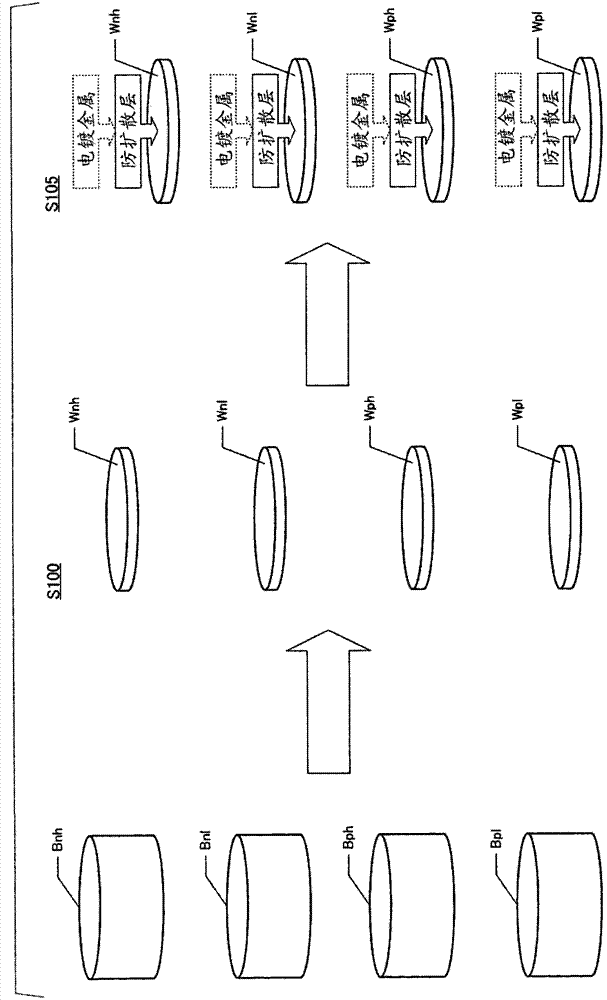
本發(fā)明涉及一種熱電轉(zhuǎn)換組件及熱電轉(zhuǎn)換組件的制造方法。
背景技術(shù):以前,出于各種目的使用熱電材料,以進行熱量與電力的轉(zhuǎn)換。例如,開發(fā)了一種熱電轉(zhuǎn)換組件,該熱電轉(zhuǎn)換組件將n型熱電材料與p型熱電材料串聯(lián)地電連接并排列配置在對置的基板之間,從而將基板中的一方用作高溫部,將基板中的另一方用作低溫部。該熱電轉(zhuǎn)換組件用于將由高溫部供給到熱電轉(zhuǎn)換組件的熱量轉(zhuǎn)換成電力的用途和通過通電來利用低溫部進行冷卻的用途等。在上述結(jié)構(gòu)中,高溫部的溫度千差萬別,但為了在超過焊料熔點的溫度區(qū)域中使用,開發(fā)了一種用于不利用焊料制造熱電轉(zhuǎn)換組件的技術(shù)。例如在日本特開2004-273489號公報中,公開了一種使在液體中分散有平均粒徑為1~10nm的金屬微粒子的導(dǎo)電性漿料涂敷于熱電元件、電極板等之后,通過將金屬微粒子彼此燒結(jié)而使熱電元件等接合的技術(shù)。在現(xiàn)有技術(shù)中,不能構(gòu)成在高溫部與低溫部的溫差大的使用條件下耐用的具有充足耐久性的熱電轉(zhuǎn)換組件。例如,假定在利用熱電元件進行發(fā)電時,在高溫部為300℃以上、低溫部為常溫(25℃左右)的環(huán)境下使用熱電轉(zhuǎn)換組件。在上述環(huán)境下,熱電轉(zhuǎn)換組件的高溫部與低溫部會產(chǎn)生較大的溫差,熱電元件與電極之間也會產(chǎn)生較大的溫差。由于熱電元件與電極的結(jié)構(gòu)要素通常完全不同,所以,在產(chǎn)生了較大溫差的使用環(huán)境下,熱電元件與電極的熱膨脹程度大不相同,兩者之間會產(chǎn)生較大的熱應(yīng)力。因此,即便使用金屬微粒子形成接合層,在沒有假定對熱應(yīng)力加以緩和的現(xiàn)有技術(shù)中,也將導(dǎo)致接合層損壞等。
技術(shù)實現(xiàn)要素:本發(fā)明是鑒于上述技術(shù)問題而做出的,其目的是提供一種能夠在溫差大的使用條件下使用的熱電轉(zhuǎn)換組件。為了解決上述技術(shù)問題,在本發(fā)明中,熱電轉(zhuǎn)換組件具有形成在一對基板的對置的面上的電極、配置在上述電極之間的熱電元件和接合電極與熱電元件的接合層,其中,該接合層的厚度設(shè)為30μm以上。而且,該接合層包括平均晶體粒徑大于1μm且為10μm以下的第一層和平均晶體粒徑大于10μm的第二層。即,由于接合層形成30μm以上的厚度,且接合層包括平均晶體粒徑大于1μm且為10μm以下的第一層和平均晶體粒徑大于10μm的第二層,所以,即便隨著熱電轉(zhuǎn)換組件的使用,熱應(yīng)力作用于該電極與熱電元件之間的接合層,也能夠緩和該熱應(yīng)力。其結(jié)果是,能夠防止熱電轉(zhuǎn)換組件破損。而且,本發(fā)明的熱電轉(zhuǎn)換組件的制造方法具有:在一對基板的對置的面上形成電極的工序;在上述電極之間配置熱電元件的工序;在所述電極與所述熱電元件之間形成包含小于100nm的金屬粒子的漿料,并通過燒結(jié)所述漿料而形成將所述電極與所述熱電元件接合的、厚度為30μm以上的接合層的工序。由于該接合層是通過對包含小于100nm的金屬粒子的漿料進行燒結(jié)而形成的,所以,燒結(jié)前以小于100nm的粒徑存在的金屬粒子在燒結(jié)后變成更大的晶粒且相互牢固地結(jié)合,構(gòu)成接合層。其結(jié)果是,接合層的強度變強。另外,接合層的電導(dǎo)率變大,能夠防止熱電轉(zhuǎn)換組件的熱電轉(zhuǎn)換效率下降。在本發(fā)明的實施方式中,一對基板能夠以夾著熱電元件的狀態(tài)保持熱電元件即可,一方的基板成為高溫部,一方的基板成為低溫部。另外,基板的至少一個面形成為平面狀(或者曲面狀),且通過使熱電元件在一對基板的面平行的狀態(tài)下配置在上述基板的面之間,構(gòu)成熱電轉(zhuǎn)換組件。此外,為了提高熱電轉(zhuǎn)換效率,優(yōu)選的是熱量從高溫部有效地傳導(dǎo)到熱電元件,熱量從熱電元件有效地傳導(dǎo)到低溫部的狀態(tài),所以也可以利用導(dǎo)熱系數(shù)高的部件構(gòu)成基板,或者也可以為了提高低溫部的散熱效率而形成為設(shè)置冷卻器(風(fēng)扇或者散熱片等)的結(jié)構(gòu)。在本發(fā)明的實施方式中,電極形成在基板的對置的面上,能夠通過使熱電元件接合于上述電極而將熱電元件電連接,以便能夠在熱電轉(zhuǎn)換組件中進行熱電轉(zhuǎn)換即可。例如,在將多個n型熱電元件和多個p型熱電元件夾持在基板之間且利用多個電極連接上述熱電元件的結(jié)構(gòu)中,一個n型熱電元件與一個p型熱電元件通過一方的基板上的一個電極電連接的情況下,該n型熱電元件與p型熱電元件構(gòu)成為在另一方的基板上與不同電極連接。即,構(gòu)成為n型熱電元件和p型熱電元件以電氣方式按順序串聯(lián)連接,n型熱電元件與p型熱電元件之間用電極連接。而且,配置在n型熱電元件與p型熱電元件之間的各個電極構(gòu)成為交替地接合于一對基板的狀態(tài)。當(dāng)然,在此也可以采用為了適當(dāng)?shù)剡M行熱電轉(zhuǎn)換而附帶的結(jié)構(gòu),例如將用于確?;迮c電極之間的電絕緣的部件(絕緣部件等)安裝于電極等的結(jié)構(gòu)等。在本發(fā)明的實施方式中,熱電元件通過將能夠進行熱電轉(zhuǎn)換的熱電材料設(shè)為規(guī)定的大小及形狀而形成,構(gòu)成為能夠配置在一對基板之間即可。當(dāng)然,熱電元件既可以設(shè)有多個,也可以由n型熱電元件和p型熱電元件構(gòu)成。在本發(fā)明的實施方式中,接合層是為了接合電極與熱電元件而形成的,能夠通過各種方法形成,但是厚度至少為30μm以上。即,調(diào)整接合層的厚度,以便能夠緩和作用在熱電元件與電極之間的熱應(yīng)力即可。另外,雖然接合層是通過對包含小于100nm的金屬粒子的漿料進行燒結(jié)而形成的,但是通過該燒結(jié)至少形成接合層的一部分即可。即,在本發(fā)明的實施方式中,漿料為金屬粒子包含在具有流動性的溶劑中的狀態(tài),為漿料自身具有流動性的狀態(tài),但在燒結(jié)后,變?yōu)槿軇]發(fā)而留下金屬粒子的、沒有流動性的狀態(tài)。