃以上高溫加熱之后,整體結構將會出現(xiàn)明顯的下降,一旦溫度繼續(xù)上升,將導致漆膜裂紋,甚至焚燒、破壞等問題,直接影響涂層隔熱效果,威脅到爐頭的使用性能和使用壽命。因此,進一步對熱防護電泳涂料性能的改進將對提高相關器件的工作時整體性能具有積極作用。技術實現(xiàn)要素:本發(fā)明所要解決的技術問題在于,提供一種熱防護電泳涂料及其制備方法、涂膜,具有優(yōu)良的熱防護效果,較小的防護面密度、較強的強度和粘附能力,受熱后涂膜不出現(xiàn)起泡、脫落、龜裂、焚燒破壞等問題。為了解決上述技術問題,本發(fā)明提供了一種熱防護電泳涂料,采用砂磨機研磨涂料至固體顆粒粒徑1-20μm,所述涂料包括以下按重量份計的原料制成:環(huán)氧樹脂200-220份;醇醚溶劑12-20份;有機酸5-7份;乳化劑1-2份;催干劑25-35份;高嶺土100-120份;炭黑60-80份;溶劑15-30份;純水320-350份。作為所述熱防護電泳涂料的優(yōu)選技術方案,所述醇醚溶劑為乙二醇丁醚或乙二醇乙醚。作為所述熱防護電泳涂料的優(yōu)選技術方案,所述有機酸為冰醋酸或甲酸。相應地,本發(fā)明還公開一種熱防護電泳涂料的制備方法,包括以下步驟:(1)按配比稱取環(huán)氧樹脂、醇醚溶劑、有機酸、乳化劑、催干劑、高嶺土、炭黑、溶劑、純水;(2)將上述原料投入分散釜中,攪拌分散1小時;(3)將分散后的物料使用砂磨機多次砂磨,直至固體顆粒粒度在1-20μm時,制得本發(fā)明所述熱防護電泳涂料。作為所述熱防護電泳涂料的制備方法的優(yōu)選技術方案,步驟(1)中包括以下按重量份計的原料:環(huán)氧樹脂200-220份;醇醚溶劑12-20份;有機酸5-7份;乳化劑1-2份;催干劑25-35份;高嶺土100-120份;炭黑60-80份;溶劑15-30份;純水320-350份。作為所述熱防護電泳涂料的制備方法的優(yōu)選技術方案,所述步驟(3)采用刮板細度計判斷涂料的固體顆粒粒度是否符合生產(chǎn)要求。相應地,本發(fā)明還提供一種熱防護電泳涂膜,采用所述熱防護電泳涂料經(jīng)電泳涂裝制得的涂膜,涂膜厚度為8-12μm。實施本發(fā)明,具有如下有益效果:本發(fā)明所述熱防護電泳涂料通過多次研磨使得固體顆粒粒徑在1-20μm范圍內(nèi),在涂層耐高溫燒蝕后,能保持平整、光滑且緊密的漆膜外觀,減少涂層高溫燒蝕后裂紋等弊病出現(xiàn),從而增強涂料涂層的防護作用,延長工件的使用壽命。而且使用本發(fā)明的涂層只需8-12μm厚度即可達到最佳使用效果,使用量更小,使用成本低,具有較強的市場競爭力。本發(fā)明對熱防護電泳涂料的性能改進、擴大熱防護電泳涂料的使用范圍,具有十分重大的意義。附圖說明圖1是實驗一試樣1#、2#、3#和4#表層溫度曲線;圖2是實驗二試樣5#和6#表層溫度曲線。具體實施方式為使本發(fā)明的目的、技術方案和優(yōu)點更加清楚,下面將結合附圖對本發(fā)明作進一步地詳細描述。普通環(huán)氧樹脂類的電泳涂料是包括樹脂以及填料組成的一種復合材料,配方中的固體顆粒粒徑一般達到80μm,特別是當涂膜的厚度較薄時,由于樹脂對調(diào)料產(chǎn)生的浸潤能力不足,在350℃以上高溫加熱之后,表層的涂膜會出現(xiàn)較為明顯的龜裂以及粗糙等問題,影響涂層隔熱效果,降低工件的使用性能,縮短工件使用壽命。