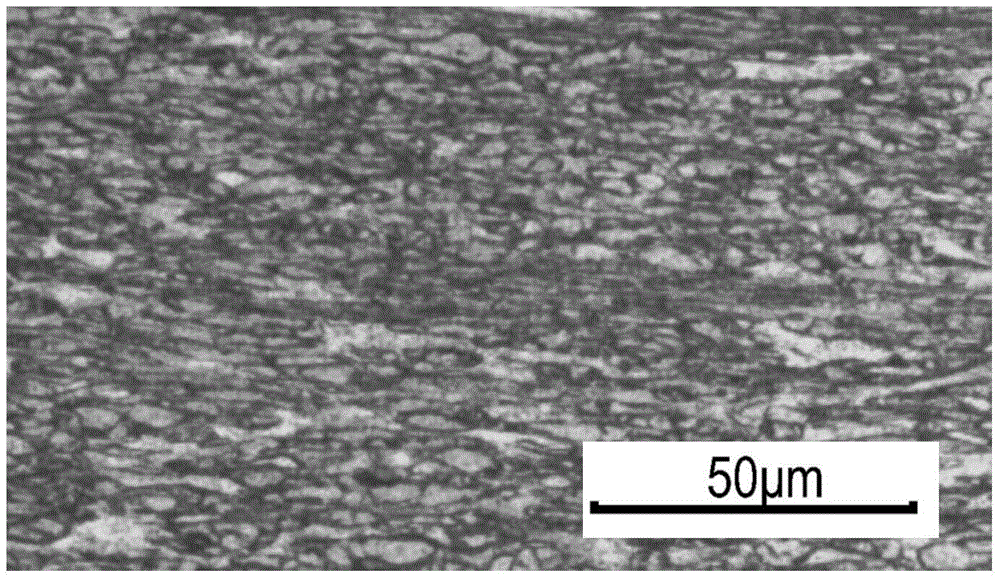
本發(fā)明涉及有色金屬合金技術領域,具體涉及一種銅鐵合金絲材及其制備方法。
背景技術:金屬材料有著廣泛的應用范圍,但國內(nèi)外對銅鐵合金的報道卻極少,由金屬材料學的知識可以預測到Cu-Fe合金的一些特點:(1)熔點應高于Cu而低于Fe,若將其用做真空電觸頭材料來替代Cu合金,則可改善其耐電弧燒蝕能力;(2)純銅和純鐵都具有良好的延展性,因此Cu-Fe合金應該也具備該性能;(3)用Fe替代部分Cu可以降低Cu材料的成本;(4)具有電磁屏蔽效果。圖1所示為Cu-Fe二元合金相圖,初級固溶理論認為:兩種元素的原子半徑及電化學性質(zhì)越相似,則越容易形成固溶體,但Fe-Cu系卻是例外,它們的原子半徑幾乎相等,化學親和力或電負性以及其他化學性質(zhì)都很類似,但在熔點以下的溶解度卻很小,從金屬相圖上看Fe在Cu中只有2.5%無限固溶。隨著Fe含量的增加,Cu-Fe合金在凝固過程中極易形成偏析嚴重的組織,即合金的顯微組織主要以初生的富Fe枝晶形式存在于Cu基體中,F(xiàn)e含量越高,α-Fe枝晶越粗大,因為該合金的這一特性,大大阻礙了Cu-Fe合金的生產(chǎn)與應用。合金在冶煉過程中,一些元素是以中間合金的方式加入。利用中間合金加入的方式,一方面可以減少合金元素的熔煉損耗,從而實現(xiàn)對合金化學成分的精確控制;另一方面,在降低熔煉溫度的同時也縮短了熔煉時間,有利于提高熔煉設備的壽命,且節(jié)約能源。另有研究表明,中間合金的組成、結構等因素也會對所制備合金的性能產(chǎn)生重要影響。因此,通過在生產(chǎn)Cu-Fe二元合金過程中采用特定的中間合金母料,以期改變所制備Cu-Fe二元合金的固溶性,優(yōu)化其性能及拓展應用范圍,成為一種新的研究思路。
技術實現(xiàn)要素:本發(fā)明的目的在于提供一種銅鐵合金絲材及其制備方法,采用特定組成的中間合金母料,結合特定的工藝,制備的CuFe合金鑄態(tài)和鍛態(tài)時Fe與Cu固溶良好,F(xiàn)e元素分布均勻、不偏析,具有良好的加工性。進一步加工成絲材后,具有優(yōu)異的機械強度和延伸率。為實現(xiàn)上述目的,本發(fā)明所采用的技術方案如下:一種銅鐵合金絲材,按重量百分含量計,該銅鐵合金絲材化學成分為:Fe為8.0~13.0%,余量為Cu及不可避免的雜質(zhì);該絲材優(yōu)選的化學成分為:Fe為8.5~11.5%,余量為Cu及不可避免的雜質(zhì);其化學成分中:C≤0.03%,S≤0.01%,P≤0.01%。該銅鐵合金絲材成品尺寸公差精度高,其直徑Ф0.05~0.1mm,抗拉強度≥440N/mm2;延伸率≥10%;該絲材還具有優(yōu)異的電磁屏蔽效果。所述銅鐵合金絲材按照如下步驟進行制備:(1)原料準備及配料將陰極銅和中間合金母料表面依次經(jīng)酸洗、水洗和烘干處理,確保所有原料清潔,然后按所需比例準確稱重;所述酸洗是指:陰極銅采用濃度30vol.%的硫酸清洗,工業(yè)純鐵采用濃度30vol.%的鹽酸清洗,電解鎳采用濃度40vol.