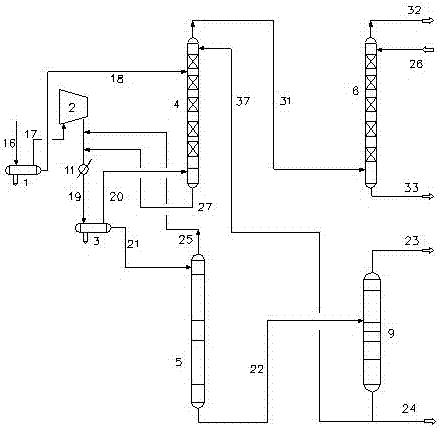
本發(fā)明涉及石油煉制工業(yè),特別是催化裂化、延遲焦化等裝置吸收穩(wěn)定工藝與系統(tǒng)。
背景技術(shù):
:吸收穩(wěn)定系統(tǒng)是石油煉制工業(yè)中催化裂化裝置和延遲焦化裝置的后處理過(guò)程,其目的是利用吸收和精餾原理將分餾塔塔頂油氣分離罐中的富氣和粗汽油分割成干氣(c2以下)、液化氣(c3、c4)和蒸汽壓合格的穩(wěn)定汽油。吸收穩(wěn)定系統(tǒng)的裝置和工藝流程優(yōu)化對(duì)催化裂化和延遲焦化裝置的節(jié)能增效起著十分重要的作用。目前大多數(shù)煉廠吸收-穩(wěn)定工藝流程是:分餾塔塔頂富氣經(jīng)富氣壓縮機(jī)升壓后與吸收塔底油、解吸塔頂油氣混合,經(jīng)冷卻器冷卻后進(jìn)入氣液平衡罐進(jìn)行氣液分離。分離出來(lái)的氣體進(jìn)入吸收塔下部;分離出來(lái)的凝縮油進(jìn)入解吸塔頂部。分餾塔塔頂分離罐液相粗汽油作為吸收塔的吸收劑。吸收塔頂部出來(lái)的貧氣進(jìn)入再吸收塔,用分餾塔柴油作為吸收劑進(jìn)行再次吸收,以回收吸收塔頂攜帶出來(lái)的汽油組分。再吸收塔塔底富吸收油返回分餾塔。塔頂干氣送出裝置。解吸塔塔底脫乙烷汽油送至穩(wěn)定塔。穩(wěn)定塔塔頂氣經(jīng)塔頂冷卻器冷凝冷卻后,分離出來(lái)的液化石油氣。穩(wěn)定塔塔底油分兩路,一路作為產(chǎn)品送出裝置;另一路送到吸收塔作為補(bǔ)充吸收劑。在系統(tǒng)中為提高吸收塔吸收效率,吸收塔一般設(shè)置中段冷卻器。近年來(lái)隨著低碳化工的快速發(fā)展和民用液化氣需求量逐漸擴(kuò)大,提高干氣和液化氣的分離精度,提高液化氣產(chǎn)量,已經(jīng)成為煉廠提升經(jīng)濟(jì)效益的一個(gè)重要手段,另外隨著節(jié)能減排壓力的日益增加,如何降低生產(chǎn)能耗也成為關(guān)注的焦點(diǎn)。目前煉廠吸收穩(wěn)定系統(tǒng)普遍存在的問(wèn)題主要表現(xiàn)為:1、干氣不干,干氣中夾帶大量的液化氣,液化氣含量在3%(v)以上,導(dǎo)致大量高附加值的液化氣被當(dāng)作燃料直接燃燒從而造成資源的巨大浪費(fèi);2、吸收塔吸收效果不理想,為了降低干氣中的液化氣濃度,必須靠加大補(bǔ)充吸收劑(穩(wěn)定汽油)循環(huán)量來(lái)提高吸收效果,穩(wěn)定汽油內(nèi)循環(huán)的存在導(dǎo)致了系統(tǒng)能耗的大幅增加和處理能力的降低。技術(shù)實(shí)現(xiàn)要素:目前我國(guó)柴油餾程范圍在180℃~360℃,汽油終餾點(diǎn)為205℃,因此存在柴油中夾帶一定量汽油的問(wèn)題,由于柴油價(jià)值較低,而汽油價(jià)值較高,因此低價(jià)值的柴油中夾帶部分高質(zhì)量的汽油無(wú)疑會(huì)造成一定的經(jīng)濟(jì)損失?,F(xiàn)有的催化裝置中,柴油通過(guò)分餾塔的側(cè)線采出,粗汽油從分餾塔頂部采出,這種分離流程不可能實(shí)現(xiàn)汽油和柴油的清晰切割,如何實(shí)現(xiàn)柴油和汽油的清晰切割,更大量的得到汽油餾分也是目前需要解決的一個(gè)問(wèn)題?,F(xiàn)有的吸收穩(wěn)定工藝及系統(tǒng)都設(shè)置有補(bǔ)充穩(wěn)定汽油內(nèi)循環(huán),為了保證干氣的干度,還需要利用柴油補(bǔ)充吸收,柴油富吸收油再返回分餾塔中部,利用分餾塔的熱量實(shí)現(xiàn)柴油與輕烴的分離。由于受分餾塔熱平衡的限制,柴油吸收劑的量又不能太大,所以無(wú)法通過(guò)加大柴油吸收劑量以取消穩(wěn)定汽油內(nèi)循環(huán)。申請(qǐng)人研究后還發(fā)現(xiàn),造成吸收穩(wěn)定系統(tǒng)能耗較高的原因主要在于系統(tǒng)內(nèi)循環(huán)物流量較大,增加了吸收和精餾負(fù)荷造成系統(tǒng)能耗高。一方面是大量解吸氣在解吸塔和吸收塔間循環(huán)。目前的流程中解吸氣與富氣、吸收塔塔底富吸收油混合進(jìn)入平衡分離罐,大量的解吸氣主要是c1、c2組分,降低了平衡罐富氣中c3、c4組分及富吸收油中輕烴的分壓,使平衡罐氣相組成中c3、c4的含量增加,從而加大了平衡罐氣相進(jìn)入吸收塔的量,加大了吸收塔負(fù)荷。不僅影響了吸收塔吸收效果,而且增加了吸收塔能耗;另一方面吸收塔氣相負(fù)荷大,為了降低富氣中液化氣含量就需要更大量的穩(wěn)定汽油補(bǔ)充吸收劑。造成大量的穩(wěn)定汽油在吸收塔、解吸塔和穩(wěn)定塔間循環(huán),導(dǎo)致系統(tǒng)能耗顯著增大。本發(fā)明針對(duì)現(xiàn)有工藝存在的不足,提供一種吸收穩(wěn)定工藝及系統(tǒng),在使干氣中液化氣濃度大幅降低的同時(shí),可以提高催化汽油及液化氣的收率,并大幅降低系統(tǒng)能耗。本發(fā)明提供一種吸收穩(wěn)定系統(tǒng),所述吸收穩(wěn)定系統(tǒng)包括氣液平衡罐、富氣壓縮機(jī)、富氣平衡罐、吸收塔、解吸塔、穩(wěn)定塔、再吸收塔、再生罐、解吸氣平衡罐和真空泵;所述氣液平衡罐入口與來(lái)自分餾塔塔頂?shù)倪M(jìn)料管線連接,氣液平衡罐氣相出口與富氣壓縮機(jī)入口經(jīng)管線連接,氣液平衡罐液相出口與吸收塔吸收劑入口經(jīng)管線連接,富氣壓縮機(jī)出口與富氣平衡罐入口經(jīng)管線連接,富氣平衡罐氣相出口與吸收塔氣相入口經(jīng)管線連接,富氣平衡罐液相出口與解吸塔進(jìn)料口經(jīng)管線連接,解吸塔塔底出料口與穩(wěn)定塔入口經(jīng)管線連接,解吸塔塔頂氣相出口經(jīng)解吸氣平衡罐冷卻器后與解吸氣平衡罐入口經(jīng)管線連接,解吸氣平衡罐液相出口經(jīng)管線與解吸塔循環(huán)物料入口連接,解吸氣平衡罐氣相出口與吸收塔氣相入口連接,吸收塔塔底出料口分兩路,其中一路經(jīng)解吸氣平衡罐冷卻器后與解吸氣平衡罐入口連接,另一路經(jīng)管線與富氣平衡罐入口連接,吸收塔塔頂氣相出口經(jīng)管線與再吸收塔入口連接,再吸收塔塔底液相出料口與再生罐入口經(jīng)管線連接,再生罐氣相出口經(jīng)真空泵與富氣壓縮機(jī)入口連接,再生罐液相出口分兩路,其中一路經(jīng)管線與再吸收塔吸收劑入口連接,另一路出裝置。