為此,為了改善現(xiàn)有用于熱防護的環(huán)氧樹脂類電泳涂料,本發(fā)明人分析比較影響熱防護電泳涂料涂層性能的因素,通過改進涂料的細度和施工工藝,杜絕了涂層加熱時出現(xiàn)的表面龜裂現(xiàn)象,表面粗糙程度也得到明顯降低,涂層的力學性能得到了提高,同時涂料施工的工藝性也得到了改善。本發(fā)明提供一種熱防護電泳涂料,采用砂磨機研磨涂料至固體顆粒粒徑1-20μm,所述涂料包括以下按重量份計的原料制成:環(huán)氧樹脂200-220份;醇醚溶劑12-20份;有機酸5-7份;乳化劑1-2份;催干劑25-35份;高嶺土100-120份;炭黑60-80份;溶劑15-30份;純水320-350份。本發(fā)明所述熱防護電泳涂料包括樹脂、填料(高嶺土)和顏料(炭黑)組成的一種復合材料,當填料和顏料研磨越細時,樹脂對填料和顏料產(chǎn)生的浸潤能力就越強,而樹脂與填料、顏料之間的粘附能力也越大;經(jīng)過研磨處理之后的樹脂體積減小,而表面積有所增加,使得分子的表面能增大,導致分子之間的作用力明顯增強,有利于樹脂與填料、顏料之間的有效粘接;因為樹脂的熱分解溫度較低,在進行加熱試驗時涂層的樹脂受熱分解,導致填料留在涂層的表面,而這時如果粒度越小,則涂層的表面光潔度將有所增加。下面通過對比實驗進一步說明實驗一:使用多次研磨后的涂料與一次研磨后的涂料分別涂裝后涂膜在模擬加熱實驗表面裂紋程度、表面粗糙程度的對比。1、實驗對象試樣1#、2#、3#和4#,各試樣具體制備方法、條件如表1所示:表1不同粒度模擬試驗的方法及條件試樣涂料制作涂膜燒蝕條件燒蝕后處理1#研磨一次350℃以上高溫燒蝕30s250mpa高壓氣流對涂層進行沖刷30s2#研磨一次350℃以上高溫燒蝕30s不處理3#研磨四次350℃以上高溫燒蝕30s250mpa高壓氣流對涂層進行沖刷30s4#研磨四次350℃以上高溫燒蝕30s不處理2、實驗方法2.1在相同的升溫條件下對上述試樣1#、2#、3#和4#涂料制備的四種涂膜的表面溫度的檢測,記錄數(shù)據(jù)并繪制成曲線。2.2使用4倍放大鏡對試樣1#、2#、3#和4#涂料制備的四種涂膜表面裂紋情況和表面粗糙情況進行觀察。3、實驗結果圖1中顯示的是試樣1#、2#、3#和4#表層溫度曲線。表2為試樣1#、2#、3#和4#在模擬加熱實驗結果。表2不同試樣的加熱實驗及其結果試樣涂料固體顆粒粒徑(μm)涂層厚度(μm)涂層燒蝕情況表面裂紋情況表面粗糙情況1#801024s時溫度達到最高溫度700℃平均每平方厘米出現(xiàn)2-3條裂紋,裂紋長度0.50mm-25.00mm,裂紋寬度0.01-0.05mm。平均每平方厘米出現(xiàn)5-6個凸起裂紋,表面較3#試樣粗糙2#801025s時溫度達到最高溫度700℃平均每平方厘米出現(xiàn)2-3條裂紋,裂紋長度0.50mm-25.00mm,裂紋寬度0.01-0.03mm。