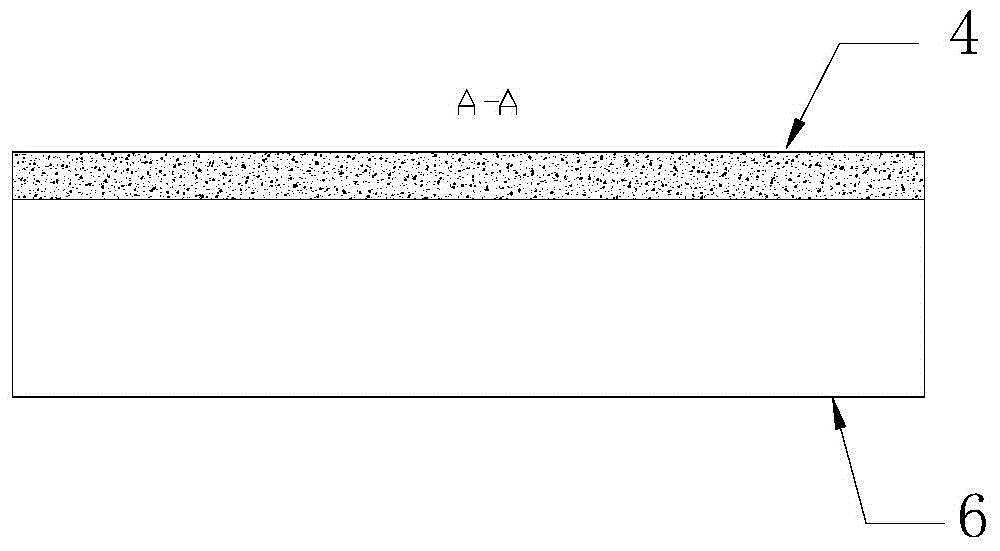
本發(fā)明涉及鋼鐵領(lǐng)域加熱爐排渣方法,具體的說是一種提高高溫加熱爐排渣效果方法。
背景技術(shù):鋼鐵企業(yè)常規(guī)鋼種熱軋步進(jìn)式加熱爐高溫加熱爐溫約為1300℃,爐內(nèi)加熱時間約為110分鐘,鋼坯爐內(nèi)加熱形成的氧化鐵皮較少,固態(tài)氧化鐵皮爐內(nèi)脫落量更少,因此,爐底氧化鐵皮爐渣堆積到影響加熱爐下部燒嘴正常燃燒的一定高度需持續(xù)較長的時間,一般為6~9個月,在加熱爐停爐小修時進(jìn)行人工清渣,恢復(fù)加熱爐的爐內(nèi)有效容積與熱工性能。而對于在加熱爐內(nèi)加熱溫溫度高、加熱時間長的部分鋼種而言,如取向硅鋼,軋前加熱要求出爐溫度高(高溫段加熱溫度1390±10℃),加熱時間長(總在爐時間≥560分鐘),鋼坯在爐內(nèi)會產(chǎn)生大量液態(tài)熔融鋼渣,熔融鋼渣在爐內(nèi)不斷積聚,特別是當(dāng)爐底鋼渣集聚到一定高度后會破壞爐體設(shè)備,迫使加熱爐無法正常運(yùn)行,嚴(yán)重影響正常生產(chǎn),因此取向硅鋼加熱爐在較短的生產(chǎn)周期(通常為20天左右)內(nèi)就必須停爐清渣,爐底積渣嚴(yán)重成為限制加熱爐硅鋼產(chǎn)能的主要環(huán)節(jié)。針對上述問題,國內(nèi)外目前主要通過設(shè)置液態(tài)出渣裝置、改變加熱爐爐體結(jié)構(gòu)與使用化渣清理裝置等技術(shù)措施以提高出渣量與清渣效率,期延長加熱爐生產(chǎn)周期。例如:公開號為CN2363184Y的中國專利,公開了一種連續(xù)加熱爐新型液態(tài)排渣裝置,由出渣口燒嘴、出渣口通道、粒化裝置及爐門密封等組成。通過改變燒嘴結(jié)構(gòu)與增加出渣通道傾斜角度等技術(shù)措施,使?fàn)t內(nèi)熔渣排出順利,不會再排渣通道內(nèi)產(chǎn)生凝固現(xiàn)象,提高了軋制周期量,減少了加熱爐故障停機(jī)次數(shù)。公開號為CN202660889U的中國專利,公開了一種液態(tài)出渣高溫取向硅鋼步進(jìn)梁式板坯加熱爐,其特征在于加熱爐第二加熱段與均熱段為5°斜坡結(jié)構(gòu),并在側(cè)墻設(shè)有液態(tài)出渣口,提高了液態(tài)出渣量,減緩了高溫段爐底鋼渣堆積速度,延長了加熱爐周期作業(yè)時間。公開號為CN102944122的中國專利,公開了一種硅鋼爐化渣清理裝置及應(yīng)用方法,具體包括鋼板、清渣桿、鎖緊螺栓和撬棍,通過清渣桿與水梁積渣接觸時的機(jī)械作用,使積渣破碎、脫落,提高了人工清渣效率。雖然上述技術(shù)在一定程度上,促進(jìn)了液態(tài)渣的排出,起到了改善生產(chǎn)過程中爐內(nèi)積渣程度的作用,但在實際生產(chǎn)過程中,由于沉積爐底的液態(tài)渣通過爐內(nèi)氣氛的進(jìn)一步氧化及其對加熱爐耐火材料的侵蝕反應(yīng),會逐步形成熔點高、成分復(fù)雜的爐渣,導(dǎo)致爐渣粘度不斷提高,液態(tài)出渣量遠(yuǎn)低于40%的設(shè)計水平,高溫取向硅鋼實際周期加熱量也低于設(shè)計水平。因而,提高熔渣流動性是提高周期加熱量的重要研究方向。
