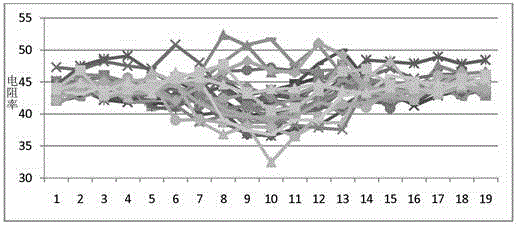
本發(fā)明創(chuàng)造區(qū)熔單晶硅生長技術(shù)領(lǐng)域,具體涉及單晶硅區(qū)熔爐中一種摻雜氣路。
背景技術(shù):區(qū)熔硅單晶制備過程中,摻入一定量的電活性雜質(zhì)可將高純度多晶硅原料制成具有一定電學(xué)性質(zhì)的摻雜硅單晶。目前,區(qū)熔硅單晶的摻雜方法有多晶沉積法、硅芯摻雜法、溶液涂敷摻雜法、棒孔摻雜法、中子嬗變摻雜法(NTD)和氣相摻雜法等。其中,中子嬗變摻雜法,即NTD單晶的電阻率軸向及徑向均勻性是最好的,同時加工周期長,價格也十分昂貴。故而,各大廠家考慮到成本問題便轉(zhuǎn)向低成本、電阻率均勻性較低的氣相摻雜法制備的硅單晶,以至于目前全球各類區(qū)熔硅單晶總量的80%為氣相摻雜單晶。由于單晶硅材料的電學(xué)性質(zhì)幾乎對所有雜質(zhì)都非常敏感,且單晶硅生長過程對軸向和平面內(nèi)的摻雜均勻性都提出了嚴格的要求,因此摻雜過程中對摻雜工藝的控制是非常重要的,對摻雜工藝的控制也是本領(lǐng)域技術(shù)人員不斷研究和改善的課題。申請人已經(jīng)對區(qū)熔硅單晶氣相摻雜生長工藝進行了大量的研究,設(shè)計出了一整套合理的氣相摻雜生長工藝,其中包括公開號為CN1455028、CN1763266、CN1865530、CN1865531、CN103114325A、CN103114326A的專利申請,在此并入作為參考。但是在上述研究中未涉及到摻雜氣路對摻雜工藝影響的研究。摻雜氣路用于將確定流量的保護氣及摻雜氣經(jīng)混合后輸送入?yún)^(qū)熔爐中,普通的氣路管道結(jié)構(gòu)如圖1所示,類似“工”字型,摻雜氣路的混合部分一般位于區(qū)熔爐內(nèi)一個固定的空間,空間的大小受到限制,一般在80cm×95cm以內(nèi),因此氣體往往未經(jīng)混合均勻便直接輸送至區(qū)熔爐內(nèi),導(dǎo)致區(qū)熔爐內(nèi)摻雜氣分布不均,生產(chǎn)出的氣摻單晶硅軸向均勻性不佳,氣摻單晶均勻性的重復(fù)性也并不理想。
技術(shù)實現(xiàn)要素:本發(fā)明創(chuàng)造為解決上述問題,提供一種區(qū)熔氣摻單晶的摻雜氣路,能夠在區(qū)熔爐有限的空間內(nèi)使摻雜氣與保護氣在入爐前充分均勻混合,改善氣摻單晶均勻性、提高摻雜效率。為解決上述技術(shù)問題,本發(fā)明創(chuàng)造采用的技術(shù)方案是,將摻雜氣路管道結(jié)構(gòu)改造為類似“π”字型,所述“π”字型摻雜氣路中間為一段足夠長的L段管道,所述L段管道的一端連通保護氣進氣口、摻雜氣進氣口,另一端連通出氣口及排氣口,所述出氣口進入爐膛內(nèi)部,所述保護氣進氣口、摻雜氣進氣口及出氣口均設(shè)有流量計,所述排氣口設(shè)有壓力閥。其中,所述壓力閥能夠保證進入爐膛的氣體具有穩(wěn)定的濃度和壓力,且“π”字型彎道的設(shè)置也能夠保證入爐氣體流動的穩(wěn)定性,不會引起入爐氣體的擾動。