平均每平方厘米出現(xiàn)5-6個凸起裂紋,表面較4#試樣粗糙3#101024s時溫度達到最高溫度700℃無裂紋平均每平方厘米出現(xiàn)0.2-0.3個凸起裂紋,表面比1#試樣平整4#101030s時溫度達到最高溫度720℃無裂紋平均每平方厘米出現(xiàn)0.2-0.3個凸起裂紋,表面比2#試樣平整從圖1和表2的實驗結果分析,在工件上熱效應溫度曲線基本相同的條件下,當粒度為80μm的涂料制備的涂層,經(jīng)燒蝕等處理之后的表層出現(xiàn)了較為明顯的龜裂,而且表面質(zhì)量較為粗糙;而當粒度為10μm的涂料制備的涂層,經(jīng)燒蝕等處理之后,保持了很好的表面狀態(tài),龜裂問題基本得到解決,粗糙度也得到明顯改善。相應地,本發(fā)明還公開一種熱防護電泳涂料的制備方法,包括以下步驟:(1)按配比稱取環(huán)氧樹脂、醇醚溶劑、有機酸、乳化劑、催干劑、高嶺土、炭黑、溶劑、純水;(2)將上述原料投入分散釜中,攪拌分散1小時;(3)將分散后的物料使用砂磨機多次砂磨,直至固體顆粒粒度在1-20μm時,制得本發(fā)明所述熱防護電泳涂料。優(yōu)選地,步驟(1)中包括以下按重量份計的原料:環(huán)氧樹脂200-220份;醇醚溶劑12-20份;有機酸5-7份;乳化劑1-2份;催干劑25-35份;高嶺土100-120份;炭黑60-80份;溶劑15-30份;純水320-350份。優(yōu)選地,所述步驟(3)采用刮板細度計判斷涂料的固體顆粒粒度是否符合生產(chǎn)要求。一般來說,重復四次研磨工序可使涂料中的固體顆粒粒度達到標準。相應地,本發(fā)明還提供一種熱防護電泳涂膜,采用所述熱防護電泳涂料經(jīng)電泳涂裝制得的涂膜,涂膜厚度為8-12μm。實驗二:涂膜厚度對涂料層龜裂與粗糙度的影響1、實驗對象試樣5#和6#,各試樣具體制備方法、條件如表3所示:表3不同膜厚模擬試驗的方法及條件試樣涂層制作涂層燒蝕條件燒蝕后處理5#涂層膜厚25μm350℃以上高溫燒蝕30s不處理6#涂層膜厚10μm350℃以上高溫燒蝕30s不處理使用磷化鋼板為底材,使用80v電壓、28-30℃條件下電泳3min,得到厚度為10μm的涂層,得到6#試樣;使用150v電壓、28-30℃條件下電泳3min,得到厚度為25μm的涂層,得到5#試樣。純水洗凈表面后,180℃條件下烘烤30min制板,并檢測漆膜性能。2、實驗方法2.1在相同的升溫條件下對上述試樣5#和6#涂料制備的四種涂膜的表面溫度的檢測,記錄數(shù)據(jù)并繪制成曲線。2.2使用4倍放大鏡對試樣5#和6#涂料制備的四種涂膜表面裂紋情況和表面粗糙情況進行觀察。3、實驗結果圖2中顯示的是試樣5#和6#表層溫度曲線。表4為試樣5#和6#在模擬加熱實驗結果。表4不同試樣加熱實驗結果試樣涂料固體顆粒粒徑(μm)涂層厚度(μm)涂層燒蝕情況表面裂紋情況表面粗糙情況5#102516s時溫度達到最高溫度650℃平均每平方厘米出現(xiàn)0.2-0.5條裂紋,深度較大,局部甚至可以看到底部的殼體材質(zhì)。平均每平方厘米出現(xiàn)0.5-0.7個凸起裂紋,表面比6#試樣粗糙。6#101038s是溫度達到最高溫度680℃幾乎無裂紋。平均每平方厘米出現(xiàn)0.2-0.3個凸起裂紋,表面比5#試樣平整。從圖2和表4的實驗結果進行分析,涂層厚度在10μm的6#試樣,比涂層厚度在25μm的5#試樣,性能要更優(yōu)異。