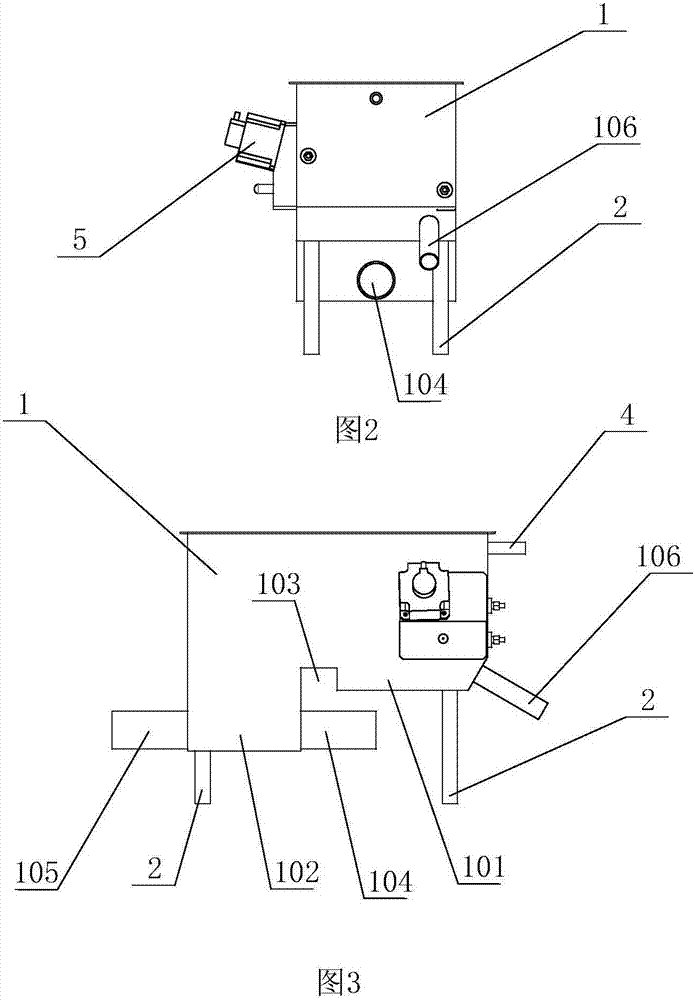
本發(fā)明涉及新型智能制藥設(shè)備技術(shù)領(lǐng)域,尤其是涉及一種制藥過(guò)程中強(qiáng)吸附組分的分離方法及分離裝置,主要用于天然中草藥、生物制藥中較強(qiáng)吸附組分與較弱吸附組分的分離。
背景技術(shù):在制藥工業(yè)中,無(wú)論是天然中草藥、生物制藥、還是合成原料藥,都有一個(gè)很重要的工藝環(huán)節(jié),那就是分離,先將原料藥中的目標(biāo)物與其他物質(zhì)分離,然后才能夠進(jìn)行后續(xù)的工藝過(guò)程。根據(jù)藥物特性可以選擇的分離技術(shù)和設(shè)備有很多,包括各種物理的和化學(xué)的方法。目前,使用最多的物理方法是過(guò)濾,利用物料顆粒直徑的差異,進(jìn)行空間排阻的方式。其次是納入中間介質(zhì),利用并且放大物料分子之間吸附能力的差異,不斷進(jìn)行分子與介質(zhì)之間吸附、解吸附的操作,從而改變分子運(yùn)動(dòng)速度,達(dá)到分離效果。這種方法一般是在一個(gè)或幾個(gè)空心柱體內(nèi)進(jìn)行,所以通常叫做“柱分離”。目前的分離方法中,有的工藝簡(jiǎn)單卻分離效率較低,有的分離效果較高卻工藝較復(fù)雜,且多數(shù)分離方法通過(guò)單一的分離原理實(shí)現(xiàn)分離,嚴(yán)重影響了分離效果及分離效率,從而嚴(yán)重影響了制藥過(guò)程的工作效率。因此,如何提供一種既工藝簡(jiǎn)單,成本較低,又能高效地分離強(qiáng)吸附組分的分離方法是本領(lǐng)域技術(shù)人員亟需解決的技術(shù)問(wèn)題。
技術(shù)實(shí)現(xiàn)要素:本發(fā)明的目的在于提供一種制藥過(guò)程中強(qiáng)吸附組分的分離方法,該分離方法具有工藝簡(jiǎn)單、成本較低以及高效分離的特點(diǎn)。本發(fā)明還提供一種實(shí)現(xiàn)上述分離方法的分離裝置。為解決上述的技術(shù)問(wèn)題,本發(fā)明提供的技術(shù)方案為:一種制藥過(guò)程中強(qiáng)吸附組分的分離方法,將分離帶浸漬穿過(guò)液態(tài)的待分離物料過(guò)濾并同時(shí)吸附所述待分離物料中的目標(biāo)吸附組分,然后用洗脫劑將所述分離帶上的目標(biāo)吸附組分洗脫下來(lái),然后收集洗脫下來(lái)的目標(biāo)吸附組分;所述分離帶包括帶有微孔的改性硅膠纖維帶以及環(huán)繞包裹在所述改性硅膠纖維帶的四周邊沿上的環(huán)狀碳纖維支撐骨架。優(yōu)選的,所述改性硅膠纖維帶的微孔的孔徑為3-100微米,以實(shí)現(xiàn)所述分離帶的過(guò)濾功能。本發(fā)明提供了一種制藥過(guò)程中強(qiáng)吸附組分的分離方法,通過(guò)采用獨(dú)特結(jié)構(gòu)設(shè)計(jì)的分離帶,設(shè)計(jì)所述分離帶包括帶有微孔的改性硅膠纖維帶以及環(huán)繞包裹在所述改性硅膠纖維帶的四周邊沿上的環(huán)狀碳纖維支撐骨架,采用分離帶中的微孔過(guò)濾待分離物料中的目標(biāo)組分,同時(shí)采用分離帶中的改性硅膠纖維吸附待分離物料中的強(qiáng)吸附組分,使得過(guò)濾和吸附同時(shí)進(jìn)行,過(guò)濾過(guò)程主要分離待分離物料中的粒徑較大的目標(biāo)組分,吸附過(guò)程主要分離待分離物料中粒徑較小的目標(biāo)組分,二者相輔相成,相互促進(jìn),使得本發(fā)明提供的分離方法具有工藝簡(jiǎn)單,成本較低,又能高效地分離強(qiáng)吸附組分等特點(diǎn)。