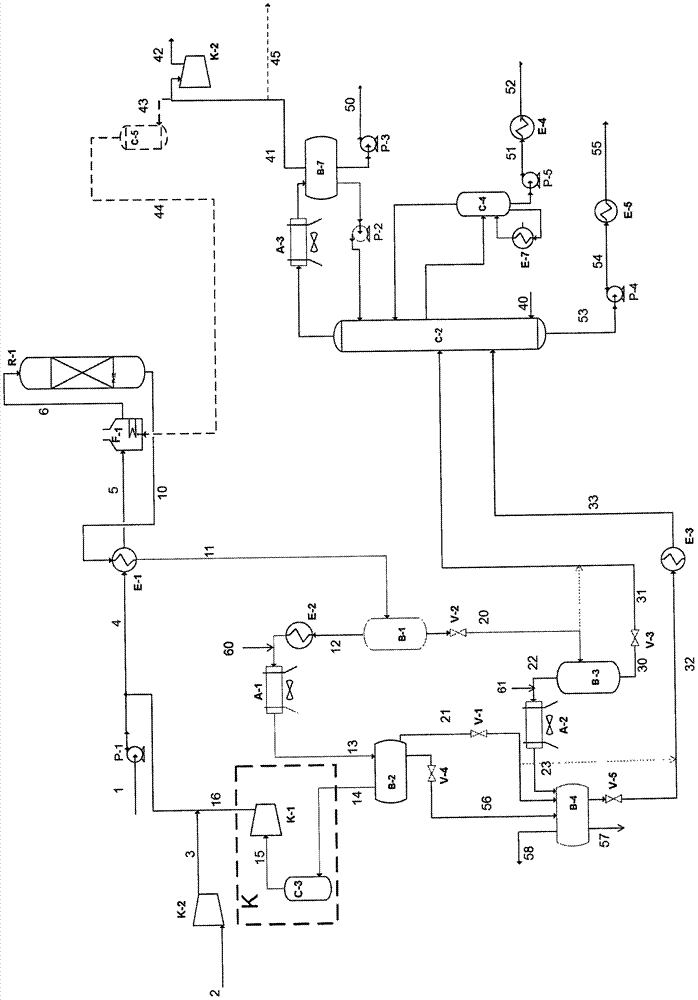
本發(fā)明涉及加氫處理或加氫轉(zhuǎn)化方法的領(lǐng)域。用于加氫處理或加氫轉(zhuǎn)化瓦斯油、減壓餾出物、常壓或減壓渣油或來(lái)自費(fèi)-托單元的流出物的常規(guī)方法通常包括用于分餾來(lái)自反應(yīng)段的流出物的分段,其主要具有兩個(gè)目的,即除去H2S和輕質(zhì)化合物,以及來(lái)自該單元的產(chǎn)物的主分餾。無(wú)論在絕對(duì)值上還是相對(duì)于整個(gè)過(guò)程,實(shí)現(xiàn)這兩個(gè)目的需要消耗能量并且代表了大量的投資和高的操作成本。
背景技術(shù):
:專利US3733260描述了用于瓦斯油的加氫脫硫的方法,其包括加氫脫硫反應(yīng)段,在高溫和高壓下將來(lái)自該段的流出物分離成氣體餾分和第一液體餾分,將所述氣相部分冷凝成基本上包含氫的氣體餾分和第二液體餾分,使用預(yù)處理的氫從第一和第二液體餾分中汽提H2S和輕質(zhì)烴,將汽提的烴分離成石腦油和瓦斯油,并將所述石腦油再循環(huán)到冷凝步驟。這種配置需要產(chǎn)生回流以進(jìn)行汽提,并且具有在汽提塔的頂部空氣冷凝器中消耗來(lái)自反應(yīng)段的流出物中所包含的一些能量的缺點(diǎn)。此外,由于供應(yīng)到汽提塔所需的最佳溫度低于下游分離所需的最低溫度,這意味著用于該分離的進(jìn)料必須被加熱。專利US3371029描述了用于分離來(lái)自烴轉(zhuǎn)化反應(yīng)器的含氫流出物的方法,其中在將主要的烴分離為石腦油、瓦斯油和較重的化合物上游不存在汽提H2S和烴。后一種配置具有的缺點(diǎn)在于,在除去H2S之后,不可避免地獲自在接近大氣壓的壓力下操作的主分離的酸性氣體必須在返回到煉油廠的燃料氣系統(tǒng)之前被壓縮。本發(fā)明通過(guò)最小化或甚至省去頂部分離壓縮機(jī),同時(shí)使過(guò)程的能量效率最大化來(lái)克服這些缺點(diǎn)。附圖說(shuō)明對(duì)于設(shè)施的相同設(shè)備,圖1和圖2具有相同的編號(hào)。圖1描述了根據(jù)本發(fā)明的方法的布置,其中向汽提塔C-1供應(yīng)來(lái)自中壓冷分離器鼓B-4的底部餾分、和接連地在高壓鼓B-1、然后中壓鼓B-3、然后低壓鼓B-5中分離獲自反應(yīng)段R-1的流出物之后獲得的最輕的餾分。向主分餾塔C-2供應(yīng)來(lái)自鼓B-5和來(lái)自汽提塔C-1的底部餾分。圖2描述了根據(jù)現(xiàn)有技術(shù)的方法的布置,其中既沒(méi)有鼓B-5也沒(méi)有汽提塔C-1。將獲自反應(yīng)段R-1的流出物接連地送到高壓鼓B-1、然后是中壓鼓B-3、然后直接與獲自鼓B-4的底部餾分一起送到主分餾塔C-2。