與此同時,通過使金屬粒子彼此結(jié)合而變?yōu)殡娮璧偷臓顟B(tài),從而變?yōu)殡姌O側(cè)與熱電元件側(cè)電接合的狀態(tài)即可。因此,在將熱電元件與電極接合之前,熱電元件與電極之間存在漿料,在可自由改變彼此的位置的狀態(tài)下,將熱電元件和電極的位置調(diào)整到規(guī)定位置,并在調(diào)整位置之后,通過進行燒結(jié)而以使熱電元件和電極固定到該位置的方式利用漿料即可。因此,通過燒結(jié)漿料而形成接合層的厚度方向上的至少一部分即可。當(dāng)然,30μm以上的接合層也可以全部通過燒結(jié)形成。此外,在本發(fā)明的實施方式中,漿料包含小于100nm的金屬粒子即可,選擇金屬粒子的大小和元素的種類,以便通過燒結(jié)而使粒子相互結(jié)合,且在燒結(jié)后使熱電元件與電極電連接即可。另外,構(gòu)成漿料的溶劑優(yōu)選為有機溶劑。即,如果是金屬粒子分散在有機溶劑中而形成的漿料,則能夠通過燒結(jié)使有機溶劑揮發(fā),能夠在燒結(jié)后通過溶劑成分防止電導(dǎo)率變大。此外,金屬粒子的大小例如也可以是大于10nm且小于100nm的大小。即,由于10nm以下的金屬粒子容易氧化,所以如果利用大于10nm且小于100nm的金屬粒子,則能夠在抑制接合層中含有的氧的量的同時形成接合層。另外,在本發(fā)明的實施方式中,作為燒結(jié)的例子,也可以采用在金屬粒子變得粗大、所述熱電元件的晶粒不變得粗大的溫度下進行燒結(jié)的結(jié)構(gòu)。即,為了在燒結(jié)后確保接合層的強度,需要變?yōu)闈{料內(nèi)的金屬粒子彼此通過燒結(jié)相互結(jié)合、且結(jié)合不被熱應(yīng)力破壞的狀態(tài)。因此,如果在金屬粒子變得粗大的溫度以上的溫度下進行燒結(jié),則在燒結(jié)的過程中,金屬粒子彼此結(jié)合而變得粗大,能夠在燒結(jié)后變?yōu)樵摻Y(jié)合不被熱應(yīng)力破壞的狀態(tài),能夠形成高強度的接合層。而且,在本發(fā)明的實施方式中,為了在高性能的熱電元件中維持其性能,優(yōu)選不改變熱電元件內(nèi)的晶體的狀態(tài)。即,為了提高熱電元件的性能,需要使性能指數(shù)Z=α2/(ρ×κ)變大(α是塞貝克系數(shù)),優(yōu)選減小電阻率ρ,減小導(dǎo)熱系數(shù)κ。在多晶物質(zhì)中,晶粒越微細(xì)且晶軸的方向越雜亂,電阻率ρ越變大,所以為了使電阻率ρ變小,優(yōu)選使晶粒變大。然而,如果晶粒變大,晶體的取向程度變得均勻,則導(dǎo)熱系數(shù)κ變大。因此,在提高性能指數(shù)Z方面,電阻率ρ與導(dǎo)熱系數(shù)κ呈制衡的關(guān)系,而在BiTe系等熱電材料中,通常,晶軸的取向性強、晶軸在特定方向上整齊的材料的電阻率ρ小。因此,通過在適當(dāng)微細(xì)化的多晶材料中形成為晶軸在特定方向上取向的狀態(tài),制造電阻率ρ小且導(dǎo)熱系數(shù)κ也小的熱電材料,提高熱電材料的性能。并且,通過切取提高性能的熱電材料來制造高性能的熱電元件。因此,在本發(fā)明的實施方式中,若在高性能熱電元件內(nèi)的晶粒變得粗大的溫度下進行燒結(jié)而形成接合層,則導(dǎo)致熱電元件的性能下降。因此,如果在比熱電元件的晶粒變得粗大的溫度低的溫度下進行燒結(jié),則能夠防止因燒結(jié)而導(dǎo)致熱電元件的性能下降。而且,在本發(fā)明的實施方式中,也可以將接合層構(gòu)成為包括通過燒結(jié)漿料而形成的燒結(jié)層和鄰接該燒結(jié)層的電鍍層,并通過電鍍利用與漿料中含有的金屬粒子相同的金屬形成該電鍍層。即,如果在燒結(jié)前,在電極和熱電元件中的至少一方上利用與漿料中包含的金屬粒子相同的金屬形成電鍍層,并在該電鍍層與漿料接觸的狀態(tài)下進行燒結(jié),則在燒結(jié)時,金屬粒子與電鍍層就會容易地結(jié)合,所以能夠使接合層的強度為高強度。此外,電鍍層與燒結(jié)層鄰接地形成即可,從該燒結(jié)層觀察,電鍍層既可以形成于厚度方向上的一側(cè),也可以形成于兩側(cè)。即,如果在燒結(jié)層的兩側(cè)都需要利用電鍍層提高強度,則可以在兩側(cè)形成電鍍層,如果僅在一側(cè)需要利用電鍍層提高強度,則也可以僅在一側(cè)形成電鍍層。此外,在本發(fā)明的實施方式中,電鍍層的平均粒徑與燒結(jié)層的平均粒徑多不相同。例如,能夠假定如下結(jié)構(gòu):通過燒結(jié)包含小于100nm的金屬粒子的漿料,形成平均晶體粒徑大于1μm且為10μm以下的第一層,通過電鍍而形成平均晶體粒徑大于10μm的第二層。因此,通過本發(fā)明,也可以理解為形成包括第一層和第二層的接合層。當(dāng)然,也可以形成多層第一層及第二層。另外,在本發(fā)明的實施方式中,在通過燒結(jié)漿料來形成接合層的至少一部分的情況下,燒結(jié)前與漿料接觸的部位(例如,熱電元件、電極、熱電元件上的電鍍層、電極上的電鍍層等)發(fā)生氧化,故而氧濃度多半會局部性地變高。因此,燒結(jié)前夾持漿料的兩處部位的氧濃度高。另外,若反復(fù)多次利用漿料進行燒結(jié),則氧濃度高的部位同樣會兩處兩處地增加。因此,根據(jù)本發(fā)明,也可以理解為形成包括多層高氧濃度層的接合層,上述高氧濃度層以氧濃度沿厚度方向的變化超過規(guī)定基準(zhǔn)的位置為界面。此外,在本發(fā)明的實施方式中,規(guī)定基準(zhǔn)能夠判斷層內(nèi)任意位置的氧濃度與其它位置的氧濃度相比是否變多即可,例如,可以采用如下結(jié)構(gòu)等:以統(tǒng)計方式確定在燒結(jié)前接觸空氣等周圍氣體的部分與未接觸空氣等周圍氣體的部分在燒結(jié)后的氧濃度之差,并針對單位距離內(nèi)的氧濃度的變化設(shè)定規(guī)定基準(zhǔn),以便能夠區(qū)分這兩者。氧濃度能夠通過各種指標(biāo)評價,既可以通過單位面積或者單位體積內(nèi)的氧濃度來評價,也可以通過在特定的觀測方法中觀測到的氧的量、觀測頻度來評價。當(dāng)然,氧的濃度既可以通過絕對量進行評價也可以通過相對量進行評價。而且,在本發(fā)明的實施方式中,也可以形成與接合層鄰接且具有各種功能的層。