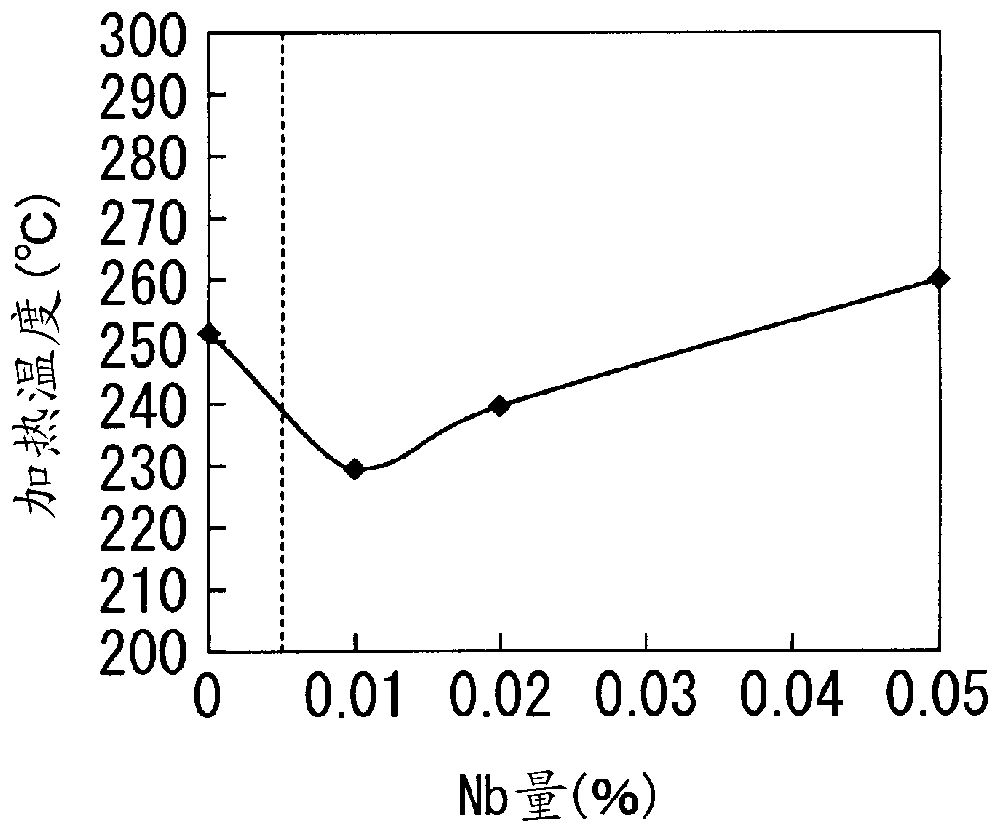
本發(fā)明涉及通過淬火回火處理被制造的作為各種機(jī)械零件的材料的高碳冷軋鋼板。特別地涉及如下高碳冷軋鋼板,前述高碳冷軋鋼板的板厚不足1.0mm,前述高碳冷軋鋼板在短時(shí)固溶處理淬火后,又在低溫回火處理后,兼?zhèn)涑浞值挠捕?600~750hv)和優(yōu)異的沖擊特性(韌性),能夠適當(dāng)?shù)貞?yīng)用于還對(duì)于耐久性、耐磨損性等要求苛刻的織針等。這里,短時(shí)固溶處理是指在760~820℃的溫度范圍內(nèi)在3~15分的時(shí)間內(nèi)進(jìn)行的處理,低溫回火處理是指200~350℃的溫度范圍下的處理。
背景技術(shù):
:一般地,jis所規(guī)定的機(jī)械結(jié)構(gòu)用碳素鋼(s××c)或碳素工具鋼(sk)被使用于各種大小的各種機(jī)械零件。在作為軋平材料被使用的情況下,在經(jīng)過沖裁加工、各種塑性加工成形為零件形狀后,進(jìn)行淬火?回火處理。由此,被賦予既定的硬度和韌性(沖擊特性)。特別是,例如,一種編織針織布料的織針,所述織針在以高速重復(fù)往復(fù)運(yùn)動(dòng)的同時(shí),將線拖拉來編織針織布料。因此,織針在與旋轉(zhuǎn)驅(qū)動(dòng)部接觸的針主體的針踵部需要充分的強(qiáng)度和耐磨損性,在末端部需要優(yōu)異的沖擊特性,在與線互相摩擦的鉤部還需要充分的耐磨損性。作為織針用材料被使用的高碳冷軋鋼板在板厚為1.0mm以上的情況下用作橫織機(jī)用織針,在其板厚不足1.0mm的情況下適合用作圓織機(jī)或縱織機(jī)用織針。對(duì)于圓織機(jī)或縱織機(jī)用織針,具有0.4~0.7mm的板厚的材料多被使用,因?yàn)檫@樣的織針將細(xì)徑的線高速編織??椺樣貌牧喜粌H需要具有優(yōu)異的冷加工性(以下也稱作二次加工性),而且需要在成形為針形狀(二次加工)并淬火回火后,具有充分的硬度和在針末端部處的充分的韌性。jis所規(guī)定的機(jī)械結(jié)構(gòu)用碳素鋼(s××c)或碳素工具鋼(sk)等所謂的高碳鋼根據(jù)含碳量,將用途較細(xì)地分類。在含碳量不足0.8質(zhì)量%的等級(jí)、即具有亞共析成分的鋼,鐵素體相的分?jǐn)?shù)較高,因此,冷加工性優(yōu)異,但難以得到充分的淬火硬度。因此,具有亞共析成分的鋼不適合需要鉤部的耐磨損性、針主體的耐久性的織針用途等。另一方面,0.8質(zhì)量%以上的等級(jí)、即在具有亞共析成分的鋼中,含碳量大于1.1質(zhì)量%的高碳鋼具有優(yōu)異的淬火性,但由于較多地含有碳化物(滲碳體),冷加工性極端地差。因此,該等級(jí)不適合進(jìn)行槽切加工等精密且細(xì)微的加工的織針用途等。含碳量比1.1質(zhì)量%大的高碳鋼被限定于刀具、冷作模具等具有簡(jiǎn)單形狀且需要高硬度的零件用途。以往以來,對(duì)于織針,含有c:0.8~1.1質(zhì)量%的碳素工具鋼或合金工具鋼或含有將這些鋼的成分作為基礎(chǔ)來向其添加第3元素的鋼的成分的材料被廣泛使用。在該織針的制造過程中,該材料被供于沖裁(剪切加工)、切削、拉絲、機(jī)械結(jié)合、彎曲等多種多樣的塑性加工。因此,該織針制造用的材料需要具備針的制造工序中的材料加工時(shí)具有充分的加工性(二次加工性),并且具備在作為針實(shí)際使用時(shí)所要求的淬火回火處理后的硬度特性、沖擊特性(韌性)。在織針的制造中,為了確保既定的硬度特性,對(duì)材料進(jìn)行淬火回火處理。在該回火處理中,一般采用在200~350℃的溫度范圍下的低溫回火處理。但是,當(dāng)增加對(duì)于淬火性有效的mn、cr的添加量時(shí),或較多地添加其他的第3元素時(shí),重視硬度特性,有馬氏體相的回火不充分,導(dǎo)致沖擊特性(韌性)的提高不充分或韌性值不均的情況。另一方面,以提高織針的沖擊特性為目的,減少材料的化學(xué)成分的作為雜質(zhì)元素的p、s,使p的晶界偏析、mns夾雜物的生成極小化,實(shí)現(xiàn)將這些元素的不利影響的減少也是有效的對(duì)策。但是,從制鋼技術(shù)上及成本經(jīng)濟(jì)性的觀點(diǎn)出發(fā),在通過減少p、s來實(shí)現(xiàn)織針的沖擊特性的提高的方面存在極限。作為使沖擊特性提高的手段,以往已知微觀組織的細(xì)微化是有效的。例如,在專利文獻(xiàn)1及2中,公開了添加ti、nb、v等碳氮化物形成元素來利用這些元素的細(xì)微碳氮化物使金屬組織細(xì)微化的技術(shù)。但是,這些元素一般作為含有0.8質(zhì)量%以下的含碳量的亞共析成分的鋼的韌性提高對(duì)策而被添加。特別地,在200~350℃的低溫回火條件下的馬氏體相的沖擊特性的各個(gè)第3元素的影響(特別是相互作用)未被充分弄清,假設(shè)各個(gè)元素的效果等價(jià)來進(jìn)行成分設(shè)計(jì)的情況較多。例如,在專利文獻(xiàn)1中所記載的技術(shù)將含有c:0.5~0.7質(zhì)量%的亞共析鋼作為對(duì)象,向其添加v、ti、nb等碳氮化物形成元素,來將舊奧氏體粒細(xì)微化,由此使韌性值(沖擊特性)提高。