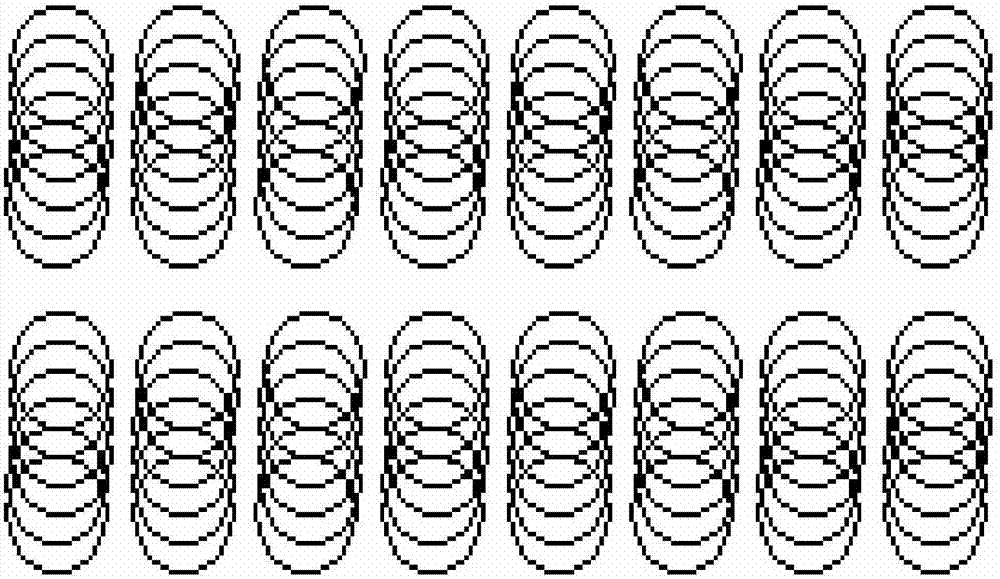
本發(fā)明涉及光纖連接器加工技術(shù)領(lǐng)域,具體是指一種零損耗光纖連接器的制作方法。
背景技術(shù):隨著大數(shù)據(jù)時代到來,數(shù)據(jù)傳輸量越來越大,對光纖互連質(zhì)量要求越來越高。光纖互連性能直接影響網(wǎng)絡(luò)傳輸品質(zhì)。一個常見現(xiàn)象:運(yùn)營商承諾用戶端帶寬10Mbps,然而實(shí)際網(wǎng)速卻僅有5到6Mbps,這代表中間傳輸環(huán)節(jié)有大量的傳輸損耗。在光纖鋪設(shè)環(huán)節(jié)上,光纖互連的光功率損耗(powerloss)會造成接收端的誤碼(biterror),從而增加了傳輸?shù)难舆t(latency),拖累實(shí)際網(wǎng)速。從電信機(jī)房主干網(wǎng)到用戶端,需要多級光纖連接器連接。以目前光纖連接器生產(chǎn)工藝,大部分接入損耗約在0.25到0.5dB,即單次連接的光功率損耗即為5.6%到10.9%。經(jīng)過多次分支連接,傳輸光功率損耗越來越大,造成誤碼、誤幀(frameerror)現(xiàn)象愈趨嚴(yán)重,進(jìn)而拉低傳輸速率,此為我國網(wǎng)路帶寬和實(shí)際網(wǎng)速存在落差的最根本原因。國際電工委員會(IEC)對光纖連接器的光學(xué)性能定義三個級別:B級隨機(jī)互配(randommating)接入損耗平均值≤0.12dB,最大值≤0.25dB;C級平均值≤0.25dB,最大值≤0.5dB;D級平均值≤0.5dB,最大值≤1dB。隨著超高速網(wǎng)路逐漸興起,IEC正著手制定A級標(biāo)準(zhǔn)。國內(nèi)大部分廠商生產(chǎn)的光纖連接器處于C到D級水平。國外僅有數(shù)家技術(shù)領(lǐng)先公司如:瑞士Reichle&De-Massari、瑞士Diamond、日本住友等生產(chǎn)的光纖連接器可優(yōu)于B級水平,插入損耗平均值約在0.07到0.1dB,然而價格十分高昂,產(chǎn)量亦少。傳統(tǒng)的光纖連接器制造工藝存在光纖損傷風(fēng)險、良率難控制以及生產(chǎn)效率低等問題。且大部分光纖連接器插入損耗為0.25到0.5dB,很難有突破。特別在以下幾方面,傳統(tǒng)工藝存在嚴(yán)重問題:1.傳統(tǒng)工藝在一些關(guān)鍵工序上仍以不合理的工具操作,人為因素決定了產(chǎn)品質(zhì)量。例如:傳統(tǒng)工藝以米勒鉗剝除光纖外被,若光纖外被材料較硬,或光纜包覆力較緊,或處于溫度較低的環(huán)境,采用米勒鉗便不易剝除表面外被,而強(qiáng)力剝除會造成光纖損傷。當(dāng)光通過表面損傷光纖時,光會穿透損傷表面,產(chǎn)生功率損耗。在其它工具使用上,傳統(tǒng)工藝也存在損傷光纖的問題。2.光纖研磨(polishing)是光纖連接器生產(chǎn)的重要工序。