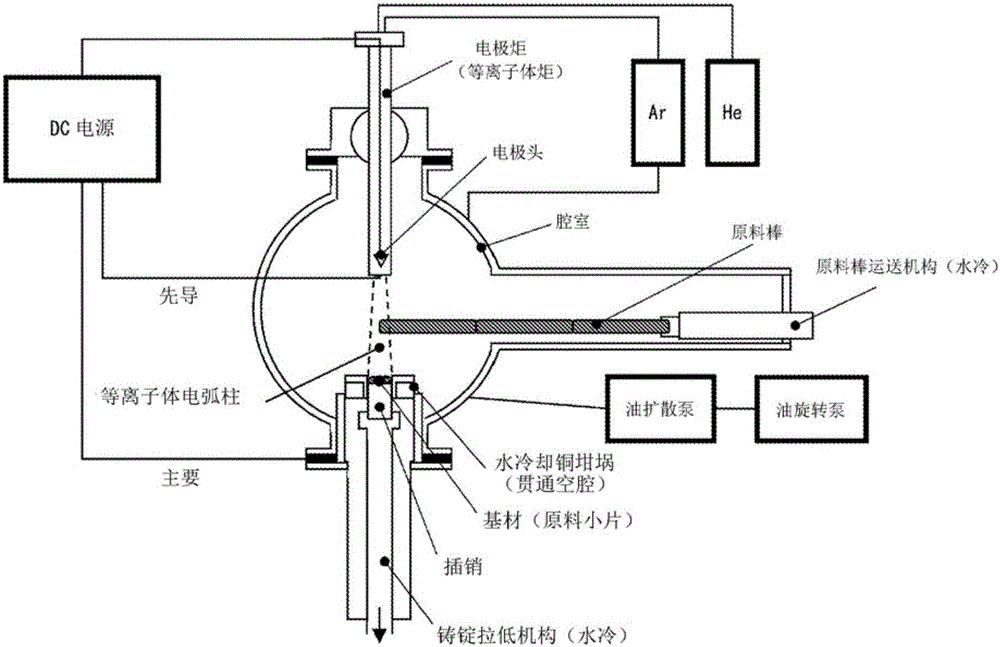
本發(fā)明涉及一種鉑族基合金的制造方法,具體涉及一種鉑族基合金的制造方法中的熔解錠制造。
背景技術(shù):
:鉑族基合金通過(guò)利用鉑族金屬所具備的耐熱性、耐氧化性、耐化學(xué)品性而設(shè)計(jì),廣泛用作高溫構(gòu)件和/或耐蝕制品。此處鉑族金屬是指Pt、Pd、Rh、Ir、Ru、Os的總稱。鉑族基合金的制造工序通常包含合金原料的配混工序、熔解工序、塑性加工工序等,其熔解方法分為幾個(gè)類型。主要成分的鉑族金屬的熔點(diǎn)非常高,因而使用了電感加熱熔解爐或能量束熔解爐。關(guān)于電感加熱熔解,最近也在進(jìn)行冷坩堝的嘗試,但是主流是使用了氧化物系耐火物坩堝的在真空或非活性氣體中的熔解法(例如專利文獻(xiàn)1)。關(guān)于能量束熔解,適用非消耗電極型電弧熔解、消耗電極型電弧熔解、真空等離子體熔解、電子束熔解等,主流是非消耗電極型電弧熔解(例如專利文獻(xiàn)2)。非消耗電極型電弧熔解是:在將放電端銳利地研磨了的W(鎢)電極與放置于舟形的水冷卻銅坩堝上的合金原料之間形成電弧柱,將該電弧柱設(shè)為熱源而將合金原料熔解的方法。消耗電極型電弧熔解是將原料自身設(shè)為電極,在電極的前端與水冷卻銅坩堝之間形成電弧柱的熔解方法;具有數(shù)百kg的熔解能力,因而應(yīng)用于Ti等非貴金屬的制造中,但是不會(huì)應(yīng)用于鉑族基合金的熔解中。關(guān)于真空等離子體熔解以及電子束熔解,由于在真空~高真空中熔解,因而具有精煉作用,另外,由于使用高能量密度的束因而適合大量熔解(例如專利文獻(xiàn)3)。關(guān)于電感加熱熔解,通常是將耐火物坩堝內(nèi)的合金原料熔解,將坩堝傾注向鑄模中進(jìn)行鑄造從而制造熔解錠。在耐火物坩堝的耐熱溫度方面存在局限,用于制造熔點(diǎn)比較低(大致2000℃以下)的鉑族基合金。該方法具有可在短時(shí)間制造數(shù)十kg的熔解錠的優(yōu)點(diǎn),但是耐火物坩堝與熔液不可避免地接觸,因而伴隨著卷入耐火物的風(fēng)險(xiǎn),有時(shí)會(huì)混入于熔解錠中。另外,在此方法中,也產(chǎn)生縮孔、氣孔、鑄件表面粗糙等鑄造缺陷,需要采取將該部分切斷、切削或磨削等去除加工,因而也存在有材料成品率低的問(wèn)題。關(guān)于非消耗電極型電弧熔解,熔解時(shí)間(電弧放電時(shí)間)較長(zhǎng)時(shí),則W電極的放電端緩慢地?fù)p耗,電弧柱發(fā)生切斷或者迷走從而無(wú)法繼續(xù)熔解,因而必須中斷熔解作業(yè)而將W電極的放電端進(jìn)行再研磨。另外,也與電弧柱的照射范圍比較小這一情況相互結(jié)合,因而無(wú)法實(shí)現(xiàn)連續(xù)鑄造。即,生產(chǎn)率低劣,可一次性地熔解的合金的量被制約為數(shù)kg左右。另外,在熔解中被減壓為不足0.8atm的情況是普通的,在將包含蒸氣壓差大的成分元素的合金進(jìn)行熔解時(shí),蒸氣壓高的成分元素更多地蒸發(fā),使得合金組成發(fā)生變動(dòng)。關(guān)于真空等離子體熔解和/或電子束熔解,通常具有連續(xù)鑄造相比于非消耗電極型電弧熔解而言大量的合金的能力,由于熔解氣氛是真空,因而可蒸發(fā)去除雜質(zhì)(精煉效果),因此適合于純金屬的熔解,但是在熔解合金時(shí),蒸氣壓高的成分元素更多地蒸發(fā),使得合金組成發(fā)生變動(dòng)。