在專利文獻(xiàn)2中所記載的技術(shù)將含有c:0.60~1.30質(zhì)量%的亞共析鋼到過共析鋼的具有廣泛的碳含量的鋼作為對(duì)象,根據(jù)需要,向其添加ni:1.8質(zhì)量%以下、cr:2.0質(zhì)量%以下、v:0.5質(zhì)量%以下、mo:0.5質(zhì)量%以下、nb:0.3質(zhì)量%以下、ti:0.3質(zhì)量%以下、b:0.01質(zhì)量%以下、ca:0.01質(zhì)量%以下的一種或二種以上,將未溶解碳化物的體積分?jǐn)?shù)(vf)控制在(15.3×c質(zhì)量%-vf)超過8.5~不足10.0的范圍,由此使沖擊特性提高。專利文獻(xiàn)1:日本特開2009-24233號(hào)公報(bào)。專利文獻(xiàn)2:日本特開2006-63384號(hào)公報(bào)。然而,專利文獻(xiàn)1所記載的技術(shù)限于亞共析鋼,是期待通過添加v、ti、nb等碳氮化物形成元素,來借助這些細(xì)微碳氮化物將舊奧氏體粒細(xì)微化的效果的技術(shù)。由于碳濃度是亞共析成分,所以專利文獻(xiàn)1所記載的技術(shù)也是改善鐵素體母相的成形性的技術(shù)。因此,難以將該技術(shù)應(yīng)用于織針那樣的需要高硬度的機(jī)械零件。此外,在專利文獻(xiàn)2所記載的技術(shù)中,對(duì)于碳含量為0.67~0.81質(zhì)量%的范圍的亞共析鋼,添加mo、v、ti、nb、b等。該mo、v、ti、nb、b等的添加顯然為欲將亞共析鋼的特性改善的添加。專利文獻(xiàn)2沒有公開任何關(guān)于各個(gè)第3元素在具有超過0.81質(zhì)量%的含碳量的鋼中的作用及其最佳化。進(jìn)而,專利文獻(xiàn)2所記載的技術(shù)關(guān)于第3元素的添加量,僅規(guī)定了不會(huì)由于第3元素對(duì)沖擊值造成不利影響的上限值,未規(guī)定其下限值。由此,也可以說,專利文獻(xiàn)2未公開以下技術(shù):在預(yù)期的范圍內(nèi)添加第3元素,積極地希望添加元素的作用來增強(qiáng)沖擊特性。進(jìn)而,關(guān)于高碳冷軋鋼板,專利文獻(xiàn)1、專利文獻(xiàn)2也未公開以下技術(shù):在3~15分那樣的短時(shí)固溶處理保持時(shí)間進(jìn)行淬火,并且通過200~350℃的低溫回火后,將所希望的沖擊特性及既定硬度有利地改善,此外,關(guān)于板厚不足1.0mm的鋼板進(jìn)行評(píng)價(jià)沖擊特性的技術(shù)也未被公開。技術(shù)實(shí)現(xiàn)要素:因此,本發(fā)明的目的在于提供一種高碳冷軋鋼板(以下也簡(jiǎn)稱作“冷軋鋼板”),前述高碳冷軋鋼板在實(shí)施短時(shí)固溶處理后和淬火及低溫回火處理后,能夠顯示沖擊值為5j/cm2以上、且硬度為600~750hv的范圍的機(jī)械特性,前述高碳冷軋鋼板的板厚不足1.0mm。本發(fā)明人們?yōu)榱私鉀Q上述問題,對(duì)于高碳冷軋鋼板的化學(xué)成分的適當(dāng)?shù)奶砑臃秶弯撝械奶蓟锏牧胶痛嬖诜绞竭M(jìn)行了廣泛研究。從加工性、淬火性、低溫回火后的硬度和韌性等觀點(diǎn)來看,本發(fā)明將含碳量限于適合織針的c:0.85質(zhì)量%以上1.10質(zhì)量%以下,本發(fā)明的核心是發(fā)現(xiàn)以下內(nèi)容:為了顯示目標(biāo)特性,在該含碳量的范圍作為第3元素在既定的范圍添加nb,并且控制碳化物的平均粒徑和球化的程度較為有效。特別地,本發(fā)明人們開發(fā)了,將以往韌性評(píng)價(jià)較難的板厚不足1.0mm的鋼板為對(duì)象的、用于韌性評(píng)價(jià)的新的試驗(yàn)法(新沖擊試驗(yàn)法)。將新的試驗(yàn)法(新沖擊試驗(yàn)法)在圖1及圖2中表示。利用該新沖擊試驗(yàn)法,對(duì)于添加了各種第3元素的板厚不足1.0mm的高碳冷軋鋼板,調(diào)查淬火和低溫回火狀態(tài)的沖擊值。結(jié)果,發(fā)現(xiàn)以下新的內(nèi)容:只有既定量的nb的添加是滿足上述目標(biāo)的特性的。本發(fā)明是基于這樣的知識(shí)而作出的。即,本發(fā)明人們?yōu)榱私鉀Q上述課題而進(jìn)行銳意研究,發(fā)現(xiàn)以下內(nèi)容:對(duì)于將基本成分規(guī)定為c:0.85~1.10質(zhì)量%,mn:0.50~1.0質(zhì)量%,si:0.10~0.35質(zhì)量%,p:0.030質(zhì)量%以下,s:0.030質(zhì)量%以下,cr:0.35~0.45質(zhì)量%的范圍的高碳鋼必須添加0.005~0.020質(zhì)量%的nb,將碳化物的球化和平均粒徑控制在既定的范圍,由此能夠得到兼具優(yōu)異淬火性和優(yōu)異韌性的高碳冷軋鋼板,還發(fā)現(xiàn)這也能夠?qū)崿F(xiàn)淬火處理時(shí)間的短縮或回火溫度的下降。此外,通過采用適當(dāng)?shù)脑u(píng)價(jià)薄板的沖擊特性的試驗(yàn)方法,能夠規(guī)定適當(dāng)?shù)幕瘜W(xué)成分及碳化物的球化率、平均粒徑。首先,對(duì)本發(fā)明人們進(jìn)行的實(shí)驗(yàn)結(jié)果進(jìn)行說明。一種冷軋鋼板(小于1mm厚)以如下方式被制造:對(duì)于熱軋鋼板(4mm厚),分別重復(fù)冷軋(輥制壓下率:25~65%,最終為3~50%)和軟化退火及球化退火(640~700℃)5次,前述熱軋鋼板具有的成分以質(zhì)量%計(jì)含有1.01%c-0.26%si-0.73%mn-0.42%cr-0.02%mo,進(jìn)而將nb的量變化為0%、0.010%、0.020%、0.055%來添加,剩余部分為fe及不可避的雜質(zhì)。