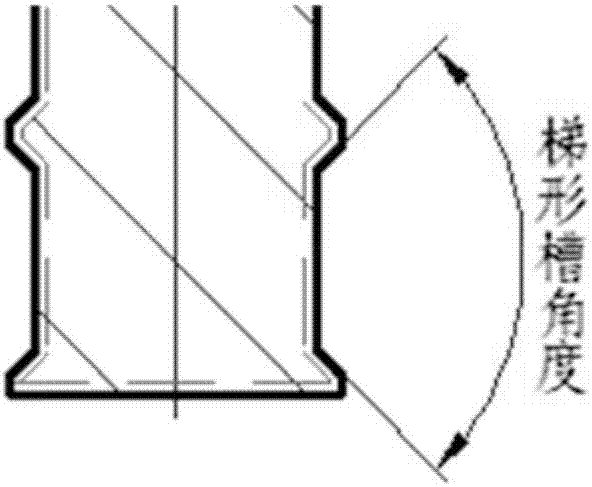
本發(fā)明涉及在保證低成本的同時切削能力強、加工精度高、適用玻璃范圍廣、并且所得玻璃的邊部質(zhì)量高的玻璃面板的加工方法。進一步,涉及包含利用該方法加工得到的玻璃面板的光伏/光熱器件。
背景技術(shù):
:隨著世界范圍內(nèi)能源供應(yīng)緊張狀況日益加劇,能源將成為制約各國經(jīng)濟的主要因素。太陽能作為清潔的可再生能源,越來越受到人們的重視,應(yīng)用領(lǐng)域也越來越廣泛。作為同樣都是利用太陽能進行發(fā)電的可再生能源技術(shù),太陽能光熱(集熱)發(fā)電是將光能轉(zhuǎn)變?yōu)闊崮堋⑷缓笤偻ㄟ^傳統(tǒng)的熱力循環(huán)做功發(fā)電的技術(shù)。而光伏發(fā)電是由光子使電子躍遷,形成電位差,從而將光能直接轉(zhuǎn)變?yōu)殡娔艿募夹g(shù)。光熱發(fā)電與光伏發(fā)電都是人類對太陽能的有效利用方式,是解決當(dāng)前乃至未來人類能源、資源、環(huán)境等問題的有效途徑和方法。伴隨光伏/光熱產(chǎn)業(yè)的發(fā)展,玻璃面板的應(yīng)用領(lǐng)域越來越廣泛,對于光伏/光熱玻璃面板的需求也越來越大,前期種類以鈉鈣玻璃居多,而隨著玻璃技術(shù)的發(fā)展,高鋁玻璃的性能遠遠優(yōu)于鈉鈣玻璃,以高鋁玻璃為主導(dǎo)的光伏/光熱組件由于在經(jīng)過各工序加工后性能優(yōu)異,因而已成為主流趨勢。市場上的光伏/光熱玻璃面板的厚度一般為1mm以上,迄今為止,對厚度為1mm以上的玻璃面板的外形加工大多是通過仿形磨邊機而實現(xiàn)的。需要說明的是,傳統(tǒng)的仿形磨邊機通常依靠固定式、旋轉(zhuǎn)的砂輪,通過移動玻璃面板邊部與砂輪接觸而實現(xiàn)對玻璃面板邊部的加工。但是,這樣的傳統(tǒng)仿形磨邊機由于工作機理是移動玻璃而固定用于磨削的砂輪,因此加工穩(wěn)定性較差,進而,這樣得到的玻璃板的邊部質(zhì)量缺陷較多,很容易發(fā)生崩邊、燒邊、欠磨等,尤其是邊部崩邊尺寸經(jīng)??蛇_100~200um、甚至有時大于200um,嚴重影響了后續(xù)工序良率。并且,這樣得到的玻璃板的外形尺寸精度不高,尺寸誤差通常在±1mm左右,而這樣的尺寸誤差很可能影響到后續(xù)模組裝配。另外,很多特異的異形形狀是利用傳統(tǒng)的仿形磨邊機所無法實現(xiàn)的。技術(shù)實現(xiàn)要素:發(fā)明要解決的問題鑒于上述情況,本發(fā)明的目的在于解決如上所述的傳統(tǒng)仿形磨邊機中存在的問題,提供在保證低成本的同時切削能力強、加工精度高、適用玻璃范圍廣、并且所得玻璃的邊部質(zhì)量高的玻璃面板的加工方法。進一步,本發(fā)明的目的還在于提供包含利用該方法加工得到的玻璃面板的光伏/光熱器件。解決問題的方法本發(fā)明人等為了達成上述目的而進行了深入研究,結(jié)果發(fā)現(xiàn),通過利用特定的磨削組合刀具代替?zhèn)鹘y(tǒng)的仿形磨邊機、并采取包含特定的分段磨削加工工序的加工方法對玻璃面板進行邊部加工,可以在保證高切削強度的同時實現(xiàn)尺寸誤差在±0.03mm以內(nèi)的高加工精度,并且可以大幅減少崩邊、燒邊、欠磨等邊部質(zhì)量缺陷,獲得理想的邊部質(zhì)量,同時,能夠廣泛地對應(yīng)各種尺寸及形狀的玻璃,另外,由于所使用的磨削組合刀具更換方便、使用壽命長,因而可大幅降低成本。具體而言,本發(fā)明提供一種玻璃面板的加工方法,其包括開料工序:利用開料機將待加工玻璃面板切割成比成品尺寸大0.6mm以上、優(yōu)選大0.6~2.0mm,以及,邊部加工工序:利用磨削組合刀具對在開料工序中得到的玻璃面板進行邊部加工。