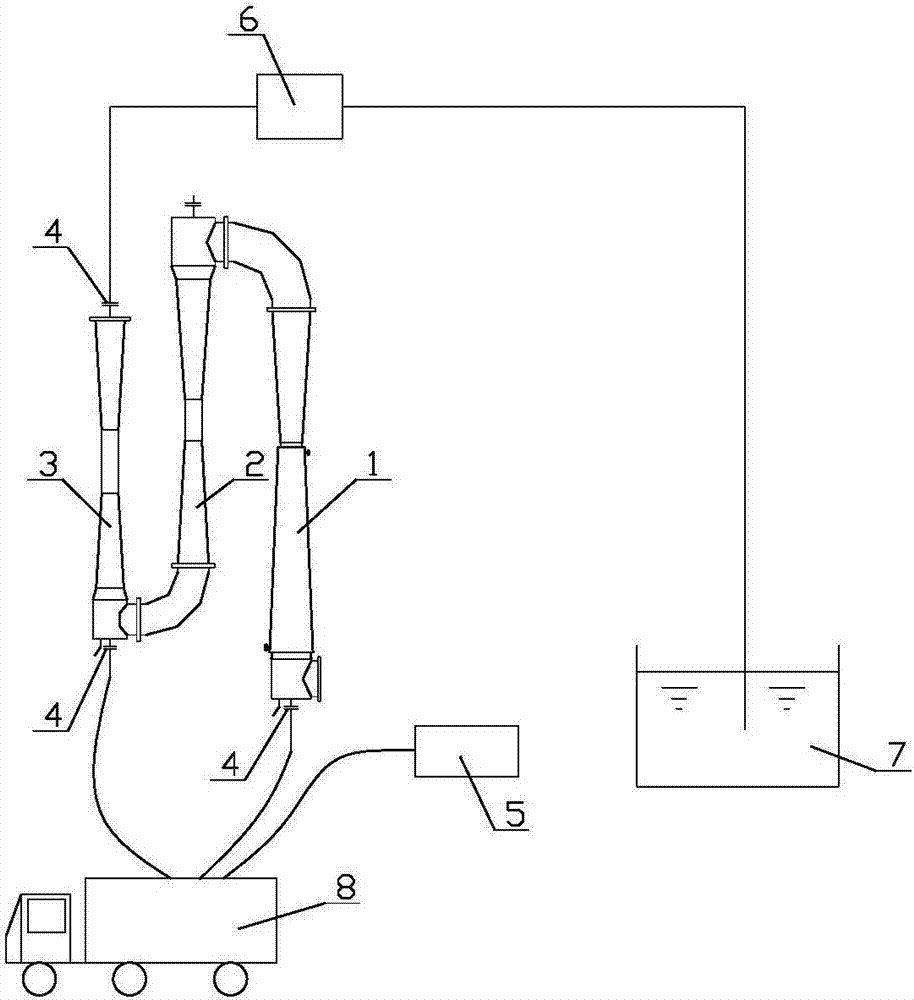
本發(fā)明涉及工業(yè)設(shè)備化學(xué)清洗
技術(shù)領(lǐng)域:
,尤其涉及一種vod/vd爐真空泵清洗方法及真空泵清洗液。
背景技術(shù):
:全蒸汽噴射泵系統(tǒng)vod/vd爐是以脫碳精煉為主,主要由氧的供給速度(強(qiáng)度)、頂吹氧槍的高度、真空度(真空泵的啟動(dòng)臺(tái)數(shù))和底吹氬流量來(lái)控制??梢跃珶捿S承鋼、合金結(jié)構(gòu)鋼、彈簧鋼、優(yōu)質(zhì)碳素鋼、超低碳不銹鋼等。由于它具有極強(qiáng)的真空脫氣能力,因此可保證鋼種的氫、氧、氮含量達(dá)到最低水平,并精確調(diào)整鋼水成分,使夾雜物充分上浮,而有效提高鋼的純潔度。由于vod/vd爐的脫碳是在真空缶中進(jìn)行的,因此vod/vd爐的管道系統(tǒng)內(nèi)必須是真空凈化狀態(tài)。而且真空泵氣體壓差轉(zhuǎn)換控制對(duì)整個(gè)冶煉過(guò)程的順利進(jìn)行和成品碳含量的控制都極其重要;但是,真空泵一、二、三級(jí)噴射器及擴(kuò)壓器的喉部管內(nèi)壁上的粉塵附著物逐漸形成的粉塵結(jié)垢層,嚴(yán)重影響了vod/vd爐運(yùn)行的可靠性、穩(wěn)定性。全蒸汽噴射泵系統(tǒng)vod/vd爐真空管道內(nèi)壁粉塵的結(jié)垢,主要形成在真空脫氣階段,從熔融鋼水表面蒸發(fā)的氣體很快被冷凝,產(chǎn)生大量的金屬和金屬氧化合物粉末,這些粉末進(jìn)入到真空系統(tǒng);此時(shí)氣壓小于100pa,在這樣低的氣壓下,氣體的密度也很低,在冶煉階段,上述低氣壓將阻止粉塵顆粒排出脫氣裝置;尤其是當(dāng)vod/vd爐除塵設(shè)備效果不佳時(shí),這些粉塵將在脫氣裝置中冷卻壁上或在前幾米連接管道上沉積;在下一爐冶煉抽真空階段,由于高密度氣體流導(dǎo)致煙塵量增加(“真空吸塵器效應(yīng)”),在脫氣過(guò)程中產(chǎn)生大量粉塵進(jìn)入真空管道內(nèi);部分粉塵粉末不能隨氣體進(jìn)入脫氣裝置或旋風(fēng)除塵器,而是附著在真空管道內(nèi)壁上或在噴射泵內(nèi)形成粉塵沉積,逐漸形成大約厚度在3-12mm粉塵附著物,如果擴(kuò)壓器內(nèi)粉塵達(dá)到一定厚度,會(huì)改變擴(kuò)壓器的軸心線,這時(shí)拉瓦爾噴嘴噴出的高速蒸汽會(huì)在擴(kuò)壓器內(nèi)部產(chǎn)生一種紊流現(xiàn)象,使泵的工作特性明顯下降,影響泵的抽氣性能;最終結(jié)果是降低了設(shè)備系統(tǒng)的工作效率,增加了冶煉生產(chǎn)過(guò)程中的運(yùn)行成本。