%的硝酸清洗;所述中間合金母料為條狀銅鐵中間合金,按重量百分含量計,該中間合金化學成分為:Fe45~60%,Ni0.20~0.35%,RE>0,Cu為余量;其中:RE為稀土元素La和Ce;該中間合金化學成分優(yōu)選為:Fe48~52%,Ni0.20~0.30%,La<0.02%,Ce<0.04%,Cu為余量。所述中間合金母料作為鐵元素和部分銅元素的來源,所述陰極銅作為剩余部分銅元素的來源;所述中間合金母料的制備包括如下(a)-(e)步驟:(a)原料準備:原料選擇陰極銅、工業(yè)純鐵和電解鎳,原料使用前依次經(jīng)酸洗、水洗和烘干處理,以保證所有原料清潔;所述酸洗是指:陰極銅采用濃度30vol.%的硫酸清洗,工業(yè)純鐵采用濃度30vol.%的鹽酸清洗,電解鎳采用濃度40vol.%的硝酸清洗。按重量百分含量計,原料中各元素百分含量為:Fe45~60%,Ni0.20~0.35%,RE0.05~0.1%,Cu為余量;其中:RE為稀土元素La和Ce;原料中各元素百分含量優(yōu)選為:Fe48~52%,Ni0.25~0.30%,La0.02~0.025%,Ce0.04~0.045%,Cu為余量。(b)真空感應熔煉:按照原料中各元素比例配料,然后進行真空感應熔煉,熔煉過程具體為:將陰極銅、工業(yè)純鐵按配比裝入坩堝內(nèi),爐內(nèi)抽真空后送電熔化,1300~1550℃精煉20-30min;加入Ni和CaF后再次精煉20-30min;最后加入La和Ce,40~50秒后開始帶電澆鑄;熔煉過程中,真空度≤8Pa,精煉溫度控制在1300~1550℃;澆鑄獲得合金鑄錠;(c)鑄錠銑面:用立式銑床去除鑄錠表面2-3mm厚的表層,其目的是除去雜質(zhì)含量高的部分,同時利于后續(xù)加工;(d)熱軋開坯:軋制溫度1000~1015℃,保溫90~100分鐘,軋制6-7個道次,熱軋至10~12mm,然后冷加工至5~6mm;(e)熱軋開坯后的板材進行清洗,清洗過程為:先用濃度30vol.%的硫酸洗去板材表面的氧化皮,再用清水將表面的殘酸沖洗干凈;清洗后剪切成所需規(guī)格的條狀銅鐵中間合金材料。(2)真空熔煉將陰極銅、中間合金母料裝入坩堝內(nèi),送電熔化后精煉20-30min,然后加入CaF,再次精煉20-30min,再在爐內(nèi)充入惰性氣體Ar后開始帶電澆鑄,即獲得所述銅鐵合金鑄錠;真空熔煉過程中:精煉溫度控制在1200~1500℃;真空度≤2Pa;所制備的銅鐵合金(鑄錠)中Fe元素分布均勻、不偏析。(3)合金鑄錠車光:將銅鐵合金鑄錠表面車光。(4)熱鍛及鍛后車光:在750Kg空氣錘上自由鍛造,電爐加熱溫度850~875℃,保溫60~100分鐘后,進行兩鐓兩拔后鍛至Ф42~50mm棒材;然后車光至Ф40~45mm棒材。(5)熱軋制:電爐加熱溫度845~855℃,保溫70~80分鐘后,在Ф250×350孔型軋機上軋制(梗壓)至Ф10~15mm棒材。(6)冷加工及中間過程真空退火:將步驟(3)所得Ф10~15mm棒材依次進行盤圓、退火和冷拉拔處理,重復該過程3~5次,獲得Ф1.2~2.0mm絲材后再進行退火處理,退火溫度550~730℃。