其中,所述邊部加工工序包括粗磨工序及多段精磨倒邊工序,所述磨削組合刀具包含磨削機構(gòu)、驅(qū)動機構(gòu)及控制機構(gòu)。在本發(fā)明的如上所述的玻璃面板的加工方法中,所述磨削機構(gòu)優(yōu)選包含安裝柄、粗磨磨削區(qū)及精磨倒邊區(qū),在所述粗磨磨削區(qū)和所述精磨倒邊區(qū)之間任選具有分界槽,所述精磨倒邊區(qū)優(yōu)選至少包含第一精磨倒邊區(qū)及第二精磨倒邊區(qū),所述驅(qū)動機構(gòu)優(yōu)選為精雕機,所述控制機構(gòu)優(yōu)選為計算機輔助系統(tǒng)。并且,優(yōu)選所述磨削機構(gòu)安裝在所述驅(qū)動機構(gòu)的主軸上,并利用所述控制機構(gòu)對所述驅(qū)動機構(gòu)進行控制。在本發(fā)明的如上所述的玻璃面板的加工方法中,所述玻璃面板厚度優(yōu)選為0.55mm以上、更優(yōu)選為0.55~5mm。所述磨削組合刀具的磨削機構(gòu)優(yōu)選是在基體上形成金剛石顆粒層而成的。其中,所述基體的材質(zhì)優(yōu)選為硬質(zhì)合金、更優(yōu)選為鎳鉻合金。所述磨削機構(gòu)的總長優(yōu)選為40~60mm,其中的安裝柄直徑優(yōu)選為6mm以上,粗磨磨削區(qū)的直徑優(yōu)選為6mm以上,精磨倒邊區(qū)的直徑優(yōu)選為6mm以上。在本發(fā)明的如上所述的玻璃面板的加工方法中,在所述粗磨磨削區(qū)形成的金剛石顆粒層為金剛石粗顆粒層,所述金剛石粗顆粒的目數(shù)優(yōu)選為200~600目、更優(yōu)選為300~500目、最優(yōu)選為400目,在所述精磨倒邊區(qū)形成的金剛石顆粒層為金剛石細顆粒層,在所述第一精磨倒邊區(qū)形成的金剛石細顆粒的目數(shù)優(yōu)選為800~1100目、更優(yōu)選為1000目,在所述第二精磨倒邊區(qū)形成的金剛石細顆粒的目數(shù)優(yōu)選為1000~1500目、更優(yōu)選為1200目。在本發(fā)明的如上所述的玻璃面板的加工方法中,在所述精磨倒邊區(qū)優(yōu)選設(shè)置有倒邊形狀槽,該倒邊形狀槽優(yōu)選為梯形槽、v型槽、u型槽、圓弧形槽,其中更優(yōu)選為梯形槽。其中,為梯形槽時,所述梯形槽的梯形槽角度優(yōu)選為50°~120°、更優(yōu)選為60°~100°、進一步優(yōu)選為90±1°,所述梯形槽的倒角大小優(yōu)選為玻璃厚度的15%~45%、更優(yōu)選為20%~40%、進一步優(yōu)選為25%~35%、最優(yōu)選為30%。在本發(fā)明的如上所述的玻璃面板的加工方法中,在所述邊部加工工序中,所述驅(qū)動機構(gòu)的主軸轉(zhuǎn)速優(yōu)選為40000~60000轉(zhuǎn)/min,所述磨削機構(gòu)的所述安裝柄、粗磨磨削區(qū)及精磨倒邊區(qū)的同軸度優(yōu)選為0.01~0.05mm、更優(yōu)選為0.02mm、進一步優(yōu)選為0.01mm以下,所述主軸徑向跳動優(yōu)選小于0.05mm、更優(yōu)選為0.03mm。在本發(fā)明的如上所述的玻璃面板的加工方法中,在所述邊部加工工序中,在所述玻璃面板的厚度為0.55~1.0mm時,所述主軸轉(zhuǎn)速優(yōu)選為40000~60000轉(zhuǎn)/min、更優(yōu)選為45000mm/min,磨削量優(yōu)選為0.10~0.25mm、更優(yōu)選為0.20mm,粗磨工序的進給倍率優(yōu)選為400~800mm/min、更優(yōu)選為600mm/min,精磨工序的進給倍率優(yōu)選為500~900mm/min、更優(yōu)選為700mm/min;在所述玻璃