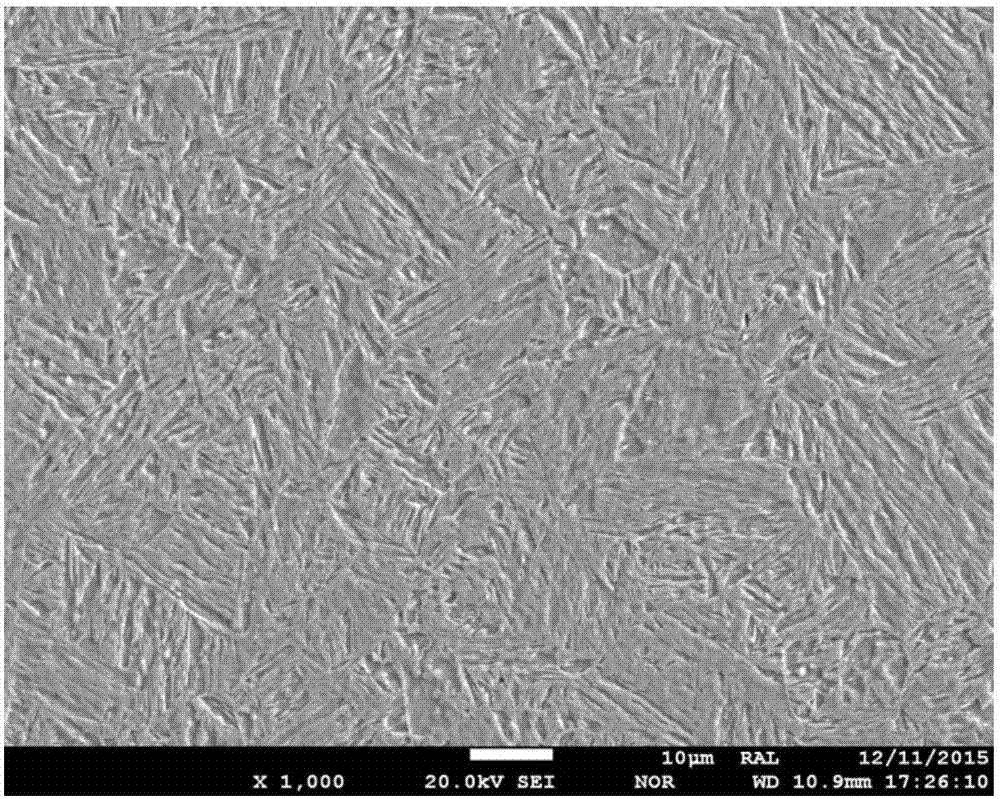
本發(fā)明涉及汽車結(jié)構(gòu)件熱成形
技術(shù)領(lǐng)域:
,具體涉及熱成形件沖壓生產(chǎn)過程中,在不降低零件強(qiáng)度的前提下,穩(wěn)定降低板料成形溫度的方法。
背景技術(shù):
:熱成形件因其較高的強(qiáng)度(1500mpa左右),在汽車結(jié)構(gòu)件上得到廣泛應(yīng)用。然而成形溫度過高,成形溫度在720~850℃范圍內(nèi)(具體溫度與板料厚度和轉(zhuǎn)移時(shí)間有關(guān));板料成形過程中,模具與板料接觸有先后,導(dǎo)致板料溫度不均勻,故不同區(qū)域的流變抗力不同;板料流變抗力不均勻從而導(dǎo)致局部塑性變形過大,零件容易開裂。降低板料的溫度可以有效解決該問題;然而目前降低成形溫度的方法有很多的局限性,如:延長轉(zhuǎn)移時(shí)間,快速降溫,兩相區(qū)加熱等。中國專利cn103069041a公開了《鍍鋅板的熱沖壓方法》,該方法中為了保證板料低于鍍鋅層熔點(diǎn)(780℃),發(fā)明了一種判斷板料低于780℃的方法;利用觀測波長為1.4um以上的發(fā)射率測定儀來檢測鍍鋅鋼板表面的發(fā)射率,根據(jù)變化來判斷板料溫度是否低于780℃。然而該方法只能單一控制低于780℃;需要通過延長空冷時(shí)間實(shí)現(xiàn),且控制工藝復(fù)雜,自動(dòng)化控制要求較高。日本特開2007-182608號公報(bào)中,鍍鋅鋼板在加熱爐中加熱至奧氏體化后,料片出爐后經(jīng)過驟冷設(shè)備被降低至500~730℃,接著進(jìn)行熱成形。該方法雖然能夠有效降低板料成形溫度,但需要驟冷設(shè)備,自動(dòng)化控制難度較大。專利cn1698993a公開了《溫?zé)峄驘岢尚萎a(chǎn)品的生產(chǎn)方法》,該方法中通過兩相區(qū)加熱或者緩慢冷卻,從而降低板料的成形溫度,提高了板料的成形性能;然而該方法將鐵素體引入最終組織,導(dǎo)致零件的抗拉強(qiáng)度降低。技術(shù)實(shí)現(xiàn)要素:為克服所述不足,在保證高強(qiáng)度的前提下,提供一種穩(wěn)定降低熱成形溫度的工藝方法。