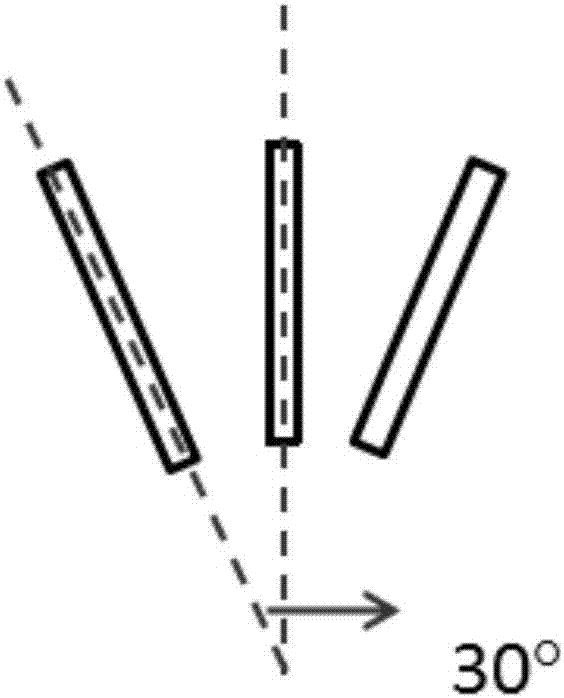
本發(fā)明涉及新材料粉體生產(chǎn)裝置
技術(shù)領(lǐng)域:
,具體是一種亞微米及納米金屬粉體的生產(chǎn)設(shè)備。
背景技術(shù):
:納米材料的生產(chǎn)技術(shù)是納米材料技術(shù)發(fā)展、研究和應(yīng)用的關(guān)鍵,目前納米材料的制備技術(shù)多達(dá)幾十種。納米金屬粉體作為納米材料一種廣泛應(yīng)用的材料,特別是在高品質(zhì)納米金屬粉體的制備上,實(shí)現(xiàn)產(chǎn)業(yè)化最好方法有蒸發(fā)-冷凝法和高溫氫還原法。蒸發(fā)-冷凝法生產(chǎn)過(guò)程可控,系統(tǒng)密閉,生產(chǎn)過(guò)程無(wú)廢氣廢水,而且粉體性能優(yōu)良,是生產(chǎn)高品質(zhì)亞微米及納米金屬粉體最好的方法。1984年,gleiter首次使用蒸發(fā)-冷凝法制備了超細(xì)鎳粉,該方法是利用電弧、高頻電場(chǎng)或等離子體等高溫?zé)嵩磳⒔饘僭显诟哒婵栈蛘叩蛪憾栊詺怏w中,加熱氣化或升華,然后快速冷凝成超細(xì)粉體,該方法可制備各種超細(xì)金屬粉體,特點(diǎn)為表面光潔,粒徑可控,球形度好。在隨后的30多年,各國(guó)研究者在gleiter的研究基礎(chǔ)上進(jìn)行再度研發(fā),通過(guò)設(shè)備的升級(jí),加熱方式的改變,理論基礎(chǔ)的深入研究,蒸發(fā)-冷凝法的技術(shù)得到了長(zhǎng)足的發(fā)展。根據(jù)加熱方式不同,蒸發(fā)-冷凝法具體可分為電阻加熱法、高頻感應(yīng)加熱法、激光加熱法,電子束加熱法及等離子體加熱法等,其不同加熱方法的簡(jiǎn)要比較,如表1所示。表1蒸發(fā)-冷凝法不同加熱方式的比較表加熱方式氣氛系統(tǒng)壓力(pa)產(chǎn)量設(shè)備要求電阻加熱惰性氣體133~13332低低高頻感應(yīng)加熱惰性氣體133~6500低低電子束加熱惰性氣體133低高激光束加熱惰性氣體1300~14000低高等離子體加熱惰性氣體26000~100000中等低從表1可知,等離子體加熱法因蒸發(fā)效率快,設(shè)備要求較低,所制備的超細(xì)粉體形核速率快,是目前蒸發(fā)-冷凝法中最好的制備超細(xì)金屬粉的方法之一。在等離子體加熱蒸發(fā)-冷凝法法制備金屬粉末工藝中,一般采用高頻等離子體、感應(yīng)等離子體、轉(zhuǎn)移弧等離子體或者非轉(zhuǎn)移弧等離子體加熱方法來(lái)蒸發(fā)金屬得到金屬蒸氣,隨后急冷金屬蒸氣得到超微細(xì)金屬粉末。在高頻等離子體、感應(yīng)等離子體、非轉(zhuǎn)移弧等離子體蒸發(fā)金屬設(shè)備制備超微細(xì)金屬粉末工藝中,一般采用一定粒度(50~300μm)的金屬粉作為原料,金屬粉直接加入到等離子體弧中,金屬粉在高頻等離子體弧的高溫作用下,金屬粉被蒸發(fā)變成金屬蒸氣,然后金屬蒸氣聚冷得到超微細(xì)金屬粉末。但由于進(jìn)料的金屬粉有一定的粒度分布,高頻等離子體、感應(yīng)等離子體、非轉(zhuǎn)移弧等離子體因能量不足,不僅蒸發(fā)量較低,而且會(huì)有部分粒徑比較大的金屬粒子蒸發(fā)不完全,殘留在超微細(xì)金屬粉中。