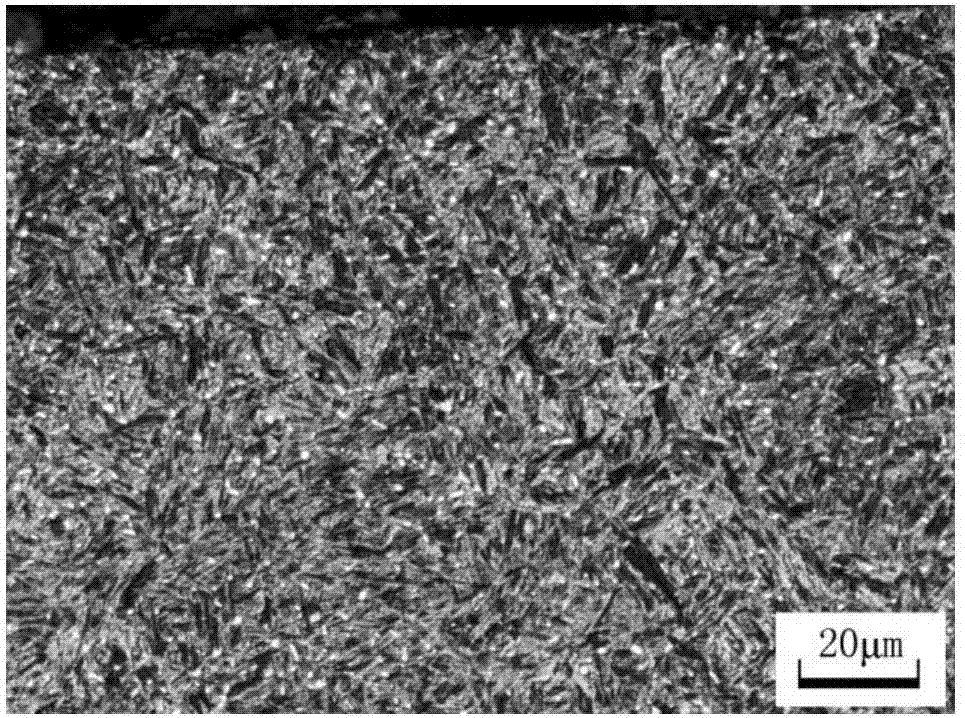
本發(fā)明涉及工程機(jī)械用鋼
技術(shù)領(lǐng)域:
,特別涉及一種低淬透性耐磨帶鋼及其制造方法。
背景技術(shù):
:低淬透性薄帶耐磨鋼特別適用于制造耐磨鋼管和耐磨薄片構(gòu)件,如礦山機(jī)械、水泥生產(chǎn)等所需的大量管狀、帶狀耐磨零部件或構(gòu)件。低淬透性薄帶耐磨鋼,具有良好的塑韌性,易于加工成型。一般采用該鋼制作的零部件,采用電阻焊接后,可直接進(jìn)行整體淬火或者高頻感應(yīng)淬火,獲得外表面具有1mm~2mm高硬度耐磨層的構(gòu)件,且構(gòu)件心部具有較高的塑韌性。普通的耐磨鋼雖然表面具有較高硬度,但由于添加了較多的cr、mo、ni等用于增加淬透性的元素,導(dǎo)致其心部具有同樣的高強(qiáng)高硬組織,進(jìn)而使其在受到折彎、剪切力時(shí)容易發(fā)生開(kāi)裂、崩裂,并且成形性較差。而低淬透性耐磨帶鋼,可根據(jù)需要加工成各種形狀,然后采用整體淬火或者感應(yīng)淬火的方法,制得具有良好塑韌性心部的構(gòu)件,具有成本低,易于批量生產(chǎn),使用靈活方便的特點(diǎn)。公告號(hào)為cn103725976b的中國(guó)發(fā)明專(zhuān)利公布了一種高耐磨雙金屬?gòu)?fù)合耐磨板,該發(fā)明在低碳鋼板或低碳合金鋼板上焊接耐磨合金層,按質(zhì)量百分?jǐn)?shù)計(jì),該耐磨合金層中各成分含量如下:c:0.35~0.55%、si:2~2.4%、mn:2.7~3.2%、cr:11~12.5%、mo:2.5~2.9%、v:0.7~1.8%、w:2.2~3.6%、b:0.7~1.1%,其余為fe。該發(fā)明采用堆焊方法,將上述耐磨合金層堆焊在低碳鋼表面,堆焊合金的硬度為hrc55~hrc58,所制構(gòu)件心部為低碳鋼板,具有較好的塑韌性,而表面為高碳高合金鋼板,具有較高的耐磨性。但其耐磨性完全是依靠耐磨合金本身的耐磨屬性,合金含量很高,使得所制構(gòu)件成本較高,并且所采用的堆焊方法具有施工速度慢的特點(diǎn),其只能在較為簡(jiǎn)單的構(gòu)件上使用。公告號(hào)為cn102134682b的中國(guó)發(fā)明專(zhuān)利公布了一種耐磨鋼板,該發(fā)明提供一種耐磨鋼板,其化學(xué)成分(重量%)為:c:0.31~0.40%、si:0.10~0.80%、mn:0.20~1.50%、p:≤0.050%、s:≤0.030%、cr:0~1.50%、mo:0~0.80%、al:0.02~0.20%、b:0.0005~0.0040%、ti:0~0.10%、ca:0~0.030%、0.10%≤cr+mo≤1.80%、0.05%≤al+ti≤0.18%,余量為fe和不可避免的雜質(zhì)。該耐磨鋼板的制造方法,包括冶煉、精煉、鑄造、軋制、淬火和回火等步驟。通過(guò)以上成分及工藝得到的550hb級(jí)耐磨鋼板硬度高≥550hb,可焊接和彎曲,微觀組織為馬氏體或馬氏體和殘余奧氏體。