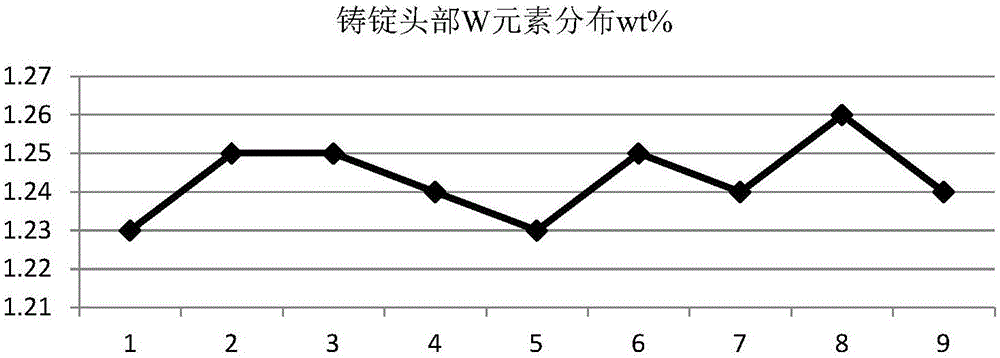
本發(fā)明屬于高溫合金冶煉
技術領域:
,具體涉及一種提高GH4720Li合金W元素成分均勻性的方法。
背景技術:
:GH4720Li是一種鎳基時效強化型高溫合金,主要用于制造使用溫度為650-750℃的高性能壓氣機和渦輪盤以及在短時間內900℃使用的渦輪盤。GH4720Li的合金化程度非常高,同時也帶來了高溫合金鑄錠中的合金元素偏析。經過熔煉的鑄錠在凝固過程中由于偏析作用易形成低熔點γ+γ'共晶、η相和Ni5Zr等低熔點組織,這對后續(xù)的均勻化處理和鍛造制造了困難,同時也對GH720Li的變形提出了嚴峻的考驗。該合金中合金元素的含量較高達到40%以上,Al、Ti元素大大增加了主要沉淀強化相γ'相的含量,大量的Co、Mo等固溶強化元素以及起晶間強化的Zr、B等元素,使該高溫合金具有優(yōu)良的高溫性能,其中W元素既能起到固溶強化的作用,也可以進入γ'相中,增加γ'與基體間的錯配度;同時W元素也能夠明顯降低基體的層錯能,有效改善高溫合金的蠕變性能。因此提高W元素在鑄錠中的均勻性,對于提高鑄錠均勻性,改善鍛造性能,具有重要作用。技術實現要素:本發(fā)明的目的是提供一種提高GH4720Li合金W元素成分均勻性的方法,解決了現有Φ440-560mm規(guī)格GH4720Li鑄錠中存在的W元素分布不均勻的問題。本發(fā)明所采用的技術方案是:一種提高GH4720Li合金W元素成分均勻性的方法,具體包括以下步驟:步驟1,按照GH4720Li合金配比,確定原料電解鎳、純鉻、電鈷、鎳鎢合金、鎳鉬合金、純鈦、純鋁、鎳硼合金、純鋯、碳的用量;步驟2,真空感應熔煉:將步驟1所述原料分別加入真空感應爐中進行真空感應熔煉為鑄錠;步驟3,真空自耗熔煉:對步驟3得到的鑄錠進行兩次真空自耗熔煉,第二次真空自耗熔煉采用低熔速控制熔煉。本發(fā)明的特點還在于,步驟1中鎳鎢合金為NiW45中間合金。步驟1中電解鎳、電鈷進行表面處理,處理完成后表面應潔凈且呈現金屬亮色,然后與鎳鎢合金、鎳鉬合金、純鈦、純鋁、純鉻在100℃下進行10h的干燥。步驟2具體為:首先加入電解鎳、純鉻、電鈷、鎳鎢合金、鎳鉬合金和碳熔化,熔化速度小于1/4最大爐容量/h,然后加入純鈦、純鋁、鎳硼合金、純鋯進行精煉;精煉后控制澆注溫度澆注。精煉溫度為1450-1550℃,精煉時間為30-90min;澆注溫度為1450-1550℃。澆注錠模規(guī)格為Φ280~Φ400mm。步驟3中一次真空自耗熔煉采用Φ340~480mm的坩堝,熔前漏氣率控制在2.0Pa/min以下,在熔煉過程中真空度控制在2.0Pa以下,熔煉電流選擇2~10kA,熔煉電壓選擇22~25V,熔速控制在4-7kg/min,熔煉后冷卻時間大于1.0小時。步驟3中二次真空自耗熔煉,采用Φ410~560mm的坩堝,熔前漏氣率控制在1.0Pa/min以下,在熔煉過程中真空度控制在1.0Pa以下,熔煉電流選擇2~8kA,熔煉電壓選擇21~25V,熔速控制在2-5kg/min,熔煉后冷卻時間大于1.0小時。步驟3中兩次真空自耗熔煉過程中充入氦氣冷卻,充氦壓力控制在200-600Pa。本發(fā)明的有益效果是,一種提高GH4720Li合金W元素成分均勻性的方法,采用NiW中間合金代替高熔點的W金屬,使用真空感應熔煉加兩次真空自耗熔煉的熔煉方式,在第三次熔煉中使用低熔速控制的方法實現過程穩(wěn)定控制。