面板的厚度為1.0~2.0mm時,所述主軸轉(zhuǎn)速優(yōu)選為30000~50000轉(zhuǎn)/min、更優(yōu)選為40000mm/min,磨削量優(yōu)選為0.10~0.30mm、更優(yōu)選為0.20mm,粗磨工序的進給倍率優(yōu)選為300~600mm/min、更優(yōu)選為400mm/min,精磨工序的進給倍率優(yōu)選為700~900mm/min;在所述玻璃面板的厚度為2.0~5.0mm時,所述主軸轉(zhuǎn)速優(yōu)選為30000~40000轉(zhuǎn)/min、更優(yōu)選為38000mm/min,磨削量優(yōu)選為0.10~0.30mm、更優(yōu)選為0.20mm,粗磨工序的進給倍率優(yōu)選為200~500mm/min、更優(yōu)選為300mm/min,精磨工序的進給倍率優(yōu)選為700~900mm/min。進一步,本發(fā)明提供一種光伏/光熱器件,其包含利用上述任一玻璃面板的加工方法加工得到的玻璃面板。發(fā)明的效果根據(jù)本發(fā)明的玻璃面板的加工方法,通過利用特定的磨削組合刀具代替?zhèn)鹘y(tǒng)的仿形磨邊機、并采取包含特定的分段磨削加工工序的加工方法對玻璃面板進行邊部加工,可以在利用在刀具上形成的金剛石顆粒來保證高切削強度的同時實現(xiàn)尺寸誤差在±0.03mm以內(nèi)的高加工精度,并且,通過分多段進行不同程度的磨削,并嚴格管理磨削機構(gòu)中各部分間的同軸度,可以大幅減少崩邊、燒邊、欠磨等邊部質(zhì)量缺陷,獲得理想的邊部質(zhì)量,另外,通過將精磨倒邊區(qū)的倒邊形狀槽靈活地設(shè)置為梯形槽、v型槽、u型槽、圓弧形槽,并靈活地設(shè)置倒邊形狀槽的角度,能夠廣泛地對應(yīng)各種尺寸及形狀的玻璃。此外,根據(jù)本發(fā)明,還能夠提供包含利用如上所述的玻璃面板的加工方法加工得到的玻璃面板的光伏/光熱器件。附圖說明[圖1]示出了本發(fā)明的一個實施方式的磨削組合刀具的磨削機構(gòu)的構(gòu)成的示意圖。[圖2]示意性地示出了梯形槽角度的概念圖。[圖3]示意性地示出了倒角大小的概念圖。[圖4]示出了本發(fā)明的另一實施方式的磨削組合刀具的磨削機構(gòu)的構(gòu)成的示意圖。符號說明1第一精磨倒邊區(qū)2第二精磨倒邊區(qū)3分界槽4粗磨磨削區(qū)5安裝柄具體實施方式本發(fā)明涉及的玻璃面板的加工方法,其包括利用開料機將待加工玻璃面板切割成比成品尺寸大0.6mm以上、優(yōu)選大0.6~2.0mm的開料工序、和利用磨削組合刀具對在開料工序中得到的玻璃面板進行邊部加工的邊部加工工序。其中,所述邊部加工工序包括粗磨工序及多段精磨倒邊工序,并且,所述磨削組合刀具包含磨削機構(gòu)、驅(qū)動機構(gòu)及控制機構(gòu)。在利用開料機進行的開料工序中,所述開料機例如可以使用全自動玻璃切割機,其中,切割刀輪優(yōu)選選用高滲透鉆石刀輪,刀輪切割角度優(yōu)選設(shè)為155°以下,切割速度優(yōu)選設(shè)為30000~50000mm/min,切割壓力優(yōu)選設(shè)為4000hp以下(英制馬力單位,1hp=746w)。其中,可配合適當(dāng)濃度的切削液或類似于保護刀頭的液體,從而確保切割后的光伏光熱玻璃邊部效果更佳,更有利于后序的邊部加工。關(guān)于待加工玻璃,可以選用厚度為0.55mm以上、優(yōu)選為0.55~5mm的玻璃面板。該玻璃面板的透光率優(yōu)選為91.5%以上,由此,可謀求加工得到的玻璃面板兼具高透光性、和耐化性及抗沖擊性等機械性能。在選用0.55~5mm的玻璃面板時,可以進一步根據(jù)玻璃面板的厚度的差異而選擇不同的開料條件。