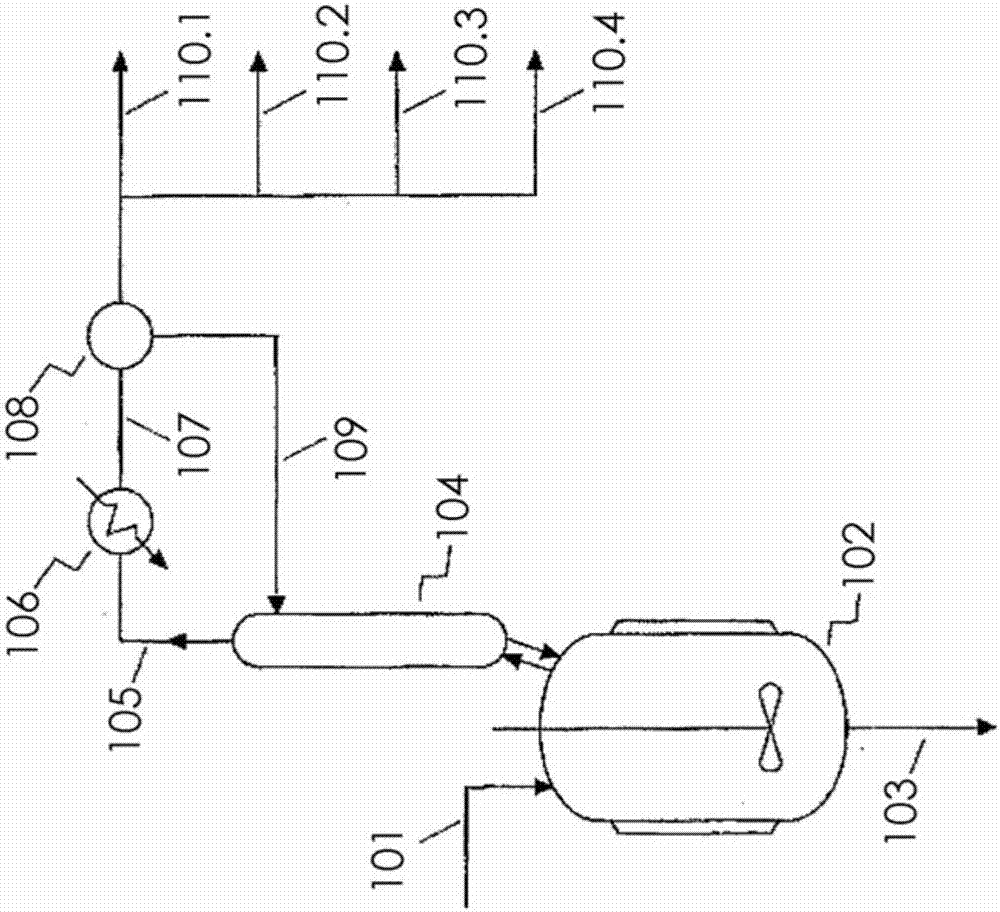
本發(fā)明涉及用于制備高純度的氯化c3-6烷烴化合物例如四氯丙烷、五氯丙烷、五氯丁烷和七氯己烷的方法,以及包含此類化合物的組合物。鹵代烷烴可用在一系列應用中。例如,鹵代烴廣泛用作制冷劑、發(fā)泡劑和起泡劑。在二十世紀下半葉,氯氟代烷烴的使用一直成指數(shù)增長,直到20世紀80年代,當時對它們的環(huán)境影響提出了關注,特別是關于臭氧層的消耗。隨后,氟化烴例如全氟碳和氫氟碳已被用于代替氯氟代烷烴,但最近已經提出了關于使用該類化合物的環(huán)境問題,并且已在歐盟和其它地方頒布立法以減少其使用。新興的環(huán)保型鹵代烴正在出現(xiàn)并被調查,在一些情況下用于多種應用中,尤其是在汽車和家庭用品領域中作為制冷劑。此類化合物的實例包括1,1,1,2-四氟乙烷(r-134a)、2-氯-3,3,3-三氟丙烯(hfo-1233xf)、1,3,3,3-四氟丙烯(hfo-1234ze)、3,3,3-三氟丙烯(hfo-1243zf)和2,3,3,3-四氟丙烯(hfo-1234yf)、1,2,3,3,3-五氟丙烯(hfo-1225ye)、1-氯-3,3,3-三氟丙烯(hfo-1233zd)、3,3,4,4,4-五氟丁烯(hfo-1345zf)、1,1,1,4,4,4-六氟丁烯(hfo-1336mzz)、3,3,4,4,5,5,5-七氟戊烯(hfo1447fz)、2,4,4,4-四氟丁-1-烯(hfo-1354mfy)和1,1,1,4,4,5,5,5-八氟戊烯(hfo-1438mzz)。雖然這些化合物相對來說在化學上并不復雜,但它們以所需的純度水平在工業(yè)規(guī)模上的合成具有挑戰(zhàn)性。為此類化合物提出的許多合成路線越來越多地使用氯化烷烴或烯烴作為原材料或中間體。歷史上,用于制備此類化合物而開發(fā)的許多方法涉及向氟化烯烴中添加氯化烷烴。然而,此類方法被認為是不可接受地有效的并且導致許多雜質的產生。最近開發(fā)的方法通常更直接,并且涉及使用氟化氫和過渡金屬催化劑例如基于鉻的催化劑將氯化烷烴或烯烴原材料或原料轉化為氟化目標化合物。已經認識到,當從多步驟方法獲得氯化原料時,尤其是如果這樣的步驟連接并連續(xù)運行以達到工業(yè)上可接受的產物體積,則在每個工藝步驟防止累積的副反應產生不可接受的雜質的需要非常重要。氯化原材料的純度對用于制備所需氟化產物的方法(尤其是連續(xù)方法)的成功和可行性具有重要影響。某些雜質的存在會導致副反應,從而使所需化合物的產率最小化。甚至使用強化蒸餾步驟來移除這些雜質也具有挑戰(zhàn)性。另外,某些雜質的存在會通過例如使催化劑中毒而損害催化劑壽命。因此,需要制備用于合成上述氟化化合物以及其它特殊化合物的高純度氯化烷烴的有效、可靠和高選擇性的方法。在本領域,例如us6187978、us6313360、us2008/091053、us6552238、us6720466、jp2013-189402和us2014/0171698中已經提出了用于制備純化的氯化化合物的幾種方法。盡管有這些進展,通過使用從上述方法獲得的氯化化合物仍然產生問題。特別地,雜質,特別是不容易與目標化合物分離(例如由于沸點接近)或者降低下游過程中使用的催化劑有效性或工作壽命的那些雜質的存在可能是有問題的。為了將這些缺點降低到最少,對于高純度的氯化烷烴化合物,以及用于制備此類化合物的有效、可靠和高選擇性的方法仍然存在需求。因此,根據(jù)本發(fā)明的一個方面,提供一種用于制備氯化c3-6烷烴的方法,其包括:在主烷基化區(qū)中提供包含烯烴和四氯化碳的反應混合物,以在所述反應混合物中產生氯化c3-6烷烴,以及從所述主烷基化區(qū)提取一部分反應混合物,其中:a)將所述主烷基化區(qū)中的反應混合物中的氯化c3-6烷烴的濃度保持在這樣的水平,使得當所述主烷基化區(qū)在連續(xù)操作中時從所述烷基化區(qū)提取的反應混合物中氯化c3-6烷烴:四氯化碳的摩爾比·在所述主烷基化區(qū)連續(xù)操作的情況下,不超過95:5,或者·在所述主烷基化區(qū)分批操作的情況下,不超過99:1;和/或b)從所述主烷基化區(qū)提取的反應混合物另外包含烯烴,并且使所述反應混合物經歷脫烯化步驟,其中所述存在于反應混合物中的烯烴的至少約50重量%或更多由其提取,并且至少約50%的提取的烯烴被返回進料至所述主烷基化區(qū)中提供的反應混合物中;和/或c)存在于所述主烷基化區(qū)中的反應混合物以及從所述主烷基化區(qū)提取的反應混合物另外包含催化劑,并且使從所述主烷基化區(qū)提取的反應混合物經歷水性處理步驟,其中使所述反應混合物與水性介質在水性處理區(qū)中接觸,形成兩相混合物,并從所述兩相混合物提取包含催化劑的有機相。本發(fā)明的方法集中在高選擇性調聚反應,其部分或完全在主烷基化區(qū)中進行。在該反應中,四氯化碳與烯烴反應以產生c3-6氯化烷烴。雖然制備c3-6氯化烷烴的調聚反應是本領域已知的,但此類方法的一個問題是產生不想要的雜質;仍然需要一種用于以工業(yè)量并且在理想情況下連續(xù)地制備高純度c3-6氯化烷烴的方法。意外地并且有利地發(fā)現(xiàn),當從烯烴和四氯化碳制備氯化c3-6烷烴時,進行上述步驟a)至c)中的一個、一些或全部會提高效率(包括降低能量消耗)和/或使雜質的形成最小化,所述雜質原本可能難以從感興趣的氯化c3-6烷烴移除和/或在可使用氯化c3-6烷烴的下游反應中是有問題的。此外,令人驚奇的是,本發(fā)明的方法以高選擇性和高產率平衡了這些優(yōu)點。所述反應混合物通過使烯烴和四氯化碳接觸而形成。這可在主烷基化區(qū)中進行,例如通過將烯烴和四氯化碳兩者均進料至該區(qū)域中。另外或可選擇地,烯烴可以在主烷基化區(qū)上游的區(qū)域中與四氯化碳接觸,然后進料至主烷基化區(qū)中。在本發(fā)明的實施方案中,反應混合物中氯化c3-6烷烴:四氯化碳的摩爾比被控制在某些數(shù)量上限定的范圍內。如本領域技術人員將理解的,在此類實施方案中,盡管本文以四氯化碳原材料與c3-6氯化烷烴產物的摩爾比描述對該方法的控制,但也可以認為是控制原材料向產物的轉化率,因此,95:5的原材料與產物的摩爾比等于5%的轉化率。本發(fā)明人已發(fā)現(xiàn),如上所述限制原材料的轉化使得不期望的雜質的形成最小化。另外,當提及原材料:產物的摩爾比大于給定值時,這意味著原材料向產物的轉化程度更高,即,使得產物的比例增加,而原材料的比例減小。例如,在本發(fā)明的實施方案中,可使用在主烷基化區(qū)上游的初級烷基化區(qū)。反應混合物可以通過以下方式形成:將四氯化碳和烯烴進料至初級烷基化區(qū)中以形成反應混合物,然后將所述反應混合物進料至主烷基化區(qū)中。在此類實施方案中,可以在初級烷基化區(qū)中發(fā)生四氯化碳向感興趣的c3-6氯化烷烴的部分轉化,由此烷烴形成并且與四氯化碳一起包含在進料至主烷基化區(qū)中的反應混合物中。在另外或可選擇的實施方案中,進料至初級烷基化區(qū)中的烯烴的量可加以限制以延緩在初級烷基化區(qū)中四氯化碳向感興趣的c3-6氯化烷烴的轉化,使得從那里進料至主烷基化區(qū)中的反應混合物包含四氯化碳和c3-6氯化烷烴,但水平較低或基本上不含烯烴。本發(fā)明的方法中使用的烯烴和四氯化碳可以通過使用本領域技術人員已知的任何技術或設備,例如通過分散裝置,例如浸管、噴嘴、噴射器、靜態(tài)混合裝置和/或噴霧器進料至區(qū)域中,而在所述區(qū)域(例如,初級烷基化區(qū)或主烷基化區(qū))中接觸。在此類實施方案中,烯烴和/或四氯化碳的進料可以是連續(xù)的或間歇的。作為進料供應至其中形成反應混合物的區(qū)域中的烯烴可以呈液體和/或氣體形式。同樣,四氯化碳可以呈液體和/或氣體形式。在本發(fā)明的實施方案中,存在于主烷基化區(qū)(和/或可以使用的任何其它烷基化區(qū))中的反應混合物(包含四氯化碳、c3-6氯化烷烴產物以及任選的催化劑和/或未反應的烯烴)可以是均質的,即在單相中,例如液相或氣相。這甚至在反應混合物的一種組分以與其它組分不同的相引入體系中的情況下也能實現(xiàn)。例如,在實施方案中,氣態(tài)烯烴可與液體四氯化碳接觸,導致烯烴溶解,從而形成液相均相反應混合物??蛇x擇地,反應混合物可以是非均質的。