這樣地,以往廣泛地使用的熔解方法在成品率良好地制造沒(méi)有組成變動(dòng)的大量的鉑族基合金方面存在局限?,F(xiàn)有技術(shù)文獻(xiàn)專利文獻(xiàn)專利文獻(xiàn)1:日本特開(kāi)H10-280070號(hào)公報(bào)專利文獻(xiàn)2:日本特開(kāi)2011-179025號(hào)公報(bào)專利文獻(xiàn)3:日本特開(kāi)H11-61392號(hào)公報(bào)技術(shù)實(shí)現(xiàn)要素:發(fā)明想要解決的課題本發(fā)明鑒于上述那樣的現(xiàn)有技術(shù)的問(wèn)題而開(kāi)發(fā),其目的在于,在鉑族基合金的制造方法方面,提供一種可大量地制造鉑族基合金的健全的熔解錠的方法。用于解決問(wèn)題的方案(第1發(fā)明)第1發(fā)明是一種鉑族基合金的制造方法,其特征在于,使用于真空腔室內(nèi)上部設(shè)置的電極炬(以下,亦稱為等離子體炬)與具有截面積為S1的空腔的在腔室內(nèi)下部的水冷卻銅坩堝之間形成等離子體電弧柱的等離子體電弧熔解爐,一邊將包含鉑族基合金的原料棒端部插入于該等離子體電弧柱進(jìn)行熔解,一邊滴下于該水冷卻銅坩堝內(nèi)的基材上并形成熔融池,并且,一邊通過(guò)拉低該基材而將該熔融池的液面高度維持一定,一邊使熔融池底部凝固,在這樣的連續(xù)鑄造方式的熔解錠制造工序中,該熔解錠的水平截面積S與長(zhǎng)度L滿足下面的關(guān)系,且,熔解時(shí)的腔室內(nèi)壓力為0.8atm以上,拉低速度為10mm/min以下。Sl≥S>500(mm2),此處,截面積S是重要的熔解參數(shù)。截面積S小于500mm2時(shí),則與水冷卻銅坩堝的接觸面積相對(duì)應(yīng)的熔融池的體積相對(duì)地減少,即,維持熔融的內(nèi)部能量不足而變得容易凝固,無(wú)法維持均勻的熔融與凝固狀態(tài),因而熔解錠的鑄件表面顯著地粗糙。截面積S通常因凝固收縮而成為空腔S1以下??涨坏男螤羁扇我膺x擇,但是為了維持更均勻的熔融與凝固狀態(tài),因而圓形、大致方形、大致多邊形是合適的。然而,關(guān)于鉑族基合金,作為主要成分的鉑族金屬的熔點(diǎn)為1500℃以上之高,且,定容潛熱與其它的高熔點(diǎn)金屬相比顯著地高,因而維持熔融池的均勻的熔融狀態(tài)是特別困難的。此處定容潛熱(kJ/cm3)是指為了熔解單位體積的物質(zhì)而必需的潛熱,由熔解熱(kJ/mol)與摩爾質(zhì)量(g/mol)與密度(g/cm3)定義。即,在熔解鉑族金屬(例如Ir)時(shí),相比較于相同體積且具有類似的熔點(diǎn)的其它的高熔點(diǎn)金屬(例如Nb),必須持續(xù)供給大概2倍的熱量(圖1)。此處,在圖1中,表示了鉑族金屬以及除了鉑族以外的高熔點(diǎn)金屬的定容潛熱與比熱的關(guān)系。因此,如果減少源自等離子體電弧柱的輸入熱,則維持熔融的內(nèi)部能量立即不足而變得容易凝固,與其它的高熔點(diǎn)金屬相比不易維持均勻的熔融與凝固狀態(tài),無(wú)法獲得鑄件表面平滑,即,沒(méi)有鑄造缺陷的健全的熔解錠。發(fā)明人等致力于克服此課題,發(fā)現(xiàn)了如果將腔室內(nèi)壓力設(shè)為0.8atm以上,則可制造截面積S為500mm2以上的鑄件表面粗糙少的熔解錠。等離子體電弧熔解法中,在電極炬與熔融池的電場(chǎng)中形成等離子體電弧柱。電場(chǎng)中的氣體密度高時(shí),則將等離子體電弧柱進(jìn)行高電壓化,并且在磁箍縮效應(yīng)的作用下集攏等離子體電弧柱,因而可更加提高能量密度。其結(jié)果,即使是本發(fā)明的小面積的熔融池(500mm2)也可維持均勻的熔融與凝固狀態(tài)。