其中,所述保護氣一般為氬氣,所述摻雜氣可以為磷烷(PH3)、硼烷(B2H6)中的一種或多種。優(yōu)選的,所述摻雜氣進氣口位于所述保護氣進氣口上方,所述出氣口位于所述排氣口上方。由于保護氣體的流量一般較大,保護氣體在管道中由下方涌入上方并與位于上方管道中的摻雜氣混合時,具有較大的沖量作用而在管道內(nèi)產(chǎn)生湍流,從而加強混合效果。進一步,所述L段管道的長度為35-50cm,優(yōu)選為40-45cm。進一步,所述“π”字型摻雜氣路的管道內(nèi)徑為0.3-0.6cm,優(yōu)選為0.4-0.6cm。進一步,所述保護氣進氣口的流量范圍控制在0-30L/min,所述摻雜氣進氣口的流量范圍控制在0-1L/min,所述出氣口的流量范圍控制在0-200ml/min,所述排氣口壓力的調(diào)節(jié)范圍控制在0-20bar。優(yōu)選的,所述保護氣進氣口的流量范圍控制在0-10L/min,所述摻雜氣進氣口的流量范圍控制在0-0.5L/min,所述出氣口的流量范圍控制在0-100ml/min,所述排氣口壓力的調(diào)節(jié)范圍控制在0-10bar。本發(fā)明創(chuàng)造具有的優(yōu)點和積極效果是:能夠在有限的空間內(nèi)改善氣路中摻雜氣體的混合效果,一方面可以使得氣摻單晶的軸向綜合均勻性提高1.5以上個百分點,甚至可以達到接近于NTD電阻率均勻性的效果;另一方面可以提高摻雜效率,使摻雜氣的使用量節(jié)省5%以上,降低生產(chǎn)成本;同時,通過精確控制摻雜氣體的流量,氣摻單晶均勻性的重復(fù)性也有顯著的提高。附圖說明圖1是普通的區(qū)熔氣摻單晶的摻雜氣路結(jié)構(gòu)示意圖。圖2是本發(fā)明創(chuàng)造一種區(qū)熔氣摻單晶的摻雜氣路的一種優(yōu)選實施方案。圖3是實施例1生產(chǎn)的單晶產(chǎn)品軸向電阻率的測試結(jié)果。圖4是對比例1生產(chǎn)的單晶產(chǎn)品軸向電阻率的測試結(jié)果。其中,1-摻雜氣進氣口;2-保護氣進氣口;3-出氣口;4-排氣口;5-壓力閥;6-L段管道。具體實施方式下面結(jié)合附圖對本發(fā)明創(chuàng)造進行進一步說明。常見的區(qū)熔氣摻單晶的摻雜氣路位于區(qū)熔爐限定空間內(nèi)的部分結(jié)構(gòu)如圖1所示,摻雜氣與保護氣分別通過摻雜氣進氣口(1)和保護氣進氣口(2)進入管道,然后很快經(jīng)由出氣口(3)進入爐膛內(nèi)部,排氣口(4)直接與保護氣進氣口(2)連通,雖然起到了控制爐膛氣壓的作用,但是對混合氣體的精確比例控制造成擾動。本發(fā)明創(chuàng)造一種區(qū)熔氣摻單晶的摻雜氣路的一種優(yōu)選實施方案如圖2所示。