因此,根據(jù)本發(fā)明的一個方面,提供一種用于制備氯化c3-6烷烴的方法,其包括:在初級烷基化區(qū)中提供包含烯烴和四氯化碳的反應混合物,以在所述反應混合物中產生氯化c3-6烷烴,并從所述初級烷基化區(qū)提取一部分所述反應混合物,并將所述提取的一部分所述反應混合物進料至主反應區(qū)中,并從所述主反應區(qū)提取一部分所述反應混合物,其中從所述主烷基化區(qū)提取的所述反應混合物中的氯化c3-6烷烴:四氯化碳的摩爾比大于從所述初級烷基化區(qū)提取的所述反應混合物中的氯化c3-6烷烴:四氯化碳的摩爾比。用于本發(fā)明的方法中的烯烴可以是c2-5烯烴,例如乙烯(即c2烯烴)、丙烯、丁烯或戊烯。烯烴可以或可以不被鹵化例如氯化和/或被取代。在其中烯烴被氯化的布置中,其優(yōu)選包含1個、2個、3個、4個或5個氯原子。在本發(fā)明的實施方案中,氯代烯烴具有以下通式:chaxb=r,其中a為1或2,b為0或1,x為鹵素(例如氯),并且r為取代或未取代的c1-4烷基??捎糜诒景l(fā)明的方法中的烯烴材料的實例包括乙烯、氯乙烯、丙烯、2-氯丙烯、3-氯丙烯、2,3,3,3-四氯丙烯、1,1-二氯乙烯、三氯乙烯、氯氟乙烯、1,2-二氯乙烯、1,1-二氯-二氟乙烯、1-氯丙烯、1-氯丁烯和/或us5902914和ep131561中公開的任何其它烯烴,所述專利的內容通過引用并入本文中。本發(fā)明的方法中使用的四氯化碳和烯烴原材料可以具有高純度,例如,這些材料中的任一種或兩種可以是至少約95%純,至少約97%純,至少約99%純,至少約99.5%純,至少約99.7%純,或至少約99.9%純。在本發(fā)明的實施方案中,四氯化碳原材料包含少于約2000ppm、少于約1000ppm、少于約500ppm、少于約200ppm、少于約100ppm、少于約50ppm或少于約20ppm的溴化物或溴化有機化合物。另外或可選擇地,四氯化碳原材料可以具有約200ppm或更少、約100ppm或更少、約50ppm或更少或者約35ppm或更少的水分含量。在本發(fā)明的方法中,優(yōu)選使用四氯化碳作為鹵代烷烴原料。然而,在本發(fā)明的可選擇的實施方案中,可以使用除四氯化碳以外的鹵代烷烴原料,例如1,1-二氯甲烷、1,1,1-三氯乙烷、二氯氟甲烷、1,1,1-三氯三氟乙烷、1,1,2-三氯三氟乙烷、四氯乙烷、五氯乙烷、六氯乙烷和/或us5902914中公開的任何其它氯代烷烴,所述專利的內容通過引用并入本文中。四氯化碳源可以位于與用于操作本發(fā)明的方法的設備相同的位置。在實施方案中,四氯化碳源可以與具有例如膜電解設備的氯堿設施相鄰,從所述設施可獲得高純度氯用于生產四氯化碳。該位置還可以包括用于生產表氯醇(例如從甘油原料)、縮水甘油和/或環(huán)氧樹脂的設備,使得在任何相關步驟或方法中作為副產物產生的氯化氫氣體也被有效地利用。因此,為了最佳經濟使用氯堿設施,設想具有用于氯反應和氯化氫的捕集/再使用的設備的綜合設施。所述反應混合物可以從主烷基化區(qū)(和/或如果使用的話,初級烷基化區(qū))連續(xù)或間歇地提取。為免生疑問,當在本申請中提及從本發(fā)明的方法中使用的區(qū)域連續(xù)提取材料時,不應賦予其純粹的字面含義。本領域技術人員應認識到,在此類實施方案中,在所討論的區(qū)域處于操作條件下,并且如果其目的是建立穩(wěn)態(tài)反應(例如烷基化),一旦其中的反應混合物達到所需穩(wěn)態(tài),可以基本上連續(xù)地移除材料。本發(fā)明的一個優(yōu)點是,通常在工業(yè)上供應的烯烴中觀察到的某些雜質(例如某些有機雜質,例如醇、醚、酯和醛)的存在可以容忍和/或使用本文所述的工藝步驟來移除。該優(yōu)點在其中烯烴是乙烯的布置中特別有益;乙烯可以衍生自生物乙醇、乙醇或原油。本發(fā)明的方法的另一優(yōu)點是,i)氯化烷烴的連續(xù)生產和ii)烯烴原材料的基本上完全利用可以實現(xiàn),而沒有烯烴逸出至廢氣系統(tǒng)中。氯化c3-6烷烴可以是氯丙烷、氯丁烷、氯戊烷或氯己烷。氯化c3-6烷烴可以包含4個、5個、6個、7個、8個或更多個氯原子??梢愿鶕?jù)本發(fā)明的方法以高純度制備的氯化c3-6烷烴化合物的實例包括四氯丙烷例如1,1,1,3-四氯丙烷、四氯丁烷、六氯丁烷、七氯丁烷、八氯丁烷、五氯丙烷、五氯丁烷例如1,1,1,3,3-五氯丁烷,以及七氯己烷。本發(fā)明的方法的一個優(yōu)點是,它們可容許以高異構選擇性制備感興趣的c3-6氯化烷烴。因此,在本發(fā)明的此類實施方案中,制備c3-6氯化烷烴產物,其異構選擇性為至少約95%、至少約97%、至少約98%、至少約99%、至少約99.5%、至少約99.7%、至少約99.8%或至少約99.9%。可通過使用催化劑來加速在本發(fā)明的方法中進行的產生氯化c3-6烷烴的烷基化反應。如本文所用,術語催化劑不僅用于涵蓋使用具有催化效果的單一化合物或材料,例如固體金屬或金屬鹽,而且涵蓋使用可另外包含催化材料和助催化劑(co-catalyst)或助催化劑(promoter)例如配體的催化劑體系??梢允褂帽绢I域技術人員已知的用于從四氯化碳和烯烴形成氯化c3-6烷烴的任何催化劑。在本發(fā)明的實施方案中,催化劑是金屬的??梢允褂每捎米鞅景l(fā)明的烷基化反應中的催化劑的任何金屬,包括但不限于銅和/或鐵。金屬催化劑可以下列形式存在:固體形式(例如,在銅或鐵的情況下,以顆粒(例如粉末或銼屑)、絲和/或網等形式),和/或作為鹽,其中金屬可處于任何氧化態(tài)(例如亞銅鹽,例如氯化亞銅、溴化亞銅、氰化亞銅、硫酸亞銅、苯基亞銅和/或亞鐵鹽和/或鐵鹽,例如氯化亞鐵和氯化鐵)。在本發(fā)明的方法中使用金屬鹽作為催化劑的情況下,這些鹽可添加至烷基化區(qū)中和/或在烷基化區(qū)中原位形成。在后一種情況下,可以將固體金屬添加至烷基化區(qū)中,并且由于其中的條件,可以形成鹽。例如,如果將固體鐵添加至氯化反應混合物中,則存在的氯可與單質鐵組合以原位形成氯化鐵或氯化亞鐵。在原位形成金屬鹽的情況下,仍然需要在反應混合物中保持預定水平的單質金屬催化劑(例如,與金屬鹽和/或配體的水平相比,過量的單質金屬),因此,隨著反應進行,可連續(xù)或間歇地添加另外的單質金屬催化劑。如上所述,在本發(fā)明的實施方案中,催化劑還可以包含可與金屬催化劑形成絡合物的配體,優(yōu)選有機配體。合適的配體包括胺、亞硝酸酯、酰胺、磷酸酯和亞磷酸酯。在本發(fā)明的實施方案中,所使用的配體是磷酸烷基酯,例如磷酸三甲酯、磷酸三乙酯、磷酸三丁酯和磷酸三苯酯。另外的金屬催化劑和配體是本領域技術人員已知的,并且在現(xiàn)有技術中公開,例如us6187978,其內容通過引用并入本文中。使用時,催化劑體系的組分可以連續(xù)或間歇地進料至烷基化區(qū)(例如主烷基化區(qū),和/或如果使用的話,初級烷基化區(qū))中。另外或可選擇地,它們可以在烷基化反應開始之前和/或期間被引入烷基化區(qū)(例如主烷基化區(qū),和/或如果使用的話,初級烷基化區(qū))中。另外或可選擇地,催化劑(或催化劑的組分,例如配體)可以與反應混合物的其它組分一起,例如在四氯化碳和/或乙烯的進料中進料至烷基化區(qū)(例如主烷基化區(qū),或者如果使用的話,初級烷基化區(qū))中。在其中催化劑包含金屬催化劑和助催化劑例如配體的本發(fā)明的實施方案中,主烷基化區(qū)和/或如果使用的話,初級烷基化區(qū)中存在的反應混合物中助催化劑:金屬催化劑的摩爾比保持在大于1:1的比率,更優(yōu)選大于2:1、5:1或10:1的比率。當將固體金屬催化劑添加至反應混合物中時,可將其添加至如果使用的話初級烷基化區(qū)和/或主烷基化區(qū)中。在本發(fā)明的實施方案中,固體金屬催化劑以按反應混合物的重量計保持約0.1%至4%、約0.5%至3%或約1%至2%的水平的量添加至初級烷基化區(qū)(如果使用的話和/或主烷基化區(qū)中。另外或可選擇地,當使用金屬催化劑時,添加這些物質以建立按反應混合物的重量計約0.1%、約0.15%或約0.2%至約1.0%、約0.5%或約0.3%的溶解金屬含量。在其中使用的催化劑體系包含金屬催化劑和助催化劑的本發(fā)明的實施方案中,金屬催化劑和助催化劑可以同時和/或在設備的相同部分中,例如在初級烷基化區(qū)(如果使用的話)和/或主烷基化區(qū)中添加至反應混合物中??蛇x擇地,金屬催化劑和助催化劑可以在設備中的不同位置,或者按順序或分開添加。