當(dāng)鋼中的碳含量要求達(dá)到0.03%以下時(shí),在進(jìn)行真空脫碳階段,要求的終點(diǎn)碳越低,真空度或高真空度反彈幅度次數(shù)越大,脫碳時(shí)間越長(zhǎng),用氣相定碳法無(wú)法準(zhǔn)確測(cè)定到廢氣總量及其co、co2的含量,也無(wú)法計(jì)算出堿含量隨時(shí)間的降低曲線,終點(diǎn)碳標(biāo)準(zhǔn)很難實(shí)現(xiàn),同時(shí)加大了蒸汽的能耗,進(jìn)而破壞真空系統(tǒng)的穩(wěn)定性、平衡性,導(dǎo)致無(wú)法滿足生產(chǎn)的工藝要求,必須停機(jī)清理管道及噴射器內(nèi)的粉塵沉積層和結(jié)垢層。生產(chǎn)實(shí)踐證明,vod/vd爐真空泵是系統(tǒng)深脫氣、深脫碳關(guān)鍵主泵,也是粉塵結(jié)垢最嚴(yán)重的區(qū)域,真空泵內(nèi)壁形成的粉塵沉積層與粉塵結(jié)垢層,制約了vod/vd爐真空管道系統(tǒng)的使用功能,如果經(jīng)常性的清灰不但繁重且空間狹窄,不易解決且費(fèi)時(shí)費(fèi)力;因真空泵空間狹小,無(wú)法進(jìn)行人工清洗,常規(guī)方法是采用高壓水清洗、pig清管清洗:其中高壓水清洗是采用50mpa以上的高壓水射流,對(duì)管道內(nèi)表面污垢進(jìn)行高壓水射流剝離清洗。該技術(shù)主要用于短距離管道,并且管道直徑必須大于50cm以上。pig工業(yè)清管技術(shù)是依靠泵推動(dòng)流體產(chǎn)生的推動(dòng)力驅(qū)動(dòng)pig(清管器)在管內(nèi)向前推動(dòng),將堆積在管線內(nèi)的污垢排出管外,從而達(dá)到清洗的目的;但是上述方法均無(wú)法對(duì)vod/vd爐的真空泵進(jìn)行快捷徹底的清洗。申請(qǐng)?zhí)枮?01320435807.9的中國(guó)專利公開(kāi)了“一種真空泵在線清洗裝置”,申請(qǐng)?zhí)枮?01410505365.x的中國(guó)專利公開(kāi)了一種“蒸汽噴射泵內(nèi)壁清理裝置”;均采用在真空泵內(nèi)設(shè)置噴淋裝置的方法對(duì)真空泵進(jìn)行在線清洗,但是噴淋的有效覆蓋面積有限,無(wú)法對(duì)真空泵內(nèi)壁進(jìn)行全面且徹底的清洗;另外,兩者均是采用清水清洗,對(duì)于由于真空泵內(nèi)壁結(jié)垢的成分復(fù)雜、附著力強(qiáng),采用水洗方式根本無(wú)法達(dá)到有效去除真空泵內(nèi)壁結(jié)垢層的目的。技術(shù)實(shí)現(xiàn)要素:本發(fā)明提供了一種vod/vd爐真空泵清洗方法,基于對(duì)真空泵內(nèi)壁結(jié)垢層進(jìn)行化學(xué)成分分析,配制出專用真空泵清洗液;進(jìn)而采用真空泵清洗液通過(guò)化學(xué)清洗和循環(huán)清洗的方式,達(dá)到干凈徹底地清除真空泵內(nèi)壁結(jié)垢的目的;清洗后,vod/vd爐的運(yùn)行穩(wěn)定性和冶煉效率均得到大幅提高。