對(duì)于所得到的冷軋鋼板,實(shí)施以780℃、800℃的兩個(gè)級(jí)別的加熱溫度、使保持時(shí)間在0~16分的范圍內(nèi)變化的固溶處理后,進(jìn)行油淬火,然后測(cè)定維氏硬度(hv)。將所得到的結(jié)果以固溶處理的加熱保持時(shí)間(分)和淬火硬度(hv)的關(guān)系表示在圖3(加熱溫度:800℃)、圖4(加熱溫度:780℃)。根據(jù)圖3、圖4可知,nb含量為0.010質(zhì)量%的冷軋鋼板以最短的加熱保持時(shí)間,能夠確保超過700hv的淬火硬度。當(dāng)nb含量超過0.010質(zhì)量%時(shí),短時(shí)間加熱保持的硬度上升減慢。根據(jù)圖4的結(jié)果,在固溶處理的加熱溫度為780℃的情況下,求出淬火硬度到達(dá)700hv的加熱保持時(shí)間,將與nb含量的關(guān)系在圖5中表示。圖5示出當(dāng)nb含量為0.020質(zhì)量%以上時(shí),淬火硬度到達(dá)700hv的固溶處理的加熱保持時(shí)間大致恒定。當(dāng)nb含量為0.005~0.015質(zhì)量%的范圍時(shí),為了確保所希望的淬火硬度(700hv)的固溶處理的加熱保持時(shí)間變?yōu)樽疃蹋瑫r(shí)能夠確保穩(wěn)定的淬火性。進(jìn)而,以該范圍的nb含量,能夠縮短固溶處理的加熱保持時(shí)間。根據(jù)以上事實(shí),發(fā)現(xiàn)使nb含量變?yōu)?.005~0.015質(zhì)量%的范圍,是能夠有效防止針加工制造商中的如下問題的對(duì)策,前述問題為,淬火引起的膨脹不均和淬火引起的彎曲。與此同時(shí),對(duì)于具有各種nb含量的冷軋鋼板,實(shí)施加熱溫度:800℃、加熱保持時(shí)間:10分的固溶處理,進(jìn)行油淬火,進(jìn)而實(shí)施回火處理。在回火處理中,回火溫度設(shè)為150℃、200℃、250℃、300℃、350℃的各種溫度,將保持時(shí)間設(shè)為1小時(shí)?;鼗鹛幚砗笳{(diào)查沖擊特性。另外,沖擊特性使用圖1、圖2所示的新試驗(yàn)法來進(jìn)行。將所得到的結(jié)果表示在圖6中。沖擊值在回火溫度為200℃以上的情況下,nb含量為0.010質(zhì)量%的情況最高。根據(jù)圖6,求出得到?jīng)_擊值:5j/cm2的回火溫度,將與nb含量的關(guān)系在圖7中表示。圖7示出得到?jīng)_擊值:5j/cm2的回火溫度在nb含量:0.010質(zhì)量%的鋼板的情況為最低。當(dāng)nb含量超過0.020質(zhì)量%地增加時(shí),得到?jīng)_擊值:5j/cm2的回火溫度為高溫側(cè)。在回火溫度為高溫時(shí),硬度低下,作為針的耐久性下降。此外,發(fā)現(xiàn)nb含量不足0.005質(zhì)量%的情況下,為了確保所希望的沖擊值,需要使回火溫度為高溫。圖5、圖7示出,為了兼具回火后的高硬度和優(yōu)異沖擊特性,nb含量的下限為0.005質(zhì)量%,上限為0.020質(zhì)量%。進(jìn)而,為了使固溶處理的加熱保持時(shí)間為短時(shí)間,優(yōu)選地使nb含量的上限被設(shè)為0.015質(zhì)量%。本發(fā)明是基于該見解進(jìn)一步加以研究而完成的。即,本發(fā)明的要旨如下所述。[1]一種高碳冷軋鋼板,其特征在于,鋼板的化學(xué)成分含有,c:0.85~1.10質(zhì)量%,mn:0.50~1.0質(zhì)量%,si:0.10~0.35質(zhì)量%,p:0.030質(zhì)量%以下,s:0.030質(zhì)量%以下,cr:0.35~0.45質(zhì)量%,nb:0.005~0.020質(zhì)量%,剩余部分為fe及不可避雜質(zhì),分散于前述鋼板中的碳化物的平均粒徑dav和球化率(nsc/ntc)×100%分別滿足下述(1)式及(2)式,前述鋼板的板厚不足1.0mm,0.2≤dav≤0.7(μm)(1);(nsc/ntc)×100≥90%(2);其中,(1)式的平均粒徑dav為各個(gè)圓的直徑的平均值,此時(shí),假設(shè)前述圓具有與在鋼板截面被觀察的各個(gè)碳化物相等的面積,前述圓的直徑即為圓等效直徑,而且,(2)式的ntc及nsc分別為,ntc:每100μm2觀察面積的碳化物的總個(gè)數(shù),nsc:滿足dl/ds為1.4以下的條件的碳化物個(gè)數(shù),將碳化物的長(zhǎng)軸設(shè)為dl,短軸設(shè)為ds。[2]一種前述[1]所述的高碳冷軋鋼板,其特征在于,前述化學(xué)成分還含有從mo及v內(nèi)選擇的1種或2種,各自的含量均為0.001質(zhì)量%以上且不足0.05質(zhì)量%。[3]一種高碳冷軋鋼板的制造方法,其特征在于,對(duì)由[1]或[2]所述的化學(xué)成分組成的熱軋鋼板重復(fù)進(jìn)行冷軋及球化退火來制造高碳冷軋鋼板的方法中,分散于前述高碳冷軋鋼板中的碳化物的平均粒徑dav、球化率nsc/ntc分別滿足下述(1)式及(2)式,前述高碳冷軋鋼板的板厚不足1.0mm,0.2≤dav≤0.7(μm)(1);(nsc/ntc)×100≥90%(2);其中,(1)式的平均粒徑dav為各個(gè)圓的直徑的平均值,此時(shí),假設(shè)前述圓具有與在鋼板截面被觀察的各個(gè)碳化物相等的面積,前述圓的直徑即為圓等效直徑,此外,(2)式的ntc及nsc分別為,ntc:每100μm2觀察面積的碳化物的總個(gè)數(shù);nsc:滿足dl/ds為1.4以下的條件的碳化物個(gè)數(shù),將碳化物的長(zhǎng)軸設(shè)為dl,短軸設(shè)為ds。