例如,可以將固體金屬催化劑添加至初級烷基化區(qū)中,而將助催化劑從循環(huán)回路進料至該區(qū)域中,也可以向所述區(qū)域中添加另外的新鮮助催化劑。在本發(fā)明的實施方案中,初級烷基化區(qū)和/或主烷基化區(qū)在大氣壓或超大氣壓下,即在大于約100kpa、大于約200kpa、大于約300kpa、大于約400kpa、大于約500kpa、大于約600kpa、大于約700kpa或大于約800kpa的壓力下操作。通常,初級烷基化區(qū)和/或主烷基化區(qū)中的壓力等于或低于約2000kpa、約1700kpa、約1500kpa、約1300kpa、約1200kpa或約1000kpa。另外或可選擇地,在本發(fā)明的實施方案中,初級烷基化區(qū)和/或主烷基化區(qū)在升高的溫度下,即在等于或高于約30℃、約40℃、約50℃、約60℃、約70℃、約80℃、約90℃或約100℃的溫度下操作。通常,初級烷基化區(qū)和/或主烷基化區(qū)在等于或低于約200℃、約180℃、約160℃、約140℃、約130℃、約120℃或約115℃的溫度下操作。已經有利地發(fā)現(xiàn),使用這些范圍內的溫度和壓力結合本發(fā)明的方法的其它特征會使感興趣的氯化c3-6烷烴的產率和/或選擇性最大化,同時使有問題的副產物的形成最小化。在本發(fā)明的方法中,可以使用多個烷基化區(qū)。可以使用任何數(shù)量的烷基化區(qū),例如1個、2個、3個、4個、5個、6個、7個、8個、9個或10個或更多個。在其中使用多個初級烷基化區(qū)和/或主烷基化區(qū)的實施方案中,可以存在任何數(shù)量(例如1個、2個、3個、4個、5個、6個、7個、8個、9個或10個或更多個)的初級烷基化區(qū)和/或主烷基化區(qū)。為免生疑問,當提及烷基化區(qū)(初級烷基化區(qū)和/或主烷基化區(qū))的性質時,例如其操作條件、其操作方法、其性質等,就包括多個初級烷基化區(qū)和/或主烷基化區(qū)的本發(fā)明的實施方案而言,這些區(qū)域中的一個、一些或全部可表現(xiàn)出所討論的性質。例如,如果為了簡潔起見,提及具有指定操作溫度的主烷基化區(qū),那么就包括多個主烷基化區(qū)的實施方案而言,應將其作為參考,這些主烷基化區(qū)中的一個、一些或全部在所述指定溫度下操作。在使用多個初級烷基化區(qū)和/或主烷基化區(qū)的布置中,這些烷基化區(qū)可以平行和/或連續(xù)操作。在使用初級烷基化區(qū)和主烷基化區(qū)的布置中,可以控制烯烴和四氯化碳之間的烷基化反應,以防止其在初級烷基化區(qū)中進行至超過一定的完成程度,例如使得從初級烷基化區(qū)提取和/或進料至主烷基化區(qū)中的反應混合物中氯化c3-6烷烴:四氯化碳的摩爾比不超過85:15、90:10、93:7或95:5,盡管這不是必要的。另外或可選擇地,可以允許反應運行至相對較晚的完成階段,使得從初級烷基化區(qū)提取和/或進料至主烷基化區(qū)中的反應混合物中氯化c3-6烷烴:四氯化碳的摩爾比大于50:50、60:40、70:30、75:25或80:20。通過使用不利于四氯化碳完全轉化為1,1,1,3-四氯丙烷的反應條件,可以控制初級烷基化區(qū)中的烷基化反應的進程。另外或可選擇地,可以通過仔細選擇反應混合物在初級烷基化區(qū)中的停留時間,例如約20分鐘至300分鐘、約40分鐘至250分鐘、約60分鐘至約200分鐘或約90分鐘至約180分鐘來控制初級烷基化區(qū)中的烷基化反應的進程。在本發(fā)明的實施方案中,所述摩爾比可以通過限制進料至初級烷基化區(qū)和/或主烷基化區(qū)中的烯烴的量來控制。例如,進料至初級烷基化區(qū)和/或主烷基化區(qū)中的四氯化碳:烯烴的摩爾比可以為約50:50至約55:45,約60:40,約65:35,約70:30,約75:25,約80:20,約85:15或約90:10。在其中使用初級烷基化區(qū)和主烷基化區(qū)的實施方案中,大部分氯化c3-6烷烴可以在初級烷基化區(qū)中產生。在此類實施方案中,在主反應區(qū)中產生的c3-6烷烴的比例可以顯著降低,例如使得反應混合物中氯化c3-6烷烴:四氯化碳的摩爾比增加1至10、2至8或3至5。例如,如果從初級烷基化區(qū)提取并進料至主烷基化區(qū)中的反應混合物中氯化c3-6烷烴:四氯化碳的摩爾比為90:10,則在主烷基化區(qū)中該摩爾比可以增加2、3或5,使得從主烷基化區(qū)提取的混合物中存在的氯化c3-6烷烴:四氯化碳的摩爾比可以為92:8、93:7或95:5。然而,本發(fā)明的方法的可行性不依賴于在初級反應區(qū)中發(fā)生的主要部分的四氯化碳向氯化c3-6烷烴的轉化。因此,在可選擇的實施方案中,四氯化碳向感興趣的氯化c3-6烷烴的轉化程度可以在初級烷基化區(qū)和主烷基化區(qū)之間進行平衡,或者主烷基化區(qū)中的轉化程度可大于初級烷基化區(qū)中的轉化程度。然后,可以將反應混合物從初級烷基化區(qū)(連續(xù)或間歇地)取出并進料至主烷基化區(qū)中,在主烷基化區(qū)中反應混合物中存在的剩余四氯化碳的一部分轉化為感興趣的氯化c3-6烷烴。在此類實施方案中,存在于反應混合物中的任何未反應的烯烴原材料可以有利地完全(或至少幾乎完全)被利用。在本發(fā)明的方法中,如果使用的話,初級烷基化區(qū)和主烷基化區(qū)可以在不同條件下操作。主烷基化區(qū)可以在比初級烷基化區(qū)更高的壓力下,例如在高至少約10kpa、高約20kpa、高約50kpa、高約100kpa、高約150kpa、高約200kpa、高約300kpa或高約500kpa的壓力下操作。在本發(fā)明的實施方案中,烯烴可以不進料至主烷基化區(qū)中;那些區(qū)域的唯一的烯烴源可位于進料至主烷基化區(qū)中的反應混合物中。另外,在四氯化碳和烯烴之間的烷基化反應被金屬催化劑(任選地包含配體)催化的實施方案中,金屬催化劑和/或配體可以不進料至主烷基化區(qū)中。在此類實施方案中,唯一的催化劑源可以是進料至主烷基化區(qū)中的反應混合物。另外或可選擇地,主烷基化區(qū)可以設置有催化劑床。在本發(fā)明的方法中,在使用初級烷基化區(qū)和主烷基化區(qū)并且固體金屬催化劑存在于初級烷基化區(qū)中的反應混合物中(例如通過直接添加至其中)的情況下,當從初級烷基化區(qū)提取反應混合物以便進料至主烷基化區(qū)中時,可以從初級烷基化區(qū)提取反應混合物,使得在反應混合物中存在非常少(如果有的話)的固體金屬催化劑,例如每升反應混合物少于約5mg、約2mg、約1mg、約0.5mg、約0.2mg、約0.1mg固體金屬催化劑。這可以通過使用本領域技術人員已知的任何技術和/或設備來實現(xiàn),例如在適當位置延伸至初級烷基化區(qū)中、設置有過濾網和/或具有適當直徑的管。當使用時,初級烷基化區(qū)和主烷基化區(qū)可以在相同或不同的反應器中,所述反應器可以是相同或不同類型的反應器。此外,在使用多個初級烷基化區(qū)的實施方案中,這些初級烷基化區(qū)可以在相同或不同的反應器中。同樣,在使用多個主烷基化區(qū)的實施方案中,這些主烷基化區(qū)可以在相同或不同的反應器中。本領域技術人員已知的任何類型的反應器可用于本發(fā)明的方法中??捎糜谔峁┩榛瘏^(qū)的反應器的具體實例是塔式反應器(例如塔式氣液反應器)、管式反應器、鼓泡塔式反應器、塞流反應器(例如管式塞流反應器)和攪拌槽反應器(例如連續(xù)攪拌槽反應器)。初級烷基化區(qū)存在于連續(xù)攪拌槽反應器(cstr)中并且主烷基化區(qū)存在于塞流反應器中的布置已經提供了有利的結果。本發(fā)明的方法的一個優(yōu)點是,無論烷基化區(qū)(例如,初級烷基化區(qū)和/或主烷基化區(qū))是以連續(xù)(穩(wěn)態(tài))或分批過程進行操作,都獲得期望的結果。術語“連續(xù)過程”和“分批過程”為本領域技術人員所理解。在實施方案中,當使用時,初級烷基化區(qū)以連續(xù)或分批過程進行操作。另外或可選擇地,當使用時,第二烷基化區(qū)以連續(xù)或分批過程進行操作。在本發(fā)明的方法中,保持主烷基化區(qū)中反應混合物中氯化c3-6烷烴的濃度水平,使得從主烷基化區(qū)提取的反應混合物中氯化c3-6烷烴:四氯化碳的摩爾比:i)在主烷基化區(qū)連續(xù)操作的情況下不超過95:5,或者ii)在主烷基化區(qū)分批操作的情況下不超過99:1。