例如,也可以在接合層與熱電元件之間以及接合層與電極之間的至少一方上形成防止材料擴散的防擴散層。即,在接合層與熱電元件的界面處,可能發(fā)生接合層內(nèi)的材料向熱電元件側(cè)擴散,或者熱電元件內(nèi)的材料向接合層側(cè)擴散的情況。另外,在接合層與電極的界面處,可能發(fā)生接合層內(nèi)的材料向電極側(cè)擴散,或者電極內(nèi)的材料向接合層側(cè)擴散的情況。因此,為了防止上述擴散,利用難以發(fā)生擴散的材料形成層就能夠作為防擴散層起作用。作為上述防擴散層起作用的材料可以根據(jù)接合層、熱電元件和電極的組成來選擇,例如,在Ag、Cu等金屬、BiTe系熱電材料中,利用Ni形成層就能夠作為防擴散層起作用。而且,在本發(fā)明的實施方式中,能夠在各種環(huán)境下進行燒結(jié),例如,也可以采用在從電極及熱電元件向接合層施加壓力的狀況下進行燒結(jié)的結(jié)構(gòu)。即,在加壓以壓縮接合層的環(huán)境下進行燒結(jié)。根據(jù)該結(jié)構(gòu),與不加壓的狀況相比,能夠降低燒結(jié)層中空隙的含有率,能夠降低燒結(jié)層的電阻。附圖說明圖1是表示本發(fā)明實施方式的熱電轉(zhuǎn)換組件的制造方法的流程圖。圖2是示意性地表示本發(fā)明實施方式的熱電轉(zhuǎn)換組件的制造方法的圖。圖3是示意性地表示本發(fā)明實施方式的熱電轉(zhuǎn)換組件的圖2的后續(xù)制造方法的圖。圖4是表示本發(fā)明一實施方式的熱電轉(zhuǎn)換組件的電極之間的結(jié)構(gòu)的截面圖。圖5A及圖5B是表示本發(fā)明一實施方式的熱電轉(zhuǎn)換組件的接合層內(nèi)的氧濃度的曲線圖。圖6是表示本發(fā)明其它實施方式的熱電轉(zhuǎn)換組件的電極之間的結(jié)構(gòu)的截面圖。具體實施方式在此,按照下述順序?qū)Ρ景l(fā)明的實施方式進行說明:(1)熱電轉(zhuǎn)換組件的制造方法;(2)實施例;(3)其它實施方式。(1)熱電轉(zhuǎn)換組件的制造方法圖1是表示熱電轉(zhuǎn)換組件的制造方法的一實施方式的流程圖。本實施方式的熱電轉(zhuǎn)換組件的制造方法是在制造熱電材料的塊體之后實施的。即,在實施圖1所示的熱電轉(zhuǎn)換組件的制造方法以前,預(yù)先制造n型熱電材料及p型熱電材料的塊體。本實施方式的n型熱電材料及p型熱電材料為Bi2Te3系熱電材料,稱量原料,以利用從由Bi、Sb組成的族中選擇的至少一種元素和從由Te、Se組成的族中選擇的至少一種元素組成(Bi,Sb)2(Te,Se)3這樣的組分,通過對稱量的原料應(yīng)用各種加工方法來制造n型熱電材料及p型熱電材料。此外,即使(Bi,Sb)與(Te,Se)的組分比略微偏離2∶3,只要與Bi2Te3為相同的晶體結(jié)構(gòu)(空間群為的菱面體晶體結(jié)構(gòu)),就是Bi2Te3系熱電材料。例如,能夠通過擠壓處理(熱壓法等)、伴有塑性變形的擠壓處理(剪切擠壓法(せん斷付與押出法)、ECAP法、熱鍛法等)、軋制處理、單向凝固法及單晶法等進行加工而使特定的晶軸向特定的取向方位取向,由此制造Bi2Te3系的n型熱電材料及p型熱電材料。本實施方式中預(yù)先準(zhǔn)備的熱電材料的塊體是n型熱電材料和p型熱電材料,并且由在高溫部的溫度區(qū)域中性能指數(shù)相對較高的高溫材料和在低溫部的溫度區(qū)域中性能指數(shù)相對較高的低溫材料構(gòu)成。圖2及圖3是示意性地表示圖1所示的制造方法的主要工序中的加工對象的圖。在圖2中,把在實施圖1所示的制造之前制造出的塊體表示成Bnh、Bnl、Bph、Bpl。在此,塊體Bnh為n型熱電材料的高溫材料,塊體Bnl為n型熱電材料的低溫材料,塊體Bph為p型熱電材料的高溫材料,塊體Bpl為p型熱電材料的低溫材料。即,在高溫區(qū)域(300℃附近的溫度區(qū)域)中,塊體Bnh的熱電材料的性能指數(shù)比塊體Bnl的熱電材料的性能指數(shù)高,在低溫區(qū)域(50℃附近的溫度區(qū)域)中,塊體Bnh的性能指數(shù)比塊體Bnl的熱電材料的性能指數(shù)低。同樣,在高溫區(qū)域(300℃附近的溫度區(qū)域)中,塊體Bph的熱電材料的性能指數(shù)比塊體Bpl的熱電材料的性能指數(shù)高,在低溫區(qū)域(50℃附近的溫度區(qū)域)中,塊體Bph的熱電材料的性能指數(shù)比塊體Bpl的熱電材料的性能指數(shù)低。在圖1所示的制造方法中,切割上述Bi2Te3系熱電材料的塊體Bnh、Bnl、Bph、Bpl來制造薄板狀的晶片(步驟S100)。在本實施方式中,由于是通過后述工序在兩片晶片之間形成接合層來制造直六面體的熱電元件,所以各晶片的厚度被設(shè)定成根據(jù)熱電元件的大小而預(yù)先確定的厚度。在圖2中,將由n型熱電材料的塊體Bnh制造的晶片表示成Wnh,將由n型熱電材料的塊體Bnl制造的晶片表示成Wnl,將由p型熱電材料的塊體Bph制造的晶片表示成Wph,將由p型熱電材料的塊體Bpl制造的晶片表示成Wpl。此外,在本實施方式中,在熱電材料之間形成有接合層,在熱電元件與電極之間也形成有接合層,所以將前者稱為材料間接合層,將后者稱為元件電極間接合層。另外,在其它類似的層中,也根據(jù)需要利用材料間和元件電極間來區(qū)分各層。例如,將熱電材料之間的A層稱為材料間A層,將熱電元件與電極之間的A層稱為元件電極間A層。在制造了晶片時,接下來,在晶片表面上形成防擴散層(步驟S105)。在步驟S105中形成的防擴散層可以存在于熱電材料之間,也可以存在于熱電元件與電極之間。因此,該防擴散層可能成為材料間防擴散層和元件電極間防擴散層這兩者。此外,還可以進一步利用與后述漿料中包含的金屬粒子相同的金屬,對形成有防擴散層后的晶片進行形成金屬電鍍層的處理。在圖2中,利用實線矩形表示通過步驟S105形成防擴散層的情況,利用虛線矩形表示還可以形成金屬電鍍層的情況。在進行了電鍍時,向高溫材料與低溫材料之間涂覆包含小于100nm的金屬粒子的漿料并進行燒結(jié),使高溫材料與低溫材料粘在一起(步驟S110)。在本實施方式中,將燒結(jié)對象送入回流爐內(nèi)且形成規(guī)定的氣氛(真空、氬氣、氮氣、空氣等)之后,通過在規(guī)定的燒結(jié)溫度下加熱規(guī)定時間來進行燒結(jié)。在此,如圖3所示,在n型熱電材料的高溫材料的晶片Wnh與低溫材料的晶片Wnl之間夾持有漿料PM的狀態(tài)下進行燒結(jié),在p型熱電材料的高溫材料的晶片Wph與低溫材料的晶片Wpl之間夾持有漿料PM的狀態(tài)下進行燒結(jié)。