例如,在所述玻璃面板的厚度為0.55~1.0mm時,所述刀輪切割角度優(yōu)選為125°以下,切割速度優(yōu)選為30000~50000mm/min,切割壓力優(yōu)選為3000hp以下。由此,玻璃切割后的切線細膩、斷面平滑,無明顯側(cè)裂紋和凹凸感,切割良品率高,便于后續(xù)的邊部加工。在所述光伏光熱玻璃面板厚度為1~2mm時,所述刀輪切割角度優(yōu)選為125~135°,切割速度優(yōu)選為30000~40000mm/min,切割壓力優(yōu)選3000~4000hp。由此,玻璃切割后的切線細膩、斷面平滑,無明顯側(cè)裂紋和凹凸感,切割良品率高,便于后續(xù)的邊部加工。在所述光伏光熱玻璃面板厚度為2~3mm時,所述刀輪切割角度優(yōu)選為135°~145°,切割速度優(yōu)選為30000~40000mm/min,切割壓力優(yōu)選為2000~3000hp,其特征在于玻璃切割后切線細膩、斷面平滑,無明顯側(cè)裂紋和凹凸感,切割良品率高,便于后續(xù)的邊部加工。在所述光伏光熱玻璃面板厚度3mm~5mm時,所述刀輪切割角度優(yōu)選為145°~155°,切割速度優(yōu)選為30000mm/min以下,切割壓力優(yōu)選為3000~4000hp。由此,玻璃切割后切線細膩、斷面平滑,無明顯側(cè)裂紋和凹凸感,切割良品率高,便于后續(xù)的邊部加工。接著,將在上述開料工序中切割得到的玻璃面板依靠真空吸附機構(gòu)吸附在專用治具上,利用本發(fā)明的磨削組合刀具對該玻璃面板進行邊部加工。以圖1所示的本發(fā)明的一個實施方式的磨削組合刀具的磨削機構(gòu)為例,所述磨削組合刀具包含磨削機構(gòu)、驅(qū)動機構(gòu)及控制機構(gòu)。所述磨削機構(gòu)包含安裝柄5、粗磨磨削區(qū)4及精磨倒邊區(qū),該精磨倒邊區(qū)至少包含第一精磨倒邊區(qū)1及第二精磨倒邊區(qū)2。具體而言,所述磨削組合刀具的磨削機構(gòu)是在基體上形成、例如電鍍金剛石顆粒層而成的,其總長優(yōu)選為40~60mm。在安裝柄前端設(shè)置有包含第一精磨倒邊區(qū)及第二精磨倒邊區(qū)的精磨倒邊區(qū),安裝柄的直徑優(yōu)選為6mm以上,優(yōu)選優(yōu)選選用表面光滑的材質(zhì),例如,安裝柄的材質(zhì)優(yōu)選為硬質(zhì)合金、更優(yōu)選為鎳鉻合金。精磨倒邊區(qū)的直徑優(yōu)選為6mm以上。連接精磨倒邊區(qū)和安裝柄之間的是粗磨磨削區(qū),粗磨磨削區(qū)的直徑優(yōu)選為6mm以上。通過這樣地設(shè)置磨削機構(gòu)各部分的尺寸,可使加工的尺寸精準、使用方便、加工效率高、穩(wěn)定性優(yōu)良。另外,在所述粗磨磨削區(qū)形成的金剛石顆粒層為金剛石粗顆粒層,所述金剛石粗顆粒的目數(shù)優(yōu)選為200~600目、更優(yōu)選為300~500目、最優(yōu)選為400目。通過這樣地設(shè)置金剛石粗顆粒層的金剛石顆粒的目數(shù),可以進一步提高加工效率,獲得更佳的切削能力。需要說明的是,通常使在所述粗磨磨削區(qū)形成的金剛石顆粒層的長度大于待加工玻璃面板的厚度,以便靈活調(diào)整粗磨,提高刀具的使用壽命。在所述精磨倒邊區(qū)形成的金剛石顆粒層為金剛石細顆粒層,在所述第一精磨倒邊區(qū)和所述第二精磨倒邊區(qū)上電鍍有不同粒度的金剛石細顆粒層。例如,在所述第一精磨倒邊區(qū)形成的金剛石細顆粒的目數(shù)優(yōu)選為800~1100目、更優(yōu)選為1000目,在所述第二精磨倒邊區(qū)形成的金剛石細顆粒的目數(shù)優(yōu)選為1000~1500目、更優(yōu)選為1200目。