在主烷基化區(qū)連續(xù)操作的本發(fā)明的某些實施方案中,可以控制氯化c3-6烷烴的含量,使得從主烷基化區(qū)提取的反應混合物中該化合物:四氯化碳的比率不超過約94:6、約92:8或約90:10。在主烷基化區(qū)分批操作的本發(fā)明的可選擇的實施方案中,可以控制氯化c3-6烷烴的含量,使得從主烷基化區(qū)提取的反應混合物中該化合物:四氯化碳的比率不超過約97:3、約95:5或約90:10。不管主烷基化區(qū)處于連續(xù)過程還是分批過程,可以控制氯化c3-6烷烴的含量,使得從主烷基化區(qū)提取的反應混合物中該化合物:四氯化碳的比率等于或大于約70:30、約80:20、約85:15或約90:10。令人驚奇地發(fā)現(xiàn),通過控制四氯化碳向感興趣的氯化c3-6烷烴的轉化程度,并且防止反應進行至完成,可有利地減少雜質的形成。例如,在本發(fā)明的方法中使用的烯烴原料是乙烯的實施方案中,不希望的副產物例如戊烷(其原本會形成)的產生被最小化。因此,在本發(fā)明的實施方案中,從主反應區(qū)提取的反應混合物包含少于約5%、少于約2%、少于約1%、少于約0.5%、少于約0.2%、少于約0.1%、少于約0.05%或少于約0.02%的系列反應產物,即所包含的碳原子的數(shù)量多于c3-6氯化烷烴產物的化合物。氯化c3-6烷烴的含量的控制可以通過延緩烷基化過程的進程和/或將另外的四氯化碳引入主烷基化區(qū)中來實現(xiàn)。在其中通過延緩烷基化過程來控制氯化c3-6烷烴的含量的實施方案中,這可以通過使用不利于四氯化碳完全轉化為1,1,1,3-四氯丙烷的反應條件來實現(xiàn)。例如,這可以通過使反應混合物或其至少一部分暴露于減速或停止烷基化反應的進程的條件來實現(xiàn)。在此類實施方案中,反應混合物在烷基化區(qū)(例如,當使用時,主烷基化區(qū))中的暴露壓力可以顯著降低,例如降低至少約500kpa,至少約700kpa,至少約1000kpa。另外或可選擇地,反應混合物的暴露壓力可以降低至大氣壓或低于大氣壓。壓力的降低可以發(fā)生在一個或多個烷基化區(qū)(例如,如果使用的話,一個、一些或全部主烷基化區(qū))中。另外或可選擇地,壓力的降低可以發(fā)生在從烷基化區(qū)提取反應混合物之后。另外或可選擇地,在通過延緩烷基化過程來控制氯化c3-6烷烴的含量的實施方案中,這可以通過限制反應混合物中存在的烯烴的水平來實現(xiàn)。在本發(fā)明的實施方案中,可以通過仔細選擇反應混合物在烷基化區(qū)中的停留時間來控制烷基化區(qū)中的烷基化反應的進程。例如,在其中使用一個或多個主烷基化區(qū)的實施方案中,反應混合物在那些區(qū)域中的停留時間可以是例如約1分鐘至120分鐘、約5分鐘至100分鐘、約15分鐘至約60分鐘或約20分鐘至約40分鐘。在通過延緩烷基化過程來控制氯化c3-6烷烴的含量的實施方案中,另外或可選擇地,這可以通過使主烷基化區(qū)的操作溫度降低例如約5℃或更多、約10℃或更多、約20℃或更多、約50℃或更多或者約100℃或更多來實現(xiàn)。另外或可選擇地,主轉化區(qū)的操作溫度可以降低至約20℃、約10℃或約0℃。另外或可選擇地,可以通過限制反應混合物中存在的催化劑的量或從主烷基化區(qū)移除催化劑床(如果存在)來延緩烷基化過程。也可以降低主烷基化區(qū)的攪動或攪拌速率以延緩烷基化過程。如上所述,從主烷基化區(qū)提取的反應混合物包含四氯化碳和氯化c3-6烷烴。然而,在本發(fā)明的實施方案中,根據(jù)所使用的條件和設備,從主烷基化區(qū)提取的反應混合物可以另外包含未反應的烯烴原材料、催化劑和/或雜質(例如氯化烷烴雜質、氯化烯烴雜質和/或含氧有機化合物)。鑒于在氯化c3-6烷烴旁邊存在未反應的烯烴特別是對于使用氯化c3-6烷烴的下游過程可能是有問題的,在本發(fā)明的實施方案中,使從主烷基化區(qū)提取的反應混合物經歷脫烯化步驟,其中至少約50重量%或更多的存在于反應混合物中的烯烴從其提取出來,并且至少約50%的提取的烯烴被進料回在主烷基化區(qū)中提供的反應混合物中。此類實施方案是特別有利的,因為它們能夠實現(xiàn)本發(fā)明的方法中使用的烯烴進料的基本上全部(如果不是全部)利用。在本發(fā)明的實施方案中,至少約60%、至少約70%、至少約80%、至少約90%、至少約95%、至少約97%或至少約99%的從主烷基化區(qū)提取的反應混合物中存在的烯烴在脫烯化步驟期間被移除??梢允褂帽绢I域技術人員已知的任何技術來從反應混合物移除未反應的烯烴。在本發(fā)明的實施方案中,從反應混合物提取烯烴可以使用蒸餾技術來實現(xiàn),所述蒸餾技術獲得富含烯烴的流,例如閃蒸,其可方便地在其中烯烴的沸點大幅低于反應混合物中存在的其它化合物的沸點的實施方案中使用,如對于乙烯(-103.7℃)對四氯化碳(76.6℃)和1,1,1,3-四氯丙烷(159℃),情況即為如此。反應混合物的脫烯化可以是選擇性的。換句話說,烯烴是選擇性提取的,而不從反應混合物大量移除其它化合物。在此類實施方案中,從反應混合物提取的烯烴可以包含少于約10%、少于約5%、少于約2%或少于約1%的除烯烴原材料以外的化合物??梢酝ㄟ^本領域技術人員已知的任何技術或使用本領域技術人員已知的任何設備來蒸餾反應混合物。例如,可以使用常規(guī)蒸餾設備(例如蒸餾塔)。另外或可選擇地,在本發(fā)明的實施方案中,當提取反應混合物的主烷基化區(qū)中的壓力超過大氣壓時,烯烴從反應混合物的蒸發(fā)可以通過將反應混合物在從主烷基化區(qū)提取后保持在超大氣壓壓力下并將其進料至蒸發(fā)區(qū)中來實現(xiàn),在所述蒸發(fā)區(qū)中從反應混合物蒸發(fā)烯烴。在本發(fā)明的實施方案中,在蒸發(fā)區(qū)中從反應混合物蒸發(fā)烯烴可以通過減壓,例如通過顯著降低反應混合物所處的壓力,例如降低至少約500kpa、至少約700kpa、至少約1000kpa和/或降低至大氣壓或低于大氣壓的壓力來實現(xiàn)。方便地,在部分或完全使用減壓來減速或停止四氯化碳向感興趣的氯化c3-6烷烴的轉化并且也從反應混合物分離烯烴的實施方案中,這些目的可以在單一減壓步驟中同時實現(xiàn)。蒸發(fā)區(qū)可以在其中可以實現(xiàn)反應混合物中存在的烯烴的蒸發(fā)的任何設備,例如閃蒸設備,例如閃蒸鼓中。例如通過閃蒸從反應混合物蒸餾出來的烯烴優(yōu)選以液體或氣體形式從蒸餾設備提取出來。在本發(fā)明的方法中,至少約50重量%、至少約70重量%、至少約80重量%、至少約90重量%、至少約95重量%、至少約97重量%或至少約99重量%的從蒸發(fā)區(qū)提取的烯烴被進料回(即循環(huán))初級烷基化區(qū)和/或主烷基化區(qū)。為免生疑問,在本發(fā)明的實施方案中,如果蒸餾烯烴呈氣體形式,則在進料至在主烷基化區(qū)中提供的反應混合物中之前可以轉化回液體或可以不轉化回液體。例如,氣態(tài)烯烴轉化成液體烯烴可以通過使其通過冷凝器和/或捕集在液體(優(yōu)選冷卻的)四氯化碳流中來實現(xiàn),然后可將其進料至烷基化區(qū)中。氣態(tài)烯烴可以使用本領域技術人員已知的任何技術或設備,例如吸收塔捕集在液體四氯化碳流中。這種布置是有利的,因為它有助于在烷基化過程中使用的化合物的完全工業(yè)利用。如上所述,在本發(fā)明的實施方案中,可以在存在于烷基化區(qū)中的反應混合物中使用催化劑,例如包含固體金屬和/或金屬鹽催化劑和助催化劑例如配體的催化劑體系。在此類實施方案中,從烷基化區(qū)提取的反應混合物可以包含催化劑。鑒于催化劑的存在在使用氯化c3-6烷烴的下游反應中可能是有問題的,可優(yōu)選從反應混合物移除催化劑。另外,對于其中使用昂貴的催化劑和/或助催化劑例如上述磷酸烷基酯和亞磷酸烷基酯配體的催化劑體系,回收可重復使用的催化劑體系和/或其組分也是優(yōu)選的,以使得必須使用的新鮮催化劑的量最小化,從而降低操作成本。雖然過去已經解決了從反應混合物移除本發(fā)明的方法中使用的類型的催化劑的挑戰(zhàn),但用于這樣做的技術和條件(通常涉及使用侵蝕性條件進行蒸餾)可能損害催化劑體系并且可能降低其催化能力。當催化劑體系是溫度敏感的時,尤為如此,對于包含某些有機配體例如磷酸烷基酯和亞磷酸烷基酯作為助催化劑的體系,情況即為如此。