技術(shù)實現(xiàn)要素:本發(fā)明的目的是為了解決上述技術(shù)問題,提供一種工藝簡單、有效提高排渣效果,降低爐渣沉積的高溫加熱爐排渣方法。本發(fā)明提高高溫加熱爐排渣效果方法為,高溫加熱爐停爐清渣后,在高溫加熱爐的第二加熱段爐底表面鋪設(shè)石英砂,鋪設(shè)完后再啟動高溫加熱爐進(jìn)行加熱生產(chǎn)。高溫加熱爐停爐清渣后,同時在高溫加熱爐的均段爐底表面鋪設(shè)石英砂。所述石英砂的鋪設(shè)厚度為50-100mm。所述石英砂粒度為0.5-3mm,石英砂中SiO2含量≥98wt%。本發(fā)明方法適用于需要在高溫加熱爐內(nèi)進(jìn)行高溫(操作溫度為1350℃以上)、長時間(操作時間即總在爐時間≥400分鐘)加熱的鋼種,如高溫取向硅鋼等,這類鋼種的鋼坯在進(jìn)入加熱爐后由于工藝要求,需要在爐內(nèi)進(jìn)行高溫長時間加熱,因而存在背景技術(shù)中所述問題。針對上述問題,發(fā)明人改變了過去對加熱爐或排渣裝置進(jìn)行結(jié)構(gòu)改進(jìn)的固有思維,通過對高溫加熱爐爐渣進(jìn)行深入研究及取樣分析與檢測,探明了高溫加熱爐爐渣的形成機(jī)理,以硅鋼為例,由于硅鋼中含有約4%的Si,在加熱過程中,板坯表面的Fe、Si元素氧化后便形成以鐵撖欖石(2FeO·SiO2)為主要成分的氧化鐵渣;而FeO-2FeO·SiO2的共晶溫度是1177℃,在1200℃左右就有液相產(chǎn)生,到1340℃左右會完全轉(zhuǎn)變?yōu)橐合?。因此,在長時間高溫(1390±10℃)加熱過程中,板坯表面形成以鐵橄欖石和方鐵石(FeO)為主的熔融渣并不斷下淌,隨著在爐時間的不斷增加,熔融渣中富余的FeO和鐵橄欖石中的FeO繼續(xù)氧化生成Fe3O4、Fe2O3,熔渣流動性變差。最后,少量熔融渣通過液態(tài)排渣系統(tǒng)排出,大部分沉積于爐底,而隨著氧化的繼續(xù)進(jìn)行,導(dǎo)致爐渣物相最終轉(zhuǎn)化為Fe3O4與Fe2O3。本發(fā)明通過在加熱爐二段和均熱段均勻鋪設(shè)石英砂,使流淌至爐底的液態(tài)熔融渣中的FeO與石英砂中SiO2發(fā)生反應(yīng)(反應(yīng)溫度1177℃),生成低熔點化合物硅酸亞鐵Fe2SiO4(熔點1205℃),從而大幅度降低爐渣熔點,改善爐底液態(tài)渣的流動性,促進(jìn)其從液態(tài)排渣口排出。試驗結(jié)果表明,采取本發(fā)明后,相同條件下爐底平均積渣厚度降低20%以上。對于石英砂的鋪設(shè),優(yōu)選石英砂的鋪設(shè)厚度為50-100mm,不可過薄,過薄會導(dǎo)致參加反應(yīng)的SiO2數(shù)量不夠,影響Fe2SiO4的生成量,降低排渣效果;也不可過厚,雖然石英砂鋪設(shè)具有一定的厚度可以延長軋制周期,但過厚也會導(dǎo)致反應(yīng)后石英砂數(shù)量富余,影響生產(chǎn)成本的降低和增加清渣過程中的勞動強(qiáng)度。進(jìn)一步的,優(yōu)選石英砂粒度為0.5-3mm,石英砂的粒度過大會導(dǎo)致比表面積降低,影響石英砂與熔融渣的反應(yīng)效果,過小會導(dǎo)致熔融渣滴落過程中石英砂粉的飛揚(yáng),進(jìn)而與鋼坯接觸反應(yīng),影響鋼坯質(zhì)量。