為了達(dá)到上述目的,本發(fā)明采用以下技術(shù)方案實(shí)現(xiàn):一種vod/vd爐真空泵清洗方法,包括如下步驟:1)配制真空泵清洗液;所述真空泵清洗液由以下組分按質(zhì)量百分比組成:鹽酸35%~45%,十二烷基硫酸鈉6%~14%,六次甲基四胺2%~6%,氫氟酸1%~4%,磷酸三鈉10%~15%,氫氧化鈉20%~28%;以上組分混合均勻后配制成真空泵清洗液備用;2)將真空泵從原系統(tǒng)中隔離出來(lái);將一級(jí)真空泵的下蒸汽入口、三級(jí)真空泵的下蒸汽入口與相連的蒸汽管道斷開(kāi),將三級(jí)真空泵的上蒸汽出口與相連的冷凝器斷開(kāi),并在斷開(kāi)處的管道上分別安裝臨時(shí)閥門,臨時(shí)閥門與管道密封連接,且安裝后臨時(shí)閥門均處于關(guān)閉狀態(tài);3)組成清洗液循環(huán)系統(tǒng);將一級(jí)真空泵下蒸汽入口的臨時(shí)閥門的另一端通過(guò)管道與循環(huán)清洗泵的清洗液出口連通,循環(huán)清洗泵的清洗液入口連接清洗液容器;將三級(jí)真空泵上蒸汽出口的臨時(shí)閥門的另一端通過(guò)管道與液體過(guò)濾裝置連通,液體過(guò)濾裝置的另一端連接清洗液容器;以上連接完成后形成清洗液循環(huán)系統(tǒng);4)使用清洗液清洗;將配制好的真空泵清洗液加入清洗液容器中,打開(kāi)一級(jí)真空泵下蒸汽入口和三級(jí)真空泵上蒸汽出口的臨時(shí)閥門,使清洗液循環(huán)系統(tǒng)形成通路;啟動(dòng)循環(huán)清洗泵,通過(guò)真空泵清洗液對(duì)一級(jí)、二級(jí)、三級(jí)真空泵進(jìn)行循環(huán)清洗;真空泵清洗液與真空泵內(nèi)壁的積垢發(fā)生化學(xué)反應(yīng),積垢溶解后隨清洗液流出,經(jīng)液體過(guò)濾裝置將其中的大顆粒雜質(zhì)進(jìn)行過(guò)濾后,進(jìn)入清洗液容器內(nèi)反復(fù)使用;用真空泵清洗液清洗真空泵3-6個(gè)小時(shí)后關(guān)閉循環(huán)清洗泵;5)清洗液循環(huán)系統(tǒng)放空;關(guān)閉一級(jí)真空泵下蒸汽入口和三級(jí)真空泵上蒸汽出口的臨時(shí)閥門,將循環(huán)清洗泵的清洗液入口與清洗液容器之間的連接斷開(kāi);將循環(huán)清洗泵的清洗液出口、三級(jí)真空泵下蒸汽入口及一級(jí)真空泵下蒸汽入口的臨時(shí)閥門通過(guò)軟管連接罐車,打開(kāi)一級(jí)真空泵下蒸汽入口和三級(jí)真空泵上蒸汽出口的臨時(shí)閥門,將清洗液循環(huán)系統(tǒng)中殘余的真空泵清洗液與積垢混合物排出到罐車中外運(yùn);然后將清洗液循環(huán)系統(tǒng)重新連接;6)使用清水清洗;將循環(huán)清洗泵的清洗液入口連接清水容器,按照與步驟4)相同的方法使用清水對(duì)一級(jí)、二級(jí)和三級(jí)真空泵進(jìn)行清洗;清洗時(shí)間1-2小時(shí);然后按照與步驟5)相同的方法將清水清洗后的清洗液循環(huán)系統(tǒng)放空;7)清洗過(guò)程結(jié)束,恢復(fù)原系統(tǒng);以上過(guò)程全部結(jié)束后,將一級(jí)真空泵與循環(huán)清洗泵之間的連接斷開(kāi),將三級(jí)真空泵與液體過(guò)濾裝置之間的連接斷開(kāi);將一級(jí)真空泵的下蒸汽入口、三級(jí)真空泵的下蒸汽入口及三級(jí)真空泵的上蒸汽出口的臨時(shí)閥門取下,將一級(jí)、二級(jí)、三級(jí)真空泵重新接入原系統(tǒng)中。