因此,在本發(fā)明的實施方案中,使從主烷基化區(qū)提取的反應混合物經歷水性處理步驟,其中使反應混合物與水性介質在水性處理區(qū)中接觸,形成兩相混合物,并從所述兩相混合物提取包含催化劑的有機相。在其中使反應混合物經歷水性處理步驟的本發(fā)明的實施方案中,反應混合物可以包含未反應的四氯化碳和c3-6氯化烷烴產物。另外,反應混合物可包含催化劑(例如金屬催化劑和催化劑配體的絡合物,或者游離催化劑配體)和/或未反應的烯烴原材料。通過使用水性處理步驟,可以避免現(xiàn)有技術中描述的損害條件(例如,高溫、高催化劑濃度和/或無水形式的鐵化合物的存在),這意味著回收的催化劑和/或其組分(例如配體或助催化劑)可以重復使用(例如,其可以循環(huán)回在烷基化區(qū)中提供的反應混合物),而催化能力沒有任何大幅度損失。在本發(fā)明的實施方案中,優(yōu)選兩相水性處理混合物的汽提,因為可以避免超過100℃的鍋爐溫度,并且可以使用大氣壓。水性處理步驟的另一優(yōu)點是,其使得從反應混合物移除雜質,例如如果存在的話,含氧有機產物。更具體地,當方法涉及作為前體的烯烴時,例如乙烯、丙烯、1-丁烯、2-丁烯、1-己烯、3-己烯、1-苯基-3-己烯、丁二烯、乙烯基鹵化物等,可潛在地形成含氧有機化合物(例如烷醇、烷?;痛祟惡趸衔锏穆然愃莆?。有利地,通過水性處理步驟,反應混合物中此類材料的水平如果不消除,則顯著降低至可接受的水平。在進行水性處理步驟的本發(fā)明的實施方案中,在水性處理區(qū)中提供的反應混合物可以包含感興趣的氯化c3-6烷烴(例如其量為約50%或更高)、催化劑和任選的四氯化碳和/或雜質,例如有機含氧化合物、氯化烷烴化合物(除感興趣的氯化c3-6烷烴以外)和/或氯化烯烴化合物。該催化回收過程涉及使反應混合物經歷水性處理步驟,其中使反應混合物與水性介質在水性處理區(qū)中接觸。在實施方案中,水性介質是水(作為液體和/或蒸汽)。另外,水性介質可以另外包含其它化合物,例如酸??梢允褂脽o機酸,例如鹽酸、硫酸和/或磷酸。當進料至水性處理區(qū)中的水性介質部分或全部為液體形式時,在液體水性介質與反應混合物接觸時會形成兩相混合物。可選擇地,當水性介質呈氣體形式,例如水蒸汽時,兩相混合物可能不立即形成,而是一旦氣體水性介質冷凝就形成。在水性處理步驟中使用的設備可以被配置為使得水性介質冷凝以形成兩相混合物在水性處理區(qū)內和/或遠離水性處理區(qū)發(fā)生。在本發(fā)明的實施方案中,可以從在水性處理區(qū)中形成的混合物提取c3-6氯化烷烴產物。進料至水性處理區(qū)中的反應混合物中存在的氯化c3-6烷烴中的大部分(例如至少約50%、至少約60%、至少約70%、至少約80%或至少約90%)可以使用本領域技術人員已知的任何技術或設備從在水性處理區(qū)中形成的混合物提取。在本發(fā)明的實施方案中,使用蒸餾從在水性處理區(qū)中形成的混合物提取c3-6氯化烷烴產物。蒸餾可以獲得富含c3-6氯化烷烴產物的流。如在本說明書中所用,術語“富含特定化合物的流”(或相應的語言)用于指該流包含至少約90%、約95%、約97%、約98%或約99%的特定化合物。此外,術語“流”不應被狹義地解釋,而是涵蓋通過任何方式從混合物提取的組合物(包括級分)。例如,c3-6烷烴可以例如從包含該烷烴和水蒸汽的氣體混合物蒸餾出來。c3-6氯化烷烴可以在富含c3-6氯化烷烴的流中蒸餾出來。在其中水性介質部分或全部為液體形式的本發(fā)明的實施方案中,c3-6氯化烷烴的蒸餾可以通過例如使用蒸汽蒸餾技術煮沸存在的混合物以蒸發(fā)氯化c3-6烷烴并產生氣態(tài)氯化c3-6烷烴/水蒸汽混合物來實現(xiàn),從所述混合物可以蒸餾出氯化c3-6烷烴。另外或可選擇地,當水性介質部分或全部以氣體形式提供時,這將蒸發(fā)氯化c3-6烷烴以形成包含該烷烴和水蒸汽的氣體混合物,隨后可以任選地對其進行蒸餾以移除氯化c3-6烷烴,例如蒸汽蒸餾。c3-6氯化烷烴可以在富含該化合物的流中獲得。在其中氯化c3-6烷烴從氯化c3-6烷烴和水蒸汽的氣體混合物蒸餾出來的實施方案中,蒸餾設備可以連接至水性處理區(qū),使得氣態(tài)氯化烷烴/水蒸汽混合物可以從水性處理區(qū)直接通入該設備。可選擇地,蒸餾設備可以遠離水性處理區(qū)定位,使得首先從水性處理區(qū)提取氣態(tài)混合物,然后輸送至蒸餾設備。在任一布置中,c3-6氯化烷烴可以在富含該化合物的流中獲得。在水性介質和反應混合物為液體形式的可選擇的實施方案中,可以使用本領域技術人員已知的常規(guī)蒸餾技術從該液體混合物提取氯化c3-6烷烴。c3-6氯化烷烴可以在富含該化合物的流中獲得。兩相混合物可以在水性處理區(qū)內或遠離水性處理區(qū)形成。兩相混合物包含水相(作為添加至水性處理區(qū)中的水性介質的結果)和有機相(包含氯化c3-6烷烴、任選未反應的四氯化碳以及重要的是催化劑)。為了使有機相的體積最大化,從而促進從兩相混合物提取該相,鹵代烷烴提取劑(例如四氯化碳和/或感興趣的氯化c3-6烷烴)可以使用本領域技術人員已知的技術和設備向兩相混合物中添加(例如通過連續(xù)或間歇地進料至水性處理區(qū)中)。可以使用本領域技術人員已知的任何技術,例如傾析從兩相殘渣提取有機相。例如,有機相的提取可以通過從水性處理區(qū)或容納其的容器進行順序相提取來進行??蛇x擇地,可以從水性處理區(qū)提取兩相混合物,并使其經歷遠離水性處理區(qū)的相分離步驟。在本發(fā)明的實施方案中,可以對兩相混合物和/或提取的有機相進行過濾。在實施方案中,這將獲得可以任選地完全或部分地用作鐵源的濾餅。從在水性處理步驟期間形成的混合物提取c3-6氯化烷烴產物可以在從其提取有機相之前和/或在從該混合物提取有機相之后進行。上文概述了從在水性處理步驟期間形成的混合物提取c3-6氯化烷烴產物的一些示例性實施方案。作為另一實例,可以加熱兩相混合物以形成氣體混合物,可以例如通過蒸餾從其提取c3-6氯化烷烴產物(任選地作為富含c3-6氯化烷烴的流)。然后,可以從兩相混合物提取c3-6氯化烷烴的比例減小的有機相。另外或可選擇地,可以如上所討論從兩相混合物提取有機相。然后,可以例如通過蒸餾從該相提取c3-6氯化烷烴(任選地作為富含c3-6氯化烷烴的流)。在此類實施方案中,當有機相包含催化劑時,所選擇的提取c3-6氯化烷烴的蒸餾條件是溫和的,以使催化劑體系的失活最小化,例如在約100℃或更低、約95℃或更低、約90℃或更低、約85℃或更低或者約80℃或更低的溫度下和/或在約1kpa至10kpa的壓力下。另外或可選擇地,可以使用更低的壓力。提取的有機相可以包含四氯化碳和/或c3-6氯化烷烴產物。另外,反應混合物可以包含催化劑(例如金屬催化劑和催化劑配體的絡合物或者游離配體)和/或未反應的烯烴原材料。一旦富含c3-6氯化烷烴的流已經從在水性處理步驟中形成的混合物提取出來(直接地或在從其提取有機相之后),該相的c3-6氯化烷烴的含量將低于反應混合物中的含量。在本發(fā)明的布置中,特別是其中有機相包含四氯化碳和/或催化劑的那些,有機相可以例如以液體形式進料回烷基化區(qū)。在此類布置中,烯烴原材料(例如以氣體形式)可以被捕集在被進料至烷基化區(qū)中的有機相流中。在本發(fā)明的實施方案中,可以在該方法的任何時刻進行除上文所討論之外的一個或多個蒸餾步驟,以任選地獲得富含特定產物的流。例如,在水性處理步驟之前,如果進行的話,可以使反應混合物經歷蒸餾步驟。在其中反應混合物含有溫度敏感的催化劑體系,例如包含有機配體作為助催化劑的催化劑體系的實施方案中,蒸餾步驟通常在避免催化劑失活的條件下進行,例如在約100℃或更低、約95℃或更低、約90℃或更低、約85℃或更低或者約80℃或更低的溫度下和/或在約1kpa至10kpa的壓力下。另外或可選擇地,可以使用更低的壓力。另外,已發(fā)現(xiàn),通過不過度蒸餾反應混合物可以避免溫度敏感的催化劑體系的失活。因此,在其中蒸餾含有催化劑體系的反應混合物的本發(fā)明的實施方案中,可能不允許蒸餾導致蒸餾設備中的處理液體的體積減少至使得該處理液體中的催化劑體系的濃度是在主烷基化區(qū)中提供的反應混合物中存在的所述催化劑體系的水平的約2倍、約5倍或約10倍。在水性處理步驟(如果進行的話)之前進行的蒸餾步驟可以使用本領域技術人員已知的技術和設備,例如與真空蒸餾塔連通的蒸餾鍋爐(分批或連續(xù))來進行。