技術(shù)實(shí)現(xiàn)要素:本發(fā)明描述了用于加氫處理或加氫轉(zhuǎn)化瓦斯油、減壓餾出物、常壓或減壓渣油或來(lái)自費(fèi)-托單元的流出物的設(shè)施,其至少包括:·反應(yīng)段R-1,·高壓熱分離器鼓B-1,向其供應(yīng)獲自反應(yīng)段R-1的流出物,并且將其底部物流供應(yīng)到分離器鼓B-5,·高壓冷分離器鼓B-2,向其供應(yīng)離開(kāi)高壓熱分離器鼓B-1的頂部物流,并且將其底部物流供應(yīng)到汽提塔C-1,·壓縮區(qū)K,其用于獲自B-2的稱為再循環(huán)氫的氣體流出物,·低壓熱分離器鼓B-5,向其供應(yīng)獲自B-1的液體物流,并且其頂部氣體流出物構(gòu)成汽提塔C-1的進(jìn)料的一部分,并且其液體流出物構(gòu)成分餾塔C-2的進(jìn)料的第一部分,·分離塔C-1(也稱為汽提塔),向其供應(yīng)獲自B-2的液體物流、和獲自B-5的氣體物流,其底部產(chǎn)物構(gòu)成分餾塔C-2的進(jìn)料的另一部分,·主分餾塔C-2,向其供應(yīng)來(lái)自汽提塔C-1的底部產(chǎn)物和獲自B-5底部的液體物流,并且其分離出以下餾分:石腦油(輕質(zhì)和重質(zhì))、柴油、煤油和渣油,·爐F-1,其用于加熱反應(yīng)段R-1的進(jìn)料和/或所述反應(yīng)段所需的氫的一部分。在根據(jù)本發(fā)明的設(shè)施的變體中,所述設(shè)施進(jìn)一步包括:·中壓熱分離器鼓B-3,向其供應(yīng)獲自B-1的液體物流,并且將其液體流出物供應(yīng)到鼓B-5,·中壓冷分離器鼓B-4,向其供應(yīng)獲自B-2的液體物流和獲自B-3的氣體物流,并且其液體流出物構(gòu)成汽提塔C-1的進(jìn)料的一部分。本發(fā)明還涉及使用上述設(shè)施對(duì)瓦斯油、減壓餾出物、常壓或減壓渣油進(jìn)行加氫處理或加氫轉(zhuǎn)化的方法。在根據(jù)本發(fā)明的方法中,分離塔C-1通常在以下條件下操作:總壓力在0.6至2.0MPa的范圍內(nèi),優(yōu)選在0.7至1.8MPa的范圍內(nèi)。在根據(jù)本發(fā)明的方法中,分餾塔C-2通常在以下壓力條件下操作:總壓力在0.1MPa至0.4MPa的范圍內(nèi),優(yōu)選在0.1MPa至0.3MPa的范圍內(nèi)。根據(jù)本發(fā)明的方法的一個(gè)變體,將含有殘留酸性氣體的獲自分餾塔C-2的頂部餾分的至少一部分送至在非常低的壓力下操作的滌氣塔C-5,以除去至少一部分H2S,然后將頂部餾分的所述部分通過(guò)作為用于反應(yīng)段的爐F-1中的燃料的補(bǔ)充來(lái)使用。根據(jù)本發(fā)明的方法的另一變體,將含有殘留酸性氣體的獲自分餾塔C-2的頂部餾分的至少一部分送至流化催化裂化單元(FCC)的酸性氣體壓縮機(jī)。最后,根據(jù)本發(fā)明的方法的進(jìn)一步變體,高壓熱分離器鼓B-1的溫度以使得主分餾塔C-2的進(jìn)料不需要爐的方式選擇。發(fā)明詳述本說(shuō)明書(shū)的其余部分提供了關(guān)于該方法的操作條件和在反應(yīng)段中使用的催化劑的補(bǔ)充信息。