此外,燒結(jié)溫度是使?jié){料中包含的小于100nm的金屬粒子變得粗大、且使熱電材料的晶粒不變得粗大的溫度。即,在本實施方式的漿料中包含小于100nm的金屬粒子,若加熱上述微小的金屬粒子,則在遠(yuǎn)低于該金屬的熔點的溫度下,晶體彼此結(jié)合,金屬粒子變得粗大。另外,有機溶劑揮發(fā)。若通過上述燒結(jié)使金屬粒子變得粗大,則曾為漿料的部分失去流動性,牢固地固化。并且,該固化的部分直至達到該金屬的熔點也不熔化,該固化的部分即使作為熱電轉(zhuǎn)換組件的高溫部而再次被加熱到假定的300℃左右,也以固體形式維持穩(wěn)定的狀態(tài)。因此,燒結(jié)前曾為漿料的部分在燒結(jié)后變成牢固地接合在熱電材料之間的材料間接合層,即使加熱到使用熱電轉(zhuǎn)換組件的溫度區(qū)域,燒結(jié)前曾為漿料的部分也將作為牢固地接合在熱電材料之間的接合層起作用。此外,燒結(jié)溫度越變高,漿料內(nèi)的金屬粒子越容易變得粗大,但若設(shè)為過高的溫度,則熱電材料內(nèi)的晶粒變得粗大而使性能指數(shù)下降。因此,燒結(jié)溫度被設(shè)定為比熱電材料內(nèi)的晶粒變得粗大的溫度低的溫度。而且,漿料在燒結(jié)溫度下維持的規(guī)定時間,被設(shè)定為能夠通過由燒結(jié)引起的金屬粒子粗大化,而使材料間接合層的強度充分提高、且使材料間接合層的電導(dǎo)率充分下降即可,例如可以采用如下結(jié)構(gòu)等,即,將規(guī)定時間設(shè)定為能在經(jīng)過規(guī)定時間后確認(rèn)1um以上的金屬粒子這樣的時長。此外,作為漿料,可以舉出例如同和電子科技公司制造的銀納米漿料、大研化學(xué)工業(yè)制造的NAG-10、三之星機帶科技公司制造的MDot等。若以上燒結(jié)的結(jié)果為制造出高溫材料層、由漿料形成的材料間燒結(jié)層和低溫材料層成為一體的晶片狀的熱電材料,則接下來切割燒結(jié)后的熱電材料來制造熱電元件(步驟S115)。在本實施方式中,由于是制造直六面體的熱電元件,所以將切割方向設(shè)定為在晶片的圓形表面內(nèi)相互垂直的兩個方向。通過該切割,得到圖3所示的直六面體的n型熱電元件Pn和p型熱電元件Pp。此外,在各個n型熱電元件Pn、p型熱電元件Pp中,熱電元件之間成為Ni電鍍層(材料間防擴散層)、由漿料形成的材料間燒結(jié)層和Ni電鍍層(材料間防擴散層)這樣的結(jié)構(gòu),熱電元件表面的最外層成為Ni電鍍層。該熱電元件最表層的Ni電鍍層通過后面的工序成為元件電極間防擴散層。接下來,在基板上形成電極(步驟S120)。即,在本實施方式中,由于將薄的矩形板狀的基板用作支承熱電元件且向熱電元件傳導(dǎo)熱量、承接來自熱電元件的熱量的部位,所以,預(yù)先針對該基板確定電極的配置圖案以便能夠以電氣方式串聯(lián)連接熱電元件,并使電極以形成該配置圖案的方式形成在基板上。例如,可以通過用Cu在陶瓷基板上形成電極圖案來形成上述電極。在圖3中,示意性地表示了在基板Pb1上沿橫向排列形成有三個直六面體的電極E、沿縱向(附圖的進深方向)排列形成有兩個直六面體的電極E的例子,但在構(gòu)成熱電轉(zhuǎn)換組件的一對基板中,一方的基板的電極圖案與另一方的基板的電極圖案也可以不同。接下來,通過鍍Ni在電極表面上形成防擴散層(步驟S125)。步驟S125中形成的防擴散層由于是存在于熱電元件與電極之間的層,所以是元件電極間防擴散層。此外,在此,也可以在形成防擴散層后,進一步進行形成金屬電鍍層的處理。在圖3中,利用實線矩形表示通過步驟S125在電極E的表面上形成防擴散層的情況,利用虛線矩形表示還可以形成金屬電鍍層的情況。此外,步驟S120、S125也可以先于步驟S100進行。在對電極表面進行了電鍍時,如圖3所示,將漿料PM涂覆于電極上的防擴散層(步驟S130)。在此,預(yù)先確定漿料的量,以使?jié){料在燒結(jié)后具有30μm以上的厚度。即,本實施方式的漿料是包含小于100nm的金屬粒子的有機溶劑,通過燒結(jié),有機溶劑全部揮發(fā),所以,能夠涂覆漿料以便在有機溶劑全部揮發(fā)的情況下變?yōu)樗韬穸龋瑥亩篃Y(jié)后形成的層(元件電極間接合層)的厚度為所需厚度。此外,有機溶劑和金屬粒子的比率不受限定,但為了形成所需厚度的元件電極間接合層,有機溶劑的量優(yōu)選較少,例如,金屬粒子的重量比優(yōu)選為80%以上。更具體地說,可以以規(guī)定的升溫速度加熱6.3mg的Ag漿料,并通過在310℃下保持30分鐘,來利用0.988mg有機溶劑完全揮發(fā)的Ag漿料(即,Ag粒子為84.3重量%)形成厚度在30μm以上的元件電極間接合層。作為上述Ag漿料,可以舉出例如同和電子科技公司制造的銀納米漿料、大研化學(xué)工業(yè)制造的NAG-10、三之星機帶科技公司制造的MDot等。接下來,在漿料上安裝熱電元件(步驟S135)。在本實施方式中,如圖3所示,表示了針對每一個電極E安裝n型熱電元件Pn和p型熱電元件Pp各一個的例子。因此,若電極E為六個,則要安裝共計六個n型熱電元件Pn和共計六個p型熱電元件Pp。接下來,在熱電元件上安放基板Pb2(步驟S140),并進行燒結(jié)(步驟S145)。即,選擇與已在電極上安裝有熱電元件的基板成對的基板且將該基板安放在熱電元件上,并以熱電元件被一對基板夾持狀態(tài)送入回流爐內(nèi)。然后,在回流爐內(nèi)形成規(guī)定的氣氛(真空、氬氣、氮氣、空氣等)之后,通過在規(guī)定的燒結(jié)溫度下加熱規(guī)定時間來進行燒結(jié)。此外,如圖3所示,安放在熱電元件上的基板Pb2是通過電路圖案形成有電極的基板,該電路圖案針對安裝完的熱電元件,將各熱電元件以n型熱電元件與p型熱電元件交替連接的方式串聯(lián)連接。在此,燒結(jié)溫度也是使金屬粒子變得粗大、且使熱電元件的晶粒不變得粗大的溫度。即,設(shè)定燒結(jié)溫度,使得燒結(jié)前曾為漿料的部分在燒結(jié)后作為牢固地接合在熱電元件與電極之間的元件電極間接合層起作用。將上述燒結(jié)溫度設(shè)定為比熱電材料內(nèi)的晶粒變得粗大的溫度低的溫度,以免熱電材料內(nèi)的晶粒變得粗大而使性能指數(shù)下降。