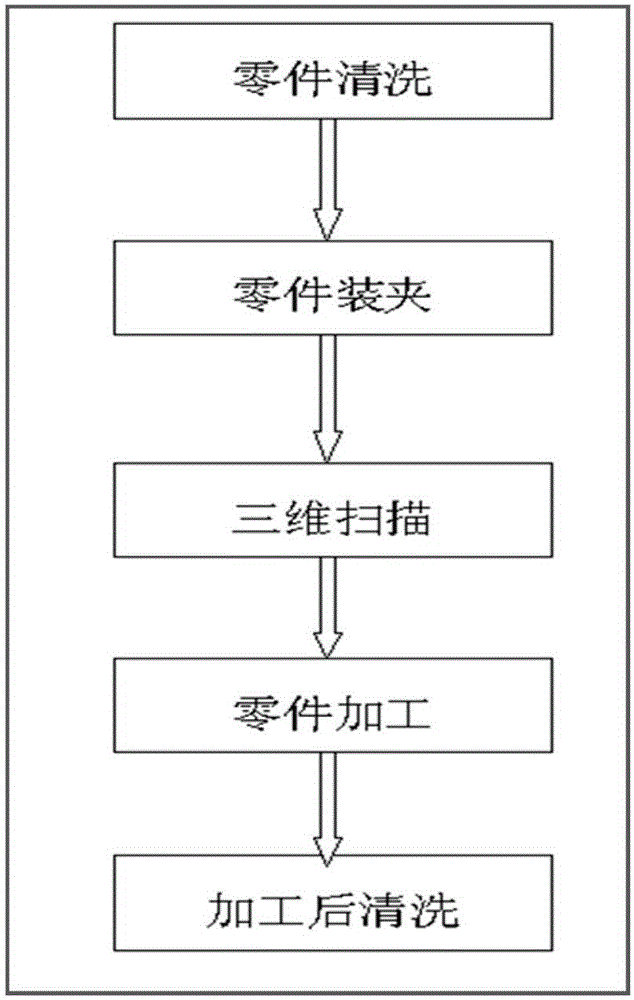
本發(fā)明涉及一種燃燒室噴油桿的加工工藝,具體地說是一種燃燒室噴油桿微孔冷成形工藝方法。
背景技術:
:隨著現(xiàn)代工業(yè)的發(fā)展,對資源節(jié)約和環(huán)境保護的要求越來越高,航空發(fā)動機燃燒室噴油桿決定著燃燒是否充分,能夠減少排污。用以前的工藝加工噴油桿,有毛刺,重鑄層,在燃燒時候容易產(chǎn)生積碳,導致燃燒室霧化效果不理想,輸出功不足;同時重鑄層也是疲勞源,導致零件壽命比較短。因此需要開發(fā)新的工藝技術解決上述問題。高精度超快激光微孔加工是主要發(fā)展方向之一,其加工的精細度和無熱效應方面遠遠高于其他技術,在加工微孔、微槽和切割方面的質(zhì)量參數(shù)也遠遠優(yōu)于機械加工和電火花加工技術,效率也高于電火花技術,是目前制造工藝發(fā)展的一個主流方向。技術實現(xiàn)要素:針對現(xiàn)有技術中燃燒室噴油桿有毛刺,重鑄層導致燃燒室霧化效果不理想或零件壽命短等不足,本發(fā)明要解決的問題是提供一種可提高霧化效果、使燃燒更充分并提高使用壽命的燃燒室噴油桿微孔冷成形工藝方法。為解決上述技術問題,本發(fā)明采用的技術方案是:本發(fā)明一種燃燒室噴油桿微孔冷成形工藝方法,包括以下步驟:零件裝夾:用定位銷將夾具在機床轉(zhuǎn)臺上進行準確定位并固定,根據(jù)夾具上的定位面和定位螺栓將零件進行定位并固定在夾具上;三維掃描:用Laserscan三維掃描模塊用測量激光頭對零件進行線掃描,確定零件的輪廓;掃描數(shù)據(jù)處理:對掃描數(shù)據(jù)進行點云處理,利用處理得到數(shù)據(jù)建立零件的坐標系,并導入零件理論圖紙坐標點與實際掃描測得點云數(shù)據(jù)進行孔位對正;生成機床加工坐標:加載測量系統(tǒng)標定、激光鉆頭標定文件,并導出機床加工坐標;孔焦點信息測量:在MMCPRO系統(tǒng)中讀取機床加工坐標調(diào)取焦距多孔測量程序,對各個孔的焦點信息進行確認;激光器參數(shù)設置:激光器的輸出功率為85%-98%,重復頻率為80kHz-100kHz;加工頭參數(shù)設置:選擇四光楔加工頭,對加工頭的參數(shù)工序進行設置并保存;孔加工:對Z軸單步進給量、掃描層數(shù)進行設置并保存,調(diào)取多孔加工程序,進行加工;加工后清洗:加工完后,將零件放入充滿煤油的超聲波槽內(nèi)進行清洗,并保存。加工頭的參數(shù)工序進行設置為:對激光頭加工參數(shù)工序一孔徑角度進行優(yōu)化,其中孔徑15-30DEG,工序一起始0-8DEG,旋轉(zhuǎn)速度2000-3000RPM,錐度控制量30-40mm。所述Z軸單步進給量設置為1-100um,掃描層數(shù)設置為200-600層。所述將零件放入充滿煤油的超聲波槽內(nèi)進行清洗為:進油嘴與清洗機相接,啟動設備進行超聲振動清洗,時間不少于10~20分鐘,保證內(nèi)外表面沒有臟物,取出零件,控凈內(nèi)腔余油。