通常,在使用根據(jù)本發(fā)明的設(shè)施的方法中,反應(yīng)段R-1可以包括串聯(lián)或并聯(lián)設(shè)置的多個(gè)反應(yīng)器。反應(yīng)段的每個(gè)反應(yīng)器包括至少一個(gè)催化劑床。催化劑可以在固定床或膨脹床中使用,或者事實(shí)上在沸騰床中使用。在其中催化劑在固定床中使用的情況下,可以在至少一個(gè)反應(yīng)器中提供多個(gè)催化劑床。本領(lǐng)域技術(shù)人員已知的任何催化劑可以用于根據(jù)本發(fā)明的方法中,例如包含選自周期分類的第VIII族(新周期分類的第8、9和10族)的元素中的至少一種元素,以及任選地選自周期分類的第VIB族(新周期分類的第6族)的元素中的至少一種元素的催化劑。加氫處理或加氫轉(zhuǎn)化反應(yīng)段R-1的操作條件通常如下:溫度通常在約200℃至約460℃的范圍內(nèi),總壓力通常在約1MPa至約20MPa的范圍內(nèi),通常在2至20MPa的范圍內(nèi),優(yōu)選在2.5至18MPa的范圍內(nèi),并且高度優(yōu)選在3至18MPa的范圍內(nèi),每個(gè)催化步驟的液體進(jìn)料的總時(shí)空速通常在約0.1至約12的范圍內(nèi),優(yōu)選在約0.4至約10h-1的范圍內(nèi)(時(shí)空速定義為進(jìn)料的體積流量除以催化劑的體積),在根據(jù)本發(fā)明的方法中使用的再循環(huán)氫的純度通常在50體積%至100體積%的范圍內(nèi),相對(duì)于液體進(jìn)料的再循環(huán)氫的量通常在約50至約2500Nm3/m3的范圍內(nèi)。為了實(shí)施根據(jù)本發(fā)明的方法,可以使用包含在無(wú)定形載體上的至少一種具有加氫脫氫功能的金屬或金屬化合物的常規(guī)加氫轉(zhuǎn)化催化劑。該催化劑可以是包含來(lái)自第VIII族的金屬如鎳和/或鈷,并且通常結(jié)合有至少一種來(lái)自第VIB族的金屬如鉬和/或鎢的催化劑。作為實(shí)例,可以使用包含在無(wú)定形礦物載體上的0.5重量%至10重量%的鎳(以氧化鎳NiO表示)和1重量%至30重量%的鉬,優(yōu)選5重量%至20重量%的鉬(以氧化鉬MoO3表示)的催化劑。在催化劑中來(lái)自第VI和VIII族的金屬氧化物的總量通常在5重量%至40重量%的范圍內(nèi),優(yōu)選在7重量%至30重量%的范圍內(nèi)。來(lái)自第VI族的金屬(一種或多種)與來(lái)自第VIII族的金屬(一種或多種)的重量比(基于金屬氧化物表示)通常為約20至約1,并且通常為約10至約2。作為實(shí)例,載體選自氧化鋁、二氧化硅、二氧化硅-氧化鋁、氧化鎂、粘土和這些礦物中至少兩種的混合物。該載體也可以包括其它化合物,例如選自氧化硼、氧化鋯、氧化鈦和磷酸酐的氧化物。通常,使用氧化鋁載體,優(yōu)選η或γ氧化鋁。催化劑還可以含有助催化劑元素,例如磷和/或硼。該元素可以已經(jīng)被引入到基質(zhì)中,或者優(yōu)選地,其可以已經(jīng)沉積在載體上。