這部分殘留的金屬粒子粒徑遠(yuǎn)遠(yuǎn)大于超微細(xì)金屬粉的粒徑,造成產(chǎn)品質(zhì)量的下降。在等離子體轉(zhuǎn)移弧蒸發(fā)金屬設(shè)備制備超微細(xì)金屬粉末工藝中,一般等離子體轉(zhuǎn)移弧直接作用在金屬液面上,利用等離子體轉(zhuǎn)移弧的高溫蒸發(fā)金屬得到金屬蒸氣,然后金屬蒸氣急冷得到超微細(xì)金屬粉末。但由于受到直流等離子體轉(zhuǎn)移弧與金屬液面熱量傳遞的限制,與金屬液面的接觸面小,造成金屬蒸發(fā)效率低,金屬粉體產(chǎn)量低,能量的消耗大,成本高。本發(fā)明要解決的技術(shù)問(wèn)題是,提供一種能提高金屬蒸發(fā)效率又無(wú)殘留金屬大顆粒在超微細(xì)金屬粉中的金屬蒸發(fā)設(shè)備,這種設(shè)備可以用于亞微米及納米金屬粉的生產(chǎn),特別是生產(chǎn)高熔點(diǎn)亞微米及納米金屬粉體材料。技術(shù)實(shí)現(xiàn)要素:本發(fā)明的目的在于提供一種亞微米及納米金屬粉體的生產(chǎn)設(shè)備,以解決上述
背景技術(shù):
中提出的問(wèn)題。為實(shí)現(xiàn)上述目的,本發(fā)明提供如下技術(shù)方案:一種亞微米及納米金屬粉體的生產(chǎn)設(shè)備,包括:等離子體發(fā)生器、等離子體轉(zhuǎn)移弧炬、金屬粉加料設(shè)備、密封不銹鋼外殼、陶瓷坩堝、電極石墨棒、廢料取料口、金屬蒸氣過(guò)渡區(qū)、粉體收集器;等離子體轉(zhuǎn)移弧炬安裝在密封不銹鋼外殼的上方,電極石墨棒貫穿陶瓷坩堝以及密封不銹鋼外殼的底部;陶瓷坩堝放置在密封不銹鋼外殼內(nèi)的底部;密封不銹鋼外殼的側(cè)面設(shè)有金屬蒸氣過(guò)渡區(qū),且金屬蒸氣過(guò)渡區(qū)的另一端連接有粉體收集器;金屬粉加料設(shè)備位于多把等離子體轉(zhuǎn)移弧炬中間,且貫穿密封不銹鋼外殼頂部;等離子體發(fā)生器的負(fù)極與等離子體轉(zhuǎn)移弧炬電連接,等離子體發(fā)生器的正極與電極石墨棒電連接。作為本發(fā)明進(jìn)一步的方案:密封不銹鋼外殼底部的一側(cè)設(shè)有廢料取料口。作為本發(fā)明進(jìn)一步的方案:等離子體轉(zhuǎn)移弧炬產(chǎn)生等離子體轉(zhuǎn)移弧,所述等離子體轉(zhuǎn)移弧的產(chǎn)生的介質(zhì)氣體包括氬氣、氮?dú)?、氫氣、氨氣中的一種或多種。作為本發(fā)明進(jìn)一步的方案:所述等離子體轉(zhuǎn)移弧炬的安裝數(shù)目為3~8把。作為本發(fā)明進(jìn)一步的方案:等離子體轉(zhuǎn)移弧炬與密封不銹鋼外殼上方垂直方向的夾角為10~60°。作為本發(fā)明進(jìn)一步的方案:通過(guò)金屬粉加料設(shè)備進(jìn)料的金屬粉為高熔點(diǎn)金屬粉或低熔點(diǎn)金屬粉,其中高熔點(diǎn)金屬粉包括鉭粉、鉭合金粉、鎢合金粉、鈦粉、鈦合金粉,粒徑為50~300μm;低熔點(diǎn)金屬粉包括鎳粉、鎳合金粉、銅粉、銅合金粉、鋁粉、鋁合金粉、錫合金粉與不銹鋼粉,粒徑為50~300μm。作為本發(fā)明進(jìn)一步的方案:陶瓷坩堝的直徑為150-350mm,放在等離子體轉(zhuǎn)移弧炬的中心下的80-250mm處。作為本發(fā)明進(jìn)一步的方案:粉體收集器內(nèi)放置冷卻系統(tǒng)。