實(shí)現(xiàn)高強(qiáng)度、高硬度和較佳韌性的匹配,并具有可焊接性。該發(fā)明通過(guò)軋制、熱處理進(jìn)行組織調(diào)控,獲得了高強(qiáng)度、高硬度和高韌性的匹配,但其添加的合金元素依然較多,且經(jīng)過(guò)軋制淬火、回火步驟后鋼板本身具有高強(qiáng)度,導(dǎo)致其成形性、延展性差,不適宜于進(jìn)一步折彎成型、加工成復(fù)雜構(gòu)件。技術(shù)實(shí)現(xiàn)要素:本發(fā)明的目的就是要解決現(xiàn)有耐磨鋼淬透性高、使用過(guò)程中易發(fā)生開(kāi)裂、制備工藝復(fù)雜和成本較高的問(wèn)題,提供一種低淬透性耐磨帶鋼及其制造方法。為實(shí)現(xiàn)上述目的,本發(fā)明所設(shè)計(jì)的低淬透性耐磨帶鋼,按重量百分?jǐn)?shù)計(jì),其化學(xué)組成為:c:0.405~0.685%、si:0.10~0.20%、mn≤0.12%、p≤0.015%、s≤0.005%、ti:0.012~0.028%、nb:0.025~0.075%、als:0.015~0.038%、n:0.005~0.015%,余量為fe和不可避免雜質(zhì)。進(jìn)一步地,所述的低淬透性耐磨帶鋼,按重量百分?jǐn)?shù)計(jì),其化學(xué)組成為:c:0.480~0.600%、si:0.15~0.18%、mn≤0.10%、p≤0.010%、s≤0.003%、ti:0.012~0.023%、nb:0.025~0.065%、als:0.020~0.030%、n:0.007~0.010%,余量為fe和不可避免的雜質(zhì)。進(jìn)一步地,所述的低淬透性耐磨帶鋼,按重量百分?jǐn)?shù)計(jì),其化學(xué)組成為:c:0.600%、si:0.15%、mn:0.008%、p:0.008%、s:0.003%、ti:0.012%、nb:0.040%、als:0.030%、n:0.010%,余量為fe和不可避免的雜質(zhì)。本發(fā)明各元素的作用及組成依據(jù)如下:c:c是提高硬度、強(qiáng)度和耐磨性的主要元素,鋼中的c在0.405~0.685%范圍可保證淬火后表面硬度,當(dāng)鋼中碳含量大于0.685%,淬透性深度會(huì)增加,導(dǎo)致薄鋼板淬透性超過(guò)要求的值;當(dāng)鋼中碳含量小于0.405時(shí),表面淬火硬度不夠。本發(fā)明中c含量控制在0.405~0.685%,優(yōu)選的c含量為0.48~0.60%。si:si是煉鋼脫氧的必要元素,以固溶強(qiáng)化形式提高鋼的強(qiáng)度,且能提高c在鋼中的活度,從而加大鋼帶表面脫碳傾向,si含量太低脫氧效果不佳,si含量太高會(huì)增加淬透性和降低韌性。本發(fā)明中si含量控制在0.10~0.20%,優(yōu)選的si含量為0.15~0.18%mn:mn是提高鋼板淬透性的重要元素,mn含量高會(huì)造成較嚴(yán)重的中心偏析和降低韌性。