本發(fā)明在保證不降低鑄錠成品率的前提下,使得鑄錠中的W元素分布更加均勻。解決了由于W元素成分分布不均勻導致的鑄錠各位置成分差異,從而影響合金的鍛造工藝,對于解決W元素的成分均勻性及鍛件的性能均勻性具有重要作用。附圖說明圖1是本發(fā)明方法的流程圖;圖2是實施例1制得的鑄錠頭部橫向九點W元素分布圖;圖3是實施例1制得的鑄錠縱向五點W元素分布圖;圖4是實施例2制得的鑄錠頭部橫向九點W元素分布圖;圖5是實施例2制得的鑄錠縱向五點W元素分布圖。具體實施方式下面結合附圖和實施例對本發(fā)明進行詳細說明。本發(fā)明一種提高GH4720Li合金W元素成分均勻性的方法,如圖1所示,具體包括以下步驟:步驟1,將符合國家標準的優(yōu)質電解鎳、電鈷等進行表面處理,處理完成后表面應潔凈且呈現金屬亮色,處理完成后與鎳鎢合金、鎳鉬合金、純鈦、純鋁、純鉻等合金原料在100℃下進行10h的干燥。其中選用的鎳鎢合金為NiW45。步驟2,按照合金目標成分計算所需要加入的合金量,GH4720Li合金的成分要求見表1。表1合金化學成分要求,wt%步驟3,真空感應熔煉:將原料加入真空感應爐中進行真空感應熔煉,首先加入Ni、Cr、Co、NiW、NiMo、C熔化,熔化速度小于1/4最大爐容量/h,然后加入Al、Ti、NiB、Zr進行精煉,精煉溫度1450-1550℃,精煉時間30-90min;精煉后控制澆注溫度為1450-1550℃在規(guī)格為Φ260~Φ410mm的錠模重澆注。熔煉完成后對得到的鑄錠進行打磨處理。步驟4,一次真空自耗熔煉:將電極掉頭焊接,在直徑Φ340~480mm的坩堝中進行一次真空自耗熔煉,熔前漏氣率控制在2.0Pa/min以下,在熔煉過程中真空度控制在2.0Pa以下,熔煉電流選擇2~10kA,熔煉電壓選擇22~25V,熔煉速度選擇4-7kg/min,熔煉后冷卻時間大于1.0小時,熔煉完成后整錠扒皮處理;熔煉過程中充入氦氣冷卻,充氦壓力控制在200-600Pa。步驟5,二次真空自耗熔煉:將電極掉頭焊接,在直徑Φ440~560mm的坩堝進行二次真空自耗熔煉,熔前漏氣率控制在1.0Pa/min以下,在熔煉過程中真空度控制在1.0Pa以下,熔煉電流選擇2~8kA,熔煉電壓選擇21~25V,熔速選擇2-5kg/min,采用低熔速控制,熔煉后冷卻時間大于1.0小時。熔煉過程中充入氦氣冷卻,充氦壓力控制在200-600Pa。本發(fā)明提高GH4720Li合金W元素成分均勻性的生產方法,通過:1)選擇合適的鎢元素中間合金。純鎢金屬的熔點為3422℃,而真空感應熔煉的熔池溫度一般為1400-1600℃之間,遠遠低于鎢金屬的熔點。因此需要非常長的時間來將鎢金屬進行溶解,很難獲得鎢元素分布均勻的熔體。通過選擇鎳鎢中間合金,合金中鎢元素重量百分數為45%,將合金熔點降低到1500℃左右,接近于真空感應熔煉的熔池溫度,極大的縮短了鎢元素的熔化時間和均勻化時間,更容易獲得W元素分布均勻的合金熔體。2)采用兩次真空自耗熔煉,每次自耗熔煉進行掉頭焊接,促進合金頭尾成分的均勻性。3)在二次真空自耗熔煉中采用低熔速控制熔煉方法,減少能量輸入,縮短糊狀區(qū)的寬度,同時可以提高熔煉過程的穩(wěn)定性,進一步提高鎢元素的成分均勻性。采用本發(fā)明方法熔煉的不同規(guī)格的GH4720Li合金,均取得了良好的效果。實施例1熔煉直徑為Φ510mm的GH4720Li高溫合金鑄錠。1.原材料處理:將電解Ni和電鈷進行表面噴砂處理,處理后與與鎳鎢合金、鎳鉬合金、純鈦、純鋁、純鉻在100℃下進行10h的干燥。