通過這樣地設(shè)置金剛石細顆粒層的金剛石顆粒的目數(shù),可以達到更理想的邊部磨削效果,使經(jīng)過多段精磨倒邊工序后的玻璃面板的邊部達到更理想的光亮、光滑程度。另外,在所述粗磨磨削區(qū)和所述精磨倒邊區(qū)之間任選具有分界槽3,優(yōu)選設(shè)置有環(huán)型分界槽。在所述精磨倒邊區(qū)(至少包括第一精磨倒邊區(qū)及第二精磨倒邊區(qū))設(shè)置有倒邊形狀槽,該倒邊形狀槽優(yōu)選為梯形槽、v型槽、u型槽、圓弧形槽,更優(yōu)選為梯形槽。通過這樣地設(shè)置倒邊形狀槽并根據(jù)實際需要而選擇該倒邊形狀槽的形狀,可以實現(xiàn)對不同形狀及種類的玻璃面板的加工,并且可以進一步提高加工穩(wěn)定性。需要說明的是,在本發(fā)明中優(yōu)選的梯形槽,不僅包括梯形的上底及下底長度不等的形狀,也包括梯形上底和下底長度相等的情形。即,就圖2所示的梯形槽角度而言,包括該角度為90°的情況。在選擇梯形槽作為倒邊形狀槽的情況下,其梯形槽角度優(yōu)選為50°~120°、更優(yōu)選為60°~100°、進一步優(yōu)選為90°,需要說明的是,這里的90°包括存在少許誤差的情況,例如,可以包含90±1°的情況。通過這樣地設(shè)置梯形槽角度,可以減少玻璃面板被磨削時與刀具之間的震動,進一步達到更理想的加工效果。另外,所述梯形槽的倒角大小優(yōu)選為玻璃厚度的15%~45%、更優(yōu)選為20%~40%、進一步優(yōu)選為25%~35%、最優(yōu)選為30%。這里,所述倒角大小即倒邊尺寸大小,如圖3所示,指的是相對于玻璃厚度而言的斜邊的邊長尺寸大小,即圖3中的倒角大小c。例如:玻璃厚度為0.55mm,倒角大小為厚度的30%,即,0.55×0.30=0.165mm,玻璃經(jīng)研磨后,端面形狀為梯形狀,倒角大小為0.165mm為斜邊邊長尺寸大小。通過這樣地設(shè)置梯形槽的倒角大小,可以減少玻璃面板磨削時與刀具之間的震動,進一步達到更理想的加工效果。在本發(fā)明的磨削組合刀具中,所述驅(qū)動機構(gòu)優(yōu)選為精雕機,通過將所述磨削機構(gòu)安裝在所述驅(qū)動機構(gòu)、例如精雕機的主軸上,并利用所述控制機構(gòu)對所述驅(qū)動機構(gòu)進行控制,可以達到更理想的邊部磨削效果,使經(jīng)過邊部磨削后的崩邊尺寸最小。另外,所述驅(qū)動機構(gòu)、例如精雕機的主軸轉(zhuǎn)速優(yōu)選為40000~60000轉(zhuǎn)/min,所述主軸徑向跳動,也稱主軸徑向跳動幅度,即磨頭在旋轉(zhuǎn)過程中的徑向擺動。需要說明的是,擺動會使磨頭對玻璃邊部的切削力不均,易產(chǎn)生崩邊及微裂紋,且形態(tài)為連續(xù)性。主軸徑向跳動優(yōu)選小于0.05mm、更優(yōu)選為0.03mm。這是由于,驅(qū)動機構(gòu)的主軸高速旋轉(zhuǎn)時的轉(zhuǎn)速越高,刀具切削力越大,但主軸徑向跳動越大,邊部質(zhì)量越差,反之,轉(zhuǎn)速越低則刀具切削力越小,但主軸徑向跳動越小,邊部質(zhì)量越好,因此,需要使主軸轉(zhuǎn)速與刀具粒度、刀具加工質(zhì)量、磨削量等參數(shù)相匹配。其中,通過將主軸轉(zhuǎn)速設(shè)定為如上所述的范圍,可以進一步提高磨削邊部的加工質(zhì)量。通過將主軸徑向跳動設(shè)定在上述范圍,可以進一步提高磨削邊部的加工穩(wěn)定性。另外,所述磨削機構(gòu)的所述安裝柄、粗磨磨削區(qū)及精磨倒邊區(qū)的同軸度優(yōu)選為0.01~0.05mm、更優(yōu)選為0.02mm、進一步優(yōu)選為0.01mm以下。這里,所述同軸度是指插芯內(nèi)徑距離整個圓心的偏移程度,理想狀態(tài)是0,就是不偏移。但是在實際中無法達到理想狀態(tài),會產(chǎn)生一定的偏移。