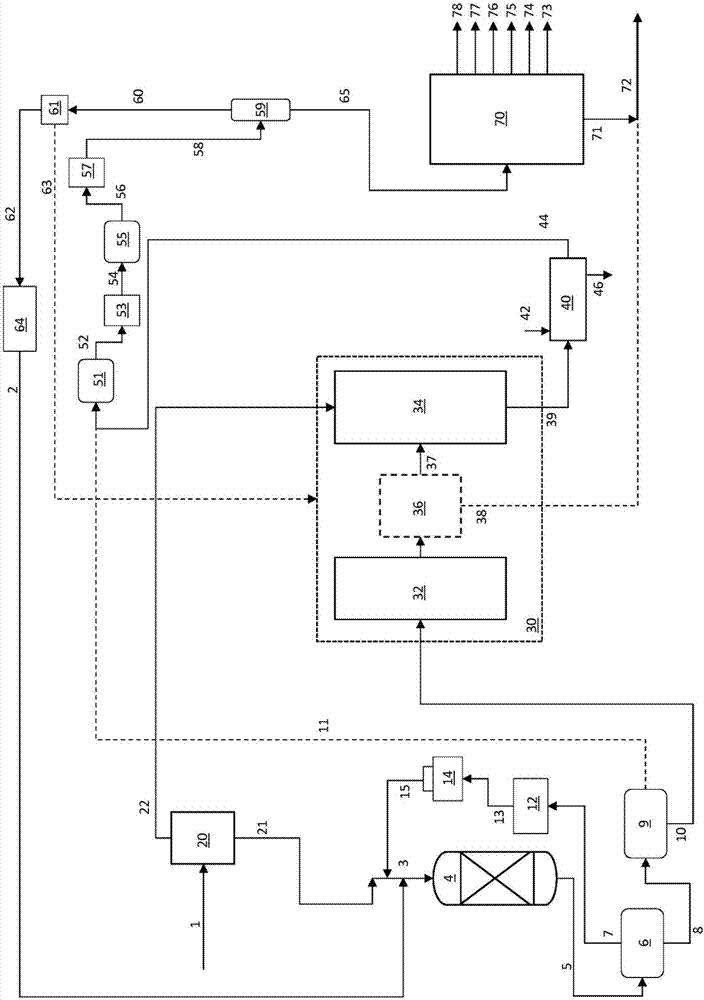
本申請是申請日為2013年1月27日、申請?zhí)枮?01380006605.5、發(fā)明名稱為“用于直接加工原油的包括氫再分布的整合的加氫處理和水蒸氣熱解方法”的發(fā)明專利申請的分案申請。相關(guān)申請本申請要求2012年1月27日提交的美國臨時(shí)專利申請?zhí)?1/591,814的權(quán)益,所述申請的公開內(nèi)容以引用的方式整體并入本文。發(fā)明背景發(fā)明領(lǐng)域本發(fā)明涉及一種用于直接加工原油以生產(chǎn)石油化學(xué)產(chǎn)品如烯烴和芳香族化合物的整合的加氫處理和水蒸氣熱解方法。相關(guān)技術(shù)說明低級烯烴(即,乙烯、丙烯、丁烯以及丁二烯)和芳香族化合物(即,苯、甲苯以及二甲苯)為石油化學(xué)和化學(xué)工業(yè)中廣泛使用的基本中間體。熱裂解或水蒸氣熱解為通常在存在水蒸氣的情況下并且在不存在氧的情況下用于形成這些材料的主要類型的方法。用于水蒸氣熱解的原料可以包括石油氣和餾出物如石腦油、煤油以及瓦斯油。這些原料的可獲得性通常是有限的并且需要原油精煉廠中的昂貴的且能量密集型的方法步驟。已經(jīng)使用重質(zhì)烴作為水蒸氣熱解反應(yīng)器的原料進(jìn)行了研究。常規(guī)重質(zhì)烴熱解操作中的主要缺點(diǎn)為焦炭形成。例如,用于重質(zhì)液體烴的水蒸氣裂解方法公開于美國專利號4,217,204中,其中將熔鹽的霧狀物引入到水蒸氣裂解反應(yīng)區(qū)中以試圖最小化焦炭形成。在使用具有3.1重量%的康拉遜殘?zhí)恐档陌⒗p質(zhì)原油的一個(gè)實(shí)例中,裂解設(shè)備能夠在存在熔鹽的情況下持續(xù)操作624小時(shí)。在不添加熔鹽的對比實(shí)例中,水蒸氣裂解反應(yīng)器在僅5小時(shí)之后由于反應(yīng)器中焦炭的形成而變得阻塞且不可操作。此外,使用重質(zhì)烴作為水蒸氣熱解反應(yīng)器的原料的烯烴和芳香族化合物的產(chǎn)率和分布不同于使用輕質(zhì)烴原料的那些。重質(zhì)烴具有比輕質(zhì)烴高的芳香族化合物含量,如由較高的美國礦務(wù)局關(guān)聯(lián)指數(shù)(bmci)所指示的。bmci是原料的芳香性的度量并且計(jì)算如下:bmci=87552/vapb+473.5*(sp.gr.)-456.8(1)其中:vapb=以蘭氏度(degreesrankine)計(jì)的體積平均沸點(diǎn),并且sp.gr.=原料的比重。隨著bmci降低,乙烯產(chǎn)量預(yù)期增加。因此,對于水蒸氣熱解來說,高鏈烷烴或低芳香族化合物進(jìn)料通常是優(yōu)選的,從而獲得較高產(chǎn)率的所需烯烴并且避免較高的不需要的產(chǎn)物和反應(yīng)器盤管段中的焦炭形成。水蒸氣裂解器中的絕對焦炭形成速率已由cai等人,“cokeformationinsteamcrackersforethyleneproduction,”chem.eng.&proc.,第41卷,(2002),199-214進(jìn)行了報(bào)道。一般來說,絕對焦炭形成速率是按照烯烴>芳香族化合物>鏈烷烴的遞增順序,其中烯烴代表重質(zhì)烯烴。為了能夠響應(yīng)于對這些石油化學(xué)產(chǎn)品的增長的需求,能夠以較大量獲得的其它類型的進(jìn)料如原油對于生產(chǎn)者來說具有吸引力。使用原油進(jìn)料將最小化或消除精煉廠在這些石油化學(xué)產(chǎn)品的生產(chǎn)中出現(xiàn)瓶頸現(xiàn)象的可能性。雖然水蒸氣熱解方法良好發(fā)展并且適合于其預(yù)定目的,但原料的選擇一直非常有限。發(fā)明概述本文的系統(tǒng)和方法提供一種與包括氫再分布的加氫加工區(qū)整合的水蒸氣熱解區(qū)以便允許直接加工原油原料來生產(chǎn)石油化學(xué)產(chǎn)品,包括烯烴和芳香族化合物。