硅也可以單獨(dú)或與磷和/或硼一起沉積在載體上。優(yōu)選地,催化劑包含沉積在載體如氧化鋁上的硅,任選地具有沉積在載體上的磷和/或硼,并且還包含至少一種來(lái)自第VIII族的金屬(Ni、Co)和至少一種來(lái)自第VIB族的金屬(Mo、W)。所述元素的濃度通常小于約20重量%(基于氧化物計(jì)),通常小于約10%。三氧化二硼(B2O3)的濃度通常為約0至約10重量%。另一種催化劑是包含至少一種來(lái)自第VIII族的金屬和至少一種來(lái)自第VIB族的金屬的二氧化硅-氧化鋁??捎糜诟鶕?jù)本發(fā)明的方法的另一種類型的催化劑是含有至少一種基質(zhì)、至少一種Y沸石和至少一種加氫脫氫金屬的催化劑。上述基質(zhì)、金屬和附加元素也可以形成該催化劑的組成的一部分。在專利申請(qǐng)WO00/71641、EP0911077以及US4738940和US4738941中描述了在根據(jù)本發(fā)明的方法的背景下使用的有利的Y沸石。已知具有堿性性質(zhì)的某些化合物如堿性氮顯著降低酸催化劑如二氧化硅-氧化鋁或沸石的裂化活性。催化劑(二氧化硅-氧化鋁、或甚至沸石)的酸性性質(zhì)越明顯,通過(guò)稀釋降低的堿性化合物濃度越大,這會(huì)對(duì)溫和加氫裂化反應(yīng)具有有利的影響。分離塔(汽提塔)C-1旨在除去獲自裂化的氣體(通常稱為酸性氣體),特別是獲自反應(yīng)段的反應(yīng)的H2S。所述塔C-1可以使用任何汽提氣體,例如含氫氣體或蒸汽。優(yōu)選地,使用蒸汽進(jìn)行根據(jù)本發(fā)明的汽提。在本發(fā)明的一個(gè)變體中,分離塔(汽提塔)C-1可以再沸。該分離塔C-1的壓力通常足夠高,以能夠?qū)@自該分離的酸性氣體再注入到現(xiàn)場(chǎng)(site)的燃料氣系統(tǒng)中,所述酸性氣體所含的H2S已經(jīng)被清除??倝毫νǔT诩s0.4MPa至約2.0MPa的范圍內(nèi),通常在0.6至2.0Ma的范圍內(nèi),優(yōu)選在0.7至1.8MPa的范圍內(nèi)。優(yōu)選向分餾塔C-2供應(yīng)任何汽提氣體,優(yōu)選蒸汽。分餾塔C-2的總壓力通常在0.1MPa至0.4MPa的范圍內(nèi),優(yōu)選在0.1MPa至0.3MPa的范圍內(nèi)。來(lái)自分餾塔C-2的頂部餾分含有殘留酸性氣體,其在被送往通常使用胺滌氣塔的酸性氣體處理段之前在壓縮機(jī)K-2中被壓縮。在滌氣之后,然后將該酸性氣體餾分送往燃料氣系統(tǒng)。根據(jù)該變體,將含有殘留酸性氣體的獲自分餾塔C-2的頂部餾分的至少一部分送至在非常低的壓力下操作的滌氣塔C-5,以除去至少一部分H2S,然后頂部餾分的所述部分作為用于反應(yīng)段的爐F-1中的燃料(通過(guò)補(bǔ)充的方式)來(lái)使用。根據(jù)本發(fā)明的進(jìn)一步變體,其特別適用于目的在于構(gòu)成用于催化裂化單元的進(jìn)料的加氫脫硫單元,將含有殘留酸性氣體的獲自分餾塔C-2的頂部餾分的至少一部分送到流化催化裂化單元(FCC)的酸性氣體壓縮機(jī)。