(7)微絲拉拔:真空退火后軟態(tài)Ф1.2~2.0mm絲材進行多次拉拔處理,獲得直徑Ф0.05~0.1mm銅鐵合金絲材,具體過程為:將Ф1.2~2.0mm絲材拉拔至Ф0.8~1.2mm,每道次加工率15%;連續(xù)氫氣退火爐退火處理:爐溫740℃,引取(機)速度70~80之間,退火后絲材延伸率≥25%;將Ф0.8~1.2mm絲材拉拔至Ф0.3~0.5mm,每道次加工率15%;連續(xù)氫氣退火爐退火處理:爐溫740℃,引取(機)速度70~80之間,退火后絲材延伸率≥25%;將Ф0.3~0.5mm絲材拉拔至Ф0.15~0.2mm,每道次加工率13%;連續(xù)氫氣退火爐退火處理:爐溫740℃,引取(機)速度70~80之間,退火后絲材延伸率≥20%;將Ф0.15~0.2mm絲材拉拔至Ф0.05~0.1mm,每道次加工率12%;連續(xù)氫氣退火爐退火處理:爐溫740℃,引取(機)速度70~80之間,退火后絲材延伸率≥10%。本發(fā)明的優(yōu)點及有益效果如下:1、為生產(chǎn)高強度高延展性Cu-Fe合金絲材,采用CuFe中間合金母料。母料鑄錠上、中、下成分均勻,F(xiàn)e元素分布均勻、不偏析;采用該母料并配合特點的制備工藝可降低高延展性Cu-Fe合金的熔點,減少Fe的氧化和燒損,并通過二次真空重熔,使高延展性Cu-Fe合金中Fe的分布均勻、不偏析。2、為制成成分均勻的CuFe中間合金母料,加入特定配比的稀土元素La(鑭)和Ce(鈰),稀土元素La和Ce具有凈化、去雜作用,并在特定工藝條件下與其他元素協(xié)同作用,從而充分細化Cu-Fe合金鑄態(tài)組織的晶粒,減少偏析的產(chǎn)生。3、所制備的高強高延展性銅鐵合金絲材化學成分穩(wěn)定,F(xiàn)e元素在合金中的分布均勻、不偏析。4、所制備的高強、高延展性銅鐵合金絲材成品尺寸公差精度高,微絲直徑Ф可達0.05~0.1mm;機械性能優(yōu)良,絲材抗拉強度≥440N/mm2,延伸率≥10%;銅鐵合金絲材還具有優(yōu)異的電磁屏蔽效果,性能穩(wěn)定,性價比高,具有十分廣闊的市場前景。附圖說明圖1為CuFe二元合金相圖。圖2為實施例1制備的CuFe中間合金金相微觀形貌圖。圖3為實施例1制備的CuFe合金鑄造狀態(tài)下金相微觀形貌圖。圖4為實施例1制備的CuFe合金鍛造狀態(tài)下金相微觀形貌圖。圖5為實施例1制備的CuFe合金拉伸至Ф8.4mm時金相微觀形貌圖。具體實施方式以下結合附圖及實施例詳述本發(fā)明。本發(fā)明以銅鐵中間合金作為Cu-Fe合金絲材制備用的母料,該中間合金的制備過程為:原料準備→配料→真空熔煉→母料成分分析→鑄錠銑面→熱軋→酸洗、水洗→剪切;以下實施例按照如下步驟制備:(1)原料準備原料中各元素配比為(wt.%):Fe45~60%,Ni0.20~0.35%,RE0.05~0.1%,Cu為余量;其中:RE為稀土元素La和Ce;優(yōu)選的原料配比為:Fe48~52%,Ni0.25~0.30%,La0.02~0.025%,Ce0.04~0.045%,Cu為余量。