本發(fā)明所述吸收穩(wěn)定系統(tǒng)中,所述富氣壓縮機(jī)出口與富氣平衡罐入口的連接管線上設(shè)置富氣冷卻器,所述富氣平衡罐液相出口與解吸塔進(jìn)料口的連接管線上設(shè)置有解吸塔換熱器,再吸收塔塔底液相出料口與再生罐入口連接管線上設(shè)置再生罐換熱器,所述再生罐液相出口與再吸收塔吸收劑入口連接管線上設(shè)置有進(jìn)料換熱器。本發(fā)明所述吸收穩(wěn)定系統(tǒng)中,解吸塔循環(huán)物料入口位于解吸塔進(jìn)料口上方,解吸塔循環(huán)物料入口與解吸塔進(jìn)料口之間設(shè)置3~5塊理論板。本發(fā)明提供一種吸收穩(wěn)定工藝,所述吸收穩(wěn)定工藝包括如下內(nèi)容:(1)油氣原料進(jìn)入氣液分離罐,分離后得到富氣和粗汽油;(2)步驟(1)得到的富氣經(jīng)壓縮冷卻后進(jìn)入富氣平衡罐,分離后得到氣相的第1料流和液相的第2料流;(3)步驟(2)得到的液相的第2料流經(jīng)換熱后經(jīng)解吸塔進(jìn)料口進(jìn)入解吸塔,處理后得到解吸氣和脫乙烷汽油;(4)步驟(3)得到的脫乙烷汽油進(jìn)入穩(wěn)定塔,處理后得到液化石油氣和穩(wěn)定汽油;(5)步驟(2)得到的第1料流與步驟(1)得到的粗汽油進(jìn)入吸收塔,處理后得到貧氣和液相的第3料流,液相的第3料流分為第31子料流和第32子料流,第31子料流進(jìn)入富氣平衡罐;(6)步驟(3)得到的解吸氣與步驟(5)得到的第32子料流混合并冷卻后進(jìn)入解吸氣平衡罐,分離后得到氣相的第4料流與液相的第5料流,氣相的第4料流進(jìn)入吸收塔,液相的第5料流經(jīng)解吸塔循環(huán)物料入口進(jìn)入解吸塔;(7)步驟(5)得到的貧氣進(jìn)入再吸收塔與吸收劑接觸反應(yīng),反應(yīng)后得到干氣與富吸收油;(8)步驟(7)得到的富吸收油經(jīng)換熱后進(jìn)入再生罐進(jìn)行再生,再生后得到氣相的第6料流和液相的第7料流,氣相的第6料流經(jīng)真空泵進(jìn)入富氣壓縮機(jī)與富氣混合后一起處理,液相的第7料流可以全部循環(huán)回再生罐,或者部分循環(huán)進(jìn)入再吸收塔作為吸收劑重復(fù)利用,部分排出裝置。本發(fā)明工藝中,步驟(1)得到的富氣經(jīng)壓縮冷卻至30℃~40℃后進(jìn)入富氣平衡罐。本發(fā)明工藝中,步驟(5)中所述第31子料流占第3料流的比例為10wt%~90wt%,優(yōu)選為30wt%~70wt%。本發(fā)明工藝中,步驟(2)得到的第2料流經(jīng)換熱至40℃~90℃,優(yōu)選為55℃~80℃后進(jìn)入解吸塔。本發(fā)明工藝中,所述解吸氣平衡罐的壓力比富氣壓縮后壓力高1%~20%,優(yōu)選高5%~15%。