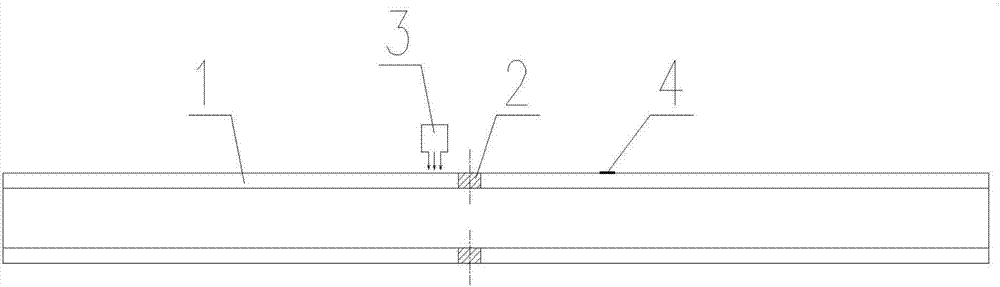
本發(fā)明屬于焊接質(zhì)量檢測(cè)
技術(shù)領(lǐng)域:
,具體涉及一種基于熱傳導(dǎo)方程的同種焊接件焊接質(zhì)量檢測(cè)方法。
背景技術(shù):
:焊接是工業(yè)上廣泛使用的一種不可拆的連接方式,它是將需要連接的金屬零件在連接處局部加熱至熔化或用熔化的金屬材料填充,或用加壓等方法使其熔合連接在一起,焊接具有施工簡(jiǎn)單,連接可靠等優(yōu)點(diǎn)。在所有運(yùn)用焊接方法進(jìn)行構(gòu)件組裝、結(jié)構(gòu)安裝、機(jī)械生產(chǎn)、船舶制造的領(lǐng)域,焊接質(zhì)量檢測(cè)是必不可少的環(huán)節(jié)。焊接質(zhì)量檢測(cè)方法可分為無損檢測(cè)法與有損檢測(cè)法。無損檢測(cè)法與有損檢測(cè)法相比,具有勿庸置疑的優(yōu)勢(shì)。目前的焊接質(zhì)量無損檢測(cè)方法主要包括:滲透檢驗(yàn)、磁粉檢驗(yàn)、射線檢驗(yàn)、超聲波檢查等。滲透檢驗(yàn)是利用帶有熒光染料或紅色染料的滲透劑的滲透作用,顯示缺陷痕跡的無損檢驗(yàn)法,常用的有熒光探傷和著色探傷。將擦洗干凈的焊件表面噴涂滲透性良好的紅色著色劑,待滲透到焊縫表面的缺陷內(nèi),將焊件表面擦凈。再涂上一層白色顯示液,待干燥后,滲入到焊件缺陷中的著色劑由于毛細(xì)作用被白色顯示劑所吸附,在表面呈現(xiàn)出缺陷的紅色痕跡。滲透檢驗(yàn)要求焊接件表面光潔,檢驗(yàn)效率低。磁粉檢驗(yàn)是將焊件在強(qiáng)磁場(chǎng)中磁化,使磁力線通過焊縫,遇到焊縫表面或接近表面處的缺陷時(shí),產(chǎn)生漏磁而吸引撒在焊縫表面的磁性氧化鐵粉。根據(jù)鐵粉被吸附的痕跡就能判斷缺陷的位置和大小。磁粉檢驗(yàn)僅適用于檢驗(yàn)鐵磁性材料表面或近表面處的缺陷。射線檢驗(yàn)有x射線和y射線檢驗(yàn)兩種。當(dāng)射線透過被檢驗(yàn)的焊縫時(shí),如有缺陷,則通過缺陷處的射線衰減程度較小,因此在焊縫背面的底片上感光較強(qiáng),底片沖洗后,會(huì)在缺陷部位顯示出黑色斑點(diǎn)或條紋。x射線照射時(shí)間短、速度快,但設(shè)備復(fù)雜、費(fèi)用大,穿透能力較y射線小,被檢測(cè)焊件厚度應(yīng)小于30mm。而y射線檢驗(yàn)設(shè)備輕便、操作簡(jiǎn)單,穿透能力強(qiáng),能照投300mm的鋼板。但檢測(cè)小于50mm以下焊縫時(shí),靈敏度不高。超聲波檢驗(yàn)是利用超聲波能在金屬內(nèi)部傳播,并在遇到兩種介質(zhì)的界面時(shí)會(huì)發(fā)生反射和折射的原理來檢驗(yàn)焊縫內(nèi)部缺陷的。當(dāng)超聲波通過探頭從焊件表面進(jìn)入內(nèi)部,遇到缺陷和焊件底面時(shí),發(fā)生反射,由探頭接收后在屏幕上顯示出脈沖波形。根據(jù)波形即可判斷是否有缺陷和缺陷位置。由于探頭與檢測(cè)件之間存在反射面,因此超聲波檢查時(shí)應(yīng)在焊件表面涂抹耦合劑。超聲波檢查要求焊接處表面平整且足夠大,否則探頭無法放置。對(duì)于大批量同種焊接件,傳統(tǒng)焊接質(zhì)量無損檢測(cè)方法,其檢測(cè)設(shè)備復(fù)雜,檢測(cè)工序繁瑣,檢測(cè)成高,檢測(cè)效率低。