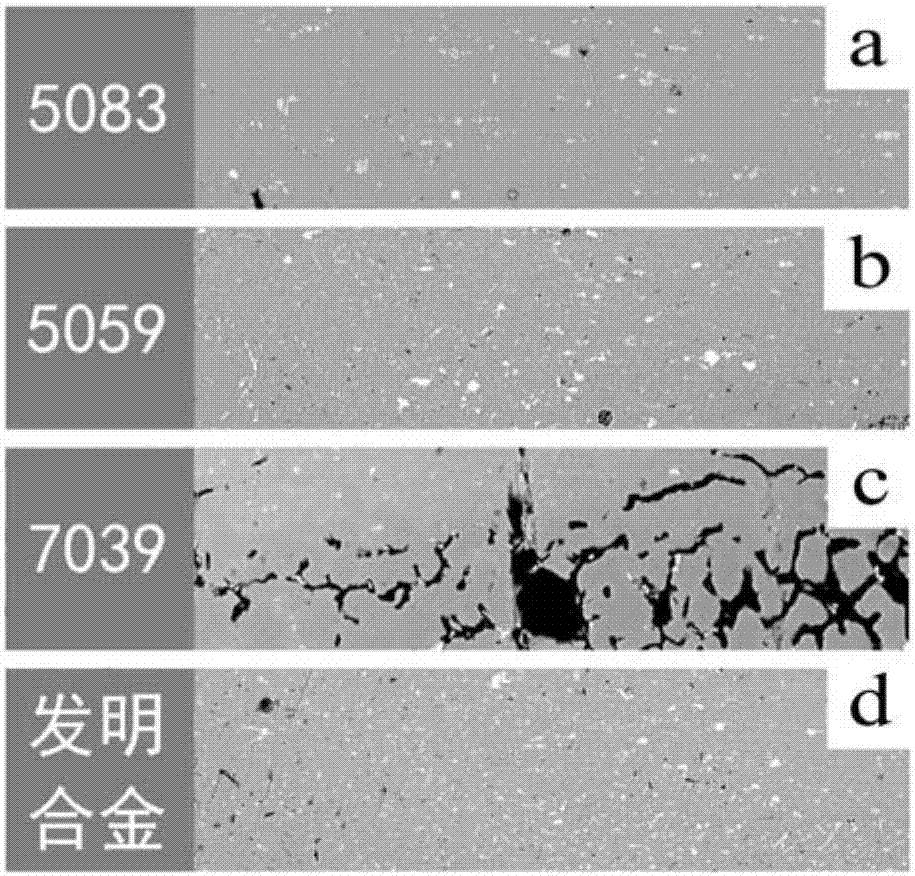
本發(fā)明屬于有色金屬及其制備領(lǐng)域,尤其涉及一種提升鋁合金焊縫強度和抗裂能力的方法,適用于船舶以及裝甲板的生產(chǎn)制造過程。
背景技術(shù):
:在船舶運輸、軍用裝甲行業(yè)中,使用高比強度鋁合金材料替換傳統(tǒng)的鋼鐵材料已經(jīng)成為一種新的趨勢,其可以保證合金使用強度不變的同時顯著減輕船舶、裝甲車輛的整體重量,從而大幅提升船舶燃油的利用效率以及裝甲車的作戰(zhàn)機動性能。由于船舶以及裝甲用材均具有大面積、高跨度的特征,在生產(chǎn)過程中必須使用金屬連接工藝(主要是焊接)將小尺寸原料相互連接進而得到,因此,所用鋁合金材料的可焊性以及焊后性能必須作為一種重要選材考量指標(biāo)?,F(xiàn)階段大量用于上述行業(yè)的鋁合金材料主要為5xxx系和7xxx系。常用的5xxx系鋁合金(例如aa5083)可焊性優(yōu)異,但其基體和焊縫強度相對較低,且該類合金的強化手段主要為加工硬化,焊接后焊縫強度損失較大,故應(yīng)用上存在一定局限;傳統(tǒng)7xxx系鋁合金(例如aa7039和aa7017)強度等力學(xué)性能相對較好,但由于mg、zn以及cu元素的含量都處于易發(fā)生焊接結(jié)晶裂紋的區(qū)間導(dǎo)致其可焊性不及5xxx系鋁合金,在焊接過程中容易產(chǎn)生焊接裂紋以及微裂紋,焊縫服役可靠性較差。因此,開發(fā)一種提升鋁合金焊縫強度和抗裂能力的技術(shù)對于船舶以及軍事工業(yè)具有重要意義。首先在選擇合金成分上,1999年,美國鋁業(yè)協(xié)會登記注冊的aa5059合金在常規(guī)5xxx系合金的基礎(chǔ)之上提高了mg和zn的含量,使得合金晶內(nèi)析出較多的t-al32(mgzn)49相。這種合金在保留常規(guī)5xxx系合金優(yōu)秀的耐蝕性、可焊性的同時,屈服及抗拉強度也得到了較大程度的提升。已公開的上述典型合金的組成范圍分別為:aa5083:mg含量為4.0~4.9,mn含量為0.4~1.0,cr含量為0.05~0.25,zn含量不高于0.25,cu含量不高于0.1,ti含量不高于0.15,fe含量不高于0.4,si含量不高于0.4;aa7039:mg含量為2.3~3.3,mn含量為0.1~0.4,cr含量為0.15~0.25,zn含量為3.5~4.5,cu含量不高于0.1,ti含量不高于0.1,fe含量不高于0.4,si含量不高于0.3;aa5059:mg含量為5.0~6.0,mn含量為0.6~1.2,cr含量不高于0.25,zn含量為0.4~0.9,cu含量不高于0.25,ti含量不高于0.2,fe含量不高于0.5,si含量不高于0.45,zr含量為0.05~0.25。其中aa5059的合金含量也公開在us-6695935-b1、us-6238495-b1、cn-101233252-a和cn-101631882-a專利中。發(fā)明專利zl201410577461.5又在aa5059合金的基礎(chǔ)上將zn含量上調(diào),降低mg在基體中的固溶量,借鑒7xxx系鋁合金時效強化的思想,最終得到晶粒內(nèi)部含大量t-al32(mgzn)49相的高強al-mg-zn合金并成功制備其板材,為時效強化型5xxx系鋁合金的設(shè)計和制備奠定了基礎(chǔ)。