(2)配料:按原料中各元素配比準確稱重。將陰極銅、工業(yè)純鐵、電解鎳表面經(jīng)酸洗、水洗、烘干處理,確保所有原料清潔。酸洗過程為:陰極銅采用濃度30vol.%的硫酸清洗,工業(yè)純鐵采用濃度30vol.%的鹽酸清洗,電解鎳采用濃度40vol.%的硝酸清洗。(3)真空熔煉將陰極銅、工業(yè)純鐵裝入坩堝內(nèi),電解鎳和CaF裝入加料斗內(nèi),稀土元素La和Ce裝入加料器內(nèi);封爐抽真空,真空度≤8Pa(即6×10-2mmHg);送電熔化后精煉25min,然后Ni(電解鎳)和CaF再次精煉25min,最后加入La和Ce,45秒后開始帶電澆鑄,獲得合金鑄錠。真空熔煉采用的真空感應電爐型號:ZG-0.025;精煉溫度控制在1300~1550℃。(4)母料成分分析采用氟化氫銨遮蔽Fe,然后用化學滴定檢測母料鑄錠上、下Cu的含量,精準確定母料中Cu、Fe成分對下一步CuFe系合金的生產(chǎn)十分重要。(5)鑄錠銑面用立式銑床去除錠表面雜質(zhì)含量高的部分(去除2mm厚度表層),同時利于后續(xù)加工。(6)熱軋開坯電爐加熱:溫度1010℃,保溫90~100分鐘,熱軋至12mm,冷加工至5~6mm。所用設備:Φ250×450二輥熱軋機。(7)酸洗、水洗:用硫酸(30vol.%)洗去母料表面的氧化皮并用清水將表面的殘酸沖洗干凈。(8)剪切:將母料板材剪切成所需規(guī)格條狀中間合金待用。將上述制備的條狀中間合金作為所需制備的高強高延展性銅鐵合金絲材的母料,用于制備高強高延展性銅鐵合金絲材的過程如下:(1)原料準備及配料將陰極銅和條狀中間合金母料表面依次經(jīng)酸洗、水洗和烘干處理,確保所有原料清潔,所述酸洗是指:陰極銅采用濃度30vol.%的硫酸清洗,工業(yè)純鐵采用濃度30vol.%的鹽酸清洗,電解鎳采用濃度40vol.%的硝酸清洗;所要制備的銅鐵合金絲材化學成分為(wt.%):Fe為8.0~13.0%,余量為Cu及不可避免的雜質(zhì);優(yōu)選的化學成分為(wt.%):Fe為8.5~11.5%,余量為Cu及不可避免的雜質(zhì);合金中:C≤0.03%,S≤0.01%,P≤0.01%。將清洗后的原料按所需合金配比準確稱重;所述中間合金母料作為所需制備高延展性銅鐵合金中鐵元素和部分銅元素的來源,所述陰極銅作為剩余部分銅元素的來源;(2)真空熔煉真空熔煉過程中:精煉溫度控制在1200~1500℃;真空度≤2Pa(即1.5×10-2mmHg);真空熔煉所用設備:ZG-0.025真空感應電爐,熔煉過程為:將陰極銅、條狀中間合金母料裝入坩堝內(nèi),CaF裝入加料斗內(nèi),封爐抽真空,送電熔化后精煉20min,然后加入CaF,再次精煉20min,再在爐內(nèi)充入惰性氣體Ar后開始帶電澆鑄,即獲得銅鐵合金鑄錠。(3)采用等離子體原子發(fā)射光譜儀(ICP-1000)檢測所制備的銅鐵合金鑄錠上、中、下Fe的成分。(4)合金鑄錠車光:將成分合格的銅鐵合金鑄錠在CA6140車床上表面車光。(5)熱鍛及鍛后車光:在750Kg空氣錘上自由鍛造,電爐加熱溫度860℃,保溫90分鐘后,進行兩鐓兩拔后鍛至Ф45mm棒材;然后車光至Ф42mm棒材。