[4]前述[3]所述的高碳冷軋鋼板的制造方法,其特征在于,對(duì)前述熱軋鋼板重復(fù)進(jìn)行冷軋及球化退火的次數(shù)設(shè)為2~5次。[5]前述[3]或[4]所述的高碳冷軋鋼板的制造方法,其特征在于,前述冷軋的輥制壓下率為25~65%,前述球化退火的溫度為640~720℃。本發(fā)明的高碳冷軋鋼板是以下鋼板:板厚不足1.0mm、特別地板厚薄至0.4~0.7mm的薄的高碳冷軋鋼板,將碳化物的平均粒徑的大小控制為0.2~0.7μm的大小,同時(shí)將球化率控制為90%以上。若對(duì)于該鋼板,實(shí)施淬火、回火的熱處理,即使通過3~15分這樣短時(shí)間的固溶處理,也能夠通過淬火、低溫回火的熱處理得到良好的沖擊特性(沖擊值:5j/cm2以上)及硬度特性(600~750hv)。進(jìn)而,本發(fā)明的高碳冷軋鋼板在短時(shí)固溶處理后,淬火,成為包括不可避免地殘留γ相的馬氏體相后,在進(jìn)行200~350℃的所謂的低溫回火的條件下,對(duì)于以往的高碳冷軋鋼板,在硬度和沖擊特性(韌性)的平衡的方面發(fā)揮明確的優(yōu)越性。即,使用本發(fā)明的高碳冷軋鋼板,能夠確保優(yōu)異淬火性,并且能夠得到淬火回火后的韌性優(yōu)異的高碳鋼制機(jī)械工具零件。特別地,在本發(fā)明中被公開的冷軋鋼板適合如下用途:前述用途不僅需要硬度和韌性的平衡,還需要耐磨損性和耐疲勞特性,例如織針那樣的苛刻的使用環(huán)境下需要優(yōu)異的耐久性。附圖說明圖1是表示用于本發(fā)明的評(píng)價(jià)的沖擊試驗(yàn)的試驗(yàn)裝置的例子的說明圖。圖2是表示用于本發(fā)明的評(píng)價(jià)的沖擊試驗(yàn)的試驗(yàn)片的形狀的說明圖。圖3是表示淬火硬度和固溶處理的加熱保持時(shí)間的關(guān)系的圖表(加熱溫度:800℃)。圖4是表示淬火硬度和固溶處理的加熱保持時(shí)間的關(guān)系的圖表(加熱溫度:780℃)。圖5是表示能夠得到淬火硬度700hv的固溶處理的加熱保持時(shí)間和nb含量的關(guān)系的圖表。圖6是表示沖擊值和回火溫度的關(guān)系的圖表。圖7是表示能夠得到?jīng)_擊值:5j/cm2的回火溫度和nb含量的關(guān)系的圖表。具體實(shí)施方式以下,對(duì)本發(fā)明的實(shí)施方式進(jìn)行說明。首先,本發(fā)明的鋼板是,將熱軋鋼板根據(jù)需要進(jìn)行軟化退火,交替重復(fù)冷軋和球化退火,作為高碳冷軋鋼板得到的板厚不足1.0mm的鋼板。之后,對(duì)該高碳冷軋鋼板進(jìn)行既定的二次加工及固溶處理,然后實(shí)施淬火和回火處理,作為織針等部件(機(jī)械零件)被使用。首先,對(duì)將本發(fā)明的鋼板的化學(xué)成分規(guī)定為c:0.85~1.10質(zhì)量%、mn:0.50~1.0質(zhì)量%、si:0.10~0.35質(zhì)量%、p:0.030質(zhì)量%以下、s:0.030質(zhì)量%以下、cr:0.35~0.45質(zhì)量%、nb:0.005~0.020質(zhì)量%的理由在以下進(jìn)行說明。c:0.85~1.10質(zhì)量%c是高碳冷軋鋼板的熱處理后為了得到充分的硬度的必需元素。決定其下限值,使得能夠確保織針等那樣的精密零件中的600~750hv的硬度,此外決定其上限值,使得能夠?qū)⑻蓟锪靠刂圃诓环恋K多種多樣的冷加工的濃度。即,下限值為了在短時(shí)間的淬火回火處理中穩(wěn)定地確保600hv的硬度而規(guī)定為0.85質(zhì)量%。上限值作為能夠承受沖裁性、模鍛性(swagingproperty)、彎曲性、切削性等多方面的塑性加工的上限而規(guī)定為1.10質(zhì)量%。若通過重復(fù)冷軋和球化退火來進(jìn)行碳化物的球化處理,則冷加工性被改善。但是,若c超過1.10質(zhì)量%,則也出現(xiàn)熱軋工序或冷軋工序中的軋制負(fù)荷變高,或線圈端部的破損的發(fā)生頻率顯著變高等制造工序上的問題。因此,c規(guī)定為0.85~1.10質(zhì)量%的范圍。另外,該范圍優(yōu)選為0.95~1.05質(zhì)量%。mn:0.50~1.0質(zhì)量%mn是對(duì)于鋼的脫氧有效的元素,并且同時(shí)是通過使鋼的淬火性提高來能夠穩(wěn)定地得到既定的硬度的元素。在以被應(yīng)用于苛刻的用途的高碳鋼板為對(duì)象的情況下,mn在0.50質(zhì)量%以上本發(fā)明的效果顯著。因此,下限值規(guī)定為0.50質(zhì)量%。另一方面,若mn超過1.0質(zhì)量%,則熱軋時(shí)mns大量析出而粗大化,所以零件加工時(shí)破損等多有發(fā)生。因此,上限值規(guī)定為1.0質(zhì)量%。由此,mn規(guī)定為0.50~1.0質(zhì)量%的范圍。另外,該范圍優(yōu)選為0.50~0.80質(zhì)量%。si:0.10~0.35質(zhì)量%si是鋼的脫氧元素,所以在熔煉清浄鋼上是有效的元素。si也是提供馬氏體的抗回火軟化性的有效的元素。由此,下限值規(guī)定為0.10質(zhì)量%。若大量添加,則低溫回火下的馬氏體的回火不充分,使沖擊特性劣化,所以其上限值規(guī)定為0.35質(zhì)量%。因此,si規(guī)定為0.10~0.35質(zhì)量%的范圍。p:0.030質(zhì)量%以下,s:0.030質(zhì)量%以下p、s作為雜質(zhì)元素不可避免地存在于鋼中,均對(duì)沖擊特性(韌性)造成不利影響,所以優(yōu)選地盡量減少。