因此,腔室內(nèi)壓力不足0.8atm時(shí)則該效果弱,即使截面積S為500mm2,熔解錠的鑄件表面粗糙也變顯著,無(wú)法達(dá)成目的。電極炬也可一邊固定一邊熔解,為了維持均勻的熔融與凝固狀態(tài),也可以以任意的旋轉(zhuǎn)半徑將該電極炬外筒前端部進(jìn)行旋轉(zhuǎn)。在旋轉(zhuǎn)電極炬外筒前端部時(shí),則等離子體電弧柱使熔融池整體進(jìn)行旋轉(zhuǎn),因而特別是在S1較大的情況下,將熔融池整體加熱的效果變好,且,基于旋渦電流而得到的熔融池的攪拌效果提高,因而是有用的。適用具有此處記載的結(jié)構(gòu)等離子體電弧熔解爐以及條件時(shí),則可連續(xù)鑄造,因而獲得截面積S、長(zhǎng)度L的長(zhǎng)尺寸熔解錠。長(zhǎng)度L的局限根據(jù)設(shè)備的拉低費(fèi)用而確定,因而沒(méi)有特別限制,但是可以為500mm以上。但是,根據(jù)此發(fā)明的目的,在L<4√(S/π)方面,其它的現(xiàn)有技術(shù)例如非消耗電極型電弧熔解爐也可充分適用,因而排除在外。另外,氣氛氣體可任意選擇,通常設(shè)為Ar,但是出于電壓升高和/或制成還原氣氛的目的,也可并用He、N2、H2、CO2等。關(guān)于在熔解時(shí)的腔室內(nèi)壓力,在設(shè)為大氣壓(1atm)以上時(shí),則有效地抑制合金元素的蒸發(fā)。關(guān)于構(gòu)成合金的成分元素的蒸氣壓,在相同的溫度和壓力下,采用各自的元素所固有的值(例如,日本金屬學(xué)會(huì)編,修訂4版金屬數(shù)據(jù)手冊(cè),406頁(yè)中的詳細(xì)記載)。將合金加熱時(shí),根據(jù)成分元素各自的蒸氣壓而發(fā)生蒸發(fā),因此在熔解錠的組成中蒸氣壓高(容易蒸發(fā))的成分元素減少,引起產(chǎn)生與熔解前的組成之間的差異(組成變動(dòng))并且無(wú)法獲得目標(biāo)組成的問(wèn)題、以及引起減少部份的成品率降低。本發(fā)明中使用的等離子體電弧熔解爐是與真空等離子體熔解爐完全不同的結(jié)構(gòu),特別是在組成變動(dòng)方面具有不同的作用。真空等離子體熔解爐具有如下的結(jié)構(gòu):通過(guò)利用源自Ta制的中空陰極(圓筒狀)的熱電子釋出、與從中空電極內(nèi)釋出的微量的等離子體源氣體(一般為Ar)而形成等離子體束,利用配置在等離子體束的周?chē)母哳l集束線圈,將等離子體束進(jìn)行集攏從而提高能量密度。關(guān)于高溫高能量密度的等離子體束,形成于中空陰極前端與水冷卻銅坩堝之間,將存在于照射范圍的熔解原料進(jìn)行熔解,形成熔融池。關(guān)于熔解中的腔室內(nèi)壓力,必須通過(guò)精密地調(diào)整等離子體源氣體的流量與排氣速度從而設(shè)為1Pa左右的真空。因此,真空等離子體熔解爐在真空中不得不熔解,因而合金組成的變動(dòng)大。另一方面,關(guān)于本發(fā)明的等離子體電弧熔解,在0.8atm以上的腔室內(nèi)壓力下熔解,因而可有效地抑制組成變動(dòng)。拉低速度也是重要的參數(shù)。拉低速度超過(guò)10mm/min時(shí)則加熱和冷卻的平衡崩塌,熔融池容易變得凝固,鑄件表面顯著地粗糙。在低速側(cè)沒(méi)有不良情況,但是在必需量以上地遲緩的情況下,生產(chǎn)率降低。更優(yōu)選為,1~4mm/min是合適的。