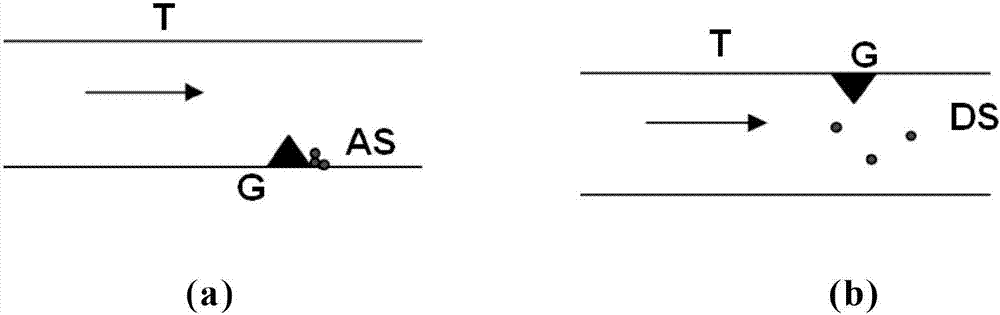
描述本發(fā)明涉及用于增加重油轉化能力的系統(tǒng)和相應的方法。重石油產品的加氫轉化可以使用不同的工藝系統(tǒng)實現。該技術的核心是加氫轉化反應器,其可以是固定床型、沸騰床型或漿料型。在后一種情況下,催化劑分散在反應介質中并均勻分布在反應器自身內。一個est系統(tǒng)(enislurrytechnology)(it-mi2007a1044;it-mi2007a1045;it-mi2007a1198;it-mi2008a1061;it-mi2010a1989)提供將流出物從反應器頭部遞送至hp/ht高壓/高溫液-氣分離器。離開hp/ht分離器的氣體被傳送到氣體處理段,富含氫氣的流從所述氣體處理段中被回收并再循環(huán)到反應器中,同時液體在降低的壓力和溫度下通過一系列的容器(中壓分離器、常壓塔和真空塔)以分離反應產物并引起催化劑和未轉化的裝料的再循環(huán)。如果反應產物僅在氣相(vpo)(氣相流出物)中獲得,則可以避免在反應器外部的可能導致焦炭形成的低壓段,即使這導致設備的產能的降低。當存在催化劑并且不存在氫氣時,在低于反應器壓力的壓力下,通過實驗已經發(fā)現,可以發(fā)生導致產生氫氣和焦炭的脫氫反應。在容器中的液體滯留物(liquidholdup)中的高溫、低壓和長停留時間可以使在反應器外部具有與反應器內相同數量級的固體形成。除此之外,如果真空單元在設計階段未被制成足夠的尺寸,則在真空塔底部的氫氣的形成可能對塔的分餾能力有顯著的影響。通過采用est系統(tǒng)(根據該系統(tǒng),僅在氣相(vpo)中獲得產物,我們將稱該系統(tǒng)為est-vpo),漿料被限制在高h2分壓的區(qū)域,這消除了與脫氫和在反應器外部形成固體相關的所有問題。相對于這一優(yōu)勢,采用從hp/ht分離器直接再循環(huán)的est-vpo設備的產能,對于相同的反應溫度,顯著低于采用從真空塔再循環(huán)的est設備的產能。通過提高反應溫度可以補償產能的損失,即使這導致反應器自身內固體的形成增加。由于氣體自身的汽提效應(strippingeffect),將具有高h2濃度的氣體(也稱為“二次(secondary)”氣體,以便將其與進料至反應器的具有相同組成的“一次”氣體區(qū)別開來)進料至在反應器與高溫/高壓分離器之間的連接管線是提高est-vpo設備的轉化能力的一種方式。不提供二次氣體的使用的est-vpo系統(tǒng)對于相同的操作條件具有較小的產能,因為離開hp/ht分離器并再循環(huán)到反應器的液體具有與離開反應器的液體相同的組成。使用二次氣體增加離開分離器頂部的反應產物的生產量(throughput)。同時,再循環(huán)到反應器中的液相的組成變化并再次經受加氫轉化反應,但此時,其較輕組分已經被貧化,所述較輕組分已經進入氣相中。由于產物只能從est-vpo系統(tǒng)中的分離器的頂部離開,因此其生產量的增加與設備的產能的增加相一致。可以證明,再循環(huán)到反應器中的液體在組成方面與離開反應器的液體越相似,朝向輕質產物的形成的轉換(shift)越多。與沒有提供其的est-vpo系統(tǒng)相比,通過二次氣體的汽提行為的作用,再循環(huán)到反應器中的液體將比離開反應器的液體更重,并且因此與氣相一起離開的產物的量將增加,盡管具有不同的組成。將具有高氫氣含量的氣體進料至在反應器的頭部和高壓/高溫hp/ht分離器之間的連接管線使增加est-vpo系統(tǒng)的轉化能力成為可能。