并且傳統(tǒng)焊接質(zhì)量無損檢測(cè)方法受到焊接件材料、厚度等諸多因素的限制。技術(shù)實(shí)現(xiàn)要素:本發(fā)明的目的在于克服現(xiàn)有技術(shù)的不足,提供一種基于熱傳導(dǎo)方程的同種焊接件焊接質(zhì)量檢測(cè)方法,其能夠快速、高效檢測(cè)同種焊接件焊接質(zhì)量是否合格,省去傳統(tǒng)焊接質(zhì)量無損檢測(cè)繁瑣工序,簡(jiǎn)單經(jīng)濟(jì)、檢測(cè)效率高。本發(fā)明的目的是這樣實(shí)現(xiàn)的:一種基于熱傳導(dǎo)方程的同種焊接件焊接質(zhì)量檢測(cè)方法,所述熱傳導(dǎo)方程為傅里葉熱傳導(dǎo)方程,如下式:式中:δq為傳導(dǎo)熱量,λ為導(dǎo)熱系數(shù),表示沿x方向的溫度變化率,δs為傳熱截面積,δt為傳熱時(shí)間;基于熱傳導(dǎo)方程的同種焊接件焊接質(zhì)量檢測(cè)方法包括如下步驟:步驟一,對(duì)于同種批量焊接件,待其冷卻至室溫后,選取n個(gè)焊接件,在該n個(gè)焊接件焊縫的一側(cè)采用穩(wěn)定熱源對(duì)焊接件施加熱能,同時(shí)在焊縫的另一側(cè)設(shè)置測(cè)溫點(diǎn),每間隔時(shí)間δt1,測(cè)一次該測(cè)溫點(diǎn)溫度,計(jì)算出該測(cè)溫點(diǎn)溫度相對(duì)室溫的升高值,并記錄;步驟二,對(duì)于步驟一中選取的n個(gè)焊接件進(jìn)行力學(xué)拉伸實(shí)驗(yàn)來判斷焊接質(zhì)量是否合格,對(duì)于滿足設(shè)計(jì)最低要求的焊接件作為標(biāo)準(zhǔn)件,其步驟一中測(cè)溫點(diǎn)相對(duì)室溫的升高值δt1作為標(biāo)準(zhǔn)值;步驟三,待檢測(cè)的焊接件冷卻至室溫后,在其焊縫的一側(cè)采用與步驟一中相同熱源對(duì)焊接件施加熱能,同時(shí)在焊縫的另一側(cè)設(shè)置測(cè)溫點(diǎn),且控制熱源以及測(cè)溫點(diǎn)在焊接件上的位置與步驟一中相同,每間隔時(shí)間δt1,測(cè)一次該測(cè)溫點(diǎn)溫度,計(jì)算出該測(cè)溫點(diǎn)溫度相對(duì)室溫的升高值δt2,并記錄;步驟四,將步驟三中記錄的溫度升高值δt2與步驟二中標(biāo)準(zhǔn)件的溫度升高值δt1比較,δt2等于δt1,判斷焊接質(zhì)量合格,δt2小于δt1,判斷焊接質(zhì)量不合格。由上述技術(shù)方案可知,本發(fā)明基于傅里葉熱傳導(dǎo)公式,對(duì)焊接質(zhì)量進(jìn)行檢測(cè),當(dāng)焊縫內(nèi)部有裂紋、氣孔或焊接不飽滿時(shí),焊縫處的傳熱截面積δs小于標(biāo)準(zhǔn)值,當(dāng)焊縫內(nèi)部有夾渣時(shí),因?yàn)閵A渣的綜合導(dǎo)熱系數(shù)λ小于焊體,這些都導(dǎo)致傳熱時(shí)間δt內(nèi)傳過焊縫的熱能δq減小,從而導(dǎo)致測(cè)溫點(diǎn)的溫度升高值低于標(biāo)準(zhǔn)值,據(jù)此可判斷焊接質(zhì)量存在問題。該基于熱傳導(dǎo)方程的同種焊接件焊接質(zhì)量檢測(cè)方法與傳統(tǒng)焊接質(zhì)量無損檢測(cè)方法相比,無需復(fù)雜設(shè)備及工序,對(duì)于大批量同種焊接件的焊接質(zhì)量檢測(cè),其檢測(cè)效率更高,成本更低。