另外,設(shè)定規(guī)定時間,以便能夠通過由燒結(jié)引起的金屬粒子粗大化,使元件電極間接合層的強度充分提高,且使元件電極間接合層的電導(dǎo)率充分下降。在此,也可以采用如下結(jié)構(gòu)等,即,將規(guī)定時間設(shè)定為能在經(jīng)過規(guī)定時間后確認(rèn)1μm以上的金屬粒子這樣的時長。圖4是示意性地表示按照上述方式制造的熱電轉(zhuǎn)換組件的電極之間結(jié)構(gòu)的截面圖,表示了沿著與基板上供電極形成的面垂直的方向切開熱電元件等的樣子。如上述圖4所示,在熱電轉(zhuǎn)換組件中,在電極E、E之間沿?zé)犭娫暮穸确较蛞来涡纬捎蠳i電鍍層(元件電極間防擴散層)LNe、通過燒結(jié)漿料而形成的元件電極間接合層Lae、Ni電鍍層(元件電極間防擴散層)LNe、高溫材料Pnh(或者Pph)、Ni電鍍層(材料間防擴散層)LNm、通過燒結(jié)漿料而形成的材料間接合層Lam、Ni電鍍層(材料間防擴散層)LNm、低溫材料Pnl(或者Ppi)、Ni電鍍層(元件電極間防擴散層)LNe、通過燒結(jié)漿料而形成的元件電極間接合層Lae和Ni電鍍層(元件電極間防擴散層)LNe。本實施方式的熱電轉(zhuǎn)換組件用于在高溫部與低溫部的溫差較大的狀態(tài)下進行發(fā)電的用途等。在上述用途中,例如,將高溫部的溫度設(shè)為300℃左右,將低溫部的溫度設(shè)為50℃左右。該情況下,圖4中的電極E中的一方為300℃左右,電極E中的另一方為50℃左右,兩者的溫差為250℃左右。因此,在電極E之間產(chǎn)生大的溫差,在電極E與熱電元件(Pnh、Pnl等)之間也產(chǎn)生大的溫差。即,若比較多個層的熱膨脹率,則在材料的組分大不相同的情況下,熱膨脹率通常大不相同。因此,在本實施方式的熱電轉(zhuǎn)換組件中,熱電元件(Pnh、Pnl等)的熱膨脹率與電極E的熱膨脹率大不相同,由于上述大的溫差的緣故,大的熱應(yīng)力作用于電極E與熱電元件(Pnh、Pnl等)之間的層。然而,在本實施方式中,通過上述制造工序,將元件電極間接合層Lae的厚度Ta調(diào)整成了30μm以上的厚度。因此,即使在夾持元件電極間接合層Lae的電極E與熱電元件(Pnh、Pnl等)之間產(chǎn)生了大的熱應(yīng)力,也能夠利用元件電極間接合層Lae緩和該熱應(yīng)力,能夠防止破損(電極E與熱電元件(Pnh、Pnl等)的機械接觸或者電接觸的損壞)。而且,元件電極間接合層Lae是通過對包含小于100nm的金屬粒子的漿料進行燒結(jié)而形成的。在該燒結(jié)過程中,有機溶劑中包含的小于100nm的金屬粒子變得粗大,變?yōu)槟軌蛴^測到1μm以上的金屬粒子的狀態(tài)。因此,燒結(jié)后的元件電極間接合層Lae變?yōu)榘?μm以上的金屬粒子的層,不久以后,金屬粒子在燒結(jié)溫度下不再變得粗大,元件電極間接合層Lae變得穩(wěn)定。另外,由于元件電極間接合層Lae變?yōu)榘?μm以上的金屬粒子的層,所以金屬粒子之間的結(jié)合比燒結(jié)前更加堅固。因此,即使如上述那樣在高溫部與低溫部的溫差為250℃左右的狀態(tài)下使用熱電轉(zhuǎn)換組件,在元件電極間接合層Lae內(nèi),金屬粒子的狀態(tài)也不會再度變化,能夠在元件電極間接合層Lae的狀態(tài)不發(fā)生變化的狀態(tài)下使用熱電轉(zhuǎn)換組件。另外,即使在電極E與熱電元件Pn(或者Pp)之間產(chǎn)生了大的熱應(yīng)力,也能夠防止元件電極間接合層Lae被破壞,并且能夠利用元件電極間接合層Lae緩和熱應(yīng)力。而且,由于通過燒結(jié)使金屬粒子變得粗大,所以元件電極間接合層Lae中的實際有效的截面積變大,元件電極間接合層Lae的電導(dǎo)率變大。其結(jié)果是,能夠防止熱電轉(zhuǎn)換組件的熱電轉(zhuǎn)換效率下降。(2)實施例接下來,對通過上述制造方法制造的熱電轉(zhuǎn)換組件的實施例進行說明。在本實施例中,把向Bi1.9Sb0.1Te2.5Se0.5這一組分比的原料中追加0.3重量%的Te而得到的物質(zhì)作為n型熱電材料的高溫材料的初始原料,將Bi1.9Sb0.1Te2.7Se0.3這一組分比的原料作為n型熱電材料的低溫材料的初始原料。另外,將Bi0.2Sb1.8Te2.85Se0.1這一組分比的原料作為p型熱電材料的高溫材料的初始原料,將Bi0.5Sb1.5Te3這一組分比的原料作為p型熱電材料的低溫材料的初始原料。另外,在本實施例中,稱量Bi、Sb、Te、Se并調(diào)整各元素的組分而形成了上述各初始原料,將各初始原料在氬氣氣氛中加熱至700℃而使之融化,并對其實施了攪拌。而且,通過對攪拌/融化后的初始原料進行冷卻而使之凝固,形成了n型熱電材料的高溫材料的合金及低溫材料的合金、p型熱電材料的高溫材料的合金及低溫材料的合金。而且,通過將所得到的各合金粉碎或者對所得到的各合金實施液體急冷處理而制造了熱電材料的粉末。粉碎可以通過球磨機、搗碎機等實施,液體急冷處理可以通過軋輥型液體急冷裝置、旋轉(zhuǎn)圓盤裝置、氣體霧化裝置等實施。此外,該液體急冷處理可以通過例如在氬氣氣氛中對加熱到800℃的合金進行急冷來實施。而且,將所得到的各粉末填充到了金屬模具中,并利用熱壓裝置或者放電等離子燒結(jié)裝置在單軸壓制的狀態(tài)下進行燒結(jié)而制造了上述塊體Bnh、Bnl、Bph、Bpi。此外,單軸壓制是通過在氬氣氣氛中在加熱到450℃的狀態(tài)下作用100MPa的壓力來實施的。當(dāng)然,塊體也可以通過伴有上述塑性變形的擠壓處理、軋制處理等制造。以上述方式制成的熱電材料在室溫下的特性如以下的表1所示?!颈?】此外,表1所示的熱電材料中,n型和p型這兩者在使用溫度從25℃改變到300℃時,性能指數(shù)在暫時上升之后下降,高溫材料的下降程度比低溫材料的下降程度小,所以在高溫區(qū)域中,高溫材料的性能指數(shù)比低溫材料的性能指數(shù)高。例如,在n型熱電材料的高溫材料中,性能指數(shù)在25℃下約為1.3左右(單位是10-3K-1,以下相同),但性能指數(shù)在50℃下變?yōu)?.9,在100℃下變?yōu)?.1,在200℃下變?yōu)?.9,在300℃下變?yōu)?.2。另一方面,在n型熱電材料的低溫材料中,性能指數(shù)在25℃下約為3.3左右,但性能指數(shù)在50℃下變?yōu)?.7,在100℃下變?yōu)?.0,在200℃下變?yōu)?.9,在300℃下變?yōu)?.35。