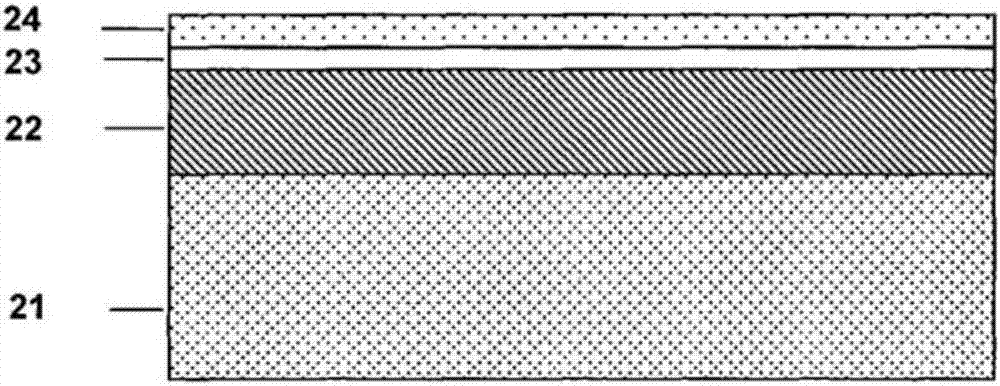
本發(fā)明涉及用于制備由涂覆有基于鋁的涂層和鋅涂層的板制造的經(jīng)壓制硬化的鋼部件的方法。所述部件具有關(guān)于磷酸鹽化的良好特性,并因此表現(xiàn)出良好的漆粘附性。特別地旨在用于制造機(jī)動(dòng)車部件。經(jīng)壓制硬化的部件可以涂覆有具有良好的抗腐蝕性和良好的熱性質(zhì)的基于鋁的合金。通常,用于制備這些部件的方法包括:獲得鋼板,切割該板以獲得坯件,加熱該坯件,壓制硬化隨后冷卻以獲得馬氏體或馬氏體-貝氏體轉(zhuǎn)變硬化,使得鋼的組織包含至少75%的等軸鐵、量大于或等于5%并且小于或等于20%的馬氏體、量小于或等于10%的貝氏體。由此獲得的經(jīng)硬化的部件具有非常良好的機(jī)械特性。通常,向經(jīng)壓制硬化的部件添加漆膜,特別是電泳層。通常預(yù)先進(jìn)行磷酸鹽化。用這種方式,磷酸鹽晶體形成在待涂覆的經(jīng)硬化的部件的表面上,增強(qiáng)了漆的粘附性,并且尤其是,電泳層的粘附性。涂覆有基于鋁的合金的部件不是可磷酸鹽化的,即,沒有磷酸鹽晶體形成在涂層的表面上。因此在沒有在前的磷酸鹽化的情況下直接進(jìn)行漆膜的添加。涂覆有基于鋁的合金的部件的表面的微粗糙度使漆粘附成為可能。然而,在一些情況下,漆不是均勻地分布在部件的表面上的,導(dǎo)致紅銹區(qū)域。紅銹出現(xiàn)在漆深深嵌入基于鋁的涂層的區(qū)域中。專利申請(qǐng)ep2270257是已知的。其公開了包括第一基于鋁的涂層和具有纖鋅礦結(jié)構(gòu)(化合物優(yōu)選為氧化鋅(zno))的第二涂層的用于壓制硬化的鋼板。zno涂層使得能夠在壓制硬化方法之后進(jìn)行磷酸鹽化。然而,實(shí)際上,該方法的實(shí)施導(dǎo)致在部件的表面上相對(duì)低的磷酸鹽晶體覆蓋的程度,約20%至70%。此覆蓋程度是不可接受的,原因在于其不能在部件的表面上實(shí)現(xiàn)良好的漆粘附性。本發(fā)明的目的是通過由經(jīng)涂覆的鋼板提供可磷酸鹽化的經(jīng)壓制硬化的部件(其因此表現(xiàn)出良好的漆粘附性)來彌補(bǔ)現(xiàn)有技術(shù)的缺點(diǎn)。特別地,本發(fā)明旨在提供能夠被磷酸鹽化的經(jīng)壓制硬化的部件以便在部件的表面上獲得高的磷酸鹽晶體覆蓋的程度,特別地覆蓋的程度大于或等于80%。本發(fā)明還涉及用于制備所述鋼板的方法。本發(fā)明還涉及用于在有利生產(chǎn)率條件下制造可磷酸鹽化的經(jīng)壓制硬化的部件的方法。本發(fā)明還涉及經(jīng)壓制硬化的部件用于制造機(jī)動(dòng)車部件的用途。為此,本發(fā)明的目的為根據(jù)權(quán)利要求1所述的鋼板。所述鋼板還可以包括權(quán)利要求2至9的特征。本發(fā)明的目的還為根據(jù)權(quán)利要求10所述的用于制備經(jīng)涂覆的鋼板的方法。該制備方法還可以包括權(quán)利要求11至13的特征。本發(fā)明的目的還為根據(jù)權(quán)利要求14所述的用于制備經(jīng)壓制硬化的部件的方法。該制備方法還可以包括權(quán)利要求15至16的特征。本發(fā)明的目的還為根據(jù)權(quán)利要求17所述的經(jīng)壓制硬化的部件。這個(gè)部件還可以包括權(quán)利要求18至20的特征。最后,本發(fā)明的目的是根據(jù)權(quán)利要求21所述的經(jīng)壓制硬化的部件的用途。當(dāng)閱讀以下的描述時(shí),本發(fā)明的另外的特征和優(yōu)點(diǎn)將變得明顯。為了舉例說明本發(fā)明,多種實(shí)施方案和測(cè)試將通過非限制性實(shí)例,特別地參照附圖來描述,附圖示出:圖1是根據(jù)本發(fā)明的一個(gè)實(shí)施方案的經(jīng)涂覆的鋼板的示意圖。圖2是根據(jù)本發(fā)明的另一個(gè)實(shí)施方案的經(jīng)涂覆的鋼板的示意圖。對(duì)于圖1和圖2,提供所示出的層的厚度僅僅是出于舉例說明的目的且不應(yīng)被認(rèn)為是多個(gè)層的真實(shí)比例表示。