因此,這可以用于省去用于加氫脫硫單元的酸性氣體壓縮機(jī)。高壓熱分離器鼓B-1通常在稍低的壓力,例如比反應(yīng)器R-1的壓力低0.1MPa至1.0MPa的壓力下操作。熱分離器鼓B-1的溫度通常在200℃至450℃的范圍內(nèi),優(yōu)選在250℃至380℃的范圍內(nèi),并且高度優(yōu)選在260℃至360℃的范圍內(nèi)。根據(jù)優(yōu)選的變體,高壓熱分離器鼓B-1的溫度以使得主分餾塔C-2不需要爐的方式選擇。因此進(jìn)料是獲自熱分離器鼓B1的氣體物流的高壓冷分離器鼓B-2在比B-1的壓力稍低的壓力,例如比B-1的壓力低0.1MPa至1.0Mpa的壓力下操作。將獲自B-2的稱為再循環(huán)氫的氣體流出物任選在塔C-3中滌氣,然后在壓縮機(jī)K-1中壓縮??紤]到現(xiàn)場(chǎng)可用的冷卻裝置,高壓冷分離器鼓B-2的溫度通??赡苁亲畹偷模允乖傺h(huán)氫的純度最大化。根據(jù)本發(fā)明的變體,將獲自冷分離器鼓B-2的液體在閥或渦輪機(jī)中減壓,并且送入中壓冷分離器鼓B-4中。后者中的總壓力優(yōu)選是以有效的方式回收在所述鼓中分離的氣體餾分中包含的氫所需的壓力。該氫回收優(yōu)選在變壓吸附單元中進(jìn)行。所述鼓B-4中的壓力通常在1.0MPa至3.5MPa的范圍內(nèi),優(yōu)選在1.5MPa至3.5MPa的范圍內(nèi)。在本發(fā)明的另一變體中,將獲自高壓熱分離器鼓B-1的液體物流送至中壓熱分離器鼓B-3。所述分離器鼓B-3的壓力以能夠向中壓冷分離器鼓B-4供應(yīng)在高壓熱分離器鼓B-3中分離的氣體物流的方式選擇。根據(jù)優(yōu)選的變體,可以將獲自B-3的一部分液體再注入到B-2中,以促進(jìn)其中輕質(zhì)烴的溶解并使再循環(huán)氣體的氫的純度最大化。優(yōu)選地,將獲自中壓熱分離器鼓B-3的液體物流減壓并送往低壓熱分離器鼓B-5。選擇所述鼓B-5的壓力足夠高,從而可以將獲自B-5的氣體流出物送往分離塔C-1。分離器鼓B-5的總壓力通常在約0.2MPa至約2.5MPa的范圍內(nèi),通常在0.3至2.0MPa的范圍內(nèi),優(yōu)選在0.4至1.8MPa的范圍內(nèi)。本發(fā)明與現(xiàn)有技術(shù)的不同之處在于:·與其中在主分餾塔C-2上游不存在分離塔的圖2的現(xiàn)有技術(shù)相比,在根據(jù)本發(fā)明的方法中,來(lái)自反應(yīng)器R-1的流出物的輕質(zhì)餾分經(jīng)歷旨在除去這些輕質(zhì)化合物,特別是H2S的分離。該分離由汽提塔C-1進(jìn)行。在分餾塔C-2上游的這種分離可用于顯著減少在所述主分餾塔C-2的頂部的酸性氣體,以及降低功率和尺寸,并且在一些情況下甚至可以省去用于廢氣的壓縮機(jī)?!ぴ谖挥谥鞣逐s(塔C-2)上游的塔C-1中汽提的來(lái)自反應(yīng)區(qū)R-1的流出物的最輕的餾分通過(guò)汽提塔C-1的頂部物流來(lái)除去,并且僅將來(lái)自反應(yīng)器的流出物的重質(zhì)餾分(在鼓B-5的出口處的物流38,和汽提塔C-1的底部物流)在連續(xù)任選的減壓之后送往主分餾塔C-2。