傳統(tǒng)研磨工藝是以“8”形狀的路徑研磨,如圖1所示,每個連接器的研磨路徑是相互重疊的,研磨產(chǎn)生的粉末會相互影響。因此傳統(tǒng)工藝制造的光纖連接器的3D性能(end-facegeometry)較差,在角度(APCangle)、偏心量(apexoffset)和曲率半徑(radiusofcurvature)上,無法達(dá)到較好的一致性。另外在光學(xué)端面的光潔度上,均有輕微的劃痕、刮傷及其它缺陷。這些都是影響光纖連接器光學(xué)性能的重要因素,然而采用傳統(tǒng)研磨工藝無法徹底改善,造成光學(xué)性能的瓶頸,難以突破。3.光纖連接器之于寬帶網(wǎng)路,就像螺絲之于工業(yè),看似平凡的零件,要批量做到頂尖品質(zhì),卻非常困難。傳統(tǒng)上,生產(chǎn)光纖連接器很難有效控制質(zhì)量,主因在于:光纖本身材質(zhì)是玻璃,需精巧處理,而自動化生產(chǎn)光纖連接器經(jīng)數(shù)十年發(fā)展仍存在諸多限制,因此目前仍須仰賴人工,避免不了人為因素造成的質(zhì)量問題。
技術(shù)實(shí)現(xiàn)要素:針對以上技術(shù)問題,本發(fā)明的目的是提供一種零損耗光纖連接器的制作方法,具有品質(zhì)一致性好、品質(zhì)隱患低、生產(chǎn)效率高、光學(xué)性能優(yōu)異、信號傳輸損耗低、綜合性能良好和成本低廉的特點(diǎn)。對此,本發(fā)明采用的技術(shù)方案為:本發(fā)明公開了一種零損耗光纖連接器的制作方法,包括以下步驟:步驟S1:裁線處理,采用自動裁線機(jī)裁取規(guī)格長度的光纜。在裁線處理過程中,由于光纜有多種長度規(guī)格,為方便區(qū)別,采用直觀的顏色識別方法:不同長度光纜綁定對應(yīng)顏色束帶。顏色識別法較為直觀、可有效檢查和追溯生產(chǎn)過程。步驟S2:前段組裝,把光纖連接器的尾套、束環(huán)、螺帽、套頭座和彈簧預(yù)安裝在裁線處理得到的光纜上并用束帶固定,以防止脫落,然后進(jìn)行剝外被、拉線、削外被操作。步驟S3:光纖固化,把完成前段組裝的光纖在光纖熱剝后進(jìn)行光纖穿入操作,將光纖穿入插芯內(nèi),然后進(jìn)行烘烤定型固化;步驟S4:后段組裝,把完成光纖固化后的光纜進(jìn)行束環(huán)預(yù)裝、鉚壓、內(nèi)框組裝和外框組裝得到光纖連接器初產(chǎn)品;步驟S5:去膠處理,把后段組裝完成后的光纖連接器初產(chǎn)品采用自動研磨去膠機(jī),配有雙工位夾頭,可實(shí)現(xiàn)交替研磨去膠處理;步驟S6:研磨處理,把完成去膠處理的光纖連接器初產(chǎn)品通過研磨夾具進(jìn)行獨(dú)立加壓方式按照螺旋旋轉(zhuǎn)的軌跡進(jìn)行分工序研磨,在分工序研磨的過程中漸進(jìn)式采用在磨料粒度上從大顆粒到小顆粒的研磨片把所述光纖連接器初產(chǎn)品固定在所述研磨夾具進(jìn)而使用不同的研磨機(jī)上進(jìn)行研磨得到最終的光纖連接器產(chǎn)品。