圖3和圖4示出了由提供有厚度為25μm的第一基于鋁的涂層和在一側(cè)上通過電鍍沉積的厚度為1μm、2μm和3μm的第二鋅涂層的鋼板制造的經(jīng)硬化的部件的兩側(cè)的實(shí)際尺寸。圖5示出了對(duì)于標(biāo)準(zhǔn)vda231-102的腐蝕循環(huán)。以下術(shù)語(yǔ)限定如下:-“鋅涂層”意指主要包含鋅和可能的雜質(zhì)的涂層。優(yōu)選地,該涂層包含鋅和可能地雜質(zhì)。-“基于鋁的涂層”意指包含如下按重量計(jì)組成的涂層:鋁的量大于50%,優(yōu)選地大于或等于70%,更優(yōu)選地大于或等于85%,有利地大于或等于88%。該涂層可為合金的或非合金的。-“磷酸鹽晶體覆蓋的程度”通過百分比來限定。0%意指部件的表面完全沒有被磷酸鹽晶體覆蓋,100%意指部件的表面完全被覆蓋。對(duì)于全部的圖1至圖5和本發(fā)明的后續(xù)內(nèi)容,名稱“鋼”或“鋼板”是指具有能夠使部件實(shí)現(xiàn)大于或等于500mpa,優(yōu)選地大于或等于1000mpa,有利地大于或等于1500mpa的拉伸強(qiáng)度的組成的用于壓制硬化的鋼板。鋼板的重量組成優(yōu)選地如下:0.03%≤c≤0.50%;0.3%≤mn≤3.0%;0.05%≤si≤0.8%;0.015%≤ti≤0.2%;0.005%≤al≤0.1%;0%≤cr≤2.50%;0%≤s≤0.05%;0%≤p≤0.1%;0%≤b≤0.010%;0%≤ni≤2.5%;0%≤mo≤0.7%;0%≤nb≤0.15%;0%≤n≤0.015%;0%≤cu≤0.15%;0%≤ca≤0.01%;0%≤w≤0.35%,組成的余量包含鐵和由工藝產(chǎn)生的不可避免的雜質(zhì)。例如,鋼板是具有如下重量組成的22mnb5板:0.20%≤c≤0.25%0.15%≤si≤0.35%1.10%≤mn≤1.40%0%≤cr≤0.30%0%≤mo≤0.35%0%≤p≤0.025%0%≤s≤0.005%0.020%≤ti≤0.060%0.020%≤al≤0.060%0.002%≤b≤0.004%,組成的余量為鐵和由工藝產(chǎn)生的不可避免的雜質(zhì)。鋼板還可以是具有如下重量組成的2000板:0.24%≤c≤0.38%0.40%≤mn≤3%0.10%≤si≤0.70%0.015%≤al≤0.070%0%≤cr≤2%0.25%≤ni≤2%0.020%≤ti≤0.10%0%≤nb≤0.060%0.0005%≤b≤0.0040%0.003%≤n≤0.010%0.0001%≤s≤0.005%0.0001%≤p≤0.025%應(yīng)理解,鈦和氮的含量滿足:ti/n>3.42,并且碳、錳、鉻和硅的含量滿足:組成任選地包含以下元素中的一種或更多種:0.05%≤mo≤0.65%0.001%≤w≤0.30%0.0005%≤ca≤0.005%,組成的余量為鐵和由工藝產(chǎn)生的不可避免的雜質(zhì)。在另一個(gè)實(shí)例中,鋼板是具有如下重量組成的500板:0.040%≤c≤0.100%0.80%≤mn≤2.00%0%≤si≤0.30%0%≤s≤0.005%0%≤p≤0.030%0.010%≤al≤0.070%0.015%≤nb≤0.100%0.030%≤ti≤0.080%0%≤n≤0.009%0%≤cu≤0.100%0%≤ni≤0.100%0%≤cr≤0.100%0%≤mo≤0.100%0%≤ca≤0.006%,組成的余量為鐵和由工藝產(chǎn)生的不可避免的雜質(zhì)。根據(jù)期望的厚度,鋼板通過熱軋并且可以任選地冷軋來生產(chǎn)。應(yīng)理解,首先,本發(fā)明涉及經(jīng)涂覆的鋼板。圖1示出了根據(jù)本發(fā)明的板1的一個(gè)實(shí)施方案。其提供有基于鋁的涂層2還包括厚度小于或等于1.1μm,優(yōu)選地小于或等于1.0μm,更優(yōu)選地小于或等于0.7μm并且優(yōu)先地小于或等于0.5μm的第二鋅涂層3。有利地,鋅涂層的厚度大于或等于0.1μm。