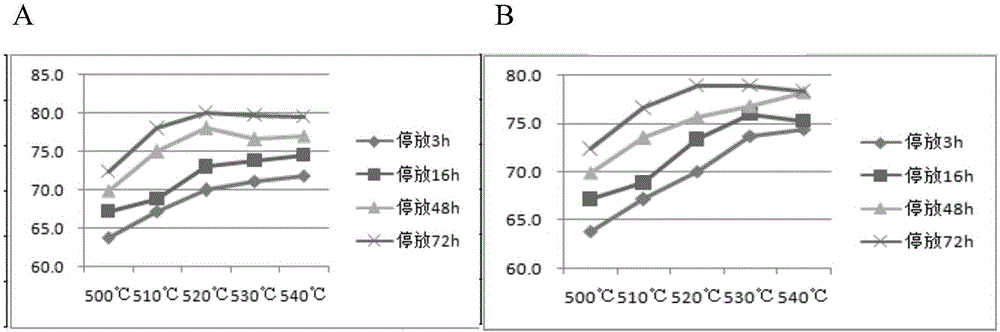
本發(fā)明涉及鋁合金
技術(shù)領(lǐng)域:
,具體地說,是一種提高6082鋁合金性能的熱處理工藝。
背景技術(shù):
:6082鋁合金屬于Al-Mg-Si系,可熱處理強(qiáng)化,Mg2Si相為強(qiáng)化相。該合金具有中等強(qiáng)度、耐腐蝕性高,無應(yīng)力腐蝕破裂傾向,焊接性能好,成型性和工藝性能良好等優(yōu)點(diǎn)。具有良好的綜合性能,該合金廣泛用于制造中等強(qiáng)度,塑性和抗腐蝕要求高的飛機(jī)零件,大型結(jié)構(gòu)件以及常溫下工作的鍛件。近期,我司生產(chǎn)的6082-T6鋁合金型材沖壓件出現(xiàn)停放較長時間后硬度偏高(12.5HW-14HW),性能不均,“停放效應(yīng)”明顯的現(xiàn)象,客戶沖壓工序因此原因?qū)е碌膹U品率升高,跟蹤客戶生產(chǎn)現(xiàn)場沖壓報廢得到的數(shù)據(jù):每10件約有2-3件因上述原因報廢,報廢率較高??蛻羰褂帽井a(chǎn)品加工成汽車橫梁,加工設(shè)備是沖壓機(jī)床。加工過程中,因?yàn)椤白匀粫r效”,產(chǎn)品硬度增加,抵抗變形能力增強(qiáng),在沖壓完成后,有回彈傾向,回彈后輪廓度檢具超差,影響整車裝配時精度;為提高客戶沖壓合格率,開展了本發(fā)明研究。技術(shù)實(shí)現(xiàn)要素:本發(fā)明的目的在于研究擠壓型材淬火溫度(固溶溫度)、時效前停放效應(yīng)等參數(shù)對6082鋁合金組織性能,硬度的變化規(guī)律,找出符合客戶沖壓條件的工藝參數(shù)。本發(fā)明提供一種提高6082鋁合金性能的熱處理工藝,將6082鋁合金依次經(jīng)過如下步驟處理:S1,擠壓工藝,淬火;S2,回歸工藝;S3,時效工藝。其中,所述的步驟S1擠壓過程鑄錠設(shè)定加熱溫度:460℃-470℃;擠壓筒設(shè)定溫度:450℃;擠壓桿前進(jìn)速度:1.5-2.0;擠壓過程擠壓桿前進(jìn)速度,適當(dāng)調(diào)節(jié),滿足出口溫度范圍。優(yōu)選的,所述的步驟S1淬火溫度(擠壓型材入淬火系統(tǒng)極限溫度):510℃-530℃,停放時間為16h-48h。優(yōu)選的,所述的步驟S1冷卻方式:水冷(噴水)。優(yōu)選的,所述的步驟S2回歸工藝為:255℃/5min(回歸的溫度255℃,保溫5分鐘);此工藝在于解決型材硬度大于12.5HW的情況,小于12.5HW的型材不必使用;所以客戶與我司需緊密對接,生產(chǎn)完成的產(chǎn)品立即轉(zhuǎn)入沖壓工序,若停放時間過長,需要對型材進(jìn)行回歸后使用。優(yōu)選的,所述的步驟S3時效工藝參數(shù)為180℃/6h(180℃,保溫6小時)。優(yōu)選的,所述的6082鋁合金型號為PSG390型材。優(yōu)選的,所述的6082鋁合金鑄錠的化學(xué)成分為:Si1.07~1.17%,F(xiàn)e0.25%,Cu0.02-0.06%,Mg0.65~0.75%,Mn0.50~0.55%,Zn0.10%,Ti0.10%,Cr0.10-0.15%,余量為Al。本發(fā)明優(yōu)點(diǎn)在于:采用本發(fā)明的工藝處理后的鋁合金型材,沖壓情況良好,滿足其使用要求,并解決了因自然時效造成硬度升高的產(chǎn)品報廢的情況,大大提高的材料的利用率,廢品率顯著降低。