該同軸度的測定方法包括擺差測定儀測量法、手動影像測量儀法、圓度測量儀法、三坐標測量機法、全自動影像測量儀法等,本發(fā)明中采用的是擺差測定儀測量法。通過將同軸度設(shè)定在上述范圍,可以進一步減少加工得到的玻璃面板的邊部崩邊等缺陷。在邊部加工工序中,選用0.55~5.0mm的玻璃面板時,可以進一步根據(jù)玻璃面板的厚度的差異而選擇不同的邊部加工條件。例如,在所述玻璃面板的厚度為0.55~1.0mm時,所述主軸轉(zhuǎn)速優(yōu)選為40000~60000轉(zhuǎn)/min、更優(yōu)選為45000mm/min,由此,可以進一步提高磨削邊部的加工質(zhì)量,磨削量優(yōu)選為0.10~0.25mm、更優(yōu)選為0.20mm,粗磨工序的進給倍率優(yōu)選為400~800mm/min、更優(yōu)選為600mm/min,精磨工序的進給倍率優(yōu)選為500~900mm/min、更優(yōu)選為700mm/min,由此,可以保證加工質(zhì)量并提高加工效率;在所述玻璃面板的厚度為1.0~2.0mm時,所述主軸轉(zhuǎn)速優(yōu)選為30000~50000轉(zhuǎn)/min、更優(yōu)選為40000mm/min,由此,可以進一步提高磨削邊部的加工質(zhì)量,磨削量優(yōu)選為0.10~0.30mm、更優(yōu)選為0.20mm,粗磨工序的進給倍率優(yōu)選為300~600mm/min、更優(yōu)選為400mm/min,精磨工序的進給倍率優(yōu)選為700~900mm/min,由此,可以保證加工質(zhì)量并提高加工效率;在所述玻璃面板的厚度為2.0~5.0mm時,所述主軸轉(zhuǎn)速優(yōu)選為30000~40000轉(zhuǎn)/min、更優(yōu)選為38000mm/min,由此,可以進一步提高磨削邊部的加工質(zhì)量,磨削量優(yōu)選為0.10~0.30mm、更優(yōu)選為0.20mm,粗磨工序的進給倍率優(yōu)選為200~500mm/min、更優(yōu)選為300mm/min,精磨工序的進給倍率優(yōu)選為700~900mm/min,由此,可以保證加工質(zhì)量并提高加工效率。需要說明的是,上述中的磨削量指的是待加工玻璃面板的表面到實際加工表面的垂直距離。所述進給倍率指的是刀具加工時的行進的速度。例如,相對于十分鐘可加工完成的情況而言,如果調(diào)大進給倍率,即可縮短加工時間縮短,如果減小進給倍率,即可時加工時間波長。另外,在粗磨工序及多段精磨倒邊工序中,刀數(shù)為1以上即可,所述刀數(shù)也稱下刀數(shù),指的是加工的次數(shù)。本發(fā)明中,通過將粗磨工序及多段精磨倒邊工序設(shè)置為1以上,可保證加工質(zhì)量和提高加工效率。另外,本發(fā)明的磨削組合刀具中的控制機構(gòu)用于對驅(qū)動機構(gòu)進行控制。具體而言,例如可以將作為驅(qū)動機構(gòu)的精雕機與作為計算機輔助系統(tǒng)的cad/cam軟件結(jié)合使用。所述cad/cam指的是計算機輔助設(shè)計(computeraideddesign)和計算機輔助制造(computeraidedmaking),其核心是利用計算機進行設(shè)計和數(shù)值控制,從而實現(xiàn)按照工程人員的指令對驅(qū)動設(shè)備的設(shè)計、驅(qū)動及控制。除了本發(fā)明提供的光伏光熱玻璃面板磨削組合刀具,利用精雕機結(jié)合,針對加工1mm以上的光伏光熱玻璃面板,從而能加工出不同形狀高精度、高質(zhì)量的光伏光熱玻璃面板,使用金剛石得到最大程度的利用,通過調(diào)整光伏光熱玻璃面板與刀具之間的坐標高度,可以不用更換刀具,一次性完成外形粗磨、外形精磨及倒邊等步驟,簡化了工序,節(jié)約了成本,提高了生產(chǎn)效率。