用于直接加工原油以生產(chǎn)烯屬和芳香族石油化學(xué)產(chǎn)品的整合的加氫處理和水蒸氣熱解方法包括:將所述原油分離成輕質(zhì)組分和重質(zhì)組分;將所述重質(zhì)組分和氫裝料至在有效于產(chǎn)生加氫加工的流出物的條件下操作的加氫加工區(qū),所述加氫加工的流出物具有降低的污染物含量、增加的鏈烷烴含量、降低的美國礦務(wù)局關(guān)聯(lián)指數(shù)以及增加的美國石油學(xué)會(huì)比重;將所述加氫加工的流出物和水蒸氣裝料至水蒸氣熱解區(qū)的對流段;d.加熱來自水蒸氣熱解區(qū)的所述對流段的所述混合物,并且將它傳遞至蒸氣-液體分離段;從所述水蒸氣熱解區(qū)去除來自所述蒸氣-液體分離段的殘余部分;將來自所述初始分離步驟的輕質(zhì)組分,來自所述蒸氣-液體分離段的輕質(zhì)部分以及水蒸氣裝料至所述水蒸氣熱解區(qū)的熱解段;從所述水蒸氣熱解區(qū)回收混合的產(chǎn)物流;分離所述混合的產(chǎn)物流;純化從所述混合的產(chǎn)物流回收的氫,并且將它再循環(huán)至所述加氫加工區(qū);并且從所述分離的混合產(chǎn)物流回收烯烴和芳香族化合物。如本文所用,術(shù)語“原油”應(yīng)被理解為包括來自常規(guī)來源的全原油、已經(jīng)經(jīng)歷一些預(yù)處理的原油。術(shù)語原油還將被理解為包括已經(jīng)經(jīng)受水-油分離和/或氣-油分離和/或脫鹽和/或穩(wěn)定化的原油。在一些實(shí)施方案中,本發(fā)明涉及以下項(xiàng)目:1.一種用于直接加工原油以生產(chǎn)烯屬和芳香族石油化學(xué)產(chǎn)品的整合的加氫處理和水蒸氣熱解方法,所述方法包括:a.將所述原油分離成輕質(zhì)組分和重質(zhì)組分;b.將所述重質(zhì)組分和氫裝料至在有效于產(chǎn)生加氫加工的流出物的條件下操作的加氫加工區(qū),所述加氫加工的流出物具有降低的污染物含量、增加的鏈烷烴含量、降低的美國礦務(wù)局關(guān)聯(lián)指數(shù)以及增加的美國石油學(xué)會(huì)比重;c.將所述加氫加工的流出物和水蒸氣裝料至水蒸氣熱解區(qū)的對流段;d.加熱來自步驟(c)的所述混合物,并且將它傳遞至蒸氣-液體分離段;e.從所述水蒸氣熱解區(qū)去除來自所述蒸氣-液體分離段的殘余部分;f.將來自步驟(a)的輕質(zhì)組分,來自所述蒸氣-液體分離段的輕質(zhì)部分以及水蒸氣裝料至所述水蒸氣熱解區(qū)的熱解段用于熱裂解;g.從所述水蒸氣熱解區(qū)回收混合的產(chǎn)物流;h.分離所述熱裂解的混合的產(chǎn)物流;i.純化在步驟(h)回收的氫,并且將它再循環(huán)至步驟(b);j.從所述分離的混合產(chǎn)物流回收烯烴和芳香族化合物;以及k.從所述分離的混合產(chǎn)物流回收熱解燃料油。2.如項(xiàng)目1所述的整合方法,其中步驟(h)包括用多個(gè)壓縮級壓縮所述熱裂解的混合產(chǎn)物流;使所述壓縮的熱裂解混合產(chǎn)物流經(jīng)受苛性堿處理以產(chǎn)生具有降低的硫化氫和二氧化碳含量的熱裂解的混合產(chǎn)物流;壓縮所述具有降低的硫化氫和二氧化碳含量的熱裂解的混合產(chǎn)物流;使所述壓縮的具有降低的硫化氫和二氧化碳含量的熱裂解的混合產(chǎn)物流脫水;從所述脫水的壓縮的具有降低的硫化氫和二氧化碳含量的熱裂解的混合產(chǎn)物流回收氫;以及從所述脫水的壓縮的具有降低的硫化氫和二氧化碳含量的熱裂解的混合產(chǎn)物流的剩余部分獲得如步驟(j)中的烯烴和芳香族化合物以及如步驟(k)中的熱解燃料油;以及步驟(i)包括純化從所述脫水的壓縮的具有降低的硫化氫和二氧化碳含量的熱裂解的混合產(chǎn)物流回收的氫以用于再循環(huán)至所述加氫加工區(qū)。3.如項(xiàng)目2所述的整合方法,其中從所述脫水的壓縮的具有降低的硫化氫和二氧化碳含量的熱裂解的混合產(chǎn)物流回收氫進(jìn)一步包括單獨(dú)地回收甲烷供用作所述熱裂解步驟中的燃燒器和/或加熱器的燃料。4.如項(xiàng)目1所述的整合方法,其中將來自所述蒸氣-液體分離段的所述殘余部分與步驟(k)中回收的熱解燃料油進(jìn)行共混。5.如項(xiàng)目1所述的整合方法,其中將所述加熱的加氫加工的流出物分離成蒸氣餾分和液體餾分是使用基于物理和機(jī)械分離的蒸氣-液體分離裝置。6.