有益效果:本發(fā)明工藝簡單、構(gòu)思巧妙,通過在高溫加熱爐內(nèi)鋼坯停留時間最長、加熱溫度最高的部分爐底鋪設(shè)石英砂,使熔渣中的鐵離子與石英砂中的SiO2反應(yīng)生成低融點物質(zhì),以降低爐渣的熔點,從而改善液態(tài)融渣的流動性,提高高溫加熱爐的排渣效果,進(jìn)而可延長加熱爐生產(chǎn)周期,提高鋼坯周期軋制產(chǎn)量,降低工人清渣勞動強(qiáng)度。附圖說明圖1為高溫加熱爐鋪設(shè)石英砂的狀態(tài)俯視圖。圖2為圖1中爐底的A-A剖示圖。圖3為爐底積渣與爐底耐火材料結(jié)合界面微觀結(jié)構(gòu)的掃描電鏡分析圖。其中,1-高溫加熱爐、2-第二加熱段、3-均熱段、4-石英砂層、5-出渣口、6-爐底。具體實施方式下面以高溫取向硅鋼送入高溫加熱爐內(nèi)進(jìn)行高溫加熱的工藝為例對本發(fā)明提高排效效果的方法進(jìn)行描述。所述高溫加熱爐為現(xiàn)有的步進(jìn)式加熱爐。實施例1:1):在高溫加熱爐1爐底停爐清渣和耐材修補(bǔ)完畢后,將爐底清掃干凈;2):在高溫加熱爐1的第二加熱段2和均熱段3的爐底6表面均勻鋪設(shè)石英砂層4(見圖1及圖2);石英砂鋪設(shè)厚度為50mm,石英砂粒度為0.5mm,石英砂SiO2含量為99%(質(zhì)量百分比)。3):鋪設(shè)完石英砂層后再啟動高溫加熱爐1,按照現(xiàn)有的高溫取向硅鋼鋼坯爐內(nèi)加熱溫度制度要求控制各段的爐溫進(jìn)行高溫取向硅鋼鋼坯的正常加熱生產(chǎn),其中,加熱爐第二加熱段和均熱段爐溫為1380~1400℃,鋼坯在爐內(nèi)的總停留時間為600-800min。5):開啟出渣口燒嘴,保證出渣口通道高溫狀態(tài),防止流經(jīng)出渣口5通道的液態(tài)渣冷卻凝固粘接,堵塞通道。6)當(dāng)加熱爐完成一個生產(chǎn)周期后,再次進(jìn)行停爐清渣,再按照上述步驟1)-4)的順序進(jìn)行石英砂的鋪設(shè)。實施例2:第二步中石英砂鋪設(shè)厚度為100mm,石英砂粒度為1-3mm,石英砂SiO2含量為98%。其他步驟與實施例1中相同。實施例3:第二步中石英砂鋪設(shè)厚度為75mm,石英砂粒度為2-3mm,石英砂SiO2含量為99%。其他步驟與實施例1中相同實施例4:第二步中石英砂鋪設(shè)厚度為60mm,石英砂粒度為0.5-1mm,石英砂SiO2含量為98%。其他步驟與實施例1中相同。比較例:除在停爐清渣后不鋪設(shè)石英砂層外,其余同實施例1。一個軋制周期后,采用實施例技術(shù)措施后,相比比較例,試驗區(qū)域爐底積渣狀況明顯改善,爐底積渣平均厚度下降幅度達(dá)26%,爐內(nèi)清渣量減少約30%,顯著提高了液態(tài)渣排出比例。同時,由于底部液態(tài)渣流動性增強(qiáng),加熱爐關(guān)鍵耐火構(gòu)件(如土圍等)粘渣狀況也有所改善;延長了加熱爐單個周期生產(chǎn)時間(軋制周期可延長5%),硅鋼周期軋制量也可提高約5%;同時,也減少了加熱爐維修次數(shù),節(jié)約了耐火材料消耗和成本,減輕了工人勞動強(qiáng)度。進(jìn)一步地,參見圖3,對實施例1中的爐底積渣與爐底耐火材料結(jié)合界面微觀結(jié)構(gòu),進(jìn)行了掃描電鏡分析。結(jié)果表明,爐底積渣與爐底耐火材料之間界限清晰,能譜分析結(jié)果(見表1及表2)表明石英砂與爐渣反應(yīng)生成大量流動性較好的Fe2SiO4,進(jìn)一步驗證了試驗效果和機(jī)理。