本發(fā)明工藝中,解吸塔循環(huán)物料入口位于解吸塔進(jìn)料口上方,解吸塔循環(huán)物料入口與解吸塔進(jìn)料口之間設(shè)置3~5塊理論板。本發(fā)明工藝中,步驟(4)中所述的穩(wěn)定汽油經(jīng)冷卻后溫度為30℃~40℃。本發(fā)明工藝中,再吸收塔用的吸收劑可以為復(fù)合吸收劑或柴油,所述柴油可以是從分餾塔側(cè)線采出的柴油,所述復(fù)合吸收劑為離子液體和有機(jī)酸鹽的混合物,其中有機(jī)酸鹽濃度為1wt%~10wt%,優(yōu)選為1wt%~5wt%。所述復(fù)合吸收劑中的離子液體的陽(yáng)離子為咪唑陽(yáng)離子或烷基咪唑陽(yáng)離子,如1-丁基-3-甲基咪唑陽(yáng)離子或1-戊基-3-甲基咪唑陽(yáng)離子,陰離子為四氟硼酸根陰離子、六氟磷酸根陰離子、氯離子或溴離子等;具體可以為1-丁基-3-甲基咪唑四氟硼酸鹽和/或1-丁基-3-甲基咪唑六氟硼酸鹽。所述復(fù)合吸收劑中的有機(jī)酸鹽可以為醋酸鈉、丙酸鈉、醋酸鉀等中的一種或幾種。本發(fā)明工藝中,步驟(7)得到的富吸收油經(jīng)換熱至60~100℃,優(yōu)選為70~80℃后進(jìn)入再生罐進(jìn)行再生,再生過(guò)程為真空操作,再生罐操作壓力為5~50kpa,優(yōu)選為15~20kpa。本發(fā)明工藝中,當(dāng)再吸收塔采用柴油作為吸收劑時(shí),再生后的吸收劑為去除了輕烴及柴油輕端的柴油,其初餾點(diǎn)大于200℃,優(yōu)選大于205℃。與現(xiàn)有技術(shù)相比,本發(fā)明吸收穩(wěn)定工藝及系統(tǒng)具有如下優(yōu)勢(shì):本發(fā)明所述吸收穩(wěn)定系統(tǒng)通過(guò)設(shè)置解吸氣平衡罐,避免了解吸氣對(duì)富含液化石油氣的富氣在冷凝后平衡的干擾,有利于強(qiáng)化富氣平衡效果,減少平衡后進(jìn)入吸收塔的氣相量,降低吸收塔負(fù)荷,降低了對(duì)吸收劑的需求量,為取消穩(wěn)定汽油內(nèi)循環(huán)創(chuàng)造了條件,大幅降低了能耗。本發(fā)明通過(guò)解吸氣平衡罐對(duì)解吸氣單獨(dú)地吸收冷凝平衡,有利于將解吸塔中過(guò)解吸的液化石油氣充分吸收冷凝下來(lái),可以大幅降低進(jìn)入吸收塔氣相量,降低吸收塔負(fù)荷。本發(fā)明通過(guò)控制解吸氣平衡罐壓力,在保證塔底脫乙烷汽油中≤c2輕烴含量質(zhì)量要求的同時(shí),盡可能地減少解吸氣中≥c3組分的含量,降低在解吸塔和吸收塔間的循環(huán)量。不僅有利于降低吸收塔負(fù)荷,提高吸收效率;而且大幅降低過(guò)程能耗。本發(fā)明吸收穩(wěn)定工藝中,由于解吸氣平衡罐得到的第2料流和富氣平衡罐液得到的第5料流相中所含輕組分的不同,分別通過(guò)不同進(jìn)料口進(jìn)入解吸塔,并設(shè)置富氣平衡罐液相加熱器,有利于強(qiáng)化解吸效果,降低解吸塔塔底供熱負(fù)荷。