通過設(shè)置彼此獨(dú)立的連接器固定座和采用螺旋旋轉(zhuǎn)方式的軌跡進(jìn)行研磨,不同光纖連接器在研磨過程中不重疊,每個連接器研磨過程中產(chǎn)生的臟污和粉末不影響到相鄰的光纖連接器,有效避免傳統(tǒng)研磨工藝是以“8”形狀的路徑研磨,每個光纖連接器的研磨路徑是相互重疊的,研磨產(chǎn)生的粉末會相互影響的缺陷,有效提高了光纖連接器的性能。通過采用把研磨夾具固定在不同研磨機(jī)實(shí)現(xiàn)不同的研磨工序,每道研磨工序配置專門的研磨機(jī)。與傳統(tǒng)的研磨工藝是每研磨完一道工序就需要更換一次研磨墊相比,傳統(tǒng)的研磨工藝更換研磨墊時需要將底盤擦拭干凈防止底盤上的臟污造成研磨片的不平,此種做法浪費(fèi)時間,生產(chǎn)效率低。而本發(fā)明采用每道研磨工序?qū)?yīng)專門研磨機(jī)的方式,不但節(jié)省了更換研磨墊的時間,而且研磨墊與研磨機(jī)的底盤是連接裝配,保證了機(jī)臺的平面度。進(jìn)一步地,步驟S6所述研磨處理的研磨夾具包括夾具大本體、若干個小本體組件和設(shè)置在夾具大本體上的蓋板,所述夾具大本體和所述蓋板之間設(shè)有若干彼此獨(dú)立平行的立柱孔,所述夾具大本體上均設(shè)有若干個小本體組件,所述小本體組件上設(shè)有導(dǎo)向的小本體立柱,所述小本體立柱頂部通過單向螺絲活動固定在所述立柱孔,所述單向螺絲設(shè)置在所述蓋板上,所述小本體立柱上嵌套有上下活動移動的施壓彈簧。通過在小本體立柱上設(shè)置施壓彈簧,從而實(shí)現(xiàn)光纖連接器在研磨的過程中保持固定的壓力,保證了光纖連接器研磨后品質(zhì)的一致性。進(jìn)一步地,步驟S2所述前段組裝的剝外被采用帶有長度裝置的剝外被治具進(jìn)行,所述凱芙拉線采用帶有顏色墊片標(biāo)識的凱夫拉剪刀進(jìn)行剪短處理,所述削外被采用削外被治具通過上下兩塊刀片加緊后縱削進(jìn)行。用帶有長度裝置的剝外被治具操作時只需將光纜頂?shù)焦潭ㄎ恢镁涂蓜兂獗?。剝離后的長度具一致性,生產(chǎn)效率高;相比傳統(tǒng)工藝未有定位長度治具,易造成裁剪長度不一,需在后段組裝過程中重新修正,也存在抗拉強(qiáng)度不牢的問題。通過凱芙拉剪刀裝有不同厚度的顏色墊片(圖2),可精確、直觀控制凱芙拉線的裁剪長度。削外被治具采用上下兩塊刀片加緊后縱削,刀片的凸出長度根據(jù)光纜的外被厚度自由調(diào)節(jié)??v向削的速度快,不傷到光纜的內(nèi)芯。進(jìn)一步地,步驟S3所述光纖固化的步驟為:先將光纖外被和涂覆層進(jìn)行加熱軟化后剝離,剝離力度是輕微的,可避免損傷光纖包層。光纖熱剝完成后用手指輕微彎曲光纖,以再次檢測確認(rèn)光纖無損傷,光纖穿入是先用擦拭紙蘸酒精擦拭清潔光纖表面,然后將光纖穿入插芯內(nèi),最后置于烤爐上進(jìn)行烘烤。為避免外界環(huán)境對烤膠的影響,烤爐上有專門的防護(hù)蓋以阻斷外界氣流。