(6)熱軋制:電爐加熱溫度850℃,保溫70分鐘后,在Ф250×350孔型軋機上軋制(梗壓)至Ф13mm棒材。(7)冷加工及中間過程真空退火:將步驟(3)所得Ф13mm棒材依次進行盤圓、退火(退火溫度550~730℃)和冷拉拔處理,重復該過程4次,獲得Ф1.5mm絲材后再進行550~730℃條件下的退火處理;該步驟中所用設備LS-20噸鏈式拉拔機;1/560、1/350、1/250立式拉伸機;Ф800井式真空退火爐等。(8)微絲拉拔:真空退火后軟態(tài)Ф1.5mm絲材進行多道次拉拔處理,每道次加工率15%,拉拔至Ф0.9mm;連續(xù)退火爐退火處理(氫氣):爐溫740℃,引取(機)速度80,退火后絲材延伸率≥25%;將Ф0.9mm絲材進行多道次拉拔處理,每道次加工率15%,拉拔至Ф0.4mm;連續(xù)退火爐退火處理(氫氣):爐溫740℃,引取(機)速度70,退火后絲材延伸率≥25%;將Ф0.4mm絲材拉拔至Ф0.18mm,每道次加工率13%;連續(xù)氫氣退火爐退火處理:爐溫740℃,引取(機)速度70,退火后絲材延伸率≥20%;將Ф0.18mm絲材拉拔至Ф0.06mm,每道次加工率12%;連續(xù)氫氣退火爐退火處理:爐溫740℃,引取(機)速度70,退火后絲材延伸率≥10%。實施例11、本實施例制備銅鐵中間合金母料各原料的具體用量為(wt.%):Fe=48%;Ni=0.25%;La=0.02%;Ce=0.04%;Cu=51.69%;所得中間合金母料(1#)成分見表1,該中間合金金相微觀形貌圖如圖2,由圖2和表1數(shù)據(jù)可以看出,本發(fā)明制備的銅鐵中間合金化學成分穩(wěn)定,鑄錠上、中、下成分均勻;Fe元素在中間合金中分布均勻、不偏析。2、制備高強高延展性CuFe合金,化學成分設計為(wt.%):Fe=8.8%,Cu=91.2%。所制備的銅鐵合金鑄錠成分如表2所示,鑄錠化學成分穩(wěn)定,鑄錠上、中、下成分均勻;鑄造狀態(tài)下金相微觀形貌圖如圖3所示,可以看出,Cu、Fe固溶良好,尚有部分游離狀態(tài)的富Fe存在。鑄錠經(jīng)鍛造后的金相微觀形貌如圖4所示,鑄態(tài)下游離的富Fe經(jīng)過加熱和鍛打得到部分破碎。3、將CuFe合金棒材加工成絲材,拉伸至Ф8.4mm絲材時的金相微觀形貌如圖5,從圖中可以看出,經(jīng)過反復加熱、熱處理和反復梗壓、拉伸加工后,F(xiàn)e的分布更加均勻、細化。最終制備成Ф0.06mm絲材,經(jīng)測試,該Ф0.06mm絲材抗拉強度440N/mm2;延伸率為12.5%;該銅鐵合金還具有優(yōu)異的電磁屏蔽效果。實施例21、本實施例制備銅鐵中間合金母料過程同實施例1。2、制備高強高延展性CuFe合金,化學成分設計為(wt.%):Fe=9.0%,Cu=91.0%。所制備的銅鐵合金鑄錠成分如表2所示,鑄錠化學成分穩(wěn)定,鑄錠上、中、下成分均勻;3、將CuFe合金鑄錠加工成Ф0.06mm絲材,經(jīng)測試,該Ф0.06mm絲材抗拉強度443N/mm2;延伸率為12%;該銅鐵合金還具有優(yōu)異的電磁屏蔽效果。