所述真空泵清洗液與真空泵內(nèi)壁積垢發(fā)生化學(xué)反應(yīng)并使其溶解的作用機(jī)理如下:mno2+4hcl→mncl2+cl2+2h2o;fe2o3+6hcl→2fecl3+3h2o;2kmno4+16hcl→2kcl+2mncl2+5cl2+8h2o;14hcl+k2cr2o7→3cl2+2crcl3+2kcl+7h2o;cuo+2hcl→cucl2+h2o;mgo+2hcl→mgcl2+h2o;2hcl+ca(oh)2→cacl2+2h2o;2naoh+sio2→na2sio2+h2o;hcl+naoh==nacl+h2o。所述臨時(shí)閥門為耐酸球閥。所述循環(huán)清洗泵采用聚四氟乙烯泵。與現(xiàn)有技術(shù)相比,本發(fā)明的有益效果是:1)基于對(duì)真空泵內(nèi)壁結(jié)垢層進(jìn)行化學(xué)成分分析,配制了專用的真空泵清洗液;2)采用真空泵清洗液通過(guò)化學(xué)清洗和循環(huán)清洗的方式,達(dá)到干凈徹底地清除真空泵內(nèi)壁結(jié)垢的目的;3)清洗后,vod/vd爐的運(yùn)行穩(wěn)定性和冶煉效率均得到大幅提高;4)過(guò)程簡(jiǎn)單,可操作性強(qiáng),清洗效率高。附圖說(shuō)明圖1是本發(fā)明所述vod/vd爐真空泵清洗方法的原理示意圖一(清洗過(guò)程)。圖2是本發(fā)明所述vod/vd爐真空泵清洗方法的原理示意圖二(放空過(guò)程)。圖中:1.一級(jí)真空泵2.二級(jí)真空泵3.三級(jí)真空泵4.臨時(shí)閥門5.循環(huán)清洗泵6.液體過(guò)濾裝置7.清洗液容器/清水容器8.罐車具體實(shí)施方式下面結(jié)合附圖對(duì)本發(fā)明的具體實(shí)施方式作進(jìn)一步說(shuō)明:本發(fā)明所述一種vod/vd爐真空泵清洗方法,包括如下步驟:1)配制真空泵清洗液;所述真空泵清洗液由以下組分按質(zhì)量百分比組成:鹽酸35%~45%,十二烷基硫酸鈉6%~14%,六次甲基四胺2%~6%,氫氟酸1%~4%,磷酸三鈉10%~15%,氫氧化鈉20%~28%;以上組分混合均勻后配制成真空泵清洗液備用;2)將真空泵從原系統(tǒng)中隔離出來(lái);將一級(jí)真空泵1的下蒸汽入口、三級(jí)真空泵3的下蒸汽入口與相連的蒸汽管道斷開(kāi),將三級(jí)真空泵3的上蒸汽出口與相連的冷凝器斷開(kāi),并在斷開(kāi)處的管道上分別安裝臨時(shí)閥門4,臨時(shí)閥門4與管道密封連接,且安裝后臨時(shí)閥門4均處于關(guān)閉狀態(tài