二次氣體進料下游的管線的長度充當理論液/氣平衡階段。連接管線的幾何結構和流體動力學被設計成在進入分離器之前實現在反應器流出物/二次氣體混合物中的液體和蒸氣之間的平衡。在不需要實現液/氣平衡的情況下,添加二次氣體的效果在最壞的情況下可以被減小到僅僅添加氣體。雖然使用汽提氣體來幫助釋放通常將被限制在液相中的氣相中的組分并將汽提氣體進料至在反應器的頭部和分離器之間的連接管線是已知的(it-mi2007a1044),但沒有提供關于如何將汽提氣體進料至該管線的描述。在反應器的頭部和分離器之間的連接管線必須被適當地設計,以便在流進入分離器之前實現流中的液/氣平衡。我們現在已經發(fā)現,在進入液-氣分離器之前,在反應器的頭部和分離器之間的連接管線的合適的向上傾斜對于實現液/氣平衡是必不可少的。在連接管線的合適長度和/或合適的橫截面處將選擇的傾斜與二次氣體進料管線的合適的插入組合也可能是可行的。構成本發(fā)明主題的用于重油的加氫轉化的系統(tǒng)基本上包括反應器、液-氣分離器和用于在反應器外部汽提轉化產物的段,該段包括用于進料汽提氣體的導管,所述導管以使得所述氣體進料發(fā)生在反應器的頭部和液-氣分離器之間的連接導管中的點處的方式被定位,其中所述連接導管至少從進料點向上傾斜,并且坡度在2%和20%之間,優(yōu)選地在3%和12%之間。在管線適當地向上傾斜的情況下,在離開反應器的氣/液生產量的特定范圍內,建立了分層的波式流動狀態(tài)(stratifiedwavyflowregime),其中相之間的合適的再混合從二次氣體被進料的點發(fā)生。分層的波式流動狀態(tài)的確立使與氣體接觸的液體的表面的持續(xù)更新成為可能,從而提高物料交換的效率。建議的是,汽提氣體進料導管應當相對于在反應器的頭部與液-氣分離器之間的連接導管的軸線以在20°和65°之間、更優(yōu)選地在30°和60°之間、甚至更優(yōu)選地在40°和50°之間的角度傾斜。還可行的是,汽提氣體流應該優(yōu)選地沿向下的方向發(fā)生。還優(yōu)選的是,具有上文建議的傾斜角的所述進料導管應位于穿過連接導管的軸線的垂直平面中。優(yōu)選地,提供在反應器的頭部和液-氣分離器之間的連接的導管的橫截面(a)和在對于汽提氣體的進入點與至分離器的進入點之間的該導管的部分的長度(l)滿足以下關系:(a×l)(qv+qvsec+ql)>10s,更優(yōu)選地>15s,(qv+ql)/a>0.5m/s,更優(yōu)選地>1m/s,2>qvsec/qv>0.25,更優(yōu)選地1>qvsec/qv>0.5其中qv和ql是離開反應器的頭部的蒸氣和漿料(液體+固體)的體積生產量,并且qvsec是二次氣體的體積生產量。在圖1中圖示了將反應器的頭部連接到液-氣分離器的導管(t)和用于汽提氣體的進入的導管(i)的一個實施方案。離開反應器的氣體和漿料的流(1)在導管(t)上的點(b)處進入,并且借助于通過進入導管(i)進入的氣體在點(c)和點(f)之間的部分中經歷汽提,所述進入導管(i)以相對于導管(t)的軸線在20°和65°之間的角度傾斜。進入導管所插入的導管(t)的段相對于水平面以在2%至20%之間的坡度向上傾斜。已經被汽提的氣體和漿料的流最終在點(f)處離開以進入分離器。導管(t)的段的長度(l)從用于汽提氣體的進入點延伸直到分離器的進入點(在圖1中從點(c)到點(f),穿過點(d)和(e))??梢詫⒂兄谝合嗪蜌庀嗟拿芮性倩旌喜⑶以试S實現液/氣平衡的具有合適的幾何結構的障礙物插入連接反應器的頭部至分離器的入口的導管內。