但此類合金由于合金度相對于7xxx系合金較低,焊接接頭強度仍然沒有達到7xxx系合金的強度級別,使得其應(yīng)用具有一定局限性。技術(shù)實現(xiàn)要素:本發(fā)明的目的在于,基于高zn含量的al-mg合金,通過焊接、焊后人工時效工藝,使焊縫在焊接過程中具有良好的抵抗焊接裂紋的能力,焊縫強度接近7xxx系合金的強度級別,但焊縫抵御焊接裂紋能力明顯優(yōu)于7xxx系,并具有較高的服役可靠性,適用于船舶以及裝甲板的生產(chǎn)制造過程,因而具有良好的工業(yè)以及軍事應(yīng)用前景。實現(xiàn)本發(fā)明采用如下步驟:將質(zhì)量百分含量為4.0~7.0%mg、2.0~4.0%zn、0~0.6%cu、0.1~1.2%mn、0~0.1%cr、0~0.25%ti、0~0.3%zr、0~0.6%fe、0~0.6%si,其余為al的al-mg-zn系合金板材進行mig焊接,焊接后實行人工時效處理,其人工時效處理是將板材加熱至60~160℃并保溫100~180h,然后空冷。優(yōu)選地,所述al-mg-zn系合金質(zhì)量百分含量為4.0~6.0%mg,2.5~3.5%zn,0~0.4%cu,0.5~1.0%mn,0~0.1%cr,0~0.15%ti,0.05~0.25%zr,0~0.4%fe,0~0.4%si,其余為al。所述mig焊接過程中焊機工藝參數(shù)為:焊機工作電流70~110a,工作電壓8~18v,起弧停留時間小于4.0s,填絲速度5.0~10.0m/min,焊接速度5.0~18.0mm/s,氬氣流量12~18l/min。進一步地,所述mig焊接過程中,焊機的工作參數(shù)具體為:焊機工作電流80~100a,工作電壓10~15v,起弧停留時間小于2.0s,填絲速度5.0~8.0m/min,焊接速度8.0~15.0mm/s,氬氣流量12~18l/min。進一步地,所述焊后人工時效的具體工藝為:將焊接后的板材加熱至80~120℃并保溫150~170h,然后空冷。本發(fā)明的優(yōu)越性在于,第一,本發(fā)明所述al-mg-zn合金由于具有時效析出能力,經(jīng)過焊接和焊后時效強化后的焊縫強度相比5xxx系參考合金(aa5059以及aa5083)有較大幅提升,已經(jīng)接近7xxx系參考合金(aa7039)的焊縫強度水平,達到243.9mpa;第二,使用本發(fā)明所述焊接工藝對發(fā)明合金進行焊接,其焊縫抵御焊接裂紋能力與5xxx系參考合金相近,且明顯優(yōu)于7xxx系參考合金,無焊接熱裂紋。本發(fā)明所述al-mg-zn合金的焊接工藝,非常適用于船舶以及裝甲板的生產(chǎn)制造過程。附圖說明圖1是魚骨狀焊接結(jié)晶裂紋實驗的試樣尺寸示意圖。圖2是焊接液化裂紋實驗試樣斷口顯微圖像。a為5083合金斷口;b為5059合金斷口;c為7039合金斷口;d為本發(fā)明實施例1合金斷口。實施方式參考以下實施例來進一步說明本發(fā)明。實施例1本例所涉及的所有實驗合金及參考合金均在實驗室范圍內(nèi)制備完成,合金制備環(huán)節(jié)所用設(shè)備以及通用工藝(熔煉、軋制、退火等)完全相同,制備不同成分的合金共計四種,其成分及用途見表1。