在此類實施方案中,進行蒸餾的反應混合物可以包含大于約50重量%的感興趣的氯化c3-6烷烴、催化劑和任選的四氯化碳和/或雜質,例如有機含氧化合物、氯化烷烴化合物(除感興趣的氯化c3-6烷烴以外)和/或氯化烯烴化合物。蒸餾步驟通常導致氯化烷烴餾出物的流從反應混合物的移除,例如未反應的四氯化碳、感興趣的c3-6烷烴和/或氯化有機雜質(即除感興趣的c3-6烷烴和四氯化碳以外的氯化有機化合物)的流(和任選地富含這些物質的流)從反應混合物的移除。四氯化碳可以循環(huán)回烷基化區(qū)。通常包含大量氯化c3-6烷烴、四氯化碳和/或催化劑的來自這種步驟的殘渣可以經歷進一步的處理步驟,例如水性處理步驟和/或進一步的蒸餾步驟。在本發(fā)明的實施方案中,當在水性處理步驟(如果進行的話)之前使反應混合物經歷蒸餾步驟時,至少約30重量%、至少約50重量%、至少約60重量%或至少約70重量%至至多約95重量%、至多約90重量%、至多約85重量%或至多約80重量%的感興趣的氯化c3-6烷烴在該蒸餾步驟中從反應混合物移除。另外或可選擇地,可以在水性處理步驟(如果進行的話)之后進行一個或多個蒸餾步驟。例如,從進料至水性處理區(qū)中的反應混合物提取的氯化c3-6烷烴可以以包含作為主要成分的氯化c3-6烷烴、鹵代烷烴提取劑以及氯化有機雜質(即除感興趣的c3-6烷烴和四氯化碳以外的氯化有機化合物)的混合物的形式存在??梢允乖摶旌衔锝洑v一個或多個蒸餾步驟,以移除氯化有機雜質,從而獲得富含c3-6氯化烷烴的流和/或移除鹵代烷烴提取劑。再次,本領域技術人員已知的任何設備或條件,例如與真空蒸餾塔連通的蒸餾鍋爐(分批或連續(xù))可用于此類蒸餾步驟中。在此類蒸餾步驟中,可以對從在水性處理區(qū)中提供的反應混合物提取的氯化c3-6烷烴進行蒸餾,以將感興趣的氯化c3-6烷烴與氯代烷烴雜質分離。例如,在感興趣的氯化c3-6烷烴是1,1,1,3-四氯丙烷的實施方案中,已發(fā)現(xiàn),用于純化從在水性處理區(qū)中提供的反應混合物提取的氯化c3-6烷烴的蒸餾步驟對于移除氯代戊烷/氯代戊烯雜質特別有效。在本發(fā)明的方法的任何階段進行的蒸餾步驟中從包含感興趣的氯化c3-6烷烴的混合物分離的氯化有機雜質可以被回收并重新用于生產四氯化碳。這可以通過使氯化有機雜質經歷高溫氯解過程來實現(xiàn)。在這種過程中,任何存在的氯化有機化合物主要以高產率再處理變回純的四氯化碳。因此,在本發(fā)明的方法中使用氯解步驟可有效地最大化合成的總產率和感興趣的氯代烷烴的純度,同時最小化廢物產生。不管感興趣的氯化c3-6烷烴本身,在本發(fā)明的實施方案中,在水性處理步驟之后,如果使用的話,可以在蒸餾鍋爐中形成“重質(heavies)”殘渣。所述“重質”殘渣通常從系統(tǒng)提取出來,并例如進行高溫氯解過程處理,優(yōu)選導致生成氯甲烷。本發(fā)明的方法特別有利,因為其能夠通過使用本領域技術人員熟悉的簡單直接的技術和設備來制備高純度氯化烷烴。從本文提供的公開可以看出,本發(fā)明的方法可以以完全連續(xù)模式的一體化方法,任選地與其它方法組合來操作。本發(fā)明的工藝步驟可以使用轉化為高純度中間體的起始化合物,所述高純度中間體本身進一步處理成所需的感興趣的氯化化合物。這些化合物具有必需的純度,以用作一系列下游過程中的原料,例如氫氟化轉化。本發(fā)明的方法使得能夠控制產物的純度水平,以在每個步驟獲得高純度水平的化合物。所述方法有利地平衡了高產率、高選擇性和高效率,這特別是在連續(xù)方法中特別有挑戰(zhàn)性。本發(fā)明的方法使得能夠以工業(yè)規(guī)模經濟地生產高純度氯代烷烴化合物,這些化合物具有非常低水平的一系列雜質,例如鹵代烷烴或鹵代烯烴(特別是與目標化合物異構和/或具有較高分子量的那些,例如系列反應的產物),和/或含氧和/或溴化類似物,以及水和金屬物質。在本發(fā)明的實施方案中,本發(fā)明的方法可用于制備高純度氯化烷烴組合物,其包含:·約99.0%或更多、約99.5%或更多、約99.7%或更多、約99.8%或更多或者約99.9%或更多的氯化烷烴,·少于約2000ppm、少于約1000ppm、少于約500ppm、少于約200ppm或少于約100ppm的氯化烷烴雜質(即除感興趣的氯化c3-6烷烴以外的氯化烷烴化合物),·少于約2000ppm、少于約1000ppm、少于約500ppm、少于約200ppm或少于約100ppm的氯化烯烴化合物,·少于約2000ppm、少于約1000ppm、少于約500ppm、少于約200ppm或少于約100ppm的含氧有機化合物,·少于約500ppm、少于約200ppm、少于約100ppm、少于約50ppm或少于約20ppm的金屬催化劑,·少于約500ppm、少于約200ppm、少于約100ppm、少于約50ppm或少于約20ppm的助催化劑,·少于約2000ppm、少于約1000ppm、少于約500ppm、少于約200ppm或少于約100ppm的溴化物或溴化有機化合物,和/或·少于約1000ppm、少于約500ppm、少于約200ppm、少于約100ppm、少于約50ppm或少于約20ppm的水。在其中感興趣的氯化c3-6烷烴是1,1,1,3-四氯丙烷的實施方案中,以下是在本發(fā)明的方法中最少化、不產生和/或移除的特定雜質的實例:三氯甲烷、1,2-二氯乙烷、1-氯丁烷、1,1,1-三氯丙烷、四氯乙烯、1,1,3-三氯丙-1-烯、1,1,1,3,3-五氯丙烷、1,1,1,2,3-五氯丙烷、六氯乙烷、1,1,1,5-四氯戊烷、1,3,3,5-四氯戊烷、磷酸三丁酯、氯化烷醇和氯化烷?;衔?。因此,在本發(fā)明的實施方案中,產物1,1,1,3-四氯丙烷包含約500ppm或更少、約200ppm或更少、約100ppm或更少、約50ppm或更少、約20ppm或更少或者約10ppm或更少的一種或多種這些化合物。為免生疑問,如果組合物或材料的純度以百分比或ppm表示,除非另有說明,否則其為按重量計的百分比/ppm。如上所述,現(xiàn)有技術未能公開或教導用于制備具有如此高純度的氯化烷烴的方法,其中全部可能的雜質范圍得到管控。因此,根據(jù)本發(fā)明的其它方面,提供如上所述的高純度氯化烷烴組合物。附圖說明圖1-烷基化步驟圖2-第一蒸餾步驟圖3-水性催化劑回收步驟201淡鹽酸溶液流202包含催化劑的富含1,1,1,3-四氯丙烷的混合物進料流203鹵代烷烴提取劑進料流(1,1,1,3-四氯丙烷)204分批蒸餾鍋爐205分批蒸餾鍋爐出口206過濾207濾餅移除208有機相提取(圖1中的進料流13的一部分)209水相排出210用于粗1,1,1,3-四氯丙烷的蒸汽蒸餾的塔211粗1,1,1,3-四氯丙烷流212冷凝器213冷凝的粗1,1,1,3-四氯丙烷流214回流液-液分離器215回流流216用于進一步蒸餾的粗1,1,1,3-四氯丙烷流圖4-第二蒸餾步驟實施例現(xiàn)在下面的實施例中進一步說明本發(fā)明。實施例1-使用水性處理的回收催化劑的催化能力的展示。使乙烯和四氯化碳在催化劑存在下反應以產生1,1,1,3-四氯丙烷,所述催化劑i)使用常規(guī)蒸餾技術從反應混合物回收,或ii)使用本文所述的用于催化劑的創(chuàng)新水性處理步驟從反應混合物回收。所述反應混合物另外包含1,1,1,3-四氯丙烷(存在于循環(huán)流中)和四氯戊烷(在四氯化碳和乙烯之間的調聚反應存在下通常作為副產物形成的氯化烷烴雜質)。這些試驗例表明,與使用常規(guī)蒸餾技術回收的催化劑相比,使用水性處理步驟來回收催化劑,催化劑的性能顯著更高。為了簡潔起見,在下文列出的實施例中使用以下術語:tecm:四氯化碳tecpa:1,1,1,3-四氯丙烷tecpna:四氯戊烷bu3po4:磷酸三丁酯使用氣相色譜法來監(jiān)測反應進程。分批布置將裝備有攪拌器、用于溫度測量的熱電偶套管和采樣管(帶閥)的體積為405ml的不銹鋼高壓釜裝填下文所述的反應混合物并封閉。通過放置在磁(加熱)攪拌器上的油浴提供加熱。乙烯通過銅毛細管從放置在稱重秤上的10升氣瓶進料。高壓釜中的氣氛通過乙烯沖洗被替換。用乙烯加壓至5巴后,將高壓釜加熱至105℃,然后打開向高壓釜的乙烯供應。在前十分鐘手動控制乙烯供應(以保持反應溫度為112℃),然后保持在9巴的恒定壓力。允許反應進行限定的時間段。然后,將反應器冷卻,并在打開減壓反應器后取出反應混合物。比較例1-1和1-3以及實施例1-2、1-4和1-5在第一實施例中,蒸餾殘渣直接用作循環(huán)催化劑(比較例1-1)。