建議的是,所述障礙物沿著所述導管內的頂壁被插入,所述導管提供反應器的頭部與液-氣分離器之間以下述方式的連接:所述方式使得氣體在液體下方穿過,從而帶來足夠的再混合,并且同時避免在障礙物后面的固體的任何積聚,所述積聚可能由于導管的正坡度而更會發(fā)生。該實施方案在圖2中圖示出,其中障礙物(g)位于:●沿著導管(t)的下壁,可能會出現固體的積聚(as)的問題(圖2a);●沿著導管(t)的上壁,固體保持分散(ds)(圖2b)。該系統(tǒng)適用于其中流出物包括兩相l(xiāng)/v流、還包括從離開反應器的至少一個液體流和至少一個蒸氣流的合并獲得的流的所有類型的反應器,所述反應器包括可以包含分散的固體的固定床反應器、漿料反應器優(yōu)選地漿料泡罩塔(slurrybubblecolumn)和沸騰床反應器。本發(fā)明的另一個目的是使用根據本發(fā)明的系統(tǒng)進行的用于重油的加氫轉化的方法。所述用于重油的加氫轉化的方法包括:將重油送入在具有合適的氫化催化劑的反應器中進行的加氫處理階段,氫氣或氫氣與輕質烴的混合物被遞送至所述反應器中;用合適的汽提氣體對離開反應器的液體流和蒸氣流、或對從離開反應器的至少一個液體流和至少一個蒸氣流的合并獲得的流進行汽提階段;使所述流轉到在合適的分離器中的液-氣分離,所述液-氣分離將被再循環(huán)到反應器的液相(較少凈化地)與含有轉化產物的氣相分離,所述汽提階段是借助于遞送汽提氣體的導管進行的,所述導管位于連接反應器的頭部和液-氣分離器的導管上的點,并且其特征在于,所述連接導管至少從進入點以在2%和20%之間,優(yōu)選地在3%和12%之間的坡度向上傾斜。在具有漿料相氫化催化劑的反應器中進行的加氫處理階段的情況下特別推薦所要求保護的方法,所述反應器優(yōu)選地選自泡罩塔或沸騰床反應器。當使用漿料相反應器進行時,還建議其應當在反應器的出口處以大于0.75、優(yōu)選地大于0.85的體積比操作:其中漿料包括液體加固體。在反應器的頭部與液-氣分離器之間的連接導管的橫截面(a)與從用于汽提氣體的進入點到分離器的進入點的所述導管的段的長度(l)(在圖1中從點(c)到點(f))優(yōu)選地滿足以下關系:(a×l)(qv+qvsec+ql)>10s,更優(yōu)選地>15s,(qv+ql)/a>0.5m/s,更優(yōu)選地>1m/s,2>qvsec/qv>0.25,更優(yōu)選地1>qvsec/qv>0.5其中qvsec是二次氣體的體積生產量。加氫處理階段優(yōu)選地在400℃和450℃之間的溫度下和在100大氣壓和200大氣壓之間的壓力下進行。氫化催化劑優(yōu)選地基于mo或w硫化物。更多細節(jié)可以在上述申請it-mi2007a1198中找到。為了更好地定義本發(fā)明,描述了在根據本發(fā)明的方法實施方案中證明使用二次氣體的有效性的一些實施例,其導致在氣相(vpo)中獲得產物。實施例如前所述,從est系統(tǒng)(其中轉化產物在液相中并且存在低壓段)到est-vpo系統(tǒng)(其中產物僅留在氣相中)的改變導致在設備的潛在產能上的大幅度的減少。為了克服這個,必須增加反應溫度并且必須使用二次氣體,因為在沒有后者的情況下,在其他操作條件相同的情況下,設備的潛在產能與est參考案例相比無論如何都減少約20%。