在不受理論限制的情況下,顯示出,如果不滿足這些厚度條件,尤其是如果鋅厚度太高,則在熱處理期間不是全部鋅被氧化成氧化鋅(zno)。事實(shí)上,爐中存在的氧將花費(fèi)過長(zhǎng)時(shí)間擴(kuò)散到鋅涂層中而不能使其完全氧化。因此,一些鋅將在液體狀態(tài)保持太長(zhǎng)的時(shí)間,并且仍然為液體的鋅將擴(kuò)散到基于鋁的涂層中并且然后進(jìn)入鋼中。已經(jīng)深深擴(kuò)散到基底中的鋅可以引起上層(即,基于鋁的涂層和電泳層)的脆性和粘附性的損失。此外,如果不滿足厚度條件,則表面的微粗糙度將隨著鋅涂層厚度的增加而增加也是可能的,因此促進(jìn)電泳層的沉積之后的紅銹區(qū)域。因此,在大多數(shù)情況下,如果磷酸鹽晶體覆蓋的程度低,則存在電泳層的粘附性差的風(fēng)險(xiǎn)。然而,在一些情況下,即使磷酸鹽晶體覆蓋的程度高,也存在電泳層的粘附性損失和在此電泳層下的耐紅銹性差的風(fēng)險(xiǎn)。最后,存在在液體狀態(tài)下保持太長(zhǎng)時(shí)間的鋅將污染其中發(fā)生熱處理的爐的風(fēng)險(xiǎn)?;阡X的涂層優(yōu)選地通過在熔融金屬浴中的熱浸鍍來進(jìn)行。通常,所述浴包含最高至3%的鐵和9%至12%的硅,余量為鋁。層的厚度為例如5μm至50μm,優(yōu)選地10μm至35μm。在熱變形之前的熱處理期間,涂層形成表現(xiàn)出高耐腐蝕性、耐磨損性、耐磨耗性、耐疲勞性的合金層。優(yōu)選地,基于鋁的涂層的厚度和鋅涂層的厚度的乘積為2至25,優(yōu)選地4至25,更優(yōu)選地4至16,并且有利地6至13;鋅涂層的厚度小于或等于1.1μm,優(yōu)選地小于或等于1.0μm,更優(yōu)選地小于或等于0.7μm并且優(yōu)先地小于或等于0.5μm。在不受理論限制的情況下,可能的是,如果不滿足這些條件,尤其如果基于鋁的涂層的厚度太大,則基于鋁的涂層將在液相中保持太長(zhǎng)時(shí)間。因此,在熱處理開始時(shí)形成的zno層和基于鋁的涂層將在長(zhǎng)時(shí)間段內(nèi)相互作用。這種相互作用可以導(dǎo)致zno層被鋁還原成zn,該過程受緩慢的動(dòng)力學(xué)支配。鋅涂層3可通過任何適當(dāng)?shù)姆椒ǔ练e,例如通過置換沉淀(cementation)、通過電鍍或通過在真空下的聲速射流氣相沉積(sonicjetvapordeposition)(jvd)。根據(jù)一個(gè)實(shí)施方案,鋅涂層通過電鍍例如通過浸入硫酸鋅(znso4)浴中來沉積。有利地,浴的溫度t3低于70℃,t3優(yōu)選地在50℃至60℃的范圍。根據(jù)另一個(gè)實(shí)施方案,鋅涂層通過置換沉淀來沉積。當(dāng)鋅涂層通過置換沉淀來沉積時(shí),其通過噴涂或通過浸漬來進(jìn)行。因此,將涂覆有基于鋁的金屬涂層的鋼板浸入浴中或用氫氧化鈉(naoh)和氧化鋅(zno)的溶液噴涂。有利地,浸漬或噴涂進(jìn)行1秒至20秒的時(shí)間t4,t4優(yōu)選地在5秒至10秒的范圍。浸漬或噴涂在40℃至60℃的溫度t4下進(jìn)行,t4優(yōu)選為60℃。在不受具體理論限制的情況下,naoh和zno混合物根據(jù)以下反應(yīng)能夠形成鋅酸鈉(na2zno2):2naoh+zno→na2zno2+h2o。此后,根據(jù)以下反應(yīng),na2zno2將與存在于基于鋁的涂層中的鋁反應(yīng)以在涂覆有基于鋁的涂層的鋼板上形成鋅涂層:2al+3na2zno2+2h2o→3zn+2naalo2+4naoh。根據(jù)另一個(gè)實(shí)施方案,鋅涂層通過在真空下的聲速射流氣相沉積來沉積。根據(jù)該實(shí)施方案,鋅金屬蒸氣通過在優(yōu)選地6×10-2毫巴至2×10-1毫巴的壓力p5下的真空室中包含在至少600℃的溫度t5下加熱的鋅浴的坩堝的感應(yīng)加熱而產(chǎn)生,t5優(yōu)選為700℃。蒸氣經(jīng)由通向出口孔口的導(dǎo)管從坩堝中逸出(優(yōu)選地被校準(zhǔn)),以形成朝向待涂覆的基底的表面的聲速射流。