如項(xiàng)目5所述的整合方法,其中所述蒸氣-液體分離裝置包括具有進(jìn)入部分和過渡部分的預(yù)旋轉(zhuǎn)元件,所述進(jìn)入部分具有用于接收所述流動(dòng)的流體混合物的入口和曲線形導(dǎo)管,受控的旋流段,所述旋流段具有通過所述曲線形導(dǎo)管和所述旋流段的會(huì)合點(diǎn)毗連至所述預(yù)旋轉(zhuǎn)元件的入口,在所述旋流構(gòu)件的上部端的提升管段,蒸氣通過所述提升管段;以及液體收集器/沉降段,液體通過所述液體收集器/沉降段。7.如項(xiàng)目1所述的整合方法,其進(jìn)一步包括:在高壓分離器中分離所述加氫加工區(qū)反應(yīng)器流出物以便回收被清潔并且再循環(huán)至所述加氫加工區(qū)作為另外的氫來源的氣體部分;和液體部分,以及在低壓分離器中將來自所述高壓分離器的所述液體部分分離成氣體部分和液體部分,其中來自所述低壓分離器的所述液體部分是經(jīng)受熱裂解的所述加氫加工的流出物,并且來自所述低壓分離器的所述氣體部分在所述水蒸氣熱解區(qū)之后并且在步驟(h)中的分離之前與所述混合的產(chǎn)物流進(jìn)行組合。本發(fā)明的方法的其它方面、實(shí)施方案以及優(yōu)點(diǎn)在以下詳細(xì)討論。此外,應(yīng)理解前述信息與以下詳述都僅是各種方面和實(shí)施方案的說明性實(shí)例,并且旨在提供用于理解所要求保護(hù)的特征和實(shí)施方案的性質(zhì)和特性的概觀或框架。附圖是說明性的并且被提供來進(jìn)一步理解本發(fā)明的方法的不同方面和實(shí)施方案。附圖簡述本發(fā)明將在以下并且參照附圖進(jìn)行進(jìn)一步詳細(xì)描述,其中:圖1是本文所描述的整合方法的實(shí)施方案的方法流程圖;并且圖2a至圖2c是按照本文所描述的整合方法中的水蒸氣熱解單元的某些實(shí)施方案中所使用的蒸氣-液體分離裝置的透視圖、俯視圖以及側(cè)視圖進(jìn)行的示例性說明。發(fā)明詳述在圖1中示出包括具有氫再分布的整合的加氫加工和水蒸氣熱解方法和系統(tǒng)的方法流程圖。所述整合的系統(tǒng)總體上包括初始進(jìn)料分離區(qū)20、選擇性催化加氫加工區(qū)、水蒸氣熱解區(qū)30以及產(chǎn)物分離區(qū)。一般來說,將原油進(jìn)料閃蒸,借此較輕餾分(沸點(diǎn)在含有最少的要求進(jìn)一步裂解的烴和含有易于釋放的氫范圍內(nèi),例如高達(dá)約185℃)被直接傳遞至水蒸氣熱解區(qū),并且僅必要的餾分,即具有小于預(yù)定的氫含量的餾分進(jìn)行加氫加工。這是有利的,因?yàn)樗诩託浼庸し磻?yīng)器中提供增加的氫分壓,從而經(jīng)由飽和提高氫轉(zhuǎn)移的效率。這將降低氫溶液損失和h2消耗。原油進(jìn)料中含有的易于釋放的氫進(jìn)行再分布以最大化如乙烯的產(chǎn)物的產(chǎn)率。氫的再分布允許重質(zhì)產(chǎn)物的總體降低和輕質(zhì)烯烴的增加的產(chǎn)生。第一分離區(qū)20包括用于接收原料流1的入口,用于排出輕質(zhì)餾分22的出口,以及用于排出重質(zhì)餾分226的出口。分離區(qū)20可為單級分離裝置,如分餾點(diǎn)在約150℃至約260℃范圍內(nèi)的閃蒸分離器。在某些實(shí)施方案中,輕質(zhì)餾分22可為石腦油餾分。表1示出基于不同分餾點(diǎn)的氫含量。在另外的實(shí)施方案中,分離區(qū)20包括旋流相分離裝置、或基于蒸氣和液體的物理或機(jī)械分離的其它分離裝置或基本上由其組成(即,在不存在閃蒸區(qū)的情況下操作)。蒸氣-液體分離裝置的一個(gè)實(shí)例通過并且參照圖2a至圖2c進(jìn)行說明。蒸氣-液體分離裝置的類似安排還描述于美國專利公布號2011/0247500中,所述專利以引用的方式整體并入本文。在所述分離區(qū)包括基于蒸氣和液體的物理或機(jī)械分離的分離裝置或基本上由其組成的實(shí)施方案中,分餾點(diǎn)可以基于氣化溫度和進(jìn)入裝置的材料的流體速度進(jìn)行調(diào)整表1輕質(zhì)餾分的沸點(diǎn)(℃)氫含量(%)15015.2218014.8820014.7326014.34加氫加工區(qū)包括具有入口的加氫加工反應(yīng)區(qū)4,所述入口用于接收輕質(zhì)烴餾分21與從水蒸氣熱解產(chǎn)物流再循環(huán)的氫2的混合物和在必要時(shí)補(bǔ)充氫。