附圖說明圖1:硬度隨時間變化規(guī)律。圖2:硬度(布氏)隨時間變化關(guān)系。A,試樣(1);B,試樣(2)。圖3:放置72小時穩(wěn)定后硬度(布氏)曲線。圖4:停放3h,不同固溶溫度性能值變化曲線。圖5:停放16h,不同固溶溫度性能值變化曲線。圖6:停放48h,不同固溶溫度性能值變化曲線。圖7:停放72h,不同固溶溫度性能值變化曲線。圖8:相同固溶溫度,不同停放時間屈服變化規(guī)律。圖9:相同固溶溫度,不同停放時間拉伸強(qiáng)度變化規(guī)律。圖10:相同固溶溫度,不同停放時間延伸率變化規(guī)律。圖11:300℃回歸工藝硬度變化趨勢。圖12:270℃回歸工藝硬度變化趨勢。圖13:255℃回歸工藝硬度變化趨勢。具體實(shí)施方式下面結(jié)合實(shí)施例對本發(fā)明提供的具體實(shí)施方式作詳細(xì)說明。實(shí)施例1一、實(shí)驗(yàn)材料、工藝參數(shù)1、型號為PSG390型材,使用鑄錠的化學(xué)成分如下表1所列。固溶溫度(擠壓過程中淬火溫度)分別為500℃、510℃、520℃、530℃、540℃,時效制度為180℃/6h。其中,所述的鋁合金型材為型號為PSG390型材,所述的鑄錠的化學(xué)成分如下表1所示:表1合金SiFeCuMgMnZnTiCr60821.07~1.170.250.02-0.060.65~0.750.50~0.550.100.100.10-0.152、擠壓過程工藝參數(shù)設(shè)置鑄錠設(shè)定加熱溫度值:460℃-470℃;(擠壓過程鑄錠加熱溫度)擠壓筒設(shè)定溫度:450℃±10℃;(擠壓過程擠壓筒設(shè)定溫度)擠壓桿前進(jìn)速度:1.6±0.2mm/s(擠壓過程擠壓桿前進(jìn)速度,適當(dāng)調(diào)節(jié),滿足出口溫度范圍);淬火溫度(即固溶溫度:型材入淬火系統(tǒng)溫度):500-540℃;冷卻方式:水冷(噴水);3、時效工藝:180℃/6h,(T6性能驗(yàn)證:Rm≥300MPaRp0.2=270MPaA5≥8%)4、實(shí)驗(yàn)步驟:研究不同淬火溫度(固溶溫度)的初始硬度值、穩(wěn)定后的硬度區(qū)間,時效后的性能指標(biāo),繪制曲線,分析淬火溫度(固溶溫度)、停放時間對硬度、性能變化的影響規(guī)律,制定符合客戶使用要求的工藝參數(shù)值:(1)為了做本次實(shí)驗(yàn),擠壓過程中淬火溫度(固溶溫度)控制在500-540℃,其他擠壓參數(shù)要求按上述工藝參數(shù)執(zhí)行,實(shí)驗(yàn)機(jī)臺為2200T擠壓機(jī),生產(chǎn)過程中監(jiān)控每整支擠壓型材的淬火溫度(固溶溫度)并標(biāo)記;(2)擠壓過程中標(biāo)注整支鑄錠擠壓過程中型材表面溫度(為滿足所需溫度區(qū)間,可適當(dāng)調(diào)整擠壓速度),標(biāo)記溫度分別為500℃、510℃、520℃、530℃、540℃;(3)取樣后,按一定的時間間隔測量試樣布氏硬度及時效后的性能(180℃/6h)并填寫表格;(4)繪制并分析曲線,確定淬火溫度(固溶溫度)、停放時間對硬度、性能的影響規(guī)律,找到滿足硬度要求的合理的淬火溫度(固溶溫度)值或工藝參數(shù)。