有利地,在通過jvd進(jìn)行鋅沉積之前,提供有基于鋁的涂層的鋼板涂覆有包含以下按重量計(jì)組成的不銹鋼薄層:至少10%的鉻,余量為鐵,另外的元素,例如鎳、碳、鉬、硅、錳、磷或硫,以及與制造工藝相關(guān)的雜質(zhì)。優(yōu)選地,不銹鋼層包含至少10%的鉻,至少8%的鎳,余量為鐵,如前所述的另外的元素和與制造工藝相關(guān)的雜質(zhì)。該層優(yōu)選地為按重量計(jì)包含如下的不銹鋼316:16%≤cr≤18%和10%≤ni≤14%。例如,該層為不銹鋼316l,其重量組成如下:c=0.02%;16%≤cr≤18%;10.5%≤ni≤13%;2%≤mo≤2.5%,si=1%;mn=2%;p=0.04%和s=0.03%。層的厚度可以例如大于或等于2nm,優(yōu)選地2nm至15nm。圖2表示該實(shí)施方案,其中板21涂覆有基于鋁的涂層22、不銹鋼薄層23和第三鋅涂層24。不銹鋼層可通過本領(lǐng)域技術(shù)人員已知的任何方法來沉積。不銹鋼層例如通過電鍍或通過陰極磁控管濺射來沉積。不管用于沉積鋅涂層的沉積方法,都可進(jìn)行堿法脫脂以增加鋅涂層的粘附性。有利地,通過使用包含例如naoh和/或氫氧化鉀(koh),和表面活性劑的堿性浴進(jìn)行脫脂。有利地通過浸漬或噴涂1秒至120秒,優(yōu)選地2秒至20秒的時(shí)間t6進(jìn)行脫脂。脫脂溫度t6在30℃至90℃的范圍,t6優(yōu)選為60℃。所述浴的ph在10至14的范圍。也可以考慮酸法脫脂。在這種情況下,化學(xué)浴包含例如磷酸(h3po4)和表面活性劑。浴的ph在0至2的范圍。不管所實(shí)施的脫脂類型為何,脫脂之后通常沖洗。然后對(duì)根據(jù)本發(fā)明的鋼板進(jìn)行壓制硬化。該方法包括提供根據(jù)本發(fā)明的預(yù)先涂覆的鋼板,然后切割板以獲得坯件。然后在非保護(hù)氣氛中將該坯件加熱至在840℃至950℃,優(yōu)選地840℃至930℃范圍的鋼的奧氏體化溫度t1。優(yōu)選地,在惰性氣氛或包含空氣的氣氛中將坯件加熱3分鐘至12分鐘,優(yōu)選地4分鐘至10分鐘范圍的時(shí)間t1。在此熱處理期間,鋅涂層被氧化成zno。熱處理之后,將坯件轉(zhuǎn)移至熱沖壓工具,然后在600℃至830℃范圍的溫度t2下進(jìn)行熱沖壓。然后在工具本身中或在轉(zhuǎn)移到特定冷卻工具之后對(duì)所獲得的部件進(jìn)行冷卻。將冷卻速率控制為鋼的組成的函數(shù),使得在壓制硬化過程結(jié)束處鋼的最終顯微組織主要包含馬氏體,優(yōu)選地包含馬氏體,或馬氏體和貝氏體,或者包含至少75%的等軸鐵,量大于或等于5%并且小于或等于20%的馬氏體,以及量小于或等于10%的貝氏體。因此,根據(jù)本發(fā)明獲得具有zno層的可磷酸鹽化經(jīng)壓制硬化的部件。對(duì)于汽車應(yīng)用,在磷酸鹽化之后,將各個(gè)部件浸在電泳浴中。還可考慮順序地施加底漆層、基礎(chǔ)涂漆(basecoatpaint)層和任選地頂涂層。在將電泳層施加到部件之前,預(yù)先對(duì)其進(jìn)行脫脂然后磷酸鹽化以確保電泳層的粘附性。在使根據(jù)本發(fā)明的經(jīng)硬化的部件磷酸鹽化之后,獲得包括zno層并且還包括在zno層上的磷酸鹽晶體層的經(jīng)壓制硬化的部件。在經(jīng)硬化壓制的部件的表面上存在高的磷酸鹽晶體覆蓋的程度。優(yōu)選地,部件表面上的磷酸鹽晶體的覆蓋程度大于或等于80%,更優(yōu)選地大于或等于90%并且有利地大于或等于99%。電泳層對(duì)部件提供額外的抗腐蝕保護(hù)。通常通過噴槍施加的底漆層制備部件的最終外觀并且保護(hù)其抗石屑(stonechips)和抗uv?;A(chǔ)涂漆層給予部件其顏色和最終外觀。頂涂層給予部件表面良好的機(jī)械耐性、耐化學(xué)試劑侵蝕性和良好的表面外觀。通常地,磷酸鹽化層的厚度為1μm至2μm。用于保護(hù)且保證部件的最佳表面外觀的漆膜包括例如8μm至25μm厚的電泳層、35μm至45μm厚的底漆層和40μm至50μm厚的基礎(chǔ)漆層。