(第2發(fā)明)第2發(fā)明是一種鉑族基合金的制造方法,其關(guān)聯(lián)于第1發(fā)明,其特征在于,鉑族基合金包含50質(zhì)量%以上的鉑族金屬(Pt、Pd、Rh、Ir、Ru、Os)中的任意一種以上以及0.5質(zhì)量%以下的不可避免的雜質(zhì),除了不可避免的雜質(zhì)以外的成分元素之中,最高熔點(diǎn)的成分元素的熔點(diǎn)下的成分元素的蒸氣壓的最大值與最小值之差為0.1Pa以上。此處不可避免的雜質(zhì)是指原料中不可避免地包含的雜質(zhì),關(guān)于鉑族金屬,有時(shí)會(huì)包含0.5質(zhì)量%以下的其它的鉑族金屬。在成分元素間的蒸氣壓差為0.1Pa以上的合金的情況下,通過(guò)利用第1發(fā)明而使得合金元素的蒸發(fā)抑制效果特別高,可有效地抑制組成發(fā)生變動(dòng)。發(fā)明的效果如以上那樣,根據(jù)本發(fā)明,相比較于以往的制造方法而言合金的組成變動(dòng)小,可大量地制造沒(méi)有缺陷并且鑄件表面是平滑的熔解錠。關(guān)于組成變動(dòng)小這一點(diǎn),使得沒(méi)有必要在原料配混工序中預(yù)先過(guò)量地添加蒸發(fā)成分,另外,也可預(yù)防因偏離出目標(biāo)的組成范圍而導(dǎo)致的不適合品的產(chǎn)生,因而較大地有助于品質(zhì)管理。在熔解錠中沒(méi)有缺陷,鑄件表面是平滑的,這可將后續(xù)工序中的去除加工抑制在最小限度,可抑制材料成品率的降低。另外,在如本發(fā)明那樣可利用連續(xù)鑄造方式而大量地制造長(zhǎng)尺寸鑄錠時(shí),則當(dāng)然地較大地提高生產(chǎn)率。在非常昂貴的鉑族基合金的制造中,材料成品率的提高是至上的命題,本發(fā)明的制造方法有助于大幅減低經(jīng)濟(jì)損失。另外,根據(jù)本發(fā)明,盡管鉑族基合金具有非常大的定容潛熱,但還是可使高能量密度的等離子體電弧柱細(xì)細(xì)地集攏,因而獲得截面積500mm2以上這樣的細(xì)徑的熔解錠。由此,在將熔解錠加工為帶狀線的情況下,也可大幅減低加工工時(shí)。因此,對(duì)通過(guò)本發(fā)明而制造出的熔解錠進(jìn)行加工,應(yīng)用于高溫構(gòu)件和/或耐蝕制品時(shí),則也可實(shí)現(xiàn)最終制品的制造成本的減低。附圖說(shuō)明圖1是表示鉑族金屬以及除了鉑族金屬以外的高熔點(diǎn)金屬的定容潛熱的圖。圖2所示為等離子體電弧熔解爐的概略圖。圖3所示為拉低熔解的概略圖。具體實(shí)施方式本發(fā)明是鉑族基合金的制造方法,涉及基于連續(xù)鑄造方式的鑄錠制造。此處將內(nèi)燃機(jī)用火花塞的銥合金電極頭的制造工序作為一個(gè)例子而說(shuō)明。(配混工序)將Ir以及Rh等的原料粉末按規(guī)定的比率稱量,利用V型混合機(jī)進(jìn)行混合而制成混合粉(50質(zhì)量%以上的Ir粉末)?;旌戏椒ú恍枰薅ㄓ赩型混合器,如果是可充分均勻地混合粉末的方法即可。(原料棒制作工序)利用自動(dòng)壓制成型機(jī)(單軸加壓成型),將混合粉成型為20×20mm的長(zhǎng)方體。除此之外,也可以是:將混合粉填充于橡膠軟管等進(jìn)行密封,通過(guò)CIP而制成棒狀的成型體的方法。成型體在真空或者非活性氣氛中,在1300℃燒結(jié)。燒結(jié)體燒結(jié)收縮為約17×17mm。利用TIG焊接或者弧焊等將多個(gè)燒結(jié)體進(jìn)行接合而制成原料棒。此外,也可通過(guò)能量束熔解而制作原料棒。將1個(gè)或多個(gè)成型體裝載于具備有細(xì)長(zhǎng)的舟形的空腔的水冷卻銅坩堝,進(jìn)行能量束熔解。