進(jìn)一步地,步驟S4所述后段組裝的步驟為:將凱芙拉線和外被用束環(huán)和螺帽預(yù)固定在套頭座;在預(yù)裝前,使用慢干的混合AB膠涂在凱芙拉線上并進(jìn)行鉚壓;然后采用內(nèi)框組裝工具把固化后的光纖插芯固定連接在套頭座上得到光纖連接器初產(chǎn)品。傳統(tǒng)工藝多采用快干膠。快干膠是瞬時硬化,應(yīng)力并未得到完全釋放就開始鉚壓,會造成最終產(chǎn)品抗拉強(qiáng)度降低、質(zhì)量不穩(wěn)定。而采用慢干的混合AB膠,是在鉚壓6小時后才硬化,應(yīng)力釋放、縫隙填充都加強(qiáng)了抗拉強(qiáng)度。內(nèi)框組裝采用內(nèi)框組裝工具,工具輕巧、易于安裝;而傳統(tǒng)的內(nèi)框組裝采用手工組裝,需用力推進(jìn),會造成未安裝到位的不良,且容易出現(xiàn)操作疲勞,采用組裝工具后,可快速組裝,效率提高50%、且可起到防呆作用。進(jìn)一步地,所述夾具本體與所述研磨機(jī)導(dǎo)軌座之間設(shè)有墊片,所述墊片的厚度根據(jù)研磨片的使用時間和研磨機(jī)導(dǎo)軌座的高度進(jìn)行調(diào)整。通過采用不同厚度的墊片可以實(shí)現(xiàn)控制研磨壓力的目的。新使用的研磨片在輕壓力之下即可達(dá)到較好的研磨效果。但隨著時間的推移,研磨片的研磨顆粒被磨損,需要加大研磨壓力才可達(dá)到研磨效果。通過分工序?qū)ρ心|片進(jìn)行固定厚度的量化和標(biāo)準(zhǔn)化,可以實(shí)現(xiàn)研磨壓力的量化,相比常規(guī)的研磨工藝部分采用固定壓力研磨,部分采用旋鈕調(diào)節(jié)壓力而言,傳統(tǒng)的兩種都不能實(shí)現(xiàn)研磨壓力的量化式可調(diào)節(jié),不能最有效率地利用研磨片壓力的控制精度和靈活度,與本發(fā)明的控制方式存在較大的差距。進(jìn)一步地,所述研磨夾具上設(shè)有定位孔,APC型光纖連接器使用的研磨夾具小本體組件的定位孔采用8.15度傾斜;所述PC型光纖連接器使用的研磨夾具小本體組件的定位孔采用0度垂直。8.15度傾斜是為了彌補(bǔ)連接器的研磨曲率造成的偏移,3D方面可獲得較好的8度角,進(jìn)而使得光學(xué)的回波損耗(returnloss)得到提升。進(jìn)一步地,所述APC型和PC型光纖連接器分工序研磨過程中各個工序磨料的粒度依次為:30μm、30μm、15μm、9μm、1μm、ADS,所述不同工序研磨的時間為30s。與傳統(tǒng)研磨工藝的相比,傳統(tǒng)的研磨工藝磨料粒度包括15μm、1μm和ADS,本發(fā)明的研磨工序比傳統(tǒng)的研磨工序多出三道。六道研磨的各工序研磨時間僅30秒,多道短時間工序的研磨工藝,可及時地清除研磨產(chǎn)生的顆粒粉末,延長研磨片的使用時間以及提升研磨質(zhì)量,有效避免研磨的時間長產(chǎn)生粉末多,造成清潔不干凈研磨后的連接器損耗增大的弊端進(jìn)一步地,所述研磨夾具在完成研磨后使用水洗研磨端面并用高壓氣槍清除臟污。