在第二實施例中,將蒸餾殘渣用5%鹽酸萃取,過濾的有機部分用作催化劑(實施例1-2)。比較例1-1將90.1g包含63.7%tecpa、22.8%tecpna和7.49%bu3po4的蒸餾殘渣與400gtecm混合。然后,將混合物引入已經加入5.0g鐵的高壓釜中。用乙烯沖洗后,將混合物在高壓釜中加熱至110℃。在該溫度和9巴的乙烯壓力下,使反應混合物反應4.5小時。3小時后第一次取樣。實驗結束時殘留tecm的濃度為19.7%(3小時后為33.0%)。實施例1-2將90.1g包含63.7%tecpa、22.8%tecpna和7.49%bu3po4的蒸餾殘渣用370g5%hcl萃取。將底部有機層過濾,并與400gtecm混合。然后,將混合物引入已經加入5.0g鐵的高壓釜中。用乙烯沖洗后,將混合物在高壓釜中加熱至110℃。在該溫度和9巴的乙烯壓力下,使反應混合物反應4.5小時。3小時后第一次取樣。實驗結束時殘留tecm的濃度為5.5%(3小時后為24.6%)。比較例1-3比較例1-3使用與比較例1-1中所使用的條件相同的條件進行,只是使用不同濃度的四氯化碳和磷酸三丁酯。實施例1-4和1-5實施例1-4和1-5使用與實施例1-2中所使用的條件相同的條件進行,只是使用不同濃度的四氯化碳和磷酸三丁酯。比較例1-1和實施例1-2以及比較例1-3和實施例1-4和1-5的結果示于下表中??梢钥闯觯c在比較例1-1和1-3中相比,在實施例1-2、1-4和1-5中,轉化為1,1,1,3-四氯丙烷的四氯化碳的百分比顯著更高,這表明當回收催化劑時,水性處理步驟的進行對該體系具有極大的積極影響。這是由于從餾出物殘渣回收的催化劑的高活性,并且還可能由于從反應混合物移除了原本可能會延緩反應的雜質(例如含氧雜質)。連續(xù)布置:使用與上述用于分批實驗相同的不銹鋼高壓釜作為攪拌流動連續(xù)反應器。反應器最初裝填有約455g反應混合物。用乙烯加壓至5巴后,將高壓釜加熱至105℃,然后打開向高壓釜的乙烯供應,開始連續(xù)進料原料和連續(xù)取出反應混合物。將具有溶解的催化劑的原料溶液從不銹鋼槽進料至高壓釜中。將槽放置在反應器上方,因此,不使用泵來向反應器進料。反應器和槽在由銅毛細管從氣瓶分配的乙烯氣氛中,選擇氣瓶中的條件以防止反應開始。反應混合物的取樣每五分鐘通過采樣管進行。為了監(jiān)測反應過程,稱量具有原料和溶解催化劑的容器、乙烯氣瓶和取出的反應混合物。反應混合物總是收集一小時,然后更換收集容器。比較例1-6和1-8以及實施例1-7和1-9在進行和不進行水性處理步驟下進行比較循環(huán)催化劑(即蒸餾殘渣)的活性的連續(xù)實驗。在第一種情況下,蒸餾殘渣直接用作循環(huán)催化劑(比較例1-6)。在后一種情況下,用5%hcl水性處理蒸餾殘渣后的反應混合物用作含有循環(huán)催化劑的原料(實施例1-4和1-5)。比較例1-6將587.5g包含63.7%tecpa、22.8%tecpna和7.49%bu3po4的蒸餾殘渣與2200gtecm混合。該混合物包含78.7%tecm、11.8%tecpa、5.8%tecpna,并且用作用于連續(xù)布置的進料流。將構成高壓釜的反應容器裝填反應混合物和8g新鮮鐵。反應在110℃和9巴的乙烯壓力下進行。停留時間為2.7小時。在反應期間,反應的tecm的量在75%至76%之間。實施例1-7在1.5小時內,將587.5g包含63.7%tecpa、22.8%tecpna、7.49%bu3po4的蒸餾殘渣滴加至1001.5g沸騰的5%hcl中。然后,將該混合物汽提(stripped)。從頂部產物收集有機相,并將水相作為回流(reflux)返回。當所有的蒸餾殘渣都加入時,1小時后停止蒸餾。將汽提后的殘渣用200gtecm稀釋,然后在分液漏斗中進行分離。過濾底部有機相,并與蒸餾殘渣一起與2000gtecm混合。該混合物包含81.2%tecm、10.8%tecpa和5.3%tecpna。其被用作用于實驗的連續(xù)布置的進料流。將反應容器(高壓釜)裝填之前的反應混合物和8g新鮮鐵。反應在110℃和9巴的乙烯壓力下進行。停留時間為2.7小時/流量。在反應期間,反應的tecm的量在83%至85%之間。比較例1-8比較例1-8使用與比較例1-6中所使用的條件相同的條件進行,只是使用不同濃度的四氯化碳和磷酸三丁酯。實施例1-9實施例1-9使用與實施例1-7中所使用的條件相同的條件進行,只是使用不同濃度的四氯化碳和磷酸三丁酯。實施例(循環(huán)催化劑)bu3po4原料中的%tecm反應的tecm的%比較例1-61.67%78.7%75.0%實施例1-71.64%81.2%84%比較例1-81.83%76.8%60%實施例1-91.89%78.0%89%實施例2-高純度1,1,1,3-四氯丙烷的制備高純度1,1,1,3-四氯丙烷可以根據(jù)本發(fā)明的方法獲得,本發(fā)明的方法包括烷基化步驟(圖1)、第一蒸餾步驟(圖2)、水性催化劑回收步驟(圖3)和第二蒸餾步驟(圖4)。然而,應當理解,并不是所有這些步驟對于根據(jù)本發(fā)明的方法獲得高純度c3-6烷烴都是必需的。在圖1中所示的烷基化步驟中,乙烯和顆粒鐵通過管線1和管線2進料至連續(xù)攪拌槽反應器3中。將乙烯通過配備有噴嘴的浸管以氣體形式引入連續(xù)攪拌槽反應器3中。將受控的顆粒鐵進料至連續(xù)攪拌槽反應器3中。使用受控進料將顆粒鐵間歇地進料至連續(xù)攪拌槽反應器3中。使用顆粒鐵的不斷加入是因為當烷基化反應進行時,顆粒鐵溶解至反應混合物中。已發(fā)現(xiàn),通過保持反應混合物中顆粒鐵的存在可獲得最佳結果,在該實施例中,通過在初級烷基化區(qū)中加入1重量%至2重量%的反應混合物的顆粒鐵。這導致從初級烷基化區(qū)提取的反應混合物的溶解鐵含量為反應混合物的0.2重量%至0.3重量%。四氯化碳通過管線12以液體形式進料至連續(xù)攪拌槽反應器3中。在所示實施方案中,四氯化碳流用于捕集從反應混合物提取的氣態(tài)乙烯。然而,以這種方式使用四氯化碳對于本發(fā)明并不是必需的;作為四氯化碳的唯一或主要來源的新鮮四氯化碳進料可以進料至反應器3中。磷酸三丁酯/氯化鐵催化劑也通過管線12進料至連續(xù)攪拌槽反應器3中。該流中存在的磷酸三丁酯部分地從圖3中所示(并且在下文更詳細討論)的水性處理過程獲得,其余部分作為添加至體系中的新鮮磷酸三丁酯提供。管線12中的流另外包含鹵代烷烴提取劑。在所示實施方案中,使用位于連續(xù)攪拌槽反應器3中的單個初級烷基化區(qū)。當然,如果需要,可以使用例如在一個或多個連續(xù)攪拌槽反應器中的可以平行和/或連續(xù)操作的多個初級烷基化區(qū)。初級烷基化區(qū)在超大氣壓的壓力(5至8巴表壓)和升高的溫度(105℃至110℃)下操作,停留時間為100分鐘至120分鐘。選擇這些條件以使得四氯化碳和乙烯在烷基化反應中形成1,1,1,3-四氯丙烷。然而,已發(fā)現(xiàn),四氯化碳完全轉化為1,1,1,3-四氯丙烷是不希望的,因為這也導致形成不想要的雜質。因此,四氯化碳向感興趣的氯化c3-6烷烴的轉化水平受到控制,并且在本發(fā)明的該實施方案中不允許進行至超過95%。烷基化反應進程的控制部分地通過使用不利于四氯化碳完全轉化為1,1,1,3-四氯丙烷的反應條件,通過控制反應混合物在連續(xù)攪拌槽反應器中的停留時間來實現(xiàn)。將包含i)未反應的四氯化碳和乙烯,ii)1,1,1,3-四氯丙烷(本實施方案中的感興趣的氯化c3-6烷烴)和iii)磷酸三丁酯/氯化鐵催化劑的反應混合物從初級烷基化區(qū)(連續(xù)攪拌槽反應器3)提取出來,并進料至塞流反應器4(主烷基化區(qū)位于其中)中。提取反應混合物使得存在于初級烷基化區(qū)3中的顆粒鐵催化劑不被提取,因此反應混合物基本上不含顆粒材料。此外,在所示實施方案中,盡管塞流反應器4可以配備有催化劑床,但未向塞流反應器4中加入另外的催化劑。另外,未向塞流反應器4中加入另外的乙烯。在所示實施方案中,主烷基化區(qū)4中的操作壓力與初級烷基化區(qū)3中的操作壓力相同。反應混合物的停留時間為約30分鐘,其在所示實施方案中足以使得基本上全部存在的乙烯在反應中被用盡。當然,應當理解,對于不同的反應器類型和操作條件,不同的停留時間可能是最佳的。當?shù)竭_反應混合物在主烷基化區(qū)中的確定的最佳停留時間時,將反應混合物通過管線5從其提取出來,同時保持在升高的壓力和溫度下,并進料至閃蒸容器6中。在該容器中,將提取的反應混合物減壓至大氣壓。