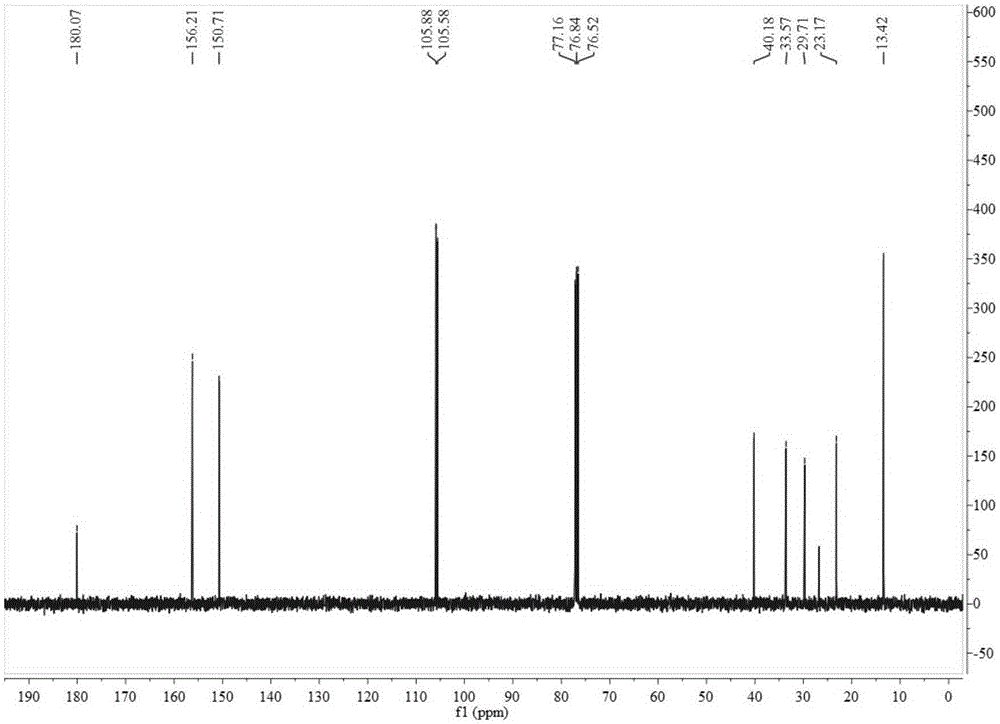
本發(fā)明涉及一種基于木質(zhì)纖維素為原料獲得平臺化合物合成液態(tài)鏈烴燃料的新路線。本發(fā)明方法共分為三部分:1)乙酰丙酸的脫水產(chǎn)物—當(dāng)歸內(nèi)酯在酸催化劑上(如路易斯酸、質(zhì)子酸、固體酸等)與2-甲基呋喃通過酸催化烷基化反應(yīng)制取4,4-二(5-甲基呋喃-2-基)戊酸;2)通過對4,4-二(5-甲基呋喃-2-基)戊酸進行加氫,有效除去其中的碳-碳雙鍵和碳-氧雙鍵,制取飽和的含氧有機化合物;3)通過采用金屬-碳催化劑對加氫后的烷基化產(chǎn)物加氫脫氧,從而獲得碳鏈長度在8至15之間的生物質(zhì)航空煤油或高質(zhì)量柴油。
背景技術(shù):
:航空煤油是一種專為飛行器而制備的燃油,為確保飛機在萬米高空正常飛行,對航空燃料制定了非常嚴(yán)格的標(biāo)準(zhǔn),要求具有高熱值(>43MJ/kg)、低冰點(JetA1≤-47℃,JetA1≤-40℃)、適度的密度(0.775~0.840g/cm3)和良好的運動黏度(-20℃時,≤8.0mm2/s)等技術(shù)指標(biāo)。航空煤油是國際上需求量很大的液體燃料。它主要由碳數(shù)范圍在C8~C16間的鏈狀烷烴、芳烴、以及環(huán)烷烴等組成,沸程為160~300℃。以目前常見JP-8為例,其經(jīng)典組成如下:C8~C15的直鏈烷烴占35%,C8~C15的支鏈烷烴占35%,C7~C10的芳香烴占18%,C6~C10的環(huán)烷烴占7%。柴油是主要的運輸燃料之一,主要是由C9至C18的鏈烴、環(huán)烴、芳香烴組成,其沸點在170~390℃之間。目前,航空煤油和柴油主要以化石資源(煤和石油)為原料制取,煤和石油都是不可再生的能源,由它們合成航空煤油和柴油在制造和使用過程會產(chǎn)生大量的二氧化碳和二氧化硫,造成溫室效應(yīng)和環(huán)境污染。和化石能源不同,生物質(zhì)屬于可再生能源,生物質(zhì)燃料在燃燒過程中產(chǎn)生的二氧化碳可以被其生長過程通過光合作用消耗的二氧化碳所抵消,因此生物質(zhì)燃料在整個使用過程中是二氧化碳中性的。因此從保護環(huán)境、國家能源安全以及潛在的經(jīng)濟價值三方面考慮,需要大力發(fā)展生物質(zhì)航空煤油技術(shù)。目前,生物質(zhì)液體燃料經(jīng)歷了三個階段,第一階段利用動物或者植物油與低碳數(shù)的甲醇或乙醇催化反應(yīng)轉(zhuǎn)化成高級脂肪酸甲酯或乙酯,經(jīng)洗滌干燥即得到生物柴油。第二階段生物質(zhì)液體燃料是以可食用的玉米、大豆和向日葵等為原料,通過發(fā)酵和提純等手段制取生物乙醇。第一階段和第二階段生產(chǎn)方式合成生物質(zhì)液體燃料在歐洲,美洲等地區(qū)作為運輸燃料已有實際應(yīng)用。但是,它是以食用油、糧食為原料,原料有限、成本高、與人爭地爭糧,不適合我國人多地少的國情。