本發(fā)明還包括以下步驟:在零件超快激光制孔之前,零件表面需要預先處理,利用擦拭紙蘸取酒精將零件待加工位置進行清洗,并晾10~15分鐘。所有工藝步驟在萬級潔凈間中進行。本發(fā)明具有以下有益效果及優(yōu)點:1.本發(fā)明方法通過三維掃描快速獲取零件模型,得到需要加工孔的位置信息,由加工程序保證,確保加工孔的一致性,能有效解決電火花加工重鑄層、微裂紋等難題;通過超快激光加工,可有效防止出現(xiàn)重鑄層,微裂紋;2.本發(fā)明方法通過超快激光加工,單孔流量穩(wěn)定,可提高零件霧化效果。3.隨著設計對零件制孔要求的提高,要求無重鑄層、微裂紋,本發(fā)明可以解決噴油桿零件加工的新要求,滿足生產(chǎn)需要,可以推廣應用到航空發(fā)動機、燃氣輪機、汽車發(fā)動機等噴油桿零件上,應用前景廣闊。附圖說明圖1為本發(fā)明方法中應用的超短脈沖激光加工原理圖;圖2為本發(fā)明方法工藝流程圖。具體實施方式下面結合說明書附圖對本發(fā)明作進一步闡述。如圖1所示,本發(fā)明一種燃燒室噴油桿微孔冷成形工藝方法,其特征在于包括以下步驟:(1)零件裝夾:找到機床轉(zhuǎn)臺定位孔,用定位銷進行將夾具在轉(zhuǎn)臺進行準確定位并固定,根據(jù)夾具上的定位面和定位螺栓將零件進行定位并固定在夾具上;(2)三維掃描:用Laserscan三維掃描模塊用測量激光頭線掃描對零件進行掃描,確定零件的輪廓;(3)掃描數(shù)據(jù)處理:接著對掃描數(shù)據(jù)進行點云處理,利用處理得到數(shù)據(jù)建立零件的坐標系,并導入零件理論圖紙坐標點與實際掃描測得點云數(shù)據(jù)進行孔位對正;(4)生成機床加工坐標:接著加載測量系統(tǒng)標定、激光鉆頭標定文件,并導出機床加工坐標;(5)孔焦點信息測量:接著在MMCPRO系統(tǒng)中讀取機床加工坐標調(diào)取焦距多孔測量程序,對各個孔的焦點信息進行確認;(6)激光器參數(shù)設置:激光器的輸出功率為85%-98%,重復頻率為80kHz-100kHz;(7)加工頭參數(shù)設置:選擇四光楔加工頭,對加工頭的參數(shù)工序一孔徑15-30DEG,工序一起始0-8DEG,旋轉(zhuǎn)速度2000-3000RPM進行設置并保存,錐度控制量30-40mm;(8)孔加工:對Z軸單步進給量1-100um、掃描層數(shù)200-600層進行設置并保存,接著調(diào)取多孔加工程序,進行加工;(9)加工后清洗:加工完后,將零件放入充滿煤油的超聲波槽內(nèi)進行清洗,并保存。本發(fā)明流程步驟如圖2所示。本發(fā)明在零件超快激光制孔之前,零件表面需要預先處理:利用擦拭紙蘸取酒精將零件待加工位置進行清洗,并晾10~15分鐘。零件表面預先處理中清洗的目的是為保證工件上不殘留有機加冷卻液等臟污;目的是為了便于零件定位準確、零件型面三維掃描精度高、防止臟污影響激光能量吸收。