該壓降導致反應混合物中存在的乙烯的蒸發(fā)。將現(xiàn)在基本上不存在乙烯的富含1,1,1,3-四氯丙烷的混合物通過管線7從閃蒸容器提取出來,并使其經歷圖2中所示并在下文更詳細討論的蒸餾步驟。將蒸發(fā)的乙烯通過管線8從閃蒸容器6提取出來,并通過冷凝器9進料。然后,將乙烯通過管線10進料至吸收塔11中,在那里其與四氯化碳和磷酸三丁酯/氯化鐵催化劑的流接觸,所述的流在圖3中所示并在下文更詳細討論的水性處理步驟中從反應混合物回收。使回收的催化劑/四氯化碳的流13通過冷卻器14,然后通過管線15進料至吸收塔11中。冷卻的四氯化碳/催化劑流動通過吸收塔11具有將乙烯捕集于其中的作用。所獲得的四氯化碳/催化劑/乙烯液體流隨后被進料回連續(xù)攪拌槽反應器3中。從圖1可以看出,所示實施方案包括乙烯循環(huán)回路,出于幾個原因,其是有利的。首先,實現(xiàn)了乙烯的幾乎完全利用,因此從系統(tǒng)損失的乙烯的量非常低。另外,乙烯循環(huán)系統(tǒng)的組件的能量需求也很低。此外,從系統(tǒng)損失的乙烯的量也非常低,這意味著環(huán)境負擔降低。現(xiàn)在轉到圖2,從圖1中以附圖標記6示出的閃蒸容器提取的富含1,1,1,3-四氯丙烷的混合物通過管線101進料至分批蒸餾鍋爐102中,分批蒸餾鍋爐102與真空蒸餾塔104連通操作。蒸餾鍋爐在90℃至95℃的溫度下操作。將進料至鍋爐102中的混合物中存在的氯代烷烴蒸發(fā),并使用蒸餾塔104(以及下游冷凝器106和回流分流器108)分離成輕餾分流110.1、四氯化碳流110.2、四氯乙烯流110.3和純化的1,1,1,3-四氯丙烷產物流110.4。輕餾分流110.1和四氯乙烯流110.3可用于制備四氯化碳,從而有利地使廢物的產生最小化。這可以通過使用高溫氯解法來實現(xiàn)。將四氯化碳流110.2循環(huán)回連續(xù)攪拌槽反應器103中。將純化的1,1,1,3-四氯丙烷產物流110.4從系統(tǒng)提取出來,并且可以儲存用于運輸或用在需要純的1,1,1,3-四氯丙烷作為原材料的下游過程中。也包含催化劑的富含1,1,1,3-四氯丙烷的混合物作為殘渣通過管線103從鍋爐102提取出來,并經歷圖3中所示的催化劑回收步驟。在該步驟中,富含1,1,1,3-四氯丙烷的混合物通過管線202與通過管線201的淡(1-5%)鹽酸溶液一起進料至分批蒸餾鍋爐204中。有利地,存在于酸溶液中的水使催化劑體系失活并保護其免受熱損傷。這使得能夠從富含1,1,1,3-四氯丙烷的混合物回收催化劑體系,并且其可以容易地在回收后再活化,并且再用于烷基化過程,而沒有任何顯著的催化活性損失。分批蒸餾鍋爐在約100℃的溫度下操作,以產生包含1,1,1,3-四氯丙烷和水蒸汽的氣體混合物。然后,將在鍋爐204中產生的氣體混合物在塔210中進行粗1,1,1,3-四氯丙烷的蒸汽蒸餾(或汽提),塔210連接至鍋爐204。將粗1,1,1,3-四氯丙烷通過管線211從蒸餾塔210提取出來,用冷凝器212冷凝,通過管線213進料至回流液-液分離器214。來自氣體混合物的水通過管線215進料回蒸餾塔210,并且通過管線216取出一部分用于在圖4中更詳細地示出并在下文更詳細地討論的進一步的蒸餾步驟。然后,將鍋爐204的操作溫度降低以停止汽提,從而使其中存在的水蒸汽冷凝。這導致形成含有水相和含催化劑體系的有機相的兩相混合物,其尚未進行汽提。為了促進有機相的提取,將鹵代烷烴提取劑(在這種情況下為1,1,1,3-四氯丙烷)通過管線203添加至鍋爐204中以增加該相的體積。從兩相混合物提取有機相通過經由管線205從鍋爐204按順序提取各相來實現(xiàn)。將有機相通過管線205從鍋爐204提取出來,并進行在206過濾。濾餅通過管線207從過濾器206移除。有機相通過管線208提取,并且在該實施方案中,如圖1中所示,具體地通過圖1中的管線13進料回初級烷基化區(qū)。水相通過管線205提取,在206過濾并通過管線209排出。使汽提的粗1,1,1,3-四氯丙烷產物經歷圖4中所示的進一步的蒸餾步驟。在該步驟中,粗產物通過管線301進料至蒸餾鍋爐302中。鍋爐302與蒸餾塔304連通。粗1,1,1,3-四氯丙烷中存在的蒸發(fā)的氯化有機化合物在蒸餾塔304(以及相關下游設備、冷凝器306和回流分流器308)中分離成純化的1,1,1,3-四氯丙烷產物流310.1和氯化戊烷/戊烯流310.2。氯化戊烷/戊烯流310.2可用于制備四氯化碳,從而有利地使廢物的產生最小化。這可以通過使用高溫氯解法來實現(xiàn)。將純化的1,1,1,3-四氯丙烷產物流310.1從系統(tǒng)提取出來,并且可以與主產物流(在圖2中以附圖標記110.4標識)組合。該產物可以儲存用于運輸或用在需要純的1,1,1,3-四氯丙烷作為原材料的下游過程中。通過管線303從鍋爐302提取的重餾分殘渣被處理或進一步加工。使用上述設備和工藝條件,以78.2kg/h的平均小時負荷連續(xù)處理2635kg四氯化碳(ctc,99.97%純度)以生產1,1,1,3-四氯丙烯(1113tecpa)。根據(jù)實施例2進行的所公開方法的基本參數(shù)如下。上述實施方案的純化產物的全部雜質分布在下表中提供。請注意,這些數(shù)字作為在圖2中的管線110.4和圖4中的管線310.1中獲得產物的分布的加權平均值給出。實施例3:反應混合物中的原材料:產物的摩爾比對選擇性的影響。除非另有說明,否則這些實施例使用上文實施例1中的“連續(xù)布置”中所述的設備和技術進行。反應混合物中的氯化c3-6烷烴產物(在這種情況下為1,1,1,3-四氯丙烷):四氯化碳的摩爾比主要通過反應混合物在烷基化區(qū)中的停留時間被控制在不同的水平。溫度保持在110℃,而壓力保持在9巴。對感興趣產物的選擇性在下表中報告:從該實施例可以看出,當連續(xù)操作該方法時,當產物:原材料的摩爾比超過95:5時,對目標產物的選擇性顯著降低。實施例4:反應混合物中的原材料:產物的摩爾比對選擇性的影響。除非另有說明,否則這些實施例使用如圖1中所示的設備和技術,參考上文實施例2中的附文進行。反應混合物中的氯化c3-6烷烴產物(在這種情況下為1,1,1,3-四氯丙烷):四氯化碳的摩爾比主要通過控制乙烯起始材料的進料速率被控制在不同的水平。溫度恒定在110℃。對目標產物的選擇性在下表中報告:從該實施例可以看出,當連續(xù)操作該方法時,當產物:原材料的摩爾比超過95:5時,對目標產物的選擇性顯著降低。實施例5:原料純度的影響除非另有說明,否則這些實施例使用如圖2中所示的設備和技術,參考上文實施例2中的附文進行。試驗5-1是從圖2中的流110.4獲得的流。試驗5-2至5-5是使用相同的設備和技術但使用不同純度的原料獲得的替代實施例。下面的數(shù)據(jù)表明,盡管在試驗5-2至5-5中使用了較低純度的原料,但當從本發(fā)明的方法獲得時,這有利地不會顯著影響產物的純度。實施例6:連續(xù)攪拌槽反應器和塞流反應器組合除非另有說明,否則這些實施例使用如圖1中所示的設備和技術,參考上文實施例2中的附文進行。評估了第二塞流反應器(圖1中的附圖標記4)的反應效率。進行了兩個試驗,其中在塞流反應器的入口處溶解不同量的乙烯,所述塞流反應器在與主cstr反應器(圖1中的附圖標記3)相同的溫度即110℃下操作。結果在下表中示出:從該實施例可以看出,在塞流反應器中乙烯的轉化率為75%至93%。因此,如果使用塞流反應器,則在反應部分中乙烯的利用更有效。串聯(lián)式塞流反應器允許cstr反應器在最佳壓力下操作,而不需要復雜和不經濟的乙烯回收過程。因此,串聯(lián)式塞流反應器在有效的閉合回路中控制乙烯的使用。實施例7:在常規(guī)蒸餾期間催化劑配體的問題降解。裝配由裝備有冷凝器、溫度計、加熱浴和真空泵系統(tǒng)的2升玻璃蒸餾四頸燒瓶組成的分餾設備。蒸餾燒瓶最初裝填有1976克反應混合物,所述反應混合物使用圖1中所示并在上文實施例2中的附文中進行說明的設備和技術獲得。在蒸餾期間,壓力從100mmhg的初始壓力逐漸降低至6mmhg的最終壓力。在此期間,提取了1792克餾出物(不同餾分)。在蒸餾期間,可見hcl氣體形成,此外還形成了相當量,即餾出物餾分的1%至19%的氯丁烷(來自磷酸三丁酯配體的分解產物)。在進行這些觀察之后,中斷蒸餾,稱取蒸餾殘渣并進行分析,發(fā)現(xiàn)四氯丙烷含量為16%。不再可能在不顯著降解磷酸三丁酯配體的情況下繼續(xù)蒸餾。當前第1頁12