本發(fā)明還提供一種實(shí)現(xiàn)上述分離方法的分離裝置,包括用于盛裝所述待分離物料的箱體、支架、分離帶機(jī)構(gòu)、噴淋機(jī)構(gòu)以及動(dòng)力機(jī)構(gòu);所述箱體包括下底面以及四個(gè)側(cè)面,所述箱體的下底面包括高下底面部和低下底面部,所述高下底面部的水平高度高于所述低下底面部的水平高度,在所述高下底面部上且與所述低下底面部的連接處設(shè)置有用于防止洗脫下來(lái)的待吸附組分返流至所述低下底面部處的待分離物料中的圍堰;所述箱體的且與所述低下底面部對(duì)應(yīng)的側(cè)面的下部設(shè)置有用于向所述箱體供給待分離物料的物料入口,所述箱體的且與所述物料入口所在的側(cè)面相對(duì)的側(cè)面的下部設(shè)置有用于將完成分離后的物料排出的物料出口,所述箱體的且與所述高下底面部對(duì)應(yīng)的側(cè)面的下部設(shè)置有用于排出洗脫下來(lái)的待吸附組分的分離液出口;所述支架設(shè)置在所述箱體的下底面上以用于支撐所述箱體;所述分離帶機(jī)構(gòu)包括主動(dòng)擠壓輪、被動(dòng)擠壓輪、中心支撐輪、間隙調(diào)整組件、大滾輪、張緊輪、調(diào)整螺母、分離帶以及滾輪架;所述滾輪架包括對(duì)稱(chēng)設(shè)置的一對(duì)安裝板以及若干個(gè)滾輪架支撐桿,一對(duì)所述安裝板通過(guò)若干個(gè)所述滾輪架支撐桿分別設(shè)置于所述箱體相對(duì)的兩塊內(nèi)側(cè)面上;所述主動(dòng)擠壓輪固定設(shè)置于一對(duì)所述安裝板上,且其軸向中心線(xiàn)偏向所述箱體的下底面與其所在的所述箱體的內(nèi)側(cè)面存在一定的夾角,且所述主動(dòng)擠壓輪懸掛于所述高下底面部的上方,所述主動(dòng)擠壓輪的水平高度高于所述大滾輪的水平高度;所述大滾輪以及中心支撐輪均固定設(shè)置于一對(duì)所述安裝板上,且所述大滾輪以及中心支撐輪的軸向中心線(xiàn)均與其所在的所述箱體的內(nèi)側(cè)面垂直,且所述大滾輪懸掛于所述低下底面部的上方;所述張緊輪活動(dòng)設(shè)置于一對(duì)所述安裝板上,且所述張緊輪的軸向中心線(xiàn)與其所在的所述箱體的內(nèi)側(cè)面垂直,所述張緊輪的安裝點(diǎn)所在的豎直平面位于所述主動(dòng)擠壓輪的安裝點(diǎn)所在的豎直平面與所述大滾輪的安裝點(diǎn)所在的豎直平面之間,所述張緊輪的安裝點(diǎn)的水平高度高于所述主動(dòng)擠壓輪的水平高度,所述調(diào)整螺母設(shè)置于所述安裝板上且與所述張緊輪連接以調(diào)整所述張緊輪的安裝點(diǎn)在所述安裝板上的具體位置;所述中心支撐輪的安裝點(diǎn)所在的豎直平面位于所述主動(dòng)擠壓輪的安裝點(diǎn)所在的豎直平面與所述大滾輪的安裝點(diǎn)所在的豎直平面之間,且所述中心支撐輪的安裝點(diǎn)的水平高度低于所述張緊輪的水平高度,且所述中心支撐輪的安裝點(diǎn)的水平高度高于所述大滾輪的水平高度;所述主動(dòng)擠壓輪與所述動(dòng)力機(jī)構(gòu)傳動(dòng)連接以帶動(dòng)所述主動(dòng)擠壓輪轉(zhuǎn)動(dòng);所述分離帶包括帶有微孔的改性硅膠纖維帶以及環(huán)繞包裹在所述改性硅膠纖維帶的四周邊沿上的環(huán)狀碳纖維支撐骨架,所述分離帶纏繞在所述主動(dòng)擠壓輪、張緊輪、大滾輪以及中心支撐輪上且由所述主動(dòng)擠壓輪帶動(dòng)而作運(yùn)動(dòng);所述被動(dòng)擠壓輪的兩端相應(yīng)地固定設(shè)置于所述箱體的兩個(gè)內(nèi)側(cè)面上,且其軸向中心線(xiàn)與所述主動(dòng)擠壓輪的軸向中心線(xiàn)的延伸方向相同,以與所述主動(dòng)擠壓輪配合擠壓所述分離帶上的液體,所述間隙調(diào)整組件設(shè)置在所述箱體的側(cè)面上且與所述被動(dòng)擠壓輪連接以用于調(diào)整所述被動(dòng)...