表1本例發(fā)明所用合金化學(xué)成分及用途表(質(zhì)量百分數(shù),wt%)本例所述合金板材的制備工藝流程如下:熔煉鑄造→雙級均勻化退火→熱軋變形→中間退火→冷軋變形→固溶淬火→雙級時效至t6狀態(tài)。鑄錠的雙級均勻化退火工藝具體為:將鑄錠以20~40℃/s的速率從室溫升溫至420~440℃并保溫3~8h,隨后以20~40℃/s的速率升溫至500~535℃保溫5~15h,最后以20~40℃/s的速率將鑄錠隨爐降溫至室溫。熱軋變形工藝具體為:將試樣加熱至470~500℃保溫2~3h,然后進行變形量90%以上的熱變形,變形溫度區(qū)間為380~480℃。中間退火及冷軋變形工藝具體為:將試樣在350~400℃進行60~90min的再結(jié)晶退火,然后進行變形量為50%的冷軋變形。固溶及時效工藝具體為:將處于冷軋態(tài)的試樣在500~535℃的鹽浴爐中保溫10~30min后立即水淬,隨后進行80~100℃和130~150℃的雙級時效處理,至t6狀態(tài),此狀態(tài)為合金板材用于焊接的最終狀態(tài)。本例所述合金板材的焊接及焊后時效工藝流程如下:所使用mig焊機的工作參數(shù)具體為:裝填er5556焊絲,焊機工作電流焊機工作電流90a,工作電壓12v,起弧停留時間1.0s,填絲速度8m/min,焊接速度10mm/s,氬氣流量15l/min,將焊接后的板材進行適當(dāng)?shù)淖匀粫r效或人工時效,所述焊后人工時效的具體工藝為:將焊接后的板材加熱至100℃并保溫160h,然后空冷得到最終焊后板材。使用拉伸試驗機測量所制得合金焊縫的強度,合金焊縫的力學(xué)性能如表2所示。本發(fā)明合金焊縫在強度級別上與傳統(tǒng)5xxx系參考合金相比更加接近于7xxx系參考合金,且大幅超過兩種5xxx系參考合金。表2合金焊接后力學(xué)性能。合金用途屈服強度(mpa)50835xxx參考合金172.650595xxx參考合金177.770397xxx參考合金245.6al-mg-zn發(fā)明合金243.9使用魚骨狀裂紋擴展實驗定量評定實驗合金焊接過程中產(chǎn)生結(jié)晶裂紋的傾向,魚骨狀試樣尺寸見附圖1,焊接該試樣的工藝與上述mig焊接工藝完全相同。該試樣可以在焊接過程中對焊縫部分的金屬熔體施加由大到小的約束使得焊縫開裂,開裂的長短可以定量評價合金抵御焊接結(jié)晶裂紋的能力的強弱。通過表3可知,發(fā)明合金與兩種5xxx系參考合金相同,在焊接過程中均未產(chǎn)生結(jié)晶裂紋,而7xxx系參考合金在mig焊接過程中產(chǎn)生了明顯的焊接結(jié)晶裂紋,且裂紋長度遠遠超過其他三種合金。由此可見,發(fā)明合金具有與常規(guī)5xxx系合金相近的抵御焊接結(jié)晶裂紋的能力,且遠遠超過常規(guī)7xxx系合金。表3魚骨狀裂紋擴展實驗結(jié)果合金用途裂紋長度(mm)50835xxx參考合金050595xxx參考合金070397xxx參考合金38al-mg-zn發(fā)明合金0使用環(huán)形拘束實驗定量評測合金在焊接過程中發(fā)生液化裂紋的傾向,焊接該試樣的工藝與上述mig焊接工藝完全相同。