熱分離器鼓(一個(gè)或多個(gè))的溫度以使得向分餾塔C-2供應(yīng)獲得分餾產(chǎn)物50、52和55所需的熱量的方式選擇。根據(jù)本發(fā)明,高壓熱鼓B-1的溫度可以使得主分餾塔的進(jìn)料不需要爐的方式選擇?!ご送猓瑏?lái)自反應(yīng)段R-1的重質(zhì)流出物的分餾是在最低壓力下在分離塔C-2中以集成的方式進(jìn)行。由于在低壓下更容易通過(guò)蒸餾進(jìn)行分離,所以該方法的能量效率將得到改進(jìn),特別是由于在塔頂?shù)目諝饫淠髦械哪芰繐p失的減少。具體實(shí)施方式下面的描述借助于圖1進(jìn)行,其描述了根據(jù)本發(fā)明的方法的可能的實(shí)施方案之一。反應(yīng)區(qū)R-1是加氫裂化區(qū);然而,這不構(gòu)成對(duì)本發(fā)明的限制,本發(fā)明涉及具有在主分餾塔C-2上游的分離器鼓(B-5)和汽提塔(C-1)組合件的設(shè)施。進(jìn)料是具有在350℃至530℃范圍內(nèi)的沸點(diǎn)的餾分,其是70重量%的重質(zhì)減壓餾出物和30重量%的來(lái)自焦化的重質(zhì)瓦斯油的混合物,具有以下特征:比重0.965硫含量重量%2.8氮含量重量ppm5000該進(jìn)料經(jīng)由管線1通過(guò)泵P-1供應(yīng)。補(bǔ)充氫(優(yōu)選相對(duì)于進(jìn)料過(guò)量)經(jīng)由管線2和壓縮機(jī)K-2然后管線3供應(yīng),并在進(jìn)入進(jìn)料-流出物交換器(E1)之前經(jīng)由管線4與進(jìn)料1混合。使用交換器E-1以使用來(lái)自加氫裂化反應(yīng)器R-1的流出物預(yù)熱進(jìn)料。在該交換之后,將進(jìn)料經(jīng)由管線5供應(yīng)到爐F-1,使得其可以達(dá)到加氫裂化反應(yīng)所需的溫度,然后經(jīng)由管線6將熱進(jìn)料送至由至少一個(gè)加氫裂化反應(yīng)器R-1構(gòu)成的加氫轉(zhuǎn)化段,所述加氫裂化反應(yīng)器包含至少一種加氫裂化催化劑。反應(yīng)段R-1由2個(gè)串聯(lián)的反應(yīng)器組成,每個(gè)具有3個(gè)催化劑床。第一反應(yīng)器的第一床由AxensHMC868、HF858和HR844催化劑組成。其它床由AxensHR844催化劑組成。所述床在約12.5MPa和在350℃至370℃的溫度下操作。在反應(yīng)段中氫的消耗量為相對(duì)于新鮮進(jìn)料的2%。然后將來(lái)自反應(yīng)段的流出物經(jīng)由管線10送至交換器E-1,然后經(jīng)由管線11送至高壓熱分離器鼓B-1。在該鼓中將氣體頂部餾分分離并經(jīng)由管線12回收。將液體餾分經(jīng)由管線20從鼓B-1的底部回收。