這樣一來。根據(jù)本發(fā)明的實施方式之一的玻璃面板的加工方法,通過將磨削機構(gòu)、驅(qū)動機構(gòu)及控制機構(gòu)相結(jié)合而構(gòu)成磨削組合刀具,并利用這樣的磨削組合刀具對經(jīng)開料工序得到的玻璃面板進行邊部加工,能夠加工出不同形狀高精度、高質(zhì)量的光伏光熱玻璃面板,使金剛石得到最大程度的利用。另外,通過調(diào)整玻璃面板與刀具之間的坐標高度,可以不用更換刀具,一次性完成外形粗磨、外形精磨及倒邊等步驟,可簡化工序、節(jié)約成本、提高生產(chǎn)效率。如上所述,示出了如圖1所示的本發(fā)明的一個實施方式的磨削組合刀具的磨削機構(gòu)的構(gòu)成。在圖1所示的構(gòu)成中,與安裝柄5的直徑相比,粗磨磨削區(qū)4、精磨倒邊區(qū)(第一精磨倒邊區(qū)1及第二精磨倒邊區(qū)2)的直徑較大。由于在這樣的情況下,在主軸轉(zhuǎn)速一定的情況下,磨削直徑越大則圓周速度越大,因此該實施方式的磨削組合刀具適合于厚度為2mm以上的較厚玻璃面板的加工,方便刀具更換,加工效率相對較高。與此相對,在本發(fā)明的另一實施方式的磨削組合刀具的磨削機構(gòu)中,也可以如圖4所示那樣,使安裝柄5的直徑與粗磨磨削區(qū)4、精磨倒邊區(qū)(第一精磨倒邊區(qū)1及第二精磨倒邊區(qū)2)的直徑相同。在該情況下,在主軸轉(zhuǎn)速一定的情況下,在磨削直徑較大時圓周速度較小,因此該實施方式的磨削組合刀具更適合于厚度小于2mm的較薄玻璃面板的加工。實施例以下,結(jié)合實施例對本發(fā)明的技術(shù)方案作進一步的說明,但本發(fā)明并不限定于此。需要說明的是,凡是對本發(fā)明技術(shù)方案進行修改或者等同替換、而不脫離本發(fā)明技術(shù)方案的精神和范圍的技術(shù)方案,均應(yīng)涵蓋在本發(fā)明的保護范圍中。在本發(fā)明的實施例中,利用包括下述工序的玻璃面板的加工方法制造了玻璃面板。(1)開料工序利用開料機(全自動玻璃切割機;型號:yxt-cnc05;制造商:東莞維迪光電器材有限公司)將下述表1所示的各厚度的待加工玻璃面板(以下,如無特殊說明,本發(fā)明的實施例中使用的待加工玻璃面板均為四川旭虹光電科技有限公司制造的玻璃面板)、基于表1中示出的各參數(shù)切割成了比目標的成品尺寸大0.6~2.0mm的玻璃面板。[表1](2)粗磨工序?qū)⒗鐖D1或圖4所示的作為磨削機構(gòu)的組合式金剛石刀具安裝在精雕機(型號:da-650t;制造商:東莞迪奧數(shù)控)的機床主軸上,將開好料的玻璃面板依靠真空系統(tǒng)吸附在專用治具上。其中,上述組合式金剛石刀具包含第一精磨倒邊區(qū)1、第二精磨倒邊區(qū)2、粗磨磨削區(qū)4及安裝柄5。具體而言,在安裝柄5前端設(shè)置的包含第一精磨倒邊區(qū)1及第二精磨倒邊區(qū)2的精磨倒邊區(qū)電鍍有1000目/1200目(砂號)的金剛石細顆粒層,并使作為梯形槽的倒邊形狀槽的倒邊角度為90°。在精磨倒邊區(qū)電鍍有400目(砂號)的金剛石粗顆粒層。另外,在第二精磨倒邊區(qū)2與粗磨磨削區(qū)4之間設(shè)置有環(huán)形分界槽3。其中,使電鍍在粗磨磨削區(qū)4的400目的金剛石粗顆粒層長度大于加工玻璃面板的厚度,以便靈活調(diào)整粗磨,提高刀具的使用壽命。精雕機通過軟件mastercam9.1(美國cncsoftwareinc.公司開發(fā)的基于pc平臺的cad/cam軟件)調(diào)整刀具與玻璃面板之間的位置高度,利用粗磨磨削區(qū)4沿玻璃面板周邊走刀至少一周以上,從而進行粗磨工序。