二、停放時間與硬度變化研究設(shè)置兩組實(shí)驗(yàn)試樣進(jìn)行對比,每個試樣測試三點(diǎn)硬度值后取平均值:1、停放時間與硬度變化趨勢從圖1“時間-硬度”曲線可以看出,在前8小時內(nèi)硬度隨停放時間的延長,上升趨勢明顯;超過8小時后,硬度變化緩慢,較穩(wěn)定,基本維持在一定的區(qū)間變化;48h小時后測量硬度基本穩(wěn)定在10-12.5HW間,98%產(chǎn)品穩(wěn)定在此區(qū)間,沖壓效果良好。2、不同淬火溫度(固溶溫度),放置相同時間后進(jìn)行硬度(布氏)測試;由表2、表3數(shù)據(jù)和圖2可知,初始淬火溫度(固溶溫度)不同,相應(yīng)的初始硬度不同,初始固溶溫度越低,對應(yīng)的硬度較低,隨著停放時間的延長,穩(wěn)定后的硬度呈遞增趨勢變化;考慮到客戶時效前進(jìn)行沖壓加工,淬火溫度(固溶溫度)低,有利于沖壓變形,在保證性能的情況下,固溶溫度可選擇在510℃-530℃較為合理。表2試樣(1)硬度(布氏)隨時間變化關(guān)系固溶溫度停放3h停放16h停放48h停放72h500℃63.967.269.972.4510℃67.268.975.078.0520℃70.073.078.080.1530℃71.173.876.679.7540℃71.874.677.079.5表3試樣(2)硬度(布氏)隨時間變化關(guān)系固溶溫度停放3h停放16h停放48h停放72h500℃63.967.269.972.4510℃67.268.973.576.6520℃70.173.475.778.9530℃73.776.076.878.9540℃74.575.378.278.43、放置72小時穩(wěn)定后硬度(布氏)曲線,硬度基本穩(wěn)定在70HB-80HB,見表4,變化規(guī)律見圖3。表4放置72小時穩(wěn)定后硬度(布氏)數(shù)據(jù)固溶溫度停放72h500℃75.2510℃75.4520℃77.4530℃78.9540℃79.8三、不同固溶溫度不同停放時間對6082合金性能的影響不同淬火溫度(固溶溫度)及不同停放時間6082型材PSG390試樣時效(180℃/6h)后拉伸性能的變化規(guī)律見性能對比圖表;淬火后停放時間分別為3h、16h、48h、72h之后進(jìn)行人工時效,檢測力學(xué)性能,繪制時效前停放時間與力學(xué)性能關(guān)系曲線。1、停放時間相同,固溶溫度從500℃上升到540℃時,時效后合金的強(qiáng)度升高,上升到540℃-550℃時,強(qiáng)度最大,伸長率下降;溫度繼續(xù)上升時,按照理論推理強(qiáng)度開始下降。隨著固溶溫度的升高,殘留結(jié)晶相的數(shù)量逐漸減少,時效后獲得的β″沉淀強(qiáng)化相的尺寸更小、密度更高,晶界無沉淀析出區(qū)更窄,強(qiáng)度和伸長率更高;但溫度過高時,再結(jié)晶嚴(yán)重,晶粒粗大,擠壓效應(yīng)消失,強(qiáng)度下降,見表5-8和圖4-7。綜合考慮強(qiáng)度和拉伸率,540-550℃是較佳的固溶溫度。表5停放3h時間,不同淬火溫度(固溶溫度)性能變化變化情況表6停放16h時間,不同淬火溫度(固溶溫度)性能變化變化情況表7停放48h時間,不同淬火溫度(固溶溫度)性能變化變化情況表8停放72h時間,不同淬火溫度(固溶溫度)性能變化變化情況2、固溶溫度相同,隨著停放時間增加,停放時間前期隨著時間增加其強(qiáng)度性能下降;停放時間在8h~14h范圍內(nèi)隨著時間增加其強(qiáng)度性能下降明顯,在10h-20h時達(dá)到最低點(diǎn)后趨于穩(wěn)定;停放時間超過30h后,隨著時間增加其強(qiáng)度性能稍有增加,見表9-11和圖8-10。