在實(shí)際中,水洗是采用溫度30℃的中度水溫清潔,只清潔研磨夾具前端凸出的插芯,避免水污染到光纖連接器的其它部分。進(jìn)一步地,所述的研磨夾具小本體組件設(shè)有可左右扳動的旋轉(zhuǎn)扳手。當(dāng)扳手旋轉(zhuǎn)至最左邊時,可以快速地插入連接器到夾具上。當(dāng)扳手向右旋轉(zhuǎn),螺絲旋進(jìn)固定夾緊連接器。研磨完成后,拆卸光纖連接器時,只需將扳手向左邊旋轉(zhuǎn)即可拆卸。采用帶旋轉(zhuǎn)扳手的螺絲固定,光纖連接器拆卸方便,且可牢固地固定光纖連接器,避免在研磨時可能出現(xiàn)的縮頭現(xiàn)象。進(jìn)一步地,所述研磨夾具采用高定位框的方式。所述定位框上設(shè)有凹形定位框鍵槽,所述定位框鍵槽對應(yīng)光纖連接器的光纖連接器卡點(diǎn),防止連接器裝反以及角度偏轉(zhuǎn),從而保證3D的key值在0.05度范圍內(nèi)。本發(fā)明一種零損耗光纖連接器的制作方法,具有如下的有益效果:第一,品質(zhì)一致性優(yōu),通過劃分工序,對獨(dú)立的工序進(jìn)行精細(xì)化操作,采用對應(yīng)的治具和裝置保證過程過程的一致性,減少人為對光纖連接器品質(zhì)一致性的影響;第二,品質(zhì)隱患低,不同的工序均采用對應(yīng)的治具進(jìn)行加工操作,同時在加工治具中注重區(qū)分和品質(zhì)防護(hù),有效降低光纖連接器的品質(zhì)隱患;第三,生產(chǎn)效率高,通過劃分工序進(jìn)行精細(xì)化生產(chǎn),實(shí)現(xiàn)標(biāo)準(zhǔn)化作業(yè)流程,實(shí)現(xiàn)流水線柔性作業(yè),有效提高了生產(chǎn)效率;第四,光學(xué)性能優(yōu)異,本發(fā)明制作方法制備的光纖連接器在插入損耗和回波損耗方面均符合國際IEC規(guī)范的性能要求,甚至諸如在隨機(jī)互配的插入損耗和回波損耗均高于國際IEC規(guī)范的要求;第五,信號傳輸損耗低,本發(fā)明制備所得的光纖連接器其曲率半徑、光纖高度、偏心量和APC角度相比國際IEC規(guī)范更嚴(yán)格,有效降低信號傳輸?shù)膿p耗;第六,綜合性能良好,本發(fā)明所述光纖連接器進(jìn)行機(jī)械性能、環(huán)境性能測試,測試結(jié)果表明本發(fā)明所生產(chǎn)光纖連接器已通過美國貝爾實(shí)驗(yàn)室TelcordiaGR-326-CORE測試;第七,生產(chǎn)成本低廉,在實(shí)際生產(chǎn)過程中,采用本發(fā)明制作方法的生產(chǎn)直通率達(dá)到100%,有效提高了物料利用率,降低了生產(chǎn)制造成本。附圖說明圖1為現(xiàn)有技術(shù)研磨軌跡示意圖(十六工位)。圖2為本發(fā)明一種零損耗光纖連接器的制作方法的研磨軌跡示意圖(十六工位)。