關(guān)于通過(guò)能量束熔解而制作出的熔解錠,制成接近大致空腔的形狀的細(xì)長(zhǎng)的形狀,可用作原料棒。關(guān)于原料棒的與長(zhǎng)度方向軸直交的剖面的最大直徑,優(yōu)選小于水冷卻銅坩堝的空腔最大直徑,更優(yōu)選為二分之一以下。(熔解工序)圖2為等離子體電弧熔解爐的概略圖。圖3為拉低熔解的概略圖。如圖2以及圖3所示那樣,將制作的原料棒把持于原料棒運(yùn)送機(jī)構(gòu)。具體而言,原料棒被原料棒運(yùn)送機(jī)構(gòu)的把持部(夾具)把持。另外,如圖2所示那樣,在配置在水冷卻銅坩堝(貫通空腔)底部的插銷(xiāo)上設(shè)置組成與原料棒相同的基材(原料小片)。利用油旋轉(zhuǎn)泵以及油擴(kuò)散泵將腔室內(nèi)進(jìn)行真空排氣后,注入Ar。在腔室中安裝了排氣閥與放氣閥,可通過(guò)設(shè)定各個(gè)閥的作動(dòng)壓力而將腔室內(nèi)的Ar壓力調(diào)節(jié)為0.8~1.2atm。在此例子中為1.2atm。在真空排氣中也可使用渦輪分子泵和/或機(jī)械性升壓泵。在此例子中水冷卻銅坩堝的空腔為圓形且直徑為35mm,即,截面積S1為962mm2。在設(shè)置于等離子體炬內(nèi)部的電極頭與等離子體炬外筒前端部之間產(chǎn)生先導(dǎo)電弧。接著,通過(guò)將DC電源從先導(dǎo)系統(tǒng)切換為主系統(tǒng),從而將放電(先導(dǎo)電弧)轉(zhuǎn)移到等離子體炬與基材水冷卻銅坩堝之間,產(chǎn)生等離子體電弧柱。此時(shí),在等離子體炬內(nèi)部流動(dòng)著Ar15L/min以及He8L/min作為等離子體源氣體。如此,在Ar的基礎(chǔ)上并用He、N2、H2、CO2等,這也對(duì)于提高等離子體電弧的能量密度而言有效。進(jìn)一步利用DC電源將輸出電流提高至約600A而開(kāi)始基材的熔解,按照在水冷卻銅坩堝的空腔內(nèi)形成熔融池的方式調(diào)整輸出電流。將輸出電流提高至約850A,然后利用原料棒運(yùn)送機(jī)構(gòu)以一定的速度將原料棒插入于等離子體電弧柱內(nèi),從原料棒前端開(kāi)始熔解。由于原料棒的熔滴連續(xù)地滴落向熔融池,因而按照可將熔融池的液面高度維持為一定的方式,利用鑄錠拉低機(jī)構(gòu)而調(diào)節(jié)基材的拉低速度(約3mm/min)。將原料棒一邊適宜追加或更換一邊連續(xù)鑄造。這般地,獲得直徑約(S為940mm2)、長(zhǎng)度L500mm以上的鑄件表面是平滑的熔解錠。(鍛造工序)將熔解錠按照成為長(zhǎng)度150mm以上的方式等分地切斷。在切斷中,可適用任意的切斷手段,但是為了重視材料成品率,因而薄刃的切斷磨刀石(金剛石或其它的磨削材料)、電火花線切割機(jī)以及線鋸是有效的。將切斷了的鑄錠加熱為1200℃~1800℃,進(jìn)行熱鍛造。關(guān)于鍛造軸,設(shè)為與圓柱狀鑄錠的中心線正交的雙軸(側(cè)面),在中心線方向打擊延長(zhǎng)而制成角棒。與圓柱狀鑄錠的中心線正交的面的截面積減少率為30%以上時(shí)則晶??砂l(fā)生微細(xì)化,上限可以不特別地設(shè)置但是為50%以下是充分的。如果這樣地鍛造,則可將熔解錠的粗大的晶粒粒徑充分地微細(xì)化,可容易進(jìn)行其后的軋制與拉絲加工。另外,熔解錠表面是平滑的,因而角棒表面也是平滑的。(軋制工序)對(duì)于角棒表面,為了去除源自鍛造機(jī)的鐵等附著物,因而使用Verder機(jī)(ベルダ機(jī))和/或研磨機(jī)等而薄薄地磨削。接著,將角棒加熱為1000℃~1400℃,利用帶有溝槽的軋制機(jī)而多次進(jìn)行熱軋,制成大致四邊形的角線。