本發(fā)明零件超快激光制孔,需要根據(jù)零件種類選擇不同的工藝參數(shù),用優(yōu)化后的參數(shù)進行加工。如步驟(7)~(9)所述,不同零件孔的加工要求,在定位準確的前提下,由激光器參數(shù)、加工頭參數(shù),Z軸進給量、掃描層數(shù)等決定。本發(fā)明在零件超快激光制孔后,需對工件進行清洗:完工后,將零件再次用煤油進行清洗,并保存,目的是為了將激光打孔的粉末清洗干凈,以免影響裝配后影響之后的霧化效果。本發(fā)明超快激光的燃燒室噴油桿微孔冷成形較優(yōu)條件為:零件三維掃描形貌時對零件進行分段掃描,步進0.1mm;激光器參數(shù)進行設置激光器的輸出功率為95%,重復頻率為100kHz;接著選擇四光楔加工頭,對加工頭的參數(shù)工序一孔徑20DEG,工序一起始5DEG,旋轉(zhuǎn)速度2400RPM進行設置并保存,錐度控制量40mm;接著對Z軸單步進給量5um、掃描層數(shù)500層進行設置并保存。本發(fā)明工藝方法所有步驟均在萬級潔凈間(又稱為無塵室或清凈室)中進行,根據(jù)GB/T16292-1996,空氣潔凈度分級標準如表1:表1GB/T16292-1996中空氣潔凈度分級標準為了減少燃燒室噴油桿孔加工后的毛刺、微裂紋和重鑄層,本發(fā)明提出了超快激光的燃燒室噴油桿微孔冷成形工藝方法,超快激光(即超短脈沖激光,其加工原理圖如圖1所示)是指P秒、飛秒激光,激光的脈寬短10-12s、10-15s量級,瞬時能量的注入,使得能量瞬間沉積在固體物質(zhì)的趨膚層內(nèi),將固體材料直接汽化;超快激光的作用時間短,使得能量以等離子體的形式被迅速帶走,熱量來不及在材料內(nèi)部擴散,是一個冷加工的過程,可視作無熱影響區(qū);無材料損傷,在整個加工過程中,材料的去除方式以蒸發(fā)和汽化的形式進行,無熔融相,因此沒有重熔層和微裂紋的形成;無飛濺物存在。由于瞬時汽化,材料以氣體形式瞬間蒸發(fā),材料表面沒有任何飛濺物,大大提高了加工材料表面的粗糙度。零件在放入充滿煤油的超聲波槽內(nèi)進行清洗,進油嘴與清洗機相接,啟動設備進行超聲振動清洗,時間不少于10~20分鐘,保證內(nèi)外表面沒有臟物,取出零件,控凈內(nèi)腔余油。實施例1試件材料:長度為55mm、直徑為6mm的GH3536零件6個(編號1~6);利用酒精將零件待加工位置進行清洗,并晾干;找到機床轉(zhuǎn)臺定位孔,用定位銷進行將夾具在轉(zhuǎn)臺進行準確定位并固定,根據(jù)夾具上的定位面和定位螺栓將零件進行定位并固定在夾具上;用Laserscan三維掃描模塊用測量激光頭線掃描對零件進行分段掃描,步進0.1mm;接著加載測量系統(tǒng)標定、激光鉆頭標定文件,并導出機床加工坐標;然后在MMCPRO系統(tǒng)中讀取機床加工坐標調(diào)取焦距多孔測量程序,對各個孔的焦點信息進行確認;激光器參數(shù)進行設置激光器的輸出功率為95%,重復頻率為100kHz;接著選擇四光楔加工頭,對加工頭的參數(shù)工序一孔徑20DEG,工序一起始5DEG,旋轉(zhuǎn)速度2400RPM進行設置并保存,錐度控制量40mm;接著對Z軸單步進給量5um、掃描層數(shù)500進行設置并保存,調(diào)取多孔加工程序,進行加工。