本發(fā)明人通過對配方成分、成膜原理和實驗結果進行分析,發(fā)現(xiàn)當涂膜較厚時,由于涂料固化過程中溶劑沒有參與到化學反應中,導致溶劑不能得到充分的揮發(fā),涂料固化之后的內(nèi)部將會出現(xiàn)疏松的孔隙,導致一些深度裂紋的存在。而涂膜厚度在8-12μm時,則涂料的溶劑充分揮發(fā),所成涂膜平整、光滑且緊密,涂覆在在工件表面的熱效應溫度曲線表現(xiàn)相近,而涂料的使用量更小,使用成本低,具有較強的市場競爭力。綜上所述,本發(fā)明所述熱防護電泳涂料通過多次研磨使得固體顆粒粒徑在1-20μm范圍內(nèi),在涂層耐高溫燒蝕后,能保持平整、光滑且緊密的漆膜外觀,減少涂層高溫燒蝕后裂紋等弊病出現(xiàn),從而增強涂料涂層的防護作用,延長工件的使用壽命。而且使用本發(fā)明的涂層只需8-12μm厚度即可達到最佳使用效果,使用量更小,使用成本低,具有較強的市場競爭力。本發(fā)明對熱防護電泳涂料的性能改進、擴大熱防護電泳涂料的使用范圍,具有十分重大的意義。下面通過具體實施例進一步說明:實施例1(1)按配比稱取200份環(huán)氧樹脂、18份醇醚溶劑、6份有機酸、1份乳化劑、28份催干劑、100份高嶺土、70份炭黑、25份溶劑、325份純水;(2)將上述原料投入分散釜中,攪拌分散1小時;(3)將分散后的物料使用砂磨機多次砂磨,直至固體顆粒粒度在12μm時,制得本發(fā)明所述熱防護電泳涂料。實施例2(1)按配比稱取220份環(huán)氧樹脂、16份醇醚溶劑、5份有機酸、2份乳化劑、30份催干劑、120份高嶺土、80份炭黑、20份溶劑、350份純水;(2)將上述原料投入分散釜中,攪拌分散1小時;(3)將分散后的物料使用砂磨機多次砂磨,直至固體顆粒粒度在10μm時,制得本發(fā)明所述熱防護電泳涂料。實施例3(1)按配比稱取210份環(huán)氧樹脂、15份醇醚溶劑、7份有機酸、2份乳化劑、32份催干劑、110份高嶺土、75份炭黑、16份溶劑、330份純水;(2)將上述原料投入分散釜中,攪拌分散1小時;(3)將分散后的物料使用砂磨機多次砂磨,直至固體顆粒粒度在15μm時,制得本發(fā)明所述熱防護電泳涂料。實施例4(1)按配比稱取215份環(huán)氧樹脂、18份醇醚溶劑、6份有機酸、1份乳化劑、30份催干劑、115份高嶺土、65份炭黑、30份溶劑、340份純水;(2)將上述原料投入分散釜中,攪拌分散1小時;(3)將分散后的物料使用砂磨機多次砂磨,直至固體顆粒粒度在10μm時,制得本發(fā)明所述熱防護電泳涂料。實施例5(1)按配比稱取212份環(huán)氧樹脂、16份醇醚溶劑、7份有機酸、2份乳化劑、25份催干劑、120份高嶺土、60份炭黑、20份溶劑、320份純水;(2)將上述原料投入分散釜中,攪拌分散1小時;(3)將分散后的物料使用砂磨機多次砂磨,直至固體顆粒粒度在15μm時,制得本發(fā)明所述熱防護電泳涂料。最后所應當說明的是,以上實施例僅用以說明本發(fā)明的技術方案而非對本發(fā)明保護范圍的限制,盡管參照較佳實施例對本發(fā)明作了詳細說明,本領域的普通技術人員應當理解,可以對本發(fā)明的技術方案進行修改或者等同替換,而不脫離本發(fā)明技術方案的實質(zhì)和范圍。當前第1頁12