在加熱中,可使用管狀型電爐和/或連續(xù)式燃?xì)鉄煲约案哳l加熱爐。此時(shí),1次的加工的剖面減少率為20%以下,優(yōu)選為15%以下時(shí),則可抑制破裂等缺陷的產(chǎn)生。在一邊在上述范圍內(nèi)將加熱溫度階段性地拉低一邊加工時(shí),則抑制基于再結(jié)晶的粒生長(zhǎng),可形成且維持纖維組織,因而可在不生成破裂等缺陷的狀態(tài)下加工。(拉絲工序)角線是利用熱間口模拉絲而加工為的圓線。將材料的加熱溫度設(shè)為900℃~1300℃的范圍,加熱方法與軋制同樣。此時(shí),1次的加工的剖面減少率為10%以下,優(yōu)選為5%以下時(shí),則可抑制破裂等缺陷的產(chǎn)生。(切斷工序)將圓線切斷為適于線鋸的長(zhǎng)度。將多條線分別平行地重疊,進(jìn)行樹(shù)脂固定,利用線鋸切斷而制成的火花塞用電極頭。實(shí)施例以實(shí)施例來(lái)進(jìn)一步說(shuō)明。將實(shí)施例和比較例的實(shí)驗(yàn)條件示于表1中,將實(shí)施例和比較例的實(shí)驗(yàn)結(jié)果示于表2中,這些結(jié)果的評(píng)價(jià)示于表3。表1表1-實(shí)施例以及比較例的實(shí)驗(yàn)條件表2表2-實(shí)施例以及比較例的實(shí)驗(yàn)結(jié)果(原料棒的制作)在實(shí)施例1、實(shí)施例3、實(shí)施例5以及實(shí)施例6中,利用高頻電感熔解法將原料熔解于氧化鋯坩堝內(nèi),傾注于水冷卻銅鑄模(鑄造)而制作出熔解錠。對(duì)表面的缺陷等進(jìn)行去除加工,利用熱鍛造以及溝槽軋制加工而成型為角棒并且成為了原料棒。在實(shí)施例2以及比較例1中,將原料粉末進(jìn)行混合后,利用壓制成型機(jī)而成型為約15×15×50mm的長(zhǎng)方體,在置換為Ar氣氛的電爐內(nèi)以1500℃×3h進(jìn)行了燒結(jié)。利用TIG焊接機(jī)將該燒結(jié)體在長(zhǎng)度方向焊接并且制成了原料棒(約13×13×390mm)。在實(shí)施例4以及比較例4中,更換壓制成型模具,制成約20×20×50mm的長(zhǎng)方體的成型體,在相同條件下燒結(jié),在后面利用TIG焊接機(jī)在長(zhǎng)度方向焊接而制成了原料棒(約17×17×390mm)。在比較例2以及比較例3中,不使用原料棒,將厚度約3mm的合金板切斷為可容納于坩堝的尺寸而制成了熔解原料。(熔解錠的制作)在實(shí)施例1~6以及比較例1中,在大氣壓等離子體電弧熔解爐的原料棒運(yùn)送機(jī)構(gòu)中在水平方向上把持了原料棒。在具備有貫通的空腔的水冷卻銅坩堝底部配置的插銷(xiāo)上,作為基材,設(shè)置了組成與原料棒相同的小片。接著,利用油旋轉(zhuǎn)泵以及油擴(kuò)散泵將熔解爐腔室內(nèi)進(jìn)行真空排氣后,注入了Ar。在熔解中,通過(guò)設(shè)定真空排氣閥與放氣閥,從而將腔室內(nèi)壓力調(diào)節(jié)為一定。進(jìn)一步,在等離子體炬內(nèi)部使Ar作為等離子體源氣體進(jìn)行流動(dòng)而產(chǎn)生先導(dǎo)電弧,然后將等離子體電弧轉(zhuǎn)移向水冷卻銅坩堝以及基材,一邊提高輸出電流一邊熔化了基材并且形成了熔融池。其后,利用輸送機(jī)構(gòu)以一定速度將原料棒插入向等離子體電弧柱之中而開(kāi)始熔融,使熔滴滴落向熔融池。為了將熔融池的液面高度維持一定,因而利用鑄錠拉低機(jī)構(gòu)來(lái)調(diào)節(jié)基材的拉低速度從而連續(xù)鑄造。