本發(fā)明中mn含量控制在mn≤0.12%,優(yōu)選的mn含量為mn≤0.10%。al:al是重要的細(xì)化晶粒元素,al可通過(guò)與n形成aln,細(xì)化奧氏體晶粒度,形成本質(zhì)細(xì)晶粒鋼,aln屬于高溫穩(wěn)定型析出物,然而al對(duì)于增加鋼的淬透性沒(méi)有明顯效果,且al含量過(guò)高,容易與o形成顆粒較大的尖角不規(guī)則形狀的al2o3,使母材韌性惡化。本發(fā)明中al含量控制在0.015~0.038%,優(yōu)選的al含量為0.020~0.030%。nb:nb具有細(xì)化晶粒的作用,且對(duì)提高鋼的淬透性效果不明顯。鋼中添加nb與c和n形成nbx(cn)y的析出物,在700℃到900℃軋制,奧氏體再結(jié)晶與合金碳氮化物析出相競(jìng)爭(zhēng),nbx(cn)y等相優(yōu)先在奧氏體內(nèi)的位錯(cuò)上析出,析出能顯著釘軋晶界,奧氏體再結(jié)晶滯后,從而使加工硬化奧氏體易于轉(zhuǎn)變?yōu)殍F素體。鋼中nb含量添加超過(guò)0.075%以后,容易形成大顆粒的nbx(cn)y析出物,不能起到顯著細(xì)化晶粒作用,而且還具有降低鋼的韌性的作用。本發(fā)明中nb含量控制在0.025~0.075%,優(yōu)選的nb含量為0.025~0.065%。ti:ti可顯著細(xì)化晶粒,能夠與n形成tin,同時(shí)不會(huì)顯著提高淬透性。鋼中的tin化合物具有較高的熱穩(wěn)定性,在1400℃左右仍不會(huì)發(fā)生明顯的溶解,可以有效釘軋奧氏體晶界,防止加熱過(guò)程中奧氏體的長(zhǎng)大。但tin夾雜物容易在連鑄過(guò)程中產(chǎn)生大顆粒立方體夾雜,這類(lèi)形狀?yuàn)A雜物對(duì)韌性具有顯著的影響,因此,ti含量不宜過(guò)高。本發(fā)明中ti含量控制在0.012~0.028%,優(yōu)選的ti含量為0.012~0.023%。n:n作為與鋼中ti和al形成高溫穩(wěn)定細(xì)小的化合物的關(guān)鍵因素,必須保證其在鋼中的含量,但n添加太多,會(huì)造成形成的al和ti的氮化物尺寸過(guò)大,不利于韌性的提高。本發(fā)明中n含量控制在0.005~0.015%,優(yōu)選的n含量為0.007~0.010%,s:s是鋼中有害元素,常以mn的硫化物形態(tài)存在,其對(duì)鋼韌性的不利影響較大,且本發(fā)明鋼由于淬透性的限制,盡可能不添加mn,若在此情況下,鋼中有較多s,會(huì)導(dǎo)致形成fes等,連鑄形成熱裂紋,因此,應(yīng)盡可能降低s含量。本發(fā)明中s含量控制在s≤0.005%,優(yōu)選的s含量為s≤0.003%p:p固溶強(qiáng)化元素,鋼中適量的p可促進(jìn)鐵素體的形成,并保持強(qiáng)度和塑形的良好平衡,但p含量過(guò)高,易引起鑄坯中心偏析,對(duì)鋼的冷彎成型性能和韌性造成不利影響。