在其中漆膜還包括頂涂層的情況下,多種漆層的厚度通常如下:-電泳層:8μm至25μm,優(yōu)選地小于20μm,-底漆層:小于45μm,-基礎(chǔ)漆層:小于20μm,和頂涂層:小于55μm。優(yōu)選地,漆膜的總厚度小于120μm,或甚至小于100μm?,F(xiàn)在將通過例示性的但不是限制性的測(cè)試說明本發(fā)明。實(shí)施例對(duì)于全部測(cè)試,使用以下鋼:1500或22mnb5。他們涂覆有厚度為14μm或25μm的包含按重量計(jì)組成9%硅、3%鐵和88%鋁的基于鋁的涂層。在實(shí)施例中使用的1500鋼板的重量組成如下:c=0.2252%;mn=1.1735%;p=0.0126%,s=0.0009%;n=0.0037%;si=0.2534%;cu=0.0187%;ni=0.0197%;cr=0.180%;sn=0.004%;al=0.0371%;nb=0.008%;ti=0.0382%;b=0.0028%;mo=0.0017%;as=0.0023%和v=0.0284%。例如,“14μm”表示如之前限定的具有厚度為14μm的包含按重量計(jì)組成9%硅、3%鐵和88%鋁的基于鋁的涂層的1500鋼。例如,“22mnb5alsi14μm”表示提供有厚度為14μm的包含按重量計(jì)組成9%硅、3%鐵和88%鋁的基于鋁的涂層的22mnb5鋼。實(shí)施例1:可磷酸鹽化的測(cè)試和鋅行為測(cè)試可磷酸鹽化的測(cè)試用于尤其通過評(píng)估部件的表面上的覆蓋的程度確定磷酸鹽晶體在經(jīng)壓制硬化的部件上的分布。實(shí)施例1a:首先,制備一系列3個(gè)樣品,標(biāo)示為1、2和3。根據(jù)ep2270257中描述的方法由提供有第一基于鋁的涂層和厚度為0.2μm的第二zno涂層的22mnb5鋼板獲得樣品1和樣品2。由25μm鋼板獲得樣品3。由還提供有厚度為0.17μm的通過置換沉淀沉積的鋅涂層的25μm鋼板獲得樣品4。通過浸入包含濃度為150g.l-1的naoh和濃度為15g.l-1的zno的浴中持續(xù)5秒進(jìn)行鋅沉積。所述浴的溫度為60℃。對(duì)于每個(gè)樣品,切割經(jīng)涂覆的鋼板以獲得坯件。然后將坯件在900℃的溫度下加熱5分鐘至5分鐘30秒范圍的時(shí)間段。然后將坯件轉(zhuǎn)移至壓機(jī),然后進(jìn)行熱沖壓以獲得部件。最后,對(duì)所述部件進(jìn)行冷卻以獲得馬氏體轉(zhuǎn)變硬化。然后使用5176和h7352的溶液在55℃的溫度下進(jìn)行脫脂。脫脂之后用水沖洗。然后在環(huán)境溫度下通過使用v6513的溶液浸漬使部件的表面活化。最后,在50℃的溫度下在包含24ta溶液的浴中通過浸漬3分鐘進(jìn)行磷酸鹽化。部件用水沖洗部件然后用熱空氣干燥。使用sem觀察這些磷酸鹽化的樣品的表面。結(jié)果顯示在下表中:注意,只有樣品4在經(jīng)硬化的部件上表現(xiàn)出高的磷酸鹽晶體覆蓋的程度。實(shí)施例1b:制備另一系列樣品,標(biāo)示為4、5和6。由還在板的一側(cè)提供有厚度為1μm的通過電鍍沉積的第二鋅涂層的25μm鋼板獲得樣品4,。由還在板的一側(cè)提供有厚度為2μm的通過電鍍沉積的第二鋅涂層的25μm鋼板獲得樣品5。由還在板的一側(cè)提供有厚度為3μm的通過電鍍沉積的第二鋅涂層的25μm鋼板獲得樣品6。對(duì)于通過電鍍的鋅沉積,首先,在80℃的溫度下通過在301溶液中浸漬3秒進(jìn)行板的脫脂。脫脂之后用水沖洗。此后,在環(huán)境溫度下通過在硫酸溶液中浸漬4秒進(jìn)行增亮(brightening)。增亮之后用水沖洗。然后在50℃的溫度下將板浸入包含硫酸(h2so4)和硫酸鋅(znso4)的電解浴中。施加至鋼板的電流密度為80a/dm2。浴的ph為0.8。然后將實(shí)施例1a中所述的壓制硬化方法應(yīng)用到這些樣品中。在這種情況下,將坯件在900℃的t1溫度下加熱6分鐘30秒的時(shí)間t1。然后使用sem觀察磷酸鹽化樣品的表面。結(jié)果顯示在下表中:注意,只有樣品4在經(jīng)硬化的部件表面上表現(xiàn)出高的磷酸鹽晶體覆蓋的程度。