第三階段生物質(zhì)液體燃料是以不可食用的木質(zhì)纖維素為原料,主要有三種途徑生成燃料:1)熱化學(xué)氣化生物質(zhì)到合成氣,然后通過費托合成制取烷烴,該過程工藝比較成熟,但是需要高溫高壓的條件;2)高溫?zé)峤馍镔|(zhì)制取生物質(zhì)油,該過程復(fù)雜,且制得的生物質(zhì)油品質(zhì)較差,無法直接用作發(fā)動機燃料,需進行進一步精煉;3)以木質(zhì)纖維素為原料獲得的生物質(zhì)平臺化合 物分子,通過羥醛縮合、烷基化反等碳-碳偶聯(lián)反應(yīng),然后加氫脫氧制取液態(tài)烷烴,該過程條件相對比較溫和,合成路線靈活。2005年,Dumesic、Huber等人在[Science,2005,308,1446-1450]和專利[US7,671,246]報道了羥甲基糠醛或糠醛與丙酮(或四氫糠醛分子間)通過堿催化的羥醛縮合反應(yīng)制取具有航空煤油鏈長范圍的含氧有機化合物,然后通過加氫和加氫脫氧等步驟制取C8至C15范圍的液態(tài)烷烴。用Pt/SiO2-Al2O3作為加氫脫氧催化劑,采用固定床四相流反應(yīng)器,反應(yīng)過程中需要加入十六烷防止催化劑失活,工藝比較復(fù)雜。Corma等人[Angew.Chem.Int.Ed.2011,50,1-5]報道了甲基呋喃與丁醛、5-甲基糠醛、5-羥甲基糠醛以及其自身三聚反應(yīng),制備了具有航空煤油或柴油鏈長范圍的含氧有機化合物,其后通過梯度床反應(yīng)器加氫脫氧獲得了液體燃料。最近,MarkMascal等人[Angew.Chem.Int.Ed.2014,53,1854-1857]報道了乙酰丙酸在蒙脫土K10催化脫水制得當(dāng)歸內(nèi)酯,當(dāng)歸內(nèi)酯在碳酸鉀催化下生成當(dāng)歸內(nèi)酯的二聚物,該二聚體在Ir-ReOx/SiO2催化加氫脫氧制得高產(chǎn)率的C7-C10的燃料。張鎖江等人[GreenChem,2014,16,3589–3595]報道了乙酰丙酸在H-ZSM-5/SiO2催化脫水制得了當(dāng)歸內(nèi)酯,在碳酸鉀、碳酸鈉或碳酸氫鈉催化下獲得當(dāng)歸內(nèi)酯的二聚和三聚的混合物,在10%Pd/C催化下加氫脫氧制得C6-C15的化合物燃料。在本課題組前期的工作中[中國專利:申請?zhí)枺?01110346501.1],采用2-呋喃與乙酰丙酸和乙酰丙酸乙酯進行羥烷基化/烷基化反應(yīng)制得C15的含氧有機化合物,通過對這些有機化合物直接加氫脫氧獲得具有航空煤油鏈長范圍的低凝固點支鏈烷烴。本專利中,利用乙酰丙酸脫水生成的當(dāng)歸內(nèi)酯具有更高的反應(yīng)活性。相同條件下,當(dāng)歸內(nèi)酯與2-甲基呋喃反應(yīng)獲得C15的含氧化合物的產(chǎn)率明顯高于乙酰丙酸、乙酰丙酸乙酯與2-甲基呋喃羥烷基化/烷基化生成C15含氧化合物的產(chǎn)率。