將反應器的頭部連接到液-氣分離器的導管(t)和進料汽提氣體的導管(i)的實施方案是圖1中已經圖示的,其中:●連接用于二次氣體的進入點到點(d)的導管的段以6%的坡度向上傾斜;●用于汽提氣體的進入導管相對于將反應器的頭部連接到液-氣分離器的導管的軸線傾斜45°的角度;●進料至在反應器的頭部和分離器之間的連接導管的汽提氣體的流在穿過連接導管的軸線的垂直平面中在向下的方向上發(fā)生。要牢記的是,二次氣體的流量(wsec)在0和100之間變化,其中0對應于不存在二次氣體,而100表示二次氣體的流量能夠在使用est系統(tǒng)下確保設備的相同的潛在產能(wsecest),雖然在較高的反應溫度下運行,但是隨著二次氣體的變化,設備產能和百分比方面(percentageterm)的增加在表1中示出。表1(wsec/wsecest)×100新鮮裝料的增加0-103.4%206.3%308.9%4011.1%5013.1%6014.8%7016.3%8017.7%9018.9%10020.1%因此,例如使用實現est系統(tǒng)設備的潛在產能所需的二次氣體的生產量的50%(但是在較高溫度下操作),存在新鮮裝料的13.1%的增加。以百分比增加表示的二次氣體對新鮮裝料的生產量的影響可以通過圖表示出在表中列出的內容來顯示(圖3)。圖4還示出了與est的潛在產能(wffest)相比,二次氣體對在較高溫度下操作的est-vpo設備的產能(wffvpo)的增加的影響。在est的情況下,在使用二次氣體的50%的流量下,設備的潛在產能達到根據上文的定義可以獲得的最大生產量的94%。二次氣體的汽提效果具有以下的結果:與其中未使用二次氣體的情況相比“較重”的產物離開設備,但在生產率方面實現的益處是可觀的??梢酝ㄟ^分析作為相對于二次氣體的百分比表示的(wsec/wsecest)比率的函數的柴油、石腦油和vgo產物的百分比增加來評估獲得的產物的不同的品質,如表2所示。表2-隨著二次氣體的變化的產物增加這里再次地,如果考慮二次氣體的生產量的50%,則所獲得的效果在柴油、石腦油和vgo中分別是11.2%、10.5%和26.8%的增加。對三種感興趣的產物的總體增加的效果也在圖5中示出,其包括相對于以百分比表示的二次氣體的(wsec/wsecest)×100比率的產物的生產量的變化。另外,采用如上文定義的二次氣體的50%,實現了對于柴油、石腦油和vgo分別可以實現的最大生產量的94%、96%和89%(圖6)。如可以看出的,與柴油和石腦油相比,二次氣體對離開設備的vgo具有更大的影響,這表明汽提效應有效地將甚至相當重的化合物朝向氣相置換(displace)。已經指出,與不使用二次氣體的est-vpo系統(tǒng)相比,再循環(huán)到反應器中的液體比由于氣體的汽提行為而離開反應器自身的液體更重。事實上,當離開hp分離器、再循環(huán)到反應器的液相的分子量與離開反應器的頭部的液相的分子量相比較被監(jiān)測時,隨著二次氣體的增加,觀察到兩個流在組成和因此的分子量方面具有越來越明顯的差異。在沒有二次氣體的情況下,兩個液相的分子量(mw)是相同的,但是隨著二次氣體的生產量增加,液相中存在的較輕的化合物傳送到產物中,然后該產物在氣相中離開設備,而液相變得越來越重。根據上文給出的定義,采用50%的二次氣體,兩個流的分子量相差11%。圖7示出了隨著二者均以百分比表示的二次氣體(wsec/wsecest)改變,兩個液體流的mw的變化。權利要求書(按照條約第19條的修改)1.用于重油加氫轉化的系統(tǒng),基本上包括反應器、液-氣分離器和在所述反應器外部的轉化產物的汽提段,所述汽提段包括在所述反應器頭部和所述液-氣分離器之間的連接導管的點處的汽提氣體的供應導管,所述連接導管至少從所述汽提氣體的供應點以相對于水平面在2%和20%之間的坡度向上傾斜。