本發(fā)明解決其技術(shù)問題所采用的技術(shù)方案是:一種穩(wěn)定降低熱成形溫度的工藝方法,包括以下步驟:步驟一:板料在加熱爐中奧氏體化,熱成形板料首先在加熱爐中,被加熱至完全奧氏體化狀態(tài),此過程中加熱溫度850-950℃,加熱時(shí)間3-10min;步驟二:板料預(yù)冷卻并保溫,步驟一加熱后的板料被轉(zhuǎn)移至另一個(gè)恒溫爐中進(jìn)行保溫,保溫溫度為750-850℃,保溫時(shí)間0-5min;步驟三:沖壓成形淬火,步驟二保溫后的板料出爐,迅速轉(zhuǎn)移至壓力機(jī)上沖壓成形并保壓淬火,獲得全馬氏體組織的零件。具體地,所述完全奧氏體化的板料轉(zhuǎn)移至低溫爐保溫時(shí)所選擇的溫度和時(shí)間,是根據(jù)最終的成形溫度要求、板料厚度、轉(zhuǎn)移時(shí)間所決定的。具體地,經(jīng)過步驟二保溫后的板料被轉(zhuǎn)移至帶有冷卻模具的壓力機(jī)上成形淬火,從而實(shí)現(xiàn)在保證成形件高強(qiáng)度的前提下,穩(wěn)定降低板料的成形溫度。具體地,所述板料包括裸板,al-si涂層板和鍍鋅板,比如板料采用22mnb5型的熱成形用鋼板,具體成分如下表1:表1熱成形用鋼化學(xué)成分(wt,%)csimncrmotialbsp0.19~0.250.2~1.30.5~1.50.1~0.40~0.30.03~0.050.02~0.060.0015~0.00500~0.0260~0.035具體地,經(jīng)過步驟一后板料完全奧氏體化后進(jìn)入第二個(gè)保溫爐保溫時(shí),保溫溫度和時(shí)間的工藝窗口是根據(jù)具體材料的熱動(dòng)力學(xué)性能決定的。本發(fā)明具有以下有益效果:通過爐溫來降低成形溫度,穩(wěn)定可靠;在降低成形溫度的同時(shí),保證原有的強(qiáng)度;成形溫度的降低,為解決“鍍鋅板熱成形過程中液化鋅層引起的開裂問題”提供新思路。附圖說明圖1為本發(fā)明工藝步驟示意圖。圖2為本發(fā)明實(shí)施例1中成形件的微觀組織圖。圖3為本發(fā)明實(shí)施例2中成型件的微觀組織圖。圖中1板料在加熱爐內(nèi)奧氏體化,2板料預(yù)冷卻并保溫,3沖壓成形淬火。具體實(shí)施方式現(xiàn)在對本發(fā)明作進(jìn)一步詳細(xì)的說明?,F(xiàn)有技術(shù)中,板料成形溫度為796℃:(1)1.5mm板料(裸板,板料成分見表1),在加熱爐中完成奧氏體化,加熱溫度為930℃,加熱時(shí)間5min;(2)加熱后的板料轉(zhuǎn)移(轉(zhuǎn)移時(shí)間為5s)至帶有冷卻水的模具上沖壓成形并保壓淬火,壓力為20mpa,保壓時(shí)間為10s。成形件的抗拉強(qiáng)度達(dá)1482mpa。