p為0.030質(zhì)量%以下、s為0.030質(zhì)量%以下的含有量在實(shí)際使用上都是沒有問題的。由此,p規(guī)定的含量為0.030質(zhì)量%以下,s的含量規(guī)定為0.030質(zhì)量%以下。另外,為了維持更優(yōu)異的沖擊特性,優(yōu)選地,設(shè)為p的含量為0.020質(zhì)量%以下、s的含量為0.010質(zhì)量%以下的含有量。cr:0.35~0.45質(zhì)量%cr是使鋼的淬火性提高的元素。但cr固溶于碳化物(滲碳體)中會(huì)引起在加熱階段的碳化物的再溶解延遲,而因此大量地添加cr,則cr相反地阻礙淬火性。因此,將cr的上限值規(guī)定為0.45質(zhì)量%??紤]淬火回火后的硬度和沖擊特性的平衡,cr的下限值規(guī)定為0.35質(zhì)量%。由此,cr規(guī)定為0.35~0.45質(zhì)量%的范圍。nb:0.005~0.020質(zhì)量%nb以往作為在熱軋時(shí)擴(kuò)大鋼的未再結(jié)晶溫度區(qū)的元素,同時(shí)作為以nbc析出而有助于奧氏體粒的細(xì)微化的元素而被公知。因此,也有期待冷軋工序以后的組織的細(xì)微化效果對(duì)高碳鋼添加nb的情況。在本發(fā)明中,將淬火后的低溫下的回火的韌性恢復(fù)為主目的,將nb以0.005~0.020質(zhì)量%添加。若是微量的nb添加,則nb呈稀?。ㄏ1。┕倘軤顟B(tài),不形成充分的nbc來有助于組織的細(xì)微化。nb呈稀薄固溶狀態(tài),由此被認(rèn)為具有bcc結(jié)構(gòu)的鐵素體相和馬氏體相中的c的擴(kuò)散被促進(jìn)。即,淬火處理的加熱時(shí)從球狀碳化物溶向鐵素體相的c向奧氏體相的擴(kuò)散、及、回火處理的加熱時(shí)馬氏體相中的過飽和固溶c的擴(kuò)散和析出被促進(jìn)。結(jié)果,在現(xiàn)在的時(shí)間考慮能夠使短時(shí)間加熱下的淬火性的提高和低溫回火處理的韌性的恢復(fù)的并存。若nb被超過0.020質(zhì)量%地添加,則nbc的析出變得顯著,不能確保nb的稀薄固溶狀態(tài),相應(yīng)地不能確認(rèn)由nb的稀薄固溶狀態(tài)引起的c的擴(kuò)散的促進(jìn)效果。因此,nb添加量的上限規(guī)定為0.020質(zhì)量%。另外,優(yōu)選為0.015質(zhì)量%以下。另一方面,nb添加量不足0.005質(zhì)量%的話,無法期待上述效果。因此,nb添加量的下限規(guī)定為0.005質(zhì)量%。由此,nb規(guī)定為0.005~0.020質(zhì)量%的范圍。上述的成分是基本的成分,在本發(fā)明中作為任意的選擇元素,根據(jù)需要,還能夠含有從mo及v中選擇的1種或2種。mo及v會(huì)被不可避地分別含有以下的量:mo:不足0.001質(zhì)量%、v:不足0.001質(zhì)量%。在本發(fā)明中,為了使淬火性或回火后的沖擊特性提高,可以將mo和v比不可避免地含有的濃度多地添加。但是,若將mo、v在既定量以上地添加,則nb的添加效果喪失。所以為了將nb的添加效果最大限度地發(fā)揮,在添加的情況下,優(yōu)選地將mo和v的含量控制為以下的范圍。mo:0.001質(zhì)量%以上且不足0.05質(zhì)量%mo是對(duì)于鋼的淬火性提高有效的元素。但添加量較多時(shí),在200~350℃的低溫回火下,有時(shí)使沖擊特性惡化。因此,在添加mo的情況下,其添加量被規(guī)定為比不可避地含有的濃度多的0.001質(zhì)量%以上、不妨礙沖擊特性的范圍的不足0.05質(zhì)量%。優(yōu)選地,mo的添加為0.01~0.03質(zhì)量%。v:0.001質(zhì)量%以上且不足0.05質(zhì)量%v是在通過將鋼組織細(xì)微化來有效地提高沖擊特性的元素,但是是有時(shí)使淬火性惡化的元素。因此,在添加v的情況下,其添加量被規(guī)定為比不可避地含有的濃度多的0.001質(zhì)量%以上、不妨礙淬火性的范圍的不足0.05質(zhì)量%。優(yōu)選地,v的添加是0.01~0.03質(zhì)量%。上述的成分以外的剩余部分是fe及不可避的雜質(zhì)。接著,對(duì)本發(fā)明的鋼板的碳化物進(jìn)行說明。在本發(fā)明的高碳冷軋鋼板中,分散于鋼板中的碳化物的平均粒徑(dav)和球化率(nsc/ntc)需要分別滿足下述(1)式及(2)式。0.2≤dav≤0.7(μm)…(1)(nsc/ntc)×100≥90%…(2)這里,(1)式的平均粒徑(dav)(μm)為,設(shè)想具有與在鋼板截面觀察的各個(gè)碳化物相等的面積的圓時(shí),各個(gè)圓的直徑(圓等效直徑)的平均值。平均粒徑(dav)處于該范圍會(huì)使得沖擊特性優(yōu)異,而且有即使通過短時(shí)固溶處理也容易地實(shí)現(xiàn)所希望的淬火硬度的效果。在經(jīng)驗(yàn)上,平均粒徑(dav)不足0.2μm會(huì)使加工成針形狀的二次加工時(shí)的負(fù)荷增大。平均粒徑(dav)超過0.7μm則不被優(yōu)選,這是因?yàn)檫@使得通過短時(shí)固溶處理難以實(shí)現(xiàn)所希望的淬火性提高。本發(fā)明中還將碳化物球化的比例即球化率用(2)式的ntc及nsc定義。這里,ntc是每100μm2觀察面積的碳化物的總個(gè)數(shù)。此外,nsc是在同一觀察視野中視為球化的碳化物的個(gè)數(shù),設(shè)為滿足dl/ds為1.4以下的條件的碳化物個(gè)數(shù)。