作為本發(fā)明進(jìn)一步的方案:冷卻系統(tǒng)包括氣相冷卻系統(tǒng)和液相冷卻系統(tǒng);其中生產(chǎn)不易氧化的金屬粉采用氣相冷卻系統(tǒng),不易氧化的金屬粉包括鎳粉、銅粉、鈷粉,氣相冷卻系統(tǒng)的氣體為氮?dú)?、氬氣、氦氣中的一種或者多種;生產(chǎn)易氧化的金屬粉采用液相冷卻系統(tǒng),易氧化的金屬粉包括鈦粉、鋁粉、鋰粉,液相冷卻系統(tǒng)的介質(zhì)包括但不限于水、酒精、柴油、煤油、癸烷。作為本發(fā)明進(jìn)一步的方案:金屬蒸氣過(guò)渡區(qū)、密封不銹鋼外殼、粉末收集器均含有通冷卻水的水夾層。與現(xiàn)有技術(shù)相比,本發(fā)明的有益效果是:本發(fā)明可以利用超高溫等離子體轉(zhuǎn)移弧直接蒸發(fā)較大粒徑的金屬粉,有效提高能量利用效率和增加金屬蒸發(fā)量,適合各種10~1000nm金屬粉體的生產(chǎn),特別是高熔點(diǎn)金屬粉體和易氧化的金屬粉。具體特點(diǎn)如下所述:1)采用3~8把等離子體轉(zhuǎn)移弧炬作為加熱源進(jìn)行加熱蒸發(fā),能量利用率高,蒸發(fā)效率更快,產(chǎn)量很大,避免了大部分金屬顆粒進(jìn)入陶瓷坩堝中造成了浪費(fèi),產(chǎn)量可到5~30kg/h,2)生產(chǎn)設(shè)備通用性強(qiáng),可適合各種10~1000nm金屬粉的生產(chǎn),生產(chǎn)成本低,容易實(shí)現(xiàn)大規(guī)模工業(yè)化生產(chǎn)。3)適合亞微米及納米級(jí)高熔點(diǎn)金屬的生產(chǎn),以及易氧化的納米級(jí)鈦粉、鋁粉、鋰粉等的生產(chǎn)。附圖說(shuō)明圖1是本發(fā)明亞微米及納米金屬粉體的生產(chǎn)設(shè)備的結(jié)構(gòu)示意圖。圖2是實(shí)施例1生產(chǎn)106nm鉭粉用6把等離子體轉(zhuǎn)移弧炬布局的主視圖;圖3是實(shí)施例1生產(chǎn)106nm鉭粉用6把等離子體轉(zhuǎn)移弧炬布局的俯視圖;圖4是實(shí)施例1所生產(chǎn)106nm鉭粉sem圖。圖5是實(shí)施例2所生產(chǎn)82nm鋁粉sem圖。圖6是實(shí)施例3所生產(chǎn)289nm鎳粉sem圖。圖7是液相冷卻系統(tǒng)流程圖。圖8是氣相冷卻系統(tǒng)流程圖。圖中:1-等離子體發(fā)生器;2-等離子體轉(zhuǎn)移弧炬;4-金屬粉加料設(shè)備;5-金屬粉;6-等離子體轉(zhuǎn)移??;7-密封不銹鋼外殼;8-陶瓷坩堝;9-電極石墨棒;10-廢料取料口;11-金屬蒸氣過(guò)渡區(qū);12-粉體收集器。具體實(shí)施方式下面將結(jié)合本發(fā)明實(shí)施例,對(duì)本發(fā)明實(shí)施例中的技術(shù)方案進(jìn)行清楚、完整地描述,顯然,所描述的實(shí)施例僅僅是本發(fā)明一部分實(shí)施例,而不是全部的實(shí)施例?;诒景l(fā)明中的實(shí)施例,本領(lǐng)域普通技術(shù)人員在沒(méi)有做出創(chuàng)造性勞動(dòng)前提下所獲得的所有其他實(shí)施例,都屬于本發(fā)明保護(hù)的范圍。