在最終階段,一邊降低輸出電流,一邊緩慢地凝固熔融池,抑制了縮孔的產(chǎn)生。予以說(shuō)明,在原料棒變短了時(shí),更換為新的原料棒而繼續(xù)了熔解。在實(shí)施例1~6中,可一邊根據(jù)材料和/或空腔的面積而適宜地調(diào)整輸出電流以及拉低速度,一邊維持均勻的熔融與凝固狀態(tài)。該熔解錠的與空腔的接觸面(鑄件表面),雖然具有微小的凹凸但是平滑,任一個(gè)都獲得了長(zhǎng)尺寸鑄錠。予以說(shuō)明,在實(shí)施例中限定了熔解量,但是熔解錠的長(zhǎng)度僅依存于拉低費(fèi)用,因而如果繼續(xù)熔解則也可制造500mm以上的長(zhǎng)尺寸鑄錠。另一方面,比較例1中,可形成熔融池,但是用肉眼看到空腔外周部斷續(xù)地凝固,難以維持均勻的熔融與凝固狀態(tài)。確認(rèn)出:在熔解錠的鑄件表面存在多個(gè)超過(guò)3mm的深的褶皺,也難以進(jìn)行去除加工,因而不適合于以后的加工。計(jì)量實(shí)施例1~6以及比較例1的熔解錠,結(jié)果是重量減少量為1%以下,并且從熔解錠切斷了插銷(xiāo)之后的材料成品率為98%以上,非常高。利用熒光X線分析對(duì)切斷面進(jìn)行定量,結(jié)果沒(méi)有確認(rèn)超過(guò)分析誤差的組成變動(dòng)。在比較例2中是以往使用的基于非消耗電弧熔解的方法,將約2kg的合金板(原料)設(shè)置于舟形的水冷卻銅坩堝上,將腔室內(nèi)進(jìn)行真空排氣后,設(shè)為0.7atm的Ar氣氛,制作出熔解錠。為了將原料全體完全地熔解,因而將原料進(jìn)行上下反轉(zhuǎn),對(duì)于每個(gè)單面熔解了各2次。鎢制電極在熔解中有消耗,在最終階段觀察到電弧柱的消失。在熔解后觀察電極放電端時(shí),則尖端部變圓,附著有凝著物。由此確認(rèn)了,非消耗電極型電弧熔解法無(wú)法實(shí)現(xiàn)超過(guò)2kg的大量的熔解。在熔解錠的外形方面,在側(cè)面存在有毛刺狀的突起,將其進(jìn)行去除加工(磨削)而計(jì)量,結(jié)果是減少5%以上,材料成品率為94%。另外,切斷熔解錠,利用熒光X線分析對(duì)切斷面進(jìn)行定量,結(jié)果確認(rèn)出約0.3質(zhì)量%的組成變動(dòng)(Ni減少)。在比較例3中,將約2kg的合金板填入于氧化鋯質(zhì)坩堝,將熔解爐腔室內(nèi)進(jìn)行真空排氣后,設(shè)為0.9atm的Ar氣氛,進(jìn)行了電感加熱熔解。在確認(rèn)完全熔解了之后,傾注坩堝,在模具內(nèi)進(jìn)行鑄造。在熔解錠的上表面,因凝固收縮而確認(rèn)了鑄造缺陷(所謂的縮孔),因而對(duì)縮孔部分進(jìn)行了去除加工(切斷)。在與鑄壁的接觸面(鑄件表面),存在有褶皺狀的凹凸,當(dāng)對(duì)鑄件表面進(jìn)行切削(深度約0.5mm)時(shí),由于內(nèi)部存在有小氣孔以及耐火物,因而對(duì)鑄件表面整面進(jìn)行了深度約2mm去除加工(切削)。計(jì)量去除加工后的鑄錠,結(jié)果是材料成品率為70%以下。由此確認(rèn)了,電感加熱熔解法無(wú)法避免材料成品率的低下。另外,對(duì)全表面進(jìn)行了去除加工,但是也殘存了在剩余部分的鑄錠中包含小氣孔和/或耐火物等缺陷的風(fēng)險(xiǎn)。利用熒光X線分析對(duì)切削面進(jìn)行定量,結(jié)果沒(méi)有確認(rèn)出超過(guò)分析誤差的組成變動(dòng)。