表9相同淬火溫度(固溶溫度),不同停放時間拉伸強(qiáng)度變化規(guī)律表10相同淬火溫度(固溶溫度),不同停放時間屈服變化規(guī)律表11相同淬火溫度(固溶溫度),不同停放時間延伸率變化規(guī)律停放效應(yīng)與室溫停留時產(chǎn)生的GP區(qū)重新溶解有關(guān)。停放時間較長,合金中將形成大量硅的偏聚團(tuán),因而固溶體中溶質(zhì)元素的濃度大大降低,人工時效時那些小于臨界尺寸的GP區(qū)將重新溶入固溶體,因而影響了材料的性能;但如果繼續(xù)延長停放時間,則那些小于臨界尺寸的GP區(qū)有可能長大到穩(wěn)定的晶核尺寸,因此,使合金的強(qiáng)度有所回升,因此室溫停放的影響又重新減小,但停放時間過長,對材料的屈服強(qiáng)度有不利影響。在本次實(shí)驗(yàn)中,高溫區(qū)域的性能變化較為明顯。五、回歸熱處理的應(yīng)用在實(shí)際生產(chǎn)中,淬火后的停放時間是根據(jù)生產(chǎn)情況而定的,并沒有嚴(yán)格的規(guī)定,有很大的隨意性,于是造成了產(chǎn)品因?yàn)橥7艜r間過長而造成強(qiáng)度上升,硬度加大,塑性降低,沖壓時出現(xiàn)斷裂的現(xiàn)象,造成產(chǎn)品報廢,為解決因停放時間長,硬度高的問題,我們通過探究本成分6082合金的回歸工藝,解決上述問題的發(fā)生,降低因自然時效造成的產(chǎn)品批量報廢。1、回歸現(xiàn)象特點(diǎn)經(jīng)過自然時效強(qiáng)化的鋁合金,快速加熱至200℃-300℃,然后快速冷卻至室溫,該合金重新軟化,恢復(fù)至新淬火狀態(tài),如將其在室溫下停放,仍能進(jìn)行正常的自然時效。這種現(xiàn)象稱為回歸現(xiàn)象。回歸現(xiàn)象實(shí)際上是經(jīng)過自然時效后的鋁合金生成的GP區(qū)或亞穩(wěn)定相,在快速短時間加熱時發(fā)生溶解,變成原有的淬火狀態(tài)。因而合金性能也恢復(fù)到新淬火狀態(tài)下的性能?;貧w現(xiàn)象具有下面幾個特點(diǎn):(1)凡自然時效強(qiáng)化的鋁合金都具有回歸現(xiàn)象。(2)回歸處理可以多次重復(fù)進(jìn)行。但是每次回歸處理后,它的性能不能完全恢復(fù)到原有狀態(tài),總有一點(diǎn)差距。(3)回歸處理的溫度越高,回歸過程越快,所需加熱時間越短。(4)經(jīng)回歸處理后的合金,其耐蝕性能有所下降。(6)在回歸熱處理時要嚴(yán)格控制溫度和時間,以免對合金的組織和性能產(chǎn)生不良影響。2、實(shí)驗(yàn)過程:分別對固溶處理后自然時效5天的試樣進(jìn)行300℃、270℃、255℃,不同保溫時間的回歸熱處理,并測定試樣回歸前的硬度值(標(biāo)記:HV1),回歸后1h內(nèi)的硬度值(標(biāo)記:HV2),求出硬度變化量ΔHV(=HV2-HV1),結(jié)果見下表12。表12PSG390(6082/T4)300℃回歸工藝試驗(yàn)(1)由上表12可看出,高溫回歸,材料明顯出現(xiàn)過時效現(xiàn)象,性能顯著降低,已經(jīng)不能滿足客戶要求。