請(qǐng)參閱圖1,本發(fā)明中,一種亞微米及納米金屬粉體的生產(chǎn)設(shè)備,包括:等離子體發(fā)生器1、等離子體轉(zhuǎn)移弧炬2、金屬粉加料設(shè)備4、密封不銹鋼外殼7、陶瓷坩堝8、電極石墨棒9、廢料取料口10、金屬蒸氣過(guò)渡區(qū)11、粉體收集器12。等離子體轉(zhuǎn)移弧炬2安裝在密封不銹鋼外殼7的上方,電極石墨棒9貫穿陶瓷坩堝8以及密封不銹鋼外殼7的底部;陶瓷坩堝8放置在密封不銹鋼外殼7內(nèi)的底部,密封不銹鋼外殼7底部的一側(cè)設(shè)有廢料取料口10;密封不銹鋼外殼7的側(cè)面設(shè)有金屬蒸氣過(guò)渡區(qū)11,且金屬蒸氣過(guò)渡區(qū)11的另一端連接有粉體收集器12;金屬粉加料設(shè)備4位于多把等離子體轉(zhuǎn)移弧炬2中間,與電極石墨棒9相對(duì),且貫穿密封不銹鋼外殼7頂部。等離子體發(fā)生器1的負(fù)極與等離子體轉(zhuǎn)移弧炬2電連接,等離子體發(fā)生器1的正極與電極石墨棒9電連接。本發(fā)明的原理是利用多把等離子體轉(zhuǎn)移弧炬2產(chǎn)生超高溫的等離子體轉(zhuǎn)移弧6直接蒸發(fā)金屬粉加料設(shè)備4下落的較大粒徑的金屬粉5,隨后通過(guò)急冷得到亞微米及納米級(jí)金屬粉體,適合各種10~1000nm金屬粉體的工業(yè)化生產(chǎn),特別是高熔點(diǎn)金屬粉體和易氧化的金屬粉。密封不銹鋼外殼7內(nèi)有介質(zhì)氣體,等離子體轉(zhuǎn)移弧6的產(chǎn)生的介質(zhì)氣體可以是氬氣、氮?dú)?、氫氣或者氨氣,也可以是上述氣體的混合氣體。等離子體轉(zhuǎn)移弧6具有能量密度高(能量密度可達(dá)105~106w/cm2),溫度高(弧柱中心溫度30000k~300000k),焰流速度大(可達(dá)300~800m/s)等優(yōu)點(diǎn)。所述等離子體轉(zhuǎn)移弧炬2,其安裝數(shù)目根據(jù)所生產(chǎn)金屬熔點(diǎn)、粒徑以及產(chǎn)量設(shè)置為3~8把,等離子體轉(zhuǎn)移弧炬2與密封不銹鋼外殼7上方垂直方向的夾角,可根據(jù)生產(chǎn)情況,選用10~60°放置。所述等離子體轉(zhuǎn)移弧炬2中心放置了金屬粉加料設(shè)備4,大粒徑的金屬粉5通過(guò)金屬粉加料設(shè)備4加入到多把等離子體轉(zhuǎn)移弧炬2產(chǎn)生的等離子體轉(zhuǎn)移弧6中。進(jìn)料的金屬粉5可以為高熔點(diǎn)金屬粉和低熔點(diǎn)金屬粉,其中高熔點(diǎn)金屬粉包括鉭及鉭合金粉、鎢合金粉、鈦及鈦合金粉,粒徑為50~300μm;低熔點(diǎn)金屬粉包括鎳及鎳合金粉、銅及銅合金粉、鋁及鋁合金粉、錫合金粉與不銹鋼粉,粒徑為50~300μm,經(jīng)過(guò)生產(chǎn)所得的亞微米及納米金屬粉粒徑為10~1000nm。電極石墨棒9與等離子體發(fā)生器1、等離子體轉(zhuǎn)移弧炬2以及等離子體轉(zhuǎn)移弧6構(gòu)成回路。陶瓷坩堝8的直徑為150-350mm,放在等離子體轉(zhuǎn)移弧炬2的中心下的80-250mm處,用于收集未蒸發(fā)的進(jìn)料金屬殘留粉。金屬蒸氣蒸發(fā)進(jìn)入金屬蒸氣過(guò)渡區(qū)11,并連接粉體收集器12,金屬蒸氣過(guò)渡區(qū)11為調(diào)節(jié)金屬蒸氣的冷卻速度和形核長(zhǎng)大的空間,粉體收集器12內(nèi)放置冷卻系統(tǒng),用于收集金屬粉末。