圖3為本發(fā)明一種零損耗光纖連接器的制作方法的研磨夾具立體組裝結(jié)構(gòu)示意圖。圖4為本發(fā)明一種零損耗光纖連接器的制作方法的研磨夾具組裝正視圖。圖5為本發(fā)明一種零損耗光纖連接器的制作方法的研磨夾具大本體。圖6為本發(fā)明一種零損耗光纖連接器的制作方法的小本體結(jié)構(gòu)圖。圖7為本發(fā)明一種零損耗光纖連接器的制作方法的光纖連接器插入小本體示意圖。圖中的標(biāo)記包括:1、夾具大本體,2、小本體立柱,3、施壓彈簧,4、單向螺絲,5、小本體固定座,6、定位孔,7、旋轉(zhuǎn)扳手,8、蓋板,9、定位框,10、立柱孔,11、擋柱,12、光纖連接器,13、光纖連接器卡點(diǎn),14、定位框鍵槽,15、光纖連接器插芯、16、小本體組件。具體實(shí)施方式為了使本技術(shù)領(lǐng)域的人員更好地理解本發(fā)明的技術(shù)方案,下面結(jié)合實(shí)施例及附圖對本發(fā)明產(chǎn)品作進(jìn)一步詳細(xì)的說明。實(shí)施例1一種零損耗光纖連接器的制作方法,其特征在于包括以下步驟:第一步:裁線處理,采用自動裁線機(jī)裁取規(guī)格長度的光纜;第二步:前段組裝,把光纖連接器的尾套、束環(huán)、螺帽、套頭座和彈簧預(yù)安裝在裁線處理得到的光纜上并用束帶固定,然后進(jìn)行剝外被、剪凱芙拉線、削外被操作,剝外被采用帶有長度裝置的剝外被治具進(jìn)行,所述凱芙拉線線采用帶有顏色墊片標(biāo)識的凱夫拉剪刀進(jìn)行剪短,所述削外被采用削外被治具通過上下兩塊刀片加緊后縱削進(jìn)行;第三步:光纖固化,把完成前段組裝的光纖的外被和涂覆層進(jìn)行加熱軟化后剝離,光纖熱剝完成后用手指輕微彎曲光纖,再用擦拭紙蘸酒精擦拭清潔光纖表面,然后將光纖穿入插芯內(nèi),最后置于烤爐上進(jìn)行烘烤固化定型;第四步:后段組裝,把完成光纖固化后的光纜進(jìn)行束環(huán)預(yù)裝、鉚壓、內(nèi)框組裝和外框組裝得到光纖連接器初產(chǎn)品。具體步驟為:將凱芙拉線和外被用束環(huán)和螺帽預(yù)固定在套頭座;在預(yù)裝前,使用慢干的混合AB膠涂在凱芙拉線上并進(jìn)行鉚壓;然后采用內(nèi)框組裝工具把固化后的光纖插芯固定連接在套頭座上得到光纖連接器初產(chǎn)品;第五步:去膠處理,把后段組裝完成后的光纖連接器初產(chǎn)品采用自動研磨去膠機(jī),配有雙工位夾頭,可實(shí)現(xiàn)交替研磨去膠處理;第六步:研磨處理,把完成去膠處理的光纖連接器初產(chǎn)品通過研磨夾具進(jìn)行獨(dú)立加壓方式按照螺旋旋轉(zhuǎn)的軌跡進(jìn)行分工序研磨,在分工序研磨的過程中漸進(jìn)式地采用在磨料粒度上從大顆粒到小顆粒的研磨片把所述光纖連接器初產(chǎn)品固定在所述研磨夾具進(jìn)而使用不同的研磨機(jī)上進(jìn)行研磨得到最終的光纖連接器產(chǎn)品。