本發(fā)明吸收穩(wěn)定工藝及系統(tǒng)建立了專(zhuān)有再吸收循環(huán)系統(tǒng),取消了原吸收穩(wěn)定系統(tǒng)的補(bǔ)充穩(wěn)定汽油吸收劑這一內(nèi)循環(huán),使得系統(tǒng)的能耗大幅降低,而且再吸收循環(huán)系統(tǒng)吸收劑循環(huán)量可以靈活控制,可使得氣產(chǎn)品中液化氣夾帶率降低到1%(v)以下,大大提高了裝置的經(jīng)濟(jì)效益,解決了傳統(tǒng)工藝受因分餾塔熱平衡限制而無(wú)法通過(guò)增大柴油吸收劑量大幅降低干氣中的c3+組分濃度的問(wèn)題。另外對(duì)于老裝置而言,還可以大幅提高裝置處理能力。當(dāng)以柴油作為二級(jí)循環(huán)吸收劑,柴油吸收劑能顯著提高從吸收塔出來(lái)的貧氣中輕烴組分的吸收效果,并且柴油吸收劑循環(huán)量可靈活控制,能夠使得干氣中的c3+組分濃度低于1%(v)以下,從而實(shí)現(xiàn)了增產(chǎn)液化氣的目的,解決了傳統(tǒng)工藝受因分餾塔熱平衡限制而無(wú)法通過(guò)增大柴油吸收劑量大幅降低干氣中的c3+組分濃度的問(wèn)題。尤其當(dāng)使用將分餾塔產(chǎn)的柴油連續(xù)補(bǔ)入再吸收循環(huán)系統(tǒng),保證了吸收劑的效果,通過(guò)真空閃蒸方式既實(shí)現(xiàn)了富柴油的再生又去除了柴油吸收劑中的汽油餾分,實(shí)現(xiàn)了柴油和汽油的清晰切割,達(dá)到了增產(chǎn)催化汽油的目的,顯著增加了裝置經(jīng)濟(jì)效益。當(dāng)采用咪唑類(lèi)離子液體與有機(jī)酸鹽的混合物作為吸收劑,其中咪唑類(lèi)離子液體對(duì)c3+組分具有良好的吸收效果,并且對(duì)c1和c2吸收效果較差,因此具有良好的選擇性;通過(guò)加入有機(jī)酸鹽與離子液體復(fù)配使用,大大提高了有機(jī)基團(tuán)的濃度,大幅提高了溶劑對(duì)c3、c4組分的吸收效果;有機(jī)酸鹽的加入大大提高了吸收劑粘度,增強(qiáng)了吸收效果,同時(shí)顯著加速了c3+組分在溶劑中的解吸速率與解吸深度,大大簡(jiǎn)化了吸收劑再生系統(tǒng),提高了再生吸收劑的質(zhì)量;離子液體與有機(jī)酸鹽的復(fù)配大大降低了降低了吸收劑在系統(tǒng)中的循環(huán)量;有機(jī)酸鹽的加入進(jìn)一步降低了離子液體的揮發(fā)性,減少價(jià)格昂貴的離子液體的損失,降低了運(yùn)行費(fèi)用。另外咪唑類(lèi)離子液體與有機(jī)酸鹽組成的復(fù)合溶劑具有熔點(diǎn)低、飽和蒸汽壓低的優(yōu)點(diǎn),這使得吸收劑再生過(guò)程變得非常容易,因此再生能耗大幅降低。本發(fā)明吸收穩(wěn)定系統(tǒng)雖然增加了冷凝器、解吸氣平衡罐及相應(yīng)真空再生措施,但工藝流程清晰、工藝先進(jìn)合理、裝置能耗低、產(chǎn)品質(zhì)量可靠等優(yōu)點(diǎn),尤其是實(shí)現(xiàn)了取消穩(wěn)定期油內(nèi)循環(huán)的目的,這大大降低了現(xiàn)有設(shè)備的負(fù)荷,在總的設(shè)計(jì)預(yù)算中并沒(méi)有增加投資量。