2.根據權利要求1所述的系統(tǒng),其中所述汽提氣體的所述供應導管以在20°和65°之間、優(yōu)選地在30°和60°之間、更優(yōu)選地在40°和50°之間的角度傾斜于在所述反應器的頭部與所述液-氣分離器之間的所述連接導管的軸線。3.根據權利要求1所述的系統(tǒng),其中進入在所述反應器頭部和所述分離器之間的所述連接導管的汽提氣體流是以向下的方向。4.根據權利要求2所述的系統(tǒng),其中所述供應導管位于穿過所述連接導管的軸線的垂直平面中。5.根據權利要求1所述的系統(tǒng),其中所述反應器是泡罩塔反應器或沸騰床反應器。6.根據權利要求1所述的系統(tǒng),其中在所述反應器頭部和所述液-氣分離器之間的所述連接導管至少從所述汽提氣體的所述供應點以在3%和12%之間的坡度向上傾斜。7.根據權利要求1所述的系統(tǒng),其中具有合適的幾何結構的障礙物被插入在所述反應器頭部和所述氣-液分離器之間的所述連接導管內,優(yōu)選地沿著在所述導管內的上壁,這有助于液相和氣相的密切混合并且使實現液/氣平衡成為可能。8.用于重油加氫轉化的方法,包括:將重油轉到在具有合適的氫化催化劑的反應器中進行的加氫處理階段,氫氣或氫氣與輕質烴的混合物被進料至所述反應器中;用合適的汽提氣體對離開所述反應器的液相流和氣相流、或對合并離開所述反應器的至少一個液體流和至少一個蒸氣流而獲得的流進行汽提的步驟;使所述流轉到在合適的分離器中的液-氣分離,所述液-氣分離將至反應器的再循環(huán)的液相,來自凈化的一部分,與含有僅在氣相中獲得的轉化產物的氣相分離,所述汽提步驟借助于在所述反應器頭部和所述液-氣分離器之間的所述連接導管中的點處進料汽提氣體來進行,其特征在于,所述連接導管至少從所述汽提氣體的供應點以相對于水平面在2%和20%之間的坡度向上傾斜。9.根據權利要求8所述的方法,其中所述加氫處理步驟在具有在漿料相中的氫化催化劑的反應器中進行,所述反應器優(yōu)選地選自泡罩塔反應器或沸騰床反應器。10.根據權利要求9所述的方法,其中在所述反應器的出口處的體積比:大于0.75,優(yōu)選地大于0.85,其中所述漿料包括液體加固體。11.根據權利要求8所述的方法,其中用于所述汽提氣體的所述進料導管相對于在所述反應器頭部和所述液-氣分離器之間的所述連接導管的軸線以在20°和65°之間、優(yōu)選地在30°和60°之間、更優(yōu)選地在40°和50°之間的角度傾斜。12.根據權利要求8所述的方法,其中在所述反應器頭部和所述液-氣分離器之間的所述連接導管的段(a)與從所述汽提氣體的所述進入點到所述分離器的進入點的所述導管的段的長度(l)滿足以下關系(a×l)(qv+qvsec+ql)>10s(qv+ql)/a>0.5m/s2>qvsec/qv>0.25其中qv和ql是離開所述反應器的所述頭部的蒸氣和漿料(液體+固體)的體積流量,并且二次氣體的體積流量為qvsec。13.根據權利要求10所述的方法,其中在所述反應器頭部和所述液-氣分離器之間的所述連接導管的段(a)與從對于所述汽提氣體的所述進入點到所述分離器的進入點的所述導管的段的長度(l)滿足以下關系(a×l)(qv+qvsec+ql)>15s(qv+ql)/a>1m/s1>qvsec/qv>0.5。14.根據權利要求8所述的方法,其中所述加氫處理步驟在400℃和450℃之間的溫度和在100大氣壓和200大氣壓之間的壓力下進行。15.根據權利要求8所述的方法,其中所述氫化催化劑是基于mo或w硫化物。當前第1頁12