還觀察到樣品4至樣品6中的每一者在900℃下的熱處理期間的鋅的行為。我們研究了其中發(fā)生鋅沉積的一側(cè)和沒有涂覆鋅的相反側(cè)上的鋅的行為。圖9和圖10示出了以此順序布置的樣品4、樣品5和樣品6。結(jié)果顯示在下表中。注意,鋅的行為在熱處理期間良好,即,對(duì)于樣品4沒有顯著的報(bào)告。然而,當(dāng)鋅層的厚度為2μm或3μm(樣品5和樣品6)時(shí),鋅擴(kuò)散到相反側(cè)。在工業(yè)規(guī)模上在其中發(fā)生用于奧氏體化的熱處理和壓制硬化的爐中鋅擴(kuò)散是不利的。實(shí)施例1c:制備另外系列的樣品,標(biāo)示為7、8、9。由還在板的一側(cè)提供有通過使用硫酸鋅浴電鍍沉積的第二鋅涂層的14μm鋼板獲得樣品。根據(jù)樣品,鋅涂層的厚度在0.5μm至1.5μm變化。對(duì)于通過電鍍的鋅沉積,首先,在80℃的溫度下通過在301溶液中浸漬3秒進(jìn)行板的脫脂。脫脂之后用水沖洗。然后,在環(huán)境溫度下通過在硫酸溶液中浸漬4秒進(jìn)行增亮。增亮之后用水沖洗。然后在50℃的溫度下將板浸入包含h2so4和znso4的電解浴中。施加至鋼板的電流密度為15a/dm2。浴的ph為3。對(duì)于各個(gè)樣品,切割經(jīng)涂覆的鋼板以獲得坯件。然后將坯件在900℃的溫度下加熱5分鐘30秒的時(shí)間段。然后將坯件轉(zhuǎn)移至壓機(jī),然后進(jìn)行熱沖壓以獲得部件,最后,對(duì)所述部件進(jìn)行冷卻以獲得馬氏體轉(zhuǎn)變硬化。然后在所獲得的經(jīng)硬化的部件上進(jìn)行如實(shí)施例1a中限定的脫脂和磷酸鹽化。用sem觀察這些磷酸鹽化樣品的表面。結(jié)果顯示在下表中:注意,所有樣品在經(jīng)硬化的部件的表面上表現(xiàn)出高的磷酸鹽晶體覆蓋的程度。實(shí)施例2:電泳層的粘附性測(cè)試:該方法用于確定沉積在經(jīng)壓制硬化的部件上的電泳層的粘附性。20μm電泳層沉積在實(shí)施例1c中所獲得的樣品7至樣品9上。為此,將樣品7至樣品9浸入包含水性溶液的浴中,所述水性溶液包含來自ppg工業(yè)的pigmentw9712和resinw7911。施加180v的電壓持續(xù)180秒,最初的30秒用0v至180v的電壓梯度。在進(jìn)行電泳沉積之后,在水中沖洗部件然后在爐內(nèi)在178℃的溫度下使部件固化30分鐘。由此獲得涂漆的經(jīng)壓制硬化的部件。實(shí)施例2a:干e-涂層粘附性測(cè)試使用切割機(jī)在涂漆的部件上制備網(wǎng)格。此后,用肉眼評(píng)估從部件剝離的漆:0表示優(yōu)異,即,沒有漆剝離并且5表示非常差,即,多于65%的漆被剝離。結(jié)果顯示在下表中:樣品101112zn厚度0.5μm1.0μm1.5μm漆粘附性005注意,當(dāng)由提供有厚度為0.5μm或1.0μm的鋅涂層的鋼板制備經(jīng)硬化的部件時(shí),漆粘附性是優(yōu)異的。然而,當(dāng)由具有厚度為1.5μm的鋅涂層的鋼板制備經(jīng)硬化的部件時(shí),漆粘附性非常差。實(shí)施例2b:濕e涂層粘附性測(cè)試首先,在50℃的溫度下在封閉的室中將涂漆的部件浸入軟化水中10天。然后,制備實(shí)施例2a中描述的網(wǎng)格,獲得以下結(jié)果:樣品131415zn厚度0.5μm1.0μm1.5μm漆粘附性014.5注意,當(dāng)由提供有厚度為0.5μm或1.0μm的鋅涂層的鋼板制備經(jīng)硬化的部件時(shí),漆粘附性非常好。然而,當(dāng)由提供有厚度為1.5μm的鋅涂層的鋼板制備經(jīng)硬化的部件時(shí),漆粘附性差。實(shí)施例3:腐蝕測(cè)試該方法用于確定耐腐蝕性,尤其是涂漆的部件上紅銹的存在。通過應(yīng)用實(shí)施例2中描述的方法制備樣品16至樣品18。在此實(shí)施例中,沉積的電泳層的厚度為8μm。為此,將電泳層沉積的總時(shí)間減少到30秒。根據(jù)新vda231-102標(biāo)準(zhǔn),此測(cè)試由使經(jīng)涂漆的部件經(jīng)受6次腐蝕循環(huán)構(gòu)成。