收集粉體性質(zhì)的不同,冷卻系統(tǒng)包括氣相冷卻系統(tǒng)和液相冷卻系統(tǒng)。其中生產(chǎn)不易氧化的金屬粉,如鎳粉、銅粉、鈷粉等,氣相冷卻系統(tǒng)的氣體可以為氮?dú)?、氬氣、氦氣中的一種或者多種;生產(chǎn)易氧化的金屬粉,如鈦粉、鋁粉、鋰粉等,液相冷卻系統(tǒng)的介質(zhì)包括水、酒精、柴油、煤油、癸烷等有機(jī)溶劑。所述的密封不銹鋼外殼7,其含有一定厚度的保溫材料,作用是防止內(nèi)部高溫區(qū)域外界空氣接觸,并減少熱損失,提高蒸發(fā)效率。所述的金屬蒸氣過(guò)渡區(qū)11、密封不銹鋼外殼7、粉末收集器12均含有通冷卻水的水夾層。具體應(yīng)用如以下實(shí)施例所述。實(shí)施例1106nm鉭電容用鉭粉的生產(chǎn)采用6把等離子體轉(zhuǎn)移弧炬2,相隔60°放置,等離子體弧炬與豎直方向的放置夾角為30°,如圖2-3所示。將平均粒徑為25~100μm的不規(guī)則鉭原料粉加入金屬粉加料設(shè)備4,檢查系統(tǒng)密封性完畢后,開(kāi)啟開(kāi)啟鼓風(fēng)機(jī),使得系統(tǒng)內(nèi)的氬氣循環(huán),開(kāi)啟等離子體發(fā)生器1,功率控制在400~500kw,隨后同時(shí)啟動(dòng)金屬粉加料設(shè)備4,進(jìn)料速度控制在5~10kg/h。大粒徑鉭粉,通過(guò)金屬粉加料設(shè)備4進(jìn)入超高溫等離子體轉(zhuǎn)移弧中心,在6把等離子體轉(zhuǎn)移弧炬2的作用下,大粒徑鉭粉瞬間蒸發(fā),并在氬氣保護(hù)下從金屬蒸氣過(guò)渡區(qū)11進(jìn)入氣相冷卻系統(tǒng),氣相系統(tǒng)流程圖如圖8所示。在冷卻系統(tǒng)中,金屬蒸氣冷卻長(zhǎng)大形成納米鉭粉,然后納米鉭粉和氬氣通過(guò)氣固分離器,收集到金屬粉末,氣體循環(huán)使用。少量未蒸發(fā)的進(jìn)料大顆粒鉭粉,再掉入在設(shè)備內(nèi)放置的陶瓷坩堝8中,陶瓷坩堝8的直徑為150-350mm,放在等離子體轉(zhuǎn)移弧炬2的中心下的80-250mm處。所得鉭粉通過(guò)比表面儀檢測(cè),其平均粒徑為106nm,另有樣品在掃描電子顯微鏡下觀察形貌,如圖4。實(shí)施例282nm固體推進(jìn)劑用高活性鋁粉的生產(chǎn)采用3把等離子槍?zhuān)喔?20°放置,等離子體弧炬與豎直方向的放置夾角為30°。將平均粒徑為15~100μm的噴霧法所生產(chǎn)大粒徑鋁粉加入金屬粉加料設(shè)備4,檢查系統(tǒng)密封性完畢后,開(kāi)啟開(kāi)啟鼓風(fēng)機(jī),使得系統(tǒng)內(nèi)的氬氣循環(huán),開(kāi)啟等離子體發(fā)生器1,功率控制在200~250kw,隨后同時(shí)啟動(dòng)金屬粉加料設(shè)備4,進(jìn)料速度控制在8~16kg/h。大粒徑鋁粉,通過(guò)金屬粉加料設(shè)備4進(jìn)入超高溫等離子體轉(zhuǎn)移弧中心,在3把等離子體轉(zhuǎn)移弧炬2的作用下,粉瞬間蒸發(fā),并在氬氣保護(hù)下從金屬蒸氣過(guò)渡區(qū)11進(jìn)入液相冷卻系統(tǒng),液相系統(tǒng)流程圖如圖7所示,液相介質(zhì)采用煤油。