在p型熱電材料的高溫材料中,性能指數(shù)在25℃下約為1.0左右,但性能指數(shù)在50℃下變?yōu)?.7,在100℃下變?yōu)?.0,在200℃下變?yōu)?.8,在300℃下變?yōu)?.1。另一方面,在p型熱電材料的低溫材料中,性能指數(shù)在25℃下約為3.2左右,但性能指數(shù)在50℃下變?yōu)?.5,在100℃下變?yōu)?.7,在200℃下變?yōu)?.7,在300℃下變?yōu)?.35。因此,在上述熱電材料中的任一種中,在50℃下,均為高溫材料的性能指數(shù)<低溫材料的性能指數(shù),在300℃下,均為高溫材料的性能指數(shù)>低溫材料的性能指數(shù)。而且,利用多線切割機切割所得到的塊體Bnh、Bnl、Bph、Bpl而制造了晶片(步驟S100),通過鍍Ni在各晶片的表面上形成了10μm的防擴散層(步驟S105)。此外,在步驟S100中,使高溫材料的高度和低溫材料的高度這兩者均為0.5mm。而且,在高溫材料與低溫材料之間涂覆了Ag漿料(例如,大研化學(xué)工業(yè)制造的NAG-10),將粘在一起的狀態(tài)下的高溫材料和低溫材料導(dǎo)入到了回流爐內(nèi),通過在空氣中加熱并在350℃下維持60分鐘而燒結(jié)了晶片(步驟S110)。其結(jié)果是,通過燒結(jié)形成了38μm的材料間接合層。之后,利用切割鋸切割燒結(jié)后的晶片而制造了熱電元件Pn、Pp(步驟S115)。在此,進行切割,使熱電元件Pn、Pp在垂直于高度的方向上的截面為0.6mm×0.6mm。因此,熱電元件Pn、Pp的大小為大約1mm×0.6mm×0.6mm。另外,在此,上述熱電元件Pn、Pp各制造了100個。而且,在兩個陶瓷制基板(氧化鋁制基板,0.5mm×10mm×11mm)之間配置了100個由n型熱電元件Pn和p型熱電元件Pp組成的組,在各基板上形成了電路圖案被預(yù)先確定的電極,以使上述n型熱電元件Pn和p型熱電元件Pp能夠按n型、p型的順序以電氣方式串聯(lián)連接(步驟S120),并通過鍍Ni在各基板上的各電極表面上形成了10μm的防擴散層(步驟S125)。而且,在電極上的防擴散層上涂覆了Ag漿料(例如,大研化學(xué)工業(yè)制造的NAG-10)(步驟S130),將通過步驟S115制造的熱電元件安裝到了Ag漿料上(步驟S135),在熱電元件上安放了基板(步驟S140),并在回流爐內(nèi)進行了燒結(jié)(步驟S145)。燒結(jié)是通過使回流爐內(nèi)的氣氛為大氣而進行加熱,并在300℃下維持60分鐘來進行的。其結(jié)果是,通過燒結(jié)而形成了46μm的元件電極間接合層。而且,在燒結(jié)后從回流爐內(nèi)取出了基板,并通過對布線用電極進行布線而制造了熱電轉(zhuǎn)換組件。將以此方式制造的熱電轉(zhuǎn)換組件的樣品作為基準(zhǔn)樣品,下面,對有關(guān)各種樣品的特性進行比較。需要說明的是,在以下實施例的各樣品中,除了在各實施例的說明中提及的參數(shù)(金屬類別、厚度等)以外,其它參數(shù)均與基準(zhǔn)樣品相同。表2表示了在步驟S105、步驟S125中,在電極與熱電元件之間形成元件電極間防擴散層的情況下所帶來的效果。【表2】表2表示了利用左列示出的各元素形成步驟S105、S125的元件電極間防擴散層并通過上述制造方法制成的樣品的發(fā)電電力下降率的時間變化特性。需要說明的是,表2的第2排樣品為基準(zhǔn)樣品,其它樣品是把在基準(zhǔn)樣品制造工序中由步驟S105、步驟S125形成的元件電極間防擴散層改變成其它防擴散層的樣品。另外,“無”是省略了步驟S105、步驟S125的樣品。在表2中,比較了剛剛制造后的發(fā)電電力與制造后經(jīng)過3個月、6個月、12個月、24個月之后的發(fā)電電力,計算并表示了發(fā)電電力因時間流逝而產(chǎn)生的下降率。如此,在沒有元件電極間防擴散層的情況下,在電極與元件電極間接合層之間或者元件電極間接合層與熱電元件之間,元素發(fā)生了擴散,所以發(fā)電電力隨著時間的流逝而下降。另外,在制造后流逝的時間很長時,元件電極間接合層發(fā)生破損,熱電轉(zhuǎn)換組件變得無法使用。另一方面,在形成有任意元件電極間防擴散層的情況下,都能夠抑制發(fā)電電力隨著時間的流逝而下降。另外,還能夠防止元件電極間接合層破損。此外,表2所示的發(fā)電電力是利用以上述方式制成的熱電轉(zhuǎn)換組件測定到的。即,測定時,使溫度調(diào)整用的珀爾帖元件接觸熱電轉(zhuǎn)換組件的低溫部并將低溫部的基板保持在50℃,使加熱器接觸高溫部并將高溫部的基板保持在300℃。然后,在該狀態(tài)下,將外部附加電阻裝置與從熱電轉(zhuǎn)換組件的電極延伸的引線連接,通過一邊改變外部附加電阻一邊測定電壓及電流來測定發(fā)電電力。步驟S145中的燒結(jié)溫度是使在步驟S130中涂覆的漿料內(nèi)的金屬粒子變得粗大、且使熱電元件Pn、Pp的晶粒不變得粗大的溫度。表3是在將包含小于100nm的金屬粒子的漿料和包含100nm以上的金屬粒子的漿料涂覆于通過步驟S125形成有元件電極間接合層的電極,進一步在步驟S145中使回流爐內(nèi)的溫度以規(guī)定的升溫速度上升,并以規(guī)定的燒結(jié)溫度燒結(jié)60分鐘的情況下,針對多個燒結(jié)溫度,對應(yīng)地表示了元件電極間接合層的接合性?!颈?】在此,表3中的表示成Ag、小于100nm、300℃的樣品為基準(zhǔn)樣品,表3中的其它樣品是改變了金屬種類、燒結(jié)溫度、漿料內(nèi)的粒子的大小的樣品。表3表示將由熱電元件Pn、Pp各自中使用的高溫材料及低溫材料的電阻率算出的電阻值、與在實際制造的熱電轉(zhuǎn)換組件中實測到的電阻值之間進行比較,并將實測值相對于計算值的增加程度不足10%的表示成圓圈,將增加程度在10%以上且不足20%的表示成△。另外,×表示電極與熱電元件不接合的樣品。如上所述,如果利用包含小于100nm的Ag粒子的漿料,則在燒結(jié)溫度處于250℃~350℃的范圍內(nèi)時,能夠制造具有電阻值充分變小的元件電極間接合層的熱電轉(zhuǎn)換組件。另外,如果利用包含小于100nm的Al粒子的漿料,則在燒結(jié)溫度處于200℃~350℃的范圍內(nèi)時,能夠制造具有電阻值充分變小的元件電極間接合層的熱電轉(zhuǎn)換組件。