表13PSG390(6082/T4)270℃回歸工藝試驗(yàn)(2)由上表13可知,保溫時間在2min時出現(xiàn)拐點(diǎn),是比較合理的回歸點(diǎn),但實(shí)際生產(chǎn)中,短時間很難控制,不適合實(shí)際生產(chǎn),而超過十分鐘,材料性能開始下降,出現(xiàn)過時效的情況。表14PSG390(6082/T4)255℃回歸工藝試驗(yàn)(3)由上表14可知,保溫時間在5min時出現(xiàn)拐點(diǎn),是比較合理的回歸點(diǎn),實(shí)際生產(chǎn)中,容易控制,而超過7min,材料硬度開始上升,出現(xiàn)硬度提升的情況。綜上所述,本發(fā)明上述成分的6082合金,合理的回歸溫度時255℃/5min,回歸后硬度換算成韋氏硬度約12-13HW,通過與客戶的溝通,沖壓情況良好,滿足其使用要求,并解決了因自然時效造成硬度升高的產(chǎn)品報廢的情況,大大提高的材料的利用率。六、總結(jié)1、硬度隨停放時間的延長逐漸上升,在前8小時內(nèi)上升迅速,超過8小時后上升緩慢,在16h-48h內(nèi)硬度基本趨于穩(wěn)定;從多次測量數(shù)據(jù)來看,最終10W-12.5W之間,客戶沖壓合格達(dá)98%以上;2、淬火溫度(固溶溫度)(500~550℃):(1)停放時間相同,隨著淬火溫度(固溶溫度)的升高,合金的強(qiáng)度先升高后下降,在540-550℃左右時達(dá)最高值;溫度繼續(xù)上升時,按照理論推理強(qiáng)度開始下降。淬火溫度(固溶溫度)影響合金初始硬度值,淬火溫度(固溶溫度)低,初始硬度低,在符合T6性能要求的條件下,為滿足客戶要求,降低因淬火溫度過低造成性能不合格的風(fēng)險,可選擇淬火溫度(固溶溫度)范圍為510℃-530℃;(2)淬火溫度(固溶溫度)相同,隨著停放時間的延長,強(qiáng)度先下降后趨于穩(wěn)定狀態(tài),延伸率先升高后趨于穩(wěn)定狀態(tài),彼此間相互對應(yīng),中高溫區(qū)域表現(xiàn)明顯,低溫區(qū)域表現(xiàn)并不理想;3、實(shí)際生產(chǎn)過程中可根據(jù)客戶使用要求收窄工藝范圍,控制停放時間及縮短加工周期,多次跟蹤客戶沖壓情況,廢品率降低至每100件中2-3件因上述原因造成的產(chǎn)品報廢;優(yōu)化后的擠壓過程工藝參數(shù):鑄錠溫度:460℃-470℃;(擠壓過程鑄錠加熱溫度)擠壓筒設(shè)定溫度:450℃±10℃;(擠壓過程擠壓筒設(shè)定溫度)擠壓桿前進(jìn)速度:1.5-2.0(擠壓桿設(shè)定速度,擠壓過程中適當(dāng)調(diào)節(jié),滿足出口溫度范圍);淬火溫度:510-530℃;(擠壓型材入淬火系統(tǒng)極限溫度)冷卻方式:水冷(噴水);回歸工藝為:255℃/5min(此工藝在于解決型材硬度大于12.5HW的情況,小于12.5HW的型材不必使用;所以要求客戶與我司解密對接,生產(chǎn)完成的產(chǎn)品立即轉(zhuǎn)入沖壓工序)。以上已對本發(fā)明創(chuàng)造的較佳實(shí)施例進(jìn)行了具體說明,但本發(fā)明創(chuàng)造并不限于所述實(shí)施例,熟悉本領(lǐng)域的技術(shù)人員在不違背本發(fā)明創(chuàng)造精神的前提下還可做出種種的等同的變型或替換,這些等同的變型或替換均包含在本申請權(quán)利要求所限定的范圍內(nèi)。當(dāng)前第1頁1 2 3