實(shí)施例2一種零損耗光纖連接器的制作方法,在第六步所述研磨處理中,所述光纖連接器通過研磨夾具進(jìn)行獨(dú)立加壓方式進(jìn)行分工序研磨:如圖3、圖4、圖5、圖6和圖7所示,所述研磨夾具包括夾具大本體1、若干個小本體組件16和設(shè)置在夾具大本體1上的蓋板8,所述夾具大本體1和所述蓋板8之間設(shè)有若干彼此獨(dú)立平行的立柱孔10,所述夾具大本體上均設(shè)有若干個小本體組件16,所述小本體組件16上設(shè)有導(dǎo)向的小本體立柱2,所述小本體立柱2頂部通過單向螺絲4活動固定在所述立柱孔10,所述單向螺絲4設(shè)置在所述蓋板8上,所述小本體立柱2上嵌套有上下活動移動的施壓彈簧3。如圖2所示,所述研磨夾具進(jìn)行獨(dú)立加壓研磨的軌跡采用螺旋旋轉(zhuǎn)方式進(jìn)行研磨。在本實(shí)施例中,所述光纖連接器為APC型。所述研磨夾具上設(shè)有定位孔6,APC型光纖連接器使用的研磨夾具小本體組件16的定位孔6采用8.15度傾斜。所述分工序研磨漸進(jìn)式地采用在磨料粒度上從大顆粒到小顆粒的研磨片把所述光纖連接器固定在所述研磨夾具進(jìn)而使用不同的研磨機(jī)上進(jìn)行研磨。具體為所述APC型光纖連接器分工序研磨過程中各個工序磨料的粒度依次為:30μm、30μm、15μm、9μm、1μm、ADS,所述不同工序研磨的時間為30s。所述夾具本體1與所述研磨機(jī)導(dǎo)軌座之間設(shè)有墊片,所述墊片的厚度根據(jù)分工序研磨的不同工序磨料粒度的降低逐漸減小。所述研磨夾具在完成研磨后使用水洗研磨端面并用高壓氣槍清除臟污。所述的研磨夾具小本體組件16設(shè)有可左右扳動的旋轉(zhuǎn)扳手7。所述研磨夾具采用高定位框9的方式。所述定位框9上設(shè)有凹形定位框鍵槽14,所述定位框鍵槽14對應(yīng)光纖連接器12的光纖連接器卡點(diǎn)13。實(shí)施例3一種零損耗光纖連接器的制作方法,在第六步所述研磨處理中,所述光纖連接器通過研磨夾具進(jìn)行獨(dú)立加壓方式進(jìn)行分工序研磨:如圖3、圖4、圖5、圖6和圖7所示,所述研磨夾具包括夾具大本體1、若干個小本體組件16和設(shè)置在夾具大本體1上的蓋板8,所述夾具大本體1和所述蓋板8之間設(shè)有若干彼此獨(dú)立平行的立柱孔10,所述夾具大本體上均設(shè)有若干個小本體組件16,所述小本體組件16上設(shè)有導(dǎo)向的小本體立柱2,所述小本體立柱2頂部通過單向螺絲4活動固定在所述立柱孔10,所述單向螺絲4設(shè)置在所述蓋板8上,所述小本體立柱2上嵌套有上下活動移動的施壓彈簧3。如圖2所示,所述研磨夾具進(jìn)行獨(dú)立加壓研磨的軌跡采用螺旋上升方式進(jìn)行研磨。在本實(shí)施例中,所述光纖連接器為PC型。所述研磨夾具上設(shè)有定位孔6,所述PC型光纖連接器使用的研磨夾具小本體組件16的定位孔6采用0度垂直。所述分工序研磨采用在磨料粒度上從大顆粒到小顆粒的漸進(jìn)式研磨片把所述光纖連接器固定在所述研磨夾具進(jìn)而使用不同的研磨機(jī)上進(jìn)行研磨。