這里,將碳化物的長(zhǎng)軸設(shè)為dl,短軸設(shè)為ds。碳化物不能稱為被形成為完全的球狀,但根據(jù)觀察面而被觀察為橢圓形的情況較多。所以根據(jù)長(zhǎng)軸和短軸的比(dl/ds),規(guī)定球化的程度。根據(jù)該情況,本發(fā)明將滿足dl/ds為1.4以下的條件的碳化物視為球化,定義其個(gè)數(shù)即nsc。此外,球化率(nsc/ntc)×100為90%以上是因?yàn)榘l(fā)現(xiàn),球化率在該范圍的話會(huì)提高鋼板的二次加工性的經(jīng)驗(yàn)上的見解。以上說明的碳化物的平均粒徑及球化率的測(cè)定使用掃描型電子顯微鏡,通過將二次電子顯微鏡圖像以2千倍的倍率觀察來進(jìn)行。通過使用冷軋后的鋼板,以與熱處理前的樣品的壓延方向成直角方向切下板狀試驗(yàn)片。進(jìn)行樹脂埋入等處理,并且在板厚中央部附近的100μm2觀察面積的范圍內(nèi),對(duì)碳化物進(jìn)行測(cè)定,來測(cè)定圓等效直徑、dl/ds比、ntc、nsc,并且計(jì)算5個(gè)視野的平均值。對(duì)于這些測(cè)定及計(jì)算,使用市售的畫像解析軟件“winroof”(商品名)。接著,對(duì)本發(fā)明的鋼板的制造方法進(jìn)行說明。本發(fā)明使用的熱軋鋼板可以是通常的制造條件下所得到的。例如,在本發(fā)明中被使用的熱軋鋼板能夠如下地被制造:將具有前述的化學(xué)成分的鋼片(slabs)加熱至1050~1250℃,在800~950℃的終軋溫度下對(duì)已加熱的鋼片進(jìn)行熱軋,在600~750℃的卷繞溫度下卷繞該產(chǎn)物。在這一點(diǎn)上,熱軋鋼板的板厚可以適當(dāng)設(shè)定,來獲得基于所希望的冷軋鋼板的板厚的優(yōu)選的冷軋壓下率。重復(fù)冷軋(25~65%)和球化退火(640~720℃)兩次以上,由此制造板厚不足1.0mm的高碳冷軋鋼板。該冷軋(25~65%)和球化退火(640~720℃)分別優(yōu)選地進(jìn)行2~5次。在本發(fā)明中,重復(fù)冷軋(25~65%)和球化退火(640~720℃)兩次以上。其理由是,如下所述,控制碳化物的平均粒徑(dav)和球化率(nsc/ntc)×100來分別滿足上述的(1)式及(2)式。首先,通過冷軋,破損被導(dǎo)入至碳化物,而且通過球化退火,開始?jí)核榈奶蓟锴蚧?。但是,僅通過一次的球化退火,難以將碳化物的球化率提高至90%以上,會(huì)殘留棒狀或板狀的碳化物。那樣的情況下,也會(huì)對(duì)淬火性有不利影響,使形成精密零件的冷加工性惡化。因此,為了使碳化物的球化率(nsc/ntc)×100為90%以上,最適合的是交替重復(fù)冷軋和球化退火。結(jié)果,得到鋼板中細(xì)微且球化率高的碳化物的分布。特別地,優(yōu)選為2~5次的冷軋和2~5次的球化退火。若對(duì)冷軋的輥制壓下率不足25%的鋼板(冷軋鋼板)進(jìn)行球化退火,則碳化物會(huì)粗大化。另一方面,在冷軋的輥制壓下率超過65%的情況下,有時(shí)冷軋操作的負(fù)荷過大。因此,冷軋的輥制壓下率優(yōu)選為25~65%的范圍。另外,在最終的冷軋中,冷軋后不進(jìn)行球化退火,所以輥制壓下率的下限不被特別地限定。若球化退火溫度比640℃低,則球化容易不充分,若以比720℃高的溫度重復(fù)球化退火,則碳化物容易粗大化。因此,球化退火溫度優(yōu)選為640~720℃的范圍。球化退火的保持時(shí)間可以以該范圍的溫度在9~30小時(shí)的范圍內(nèi)適當(dāng)選擇來進(jìn)行。在這一點(diǎn)上,關(guān)于以冷軋前的熱軋鋼板的軟化為目的的軟化退火,也優(yōu)選同樣的溫度范圍。以上是本發(fā)明的高碳冷軋鋼板的制造方法。為了制成作為該鋼板的最終的目的的織針那樣的機(jī)械零件,在該鋼板加工成既定的形狀之后,優(yōu)選進(jìn)行以下的熱處理。將分布有90%以上球化的碳化物的高碳冷軋鋼板加工成各種機(jī)械零件后(沖壓加工、槽切加工、擠鍛加工等),然后進(jìn)行固溶處理,急冷(淬火),并且實(shí)施回火處理。在固溶處理將中,加熱溫度設(shè)為760~820℃,并且將加熱保持時(shí)間設(shè)為較短時(shí)間的3~15分。淬火(急冷)優(yōu)選地使用油。在回火處理中,優(yōu)選地將回火溫度設(shè)為200~350℃?;鼗饻囟雀鼉?yōu)選為250~300℃。由此,能夠制造具有硬度600~750hv的各種機(jī)械零件。若固溶處理的加熱保持時(shí)間比15分長(zhǎng),則碳化物過度溶入,奧氏體粒粗大化,由此淬火后的馬氏體相變粗,這使得沖擊特性劣化。因此,固溶處理的加熱保持時(shí)間的上限優(yōu)選為15分。另一方面,若加熱保持時(shí)間比3分短,則碳化物的溶入不充分,這使得淬火變得困難。所以固溶處理的加熱保持時(shí)間的下限優(yōu)選為3分。更優(yōu)選為5~10分的范圍。在回火溫度不足200℃的情況下,馬氏體相的韌性恢復(fù)不充分。另一方面,若回火溫度超過350℃,則雖然沖擊值恢復(fù),但硬度低于600hv,所以耐久性、耐磨損性成為問題。由此,回火溫度的適當(dāng)范圍優(yōu)選為200~350℃。另外,更優(yōu)選為250~300℃?;鼗鸬谋3謺r(shí)間能夠在30分~3小時(shí)的范圍適當(dāng)選擇來進(jìn)行。實(shí)施例將具有各種各樣的化學(xué)成分的鋼真空溶解并鑄入30kg的鋼塊。將該鋼塊切片(slab),然后以1150℃的加熱溫度、870℃的終軋溫度的條件進(jìn)行熱軋,來生產(chǎn)4mm及2mm的熱軋鋼板。