該實驗?zāi)>呖梢詫δ讨械暮缚p金屬提供拘束,模擬較大拘束下的焊縫凝固產(chǎn)生液化裂紋或微裂紋的行為。經(jīng)過環(huán)形拘束實驗后的焊縫橫截面部分熔化區(qū)的顯微圖像如圖2,從中可見,本發(fā)明合金(d)和5xxx系參考合金(a)、(b)相同,焊后部分熔化區(qū)沒有微裂紋產(chǎn)生,而7xxx系參考合金(c)焊后部分熔化區(qū)則出現(xiàn)明顯微裂紋。由此可見,發(fā)明合金抵御焊接液化裂紋能力與5xxx系參考合金接近,強于7xxx系參考合金。實施例2本例所用發(fā)明和金成分如表4,主合金元素zn含量質(zhì)量分數(shù)降至2.5%,mg含量質(zhì)量分數(shù)降至4.5%。表4本例發(fā)明所用合金化學(xué)成分及用途表(質(zhì)量百分數(shù),wt%)本例所述合金板材的焊接及焊后時效工藝流程如下:所使用mig焊機的工作參數(shù)具體為:裝填er5556焊絲,焊機工作電流焊機工作電流75a,工作電壓10.5v,起弧停留時間2.0s,填絲速度7m/min,焊接速度8mm/s,氬氣流量16.5l/min,將焊接后的板材進行適當(dāng)?shù)淖匀粫r效或人工時效,所述焊后人工時效的具體工藝為:將焊接后的板材加熱至95℃并保溫170h,然后空冷得到最終焊后板材。使用本例工藝參數(shù)對改變主合金元素的合金進行焊接及焊后時效處理后,焊縫強度和抗焊接裂紋能力與實施例1展現(xiàn)出相同的趨勢,即焊縫強度接近7xxx系合金,同時具有接近5xxx系合金的優(yōu)異抗焊接裂紋能力。實施例3本例所用發(fā)明和金成分如表5,主合金元素zn含量質(zhì)量分數(shù)升至3.5%,mg含量質(zhì)量分數(shù)升至6%。表5本例發(fā)明所用合金化學(xué)成分及用途表(質(zhì)量百分數(shù),wt%)本例所述合金板材的焊接及焊后時效工藝流程如下:所使用mig焊機的工作參數(shù)具體為:裝填er5556焊絲,焊機工作電流焊機工作電流105a,工作電壓14.5v,起弧停留時間0.5s,填絲速度8m/min,焊接速度12mm/s,氬氣流量15l/min,將焊接后的板材進行適當(dāng)?shù)淖匀粫r效或人工時效,所述焊后人工時效的具體工藝為:將焊接后的板材加熱至105℃并保溫150h,然后空冷得到最終焊后板材。使用本例工藝參數(shù)對改變主合金元素的合金進行焊接及焊后時效處理后,焊縫強度和抗焊接裂紋能力與實施例1展現(xiàn)出相同的趨勢,即焊縫強度接近7xxx系合金,同時具有接近5xxx系合金的優(yōu)異抗焊接裂紋能力。綜上所述,本發(fā)明所設(shè)計的合金成分及對應(yīng)的焊接和焊后熱處理工藝很好的解決了船舶以及裝甲用鋁合金焊縫無法同時具備高強度和良好可焊性的問題。zn元素的提升使得合金焊接后可以被時效強化,因此可以有效避免焊縫在焊接之后由于再結(jié)晶帶來的強度損失,從而使得焊縫強度相對于不可時效強化的5083以及5059合金有了較大程度的提升,并基本趨近于7039合金的焊縫強度水平;同時,本發(fā)明合金在所述焊接工藝下可焊性表現(xiàn)與5083以及5059合金持平,在焊接過程中不易產(chǎn)生焊接結(jié)晶、液化裂紋,焊縫具有較高可焊性和服役可靠性。當(dāng)前第1頁12