當(dāng)歸內(nèi)酯與2-甲基呋喃反應(yīng)獲得C15的含氧化合物通過加氫和加氫脫氧獲得了具有航空煤油鏈烴范圍的生物質(zhì)液體燃料。技術(shù)實現(xiàn)要素:本發(fā)明的目的在于提供一種基于木質(zhì)纖維素為原料獲得平臺化合物為原料,建立完全不依賴化石能源的航空煤油和高品質(zhì)柴油鏈烴的新合成路線。本發(fā)明是通過以下技術(shù)方案實現(xiàn)的:該路線共分為三步:1)在酸催化劑的作用下,以乙酰丙酸脫水生成的當(dāng)歸內(nèi)酯與2-甲基呋喃通過液相烷基化反應(yīng),制取4,4-二(5-甲基呋喃-2-基)戊酸。2)通過對4,4-二(5-甲基呋喃-2-基)戊酸進行加氫,有效除去其中的碳-碳雙鍵和碳-氧雙鍵,制取飽和的含氧有機化合物。3)通過采用金屬-碳催化劑對加氫后的烷基化產(chǎn)物加氫脫氧,從而獲得碳鏈長度在8至15之間的生物質(zhì)航空煤油或高質(zhì)量柴油。第一步烷基化反應(yīng),當(dāng)歸內(nèi)酯與2-甲基呋喃摩爾比為10:1至1:20,優(yōu)選為1:2,未反應(yīng)的原料可通過蒸餾或精餾從反應(yīng)體系中移除,可循環(huán)使用;反應(yīng)溫度在0-100℃間,反應(yīng)時間為0.1-48h,反應(yīng)在溶液中或無溶劑存在的液態(tài)條件 下進行,溶劑為甲醇、乙醇或四氫呋喃。優(yōu)選溫度為25-60℃,優(yōu)選反應(yīng)時間為0.5-2h。使用的酸催化劑為液體酸、固體酸或路易斯酸:所述液體酸為三氟甲基磺酸、對甲苯磺酸、鹽酸、硫酸或磷酸等質(zhì)子酸中的一種或兩種以上的混合物;固體酸為Nafion樹脂、Amberlyst樹脂、蒙脫土、酸性金屬氧化物、分子篩中的一種或兩種以上的混合物,路易斯酸為無水氯化鐵、無水氯化鋅、無水氯化錫或氯化鈦等中的一種或兩種以上的混合物。通過烷基化反應(yīng)可以在較溫和的反應(yīng)條件下和較短的反應(yīng)時間內(nèi)高產(chǎn)率獲得4,4-二(5-甲基呋喃-2-基)戊酸;第二步對4,4-二(5-甲基呋喃-2-基)戊酸在催化劑作用下進行加氫反應(yīng),反應(yīng)在溶液中進行,溶劑為甲醇、乙醇、四氫呋喃,溶液的濃度為0.5-100%,優(yōu)選為0.5-80%。加氫反應(yīng)可采用間歇式釜式反應(yīng)器或固定床反應(yīng)器進行;釜式反應(yīng)器的條件為:溫度100-400℃,氫氣壓力為常壓至10.0MPa,反應(yīng)時間為0.5-60h;優(yōu)選條件為:溫度140-350℃,氫氣壓力4-7MPa,反應(yīng)時間0.5-5h;固定床反應(yīng)器的條件為:溫度100-400℃,氫氣壓力為常壓至10.0MPa,反應(yīng)原料/催化劑的質(zhì)量空速為0.1-10.0h-1,氫氣與反應(yīng)原料的摩爾比為20-1500。優(yōu)選條件為:溫度140-350℃,氫氣壓力4-7MPa,反應(yīng)原料/催化劑的質(zhì)量空速為0.3-2h-1,氫氣與反應(yīng)原料的摩爾比為200-800。