并且本發(fā)明方法沒有檢測(cè)厚度的限制。進(jìn)一步的,所述熱源與測(cè)溫點(diǎn)的連線與焊縫中心線垂直。進(jìn)一步的,所述測(cè)溫點(diǎn)到焊縫中心線的距離大于熱源到焊縫中心線的距離。熱量從熱源通過焊縫傳遞到測(cè)溫點(diǎn),測(cè)溫點(diǎn)到焊縫中心線的距離大于熱源到焊縫中心線的距離,可以檢測(cè)更寬范圍內(nèi)的焊縫的焊接質(zhì)量。進(jìn)一步的,步驟一和步驟三中采用激光照射燈照射焊接件,對(duì)焊接件施加熱能。激光照射燈方向性強(qiáng),對(duì)焊接件施加熱源穩(wěn)定。進(jìn)一步的,步驟一和步驟三中間隔時(shí)間δt1為3秒。進(jìn)一步的,步驟一和步驟三中采用接觸式測(cè)溫儀或紅外線測(cè)溫儀測(cè)出測(cè)溫點(diǎn)溫度。附圖說明圖1是本發(fā)明同種焊接件焊接質(zhì)量檢測(cè)方法的流程示意圖;圖2是實(shí)施例中對(duì)鋼管焊接質(zhì)量的檢測(cè)示意圖;圖3是實(shí)施例中對(duì)鋼板焊接質(zhì)量的檢測(cè)示意圖;圖4是實(shí)驗(yàn)中焊接件鋼管a和鋼管b的傳熱特性曲線圖;附圖中,1-焊接件;2-焊縫;3-熱源;4-測(cè)溫點(diǎn)。具體實(shí)施方式下面將結(jié)合附圖對(duì)本發(fā)明技術(shù)方案的實(shí)施例進(jìn)行詳細(xì)的描述。以下實(shí)施例僅用于更加清楚地說明本發(fā)明的技術(shù)方案,因此只作為示例,而不能以此來限制本發(fā)明的保護(hù)范圍。一種基于熱傳導(dǎo)方程的同種焊接件焊接質(zhì)量檢測(cè)方法,所述熱傳導(dǎo)方程為傅里葉熱傳導(dǎo)方程,如下式:式中:δq為傳導(dǎo)熱量,λ為導(dǎo)熱系數(shù),表示沿x方向的溫度變化率,δs為傳熱截面積,δt為傳熱時(shí)間。以焊接件1為鋼管、鋼板為例,如圖1至圖3所示,本發(fā)明所述的基于熱傳導(dǎo)方程的同種焊接件焊接質(zhì)量檢測(cè)方法是按下列步驟進(jìn)行:步驟一,對(duì)于同種批量焊接件1,待其冷卻至室溫后,選取n個(gè)焊接件1,在該n個(gè)焊接件焊縫2的一側(cè)采用穩(wěn)定熱源3對(duì)焊接件施加熱能,同時(shí)在焊縫2的另一側(cè)設(shè)置測(cè)溫點(diǎn)4,每間隔時(shí)間δt1,測(cè)一次該測(cè)溫點(diǎn)溫度,計(jì)算出該測(cè)溫點(diǎn)4溫度相對(duì)室溫的升高值,并記錄;步驟二,對(duì)于步驟一中選取的n個(gè)焊接件1進(jìn)行力學(xué)拉伸實(shí)驗(yàn)來判斷焊接質(zhì)量是否合格,對(duì)于滿足設(shè)計(jì)最低要求的焊接件1作為標(biāo)準(zhǔn)件,其步驟一中測(cè)溫點(diǎn)4相對(duì)室溫的升高值δt1作為標(biāo)準(zhǔn)值;步驟三,待檢測(cè)的焊接件1冷卻至室溫后,在其焊縫2的一側(cè)采用與步驟一中相同熱源3對(duì)焊接件1施加熱能,同時(shí)在焊縫2的另一側(cè)設(shè)置測(cè)溫點(diǎn)4,且控制熱源3以及測(cè)溫點(diǎn)4在焊接件1上的位置與步驟一中相同,每間隔時(shí)間δt1,測(cè)一次該測(cè)溫點(diǎn)4溫度,計(jì)算出該測(cè)溫點(diǎn)4溫度相對(duì)室溫的升高值δt2,并記錄;步驟四,將步驟三中記錄的溫度升高值δt2與步驟二中標(biāo)準(zhǔn)件的溫度升高值δt1比較,δt2等于δt1,判斷焊接質(zhì)量合格,δt2小于δt1,判斷焊接質(zhì)量不合格。