);3)如圖1所示,組成清洗液循環(huán)系統(tǒng);將一級(jí)真空泵1下蒸汽入口的臨時(shí)閥門4的另一端通過(guò)管道與循環(huán)清洗泵5的清洗液出口連通,循環(huán)清洗泵5的清洗液入口連接清洗液容器7;將三級(jí)真空泵3上蒸汽出口的臨時(shí)閥門4的另一端通過(guò)管道與液體過(guò)濾裝置6連通,液體過(guò)濾裝置6的另一端連接清洗液容器7;以上連接完成后形成清洗液循環(huán)系統(tǒng);4)如圖1所示,使用清洗液清洗;將配制好的真空泵清洗液加入清洗液容器7中,打開(kāi)一級(jí)真空泵1下蒸汽入口和三級(jí)真空泵3上蒸汽出口的臨時(shí)閥門4,使清洗液循環(huán)系統(tǒng)形成通路;啟動(dòng)循環(huán)清洗泵5,通過(guò)真空泵清洗液對(duì)一級(jí)、二級(jí)、三級(jí)真空泵1、2、3進(jìn)行循環(huán)清洗;真空泵清洗液與真空泵內(nèi)壁的積垢發(fā)生化學(xué)反應(yīng),積垢溶解后隨清洗液流出,經(jīng)液體過(guò)濾裝置6將其中的大顆粒雜質(zhì)進(jìn)行過(guò)濾后,進(jìn)入清洗液容器7內(nèi)反復(fù)使用;用真空泵清洗液清洗真空泵3-6個(gè)小時(shí)后關(guān)閉循環(huán)清洗泵5;5)清洗液循環(huán)系統(tǒng)放空;如圖2所示,關(guān)閉一級(jí)真空泵1下蒸汽入口和三級(jí)真空泵3上蒸汽出口的臨時(shí)閥門4,將循環(huán)清洗泵5的清洗液入口與清洗液容器7之間的連接斷開(kāi);將循環(huán)清洗泵4的清洗液出口、三級(jí)真空泵3下蒸汽入口及一級(jí)真空泵1下蒸汽入口的臨時(shí)閥門4通過(guò)軟管連接罐車8,打開(kāi)一級(jí)真空泵1下蒸汽入口和三級(jí)真空泵3上蒸汽出口的臨時(shí)閥門4,將清洗液循環(huán)系統(tǒng)中殘余的真空泵清洗液與積垢混合物排出到罐車8中外運(yùn);然后將清洗液循環(huán)系統(tǒng)重新連接;6)使用清水清洗;如圖1所示,將循環(huán)清洗泵5的清洗液入口連接清水容器7,按照與步驟4)相同的方法使用清水對(duì)一級(jí)、二級(jí)和三級(jí)真空泵1、2、3進(jìn)行清洗;清洗時(shí)間1-2小時(shí);然后按照與步驟5)相同的方法將清水清洗后的清洗液循環(huán)系統(tǒng)放空(如圖2所示);7)清洗過(guò)程結(jié)束,恢復(fù)原系統(tǒng);以上過(guò)程全部結(jié)束后,將一級(jí)真空泵1與循環(huán)清洗泵5之間的連接斷開(kāi),將三級(jí)真空泵3與液體過(guò)濾裝置6之間的連接斷開(kāi);將一級(jí)真空泵1的下蒸汽入口、三級(jí)真空泵3的下蒸汽入口及三級(jí)真空泵3的上蒸汽出口的臨時(shí)閥門4取下,將一級(jí)、二級(jí)、三級(jí)真空泵1、2、3重新接入原系統(tǒng)中。