加工完后,將零件放入充滿煤油的超聲波槽內(nèi),進油嘴與清洗機相接,啟動設備進行超聲振動清洗,時間不少于10分鐘,保證內(nèi)外表面沒有贓物。取出零件,控凈內(nèi)腔余油。對零件進行流量試驗及理化檢測。實施例2試件材料:長度為55mm、直徑為6mm的GH3625零件6個(編號6~12);利用酒精將零件待加工位置進行清洗,并晾干;找到機床轉(zhuǎn)臺定位孔,用定位銷進行將夾具在轉(zhuǎn)臺進行準確定位并固定,根據(jù)夾具上的定位面和定位螺栓將零件進行定位并固定在夾具上;用Laserscan三維掃描模塊用測量激光頭線掃描對零件進行分段掃描,步進0.1mm;接著加載測量系統(tǒng)標定、激光鉆頭標定文件,并導出機床加工坐標;然后在MMCPRO系統(tǒng)中讀取機床加工坐標調(diào)取焦距多孔測量程序,對各個孔的焦點信息進行確認;激光器參數(shù)進行設置激光器的輸出功率為95%,重復頻率為100kHz;接著選擇四光楔加工頭,對加工頭的參數(shù)工序一孔徑20DEG,工序一起始5DEG,旋轉(zhuǎn)速度2400RPM進行設置并保存,錐度控制量40mm;接著對Z軸單步進給量5um、掃描層數(shù)500進行設置并保存,調(diào)取多孔加工程序,進行加工。加工完后,將零件放入充滿煤油的超聲波槽內(nèi),噴桿與清洗機相接,啟動設備進行超聲振動清洗,時間不少于10分鐘,保證內(nèi)外表面沒有贓物。取出零件,控凈內(nèi)腔余油。對零件進行流量試驗及理化檢測。將實施例1、2的噴桿進行霧化效果檢測試驗結果如下:當壓力P為固定值時,噴桿上單孔流量為43.56~46.24L/h。表2流量試驗檢測結果序號測得值設計要求值實施例1-145.13L/h43.56~46.24L/h實施例1-245.23L/h43.56~46.24L/h實施例1-345.18L/h43.56~46.24L/h實施例1-445.25L/h43.56~46.24L/h實施例1-545.16L/h43.56~46.24L/h實施例1-645.20L/h43.56~46.24L/h實施例2-745.21L/h43.56~46.24L/h實施例2-845.24L/h43.56~46.24L/h實施例2-945.37L/h43.56~46.24L/h實施例2-1045.22L/h43.56~46.24L/h實施例2-1145.14L/h43.56~46.24L/h實施例2-1245.16L/h43.56~46.24L/h將實施例1、2的噴桿進行理化檢測結果如下:表3理化檢測結果根據(jù)表2,表3試驗結果可知超快激光加工不同材料的噴油桿,流量檢測符合設計要求并且流量值穩(wěn)定,無重鑄層,微裂紋。當前第1頁1 2 3