加氫加工反應(yīng)區(qū)4進(jìn)一步包括用于排出加氫加工的流出物5的出口。來自所述一個(gè)或多個(gè)加氫加工反應(yīng)器的反應(yīng)器流出物5在熱交換器(未示出)中進(jìn)行冷卻并且送至高壓分離器6。分離器頂部物7在胺單元12中進(jìn)行清潔并且所得到的富含氫的氣體流13被傳遞至再循環(huán)壓縮機(jī)14以便在所述加氫加工反應(yīng)器中用作再循環(huán)氣體15。來自高壓分離器6的呈大致上液相形式的底部物流8進(jìn)行冷卻并且引入至低壓冷分離器9,在所述低壓冷分離器中所述底部物流被分離成氣體流和液體流10。來自低壓冷分離器的氣體包括氫、h2s、nh3以及任何輕質(zhì)烴如c1-c4烴。通常這些氣體被送去進(jìn)一步加工如燃燒加工(flareprocessing)或燃料氣體加工。根據(jù)本文的某些實(shí)施方案,通過將包含氫、h2s、nh3以及任何輕質(zhì)烴如c1-c4烴的水蒸氣氣體流11與水蒸氣裂解器產(chǎn)物44進(jìn)行組合來回收氫。液體流10的全部或一部分用作水蒸氣熱解區(qū)30的進(jìn)料。水蒸氣熱解區(qū)30總體上包括對流段32和熱解段34,所述熱解段可以基于本領(lǐng)域已知的水蒸氣熱解單元操作來進(jìn)行操作,即在存在水蒸氣的情況下將熱裂解進(jìn)料裝料至所述對流段。此外,在如本文所描述的某些任選的實(shí)施方案中(如在圖1中用虛線所指示的),蒸氣-液體分離段36包括在段32與段34之間。來自對流段32的加熱的水蒸氣裂解進(jìn)料通過的蒸氣-液體分離段36可以是基于蒸氣和液體的物理或機(jī)械分離的分離裝置。在一個(gè)實(shí)施方案中,蒸氣-液體分離裝置通過并且參照圖2a至圖2c進(jìn)行說明。蒸氣-液體分離裝置的類似安排還描述于美國專利公布號2011/0247500中,所述專利以引用的方式整體并入本文。在這種裝置中,蒸氣和液體以旋流幾何形狀流動(dòng)通過,由此所述裝置等溫地并且在非常低的停留時(shí)間下操作。一般來說,蒸氣以環(huán)形模式渦旋以產(chǎn)生力,較重的液滴和液體待被捕獲并且引導(dǎo)穿過至液體出口作為燃料油38,例如,其被添加至熱解燃料油共混物,并且蒸氣被引導(dǎo)穿過蒸氣出口作為熱解段34的裝料37。氣化溫度和流體速度被改變以調(diào)整近似溫度分界點(diǎn),例如在某些實(shí)施方案中與殘余燃料油共混物相容,例如在約540℃。淬火區(qū)40包括與水蒸氣熱解區(qū)30的出口處于流體連通的入口、用于容許淬火溶液42進(jìn)入的入口、用于排出淬火的混合的產(chǎn)物流44的出口以及用于排出淬火溶液46的出口。一般來說,中間經(jīng)過淬火的混合的產(chǎn)物流44被轉(zhuǎn)化成中間產(chǎn)物流65和氫62,氫在本發(fā)明方法中進(jìn)行純化并且在加氫加工反應(yīng)區(qū)4中用作再循環(huán)氫氣流2。中間產(chǎn)物流65通常在分離區(qū)70中分餾成最終產(chǎn)物和殘余物,所述分離區(qū)可以為一個(gè)或多個(gè)分離單元,如多個(gè)分餾塔,包括脫乙烷塔,脫丙烷塔以及脫丁烷塔,例如如本領(lǐng)域的普通技術(shù)人員所已知的。例如,適合的設(shè)備描述于“ethylene,”ullmann’sencyclopediaofindustrialchemistry,第12卷,第531頁至581頁,具體地說圖24、圖25以及圖26中,所述文獻(xiàn)以引用的方式并入本文一般來說,產(chǎn)物分離區(qū)70包括與產(chǎn)物流65和多個(gè)產(chǎn)物出口73至78處于流體連通的入口,所述多個(gè)產(chǎn)物出口包括用于排出甲烷的出口78、用于排出乙烯的出口77、用于排出丙烯的出口76、用于排出丁二烯的出口75、用于排出混合的丁烯的出口74以及用于排出熱解汽油的出口73。此外,提供用于排出熱解燃料油71的出口。任選地,來自蒸氣-液體分離段36的燃料油部分38與熱解燃料油71相組合并且可被抽出作為熱解燃料油共混物72,例如,有待在非現(xiàn)場精煉廠中進(jìn)行進(jìn)一步加工的低硫燃料油共混物。