循環(huán)由將樣品放置在封閉的室中構(gòu)成,其中將1重量%氯化鈉的水性溶液以3ml/小時(shí)的速率噴涂在樣品上同時(shí)溫度在50℃至-15℃變化并且濕度水平在50%至100%變化。該循環(huán)顯示在圖5中。用肉眼評(píng)估紅銹的存在:3表示優(yōu)異,換句話說,幾乎沒有或沒有紅銹,并且0表示非常差,換句話說,存在大量的紅銹。樣品161718zn厚度0.5μm1.0μm1.5μm腐蝕2.52.51注意,當(dāng)由提供有厚度為0.5μm或1.0μm的鋅涂層的鋼板制備經(jīng)涂漆的部件時(shí),耐紅銹性非常好。然而,當(dāng)由提供有厚度為1.5μm的鋅涂層的鋼板制備經(jīng)涂漆的部件時(shí),耐紅銹性差。因此根據(jù)本發(fā)明硬化的部件能夠?qū)崿F(xiàn)良好的漆粘附性和良好的耐紅銹性。實(shí)施例4:粘附性測(cè)試該方法用于確定使結(jié)合在一起形成三明治結(jié)構(gòu)的兩個(gè)鋼分離所需的力。由未經(jīng)涂覆或者根據(jù)本發(fā)明的經(jīng)鋅涂覆的鋼板獲得這些鋼。為此,由還提供有厚度為0.6μm的通過電鍍沉積的第二鋅涂層的14μm鋼板獲得樣品19和樣品20。由還提供有厚度為0.6μm通過電鍍沉積的第二鋅涂層的25μm鋼板獲得樣品21和樣品22。由25μm鋼板獲得樣品23和樣品24。對(duì)于通過電鍍的鋅沉積,首先,在80℃的溫度下通過噴涂s5170-s5093溶液進(jìn)行板的第一脫脂,此后,在40℃的溫度下通過在相同的溶液中浸漬進(jìn)行第二脫脂。脫脂之后用水沖洗。然后,用硫酸溶液進(jìn)行增亮。增亮之后用水沖洗。此后將板浸入包含h2so4和znso4的電解浴中。此后,在每個(gè)情況下,切割未經(jīng)涂覆的或經(jīng)鋅涂覆的鋼板以獲得坯件。然后將坯件在900℃的溫度下加熱5分鐘至10分鐘的時(shí)間。然后將坯件轉(zhuǎn)移至壓機(jī),然后對(duì)其進(jìn)行熱壓以獲得部件。最后,對(duì)所述部件進(jìn)行冷卻以獲得馬氏體轉(zhuǎn)變硬化。對(duì)于每個(gè)樣品,使用來自dow公司的betamate1480v203g撞擊粘合劑(crashadhesive)使兩個(gè)相當(dāng)?shù)匿摪褰Y(jié)合。然后將這些樣品在180℃下加熱30分鐘以使撞擊粘合劑固化。冷卻之后,向每個(gè)板的兩側(cè)施加機(jī)械應(yīng)力以使兩個(gè)鋼板分離。然后測(cè)量以兆帕(mpa)計(jì)的平均剪切應(yīng)力。結(jié)果顯示在下表中:注意,對(duì)于每個(gè)樣品獲得高剪切應(yīng)力。因此,對(duì)于樣品19至樣品22,這意味著經(jīng)鋅涂覆的結(jié)合界面,即在熱處理期間獲得的基于鋁的涂層與zno層之間的界面和同一zno層與撞擊粘合劑之間的界面,不是易碎的。實(shí)施例5:擴(kuò)散氫測(cè)試該方法用來確定在奧氏體熱處理期間所吸收的氫的量。由還提供有厚度為0.6μm通過電鍍沉積的的第二鋅涂層的25μm鋼板獲得樣品25。由25μm鋼板獲得樣品26。對(duì)于通過電鍍的鋅沉積,重復(fù)實(shí)施例4中描述的方法。然后,對(duì)于各個(gè)樣品,切割未經(jīng)涂覆的或經(jīng)鋅涂覆的鋼板以獲得坯件。然后將坯件在900℃的溫度下加熱6分鐘30秒的時(shí)間。然后將坯件轉(zhuǎn)移至壓機(jī),然后進(jìn)行熱壓以獲得部件。最后,對(duì)所述部件進(jìn)行冷卻以獲得馬氏體轉(zhuǎn)變硬化。最后,使用tda或熱解析分析儀通過熱解吸進(jìn)行熱處理期間由樣品所吸收的氫的量的測(cè)量。為此,在氮流下在紅外線爐中緩慢地加熱放置在石英室的每個(gè)樣品。由檢漏器捕獲所釋放的氫/氮混合物以及用質(zhì)譜儀測(cè)量氫的濃度。結(jié)果顯示在下表中:注意,不論樣品是未經(jīng)涂覆的鋼板或根據(jù)本發(fā)明的涂覆有鋅的鋼板,解吸的擴(kuò)散氫的量是相似的。