對(duì)于新設(shè)計(jì)或新建裝置具有裝置能耗先進(jìn),產(chǎn)品指標(biāo)優(yōu)質(zhì)等特點(diǎn);對(duì)于舊裝置改造具有改造費(fèi)用低,降低裝置能耗,增加裝置效益等特點(diǎn)。附圖說(shuō)明圖1為本發(fā)明吸收穩(wěn)定工藝及系統(tǒng)示意圖。圖2為對(duì)比例2中所述吸收穩(wěn)定工藝示意圖。具體實(shí)施方式本發(fā)明提供一種吸收穩(wěn)定系統(tǒng),所述吸收穩(wěn)定系統(tǒng)包括氣液平衡罐1、富氣壓縮機(jī)2、富氣平衡罐3、吸收塔4、解吸塔5、穩(wěn)定塔9、再吸收塔6、再生罐7、解吸氣平衡罐8和真空泵10;所述氣液平衡罐1入口與來(lái)自分餾塔塔頂?shù)倪M(jìn)料管線16連接,氣液平衡罐1氣相出口與富氣壓縮機(jī)2入口連接,氣液平衡罐1液相出口與吸收塔4吸收劑入口經(jīng)管線連接,富氣壓縮機(jī)2出口經(jīng)富氣冷卻器后與富氣平衡罐3入口經(jīng)管線連接,富氣平衡罐3氣相出口與吸收塔4氣相入口連接,富氣平衡罐3液相出口經(jīng)解吸塔換熱器12后與解吸塔5進(jìn)料口經(jīng)管線連接,解吸塔5塔底出料口經(jīng)管線與穩(wěn)定塔9入口連接,解吸塔5塔頂氣相出口經(jīng)解吸氣平衡罐冷卻器13后與解吸氣平衡罐8入口經(jīng)管線連接,解吸氣平衡罐8液相出口經(jīng)管線與解吸塔5循環(huán)物料入口連接,解吸氣平衡罐8氣相出口與吸收塔4氣相入口連接,吸收塔塔底出料口分兩路,其中一路28經(jīng)解吸氣平衡罐冷卻器13后與解吸氣平衡罐8入口連接,另一路27經(jīng)管線與富氣平衡罐3入口連接,吸收塔4塔頂氣相出口經(jīng)管線與再吸收塔6入口連接,再吸收塔6塔底液相出料口經(jīng)再生罐換熱器后與再生罐7入口經(jīng)管線連接,再生罐7氣相出口經(jīng)真空泵10與富氣壓縮機(jī)2入口連接,再生罐液相出口分兩路,其中一路35作為產(chǎn)品出裝置,另一路36經(jīng)進(jìn)料換熱器15后與再吸收塔6吸收劑入口連接。結(jié)合圖1,對(duì)本發(fā)明吸收穩(wěn)定工藝流程進(jìn)一步說(shuō)明,來(lái)自催化裂化/焦化分餾塔頂?shù)挠蜌庠辖?jīng)進(jìn)料管線16進(jìn)入氣液平衡罐1,分離得到富氣17和粗汽油18,經(jīng)富氣壓縮機(jī)2增壓并經(jīng)富氣冷卻器11冷卻后的富氣19進(jìn)入富氣平衡罐3平衡后得到的氣相第1料流20進(jìn)入吸收塔7,與來(lái)自氣液平衡罐1的粗汽油18逆流接觸進(jìn)行吸收反應(yīng),反應(yīng)后得到貧氣31和液相第3料流,所述第3料流分為第31子料流和第32子料流,其中第31子料流27與富氣壓縮機(jī)增壓后的富氣19混合后進(jìn)入富氣平衡罐3一起處理,富氣平衡罐3得到液相第2料流21經(jīng)解吸塔換熱器12加熱后進(jìn)入解吸塔5,處理后得到解吸氣25和脫乙烷汽油22,所述脫乙烷汽油22進(jìn)入穩(wěn)定塔進(jìn)行精餾,處理后得到液化石油氣23和穩(wěn)定汽油24,塔頂?shù)玫揭夯蜌?3作為產(chǎn)品送出裝置,塔底得到的穩(wěn)定汽油24經(jīng)冷卻后作為產(chǎn)品出裝置。