所述氣體餾分(12)包括未反應(yīng)的氫、反應(yīng)期間形成的H2S以及獲自加氫裂化反應(yīng)段R-1的進(jìn)料中的烴的轉(zhuǎn)化的輕質(zhì)烴。在交換器E-2和空氣冷凝器A-1中冷卻之后,將該餾分經(jīng)由管線13供應(yīng)到高壓冷分離器鼓B-2以進(jìn)行氣-液分離和傾析水性液相兩者。在閥或液體渦輪機(jī)V-1中減壓之后,將液態(tài)烴相經(jīng)由管線21送至中壓冷分離器鼓B-4。在閥或液體渦輪機(jī)V-2中減壓之后,將獲自鼓B-1的液體流出物經(jīng)由管線20送至中壓熱分離器鼓B-3。在該鼓中將氣體餾分分離出并經(jīng)由管線22回收。氣體餾分包括未反應(yīng)的氫、H2S以及通常獲自反應(yīng)段R-1的進(jìn)料的烴的轉(zhuǎn)化的輕質(zhì)烴。在空氣冷凝器A-2中冷卻之后,將該餾分經(jīng)由管線23供應(yīng)到中壓冷分離器鼓B-4。將液體餾分從底部回收,經(jīng)由管線30和31在閥或液體渦輪機(jī)V-3中減壓并送至低壓分離器鼓B-5。將獲自高壓冷分離器鼓B-2的氣體餾分經(jīng)由管線14送至胺吸收器或滌氣塔C-3,以除去至少一部分H2S。然后將含有氫的氣體餾分經(jīng)由管線15和16在使用壓縮機(jī)K-1壓縮并與進(jìn)料1混合之后再循環(huán)到加氫裂化反應(yīng)器。獲自鼓B-4的液體烴流出物經(jīng)由管線32和33,閥或液體渦輪機(jī)V-5和交換器E-3供應(yīng)到汽提塔C-1。根據(jù)優(yōu)選的變體,優(yōu)選將蒸汽經(jīng)由管線60和61添加到來(lái)自鼓B-1和/或B-3的頂部流出物中以便于分餾。將該水在鼓B-2和B-4中分離,并在分離后經(jīng)由管線57排出。將在鼓B-2中分離的水經(jīng)由管線56和閥V-4送至鼓B-4。管線58可用于排出氣體物流。汽提塔C-1在塔頂處為0.9MPa、回流鼓B-6為45℃、和底部溫度為180℃下操作。在鼓B-5中分離氣體餾分。將該氣體餾分經(jīng)由管線34供應(yīng)到汽提塔C-1。向汽提塔C-1供應(yīng)經(jīng)由管線35以每1標(biāo)準(zhǔn)m3塔底產(chǎn)物7kg/h蒸汽的比率的汽提蒸汽。從汽提塔的頂部,經(jīng)由管線36回收氣體餾分(通常稱為酸性氣體),并且經(jīng)由管線37借助于鼓B-6和交換器E-6回收具有通常大于100℃的終沸點(diǎn)的石腦油。將從汽提塔底部回收的液體經(jīng)由管線39送至主分餾塔C-2,而不需要在爐或交換器中再加熱。將獲自鼓B-5的液體餾分經(jīng)由管線38直接供應(yīng)到主分餾塔C-2,而不需要在汽提塔或再沸分離塔中進(jìn)行分離酸性氣體的操作。主分餾塔C-2在塔頂處為0.29MPa的低壓、回流鼓B-7為45℃(在通過(guò)空氣冷凝器A-3和泵P-2之后)、底部溫度為330℃下操作。分離所需的熱量?jī)?yōu)選由在340℃和1.1MPa下操作的熱分離器鼓B-5的溫度供應(yīng)。