本發(fā)明中p含量控制在p≤0.015%,優(yōu)選的p含量為p≤0.010%本發(fā)明還提供了一種低淬透性耐磨帶鋼的制造方法,包括鐵水脫硫預(yù)處理、轉(zhuǎn)爐冶煉、lf+rh爐精煉、板坯連鑄、鑄坯緩冷、板坯加熱、熱連軋、acc冷卻和卷取工藝,所述的鑄坯緩冷工藝,采用堆垛緩冷;所述的板坯加熱工藝,加熱溫度為1170~1220℃,加熱時(shí)間300~400min;所述的熱連軋工藝,粗軋開(kāi)軋溫度≥1150℃,粗軋終軋溫度為970~1100℃,末道次壓下量≥35%,精軋開(kāi)軋溫度為880~920℃,壓下量≥65%,精軋終軋溫度為780~820℃;所述的acc冷卻工藝,采取前端冷卻,冷卻速率≤10℃/s;所述的卷取工藝,卷取溫度為700~720℃。進(jìn)一步地,由于鋼中未添加mo、ni、cu、cr等高含量的合金元素,不需要長(zhǎng)時(shí)間的高溫加熱來(lái)保證合金元素固溶,而且較低的加熱溫度輔以鋼中析出物tin的釘扎作用,可保證在加熱階段奧氏體晶粒得到充分的細(xì)化,因此,本發(fā)明所述的板坯加熱工藝中優(yōu)選的加熱溫度為1170~1210℃。進(jìn)一步地,為了在奧氏體再結(jié)晶區(qū),取得細(xì)化原奧氏體晶粒的效果,采用較大的壓下量進(jìn)行軋制,同時(shí),為了保證后期精軋溫度在一個(gè)合理的范圍內(nèi),本發(fā)明優(yōu)選的粗軋終軋溫度控制在970~1000℃,末道次壓下量≥35%。進(jìn)一步地,在較低的奧氏體非再結(jié)晶溫度進(jìn)行高的壓下量軋制,可充分扁平化奧氏體晶粒,從而在其中產(chǎn)生大量位錯(cuò)和nbx(cn)y的析出,進(jìn)而保證在精軋終軋完成之后,奧氏體向鐵素體轉(zhuǎn)變過(guò)程中,大量的鐵素體晶粒和珠光體具有充分的形核位置和高的形核率,從而有利于最大限度的細(xì)化組織,得到細(xì)晶組織,因此本發(fā)明優(yōu)選的精軋開(kāi)軋溫度控制在880℃~910℃,壓下量≥65%。本發(fā)明的主要原理是通過(guò)最大程度細(xì)化晶粒,來(lái)降低材料的淬透性,同時(shí)以廉價(jià)的c為主要增加硬度和耐磨性的元素,以nb、ti、al為顯著的細(xì)化晶粒的元素,充分減少增加淬透性元素如si、mn等的含量,可在保證低淬透性的前提下,降低生產(chǎn)成本。本發(fā)明的優(yōu)點(diǎn)在于:(1)本發(fā)明設(shè)計(jì)的低淬透性耐磨帶鋼,采用中高碳鋼成分設(shè)計(jì),未添加ni、mo、cu、cr等貴重合金和淬透性較高的合金,在降低生產(chǎn)成本的同時(shí),也可保證其低淬透性,而且本發(fā)明添加了nb、ti等細(xì)化晶粒的元素,保證了本發(fā)明所設(shè)計(jì)帶鋼基體的韌性,同時(shí)由于晶粒的細(xì)化,進(jìn)一步有利于降低其淬透性。