解吸氣25與吸收塔塔底得到的液相第32子料流混合并經(jīng)解吸氣平衡罐冷卻器13冷卻后進(jìn)入解吸氣平衡罐8,平衡后得到的氣相第4料流29進(jìn)入吸收塔7與來(lái)自富氣平衡罐的氣相第1料流20一起進(jìn)行處理,平衡后得到的液相第5料流30通過(guò)解吸塔循環(huán)物料入口進(jìn)入解吸塔8的頂部。吸收塔4塔頂?shù)玫降呢殮?1進(jìn)入再吸收塔6與吸收劑26逆流接觸進(jìn)行反應(yīng),反應(yīng)后塔頂?shù)玫礁蓺?2,塔底得到的富吸收油33經(jīng)解吸換熱器14換熱升溫后進(jìn)入再生罐7進(jìn)行再生,再生后得到氣相的第6料流34和液相的第7料流,其中氣相第6料流34經(jīng)真空泵10返回富氣壓縮機(jī)2入口,液相的第7料流可以分兩路,其中一路35作為產(chǎn)品出裝置,另一路36經(jīng)進(jìn)料換熱器15冷卻后返回再吸收塔6重復(fù)使用。下面的實(shí)施例將對(duì)本發(fā)明提供的方法予以進(jìn)一步說(shuō)明,但本發(fā)明并不因此而受任何限制。實(shí)施例1以國(guó)內(nèi)某100萬(wàn)噸/年,fcc型催化裂化裝置的吸收穩(wěn)定系統(tǒng)為例,采用aspenplus流程模擬軟件對(duì)本發(fā)明工藝進(jìn)行模擬,采用催化柴油作為吸收劑,關(guān)鍵工藝參數(shù)如下:富氣壓縮機(jī)出口壓力1.4mpa,解吸氣平衡罐操作溫度40℃,進(jìn)入解吸氣平衡罐的吸收塔底液占總的吸收塔底液相出料的40wt%,富氣平衡罐操作溫度40℃,富氣平衡罐液相換熱至80℃進(jìn)解吸塔,吸收塔設(shè)置一個(gè)中間冷卻器返塔溫度35℃,解吸塔塔底脫乙烷汽油中乙烷含量0.1wt%,新鮮催化柴油補(bǔ)入量30t/h(初餾點(diǎn)180℃,終餾點(diǎn)360℃),柴油內(nèi)循環(huán)量20t/h,再生柴油初餾點(diǎn)205℃,再生罐真空度15kpa,干氣產(chǎn)量5t/h,液化氣產(chǎn)量29t/h,穩(wěn)定汽油產(chǎn)量57t/h,設(shè)備能耗見(jiàn)表1。實(shí)施例2與實(shí)施例1相同,不同之處在于采用1-丁基-3-甲基咪唑六氟硼酸鹽與乙酸鈉的混合物(其中乙酸鈉為5wt%)作為吸收劑,工藝參數(shù)如下:富氣壓縮機(jī)出口壓力1.4mpa,解吸氣平衡罐操作溫度40℃,進(jìn)入解吸氣平衡罐的吸收塔底液占總的吸收塔底液相出料的40wt%,富氣平衡罐操作溫度40℃,富氣平衡罐液相換熱至80℃進(jìn)解吸塔,吸收塔設(shè)置一個(gè)中間冷卻器返塔溫度35℃,解吸塔塔底脫乙烷汽油中乙烷含量0.1wt%,吸收劑內(nèi)循環(huán)量40t/h,再生罐真空度15kpa,干氣產(chǎn)量5t/h,液化氣產(chǎn)量29t/h,穩(wěn)定汽油產(chǎn)量57t/h,設(shè)備能耗見(jiàn)表1。