第三步中對4,4-二(5-甲基呋喃-2-基)戊酸加氫產(chǎn)物進行催化加氫脫氧,反應(yīng)在液態(tài)條件下進行,反應(yīng)體系中可添加溶劑,溶劑為甲醇、乙醇、四氫呋喃;溶液的濃度為0.5-100%;原料溶液的濃度優(yōu)選為60-100%;加氫脫氧反應(yīng)可采用間歇式釜式反應(yīng)器或固定床反應(yīng)器進行;釜式反應(yīng)器的條件為:溫度100-400℃,氫氣壓力為常壓至10.0MPa,反應(yīng)時間為0.5-60h;優(yōu)選條件為:溫度150-400℃,氫氣壓力4-7MPa,反應(yīng)時間0.5-5h;固定床反應(yīng)器的條件為:溫度100-400℃,氫氣壓力為常壓至10.0MPa,反應(yīng)原料/催化劑的質(zhì)量空速為0.1-10.0h-1,氫氣與反應(yīng)原料的摩爾比為20-1500。優(yōu)選條件為:溫度150-400℃,氫氣壓力4-7MPa,反應(yīng)原料/催化劑的質(zhì)量空速為0.3-2h-1,氫氣與反應(yīng)原料的摩爾比為200-800。催化劑為以下的一種或多種:活性炭或者介孔碳為載體負載貴金屬Pt、Pd、Ru、Ir中的一種或多種的負載型催化劑。負載型貴金屬催化劑采用等體積浸漬的方法制備:配制2-10%的貴金屬前軀體溶液,按照計量比加入硝酸處理過的活性炭或介孔碳載體中等體積浸漬,催化劑中金屬的含量占0.5-10%,靜置2h后在80-120℃下干燥6-24h,再在200-600℃下用氫氣還原1-10h,待溫度降低至室溫后通入1%O2鈍化4h以上。通過以上步驟,取得了很高的航空煤油(或高品位柴油)鏈烷烴收率80%(以碳計算)以上。實現(xiàn)了以木質(zhì)纖維素衍生物為原料到航空煤油或高品位柴 油的選擇性合成。附圖說明圖1為4,4-二(5-甲基呋喃-2-基)戊酸的H-NMR圖;圖2為4,4-二(5-甲基呋喃-2-基)戊酸的C-NMR圖。具體實施方式下面將以具體的實施例來對本發(fā)明加以說明,但本發(fā)明的保護范圍不局限于這些實施例。實施例1.催化劑的制備:1)酸催化劑:Nafion、Amberlyst樹脂固體酸,F(xiàn)eCl3、ZnCl2、SnCl4、TiCl4、FeCl3、三氟甲基磺酸、硫酸和鹽酸為直接購買的商業(yè)催化劑產(chǎn)品。2)加氫脫氧催化劑的制備:配制質(zhì)量比10%的氯化鈀、氯化釕、氯鉑酸、氯銥酸,將其中的一種或兩種以上的金屬鹽溶液按照計量比加入硝酸處理過(50g活性炭中加入250mL33%的硝酸溶液,在80℃的水浴中處理12小時,過濾,用去離子水洗至中性,然后在120℃的烘箱干燥12小時)的活性炭中等體積浸漬,然后靜置2h,在120℃下干燥過夜,在500℃下用氫氣還原2h,待溫度降低至室溫后通入1%O2鈍化,可制備單金屬或雙金屬負載型催化劑。表1貴金屬催化劑實施例載體金屬及其擔(dān)載量實施例1AC5%Pd實施例2AC5%Ru實施例3AC5%Pt實施例4AC5%Ir2.