(2)本發(fā)明通過(guò)嚴(yán)格控制板坯加熱工藝中的加熱溫度、熱連軋工藝中的粗軋終軋溫度以及熱連軋工藝中的精軋開(kāi)軋和終軋溫度,有利于本發(fā)明所設(shè)計(jì)鋼中晶粒得到充分的細(xì)化,進(jìn)而有利于降低其淬透性和提高其韌性。本發(fā)明所設(shè)計(jì)的低淬透性耐磨帶鋼的晶粒度可達(dá)到10~12級(jí),淬硬層深度約1.5mm,其-20℃kv2沖擊功≥95j。附圖說(shuō)明圖1為本發(fā)明低淬透性耐磨帶鋼的熱軋態(tài)金相組織顯微結(jié)構(gòu)示意圖。圖2為本發(fā)明低淬透性耐磨帶鋼的淬火態(tài)表層金相組織顯微結(jié)構(gòu)示意圖。具體實(shí)施方式以下結(jié)合附圖和具體實(shí)施例對(duì)本發(fā)明作進(jìn)一步的詳細(xì)描述。本發(fā)明優(yōu)選實(shí)施例1~4對(duì)本發(fā)明所述低淬透性耐磨帶鋼及其制造方法進(jìn)行進(jìn)一步的詳細(xì)描述,并采用對(duì)比例1~4對(duì)本發(fā)明所設(shè)計(jì)的低淬透性耐磨帶鋼的化學(xué)成分及主要制備工藝參數(shù)進(jìn)行進(jìn)一步的對(duì)比說(shuō)明。表1為實(shí)施例1~4及對(duì)比例1~4的化學(xué)組成。上述實(shí)施例1~4及對(duì)比例1~4所述的低淬透性耐磨帶鋼的制造方法,主要包括鐵水脫硫預(yù)處理、轉(zhuǎn)爐冶煉、lf+rh爐精煉、板坯連鑄、鑄坯緩冷、板坯加熱、熱連軋、acc冷卻和卷取工藝;所述的鑄坯緩冷工藝,采用堆垛緩冷;所述的板坯加熱工藝,加熱溫度為1170~1220℃,加熱時(shí)間300~400min;所述的熱連軋工藝,粗軋開(kāi)軋溫度≥1150℃,粗軋終軋溫度為970~1100℃,末道次壓下量≥35%,精軋開(kāi)軋溫度為880~920℃,壓下量≥65%,精軋終軋溫度為780~820℃;所述的acc冷卻工藝,采取前端冷卻,冷卻速率≤10℃/s;所述的卷取工藝,卷取溫度為700~720℃。表2為實(shí)施例1~4及對(duì)比例1~4的主要制備工藝參數(shù)。更具體地,按照表2所示的主要制備工藝參數(shù)生產(chǎn)實(shí)施例1~4及對(duì)比例1~4所述的低淬透性耐磨帶鋼。表1:化學(xué)組成(wt%)編號(hào)csimnpsnbtialsn實(shí)施例10.4050.200.050.0080.0040.0450.020.0150.005實(shí)施例20.6850.100.040.0150.0040.0250.0280.0380.015實(shí)施例30.5200.170.120.010.0050.0750.0180.0280.012實(shí)施例40.6000.150.080.0080.0030.0400.0120.0300.010對(duì)比例10.5800.150.060.0080.0050.0350.0280.0300.011對(duì)比例20.6501