應(yīng)注意,雖然示出了六個(gè)產(chǎn)品出口,可以取決于(例如)所采用的分離單元的安排以及產(chǎn)量和分布要求而提供更少或更多產(chǎn)品出口。在采用圖1中所示的安排的方法的實(shí)施方案中,原油原料1在第一分離區(qū)20分離成輕質(zhì)餾分22和重質(zhì)餾分21。輕質(zhì)餾分22被輸送至熱階段36,即繞過加氫加工區(qū),以與水蒸氣裂解的中間產(chǎn)物部分進(jìn)行組合并且產(chǎn)生如本文所描述的混合產(chǎn)物流。重質(zhì)餾分21與有效量的氫2和15進(jìn)行混合以形成組合流3。將混合物3在300℃至450℃范圍中的溫度下裝料至選擇性加氫加工反應(yīng)區(qū)4的入口。在某些實(shí)施方案中,加氫加工反應(yīng)區(qū)4包括如共同擁有的美國專利公布號2011/0083996和pct專利申請公布號wo2010/009077、wo2010/009082、wo2010/009089以及wo2009/073436中描述的一個(gè)或多個(gè)單元操作,所述專利全部以引用的方式整體并入本文。例如,加氫加工區(qū)可以包括含有有效量的加氫脫金屬催化劑的一個(gè)或多個(gè)床,和含有有效量的具有加氫脫芳構(gòu)化、加氫脫氮、加氫脫硫和/或加氫裂解功能的加氫加工催化劑的一個(gè)或多個(gè)床。在另外的實(shí)施方案中,加氫加工反應(yīng)區(qū)4包括多于兩個(gè)催化劑床。在其它實(shí)施方案中,加氫加工反應(yīng)區(qū)4包括各自含有一個(gè)或多個(gè)(例如)不同功能的催化劑床的多個(gè)反應(yīng)容器。加氫加工反應(yīng)區(qū)4在有效于使原油原料加氫脫金屬、加氫脫芳構(gòu)化、加氫脫氮、加氫脫硫和/或加氫裂解的參數(shù)下操作。在某些實(shí)施方案中,使用以下條件進(jìn)行加氫加工:在300℃至450℃范圍中的操作溫度;在30巴至180巴范圍中的操作壓力;以及在0.1h-1至10h-1范圍中的液時(shí)空速。來自加氫加工區(qū)4的反應(yīng)器流出物5在交換器(未示出)中進(jìn)行冷卻并且送至高壓冷或熱分離器6。分離器頂部物7在胺單元12中進(jìn)行清潔并且所得到的富含氫的氣體流13被傳遞至再循環(huán)壓縮機(jī)14以便在加氫加工反應(yīng)區(qū)4中用作再循環(huán)氣體15。呈大致上液相的來自高壓分離器6的分離器底部物8進(jìn)行冷卻并且然后引入至低壓冷分離器9。包含氫、h2s、nh3以及任何輕質(zhì)烴(其可以包括c1-c4烴)的剩余氣體流11可常規(guī)地從低壓冷分離器吹掃出并且送去進(jìn)一步加工,如燃燒加工或燃料氣體加工。在本發(fā)明的方法的某些實(shí)施方案中,通過將流11(如由虛線所指示)與來自水蒸氣裂解器產(chǎn)物的裂解氣體流44組合來回收氫。來自低壓分離器9的底部物10被傳遞至水蒸氣熱解區(qū)30。加氫加工的流出物10包含降低的污染物(即,金屬、硫以及氮)含量、增加的鏈烷烴含量、降低的bmci、以及增加的美國石油學(xué)會(huì)(api)比重。加氫加工的流出物10在存在有效量的水蒸氣(例如經(jīng)由水蒸氣入口(未示出)容許進(jìn)入的)的情況下被傳遞至對流段32。在對流段32中,混合物被加熱至預(yù)定溫度,例如,使用一個(gè)或多個(gè)廢熱流或其它適合的加熱安排。輕質(zhì)餾分與水蒸氣的經(jīng)過加熱的混合物被傳遞至蒸氣-液體分離段36,以排出部分38作為適合于與熱解燃料油71共混的燃料油組分。剩余的烴部分連同來自第一分離區(qū)20的輕質(zhì)餾分22(例如石腦油餾分)一起被輸送至熱解段34以產(chǎn)生混合的產(chǎn)物流39。水蒸氣熱解區(qū)30在有效于使流出物10裂解成所需產(chǎn)物(包括乙烯、丙烯、丁二烯、混合的丁烯和熱解汽油)的參數(shù)下操作。在某些實(shí)施方案中,使用以下條件進(jìn)行水蒸氣裂解:對流段中和熱解段中400℃至900℃范圍中的溫度;對流段中0.3:1至2:1范圍的水蒸氣與烴比例;以及對流段中和熱解段中0.05秒至2秒范圍中的停留時(shí)間。在某些實(shí)施方案中,蒸氣-液體分離段36包括一個(gè)或多個(gè)如圖2a至2c中所示的蒸氣液體分離裝置80。