之后,以表1所示的制造條件進(jìn)行冷軋及球化退火,形成板厚為0.4mm以上且不足1.0mm的冷軋鋼板。接著,對(duì)該冷軋鋼板,以表2所示的條件,進(jìn)行固溶處理(被裝入800℃的爐中10分),然后進(jìn)行油淬火,并進(jìn)行回火(回火溫度:250℃)。從回火處理后的鋼板抽取既定的試驗(yàn)片,其之后被供于沖擊試驗(yàn)及硬度測(cè)定試驗(yàn)。硬度測(cè)定根據(jù)jisz2244的規(guī)定,以維氏硬度計(jì)測(cè)得的在負(fù)荷5kg重(試驗(yàn)力:49.0n)的條件下進(jìn)行。沖擊特性通過沙爾皮沖擊試驗(yàn)來評(píng)價(jià)。沖擊試驗(yàn)片設(shè)為刻痕寬度為0.2mm的u刻痕試驗(yàn)片(刻痕深度2.5mm、刻痕半徑0.1mm)。圖1表示在試驗(yàn)裝置上設(shè)置有試驗(yàn)片的狀態(tài),圖2表示試驗(yàn)片的形狀。之所以采用這樣的試驗(yàn)片及試驗(yàn)方法,是由于以下的理由。存在如下問題,在以往被使用的金屬材料用沙爾皮沖擊試驗(yàn)裝置中,試驗(yàn)裝置的額定容量為50j以上,對(duì)于本發(fā)明作為對(duì)象的板厚不足1.0mm的鋼板過大,結(jié)果不能進(jìn)行準(zhǔn)確的評(píng)價(jià)。作為試驗(yàn)裝置的額定容量比50j小的沖擊試驗(yàn)裝置,使用1j的沖擊試驗(yàn)裝置((株)東洋精機(jī)制作所制,型號(hào)為dg-gb)。該試驗(yàn)裝置是基于炭素纖維強(qiáng)化塑料的沙爾皮沖擊試驗(yàn)方法(jisk7077)的沙爾皮沖擊試驗(yàn)機(jī)。將該試驗(yàn)裝置在將支承臺(tái)間距離被從60mm改為40mm的條件下使用。在本試驗(yàn)裝置中,將支承臺(tái)間距離從60mm改為40mm,是為了得到與對(duì)于金屬材料的沙爾皮沖擊試驗(yàn)方法的jis規(guī)格(jisz2242)接近的條件。使用將u刻痕通過放電加工來形成的試驗(yàn)片,來得到刻痕深度為2.5mm、刻痕半徑為0.1mm(刻痕寬度為0.2mm)的試驗(yàn)片,如圖2所示。沙爾皮沖擊試驗(yàn)時(shí)不足1.0mm的薄板的情況下板的撓曲成為問題。因此,將刻痕半徑變小,來通過使應(yīng)力集中系數(shù)變高,使沙爾皮沖擊試驗(yàn)時(shí)的板的撓曲成為最小限度,能夠得到穩(wěn)定的沖擊值。通過采用該試驗(yàn)方法及試驗(yàn)片形狀,確認(rèn)能夠得到與實(shí)際使用環(huán)境接近的狀態(tài)的沖擊特性。在本發(fā)明中,判斷成沖擊值的數(shù)值為5j/cm2以上的情況下沖擊特性優(yōu)異。表1條件no.冷軋鋼板的制造條件(輥制壓下率、退火溫度)1熱軋(2mm)→冷軋(20-65%)→球化退火(700℃)→冷軋(3-50%)2a熱軋(2mm)→冷軋(10-20%)→球化退火(600-635℃)→冷軋(10-20%)→球化退火(600-635℃)→冷軋(3-50%)2b熱軋(2mm)→冷軋(25-65%)→球化退火(640-720℃)→冷軋(25-65%)→球化退火(640-720℃)→冷軋(3-50%)2c熱軋(2mm)→冷軋(70-85%)→球化退火(600-635℃)→冷軋(70-85%)→球化退火(600-635℃)→冷軋(3-50%)2d熱軋(2mm)→冷軋(10-20%)→球化退火(640-720℃)→冷軋(10-20%)→球化退火(640-720℃)→冷軋(3-50%)5a熱軋(4mm)→軟化退火(700℃)→冷軋(25-65%)→球化退火(690℃)→冷軋(25-65%)→球化退火(680℃)→冷軋(25-65%)→球化退火(660℃)→冷軋(25-65%)→球化退火(640℃)→冷軋(3-50%)5b熱軋(4mm)→軟化退火(700℃)→冷軋(10-20%)→球化退火(690℃)→冷軋(10-20%)→球化退火(680℃)→冷軋(10-20%)→球化退火(660℃)→冷軋(10-20%)→球化退火(640℃)→冷軋(3-50%)表2(實(shí)施例1)固溶處理后進(jìn)行油淬火,確認(rèn)涉及截面硬度及沖擊值的各種添加元素的影響。將試驗(yàn)結(jié)果與化學(xué)成分一同表示在表3及表4中。冷軋鋼板的制造條件為兩者都用5a的條件(表1)。輥制壓下率控制在被記載于表1的范圍。截面硬度通過將在壓延直角方向上切出的試驗(yàn)片埋入于樹脂,將截面研磨后,在板厚中央部進(jìn)行測(cè)定。沖擊值使用在壓延平行方向上抽取的沖擊試驗(yàn)片來測(cè)定。將所得到的結(jié)果(硬度和沖擊值)在表3及表4表示。沖擊值比5j/cm2大且同時(shí)硬度滿足600~750hv的條件評(píng)價(jià)為◎,不滿足沖擊值及硬度的上述目標(biāo)值的某一個(gè)的情況評(píng)價(jià)為×。表3注1)其他元素;p:0.010-0.020質(zhì)量%,s:0.001-0.010質(zhì)量%注2)固溶處理溫度:800℃,加熱保持時(shí)間:10分,回火溫度:250℃注3)◎:優(yōu)秀,×:劣質(zhì)。表4注1)其他元素;p:0.010-0.020質(zhì)量%,s:0.001-0.010質(zhì)量%注2)固溶處理溫度:800℃,加熱保持時(shí)間:10分,回火溫度:250℃注3)◎:優(yōu)秀,×:劣質(zhì)。在表3所示的例子中,含碳量偏離下限值的例子(鋼種no.1)顯示了沖擊值及淬火回火硬度偏離目標(biāo)值。