實(shí)施例1:如圖1所示的一種穩(wěn)定降低熱成形溫度的工藝方法,如果采用箱式爐加熱,成形溫度要求低于700℃,本發(fā)明的具體實(shí)施步驟如下:步驟一:板料在加熱爐中奧氏體化,采用1.5mm板料(裸板,板料成分見表1),在第一個(gè)加熱爐中完成奧氏體化,加熱溫度為930℃,加熱時(shí)間5min;步驟二:板料預(yù)冷卻并保溫,步驟一加熱后的板料轉(zhuǎn)移至第二個(gè)箱式爐中進(jìn)行預(yù)降溫,保溫溫度設(shè)置800℃,保溫時(shí)間3min;步驟三:沖壓成形淬火,步驟二降溫后的板料轉(zhuǎn)移(轉(zhuǎn)移時(shí)間為5s)至帶有冷卻水的模具上沖壓成形并保壓淬火,壓力為20mpa,保壓時(shí)間為10s,成形件的抗拉強(qiáng)度達(dá)1480mpa,從而在保證高強(qiáng)度的前提下,穩(wěn)定降低成形件的成形溫度,成形件的微觀組織如圖2。實(shí)施例2:如圖1所示的一種穩(wěn)定降低熱成形溫度的工藝方法,如果選用輥底式加熱爐,成形溫度要求低于700℃,本發(fā)明的具體實(shí)施步驟如下:步驟一:板料在加熱爐中奧氏體化,采用1.5mm板料(裸板,板料成分見表1)在輥底爐的第一階段完成奧氏體化,加熱溫度為930℃,保溫5min;步驟二:板料預(yù)冷卻并保溫,經(jīng)步驟一完全奧氏體化后,第二階段的輥底爐設(shè)置800℃,料片在低溫爐內(nèi)緩慢移動(dòng),保溫時(shí)間3min;步驟三:沖壓成形淬火,經(jīng)步驟二降溫后的板料出爐轉(zhuǎn)移(轉(zhuǎn)移時(shí)間為5s)至有冷卻水的模具上沖壓成形并保壓淬火,壓力為20mpa,保壓時(shí)間為10s,成形件的抗拉強(qiáng)度達(dá)1476mpa,從而在保證高強(qiáng)度的前提下,穩(wěn)定降低成形件的成形溫度,成形件的微觀組織如圖3。上面已經(jīng)結(jié)合具體示例性實(shí)施例描述了本發(fā)明,但是本發(fā)明的實(shí)施不限于此。在本發(fā)明的精神和范圍內(nèi),本領(lǐng)域技術(shù)人員可以進(jìn)行各種修改和變型,這些修改和變型將落入權(quán)利要求限定的保護(hù)范圍之內(nèi)。本發(fā)明不局限于所述實(shí)施方式,任何人應(yīng)得知在本發(fā)明的啟示下作出的結(jié)構(gòu)變化,凡是與本發(fā)明具有相同或相近的技術(shù)方案,均落入本發(fā)明的保護(hù)范圍之內(nèi)。本發(fā)明未詳細(xì)描述的技術(shù)、形狀、構(gòu)造部分均為公知技術(shù)。當(dāng)前第1頁12