所述夾具本體1與所述研磨機(jī)導(dǎo)軌座之間設(shè)有墊片,所述墊片的厚度根據(jù)分工序研磨的不同工序磨料粒度的降低逐漸減小。所述研磨夾具在進(jìn)完成研磨后使用水洗研磨端面并用高壓氣槍清除臟污。所述的研磨夾具小本體組件16設(shè)有可左右扳動的旋轉(zhuǎn)扳手7。所述研磨夾具采用高定位框9的方式。所述定位框9上設(shè)有凹形定位框鍵槽14,所述定位框鍵槽14對應(yīng)光纖連接器12的光纖連接器卡點(diǎn)13。與此同時,為了驗(yàn)證本發(fā)明所述制作方法對光纖連接器性能提升的效果,采用本發(fā)明制作方法所得的光纖連接器進(jìn)行光學(xué)性能、3D性能和測試和端面性能測試,并把具體測試結(jié)果與國際IEC規(guī)范比對,具體測試結(jié)果如所示:表1光學(xué)性能測試結(jié)果從表1可以看到,本發(fā)明制作方法制備的光纖連接器在插入損耗和回波損耗方面均符合國際IEC規(guī)范的性能要求,甚至諸如在隨機(jī)互配的插入損耗和回波損耗均優(yōu)于國際IEC規(guī)范的要求。如表2所示,本發(fā)明制備所得的光纖連接器其曲率半徑、光纖高度、偏心量和APC角度相比國際IEC規(guī)范更優(yōu),有效降低信號傳輸?shù)膿p耗。表23D性能測試結(jié)果端面性能測試采用400倍顯微鏡觀察端面的劃痕、麻點(diǎn)等外觀缺陷。從表3可以看到,本發(fā)明所制備的光纖連接器產(chǎn)品在端面性能上相比于國際IEC規(guī)范而言,其各項(xiàng)指標(biāo)遠(yuǎn)遠(yuǎn)優(yōu)于國際IEC規(guī)范的指標(biāo)要求。表3端面性能測試結(jié)果與此同時,本發(fā)明所述光纖連接器同時也進(jìn)行了機(jī)械性能、環(huán)境性能測試,測試結(jié)果表明本發(fā)明所生產(chǎn)光纖連接器已通過美國貝爾實(shí)驗(yàn)室TelcordiaGR-326-CORE測試,而常規(guī)工藝無法通過。在實(shí)際生產(chǎn)過程中,采用本發(fā)明制作方法的生產(chǎn)直通率達(dá)到100%,有效提高了物料利用率,降低了生產(chǎn)制造成本。以上所述,僅為本發(fā)明的較佳實(shí)施例而已,并非對本發(fā)明作任何形式上的限制;凡本行業(yè)的普通技術(shù)人員均可按說明書附圖所示和以上所述而順暢地實(shí)施本發(fā)明;但是,凡熟悉本專業(yè)的技術(shù)人員在不脫離本發(fā)明技術(shù)方案范圍內(nèi),可利用以上所揭示的技術(shù)內(nèi)容而作出的些許更動、修飾與演變的等同變化,均為本發(fā)明的等效實(shí)施例;同時,凡依據(jù)本發(fā)明的實(shí)質(zhì)技術(shù)對以上實(shí)施例所作的任何等同變化的更動、修飾與演變等,均仍屬于本發(fā)明的技術(shù)方案的保護(hù)范圍之內(nèi)。