所述真空泵清洗液與真空泵內(nèi)壁積垢發(fā)生化學(xué)反應(yīng)并使其溶解的作用機(jī)理如下:mno2+4hcl→mncl2+cl2+2h2o;fe2o3+6hcl→2fecl3+3h2o;2kmno4+16hcl→2kcl+2mncl2+5cl2+8h2o;14hcl+k2cr2o7→3cl2+2crcl3+2kcl+7h2o;cuo+2hcl→cucl2+h2o;mgo+2hcl→mgcl2+h2o;2hcl+ca(oh)2→cacl2+2h2o;2naoh+sio2→na2sio2+h2o;hcl+naoh==nacl+h2o。所述臨時(shí)閥門4為耐酸球閥。所述循環(huán)清洗泵5采用聚四氟乙烯泵。本發(fā)明為了實(shí)現(xiàn)對(duì)真空泵內(nèi)壁進(jìn)行化學(xué)清洗的目的,首先根據(jù)真空泵內(nèi)壁結(jié)垢的化學(xué)成分組成配制專用真空泵清洗液。首先在水質(zhì)條件符合gb10067.1-88《電熱設(shè)備基本條件--通用部分》的標(biāo)準(zhǔn)前提下,(如ph6-8,懸浮性固體<10mg/l,堿度<60mg/l等),對(duì)真空泵內(nèi)壁的粉塵結(jié)垢層進(jìn)行取樣和化驗(yàn)分析,結(jié)果其中含有近十種主要化學(xué)成分,這些化學(xué)成分及百分比含量如下表所示;序號(hào)名稱元素符號(hào)百分比含量1鎂mg1.2%2硅si3.3%3鉀k4.4%4鈣ga3.9%5鉻cr7.5%6錳mn36.9%7鐵fe29.5%8銅cu1.5%9鋅zn6.0%10鉛pb2.6%在此基礎(chǔ)上根據(jù)以下作用機(jī)理配制真空泵清洗液:mno2+4hcl→mncl2+cl2+2h2o;fe2o3+6hcl→2fecl3+3h2o;2kmno4+16hcl→2kcl+2mncl2+5cl2+8h2o;14hcl+k2cr2o7→3cl2+2crcl3+2kcl+7h2o;cuo+2hcl→cucl2+h2o;mgo+2hcl→mgcl2+h2o;2hcl+ca(oh)2→cacl2+2h2o;2naoh+sio2→na2sio2+h2o;hcl+naoh==nacl+h2o。因此,本發(fā)明所述真空泵清洗液能夠有效溶解并徹底清除真空泵內(nèi)壁的積垢,且不會(huì)損傷vod/vd爐裝置本體。本發(fā)明所述vod/vd爐真空泵清洗方法簡(jiǎn)單易操作,并且排出的污水經(jīng)過(guò)罐車收集凈化后ph呈中性,能夠保證進(jìn)一步處理后達(dá)到工業(yè)排放標(biāo)準(zhǔn)。以上所述,僅為本發(fā)明較佳的具體實(shí)施方式,但本發(fā)明的保護(hù)范圍并不局限于此,任何熟悉本
技術(shù)領(lǐng)域:
的技術(shù)人員在本發(fā)明揭露的技術(shù)范圍內(nèi),根據(jù)本發(fā)明的技術(shù)方案及其發(fā)明構(gòu)思加以等同替換或改變,都應(yīng)涵蓋在本發(fā)明的保護(hù)范圍之內(nèi)。當(dāng)前第1頁(yè)12