第一步反應(yīng):在50mL的圓底燒瓶中加入一定量的催化劑、0.98g當(dāng)歸內(nèi)酯、1.68g2-甲基呋喃,在恒溫水浴下攪拌一定時間,獲得4,4-二(5-甲基呋喃-2-基)戊酸,詳細反應(yīng)結(jié)果見表2。表2烷基化反應(yīng)及其結(jié)果由表2中實施例5-27給出的目標(biāo)產(chǎn)物4,4-二(5-甲基呋喃-2-基)戊酸的氣相色譜產(chǎn)率,從中可以看出,當(dāng)歸內(nèi)酯與2-甲基呋喃反應(yīng),在不同的催化劑:酸性Nafion、Amberlyst樹脂、H2SO4、三氟甲基磺酸、磷酸、FeCl3、SnCl4、TiCl4、ZnCl2等催化劑催化下,均有一定產(chǎn)率的產(chǎn)物生成。圖1和圖2為典型的當(dāng)歸內(nèi)酯與2-甲基呋喃烷基化產(chǎn)物的H-NMR圖和C-NMR圖,可以證明通過烷基化反應(yīng)可以合成出目標(biāo)產(chǎn)物。3.第二步反應(yīng):在固定床反應(yīng)器中,反應(yīng)管中裝入1.80g催化劑,裝入固定床中。利用高壓泵打入純化后的30%質(zhì)量濃度的4,4-二(5-甲基呋喃基)戊酸的甲醇溶液,在160℃下,氫氣壓力6.0MPa,氫氣流量120mL/min,泵流量為0.16mL/min。以Pd/C、Ru/C和Pt/C等催化劑作為加氫催化劑,一定反應(yīng)時間。加氫獲得的主要產(chǎn)物為4,4-二(5-甲基四氫呋喃-2-基)-戊醇,詳細反應(yīng)結(jié)果見表3。表3催化劑、溶劑、原料濃度對加氫反應(yīng)的影響由表3可以看出,在底物質(zhì)量濃度為25-30%時,Pd/C、Ru/C、Ir/C催化劑可以實現(xiàn)原料的完全加氫,Pd/C在連續(xù)加氫反應(yīng)48h,活性仍然保持目標(biāo)產(chǎn)物的100%轉(zhuǎn)化。4.在第三步反應(yīng)中,在固定床反應(yīng)器中,將1.8g催化劑裝入反應(yīng)管中,保 持反應(yīng)器中壓力為6.0MPa,溫度為350℃,用高效液相色譜泵以0.04mL/min的速度將第二步中的產(chǎn)品泵入反應(yīng)器中,同時將氫氣以120mL/min通入反應(yīng)器中,原料為通過減壓蒸餾純化的實施例28-45中產(chǎn)物的一種或多種,具體反應(yīng)結(jié)果見表4。表4不同催化劑和反應(yīng)時間對加氫脫氧反應(yīng)的影響由表4可以看出,當(dāng)溫度350℃時,高效液相色譜泵以0.04mL/min,氫氣壓力為6.0MPa,氫氣流量大于120mL/min時,實施例46-60的產(chǎn)物,即為碳數(shù)在8-15之間的液態(tài)混合烷烴燃料,它們可以作為航空煤油和高品質(zhì)柴油直接使用,或者作為提高十六烷值的添加劑,以一定比例加入現(xiàn)有的航空煤油和柴油中使用。當(dāng)前第1頁1 2 3