如果利用包含小于100nm的Cu粒子的漿料,則在燒結(jié)溫度處于350℃時,能夠制造具有電阻值充分變小的元件電極間接合層的熱電轉(zhuǎn)換組件。如果利用包含小于100nm的Ti粒子的漿料,則在燒結(jié)溫度處于250℃~350℃的范圍內(nèi)時,能夠制造具有電阻值充分變小的元件電極間接合層的熱電轉(zhuǎn)換組件。如果利用包含小于100nm的Cr粒子的漿料,則在燒結(jié)溫度處于300℃~350℃的范圍內(nèi)時,能夠制造具有電阻值充分變小的元件電極間接合層的熱電轉(zhuǎn)換組件。此外,如果允許自電阻值的計算值增加的增加率為10%以上且不足20%這一情況,則能夠如表3內(nèi)的△的樣品那樣,利用包含100nm以上的金屬粒子的漿料形成元件電極間接合層。表4是表示通過步驟S145的燒結(jié)形成的電極與熱電元件之間的元件電極間接合層為30μm以上的情況下所帶來的效果的表。【表4】表4是改變涂覆在熱電元件與電極之間的Ag漿料的量并進行燒結(jié)而制造熱電轉(zhuǎn)換組件的情況的例子,表示了在形成于熱電元件與電極之間的元件電極間接合層的各個厚度下,到元件電極間接合層被破壞時經(jīng)過的周期數(shù)。需要說明的是,在此,將熱電轉(zhuǎn)換組件的高溫部的基板為300℃、低溫部的基板為50℃的狀態(tài)保持5分鐘,之后將整個熱電轉(zhuǎn)換組件冷卻到25℃并保持5分鐘,把這樣的工序設(shè)為1個周期。如表4所示,元件電極間接合層的厚度越變厚,則到元件電極間接合層被破壞所需要的周期數(shù)越是增加,在元件電極間接合層的厚度為30μm以上的情況下,元件電極間接合層在經(jīng)過20000個周期數(shù)以上的周期后才被破壞。因此,如果元件電極間接合層的厚度為30μm以上,則在達到十分耐用的周期數(shù)之前,元件電極間接合層都不被破壞,可見,30μm以上的元件電極間接合層有助于緩和熱應(yīng)力。(3)其它實施方式本發(fā)明也可以采用上述實施方式以外的各種實施方式。另外,能夠?qū)⒏鞣N要素作為發(fā)明特定事項。元件電極間接合層可以如上述實施方式那樣僅由元件電極間燒結(jié)層構(gòu)成,該元件電極間燒結(jié)層通過對包含小于100nm的金屬粒子的漿料進行燒結(jié)而形成,但元件電極間接合層也可以包含通過其它方法形成的層,例如可以采用通過電鍍金屬來形成元件電極間接合層的一部分的結(jié)構(gòu)。該情況下,電鍍層優(yōu)選是由與漿料中包含的小于100nm的金屬粒子相同的金屬形成的電鍍層。即,如果在燒結(jié)前,在電極和熱電元件中的至少一方上利用與漿料中包含的金屬粒子相同的金屬形成電鍍層,并在該電鍍層與漿料接觸的狀態(tài)下進行燒結(jié),則在燒結(jié)時,金屬粒子與電鍍層就會容易地結(jié)合,所以能夠使元件電極間接合層的強度為高強度。而且,也可以在從電極及熱電元件向元件電極間接合層施加壓力的狀況下進行燒結(jié)。根據(jù)該結(jié)構(gòu),與不加壓的狀況相比,能夠降低元件電極間燒結(jié)層中空隙的含有率,能夠降低元件電極間燒結(jié)層的電阻。表5是表示各種實施例及比較例的特性的表?!颈?】壓力(MPa)燒結(jié)前(μm)燒結(jié)后(um)空隙率(%)電阻比06046281.0616042241.0446038211.0456035161.02106033141.015104881.0103212181.12表5的第1排至第5排所示的例子,是將Ag漿料涂覆于利用Ni形成有元件電極間防擴散層的熱電元件與電極之間來制造熱電轉(zhuǎn)換組件的情況的例子,該例子使左列所示的各壓力作用于電極與熱電元件之間并進行了燒結(jié)。壓力為0MPa的是上述的基準(zhǔn)樣品,通過在基準(zhǔn)樣品的制造工序中改變作用于電極與熱電元件之間的壓力而制造了其它樣品。在各樣品中,燒結(jié)前Ag漿料的厚度是相同的,但壓力越大,燒結(jié)后的元件電極間接合層的厚度越變薄。即,在以涂覆有等量的Ag漿料的狀態(tài)進行燒結(jié)的情況下,壓力越大,元件電極間接合層中Ag的密度越大。表5中表示了各樣品的元件電極間接合層的空隙率和電阻比。在此,空隙率是利用超聲波探傷裝置測定元件電極間接合層而得到的空位的面積比率。另外,電阻比是由熱電元件Pn、Pp各自中使用的高溫材料及低溫材料的電阻率算出的電阻值與在實際制造的熱電轉(zhuǎn)換組件中實測到的電阻值之比。如表5所示,壓力越大,則空隙率越少,電阻比越小。因此,通過在作用有壓力的情況下進行燒結(jié),能夠制造電阻值更小的元件電極間接合層。表5的第6排所示的例子,是在元件電極間防擴散層形成于各個熱電元件和電極之后,對該元件電極間防擴散層鍍Ag的情況的例子。即,是在元件電極間防擴散層上的Ag電鍍層上涂覆有Ag漿料的狀態(tài)下安裝熱電元件,安放基板并進行燒結(jié),利用電鍍層、燒結(jié)層、電鍍層構(gòu)成元件電極間接合層的例子。此外,在該例子中,電鍍層的厚度為20μm。并且,如表5的第6排所示,燒結(jié)前的Ag漿料的厚度為10μm,燒結(jié)后的元件電極間接合層的厚度為48μm,由此可知,由Ag漿料形成的元件電極間燒結(jié)層約為8μm。此外,在該例子中,電極與熱電元件之間也作用有壓力(5MPa)。在該例子中,由于空隙率減小到8%時,電阻比減小到1.01,所以也制造了電阻值極小的元件電極間接合層。另外,在該例子中,在進行與上述表4相同的試驗時,到破壞時經(jīng)過的周期數(shù)是20842個周期,故而能夠確認(rèn),在元件電極間接合層由電鍍層、燒結(jié)層、電鍍層構(gòu)成的例子中,也進行了高強度接合。此外,為了形成所需厚度的元件電極間接合層,優(yōu)選使用Ag粒子的重量比為80%以上的Ag漿料。表5的第7排所示的例子是利用Ag粒子的重量比為62%的Ag漿料制造熱電轉(zhuǎn)換組件的情況的例子。在該例子中,Ag粒子的重量比小而漿料的流動性高,所以難以使燒結(jié)前的Ag漿料的厚度形成為任意厚度。另外,在對燒結(jié)前厚度為32μm的Ag漿料實施燒結(jié)而形成元件電極間接合層時,變?yōu)?2μm。該情況下,空隙率為18%,是良好的數(shù)值,但電阻比增大到1.12。另外,在該例子中,在進行與上述表4相同的試驗時,到破壞時經(jīng)過的周期數(shù)是3492個周期,故而能夠確認(rèn),無法確保足夠的強度。