摻雜氣與保護氣分別通過摻雜氣進氣口(1)和保護氣進氣口(2)進入管道,經(jīng)過足夠長的L段管道(6)的充分混合,混合氣體由出氣口(3)進入爐膛內(nèi)部;排氣口(4)內(nèi)設(shè)置有壓力閥(5),當爐膛內(nèi)壓力超過臨界值時,壓力閥(5)開啟,多余的混合氣體經(jīng)排氣口(4)排出,實現(xiàn)對爐膛內(nèi)氣體壓力的控制;所述摻雜氣進氣口(1)、保護氣進氣口(2)和出氣口(3)均設(shè)有流量計(圖中未示出),能夠?qū)崿F(xiàn)對氣體流量的精確控制;所述摻雜氣路的管道內(nèi)徑為0.6cm,所述L段管道(6)的長度為40cm。為了進一步說明本發(fā)明創(chuàng)造的效果,對量產(chǎn)中區(qū)熔爐摻雜氣路改造前后的單晶產(chǎn)品進行了生產(chǎn)和檢測。為敘述方便,下述實施例和對比例中,未提及的生產(chǎn)條件和參數(shù)采用一般條件或安全生產(chǎn)規(guī)定的生產(chǎn)條件和參數(shù)。實施例1使用如圖2所示摻雜氣路,拉制4英寸氣摻單晶,生產(chǎn)目標電阻率在30-45Ω·cm的氣摻單晶。正常生產(chǎn)過程中,Ar氣流量控制為2L/min;摻雜氣(磷烷)的流量為260ml/min;混合氣入爐的流量為100ml/min;多余的氣體通過排氣口排出氣路,排氣口控制壓力為3bar。通過對氣路壓力的實施監(jiān)控,保證了入爐氣體的壓力。對比例1:使用如圖1所示普通的摻雜氣路,其他條件同實施例1。實施例2使用如圖2所示摻雜氣路,拉制4英寸氣摻單晶,生產(chǎn)目標電阻率在2000±30%Ω·cm的氣摻單晶。正常生產(chǎn)過程中,Ar氣流量控制為2.5L/min;摻雜氣(磷烷)的流量為20ml/min;混合氣入爐的流量為100ml/min;多余的氣體通過排氣口排出氣路,排氣口控制壓力為3bar。通過對氣路壓力的實施監(jiān)控,保證了入爐氣體的壓力。對比例2:使用如圖1所示普通的摻雜氣路,其他條件同實施例2。為對摻雜氣路改造前后單晶產(chǎn)品徑向電阻率均勻性和穩(wěn)定性進行評價,對兩臺區(qū)熔爐氣路改造前后分別進行了為期一個月的相同種類和批次的氣摻單晶的生產(chǎn),其中一臺區(qū)熔爐氣路改造前后分別對應(yīng)對比例1和實施例1的生產(chǎn)條件,另一臺區(qū)熔爐氣路改造前后分別對應(yīng)對比例2和實施例2的生產(chǎn)條件,獲得的單晶產(chǎn)品電阻率綜合結(jié)果如表1所示。表1其中,RRV為徑向電阻率不均勻度,表示一個面向內(nèi)電阻率的差值與最大值的比例;值越小,表示電阻率差值越小,電阻率的一致性越好。計算公式:RRV=[(電阻率最大值/電阻率最小值)-1]*100%]使用四探針CRES-Box對實施例1和對比例1單晶產(chǎn)品的電阻率進行徑向一條直徑19點的測試,測試結(jié)果如圖3和圖4所示,使用本發(fā)明創(chuàng)造的“π”字型摻雜氣路使單晶產(chǎn)品的軸向均勻性得到提高。另外,為評價摻雜氣路的摻雜氣利用率,對同一臺區(qū)熔爐氣路改造前后分別進行了為期10天的摻雜氣氣體用量記錄,記錄期間內(nèi)區(qū)熔爐采用相同的生產(chǎn)條件生產(chǎn)相同種類和批次的單晶產(chǎn)品,摻雜氣使用情況如表2所示,可以看出的摻雜氣路節(jié)省了摻雜氣使用量,摻雜氣利用效率得到提升。表2