實施例31、本實施例制備銅鐵中間合金母料過程同實施例1。2、制備高強高延展性CuFe合金,化學成分設計為(wt.%):Fe=9.5%,Cu=90.5%。所制備的銅鐵合金鑄錠成分如表2所示,鑄錠化學成分穩(wěn)定,鑄錠上、中、下成分均勻;3、將CuFe合金鑄錠加工成Ф0.06mm絲材,經(jīng)測試,該Ф0.06mm絲材抗拉強度445N/mm2;延伸率為11.2%;該銅鐵合金還具有優(yōu)異的電磁屏蔽效果。實施例41、本實施例制備銅鐵中間合金母料過程同實施例1。2、制備高強高延展性CuFe合金,化學成分設計為(wt.%):Fe=10.2%,Cu=89.8%。所制備的銅鐵合金鑄錠成分如表2所示,鑄錠化學成分穩(wěn)定,鑄錠上、中、下成分均勻;3、將CuFe合金鑄錠加工成Ф0.06mm絲材,經(jīng)測試,該Ф0.06mm絲材抗拉強度448N/mm2;延伸率為11%;該銅鐵合金還具有優(yōu)異的電磁屏蔽效果。實施例51、本實施例制備銅鐵中間合金母料各原料的具體用量為(wt.%):Fe=49%;Ni=0.26%;La=0.02%;Ce=0.04%;Cu=51.68%;所得中間合金母料(2#)成分見表1,由表1數(shù)據(jù)可以看出,本發(fā)明制備的銅鐵中間合金化學成分穩(wěn)定,鑄錠上、中、下成分均勻;Fe元素在中間合金中分布均勻、不偏析。2、制備高強高延展性CuFe合金,化學成分設計為(wt.%):Fe=10.8%,Cu=89.2%。所制備的銅鐵合金鑄錠成分如表2所示,鑄錠化學成分穩(wěn)定,鑄錠上、中、下成分均勻;3、將CuFe合金鑄錠加工成Ф0.06mm絲材,經(jīng)測試,該Ф0.06mm絲材抗拉強度452N/mm2;延伸率為10.3%;該銅鐵合金還具有優(yōu)異的電磁屏蔽效果。實施例61、本實施例制備銅鐵中間合金母料各原料的具體用量為(wt.%):Fe=50%;Ni=0.27%;La=0.02%;Ce=0.04%;Cu=49.67%;所得中間合金母料(3#)成分見表1,由表1數(shù)據(jù)可以看出,本發(fā)明制備的銅鐵中間合金化學成分穩(wěn)定,鑄錠上、中、下成分均勻;Fe元素在中間合金中分布均勻、不偏析。2、制備高強高延展性CuFe合金,化學成分設計為(wt.%):Fe=11.2%,Cu=88.8%。所制備的銅鐵合金鑄錠成分如表2所示,鑄錠化學成分穩(wěn)定,鑄錠上、中、下成分均勻;3、將CuFe合金鑄錠加工成Ф0.06mm絲材,經(jīng)測試,該Ф0.06mm絲材抗拉強度455N/mm2;延伸率為10%;該銅鐵合金還具有優(yōu)異的電磁屏蔽效果。上述實施例中CuFe中間合金母料(鑄錠)化學成分實測值如表1所示(分析方法:用氟化氫銨遮蔽Fe,然后滴定法測Cu含量,結合其他元素分析方法測其他元素含量)。所制備的銅鐵合金鑄錠化學成分實測值如表2所示,采用等離子體原子發(fā)射光譜儀(ICP-1000)檢測所制備的鑄錠上、中、下Fe的成分。表1CuFe中間合金母料(鑄錠)化學成分(wt.%)表2CuFe合金(鑄錠)化學成分實測值(wt.%)