所述玻璃面板的厚度為0.55~5.0mm,粗磨磨削邊部的磨削量與程序設(shè)置參見下述表2。[表2]需要說明的是,上述表2中示出的磨頭直徑,指的是粗磨磨削區(qū)的直徑。(3)多段精磨倒邊工序重新調(diào)整刀具和玻璃面板之間的位置,利用第一精磨倒邊區(qū)的梯形槽上形成的1000目金剛石細顆粒層、第二精磨倒邊區(qū)的梯形槽上形成的1200目金剛石細顆粒層沿玻璃面板周邊走刀至少一周以上,完成精磨倒邊工序。詳細條件與程序設(shè)置參見下述表3的記載。需要說明的是,下述表3所針對的厚度在0.55~5.0mm內(nèi)的縱400mm×橫500mm的不同玻璃面板而進行的。[表3]根據(jù)上述表3中的崩邊大小的結(jié)果可知,利用電鍍在第一精磨倒邊區(qū)3的1000目的金剛石細顆粒層、電鍍在第二精磨倒邊區(qū)4的1200目的金剛石細顆粒層,達到了更理想的邊部磨削效果,并且,玻璃邊部端面粗糙度ra均較低(均在0.18μm以內(nèi))。其中,為了證明梯形槽角度對邊部加工質(zhì)量的影響,對于同樣的玻璃縱400mm×橫500mm×厚2.0mm,在除了梯形槽角度不同以外,其它條件和程序與上述表3中厚度為1.0~2.0mm時采用的條件完全相同的情況下進行了玻璃面板的加工,并對加工得到的玻璃面板的崩邊大小進行了評價。詳情如下述表4所示。[表4]梯形槽角度(°)崩邊大小(μm)5029.66025.39020.111028.812029.613027.6需要說明的是,上述梯形槽角度是利用奧林巴斯(olympus)株式會社制造的型號為bx51-p的偏光顯微鏡進行觀察并測定的。上述崩邊大小利用奧林巴斯(olympus)株式會社制造的型號為bx51-p的偏光顯微鏡進行了觀察,需要說明的是,所示崩邊大小采用的是針對6塊以上玻璃面板進行測定而得到的平均值。根據(jù)上述表4的結(jié)果可以明確的是,在其它條件相同且均符合本發(fā)明的構(gòu)成的情況下,在梯形槽角度為90°的情況下崩邊大小明顯更小、即取得了更為優(yōu)異的邊部加工質(zhì)量。另外,為了證明在使用本發(fā)明的特定的磨削組合刀具時相對于傳統(tǒng)的仿形磨邊機(型號:fx-120、制造商:江西中航)所加工得到的玻璃的優(yōu)異性能,對于相同規(guī)格的玻璃樣品,分別采用仿形磨邊機和精雕機進行加工,并針對加工得到的玻璃的尺寸精度、磨削量、崩邊大小、端面粗糙度進行了評價和比較。詳細結(jié)果參見下述表5。[表5]需要說明的是,上述尺度精度是采用日本三豐株式會社制造的精度為±0.05mm的0~600mm數(shù)顯卡尺進行測定的。上述邊部缺陷的評價是通過利用10倍率的放大鏡對加工得到的玻璃面板的邊部進行目測觀察而進行的評價。上述崩邊大小利用奧林巴斯(olympus)株式會社制造的型號為bx51-p的偏光顯微鏡進行了觀察,需要說明的是,所示崩邊大小采用的是針對6塊以上玻璃面板進行測定而得到的平均值。上述端面粗糙度使用株式會社東京精密制造的型號為480a的粗糙度儀進行了測量。根據(jù)上述表5的結(jié)果可知,通過利用本發(fā)明特定的磨削組合刀具、并采取本發(fā)明特定的包含分段磨削加工工序的加工方法對玻璃面板進行邊部加工,與傳統(tǒng)的仿形磨邊機,在尺寸精度、磨削量、崩邊大小、端面粗糙度方面均獲得了令人滿意的技術(shù)效果。以上,結(jié)合實施例對本發(fā)明的技術(shù)方案及技術(shù)效果進行了詳細說明,但上述實施例僅為本發(fā)明的優(yōu)選實施例,并非對本發(fā)明保護范圍的限制,但凡是采用本發(fā)明的設(shè)計原理,以及在此基礎(chǔ)上對本發(fā)明技術(shù)方案進行修改或者等同替換、而不脫離本發(fā)明技術(shù)方案的精神和范圍的技術(shù)方案,均涵蓋在本發(fā)明的保護范圍之內(nèi)。當(dāng)前第1頁12