.000.050.0080.0050.0450.0220.0260.003對(duì)比例30.6000.130.070.0080.0050.1000.0280.0350.012對(duì)比例40.6300.150.250.0080.0040.0470.0250.0300.012表2:主要制備工藝參數(shù)參照gb/t225《鋼的淬透性末端淬火試驗(yàn)方法》,從本發(fā)明所制低淬透性耐磨帶鋼的熱軋態(tài)鋼板上取直徑為5mm,長(zhǎng)度100mm圓柱體進(jìn)行末端淬火試驗(yàn),試驗(yàn)中采用洛氏硬度測(cè)量末端硬度,并距離端部5mm,每間隔0.5mm測(cè)量洛氏硬度hrc值;距離端部5mm~11mm,每隔2mm測(cè)量洛氏硬度hrc值,以洛氏硬度hrc值≥56為淬硬層深度。對(duì)于厚度>7mm的帶鋼,參照gb/t229《金屬夏比缺口沖擊試驗(yàn)方法》測(cè)定本發(fā)明所制低淬透性耐磨帶鋼的-20℃低溫沖擊韌性。表3為實(shí)施例1~4及對(duì)比例1~4的洛氏硬度hrc值及-20℃kv2沖擊功。由表3可知,采用本發(fā)明方法制備的低淬透性耐磨帶鋼(實(shí)施例1~4)的淬硬層深度為1.5mm,淬透性較低,且所制鋼-20℃kv2沖擊功在95j~135j范圍內(nèi),沖擊韌性較高。對(duì)比例1因其加熱溫度過(guò)高,后續(xù)粗軋溫度和精軋溫度均偏高,壓下率較小,導(dǎo)致其晶粒較粗,淬硬層深度達(dá)到3.5mm,顯著高于實(shí)施例1~4,且其沖擊韌性顯著低于實(shí)施例1~4。對(duì)比例2因其si和n含量的提高,不利于晶粒細(xì)化,其淬硬層深度達(dá)到3.0mm,高于實(shí)施例1~4,且n含量的提高,使形成的tin析出物尺寸較大,嚴(yán)重影響其沖擊韌性。對(duì)比例3中加入過(guò)多的nb元素,使其在精軋階段形成的nbx(cn)y尺寸過(guò)大,不能起到釘扎位錯(cuò)和抑制再結(jié)晶的作用,導(dǎo)致其細(xì)化晶粒效果較差,沖擊韌性較低,顯著低于實(shí)施例1~4。對(duì)比例4中加入過(guò)多的mn元素,顯著增加了淬透性,淬硬層深度達(dá)到4.0mm,顯著高于實(shí)施例1~4,且其沖擊韌性也不高。表3:hrc值及-20℃kv2沖擊功圖1和圖2分別為采用本發(fā)明方法設(shè)計(jì)的低淬透性耐磨帶鋼熱軋態(tài)金相組織顯微結(jié)構(gòu)示意圖和淬火態(tài)表層金相組織顯微結(jié)構(gòu)示意圖。由圖1和圖2可知,采用本發(fā)明方法設(shè)計(jì)的低淬透性耐磨帶鋼的組織特征形貌均勻,金相組織為鐵素體和細(xì)密珠光體組織,無(wú)帶狀組織析出,晶粒尺寸較小,晶粒度按照gb/t6394《金屬平均晶粒度測(cè)定方法》評(píng)測(cè),達(dá)到10~12級(jí),從而使得本發(fā)明所制帶鋼具有良好的塑形、韌性和低淬透性。當(dāng)前第1頁(yè)12