所述熱源3與測(cè)溫點(diǎn)4的連線與焊縫2中心線垂直。且所述測(cè)溫點(diǎn)4到焊縫2中心線的距離大于熱源3到焊縫2中心線的距離。步驟一和步驟三中采用激光照射燈照射焊接件1,對(duì)焊接件1施加熱能。步驟一和步驟三中間隔時(shí)間δt1為3秒。步驟一和步驟三中采用接觸式測(cè)溫儀或紅外線測(cè)溫儀測(cè)出測(cè)溫點(diǎn)4溫度。步驟四,當(dāng)焊縫內(nèi)部有裂紋、氣孔或焊接不飽滿時(shí),焊縫處的傳熱截面積δs小于正常值,當(dāng)焊縫內(nèi)部有夾渣時(shí),因?yàn)閵A渣的綜合導(dǎo)熱系數(shù)λ小于焊體,這些都導(dǎo)致傳熱時(shí)間δt內(nèi)傳過焊縫的熱能δq減小,從而導(dǎo)致測(cè)溫點(diǎn)的溫度升高值低于標(biāo)準(zhǔn)值,據(jù)此可判斷焊接質(zhì)量存在問題。將步驟三中記錄的溫度升高值δt2與步驟二中標(biāo)準(zhǔn)件的溫度升高值δt1比較,δt2等于δt1,判斷焊接質(zhì)量合格,δt2小于δt1,判斷焊接質(zhì)量不合格。為了驗(yàn)證本發(fā)明基于熱傳導(dǎo)方程的同種焊接件焊接質(zhì)量檢測(cè)方法,發(fā)明人做了大量實(shí)驗(yàn),實(shí)驗(yàn)中,以外徑為45mm,壁厚為3mm的鋼管焊接件為實(shí)驗(yàn)對(duì)象,實(shí)驗(yàn)過程如下:在剛管a和鋼管b焊縫的一側(cè)施加熱能,焊縫的另一設(shè)置測(cè)溫點(diǎn),控制熱源與測(cè)溫點(diǎn)位置相同,每間隔3秒分別測(cè)出,鋼管a和鋼管b測(cè)溫點(diǎn)的溫度升高值,結(jié)果如下表所示:間隔時(shí)間03s6s9s12s鋼管a升高溫度024.26.59鋼管b升高溫度01.53.24.86.5表中數(shù)據(jù)繪制成傳熱特性曲線圖,如圖4所示,橫坐標(biāo)表示間隔時(shí)間,縱坐標(biāo)表示測(cè)溫點(diǎn)溫度升高值。從圖中可以看出焊接件鋼管b,檢測(cè)出測(cè)溫點(diǎn)的溫度升高明顯比焊接件鋼管a慢。對(duì)焊接件鋼管a進(jìn)行受拉試驗(yàn),破壞拉力值為370kn,符合設(shè)計(jì)要求,對(duì)焊接件鋼管b進(jìn)行受拉試驗(yàn),破壞拉力值僅289kn,不符合設(shè)計(jì)要求,說明焊接件鋼管b焊接質(zhì)量存在問題。最后說明的是,以上優(yōu)選實(shí)施例僅用以說明本發(fā)明的技術(shù)方案而非限制,盡管通過上述優(yōu)選實(shí)施例已經(jīng)對(duì)本發(fā)明進(jìn)行了詳細(xì)的描述,但本領(lǐng)域技術(shù)人員應(yīng)當(dāng)理解,可以在形式上和細(xì)節(jié)上對(duì)其作出各種各樣的改變,而不偏離本發(fā)明權(quán)利要求書所限定的范圍。當(dāng)前第1頁12