在冷卻系統(tǒng)中,金屬蒸氣瞬間冷卻成納米鋁粉,然后納米鋁粉和煤油通過(guò)高速離心機(jī)進(jìn)行液固分離,收集到鋁粉,煤油循環(huán)使用。少量未蒸發(fā)的進(jìn)料大顆粒鋁粉,再掉入在設(shè)備內(nèi)放置的陶瓷坩堝8中,陶瓷坩堝8的直徑為150-350mm,放在等離子體轉(zhuǎn)移弧炬2的中心下的80-250mm處。所得鋁粉通過(guò)比表面儀檢測(cè),其平均粒徑為82nm,另有樣品在掃描電子顯微鏡下觀察形貌,如圖5所示。實(shí)施例3289nm電子元器件電極材料用鎳粉的生產(chǎn)采用3把等離子槍?zhuān)喔?20°放置,等離子體弧炬與豎直方向的放置夾角為30°,如圖2所示。將平均粒徑為25~100μm的鎳粉加入金屬粉加料設(shè)備4,檢查系統(tǒng)密封性完畢后,開(kāi)啟開(kāi)啟鼓風(fēng)機(jī),使得系統(tǒng)內(nèi)的氮?dú)庋h(huán),開(kāi)啟等離子體發(fā)生器1,功率控制在250~400kw,隨后同時(shí)啟動(dòng)金屬粉加料設(shè)備4,進(jìn)料速度控制在15~25kg/h。大粒徑鎳粉,通過(guò)金屬粉加料設(shè)備4進(jìn)入超高溫等離子體轉(zhuǎn)移弧中心,在3把等離子體轉(zhuǎn)移弧炬2的作用下,瞬間蒸發(fā),并在氮?dú)獗Wo(hù)下從金屬蒸氣過(guò)渡區(qū)11進(jìn)入氣相冷卻系統(tǒng),氣相系統(tǒng)流程圖如圖5所示。在冷卻系統(tǒng)中,金屬蒸氣冷卻長(zhǎng)大形成將鎳粉,然后鎳粉和氮?dú)馔ㄟ^(guò)氣固分離器,收集到金屬粉末,氣體循環(huán)使用。少量未蒸發(fā)的進(jìn)料大顆粒鎳粉,再掉入在設(shè)備內(nèi)放置的陶瓷坩堝8中,陶瓷坩堝8的直徑為150-350mm,放在等離子體轉(zhuǎn)移弧炬2的中心下的80-250mm處。所得鎳粉通過(guò)比表面儀檢測(cè),其平均粒徑為289nm,另有樣品在掃描電子顯微鏡下觀察形貌,如圖6所示。對(duì)于本領(lǐng)域技術(shù)人員而言,顯然本發(fā)明不限于上述示范性實(shí)施例的細(xì)節(jié),而且在不背離本發(fā)明的精神或基本特征的情況下,能夠以其他的具體形式實(shí)現(xiàn)本發(fā)明。因此,無(wú)論從哪一點(diǎn)來(lái)看,均應(yīng)將實(shí)施例看作是示范性的,而且是非限制性的,本發(fā)明的范圍由所附權(quán)利要求而不是上述說(shuō)明限定,因此旨在將落在權(quán)利要求的等同要件的含義和范圍內(nèi)的所有變化囊括在本發(fā)明內(nèi)。此外,應(yīng)當(dāng)理解,雖然本說(shuō)明書(shū)按照實(shí)施方式加以描述,但并非每個(gè)實(shí)施方式僅包含一個(gè)獨(dú)立的技術(shù)方案,說(shuō)明書(shū)的這種敘述方式僅僅是為清楚起見(jiàn),本領(lǐng)域技術(shù)人員應(yīng)當(dāng)將說(shuō)明書(shū)作為一個(gè)整體,各實(shí)施例中的技術(shù)方案也可以經(jīng)適當(dāng)組合,形成本領(lǐng)域技術(shù)人員可以理解的其他實(shí)施方式。當(dāng)前第1頁(yè)12