蒸氣液體分離裝置80是操作經(jīng)濟(jì)的并且無需維護(hù)的,因?yàn)樗恍枰娏蚧瘜W(xué)供應(yīng)。一般來說,裝置80包括三個(gè)端口,包括用于接收蒸氣-液體混合物的入口端口、分別用于排出和收集所分離的蒸氣和液體的蒸氣出口端口和液體出口端口。裝置80基于以下現(xiàn)象的組合進(jìn)行操作,包括進(jìn)入的混合物的線速度通過全局流動(dòng)預(yù)旋轉(zhuǎn)段轉(zhuǎn)化成旋轉(zhuǎn)速度、用于使蒸氣與液體(殘余物)預(yù)分離的受控離心作用、以及用于促進(jìn)蒸氣與液體(殘余物)的分離的旋流作用。為了獲得這些作用,裝置80包括預(yù)旋轉(zhuǎn)段88、受控的旋流垂直段90以及液體收集器/沉降段92。如圖2b中所示,預(yù)旋轉(zhuǎn)段88包括在截面(s1)與截面(s2)之間的受控的預(yù)旋轉(zhuǎn)元件和與受控的旋流垂直段90連接并且位于截面(s2)與截面(s3)之間的連接元件。來自具有直徑(d1)的入口82的蒸氣液體混合物在截面(s1)處切向進(jìn)入設(shè)備。根據(jù)以下等式,進(jìn)入流的進(jìn)入段(s1)的面積為入口82的面積的至少10%:預(yù)旋轉(zhuǎn)元件88界定曲線流動(dòng)路徑并且其特征為從入口截面s1至出口截面s2恒定的、減少的或增加的截面。受控的預(yù)旋轉(zhuǎn)元件的出口截面(s2)與入口截面(s1)之間的比例在某些實(shí)施方案中在0.7≤s2/s1≤1.4的范圍中?;旌衔锏男D(zhuǎn)速度取決于預(yù)旋轉(zhuǎn)元件38的中心線的曲率半徑(r1),其中所述中心線被定義為連結(jié)預(yù)旋轉(zhuǎn)元件88的連續(xù)截面表面的所有中心點(diǎn)的曲線線條。在某些實(shí)施方案中,曲率半徑(r1)在2≤r1/d1≤6的范圍中,其中開口角在150°≤αr1≤250°的范圍中。雖然被描繪為總體上正方形的,但入口段s1處的截面形狀可以為矩形、圓角矩形、圓形、橢圓形、或其它直線形、曲線形或上述形狀的組合。在某些實(shí)施方案中,沿流體通過的預(yù)旋轉(zhuǎn)元件38的曲線路徑的截面的形狀(例如)從總體上正方形形狀漸進(jìn)地變化至矩形形狀。元件88的截面漸進(jìn)地變化成矩形形狀有利地使開口面積最大化,從而允許氣體在早期階段與液體混合物分離并且得到均勻的速度分布,并且使流體流動(dòng)中的剪切應(yīng)力最小化。來自受控的預(yù)旋轉(zhuǎn)元件88的流體流從截面(s2)經(jīng)過段(s3)通過所述連接元件到達(dá)受控的旋流垂直段90。所述連接元件包括為打開的并且連接至受控的旋流垂直段90中的入口或與其成整體的開口區(qū)域。流體流在高旋轉(zhuǎn)速度下進(jìn)入受控的旋流垂直段90以產(chǎn)生旋流作用。連接元件出口截面(s3)與入口截面(s2)之間的比例在某些實(shí)施方案中在2≤s3/s1≤5的范圍中?;旌衔镌诟咝D(zhuǎn)速度下進(jìn)入旋流垂直段90。動(dòng)能減小并且蒸氣在旋流作用下與液體分離。旋流在旋流垂直段90的上部水平90a和下部水平90b中形成。在上部水平90a中,混合物以高蒸氣濃度為特征,而在下部水平90b中,混合物以高液體濃度為特征。在某些實(shí)施方案中,旋流垂直段90的內(nèi)徑d2在2≤d2/d1≤5的范圍內(nèi)并且沿其高度可為恒定的,上部部分90a的長度(lu)在1.2≤lu/d2≤3的范圍內(nèi),并且下部部分90b的長度(ll)在2≤ll/d2≤5的范圍內(nèi)。旋流垂直段90的接近蒸氣出口84的末端連接至部分打開的釋放提升管并且連接至水蒸氣熱解單元的熱解段。部分打開的釋放提升管的直徑(dv)在某些實(shí)施方案中在0.05≤dv/d2≤0.4的范圍中。因此,在某些實(shí)施方案中,并且取決于進(jìn)入的混合物的特性,其中的大體積分?jǐn)?shù)的蒸氣通過具有直徑dv的部分打開的釋放管從出口84離開裝置80。具有低的蒸氣濃度或不存在蒸氣濃度的液相(例如,殘余物)通過旋流垂直段90的具有截面區(qū)域s4的底部部分離開,并且收集在液體收集器和沉降管92中。旋流垂直段90與液體收集器和沉降管92之間的連接區(qū)域在某些實(shí)施方案中具有90°的角度。