比較例1與實(shí)施例1相比,不同之處在于取消解吸氣平衡罐,解吸塔頂?shù)慕馕鼩馊窟M(jìn)入富氣平衡罐,其余流程與實(shí)施例1完全相同,設(shè)備能耗見(jiàn)表1。比較例2:采用如圖2所示的傳統(tǒng)吸收穩(wěn)定工藝流程,來(lái)自催化裂化/焦化分餾塔頂?shù)挠蜌庠辖?jīng)進(jìn)料管線16進(jìn)入氣液平衡罐1,分離得到富氣17和粗汽油18。富氣17經(jīng)壓縮機(jī)2壓縮后與來(lái)自吸收塔4塔底的吸收油27以及解吸塔頂出來(lái)的解吸氣25混合并經(jīng)冷卻器11冷卻后進(jìn)入富氣平衡罐3,分離得到的液相21進(jìn)入解吸塔5的頂部,解吸塔5塔底脫乙烷汽油22先與穩(wěn)定汽油換熱后再進(jìn)入穩(wěn)定塔9的中部,經(jīng)穩(wěn)定塔分離出穩(wěn)定汽油和液化氣23;穩(wěn)定塔塔底得到的穩(wěn)定汽油部分作為產(chǎn)品24出裝置,部分作為補(bǔ)充吸收劑37(穩(wěn)定汽油)進(jìn)入吸收塔4的頂部,粗汽油18作為吸收劑進(jìn)入吸收塔4的第四塊板,與來(lái)自富氣平衡罐3的氣相20進(jìn)行逆流接觸反應(yīng),吸收塔頂部引出的貧氣直接進(jìn)入再吸收塔6的下部,與從分餾塔來(lái)的柴油26在再吸收塔發(fā)生反應(yīng),進(jìn)一步吸收貧氣中夾帶的重組分,富吸收油33返回主分餾塔,干氣32從再吸收塔頂排出并入瓦斯管網(wǎng)。工藝參數(shù)如下:富氣壓縮機(jī)出口壓力1.4mpa,富氣平衡罐操作溫度40℃,解吸塔液相進(jìn)料溫度40℃,吸收塔設(shè)置一個(gè)中間冷卻器返塔溫度35℃,解吸塔塔底脫乙烷汽油中乙烷含量0.1wt%,仍然存在穩(wěn)定汽油內(nèi)循環(huán)和柴油再吸收過(guò)程,穩(wěn)定汽油內(nèi)循環(huán)量60t/h,再吸收塔柴油進(jìn)料量25t/h,設(shè)備能耗見(jiàn)表1。表1能耗項(xiàng)目實(shí)施例1實(shí)施例2比較例1比較例2解吸塔再沸器熱負(fù)荷3926kw3947kw4230kw5233kw穩(wěn)定塔再沸器熱負(fù)荷5827kw5801kw5903kw8826kw補(bǔ)充汽油吸收劑循環(huán)量0t/h0t/h0t/h60t/h柴油吸收劑流量50t/h50t/h25t/h離子液體復(fù)合吸收劑流量40t/h--真空泵能耗增加210kw增加190kw增加220kw-富氣壓縮機(jī)能耗增加160kw增加147kw增加170kw-干氣中c3+含量(v%)0.7%0.6%1%2.8%汽油收率增加0.79t/h0.78t/h-當(dāng)前第1頁(yè)12