此外,如上所述,在元件電極間接合層由電鍍層和燒結(jié)層構(gòu)成的結(jié)構(gòu)中,電鍍層的平均粒徑與燒結(jié)層的平均粒徑多不相同。即,通過燒結(jié)包含小于100nm的金屬粒子的漿料,形成平均晶體粒徑大于1μm且為10μm以下的第一層,通過電鍍,形成平均晶體粒徑大于10μm的第二層。因此,也可以通過制造具備下述元件電極間接合層的熱電轉(zhuǎn)換組件來實現(xiàn)本發(fā)明,上述元件電極間接合層包括平均晶體粒徑如上的第一層和第二層。在此,第一層為燒結(jié)層,第二層也可以通過電鍍以外的制法形成。表6是比較第一層和第二層中的燒結(jié)前后的Ag粒子的平均晶體粒徑的表。【表6】燒結(jié)前(μm)燒結(jié)后(μm)第一層0.0586第二層:熱電元件側(cè)1315第二層:基板側(cè)1215在此,例如,可以利用面積與某截面中的晶粒的面積相同的圓的半徑,定義第一層在燒結(jié)后、第二層在燒結(jié)前及燒結(jié)后的晶體粒徑。并且,平均晶體粒徑是通過如下方法得出的值,即,利用例如TSL公司制造的EBSD(ElectronBackScatterDiffraction:電子背散射衍射)裝置測定元件電極間接合層中的、方向與厚度方向垂直的截面,并針對截面內(nèi)的多個位置及多個截面來取晶體粒徑的平均數(shù)。另外,第一層在燒結(jié)前的平均晶體粒徑為擴散到漿料內(nèi)的Ag粒子的平均大小。如表6所示,在由Ag漿料形成的第一層中,平均晶體粒徑為6μm(大于1μm且為10μm以下),在第二層中,平均晶體粒徑為15μm。因此,如果構(gòu)成包含平均晶體粒徑大于1μm且為10μm以下的第一層和平均晶體粒徑大于10μm的第二層的層,則能夠形成電阻值小且強度高的元件電極間接合層。而且,在通過燒結(jié)漿料來形成元件電極間接合層的至少一部分的情況下,燒結(jié)前與漿料接觸的部位發(fā)生氧化,故而氧濃度多半會局部性地變高。因此,燒結(jié)前夾持漿料的兩個部位的氧濃度高。另外,若反復(fù)多次利用漿料進行燒結(jié),則氧濃度高的部位同樣會兩處兩處地增加。因此,根據(jù)本發(fā)明,也可以理解為形成包括氧濃度沿厚度方向的變化超過規(guī)定基準(zhǔn)的多層高氧濃度層的元件電極間接合層。圖5A、圖5B是表示元件電極間接合層內(nèi)的氧濃度的圖,表示了一邊沿元件電極間接合層的厚度方向改變測定位置一邊測得的氧濃度。此外,在圖5A、圖5B中,在橫軸上表示測定位置,在縱軸上表示通過俄歇電子能譜法評估氧濃度的結(jié)果,在此,將所測得的氧濃度的峰值標(biāo)準(zhǔn)化地表示成100。另外,在圖5A中,利用虛線箭頭表示了Ni電鍍層LNe、通過燒結(jié)Ag漿料而形成的元件電極間接合層Lae的位置,在圖5B中,利用虛線箭頭表示了Ni電鍍層LNe、第一層L1、第二層L2、元件電極間接合層Lae的位置。在圖5A、圖5B這兩者中,表示了熱電元件存在于曲線圖的左側(cè)、電極存在于曲線圖的右側(cè)的狀態(tài)。如圖5A所示,氧濃度在Ni電鍍層LNe與元件電極間接合層Lae的界面處增加,在其它區(qū)域中下降。其結(jié)果是,存在氧濃度沿元件電極間接合層的厚度方向的變化超過規(guī)定基準(zhǔn)(閾值)的位置,可以將以這些位置為界面的層定義為高氧濃度層。在圖5A中,利用單點劃線表示了界面的位置,把由界面夾持的區(qū)域表示成了高氧濃度層Lo。如此,在元件電極間接合層Lae內(nèi),由于Ag漿料內(nèi)含有的氧的原因而形成有高氧濃度層Lo,在如本實施例那樣進行一次燒結(jié)的情況下,高氧濃度層Lo形成在兩個部位。因此,也可以將發(fā)明理解為,本實施例的元件電極間接合層Lae包括多層高氧濃度層Lo。同樣,在圖5B所示的元件電極間接合層Lae中,如圖5B所示,氧濃度在第一層L1與第二層L2的界面處增加,在其它區(qū)域中下降。其結(jié)果是,存在氧濃度沿元件電極間接合層的厚度方向的變化超過規(guī)定基準(zhǔn)(閾值)的位置,可以將以這些位置為界面的層定義為高氧濃度層。在圖5B中,也利用單點劃線表示了界面的位置,也把由界面夾持的區(qū)域表示成了高氧濃度層Lo。如此,在元件電極間接合層Lae內(nèi),由于作為第二層L2的基礎(chǔ)的Ag電鍍層及Ag漿料內(nèi)含有的氧的原因而形成有高氧濃度層Lo,在如本實施例那樣進行一次燒結(jié)的情況下,高氧濃度層Lo形成在兩個部位。因此,也可以將發(fā)明理解為,本實施例的元件電極間接合層Lae包括多層高氧濃度層Lo。而且,通過燒結(jié)包含小于100nm的金屬粒子的漿料來形成元件電極間接合層即可,既可以通過一次燒結(jié)來形成元件電極間接合層,也可以通過多次燒結(jié)來形成元件電極間接合層。例如,也可以通過反復(fù)多次執(zhí)行涂覆包含金屬粒子的漿料并進行燒結(jié)的工序,來制造所需厚度的元件電極間接合層。而且,在上述實施方式的熱電轉(zhuǎn)換組件中,說明了使用將高溫塊體Pnh(Pph)與低溫塊體Pnl(Ppl)通過材料間接合層Lam接合的熱電元件Pn(Pp)的例子。然而,在使用不具備上述材料間接合層的熱電元件的熱電轉(zhuǎn)換組件中,也能夠使用相同的元件電極間接合層Lae。即,參照圖6,其它實施方式的熱電轉(zhuǎn)換組件使用了不具備材料間接合層Lam的電熱元件Pn′(或者Pp′)。在電極E之間,沿?zé)犭娫暮穸确较蛞来涡纬捎蠳i電鍍層(元件電極間防擴散層)LNe、通過燒結(jié)漿料而形成的元件電極間接合層Lae、Ni電鍍層(元件電極間防擴散層)LNe、電熱元件Pn′(或者Pp′)、Ni電鍍層(元件電極間防擴散層)LNe、通過燒結(jié)漿料而形成的元件電極間接合層Lae、Ni電鍍層(元件電極間防擴散層)LNe。能夠通過燒結(jié)包含小于100nm的金屬粒子的漿料來形成電極E與熱電元件Pn′(或Pp′)之間的元件電極間接合層Lae,并能夠使該元件電極間接合層Lae形成為30μm以上的厚度。該元件電極間接合層Lae也具有與圖4所示的元件電極間接合層Lae相同的結(jié)構(gòu)及性質(zhì)。通過使用上述元件電極間接合層Lae,能夠緩和隨著熱電轉(zhuǎn)換組件的使用而產(chǎn)生的熱應(yīng)力,防止熱電轉(zhuǎn)換組件破損。本申請要求于2012年2月17日申請的日本專利申請?zhí)枮?012-32491的專利申請的優(yōu)先權(quán),其內(nèi)容被引用到本文中。