在某些實(shí)施方案中,液體收集器和沉降管92的內(nèi)徑在2≤d3/d1≤4的范圍中并且為跨管道長度恒定的,并且液體收集器和沉降管92的長度(lh)在1.2≤lh/d3≤5的范圍中。具有低蒸氣體積分?jǐn)?shù)的液體通過具有直徑dl并且位于所述沉降管的底部或接近其底部處的管道86從設(shè)備去除,所述直徑dl在某些實(shí)施方案中在0.05≤dl/d3≤0.4的范圍中。雖然各種構(gòu)件分開地進(jìn)行了描述并且具有單獨(dú)的部分,但本領(lǐng)域的普通技術(shù)人員應(yīng)理解,設(shè)備80可形成為一個(gè)整體結(jié)構(gòu),例如,它可以是澆鑄的或模制的,或它可以從單獨(dú)的零件進(jìn)行組裝,例如,通過焊接或以另外的方式將單獨(dú)的部件附接在一起,所述零件可能或可能不精確地對應(yīng)于本文所描述的構(gòu)件和部分。應(yīng)理解雖然各種尺寸被作為直徑列出,但這些值在所述部件零件不為圓柱形的實(shí)施方案中也可以是等效直徑?;旌系漠a(chǎn)物流39被傳遞至淬火區(qū)40的入口,其中淬火溶液42(例如,水和/或熱解燃料油)經(jīng)由單獨(dú)的入口引入,以產(chǎn)生具有降低的溫度(例如約300℃)的中間經(jīng)過淬火的混合產(chǎn)物流44,并且廢淬火溶液46被排出。來自裂解器的氣體混合物流出物39通常是氫、甲烷、烴、二氧化碳以及硫化氫的混合物。在用水或油淬火冷卻后,混合物44在多級壓縮機(jī)區(qū)51中(通常4至6級中)進(jìn)行壓縮以產(chǎn)生壓縮的氣體混合物52。壓縮的氣體混合物52在苛性堿處理單元53中進(jìn)行處理以產(chǎn)生耗盡硫化氫和二氧化碳的氣體混合物54。氣體混合物54在壓縮機(jī)區(qū)55中進(jìn)一步壓縮,并且所得到的裂解氣體56通常在單元57中經(jīng)受低溫處理以便脫水,并且通過使用分子篩進(jìn)行進(jìn)一步干燥。來自單元57的冷的裂解氣體流58被傳遞至脫甲烷塔59,從該塔產(chǎn)生含有來自所述裂解氣體流的氫和甲烷的塔頂物流60。來自脫甲烷塔59的底部物流65然后被送去在產(chǎn)物分離區(qū)70進(jìn)一步加工,所述產(chǎn)物分離區(qū)包括多個(gè)分餾塔,包括脫乙烷塔、脫丙烷塔以及脫丁烷塔。還可以采用具有不同順序的脫甲烷塔、脫乙烷塔、脫丙烷塔以及脫丁烷塔的工藝配置。根據(jù)本文的方法,在脫甲烷塔59處與甲烷分離和在單元61中氫回收之后,獲得具有通常80體積%-95體積%的純度的氫62。單元61中的回收方法包括低溫回收(例如,在約-157℃的溫度下)。氫氣流62然后被傳遞至氫純化單元64,如變壓吸附(psa)單元,以獲得具有99.9%+純度的氫氣流2;或膜分離單元,以獲得具有約95%純度的氫氣流2。純化的氫氣流2然后再循環(huán)回來以用作加氫加工區(qū)的必需氫的主要部分。此外,小比例可以用于乙炔、丙炔以及丙二烯的氫化反應(yīng)(未示出)。此外,根據(jù)本文的方法,甲烷流63可以任選地再循環(huán)至水蒸氣裂解器中以便用作燃燒器和/或加熱器的燃料。來自脫甲烷塔59的底部物流65被輸送至產(chǎn)物分離區(qū)70的入口以便被分離成分別經(jīng)由出口78、77、76、75、74以及73排出的甲烷、乙烯、丙烯、丁二烯、混合的丁烯以及熱解汽油。熱解汽油通常包含c5-c9烴,并且可以從這種截餾分提取苯、甲苯以及二甲苯。任選地,來自蒸氣-液體分離段36的排出部分38與熱解燃料油71(例如,在高于最低沸點(diǎn)c10化合物的沸點(diǎn)的溫度下沸騰的材料,被稱為“c10+”流)組合,并且混合流可被抽出作為熱解燃料油共混物72(例如,低硫燃料油共混物)以便在非現(xiàn)場精煉廠進(jìn)行進(jìn)一步加工。本文相對于圖1描述的系統(tǒng)的優(yōu)點(diǎn)包括反應(yīng)器中增加的氫分壓和經(jīng)由飽和提高的氫轉(zhuǎn)移效率。一般來說:pt=pa+pb+pc。(2)在本發(fā)明的情況下:pt=p石腦油+ph2+px+py。(3)如果去除p石腦油,則pt保持相同,且因此ph2(以及px和py)全部增加。速率(飽和)=k飽和[反應(yīng)物]x[ph2]。