含碳量偏離上限值的例子(鋼種no.6)顯示了淬火回火硬度超過目標(biāo)值600~750hv,且沖擊值低于目標(biāo)值5j/cm2。不含nb的例子中,含碳量為0.85質(zhì)量%的例子(鋼種no.2、比較例)、含碳量為1.10質(zhì)量%的例子(鋼種no.4、比較例)顯示的沖擊值均低于目標(biāo)值5j/cm2,評(píng)價(jià)為×。與此相對(duì),相當(dāng)于發(fā)明例的化學(xué)成分的鋼板(鋼種no.3、5、7、8、9、10)顯示的淬火回火硬度在目標(biāo)范圍內(nèi),且顯示優(yōu)異的沖擊特性。在表4所示的例子中,具有相當(dāng)于發(fā)明例的化學(xué)成分的鋼板(鋼種no.15、16、17、19、21)顯示的淬火回火硬度都滿足目標(biāo)值600~750hv,且顯示優(yōu)異的沖擊特性。不添加nb的例子(鋼種no.11)、不添加nb而v添加量超過0.05質(zhì)量%的例子(鋼種no.12)、不添加nb而mo添加量超過0.05質(zhì)量%的例子(鋼種no.13)、nb+mo復(fù)合添加且nb添加量比0.005質(zhì)量%少的例子(鋼種no.14)、nb+mo復(fù)合添加且nb添加量超過0.020質(zhì)量%的例子(鋼種no.18)、nb+mo復(fù)合添加且mo添加量比0.05質(zhì)量%多的例子(鋼種no.20)、nb+mo+v復(fù)合添加且v添加量比0.05質(zhì)量%多的例子(鋼種no.22),顯示淬火回火硬度滿足目標(biāo)值600~750hv,但顯示不好的沖擊特性,或顯示沖擊特性滿足目標(biāo)值5j/cm2但顯示低淬火回火硬度,或顯示淬火回火硬度及沖擊特性都低于目標(biāo)值的下限。(實(shí)施例2)使用具有鋼種no.3(表3)的化學(xué)成分的熱軋鋼板,使表1所述的冷軋和球化處理的制造條件變化,在該條件下得到表5所示的板厚的冷軋鋼板。將所得到的冷軋鋼板的球化率、碳化物平均粒徑在表5中表示。進(jìn)而,對(duì)所得到的冷軋鋼板與實(shí)施例1同樣地,以表2所示的條件,在固溶處理后實(shí)施油淬火和低溫回火。將所得到的冷軋鋼板的固溶處理和淬火回火后的截面硬度及沖擊值與實(shí)施例1同樣地測(cè)定,在表5中表示。表5注1)表3中所述的鋼種no.3注2)固溶處理溫度:800℃,加熱保持時(shí)間:10分,回火溫度:250℃注3)◎:優(yōu)秀,×:劣質(zhì)。球化退火次數(shù)為1次的例子(制造條件no.1)的球化率不充分,且沖擊特性不好。球化退火次數(shù)為2次的情況,將球化退火溫度設(shè)為600~635℃,將輥制壓下率設(shè)為10~20%來組合分別進(jìn)行兩次球化退火和冷軋,球化不充分,沖擊特性不好(制造條件no.2a)。若將球化退火溫度設(shè)為600~635℃,將輥制壓下率設(shè)為70~85%來組合分別重復(fù)兩次球化退火和冷軋,則得到的沖擊特性充分,但碳化物的平均粒徑偏離下限,淬火回火處理后的硬度超過目標(biāo)值(制造條件no.2c)。若將球化退火溫度設(shè)為640~720℃,將輥制壓下率設(shè)為10~20%來組合分別重復(fù)2次球化退火和冷軋,則球化充分,但碳化物的平均粒徑超過目標(biāo)值的上限,沖擊特性不好(制造條件no.2d)。這是被認(rèn)為由于若碳化物過大,則淬火時(shí)馬氏體基底的未溶解碳化物變得相當(dāng)大,且容易變?yōu)槠茐臅r(shí)的起點(diǎn),未溶解的碳化物與馬氏體基底的界面的面積較大,沖擊特性不好。與此相對(duì),若通過將球化退火溫度設(shè)為640~720℃、將輥制壓下率設(shè)為25~65%的組合分別重復(fù)2次球化退火和冷軋,則球化率、碳化物粒徑、淬火回火后的硬度分別收斂于目標(biāo)值的范圍,且得到優(yōu)異的沖擊特性(制造條件no.2b)。若將球化退火次數(shù)設(shè)為4次時(shí),使第1次~第4次的冷軋的輥制壓下率都為25~65%,則球化率、碳化物粒徑收斂于目標(biāo)值的范圍,也得到優(yōu)異的沖擊特性(制造條件no.5a)。若使得與制造條件no.5a的球化退火溫度相同,使第1次~第4次的冷軋的輥制壓下率都為10~20%,則碳化物粒徑超過目標(biāo)值變?yōu)檫^大,得到不好的沖擊特性(制造條件no.5b)。(實(shí)施例3)使用具有鋼種no.16(表4)的化學(xué)成分的熱軋鋼板,使表1所述的制造條件變化,得到具有表6所示的板厚的冷軋鋼板。將所得到的冷軋鋼板的球化率、碳化物平均粒徑在表6中表示。進(jìn)而,與實(shí)施例1同樣地對(duì)所得到的冷軋鋼板以表2所示的條件,在固溶處理后實(shí)施油淬火和低溫回火。將所得到的冷軋鋼板的固溶處理后和后來的淬火回火后的截面硬度及沖擊值與實(shí)施例1相同地測(cè)定,在表6中表示。使用相當(dāng)于本發(fā)明的制造方法的制造條件no.2b、no.5a進(jìn)行冷軋、球化退火的鋼板滿足目標(biāo)球化率、目標(biāo)沖擊值。表6注1)表4中所述的鋼種no.16注2)固溶處理溫度:800℃,加熱保持時(shí)間:10分,回火溫度:250℃注3)◎:優(yōu)秀,×:劣質(zhì)。產(chǎn)業(yè)上的可利用性具有本發(fā)明范圍的化學(xué)成分的鋼板通過nb的添加,淬火性提高,且熱處理后的沖擊特性被改善,且因此適用于用作在苛刻的環(huán)境被使用的機(jī)械工具零件中的過共析鋼。含有c為0.85~1.10質(zhì)量%的過共析鋼板適合用于織針那樣的苛刻的使用環(huán)境下需要硬度和韌性平衡的用途。當(dāng)前第1頁12