在比較例4中,真空等離子體熔解爐的原料棒運(yùn)送機(jī)構(gòu)在水平方向上把持了原料棒。在具備有貫通的空腔的水冷卻銅坩堝底部的插銷(xiāo)上,作為基材,設(shè)置了組成與原料棒相同的小片。接著,利用油旋轉(zhuǎn)泵以及油擴(kuò)散泵對(duì)熔解爐腔室內(nèi)進(jìn)行了真空排氣。進(jìn)一步,在中空陰極中使Ar作為等離子體源氣體而流動(dòng)并且產(chǎn)生等離子體束,加熱,然后將等離子體束轉(zhuǎn)移向水冷卻銅坩堝以及基材,一邊提高輸出電流一邊熔化基材并且形成了熔融池。其后,利用運(yùn)送機(jī)構(gòu)以一定速度將原料棒插入向等離子體束之中而開(kāi)始熔融,使熔滴滴下至熔融池。為了將熔融池的液面高度維持一定,因而利用拉低機(jī)構(gòu)調(diào)節(jié)基材的拉低速度從而連續(xù)鑄造。在熔解中,一邊調(diào)整Ar流量一邊維持了1.5Pa的真空。予以說(shuō)明,在原料棒變短了時(shí),更換為新的原料棒而繼續(xù)了熔解。在比較例4中,可一邊調(diào)整輸出電流、源氣體流量以及拉低速度,一邊維持均勻的熔融凝固狀態(tài)。熔解錠的與空腔的接觸面(鑄件表面)與實(shí)施例1~6同樣地,雖然具有微小的凹凸但是平滑,獲得了長(zhǎng)度約105mm的長(zhǎng)尺寸鑄錠。計(jì)量該熔解錠,結(jié)果是減少量為2%以下,插銷(xiāo)切斷后的材料成品率為96%以上之高。利用熒光X線分析對(duì)切斷面進(jìn)行定量,結(jié)果確認(rèn)出1質(zhì)量%的組成變動(dòng)(Rh的減少)。這樣地,真空等離子體熔解法雖然獲得了外觀上健全的長(zhǎng)尺寸的鑄錠,但是因高蒸氣壓的合金成分的蒸發(fā)而導(dǎo)致的組成變動(dòng)是顯著的,不適合制造均質(zhì)的熔解錠。(結(jié)果的評(píng)價(jià))表3所示的評(píng)價(jià)基于下面的尺度。關(guān)于熔解錠的大型化的可能性,將不能的情況設(shè)為了×,將通過(guò)連續(xù)鑄造方式或坩堝的大型化而變得可能的情況設(shè)為了○。將鑄件表面狀態(tài)不良并且必需大幅的去除加工的情況設(shè)為×,將必需一部分去除加工的情況設(shè)為△,將大致平滑且不需要去除加工的情況設(shè)為了○。關(guān)于材料成品率,將相對(duì)于熔解前的質(zhì)量的熔解與去除加工后的質(zhì)量比不足90%的情況設(shè)為×,將90%以上的情況設(shè)為△,將其中95%以上的情況設(shè)為了○。關(guān)于鑄件表面狀態(tài)差的情況,必需去除加工并且材料成品率大幅地降低。關(guān)于組成變動(dòng),將變動(dòng)幅度超過(guò)分析誤差的情況設(shè)為×,將處于分析誤差以內(nèi)的情況設(shè)為了○。本發(fā)明的實(shí)施例在任一個(gè)評(píng)價(jià)項(xiàng)目中都良好(○),可確認(rèn)本發(fā)明的效果。表3表3-實(shí)施例以及比較例的評(píng)價(jià)結(jié)果No.大型化鑄件表面狀態(tài)材料成品率組成變動(dòng)實(shí)施例1○○○○實(shí)施例2○○○○實(shí)施例3○○○○實(shí)施例4○○○○實(shí)施例5○○○○實(shí)施例6○○○○比較例1×××○比較例2×△△×比較例3○××○比較例4○○○×從以上的結(jié)果明顯可知,根據(jù)本發(fā)明,在鉑族基合金的制造中,可獲得沒(méi)有組成變動(dòng)并且材料成品率高的大型的熔解錠。當(dāng)前第1頁(yè)1 2 3