(4)本文描述的系統(tǒng)還降低溶液損失,并且降低h2消耗。這使得此系統(tǒng)有可能作為封閉或近似封閉的系統(tǒng)進(jìn)行操作。在某些實(shí)施方案中,選擇性加氫加工或加氫處理方法可以通過芳香族化合物(尤其是聚芳香族化合物)的飽和、接著溫和的加氫裂解來增加原料的鏈烷烴含量(或降低bmci)。當(dāng)加氫處理原油時(shí),污染物如金屬、硫以及氮可以通過使原料通過一系列執(zhí)行脫金屬化、脫硫和/或脫氮的催化功能的層狀催化劑去除。在一個(gè)實(shí)施方案中,用于進(jìn)行加氫脫金屬化(hdm)和加氫脫硫(hds)的催化劑的順序是如下:a.加氫脫金屬化催化劑。hdm段中的催化劑一般是基于γ氧化鋁載體,具有約140-240m2/g的表面積。這種催化劑被最佳描述為具有非常高的孔隙體積,例如,超過1cm3/g??紫洞笮”旧硗ǔV饕谴罂椎摹R筮@一點(diǎn)以提供催化劑表面和任選的摻雜劑上的金屬攝取的大容量。通常催化劑表面上的活性金屬為按照比例ni/ni+mo<0.15的鎳和鉬的硫化物。鎳的濃度在hdm催化劑上比其它催化劑低,因?yàn)橐恍╂嚭外C預(yù)期在去除過程中從原料本身沉積,從而充當(dāng)催化劑。所使用的摻雜劑可以為一種或多種磷(參見,例如,美國專利公布號us2005/0211603,其以引用的方式并入本文)、硼、硅以及鹵素。催化劑可以是呈氧化鋁擠出物或氧化鋁珠粒的形式。在某些實(shí)施方案中,氧化鋁珠粒用于在金屬攝取在床的頂部處將在30%至100%的范圍時(shí)促進(jìn)反應(yīng)器中的催化劑hdm床的卸載。b.中間催化劑也可以用于進(jìn)行hdm與hds功能之間的過渡。它具有中間金屬負(fù)載和孔隙大小分布。hdm/hds反應(yīng)器中的催化劑基本上為呈擠出物形式的基于氧化鋁的載體,任選地存在來自第vi族的至少一種催化金屬(例如,鉬和/或鎢),和/或來自第viii族的至少一種催化金屬(例如,鎳和/或鈷)。所述催化劑還任選地包含至少一種選自硼、磷、鹵素以及硅的摻雜劑。物理特性包括約140-200m2/g的表面積,至少0.6cm3/g的孔隙體積和為中孔并且在12至50nm范圍中的孔。c.hds段中的催化劑可包括具有基于γ氧化鋁的載體材料的那些,具有朝向hdm范圍的較高端的典型表面積,例如約180-240m2/g的范圍。hds的這種所需的更高表面產(chǎn)生相對較小的孔隙體積,例如,低于1cm3/g。所述催化劑包含至少一種來自第vi族的元素(如鉬)和至少一種來自第viii族的元素(如鎳)。所述催化劑還包含至少一種選自硼、磷、硅以及鹵素的摻雜劑。在某些實(shí)施方案中,鈷用于提供相對較高水平的脫硫?;钚韵嗟慕饘儇?fù)載為較高的,因?yàn)樗杌钚暂^高,這樣使得ni/ni+mo的摩爾比在0.1至0.3的范圍中,并且(co+ni)/mo摩爾比在0.25至0.85的范圍中。d.最終催化劑(其可任選地替代第二和第三催化劑)被設(shè)計(jì)來進(jìn)行原料的氫化(而不是加氫脫硫的主要功能),例如如appl.catal.ageneral,204(2000)251中所描述。所述催化劑也將通過ni促進(jìn)并且載體將是大孔γ氧化鋁。物理特性包括朝向hdm范圍的較高端的表面積,例如180-240m2/ggr。hds的這種所需的更高表面產(chǎn)生相對較小的孔隙體積,例如,低于1cm3/g。本文的方法和系統(tǒng)提供優(yōu)于已知的水蒸氣熱解裂解方法的改進(jìn),包括使用原油作為原料以生產(chǎn)石油化學(xué)產(chǎn)品如烯烴和芳香族化合物的能力。另外雜質(zhì)如金屬、硫以及氮化合物也從起始進(jìn)料顯著去除,這避免了最終產(chǎn)物的后處理。此外,從水蒸氣裂解區(qū)產(chǎn)生的氫再循環(huán)至加氫加工區(qū),以最小化對新鮮氫的需求。在某些實(shí)施方案中,本文所描述的整合的系統(tǒng)僅需要新鮮氫來啟動(dòng)操作。一旦反應(yīng)達(dá)到平衡,氫純化系統(tǒng)可提供足夠的高純度氫氣,以維持整個(gè)系統(tǒng)的操作。在以上和所附附圖中已描述了本發(fā)明的方法和系統(tǒng);然而,修改對于本領(lǐng)域的普通技術(shù)人員來說將是清楚的,并且本發(fā)明的保護(hù)范圍將由以下權(quán)利要求書所限定。當(dāng)前第1頁12