2.配料:確定合金配比,按照配比進行投料,合金配比和所用原料和用量見表2和3。表2合金化學成分配比,wt%表3原料及用量3.真空感應熔煉:真空感應熔煉使用Φ350mm的錠模,熔化速度700kg/h,精煉溫度1480℃,精煉時間60min;澆注溫度為1480℃。熔煉完成后進行打磨。4.真空自耗熔煉:電極掉頭進行焊接進行熔煉,一次真空自耗熔煉采用Φ430mm規(guī)格坩堝,二次真空自耗熔煉采用Φ510mm規(guī)格坩堝,一次真空自耗熔煉熔速為5.5kg/min,結束后鑄錠進行扒皮處理再進行二次真空自耗熔煉,二次真空自耗熔煉的熔速為3.8kg/min。兩次熔煉的參數見表4。表4熔煉過程參數控制漏氣率Pa/min真空度Pa熔煉電流kA熔煉電壓V充氦壓力Pa冷卻時間h一次≤1.0≤24~722~24300≥1二次≤0.5≤13~622~24300≥1對得到的鑄錠頭部橫向截面進行九點取樣、表面縱向五點取樣分析鑄錠整體成分均勻性結果見圖2和圖3。由2和圖3可以看出W元素的分布均勻。實施例2熔煉直徑為Φ440mm的GH4720Li高溫合金鑄錠。1.原材料處理:將電解Ni和電鈷進行表面噴砂處理,處理后與與鎳鎢合金、鎳鉬合金、純鈦、純鋁、純鉻在100℃下進行10h的干燥。2.配料:確定合金配比,按照配比進行投料,合金配比和所用原料和用量見表5和6。表5合金化學成分配比,wt%表6原料及用量3.真空感應熔煉:真空感應熔煉使用Φ280mm的錠模,熔化速度300kg/h,精煉溫度1450℃,精煉時間30min;澆注溫度為1450℃。熔煉完成后進行打磨。4.真空自耗熔煉:電極掉頭進行焊接進行熔煉,一次真空自耗熔煉采用Φ360mm規(guī)格坩堝,二次真空自耗熔煉采用Φ440mm規(guī)格坩堝,一次真空自耗熔煉的熔速為4kg/min,結束后鑄錠進行扒皮處理再進行二次真空自耗熔煉,二次真空自耗熔煉的熔速為2kg/min。兩次熔煉的參數見表7。表7熔煉過程參數控制漏氣率Pa/min真空度Pa熔煉電流kA熔煉電壓V充氦壓力Pa冷卻時間h一次≤1.0≤22~622~24200≥1二次≤0.5≤12~522~24200≥1對得到的鑄錠頭部橫向截面進行九點取樣、表面縱向五點取樣分析鑄錠整體成分均勻性結果見圖4和圖5。由圖4和圖5可以看出W元素分布均勻性。實施例3熔煉直徑為Φ560mm的GH4720Li高溫合金鑄錠。1.原材料處理:將電解Ni和電鈷進行表面噴砂處理,處理后與與鎳鎢合金、鎳鉬合金、純鈦、純鋁、純鉻在100℃下進行10h的干燥。2.配料:確定合金配比,按照配比進行投料,合金配比和所用原料和用量見表8和9。表8合金化學成分配比,wt%表9料及用量3.真空感應熔煉:真空感應熔煉使用Φ400mm的錠模,熔化速度700kg/h,精煉溫度1550℃,精煉時間90min;澆注溫度為1550℃。熔煉完成后進行打磨。4.真空自耗熔煉:電極掉頭進行焊接進行熔煉,一次真空自耗熔煉采用Φ480mm規(guī)格坩堝,二次真空自耗熔煉采用Φ560mm規(guī)格坩堝,一次真空自耗熔煉的熔速為7kg/min,結束后鑄錠進行扒皮處理再進行二次真空自耗熔煉,二次真空自耗熔煉的熔速為5kg/min。兩次熔煉的參數見表10。表10煉過程參數控制漏氣率Pa/min真空度Pa熔煉電流kA熔煉電壓V充氦壓力Pa冷卻時間h一次≤1.0≤24~1023~25600≥1二次≤0.5≤14~823~25600≥1當前第1頁1 2 3