實(shí)施例6:焊接測(cè)試實(shí)施例6a:焊接范圍該方法用于確定樣品的有效焊接強(qiáng)度范圍,即,在沒有例如將金屬?gòu)慕饘偻繉又兄鸪龅娜秉c(diǎn)的情況下可進(jìn)行點(diǎn)焊的強(qiáng)度范圍。按照汽車制造商規(guī)格,焊接范圍通常大于1ka。由還提供有厚度為0.6μm的通過電鍍沉積的第二鋅涂層的14μm鋼板獲得樣品27。對(duì)于通過電鍍的沉積,重復(fù)實(shí)施例4中描述的方法。然后,切割樣品以獲得坯件。將坯件在900℃的溫度下加熱5分鐘30秒的時(shí)間段。然后將坯件轉(zhuǎn)移至壓機(jī),然后進(jìn)行熱沖壓以獲得部件。最后,對(duì)所述部件進(jìn)行冷卻以獲得馬氏體轉(zhuǎn)變硬化。通過應(yīng)用實(shí)施例5中描述的方法制備樣品28。在此測(cè)試中,對(duì)于各個(gè)樣品,對(duì)兩個(gè)相當(dāng)?shù)匿摪暹M(jìn)行點(diǎn)焊。為此,在每個(gè)根據(jù)本發(fā)明的經(jīng)涂覆的鋼板的兩側(cè)上放置電極。在電極之間施加450dan的壓縮力。施加到電極的頻率50hz的交流電流通過樣品,因此使得兩個(gè)鋼板被焊接。此外,在測(cè)試開始設(shè)置3ka的強(qiáng)度然后逐漸增加以確定最大強(qiáng)度(imax),在該最大強(qiáng)度處熔融的金屬被驅(qū)逐。此后,強(qiáng)度逐漸降低以確定最小強(qiáng)度(imin),在該最小強(qiáng)度處點(diǎn)焊的直徑小于可允許的閾值。焊接范圍的極限為imax和imin。結(jié)果顯示在下表中:注意,每個(gè)樣品的焊接范圍大于1ka。實(shí)施例6b:機(jī)械特性該方法用于確定點(diǎn)焊部分的機(jī)械特性。為此,將機(jī)械應(yīng)力施加至點(diǎn)焊到其破壞。樣品29和樣品31分別是實(shí)施例6a的樣品27和樣品28。樣品30和樣品32分別由14μm和25μm鋼板獲得。在該測(cè)試中,樣品包括以交叉形式焊接的兩個(gè)相當(dāng)?shù)匿摪濉J┘恿σ云茐狞c(diǎn)焊接部分。這個(gè)力(稱為交叉拉伸強(qiáng)度(crosstensilestrength,cts))以dan為單位表示。其是點(diǎn)焊的直徑和金屬厚度(即,鋼的厚度和金屬涂層的厚度)的函數(shù)。這使得其能夠計(jì)算系數(shù)α,α為cts的值相對(duì)于點(diǎn)焊的直徑乘以基底的厚度的乘積的比值。這個(gè)系數(shù)以dan/mm2為單位表示。結(jié)果顯示在下表中:注意,樣品29和樣品30的系數(shù)α與樣品31和樣品32的系數(shù)α是相似的。實(shí)施例6c:電極使用壽命該方法用于確定電極使用壽命,即,在電極過于劣化以及點(diǎn)焊的質(zhì)量不再是可接受的之前可用電極對(duì)進(jìn)行的點(diǎn)焊的數(shù)目。樣品33和樣品34分別是實(shí)施例6a中的樣品27和樣品28。該測(cè)試待利用用于進(jìn)行點(diǎn)焊的相同電極對(duì)進(jìn)行以及每100個(gè)焊接測(cè)量他們的直徑。事實(shí)上,電極對(duì)用于焊接越多,則點(diǎn)焊的直徑將減少得越多。因此,在汽車制造商規(guī)格中存在用于點(diǎn)焊的臨界直徑。這個(gè)臨界直徑通常描述為4x√t,其中t為金屬的厚度,即,以mm計(jì)的板的厚度。低于該直徑,認(rèn)為電極被磨損。點(diǎn)焊的直徑作為所進(jìn)行的焊接的數(shù)目的函數(shù)來測(cè)定。當(dāng)樣品33和樣品34的金屬厚度為1.5mm時(shí),點(diǎn)焊部分的臨界直徑為4.89mm。在1000個(gè)焊接點(diǎn)之后停止測(cè)試。結(jié)果顯示在下表中:注意,點(diǎn)焊的直徑大大高于所進(jìn)行的全部焊接的極限值4.89mm。此外,注意,焊接的直徑從200個(gè)至1000個(gè)焊接減少得非常小。當(dāng)前第1頁(yè)12