還向該塔C-2供應(yīng)經(jīng)由管線40以每1標(biāo)準(zhǔn)m3塔底產(chǎn)物7kg/h蒸汽的比率的汽提蒸汽。經(jīng)由管線41回收的頂部餾分含有殘留的酸性氣體,其在輸出到酸性氣體處理(通常為胺滌氣器或滌氣塔)之前,并在經(jīng)由管線42送至燃料氣系統(tǒng)之前在壓縮機(jī)K-2中被壓縮。根據(jù)本發(fā)明的變體,將殘留的酸性氣體經(jīng)由管線43送至在非常低的壓力下操作的胺吸收器或滌氣塔C-5,其可在較小程度地經(jīng)由管線44用作反應(yīng)段的爐F-1中的燃料之前除去至少一部分H2S。根據(jù)本發(fā)明的另一變體,其特別適合于目的在于構(gòu)成用于催化裂化單元的進(jìn)料的加氫脫硫單元,將這些殘留的酸性氣體經(jīng)由管線45送往流化催化裂化單元的酸性氣體壓縮機(jī)。經(jīng)由泵P-3獲自管線50的產(chǎn)物由石腦油餾分構(gòu)成,其通常具有小于200℃的終沸點(diǎn)。將來(lái)自主分餾塔C-2的通過(guò)任選配備有再沸器E-7的中間塔C-4(任選的)經(jīng)由管線51獲得的中間餾分在通過(guò)泵P-5之后例如借助于交換器E-4來(lái)冷卻,然后經(jīng)由管線52回收。例如為具有95體積%蒸餾溫度(NFENISO標(biāo)準(zhǔn)3405)小于360℃的瓦斯油餾分。還將來(lái)自主分餾塔的經(jīng)由管線53和54獲得的重質(zhì)餾分在通過(guò)泵P-4之后借助于交換器E-5來(lái)冷卻。由此經(jīng)由管線55獲得的餾分是具有接近初始進(jìn)料的餾出溫度的減壓瓦斯油。根據(jù)另一個(gè)實(shí)施方案,可以經(jīng)由管線50回收從石腦油到輕質(zhì)瓦斯油的餾分和經(jīng)由管線55回收補(bǔ)充重質(zhì)瓦斯油餾分。在這種情況下,分餾塔C-2不包括在C-4的中間分餾并且不存在管線51和52。根據(jù)分餾塔C-2的另一個(gè)實(shí)施方案,可以作為側(cè)物流取出煤油餾分和柴油餾分(圖1中未示出)。實(shí)施例表1比較了根據(jù)現(xiàn)有技術(shù)即沒(méi)有汽提塔C-1的溫和加氫裂化方法(圖2)和根據(jù)本發(fā)明即使用鼓B-5和汽提塔C-1的溫和加氫裂化方法(圖1)。表1在根據(jù)本發(fā)明的方法中,來(lái)自低壓主分餾塔的必須在壓縮機(jī)K-2中被壓縮的頂部酸性氣體的量(物流41)與根據(jù)現(xiàn)有技術(shù)的方法相比除以6(與608kg/h相比的107kg/h)。在根據(jù)現(xiàn)有技術(shù)的溫和加氫裂化的情況下(根據(jù)圖2),將來(lái)自中壓熱分離器鼓B-3的底部餾分和來(lái)自中壓冷鼓B-4的底部餾分的全部供應(yīng)到分餾塔C-2。在根據(jù)本發(fā)明的方法(圖1)中,低壓熱分離器鼓B-5的溫度為340℃,這意味著可以省去用于加熱從低壓鼓B-5的底部取出并供應(yīng)到塔C-2的進(jìn)料38的爐。當(dāng)前第1頁(yè)1 2 3